模具专业英语毕业课程设计外文文献翻译、中英文翻译
模具毕业设计外文翻译(英文+译文)
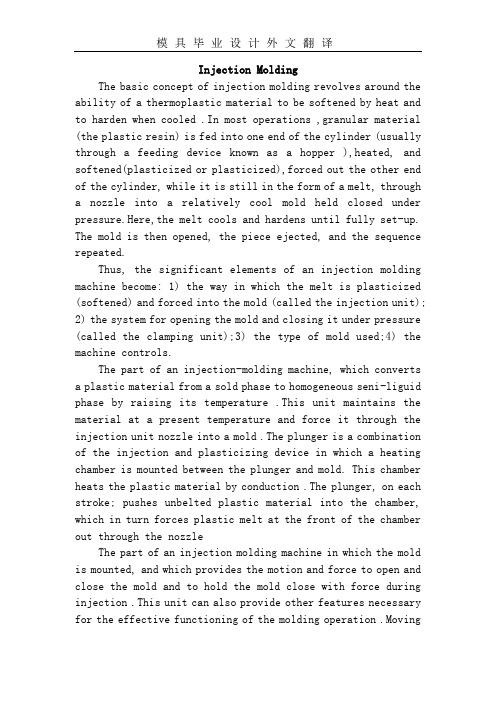
Injection MoldingThe basic concept of injection molding revolves around the ability of a thermoplastic material to be softened by heat and to harden when cooled .In most operations ,granular material (the plastic resin) is fed into one end of the cylinder (usually through a feeding device known as a hopper ),heated, and softened(plasticized or plasticized),forced out the other end of the cylinder, while it is still in the form of a melt, through a nozzle into a relatively cool mold held closed under pressure.Here,the melt cools and hardens until fully set-up. The mold is then opened, the piece ejected, and the sequence repeated.Thus, the significant elements of an injection molding machine become: 1) the way in which the melt is plasticized (softened) and forced into the mold (called the injection unit);2) the system for opening the mold and closing it under pressure (called the clamping unit);3) the type of mold used;4) the machine controls.The part of an injection-molding machine, which converts a plastic material from a sold phase to homogeneous seni-liguid phase by raising its temperature .This unit maintains the material at a present temperature and force it through the injection unit nozzle into a mold .The plunger is a combination of the injection and plasticizing device in which a heating chamber is mounted between the plunger and mold. This chamber heats the plastic material by conduction .The plunger, on each stroke; pushes unbelted plastic material into the chamber, which in turn forces plastic melt at the front of the chamber out through the nozzleThe part of an injection molding machine in which the mold is mounted, and which provides the motion and force to open and close the mold and to hold the mold close with force during injection .This unit can also provide other features necessary for the effective functioning of the molding operation .Movingplate is the member of the clamping unit, which is moved toward a stationary member. the moving section of the mold is bolted to this moving plate .This member usually includes the ejector holes and mold mounting pattern of blot holes or “T” slots .Stationary plate is the fixed member of the clamping unit on which the stationary section of the mold is bolted .This member usually includes a mold-mounting pattern of boles or “T” slots. Tie rods are member of the clamping force actuating mechanism that serve as the tension member of the clamp when it is holding the mold closed. They also serve as a gutted member for the movable plate .Ejector is a provision in the clamping unit that actuates a mechanism within the mold to eject the molded part(s) from the mold .The ejection actuating force may be applied hydraulically or pneumatically by a cylinder(s) attached to the moving plate, or mechanically by the opening stroke of the moving plate.Methods of melting and injecting the plastic differ from one machine to another and are constantly being implored .conventional machines use a cylinder and piston to do both jobs .This method simplifies machine construction but makes control of injection temperatures and pressures an inherently difficult problem .Other machines use a plasticizing extruder to melt the plastic and piston to inject it while some hare been designed to use a screw for both jobs :Nowadays, sixty percent of the machines use a reciprocating screw,35% a plunger (concentrated in the smaller machine size),and 5%a screw pot.Many of the problems connected with in ejection molding arise because the densities of polymers change so markedly with temperature and pressure. thigh temperatures, the density of a polymer is considerably cower than at room temperature, provided the pressure is the same.Therefore,if molds were filled at atmospheric pressure, “shrinkage” would make the molding deviate form the shape of the mold.To compensate for this poor effect, molds are filled at high pressure. The pressure compresses the polymer and allows more materials to flow into the mold, shrinkage is reduced and better quality moldings are produced.Cludes a mold-mounting pattern of bolt holes or “T” slots. Tie rods are members of the clamping force actuating mechanism that serve as the tension members of clamp when it is holding the mold closed. Ejector is a provision in the calming unit that actuates a mechanism within the mold to eject the molded part(s) form the mold. The ejection actuating force may be applied hydraulically or pneumatically by a cylinder(s) attached to the moving plate, or mechanically by the opening stroke of the moving plate.The function of a mold is twofold: imparting the desired shape to the plasticized polymer and cooling the injection molded part. It is basically made up of two sets of components: the cavities and cores and the base in which the cavities and cores are mounted. The mold ,which contains one or more cavities, consists of two basic parts :(1) a stationary molds half one the side where the plastic is injected,(2)Moving half on the closing or ejector side of the machine. The separation between the two mold halves is called the parting line. In some cases the cavity is partly in the stationary and partly in the moving section. The size and weight of the molded parts limit the number of cavities in the mold and also determine the machinery capacity required. The mold components and their functions are as following:(1)Mold Base-Hold cavity (cavities) in fixed, correctposition relative to machine nozzle.(2)Guide Pins-Maintain Proper alignment of entry into moldinterior.(3)Spree Bushing (spree)-Provide means of entry into moldinterior.(4)Runners-Conroy molten plastic from spree to cavities.(5)Gates-Control flow into cavities.(6)Cavity (female) and Force (male)-Control the size,shape and surface of mold article.(7)Water Channels-Control the temperature of mold surfacesto chill plastic to rigid state.(8)Side (actuated by came, gears or hydrauliccylinders)-Form side holes, slots, undercuts and threaded sections.(9)Vent-Allow the escape of trapped air and gas.(10)Ejector Mechanism (pins, blades, stripper plate)-Ejectrigid molded article form cavity or force.(11)Ejector Return Pins-Return ejector pins to retractedposition as mold closes for next cycle.The distance between the outer cavities and the primary spree must not be so long that the molten plastic loses too much heat in the runner to fill the outer cavities properly. The cavities should be so arranged around the primary spree that each receives its full and equal share of the total pressure available, through its own runner system (or the so-called balanced runner system).The requires the shortest possible distance between cavities and primary sprue, equal runner and gate dimension, and uniform culling.注射成型注射成型的基本概念是使热塑性材料在受热时熔融,冷却时硬化,在大部分加工中,粒状材料(即塑料树脂)从料筒的一端(通常通过一个叫做“料斗”的进料装置)送进,受热并熔融(即塑化或增塑),然后当材料还是溶体时,通过一个喷嘴从料筒的另一端挤到一个相对较冷的压和封闭的模子里。
塑料模具中英文对照外文翻译文献

中英文资料翻译The development of plastic mouldChina's industrial plastic moulds from the start to now, after more than half a century, there has been great development, mold levels have been greatly enhanced. Mould has been at large can produce 48-inch big-screen color TV Molded Case injection mold, 6.5 kg capacity washing machine full of plastic molds, as well as the overall car bumpers and dashboards, and other plastic mould precision plastic molds, the camera is capable of producing plastic mould , multi-cavity mold small modulus gear and molding mold. --Such as Tianjin and Yantai days Electrical Co., Ltd Polaris IK Co. manufactured multi-cavity mold VCD and DVD gear, the gear production of such size precision plastic parts, coaxial, beating requirements have reached a similar foreign the level of product, but also the application of the latest gear design software to correct contraction as a result of the molding profile error to the standard involute requirements. Production can only 0.08 mm thickness of a two-cavity mold and the air Cup difficulty of plastic doors and windows out of high modulus, and so on. Model cavity injection molding manufacturing accuracy of 0.02 to 0.05 mm, surface roughness Ra0.2 μ m, mold quality, and significantly increase life expectancy, non-hardening steel mould life up to 10~ 30 million, hardening steel form up to 50 ~ 10 million times, shorten the delivery time than before, but still higher than abroad, and the gap between a specific data table.Process, the multi-material plastic molding die, efficient multicolor injection mould, inserts exchange structure and core pulling Stripping the innovative design has also made great progress. Gas-assisted injection molding, the use of more mature technologies, such as Qingdao Hisense Co., Ltd., Tianjin factory communications and broadcasting companies, such as mold manufacturers succeeded in 29 ~ 34-inch TV thick-walled shell, as well as some parts on the use of gas-assisted mould technology Some manufacturers also use the C-MOLD gas-assisted software and achieved better results. Prescott, such as Shanghai, such as the new company will provide users with gas-assisted molding equipment and technology. Began promoting hot runner mold, and some plants use rate of more than 20 percent, the general heat-thermal hot runner, or device, a small number of units with the world's advanced level of rigorous hot runner-needle device, a small number of units with World advanced level of rigorous needle-hot runner mould. However, the use of hot runner overall rate of less than 10%, with overseas compared to 50 ~ 80%, the gap larger.In the manufacturing technology, CAD / CAM / CAE technology on the level of application of a new level to the enterprise for the production of household appliances representatives have introduced a considerable number of CAD / CAMsystems, such as the United States EDS UG Ⅱ, the United States Parametric Technology Pro / Engineer, the United States CV CADS5 company, the British company DOCT5 Deltacam, HZS's CRADE Japan, the company's Cimatron Israel, the United States AC-C-Tech Mold Company and Australia's MPA Mold flow Mold analysis software, and so on. These systems and the introduction of the software, althougha lot of money spent, but in our country die industry, and achievinga CAD / CAM integration, and to support CAE technology to forming processes such as molding and cooling, such as computer simulation, and achieved certain The technical and economic benefits, promote and facilitate China's CAD / CAM technology. In recent years, China's own development of the plastic mould CAD / CAM system has achieved significant development, the main guarantor Software Engineering Institute, is the development of CAXA, Huazhong University of Science HSC5.0 development of the system and injection mold CAE software, and so on, these Die of domestic software with the specific circumstances in the application of computer and lower prices, and other characteristics, in order to further universal CAD / CAM technology has created good conditions.In recent years, China has been more extensive use of some new plastic mold steel, such as: P20, 3Cr2Mo, PMS, SM Ⅰ, SM Ⅱ, and the quality of life of mold has a direct significant impact on the overall use of the still less . Plastic Moulds standard model planes, such as standard putter and spring has given more applications, and there have been some of the commercializationof domestic hot runner system components. However, at present China Die level of standardization and commercialization in the general level of below 30 percent and foreign advanced industrial countries has reached 70 percent compared to 80 percent, still a large gap. Table 1, at home and abroad plastic mould technology comparison table? Domestic projects abroad cavity injection model mm0.02 accuracy of 0.005 ~0.01 ~0.05mm cavity surface roughness Ra0.01 ~ 0.05 μ mRa0.20 μ m non-hardened steel die life 10 to 60 million 10 ~ 30 million hardened steel die life 160 ~ 300 million of 50 ~ 100 million hot runner mould overall utilization rate of more than 80 per cent less than 10 per cent level of standardization of 70 ~80% less than 30% of medium-sized plastic mould production cycle about a month 2 ~4 months in the mold industry in the amount of 30 to 40% 25 to 30% According to the parties concerned forecast, the market's overall vigorous mold is a smooth upward, in the next Die market, the development of plastic mould faster than the other Die, die in the proportion of industry will gradually improve. With the continuous development of the plastics industry, put on the plastic mold growing demands is a normal, and so sophisticated, large-scale, complex, long-life plastic mould development will be higher than the overall pace of development. At the same time, imports in recent years because of the mold, precision, large, complex, long-life die in the majority, therefore, reduce imports, increase Guochanhualu: perspective, in the mold of such high-end market share will gradually increase. The rapid development of theconstruction industry so that the various Profile Extrusion Die, PVC plastic pipe fittings Die Die market become a new economic growth point, the rapid development of highways, car tires also put a higher demand, radial tire Die, Die particularly active pace of development will also be higher than the overall average level of the plastic and wood, plastic and metal to make plastic molds in the automotive, motorcycle industry in the demand for huge household appliances industry in the "10th Five-Year Plan" period have greater development, especially refrigerators,air-conditioners and microwave ovens, and other parts of the great demand for plastic moulds, and electronics and communications products, in addition to audio-video products, such as color televisions, laptop computers and set-top boxes will be given a wider network development, which are Plastic Mold market is the growth point. Second, China's industrial and technological plastic mould the future direction of the major developments will include: 1, raising large, sophisticated, complex, long-life mold design and manufacturing standards and proportion. This is due to the molding plastic mould products increasingly large, complex and high-precision requirements, as well as requirements for high productivity and the development of a multi-mode due. 2, in the design and manufacture of plastic mould fully promote the use of CAD / CAM / CAE technology. CAD / CAM technology has developed into a relatively mature technology common in recent years CAD / CAM technology hardware and software prices has been reduced to SMEsgenerally acceptable level of popularity for further create good conditions; based on network CAD / CAM / CAE system integration structure the initial signs of emerging, and it will solve the traditional mixed CAD / CAM system can not meet the actual production process requirements of the division of collaboration; CAD / CAM software will gradually improve intelligence plastic parts and the 3-D mold design and prototyping process 3-D analysis will be in our plastic mould industries play an increasingly important role. 3, promote the use of hot runner technology, gas-assisted injection molding technology and high-pressure injection molding technology. Using hot runner mould technology can improve the productivity and quality of parts and plastic parts can be substantial savings of raw materials and energy conservation, extensive application of this technology is a big plastic mould changes. Hot Runner components formulate national standards, and actively produce cheap high-quality components, the development of hot runner mold is the key. Gas-assisted injection molding product quality can be guaranteed under the premise of substantially lower cost. Currently in the automotive and appliance industries gradually promote the use of the Chiang Kai-shek. Gas-assisted injection molding of the ordinary than the traditional injection of more parameters need to identify and control, and its more commonly used in large, complex products, mold design and control more difficult, therefore, the development of gas-assisted molding flow analysis software It seems veryimportant. On the other hand in order to ensure precision plastic parts to continue to study the development of technology and high-pressure injection molding and injection-compression molding mould and die technology is also very important. 4, the development of new plastics molding technology and rapid economic mold. To adapt to more variety, less volume of production. 5, and improve standardization of plastic mould standard parts usage. China's mold and die level of standard parts standardization still low, the gap between the large and foreign, to a certain extent constraining the development of industries in our country die, die to improve quality and reduce manufacturing costs Die, Die standard parts to vigorously promote the application. To this end, first of all, to formulate a unified national standards, and in strict accordance with the standards of production, secondly it is necessary to gradually scale production, to improve the commercialization of the standard of quality, and reduce costs;again it is necessary to further increase the standard specifications of varieties. 6, Die application quality materials and advanced surface treatment technology for improving the quality of life and mold it is necessary. 7, research and application of high-speed die measurement technology and reverse engineering. CMM-use 3D scanner or reverse engineering is the realization of plastic moulds CAD / CAM one of the key technologies.Research and Application of diversity, adjustment, cheap detection equipment is to achieve the necessary precondition forreverse engineering.塑料模具的发展我国塑料模工业从起步到现在,历经半个多世纪,有了很大发展,模具水平有了较大提高。
模具设计专业毕设外文翻译译文(DOC)

本科毕业设计(论文)外文翻译(附外文原文)学院:机械与控制工程学院课题名称:复杂阶梯形圆筒件拉深有限元分析专业(方向):机械设计制造及其自动化(模具设计与制造)班级:学生:指导教师:日期:拉伸模设计中拉伸壁起皱的分析摘要本文研究带有斜度的方形盒和带有阶梯的方形盒的拉深中发生的起皱现象。
这两种类型的起皱现象有一个共同的特征:全都发生在相对无支撑、无压边的拉深壁处。
在带有斜度的方形盒的拉深中,常受到工序参数的影响,例如:模具的间隙值和压边力等,所以常用有限元模拟的方法来研究分析起皱的发生。
模拟的结果表明模具的间隙值越大,起皱现象就越严重,而且增加压边力也不能抑制和消除起皱现象的发生。
在带有阶梯的方形盒拉深的起皱现象分析中,常通过实际生产中一种近似的几何结构来研究、试验。
当凸模与阶梯边缘之间的金属板料在拉深时分布并不均衡,就会在侧壁发生起皱现象。
为了消除起皱现象的发生,一个最优的模具设计常采用有限元的方法进行分析。
模拟的结果和起皱试验论证了有限元分析的准确性,并且表明了在拉深模具设计中使用有限元方法分析的优越性。
关键词:侧壁起皱;拉深模;带有阶梯的方形盒;带有斜度的方形盒1 引言起皱是金属板料成形中常见的失效形式之一。
由于功能和视觉效果的原因,起皱通常是不能为零件制品所能接受的。
在金属板料成形加工中通常存在三种类型的起皱现象:法兰起皱;侧壁起皱和由于残余压应力在未变形区产生的弹性变形。
在冲压复杂形状的时候,拉深壁起皱就是在模具型腔中形成的褶皱。
由于金属板料在拉深壁区域内相对无支撑,因此,消除拉深壁起皱比抑制法兰起皱要难得多。
我们知道在不被支撑的拉深壁区域中材料的外力拉深可以防止起皱,这可以在实践中通过增加压边力而实现,但是运用过大的拉深力会引起破裂失效。
因此,压边力必须控制在一定的范围内,一方面可以抑制起皱,另一方面也可以防止破裂失效。
合适的压边力范围是很难确定的,因为起皱在拉深零件的中心区域以一个复杂的形状形成,甚至根本不存在一个合适的压边力范围。
冲压模具设计毕业外文翻译 中英文翻译 外文文献翻译

冲压模具设计毕业外文翻译中英文翻译外文文献翻译毕业设计(论文)外文资料翻译系部:专业:姓名:学号:外文出处: The Pofessional English of DesignManufacture for Dies & Moulds附件: 1.外文资料翻译译文,2.外文原文。
指导教师评语:签名:年月日附件1:外文资料翻译译文冲压模具设计对于汽车行业与电子行业,各种各样的板料零件都是有各种不同的成型工艺所生产出来的,这些均可以列入一般种类“板料成形”的范畴。
板料成形(也称为冲压或压力成形)经常在厂区面积非常大的公司中进行。
如果自己没有去这些大公司访问,没有站在巨大的机器旁,没有感受到地面的震颤,没有看巨大型的机器人的手臂吧零件从一个机器移动到另一个机器,那么厂区的范围与价值真是难以想象的。
当然,一盘录像带或一部电视专题片不能反映出汽车冲压流水线的宏大规模。
站在这样的流水线旁观看的另一个因素是观看大量的汽车板类零件被进行不同类型的板料成形加工。
落料是简单的剪切完成的,然后进行不同类型的加工,诸如:弯曲、拉深、拉延、切断、剪切等,每一种情况均要求特殊的、专门的模具。
而且还有大量后续的加工工艺,在每一种情况下,均可以通过诸如拉深、拉延与弯曲等工艺不同的成形方法得到所希望的得到的形状。
根据板料平面的各种各样的受应力状态的小板单元体所可以考虑到的变形情形描述三种成形,原理图1描述的是一个简单的从圆坯料拉深成一个圆柱水杯的成形过程。
图1 板料成形一个简单的水杯拉深是从凸缘型坯料考虑的,即通过模具上冲头的向下作用使材料被水平拉深。
一个凸缘板料上的单元体在半径方向上被限定,而板厚保持几乎不变。
板料成形的原理如图2所示。
拉延通常是用来描述在板料平面上的两个互相垂直的方向被拉长的板料的单元体的变形原理的术语。
拉延的一种特殊形式,可以在大多数成形加工中遇到,即平面张力拉延。
在这种情况下,一个板料的单元体仅在一个方向上进行拉延,在拉长的方向上宽度没有发生变化,但是在厚度上有明确的变化,即变薄。
模具设计相关专业毕业论文(外文原文+翻译)之翻译[管理资料]
![模具设计相关专业毕业论文(外文原文+翻译)之翻译[管理资料]](https://img.taocdn.com/s3/m/63ac390ff705cc1754270968.png)
可行成形图在汽车覆盖件冲压工艺高效设计的应用Dae-Cheol Ko a,Seung-Hoon Cha b,Sang-Kon Lee c,Chan-Joo Lee b,Byung-Min Kim d,*a ILIC, Pusan National University, 30 Jangjeon-Dong, Kumjeong-Gu, Busan609-735, South Koreab Precision Manufacturing Systems Division, Pusan National University, 30Jangjeon-Dong, Kumjeong-Gu, Busan 609-735, South Koreac PNU-IFAM, Joint Research Center, Pusan National University, 30Jangjeon-Dong, Kumjeong-Gu, Busan 609-735, South Koread School of Mechanical Engineering, Pusan National University, 30 Jangjeon-Dong, Kumjeong-Gu, Busan 609-735, South Korea摘要:本文提出使用可行的成形图来表示无断裂和起皱的安全区域,进而有效和快速地设计冲压工艺方法。
要确定可行的成形图,有限元分析对应于正交实验设计的过程变量组合。
随后,基于成形极限图的有限元分析,确定断裂和起皱的特征值。
所有组合的特征值在整个过程中,通过人工神经网络训练进行了一系列预测。
可行的成形图从所有组合的过程变量中最终确定。
以汽车覆盖件如转动架和车轮毂的冲压工艺作为实例来验证利用成形图的进行过程设计有效性。
有限元模拟结果与实验模拟结果比较表明,利用可行的成形图来进行冲压工艺的设计是有效的并适用于实际的过程。
注塑模具之模具设计与制造外文文献翻译、中英文翻译
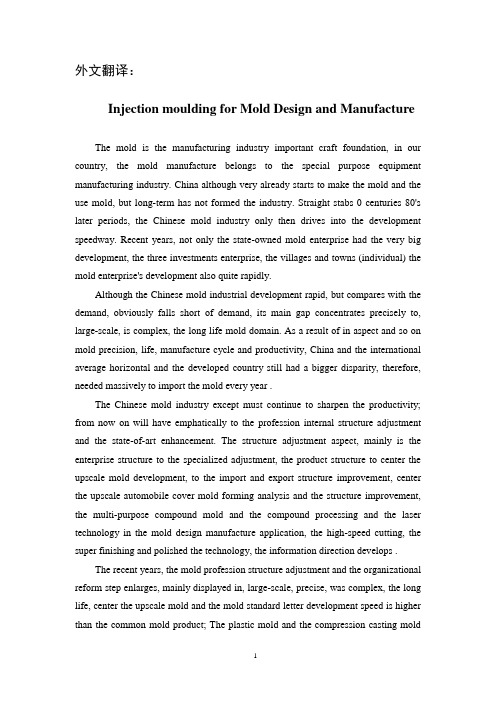
外文翻译:Injection moulding for Mold Design and ManufactureThe mold is the manufacturing industry important craft foundation, in our country, the mold manufacture belongs to the special purpose equipment manufacturing industry. China although very already starts to make the mold and the use mold, but long-term has not formed the industry. Straight stabs 0 centuries 80's later periods, the Chinese mold industry only then drives into the development speedway. Recent years, not only the state-owned mold enterprise had the very big development, the three investments enterprise, the villages and towns (individual) the mold enterprise's development also quite rapidly.Although the Chinese mold industrial development rapid, but compares with the demand, obviously falls short of demand, its main gap concentrates precisely to, large-scale, is complex, the long life mold domain. As a result of in aspect and so on mold precision, life, manufacture cycle and productivity, China and the international average horizontal and the developed country still had a bigger disparity, therefore, needed massively to import the mold every year .The Chinese mold industry except must continue to sharpen the productivity; from now on will have emphatically to the profession internal structure adjustment and the state-of-art enhancement. The structure adjustment aspect, mainly is the enterprise structure to the specialized adjustment, the product structure to center the upscale mold development, to the import and export structure improvement, center the upscale automobile cover mold forming analysis and the structure improvement, the multi-purpose compound mold and the compound processing and the laser technology in the mold design manufacture application, the high-speed cutting, the super finishing and polished the technology, the information direction develops .The recent years, the mold profession structure adjustment and the organizational reform step enlarges, mainly displayed in, large-scale, precise, was complex, the long life, center the upscale mold and the mold standard letter development speed is higher than the common mold product; The plastic mold and the compression casting moldproportion increases; Specialized mold factory quantity and its productivity increase; "The three investments" and the private enterprise develops rapidly; The joint stock system transformation step speeds up and so on. Distributes from the area looked, take Zhujiang Delta and Yangtze River delta as central southeast coastal area development quickly to mid-west area, south development quickly to north. At present develops quickest, the mold produces the most centralized province is Guangdong and Zhejiang, places such as Jiangsu, Shanghai, Anhui and Shandong also has a bigger development in recent years.Although our country mold total quantity had at present achieved the suitable scale, the mold level also has the very big enhancement, after but design manufacture horizontal overall rise and fall industry developed country and so on Yu De, America, date, France, Italy many. The current existence question and the disparity mainly display in following several aspects:(1) The total quantity falls short of demandDomestic mold assembling one rate only, about 70%. Low-grade mold, center upscale mold assembling oneself rate only has 50% about.(2) The enterprise organizational structure, the product structure, the technical structure and the import and export structure does not gatherIn our country mold production factory to be most is from the labor mold workshop which produces assembles oneself (branch factory), from produces assembles oneself the proportion to reach as high as about 60%, but the overseas mold ultra 70% is the commodity mold. The specialized mold factory mostly is "large and complete", "small and entire" organization form, but overseas mostly is "small but", "is specially small and fine". Domestic large-scale, precise, complex, the long life mold accounts for the total quantity proportion to be insufficient 30%, but overseas in 50% above 2004 years, ratio of the mold import and export is 3.7:1, the import and export balances the after net import volume to amount to 1.32 billion US dollars, is world mold net import quantity biggest country .(3) The mold product level greatly is lower than the international standardThe production cycle actually is higher than the international water broadproduct level low mainly to display in the mold precision, cavity aspect and so on surface roughness, life and structure.(4) Develops the ability badly, economic efficiency unsatisfactory our country mold enterprise technical personnel proportion lowThe level is lower, also does not take the product development, and frequently is in the passive position in the market. Our country each mold staff average year creation output value approximately, ten thousand US dollars, overseas mold industry developed country mostly 15 to10, 000 US dollars, some reach as high as 25 to10, 000 US dollars, relative is our country quite part of molds enterprises also continues to use the workshop type management with it, truly realizes the enterprise which the modernized enterprise manages fewTo create the above disparity the reason to be very many, the mold long-term has not obtained the value besides the history in as the product which should have, as well as the most state-owned enterprises mechanism cannot adapt the market economy, but also has the following several reasons: .The mold material performance, the quality and the variety question often can affect the mold quality, the life and the cost, the domestically produced molding tool steel and overseas imports the steel products to compare has a bigger disparity. Plastic,plate, equipment energy balance, also direct influence mold level enhancement.RSP ToolingRapid Solidification Process (RSP) Tooling, is a spray forming technology tailored for producing molds and dies [2-4]. The approach combines rapid solidification processing and netshape materials processing in a single step. The general concept involves converting a mold design described by a CAD file to a tooling master using a suitable rapid prototyping (RP) technology such as stereolithography. A pattern transfer is made to a castable ceramic, typically alumina or fused silica. This is followed by spray forming a thick deposit of tool steel (or other alloy) on the pattern to capture the desired shape, surface texture and detail. The resultant metal block is cooled to room temperature and separated from the pattern. Typically, the deposit’s exterior walls are machined square, allowing it to be used as an insert in a holding block such as a MUD frame [5]. The overall turnaround time for tooling is about three days, stating with a master. Molds and dies produced in this way have been used for prototype and production runs in plastic injection molding and die casting.An important benefit of RSP Tooling is that it allows molds and dies to be made early in the design cycle for a component. True prototype parts can be manufactured to assess form, fit, and function using the same process planned for production. If the part is qualified, the tooling can be run in production as conventional tooling would. Use of a digital database and RP technology allows design modifications to be easily made.Experimental ProcedureAn alumina-base ceramic (Cotronics 780 [6]) was slurry cast using a silicone rubber master die, or freeze cast using a stereolithography master. After setting up, ceramic patterns were demolded, fired in a kiln, and cooled to room temperature. H13 tool steel was induction melted under a nitrogen atmosphere, superheated about100︒C, and pressure-fed into a bench-scale converging/diverging spray nozzle, designed and constructed in-house. An inert gas atmosphere within the spray apparatus minimized in-flight oxidation of the atomized droplets as they deposited onto the tool pattern at a rate of about 200 kg/h. Gas-to-metal mass flow ratio was approximately 0.5.For tensile property and hardness evaluation, the spray-formed material was sectioned using a wire EDM and surface ground to remove a 0.05 mm thickheat-affected zone. Samples were heat treated in a furnace that was purged with nitrogen. Each sample was coated with BN and placed in a sealed metal foil packet as a precautionary measure to prevent decarburization.Artificially aged samples were soaked for 1 hour at temperatures ranging from 400 to 700︒C, and air cooled. Conventionally heat treated H13 was austenitized at 1010︒C for 30 min., air quenched, and double tempered (2 hr plus 2 hr) at 538︒C.Microhardness was measured at room temperature using a Shimadzu Type M Vickers Hardness Tester by averaging ten microindentation readings. Microstructure of the etched (3% nital) tool steel was evaluated optically using an Olympus Model PME-3 metallograph and an Amray Model 1830 scanning electron microscope. Phase composition was analyzed via energy-dispersive spectroscopy (EDS). The size distribution of overspray powder was analyzed using a Microtrac Full Range Particle Analyzer after powder samples were sieved at 200 μm to remove coarse flakes. Sample density was evaluated by water displacement using Archimedes’ principle and a Mettler balance (Model AE100).A quasi 1-D computer code developed at INEEL was used to evaluate multiphase flow behavior inside the nozzle and free jet regions. The code's basic numerical technique solves the steadystate gas flow field through an adaptive grid, conservative variables approach and treats the droplet phase in a Lagrangian manner with full aerodynamic and energetic coupling between the droplets and transport gas. The liquid metal injection system is coupled to the throat gas dynamics, and effects of heat transfer and wall friction are included. The code also includes a nonequilibriumsolidification model that permits droplet undercooling and recalescence. The code was used to map out the temperature and velocity profile of the gas and atomized droplets within the nozzle and free jet regions.Results and DiscussionSpray forming is a robust rapid tooling technology that allows tool steel molds and dies to be produced in a straightforward manner. Each was spray formed using a ceramic pattern generated from a RP master.Particle and Gas BehaviorParticle mass frequency and cumulative mass distribution plots for H13 tool steel sprays are given in Figure 1. The mass median diameter was determined to be 56 μm by interpolation of size corresponding to 50% cumulative mass. The area mean diameter and volume mean diameter were calculated to be 53 μm and 139 μm, respectively. Geometric standard deviation, d=(d84/d16)½ , is 1.8, where d84 and d16 are particle diameters corresponding to 84% and 16% cumulative mass in Figure 1.Figure1. Cumulative mass and mass frequency plots of particles in H13 tool stepsprays.Figure2 gives computational results for the multiphase velocity flow field (Figure 2a), and H13 tool steel solid fraction (Figure2b), inside the nozzle and free jetregions. Gas velocity increases until reaching the location of the shock front, at which point it precipitously decreases, eventually decaying exponentially outside the nozzle. Small droplets are easily perturbed by the velocity field, accelerating inside the nozzle and decelerating outside. After reaching their terminal velocity, larger droplets (〜150 μm) are less perturbed by the flow field due to their greater momentum.It is well known that high particle cooling rates in the spray jet (103-106 K/s) and bulk deposit (1-100 K/min) are present during spray forming [7]. Most of the particles in the spray have undergone recalescence, resulting in a solid fraction of about 0.75. Calculated solid fraction profiles of small (〜30 μm) and large (〜150 μm) droplets with distance from the nozzle inlet, are shown in Figure 2b.Spray-Formed DepositsThis high heat extraction rate reduces erosion effects at the surface of the tool pattern. This allows relatively soft, castable ceramic pattern materials to be used that would not be satisfactory candidates for conventional metal casting processes. With suitable processing conditions, fine surface detail can be successfully transferred from the pattern to spray-formed mold. Surface roughness at the molding surface is pattern dependent. Slurry-cast commercial ceramics yield a surface roughness of about 1 μm Ra, suitable for many molding applications. Deposition of tool steel onto glass plates has yielded a specular surface finish of about 0.076 μm Ra. At the current state of development, dimensional repeatability of spray-formed molds, starting with a common master, is about ±0.2%.Figure 2. Calculated particle and gas behavior in nozzle and free jet regions.(a) Velocity profile.(b) Solid fraction.ChemistryThe chemistry of H13 tool steel is designed to allow the material to withstand the temperature, pressure, abrasion, and thermal cycling associated with demanding applications such as die casting. It is the most popular die casting alloy worldwide and second most popular tool steel for plastic injection molding. The steel has low carbon content (0.4 wt.%) to promote toughness, medium chromium content (5 wt.%) to provide good resistance to high temperature softening, 1 wt% Si to improve high temperature oxidation resistance, and small molybdenum and vanadium additions (about 1%) that form stable carbides to increase resistance to erosive wear[8]. Composition analysis was performed on H13 tool steel before and after spray forming.Results, summarized in Table 1, indicate no significant variation in alloy additions.MicrostructureThe size, shape, type, and distribution of carbides found in H13 tool steel is dictated by the processing method and heat treatment. Normally the commercial steel is machined in the mill annealed condition and heat treated(austenitized/quenched/tempered) prior to use. It is typically austenitized at about 1010︒C, quenched in air or oil, and carefully tempered two or three times at 540 to 650︒C to obtain the required combination of hardness, thermal fatigue resistance, and toughness.Commercial, forged, ferritic tool steels cannot be precipitation hardened becauseafter electroslag remelting at the steel mill, ingots are cast that cool slowly and formcoarse carbides. In contrast, rapid solidification of H13 tool steel causes alloying additions to remain largely in solution and to be more uniformly distributed in the matrix [9-11]. Properties can be tailored by artificial aging or conventional heat treatment.A benefit of artificial aging is that it bypasses the specific volume changes that occur during conventional heat treatment that can lead to tool distortion. These specific volume changes occur as the matrix phase transforms from ferrite to austenite to tempered martensite and must be accounted for in the original mold design. However, they cannot always be reliably predicted. Thin sections in the insert, which may be desirable from a design and production standpoint, are oftentimes not included as the material has a tendency to slump during austenitization or distort during quenching. Tool distortion is not observed during artificial aging ofspray-formed tool steels because there is no phase transformation.注塑模具之模具设计与制造模具是制造业的重要工艺基础,在我国,模具制造属于专用设备制造业。
模具的CAD-CAE-CAM技术外文文献翻译、中英文翻译

外文资料与中文翻译外文资料:Mold CAD/CAE/CAM technologyIntroductionMold CAD/CAE/CAM is transforms the traditional mold production method the essential technology, is a high tech, the high benefit systems engineering. It take the computer software form, provides one kind of effective auxiliary means as the enterprise, causes the engineers and technicians with the aid of in the computer to the product performance, the mold structure, the formed craft, the numerical control processing and the production management carries on the design and the optimization. Mold CAD/CAE/The CAM technology can remarkably reduce the mold design and the manufacture cycle, reduces the production cost and improves the product quality to become the mold mutual recognition.Is same with any newly emerging things, mold CAD/CAE/CAM experienced in the nearly 20 years from to has been simply complex, from experiment site to popular process. Since has entered this century, mold CAD/CAE/The CAM technological development speed quicker, the application scope is broader, in order to enable the general molds worker further to deepen to this technical understanding, better display mold CAD/CAE/The CAM function, this article applies in view of the mold in most widespread, most has the representative casting mold, the forging die and the level enters the mold CAD/CAE/The CAM development condition and the tendency make the concise introduction and the analysis.Casting mold CAD/CAE/CAM development surveyThe casting forming process simulation work begins in solves the casting the temperature field distribution. In 1962 Denmark's Fursund has carried on the solidification process heat transfer computation for the first time with the finite difference method to the two-dimensional shape casting, in 1965 US General Motors Henzel and so on has carried on the temperature field simulation to the steam turbine casting success, from this time on casting in mold cavity heat transfer process numerical analysis technology in world scope rapid development. From on century 70's to the 80's, US, England, France, Japan, Denmark and so on one after another has yielded the remarkable result in the casting coagulation simulator study and the application, and promotes one batch of commercialized simulations software one after another. After enters for the 90's, our country's institutions of higher learning, like Qinghua University and the Central China scientific and technical university has alsoobtained the achievement in this domain which focuses attention on.The pure heat transfer process simulation cannot accurately calculate the flaw which the casting in the temperature change and the forecast casting possibly produces, the sufficient mold process to in the casting initial temperature field distribution influence as well as the solidification process liquid metal flowing the influence which forms to the defect casting all is noticeable. The casting sufficient mold process simulation technology begins in the century for 80's, it take calculates the hydromechanics the theory and the method as the foundation, experiences ten years, starts from the two-dimensional simple shape, deepens and the expansion gradually, already succeeded has realized the three dimensional complex shape casting sufficient mold process simulation, and could flow with the heat transfer process coupling. At present overseas had one batch of commercialized the three dimensional casting process simulation softwares, like Japan's SOLIDIA, England's SOLSTAR, France's SIMULOR, Sweden's NOV ACAST, Germany's MAGMA and US'S AFSOLID, PROCAST and so on. The home also has Qinghua University star of, Central China scientific and technical university's the casting China casts CAE and so on. These casting mold CAE softwares have covered the cast steel, the cast iron, the cast-aluminium and the cast copper and so on each kind of casting, as is big as several hundred tons, slightly to several kilograms, regardless of is and shrinks the pine in the elimination shrink hole, in the optimized pouring rising head design, aspect and so on improvement dross entrapped slag has all played the remarkable role.Is following the CAE technology in the casting domain success application, the casting craft and the mold structure CAD research and the application in unceasingly is also thorough, overseas has promoted some application software one after another, like American casting association's AFS-SOFTWARE, may use in the cast steel and casts the iron stock the pouring rising head design, English FOSECO Corporation's FEEDERCALK software, may calculate the steel casting the pouring rising head size and a choice heat preservation rising head set of type. Our country Central China scientific and technical university and Qinghua University has also done many work in the casting craft and the mold structure CAD aspect, like Qinghua University develops the THFSCAD software, mainly and the vector and the casting craft CAD two parts is composed by the graph scanning. The preceding part to scans the input the graph to carry on disappears the blue decontamination and the vector, the latter part uses for to establish the parametrization graph, to calculate the casting theprocessing remainder, the plan craft card and so on. THFSCAD is develops in the two dimensional plot geometry foundation, used the AUTOCAD software for to develop the platform. Along with the CAD technology fast progress, the three dimensional CAD system can substitute for the two-dimensional CAD system in the casting realm of production but to become the mainstream design system gradually.Forging die CAD/CAE/CAM development surveySince on century 70's, domestic and foreign many academic organizations and company to forging die CAD/CAE/The CAM technology has conducted extensive research, in the forging technological process design, the forging die structural design and the metal flowed aspect and so on simulation has obtained the remarkable result.The axial symmetry forging approximately composes about forging total 30%, in addition axial symmetry forging geometry shape simple, is easy to describe and the definition, therefore development forging die CAD/ When CAM system the domestic and foreign majority organizations and the human all are obtain from the axial symmetry forging die. Axial symmetry forging die CAD/ CAM system main constituent including forging design, drop forging technological design, forging die structural design and NC programming. The forging design refers is designs the cold forging chart and the hot forging chart, divides the modular surface, the supplement machining remainder, the increase fillet including the choice and pulls out the mold ascent and so on. The drop forging technological design decided whether uses the preliminary shaping working procedure, how uses the preliminary shaping working procedure as well as how chooses the forging and stamping equipment the tonnage.Another kind of widespread application forging is the major axis class forging, its formed working procedure design and the mold structural design are far more complex than the axial symmetry forging die, therefore development major axis class forging die CAD/The CAM system difficulty bigger, the versatility is also low, at present in many general commercialized CAD/On the CAM software two time develops major axis class forging die CAD/The CAM system only is restricted in the specific product and the specific situation application.Another kind of widespread application forging is the major axis class forging, its formed working procedure design and the mold structural design are far more complex than the axial symmetry forging die, therefore development major axis class forging die CAD/The CAM system difficulty bigger, the versatility is also low, atpresent in many general commercialized CAD/On the CAM software two time develops major axis class forging die CAD/The CAM system only is restricted in the specific product and the specific situation application.In the CAE technology aspect, the finite element method always is the analysis and the research metal forging forming main numerical analysis method, for many years has yielded many gradual result. In 1973 Lee and Kobayashi derived just the plastic finite element Lagrange algorithm by the matrix analytic method, the success has analyzed the forging forming process. In 1974 Zienkiewicz proposed just the visco-plasticity finite element punished the function method, analyzed the rolling, has extruded and draws and so on the formed craft. In 1982 Mori and Osakada proposed just in the plastic finite element material might the compression method and uses in the rolling and the extrusion.On the century at the beginning of 80's, Oh and Altan had just conducted the thorough research with large-scale plastic finite element analysis software ALPID to each kind of plastic deformation question. After 90's, overseas some commercialized specialized finite element analysis softwares, like France's FORGE2, US'S DEFORM, ABAQUS, MSC/AutoForge and so on, all successfully has applied in the forging domain. These softwares not only may forecast the forging forms entire process, moreover may the quota produce with the distortion related each kind of physical quantity, like the displacement, the speed, the stress, the strain and the load and so on, for obtained the most superior mold design, the most reasonable craft plan and the least experimental molds time has provided the technical guarantee.The level enters mold CAD/CAE/CAM development surveyThe overseas level enters mold CAD/CAE/The CAM research begins in the century at the end of for 60's, the 70's then have the preliminary application, but only are restricted in the two-dimensional graph the simple blanking level to enter the mold, its main function like strip material row of type, concave mold arrangement, process design and NC programming and so on. The curving level enters mold CAD/The CAM system appears in the 80's, like Japanese Hitachi Corporation and the Fujitsu Corporation's curving level enters the mold system and so on. In order to can adapt the complex mold design, the Fujitsu system has used the method which the automatic design and designs alternately unifies, launches, the curving snapping back computation and a labor step of arrangement in this system except the semifinished materials for the automatic reduction outside, other need to design personnel'sparticipation.Applies the three dimensional geometry modelling technology the level to enter the mold system to begin in at the end of for the 80's, like American Auto-trol Corporation's Die-Design system, this system uses the three dimensional geometry model to describe the plate work components, and applies the three dimensional graph technology in the mold structural design, demonstrates the three dimensional graph software in mold design vital role.Enters for the 90's, international famous commercialized three dimensional CAD/CAM system, like US'S Pro/E, UG-II, CADD5, Solidworks, MDT and so on one after another obtain the application in the mold. American PTC Corporation based on Pro/The E system has developed plate work components modelling module Pro/Sheet Metal. UG Solution Corporation has developed similar module UG/ in the UG-II foundationSheet Metal. Above two systems all lack face the level enter the formed craft and the mold structural design special-purpose module, but this aspect work progress is very quick, some already won initial success.Like American Computer Design Corporation develops the level enters mold software Striker Systems is sales volume big commercialization CAD/The CAM system, including the plate work components modelling (SS-DESIGN), the semifinished materials launches (SS-UNFOLD), a semifinished materials row of type (SS-STRIP DESIGN), mold design (SS-DIE DESIGN) and numerical control processing (SS-WIRE, SS-PROFILE) and so on module. This system support plate work components characteristic modelling, although had certain automated designs the function, but its design process still by alternately operates primarily, only is suitable at present in the curving blanking level enters the mold the design.At the beginning of this century, American UGS Corporation and our country Central China scientific and technical university cooperation (presently is NX) in the software platform develops in UG-II enters mold CAD/ based on the three dimensional geometry model levelCAM software NX-PDW. This software including the project initialization, the craft pre- definition, the semifinished materials launches, a semifinished materials row of type, the waste material design, strip module and so on material row of type, pressure calculation and mold structural design. Has the trick recognition and the heavy construction, the entire three dimensional structure connection and so on the remarkable characteristic, has taken the commercialized product investment □field in 2003. Our country starts from on century 90's, theCentral China scientific and technical university, Shanghai Jiaotong University, the Xian Jiaotong University and the Beijing mechanical and electrical research institute and so on developed the level to enter mold CAD/ one after anotherCAM system research and development. Like the Central China scientific and technical university mold technology country key laboratory develops in the AutoCAD software platform enters mold CAD/ based on the characteristic levelCAM system HMJC, including the plate work components characteristic modelling, based on the characteristic ramming technological design, the mold structural design, the standard letter and the modular design constructs the storehouse tool and the line cuts automatically programs five modules. Shanghai Jiaotong University fine holds (Finetool) for Swiss Fyan to flush the company to develop the successful precise blanking level to enter mold CAD/CAM system. The Xian Jiaotong University develops the multi- locations curving level to enter the mold CAD system and so on.附录F:外文译文模具的CAD/CAE/CAM技术引言模具CAD/CAE/CAM是改造传统模具生产方式的关键技术,是一项高科技、高效益的系统工程。
模具设计毕业课程设计外文文献翻译
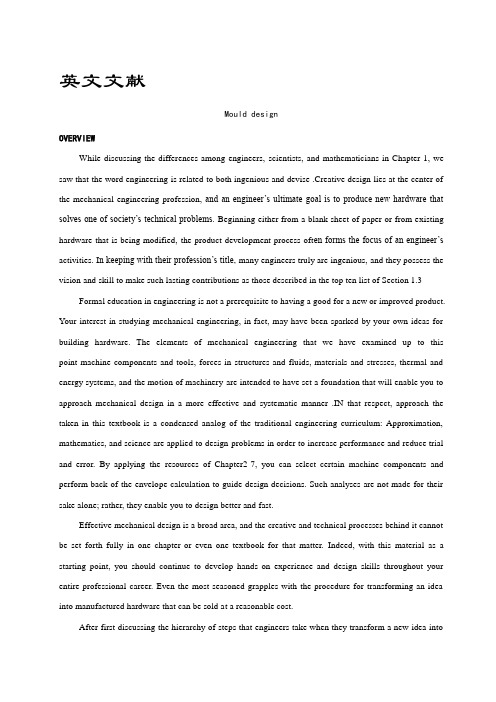
英文文献Mould designOVERVIEWWhile discussing the differences among engineers, scientists, and mathematicians in Chapter 1, we saw that the word engineering is related to both ingenious and devise .Creative design lies at the center of the mechanical engineering profession, and an engineer’s ultimate goal is to produce new hardware that solves one of society’s technical problems. Beginning either from a blank sheet of paper or from existing hardware that is being modified, the product development process oft en forms the focus of an engineer’s activities. I n keeping with their profession’s title, many engineers truly are ingenious, and they possess the vision and skill to make such lasting contributions as those described in the top ten list of Section 1.3 Formal education in engineering is not a prerequisite to having a good for a new or improved product. Your interest in studying mechanical engineering, in fact, may have been sparked by your own ideas for building hardware. The elements of mechanical engineering that we have examined up to this point-machine components and tools, forces in structures and fluids, materials and stresses, thermal and energy systems, and the motion of machinery-are intended to have set a foundation that will enable you to approach mechanical design in a more effective and systematic manner .IN that respect, approach the taken in this textbook is a condensed analog of the traditional engineering curriculum: Approximation, mathematics, and science are applied to design problems in order to increase performance and reduce trial and error. By applying the resources of Chapter2-7, you can select certain machine components and perform back-of-the-envelope calculation to guide design decisions. Such analyses are not made for their sake alone; rather, they enable you to design better and fast.Effective mechanical design is a broad area, and the creative and technical processes behind it cannot be set forth fully in one chapter-or even one textbook for that matter. Indeed, with this material as a starting point, you should continue to develop hands-on experience and design skills throughout your entire professional career. Even the most seasoned grapples with the procedure for transforming an idea into manufactured hardware that can be sold at a reasonable cost.After first discussing the hierarchy of steps that engineers take when they transform a new idea intoreality, we explore the subject of mechanical design through three case studies in the fields of conceptual design, computer-aided design, and detailed machine design. We will also discuss mechanical design from a business perspective and describe how patents protect newly developed technology. After completing this chapter, you should be able to:1)Outline the major steps and iteration in points in the high-level mechanical design procedure.2)Give an example of the processes for brainstorming and for identifying the advantages anddisadvantages of various design options3)Understand the role played by computer-aided engineering tools in mechanical design, anddescribe how such tools can be seamlessly integrated with one another.4)By using a sketch as a guide, describe the operation of an automobile automatic transmission, acomplex machine design that incorporates mechanical, electronic, computer, and hydraulic components.5)Explain what patents are, and discuss their importance to engineering’s business environment HIGH-LEVEL DESIGN PEOCEDUREIn this section, we outline the steps that engineers take when they develop new products and hardware. From the broadest viewpoint, design is defined as the systematic process for devising a mechanical system to meet one of society’s technical needs. The specific motivation could lie in the areas of transportation, communication, or security, for instance. The prospective product is expected to solve a particular problem so well, or offer such a new capability, that other will pay for it. Early on, a company’s marketing department will collaborate with engineers and managers to identify, in a general sense, new opportunities for products. Together, they define the new product’s concept by drawing upon feedback from potential customers and from user of related product. Designers will subsequently develop those concepts, work out the details, and bring the functioning hardware to realization. Many approximations, trade-offs, and choices are made along the way, and mechanical engineers are mindful that the level of precision that is need will naturally and gradually grow as the design matures. For instance, it does not make sense for an engineer to resolve specific details (should a grade 1020 or 1045 steel alloy be used? Are ball or roller bearings most appropriate? What must be the viscosity of the oil?) until the design's overall concept has taken firm shape. After all, at an early stage of the design cycle, the specifications for the product’s size, weight, power, or performance could still change. Design engineers are comfortablewith such ambiguity, and they are able to develop product even in the presence of requirements and constraints that can change.The formal procedure by which a marketing concept evolves into manufactured hardware is based upon many principles and attributes. Most engineers would probably agree that creativity, simplicity, and iteration are key factors in any successful endeavor. Innovation begins with a good idea, but also implies starting from a blank sheet of paper. Nevertheless, engineers must still take the first, perhaps uncertain, step for transforming that formative idea into concrete reality. Early design decisions are made by drawing upon a variety of source: personal experience, knowledge of mathematics and science, laboratory and field testing, and trial and error guided by good judgment. Generally speaking, simpler design concepts are better than complex ones, and the adage “keep it simple, stupid”has a well-deserved reputation among engineers for guiding decisions. Iteration is also important for improving a design and for refining hardware that works into hardware that works well. The first idea that you have, just like the first prototype that you construct, will probably not be the best ones that can be realized. With the gradual improvement of each iteration, however, the design will perform better, more efficiently, and more elegantly.From a macroscopic perspective, the mechanical design procedure can be broken down into four major steps, which are outlined with greater detail in Figure 8.1.1. Define and research objectives.Initially, a designer describes the new product’s requirements in terms of its function, weight, strength, cost, safety, reliability, and so forth. At this first stage, constraints that the design must satisfy are also established. Those constraints might be of a technical nature-say, a restriction on size or power consumption. Alternatively, the constraints could be related to business or marketing concerns, such as the product’s appearance, cost, or ease of use. When faced with a new technical challenge, engineers will conduct research and gather background information that is expected to be useful when concepts and details are later evaluated. Engineers read patents that have been issued for related technologies, consult with vendors of components or subsystems that might be used in the product, attend expositions and trade shows, and meet with potential customers to better understand the application. Early in the design process, engineers define the problem, set the objective, and gather pertinent information for the foundation of a good design.2. Generate concepts.In this stage, designers generally work in teams with the goal of devising a wide range of potential solutions to the problem at hand. This creative effort involves conceiving new ideas and combining previous ones to be greater than the sum of their parts. Hardware solutions are conceptualized and composed, and both good and not-so-good ideas are tossed about. Results from the brainstorming sessions are systematically recorded, the advantages and disadvantages of various solutions are identified, and trade-offs among the differing approaches are made. To document the suite of ideas that emerges from this synthesis stage, engineers sketch concepts, make notes, and prepare lists of “pros and cons”in their design notebooks. No particular idea is evaluated in depth, nor is any idea viewed with too critical an eye. Instead, you should focus on cataloging multiple approaches and devising a wide rang of design concepts, not necessarily all conventional ones. Even though a particular solution might not seem feasible at this early stage, should the product’s requirements or constraints change in the future (which is likely), the idea might in fact resurface as a leading contender.3. Narrow down the options.The design team further evaluates the concepts with a view toward reducing them to a promising few. For instance, engineers make preliminary calculations to compare strength, safety, cost, and reliability, and they will begin to discard the less feasible concepts. Sample hardware could also be produced at this stage. Just as a picture is worth a thousand words, a physical prototype is often useful for engineers to visualize complex machine components and to explain their assembly to others. The prototype can also be tested so that trade-off decisions are made based on the results of both measurements and analyses. One method for producing such components is called rapid prototyping, and its key capability is that complex, three-dimensional can be fabricated directly from is called fused deposition modeling, and it enables durables durable and fully functional prototypes to be fabricated from plastics and polycarbonates. As an example, Figure 8.2 depicts a computer-aided design drawing of an engine block and a physical prototype developed with the system show in Figure 8.34. Develop a detailed design.To reach this point of the high-level procedure, the design team will have brainstormed, tested, analyzed, and converged its way to what it perceives as the best concept. The implementation of the design, construction of a final prototype, and development of the manufacturing process each remain. Detailedtechnical issues are solved by applying mathematical, scientific, laboratory, and computer-aided engineering tools. Completed drawings and parts lists are prepared. The designers conduct engineering analysis and experiments to verify performance over a range of operating conditions. If necessary, changes to shape, dimensions, materials, and components will be made until all requirements and constraints are met. The design is documented through engineering drawings and written reports so that able to understand the reasons behind each of the many decisions that the designers made. Such documentation is also useful for future design teams to teams to learn from and build upon the present team’s experiences.At the most fundamental level, the final design must all of its requirements and constraints. You might thing that an engineer’s tasks are completed once the working prototype has been delivered or after the finishing touches have been applied to the drawings. However, mechanical engineers today work in a broader environment, and their hardware is viewed with a critical eye beyond the criterion of whether or not it functions as intended. For a product be successful, it must also be safe to use, reliable, environmentally sound in its use and disposal, and affordable to manufacture. After all, if the product is technically superb but it requires expensive materials and manufacturing operations, customers may avoid the product and select one that is more balanced in cost and performance. In the end, engineering is a business venture that must meet the needs of its customers.模具设计概况当我们在第1章讨论工程师,科学家和数学家之间不同的时候,我们看到工程学这个涉及到创意和设计两方面内容。
- 1、下载文档前请自行甄别文档内容的完整性,平台不提供额外的编辑、内容补充、找答案等附加服务。
- 2、"仅部分预览"的文档,不可在线预览部分如存在完整性等问题,可反馈申请退款(可完整预览的文档不适用该条件!)。
- 3、如文档侵犯您的权益,请联系客服反馈,我们会尽快为您处理(人工客服工作时间:9:00-18:30)。
资料来源:文章名:The injection molding and machine书刊名:《Professional English for mould》作者:王浩钢曹艳清出版社:人民邮电出版社章节:Chapter 1 - 3页码:P1~P18文章译名:模具专业英语外文原文:Lesson 1 The injection molding and machine 1.The injection moldingInjection molding is principally used for the production of the thermoplastic parts,although some progress has been made in developing a method for injection molding some thermosetting materials. The problem of injecting a melted plastic into a mold cavity from a reservoir of melted material has been extremely difficult to solve for thermosetting plastics which cure and harden under such conditions within a few minutes.The principle of injection molding is quite similar to that of die-casting.The process consists of feeding a plastic compound in powdered or granular form from a hopper through metering and melting stages and then injecting it into a mold?.After a brief cooling period,the mold is opened and the solidified part ejected.Injection-molding machines can be arranged for manual operation,automatic single-cycle operation,and full automatic operation.The advantage of injection molding are: (i) a high molding speed adapted for mass production is possible; (ii) there is a wide choice of thermoplastic materials Providing a variety of useful propertics; (iii)it is possible to mold threads,undercuts,side holes,and large thin sections.2.The injection-molding machineSeveral methods are used to force or inject the melted plastic into the mold. The most commonly used system in the larger machines is the in-line reciprocating screw.The screw acts as a combination injection and plasticizing unit.As the plastic is fed to the rotating screw, it passes through three zones as shown: feed, compression, and metering.After the feedzone,the screw-fight depth is gradually reduced,forcing the plastic to compress.The work is converted to heat by shearing the plastic,making it a semifluid mass.In the metering zone, additional heat is applied by conduction from the barrel surface. As the chamber in front of the screw becomes filled,it forces the screw back,tripping a limit switch that activates a hydraulic cylinder that forces the screw forward and injects the fluid plastic into the closed mold.An antiflowback valve prevents plastic under pressure from escaping back into the screw flights.The clamping force that a machine is capable of exerting is part of the size designation and is measured in tons. A rule-of-thumb can be used to determine the tonnage required for a particular job. It is based on two tons of clamp force per square inch of projected area. If the flow patter is difficult and the parts are thin, this may have to go ta three or four tons. Many reciprocating-screw machines are capable of handing thermosetting plastic materials.Previously these materials were handled by compression or transfer molding.Thermosetting materials cure or polymerize in the mold and are ejected hot in the range of 375 C~ 410 C. Thermoplastic partsmust be allowed to cool in the mold in order to remove them without distortion. Thus thermosetting cycles can be faster.Of course the mold must be heated rather than chilled,as with thermoplastics.Reading materialA competent mould designer must have a thorough knowledge of the principles of mould making as the design of the various parts of the mould depends on the technique adopted for its manufacture.This chapter is included primarily for the beginner who does not have a background knowledge ofthe various machining and other mould making techniques.To cover the topic of mould making thoroughly would require a companion work equal in size to this monograph and therefore this introduction to the subject must,of necessity,be superfcial. However,we hope that very fact that it is included in a monograph on design,will emphasize the importance ofmould making as a subject and will also encourage the beginner to a further and more complete study in this field.The majority of moulds are manufactured by the use of conventional machine tools found in most modem toolrooms. From the manufacturing viewpoint we classify the mould into two parts (i)the cavity and core, and (ii)the remainder of the mould. The lattet part is commonly referred to as bolster work.The work on the cavity and core is by far the most important as it is from these members that the plastics moulding takes its form.The work on the cavity and core can further be classified depending upon whether the form is of a simple or a complex nature.For example,the cavity and core for a circular or rectangular box-type moulding is far simpler to make than a cavity and core to produce a telephone handset moulding.The mould parts for the simple form are produced on such machine tools as the lathe andthe milling machine,whereas the more complex form requires the use of some kind of copying machine.The bolster work is not as critical as the manufacture of the cavity and core forms but nevertheless,accuracy in the manufacture of the various parts necessary to ensure that the mold can be assembled by the fitter without an undue amount of bench-work,Now,while the bolster work is always produced on conventional machine tool,the cavity and core,particularly the former,can be produced by one of a number of other techniques.These include investment casting,electro-deposition,cold hobbing,pressure casting and spark machining.1.Machine toolsThe purpose of any machine tool is to remove metal.Each machine tool removes metal in a different way.For example,in one type (the lathe) metal is removed by a single point tool as the work is rotated,whereas in another type(the milling machine)a cutter is rotated and metal is removed as the work is progressed beneath it.Which machine tool is to be used for a particular job depends to a large extent upon the type of machining required.There is,however,a certain amount of overlapping and some machine tools can be utilized for several different operations.The machine tools which will be found in the modern toolroom are as follows: (i)Lathes for turning, boring and screwcutting, etc.(ii)Cylindrical grinding machines for the production of precision cylindrical surfaces.(iii) Shaping and planing machines for the reduction of steel blocks and plates to the required thickness and for"squaring up"these plates(iv)Surface grinding machines for the production of precision flat surfaces.(v) Milling machines for the rapid removal of metal, for machining slots,recesses,boring holes machining splines,etc.(vi) Tracer-controlled milling machines for accurate reproduction of complex cavity and core forms.In addition to the above list of major machine tools there is,of course,ancillary equipment without which no toolroom would be complete. This includes power saws, drilling machines, toolpost grinders,hardening and polishing facilities,etc.2.CastingsThe manufacture of cavities and cores in steel by the conventional casting method using sand moulds is not satisfactory owing to the poor finish obtained and to the porosity which occurs on,or just below the surface of the casting.The expenditure involved in plugging,machining and finishing these conventional castings makes this method of mould making uneconomic.The Shaw investment casting process docs not,however,share the disadvantages associated with sand casting and is therefore applicable to the manufacture of cavities and cores.The process is carried out by specialists and the mould maker supplies the company with a pattern of the required mould part.As the final casting will be an accurate reproduction of the pattern supplied,this must be manufactured to close tolerances and have a good surface finish.To allow for the contraction of the steel on cooling the pattern is made approximately 0.020 mm/mm(in/ in) oversize.3.Electro-depositionElectro-deposition is an electrochemical process used to reproduce accurately a cavity or core form from a given pattern.The pattern can be made in an easily worked material and is the reverse form to that required. That is, a male pattern is required for a cavity and a female pattern for a core. Normally it is much easier to machine a male pattern than the reverse cavity form and it is for this reason that most applications for this technique are for intricate cavity work.4.Cold hobbingCold hobbing is a process in which a hardened steel master hob is forced into a soft steel blank under condiderable pressure.Hobbing is used for the production of cavities which by virtue of their shape would be difficult to die-sink on conventional machine tools.5.Pressure castingBeryllium-copper is a material which is increasingly being used in mould construction because it possesses several desirable characteristics.In particular it has a high thermal conductivity combined with a reasonable hardness (Brinell Hardness Number of about 250),which makes it suitable for certain types of cavity and core,and for other mould parts,such as hot runner unit secondary nozzles.Its high thermal conductivity means that when beryllium-copper is used fora cavity or a core,the heat from the melt will be transferred away from the impression faster than if a corresponding steel cavity and core are used,and this often results in a shorter moulding cycle.Berylium-copper can be machined, in which case the conventional machine tools are used, and it can be cold-hobbed,hot-hobbed or pressure-cast,The last technique offers certain advantages over the hobbing methods,in that cold or hot hobbing of beryllium-copper tends to work harden the material which results in the development of stress concentrations.Pressure casting (or liquid hobbing) is used mainly for the production of cavities but if can be used,where applicable,for the production of the cores as well,As the terms suggest,it is basically a process which combines the casting and hobbing techniques.6.Spark machiningThis is one of more recent additions to mould making methods and strictly speaking it should come under the machine tool section.However,as the principle of operation is different from that of all other basic machine tools it is preferable to discuss this technique separately.Spark machining is a process in which steel or other metals can be machined by the application of an electrical discharge spark.The spark is localized and metal is progressively removed in small quantities over a period of time.7.Bench fittingIrrespective of the machine tool or technique used to manufacture the various parts of the mould,the final responsibility for the finishing of the individual parts and for fitting them together lies with the bench fitter.The mould parts finishing and assembly procedure adopted by the bench fitter varies quite often from toolroom to individual toolmakers working in the same work; it is therefore impossible to set down a standard pattern for the work.In consequence,we intend only to indicate the general approach to this problem without going into details.We will do this by considering the various stages in the bench fitting involved in the manufacture of a simple mould.Lesson 2 EjectionA molding is formed in mould by injeting a plastic melt,under pressure,into an impression via a feed system.It must therefore be removed manually.Furthermore,all thermoplastic materials contract as they solidify,which means that the molding will shrink on to the core which forms it.This shrinkage makes the molding dificult to remove.Facilities are provided on the injection machine for automatic actuation of an ejector system,and this is situated behind the moving platen.Because of this,the mould's ejector system will be most effectively operated if placed in the moving half of the mould,i.e.the half attached to the moving platen. We have stated previously that we need to eject the molding from the core and it therefore follows that the core ,too, will most satisfactorily be located in the moving half.The ejector system in a mould will be discussed under three headings, namely: (i) the ejector grid; (ii) the ejector plate assembly; and (iii)the method of ejection.Ejector gridThe ejector grid is that part of the mould which supports the mould plate and provides a space into which the ejector plate assembly can be fitted and operated.The grid normally consists of a back plate on to which is mounteda number of conveniently shaped"support blocks".1.Ejector plate assemblyThe ejector plate assembly is that part of the mould to which the ejector element is attached. The assembly is contained in a pocket, formed by the ejector grid, directly behind the mould plate.The assembly consists of an ejector plate,a retaining plate and an ejector rod.One end of this lattermember is threaded and it is screwed into the ejector plat.In this particular design the ejector rod functions not only as an actuating member but also as a method of guiding the assembly.Note that the parallel portion of the ejector rod passes through an ejector rod bush fitted in the back plate of the mould.2.Ejection techniquesWhen a molding cools,it contracts by an amount depending on the material being processed.For a molding which has no internal form,for example,a solid rectangular block,the molding will shrink away from the cavity walls,thereby permitting a simple ejection technique to be adopted. However,when the molding has internal form,the molding,as it cools,will shrink onto the core and some positive type of ejection is necessary.The designer has several ejection techniques from which to choose,but in general,the choice will be restricted depending upon the shape of the molding.The basic ejection techniques are as follows:(i)pin ejection; (ii) sleeve ejection; (iii) stripper plate ejection and (iv) air ejection.Reading materialIn drop forging, a piece of metal, roughly or approximately of the desired shape, is placed between die faces having the exact form of the finished piece and forced to take this form by drawing he dies together.This method is widely used for the manufacture of parts both of steel and rge drop hammers, since the work done by a press, goes deeper. Further, the press can take a cooler ingot to closer dimensions.The forging should be done at about the same temperature as rolling; the process improves the physical properties of the steel just as rolling does. In the final forging it is important not to have the steel too hot,for an overheated steel will have poor mechanical properties when cooled.In heating for forging the temperature is usually judged by the eye, but where large numbers of the same pattern are made. The piece to be forged are heated in furnaces in which the temperature is indicated by pyrometers,and often is automatically controlled.Metal in the form of hot-rolled or cold-rolled sheets or strips may be formed into many shapes by forcing the sheet into the impressions in metal dies.This process is known as stamping or pressing of metals,and involves many different operations,such as bending,drawing,punching,etc.These operations are successfully carried out through the proper die design and proper operation of the press in which the dies are placed.Sheets or strips of steel,brass,copper,aluminum,or other metal are placed between dies and a slow action of the power press makes the dies together forcing the metal to assume the required shape.Rolling is the process of shaping meta in a machine called rolling mill Ingots of metal are rolled by forcing them between two rollers rotating in opposite directions,thus pressing the metal into the required shape. If the rollers gave no grooves on their surfaces, the metal is rolled into the form of a sheet or plate.If the rollers have grooves of a certain shape. the metalwill take the form of these grooves,thus it may be shaped into the form of bars or rods.There are two kinds of rolling: hot rolling and cold rolling. Before cold rolling, the scale covering the surface of the hot-rolled object should be removed. Cold rolling produces a higher surface finishing sheet and gives it a very exact size. The process has innumerable advantages. Many shapes may be manufactured in quantities at a rapid rate and at a relatively low cost.Lesson 3 Mould coolongOne fundamental principle of injection molding is that hot material enters the mould,where it cools rapidly to a temperature at which it solidifies sufficiently to retain the shape of the impression.The temperature of the mould is therefore important as it governs a portion of the overall molding cycle.While the melt flows more freely in a hot mould,a greater cooling period is required before the solidified molding can be ejected. Alternatively, while the melt solidifies quickly in a cold mould,it may not reach the extremities of the impression.A compromise between the two extremes must therefore be accepted to obtain the optimum molding cycle.The operating temperature for a particular mould will depend on a number of factors which include the following: type and grade of material to be molded; length of flow within the impression; wall section of the molding; length of the feed system,etc,It is often found advantagcous to use a slightly higher temperature than is required just to fill the impression,as this tends to improve the surface finish of the molding by minimizing weld lines,flow marks and other blemishes.To maintain the required temperature differential between the mould and plastic material water(or other fluid) is circulated through holes or channels within the mould These holes or channels are termed flow-ways or water-ways and the complete system of flow ways is tamed the circuit.During the impression filling stage the hottest material will be in the vicinity of the entry point,i.e.the gate,the coolest material will be at the point farthest from the entry.The temperature of the coolant fluid,however,increases as it passes through the mould.Therefore,To achieve an even cooling rate over the molding surface,it is necessary to locate the incoming coolant fluid adjacent to “hot”molding surfaces and to locate the channels containing"heated"coolant fluid adjacent to“cool" molding surfaces".However,as will be seen from the following discussion,it is not always practicable to adopt the idealized approach and the designer must use a fair amount of common sense when laying out coolant circuits if unnecessarily expensive moulds are to be avoided.Units for the circulation of water (or other fluids) are commercially available.These units are simply connected to the mould via flexible hoses,with these units the mould's temperature can be maintained within close limits.Close temperature control is not possible using the alternative system in which the mould is connected to a cold water supply.It is the mould designer's responsibility to provide an adequate circulating system within the mould.In general,the simplest systems are those in which holes are bored longitudinally through the mould plates. However,this is not necessarily the most efficient method for a particular mould.When using drillings for the circulation of the coolant, however, these mus not be positioned too close to the impression (closer than 16 mm) as this is likely to cause a marked temperature variation across the impression,with resultant molding problems.The layout of a circuit is often complicated by the fact that flow ways must not be drilled too close to any other hole in the same mould plate. It will be recalled that the mould plate has a large number ofholes or recesses, to accommodate ejector pins, guide pillars, guide bushes, sprue bush, inserts, etc. How close it is safe to position in a flow way adjacent to another hole depends to a large extent on the depth oftheflowwaydillingrqireWhdrilidowtisatefrdriwander off its prescribed course. A rule which is often applied is that for drillings up to 150 mm deep the flow way should not be closer than 3 mm to any other hole. For deeper flow ways this allowance is increased to 5 mm.To obtain the best possible position for a circuit it is good practice to lay the circuit at the earliest opportunity in the design.The other mould items such as ejector pins,guide bushes,etc,can then be positioned according.模具专业英语译文:第1课注塑模和注塑机1.注塑模尽管成型某些热固性材料的方法取得了一定进步,但注塑模主要(还是)用来生产热塑性塑件。