预分解窑熟料欠烧成因及处理
第三节预分解窑操作常见问题及处理办法

伴随现象
处理办法
1.分解炉温度偏低,参照三
2.炉内料粉悬浮不好、分解慢
3.旋风或喷腾效应差,料粉在炉内停留时间短
4.生料粒度变粗,原料质量变差
出炉气温降低,参照三
炉内温度不低,但分解率低
生料细度粗
参照三
检查调节撒料装置及翻板阀
调节风量、风速及风向
调节生料细度,适当提高分解炉温度
预分解窑几种疑难故障及处理方法
六、C5筒有大量火花(说明大量煤粉进入筒内)
可能原因
伴随现象
处理办法
1.炉内加煤过多,炉内来不及燃烧
2.窑内加煤太多或跑煤,造成机械不完全燃烧
3.分解炉煤粉悬浮不好,燃烧慢
4.炉内旋风或喷腾效应差,燃烧时间短
5.煤质变粗,挥发分减少
6.三次风温降低或漏风严重
7.三次风管积灰或三次风阀开度过小,三次风过小
2.窑内结圈或料层增厚
3.窑内物料结大球
4.冷却机阻力增大,窑头负压增高
5.仪表失灵
火焰过长,尾温升高
火焰受逼,尾温降低
负压不稳,火焰晃动
窑头负压表升高
减小总排风或开大三次风阀门
处理结圈或快窑
根据情况将之打碎、钩出或让它滚出
调节篦冷机料层厚度及放风闸门
整修仪表
八、窑尾负压过低
可能原因
伴随现象
处理办法
4.稳定窑内热工制度,防止窑温忽高忽低
第三节预分解窑操作常见问题及处理办法
一、分解炉或C5出口气温过高(表1)
可能原因
伴随现象
处理办法
1.窑、炉喂煤过多或煤仓跑煤
2.喂料量过少或断料
3.上级预热器堵塞
4.煤质变差,燃烧速度慢
预分解窑的问题分析及研究
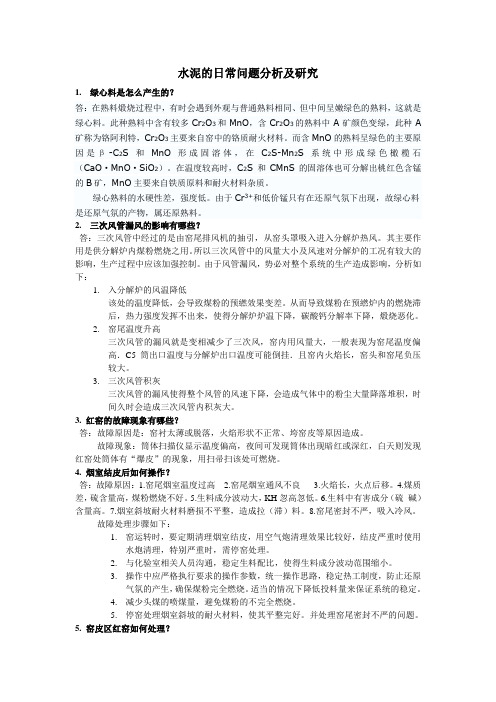
水泥的日常问题分析及研究1.绿心料是怎么产生的?答:在熟料煅烧过程中,有时会遇到外观与普通熟料相同、但中间呈嫩绿色的熟料,这就是绿心料。
此种熟料中含有较多Cr2O3和MnO,含Cr2O3的熟料中A矿颜色变绿,此种A 矿称为铬阿利特,Cr2O3主要来自窑中的铬质耐火材料。
而含MnO的熟料呈绿色的主要原因是β-C2S和MnO 形成固溶体,在C2S-Mn2S 系统中形成绿色橄榄石(CaO·MnO·SiO2)。
在温度较高时,C2S 和CMnS的固溶体也可分解出桃红色含锰的B矿,MnO主要来自铁质原料和耐火材料杂质。
绿心熟料的水硬性差,强度低。
由于Cr3+和低价锰只有在还原气氛下出现,故绿心料是还原气氛的产物,属还原熟料。
2.三次风管漏风的影响有哪些?答:三次风管中经过的是由窑尾排风机的抽引,从窑头罩吸入进入分解炉热风。
其主要作用是供分解炉内煤粉燃烧之用。
所以三次风管中的风量大小及风速对分解炉的工况有较大的影响,生产过程中应该加强控制。
由于风管漏风,势必对整个系统的生产造成影响,分析如下:1.入分解炉的风温降低该处的温度降低,会导致煤粉的预繎效果变差。
从而导致煤粉在预繎炉内的燃烧滞后,热力强度发挥不出来,使得分解炉炉温下降,碳酸钙分解率下降,煅烧恶化。
2.窑尾温度升高三次风管的漏风就是变相减少了三次风,窑内用风量大,一般表现为窑尾温度偏高.C5筒出口温度与分解炉出口温度可能倒挂.且窑内火焰长,窑头和窑尾负压较大。
3.三次风管积灰三次风管的漏风使得整个风管的风速下降,会造成气体中的粉尘大量降落堆积,时间久时会造成三次风管内积灰大。
3. 红窑的故障现象有哪些?答:故障原因是:窑衬太薄或脱落,火焰形状不正常、垮窑皮等原因造成。
故障现象:筒体扫描仪显示温度偏高,夜间可发现筒体出现暗红或深红,白天则发现红窑处筒体有“爆皮”的现象,用扫帚扫该处可燃烧。
4. 烟室结皮后如何操作?答:故障原因:1.窑尾烟室温度过高 2.窑尾烟室通风不良 3.火焰长,火点后移。
预分解窑红窑原因及处理
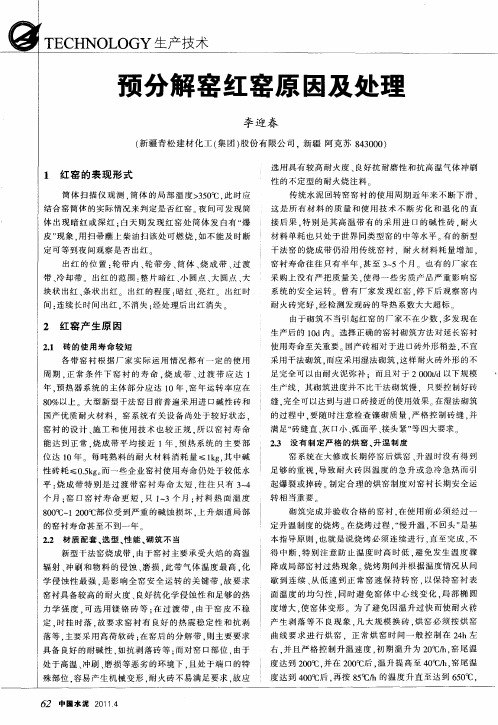
平 : 成带 特别是 过渡带窑 衬寿命 太短 , 往 只有 34 烧 往 ~ 个 月 : 口窑 衬 寿 命 更 短 . 1 3个 月 : 料 热 面 温 度 窑 只 ~ 衬 8 0C 1 0  ̄部 位 受 到 严 重 的 碱蚀 损 坏 . 升 烟道 局 部 0  ̄~ 0 2 C 上
的 窑衬 寿 命 甚 至 不 到一 年 22 材 质 配套 、 型 、 能 、 筑 不 当 . 选 性 砌 新 型 干 法 窑烧 成 带 . 由于 窑衬 主 要 承受 火 焰 的 高温
干 法 窑 的 烧 成 带仍 沿 用 传 统 窑衬 .耐 火 材 料 耗 量 增 加 . 窑 衬 寿命 往 往 只有 半 年 . 至 3 5个 月 也 有 的 厂 家在 甚 ~
采 购 上 没有 严 把 质 量 关 . 得 一 些 劣 质 产 品 严 重 影 响 窑 使 系 统 的 安全 运 转 曾有 厂 家 发 现 红 窑 . 下 后 观 察 窑 内 停 耐 火砖 完好 . 检 测 发 现砖 的导 热 系 数 大 大超 标 经 由 于砌 筑 不 当 引起 红 窑 的厂 家 不 在 少 数 . 发 现在 多
2 红 窑 产 生原 因
21 砖 的 使 用 寿命 较 短 . 各 带 窑 衬 根 据 厂 家 实 际 运 用 情 况 都 有 一 定 的使 用 周期 , 常条件 下窑 衬 的寿命 , 成带 、 渡 带应 达 1 正 烧 过 年 . 热 器 系统 的 主体 部 分 应 达 l 预 0年 . 年 运 转 率 应 在 窑 8 %以上 大 型新 型 干法 窑 目前 普遍 采 用 进 口碱 性 砖 和 0
1 红 窑 的表 现 形 式
简 体 扫 描 仪 观 测 . 体 的局 部 温 度 > 5 o 此 时 应 筒 3 0C. 结 合 窑 筒 体 的 实 际情 况 来 判 定 是否 红 窑 夜 间 可发 现 筒
预分解窑塌料原因分析及处理措施
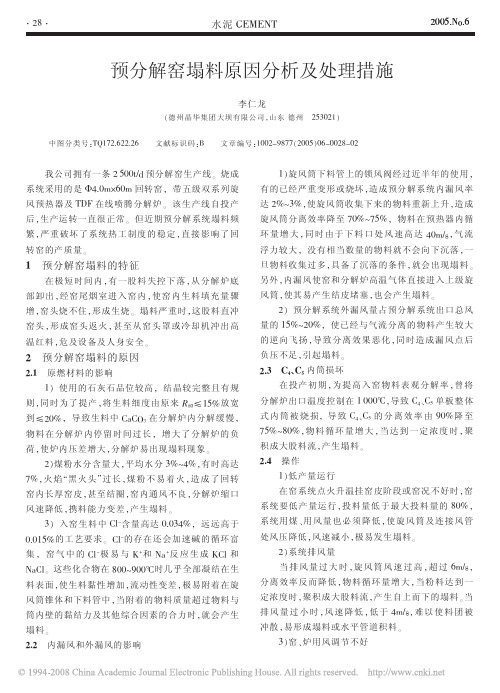
筒 % 延长其使用寿命 % 并可快捷地维修 $ 更换 % 消除系 统内物料循环量过大造成的塌料 #
"
"!"
防止预分解窑塌料的措施
加强原燃材料的质量控制
"!&
优化预分解窑的工艺操作 "稳定其工艺参数
#& 尽快跳过塌料危险区 # 当初次点火投料挂窑皮
时 % 初始投料量定为 4""*(, % 当加至 4!"*(, 时 % 稳定窑 操作 % 用 6"4’, 挂好窑皮 % 然后迅速加至最大喂料量
积成大股料流 "产生塌料 !
%$ 煤粉水分含量大 " 平均水分 85&/5 " 有时高达 95 " 火焰 % 黑火头 & 过长 " 煤粉不 易着火 " 造 成了回转
窑内长厚窑皮 " 甚至结圈 "窑内通风不良 " 分解炉缩口 风速降低 "携料能力变差 "产生塌料 ’
#!&
操作
/$ 低产量运行
在窑系统点火升温挂窑皮阶段或窑况不好时 " 窑 系统要低产量运行 " 投料量低于最大投料量的 3"5 " 系统用煤 ( 用风量也必须降低 " 使旋风筒及连接风管 处风压降低 " 风速减小 "极易发生塌料 !
/$ 旋风筒下料管上的锁风阀经过近半年的使用 "
有的已经严重变形或烧坏 "造成预分解系统内漏风率 达 !0185"使旋风筒收集下来的物料重新上升 " 造成 旋风筒分离效率降至 9"0&9#5 " 物料在预热器内循 环 量 增 大 " 同 时 由 于 下 料 口 处 风 速 高 达 /"0-= " 气 流 浮力较大 " 没有相当数量的物料就不会向下沉落 " 一 旦物料收集过多 "具备了沉落的条件 " 就会出现塌料 ! 另外 "内漏风使窑和分解炉高温气体直接进入上级旋 风筒 "使其易产生结皮堵塞 " 也会产生塌料 !
分解窑操作中常见的几个问题和产生问题的原因

分解窑操作中常见的几个问题和产生问题的原因,燃烧机(燃烧器)一、窑尾和预分解系统温度偏高1)核查是否生料kh、n值偏高,熔融相(ai203和fe203)含量偏低生料中是否si02比较高和生料细度偏粗。
如若干项情况属实,则由于生料易烧性差,熟料难烧结,上述温度偏高属正常现象。
但应注意极限温度和窑尾o:含量的控制。
2)窑内通风不好,窑尾空气过剩系数控制偏低,系统漏风产生二次燃烧。
3)排灰阀配重太轻或因为怕堵塞,窑尾岗位工把排灰阀阀杆吊起来,致使旋风筒收尘效率降低,物料循环量增加,预分解系统温度升高。
4)供料不足或来料不均匀。
5)旋风筒堵塞使系统温度升高。
6)燃烧器外流风太大、火焰太长,致使窑尾温度偏高。
7)烧成带温度太低,煤粉后燃。
8)窑尾负压太高,窑内抽力太大,高温带后移。
二、窑尾和预分解系统温度偏低1)对于一定的喂料量来说,用煤量偏少。
2)排灰阀工作不灵活,局部堆料或塌料。
由于物料分散不好,热交换差,致使预热器c,出口温度升高,但窑尾温度下降。
3)预热器系统漏风,增加了废气量和烧成热耗,废气温度下降。
三、烧成带温度太低1)风、煤、料配合不好。
对于一定喂料量,热耗控制偏低或火焰太长,高温带不集中。
2)在一定的燃烧条件下,窑速太快。
3)预热器系统的塌料以及温度低、分解率低的生料窜人窑前。
4)窑尾来料多或垮窑皮时,用煤量没有及时增加。
5)在窑内通风不良的情况下,又增加窑头用煤量,结果窑尾温度升高,烧成带温度反而下降。
6)冷却机一室篦板上的熟料料层太薄,二次风温度太低。
四、烧成带温度太高1)来料少而用煤量没有及时减少。
2)燃烧器内流风太大,致使火焰太短,高温带太集中。
3)二次风温度太高,黑火头短,火点位置前移。
五、二次风温度太高1)火焰太散,粗粒煤粉掺人熟料,人冷却机后继续燃烧。
2)熟料结粒太细致使料层阻力增加,二次风量减少,风温升高大量细粒熟料随二次风一起返回窑内。
3)熟料结粒良好,但冷却机一室料层太厚。
窑预分解系统的问题分析及改进措施

窑预分解系统的问题分析及改进措施摘要:我厂1号RSP窑经过6年多的运转,系统耐火材料呈现出不同程度的磨损、烧坏现象。
SB室下部掉砖,进而壳体烧损;SC室用风不良,导致边壁物料保护层不均衡,局部衬砖磨损严重;斜烟道及鹅颈管侧墙衬砖垮落,由于鹅颈管结构缺陷,经常结皮和堆料;MC室断面物料分布不均,物料稀相区炉壁烧损,直至筒体严重变形;因窑尾缩口处风速低,喷腾能力减弱而塌料;高温级旋风筒分离效率低,导致物料大量返回,内循环增加等。
本文依据热工标定结果,对该预分解系统出现的问题进行分析,并提出改进措施。
1 RSP窑系统工况分析热工标定主要参数对比见表1、表2,窑尾高温区工艺流程见图1。
表1 预热预分解系统温度变化℃表2 RSP炉的分解进程变化注:1997年数据为南京化工大学硅酸地方国营工程研究所的热工标定结果,SC 室出口指斜烟道出进口等同于鹅颈管出口。
图1 窑尾高温区工艺流程1.1 三次风温度及其对SC室工况的影响由表1可见,三次风温度和入炉生料温度分别只有600℃和671℃。
入炉生料温度低主要是由于C4锥体及下料管增开人孔门较多,外漏风量和散热损失增加引起的,通过加强管理,隔热堵漏后完全可以解决;三次风温度目前基本稳定在560~580℃,提高的余地很小。
其原因是:我厂采用单筒冷却机,经过多年的运转,内部装置所遭受的磨损和腐蚀不断加剧,而且增加了砌筑耐火砖的长度,熟料停留时间短(约为30min),出机熟料温度高(~290℃),使热效率本身就不高的单筒冷却机热回收率进一步降低(1997年热工标定结果为56.6%)。
三次风温度是影响分解率和燃尽率的重要因素。
较低的三次风温度导致炉内煤粉着火速度减慢,形成滞后燃烧,特别是SC室内煤粉是在纯助燃空气中燃烧,助燃空气的温度在很大程度上决定了煤粉燃尽率,三次风温度低,即使分解炉多加煤,SC室内温度也不会高,反而会加剧煤粉滞后燃烧。
从表1和表2可以看出,SC室生料出口温度和分解率分别是948℃和43.4%,结合入炉生料表观分解率已达22.6%的实际情况,说明SC室内的分解反应极低,煤粉燃烧状况不理想。
预分解窑窑皮几种异常情况的处理
预分解窑窑皮几种异常情况的处理江超,李思营,马海倩(新乡平原同力水泥有限责任公司河南新乡453011)0引言河南某水泥公司5000t/d水泥熟料生产线由天津水泥工业设计研究院有限公司设计,采用双系列五级预热器和TSD型分解炉,窑的规格为Φ×72m,配用天津仕名公司TC型四通道燃烧器。
该生产线所用燃料采用低挥发分无烟煤与烟煤按比例搭配而成的混合煤,其燃烧特性既有烟煤的也有无烟煤的,容易产生两极分化。
生产过程中因此出现了几次事故,如窑皮不平整、红窑、窑内结球、窑尾结圈漏料、熟料质量差等。
在处理事故的过程中,总结了一些宝贵的经验。
现做一简介,供同行参考。
1影响窑皮形成的主要因素生料的化学成份生料中铝质与铁质的成份比较多,熟料烧成液相量就多,容易形成窑皮。
铝含量高,液相的粘度大,形成窑皮比较困难。
铁含量高,液相的粘度就比较小,窑皮容易形成,但形成的窑皮也容易掉落。
烧成带的温度烧成带的温度低,物料形成的液相少,不易形成窑皮;相反,窑皮容易脱落。
火焰的形状和燃烧器的位置火焰形状要完整、顺畅,这样形成的窑皮厚薄一致、坚固。
燃烧器的位置应尽量向往外拉一点,同时偏料,火焰宜短不宜长。
这样高温区较集中,高温点靠前,使窑皮由窑前逐渐往窑内推进。
待窑产量增加到正常情况,燃烧器也随之移动到正常生产的位置。
喂料量和窑速挂窑皮期间,喂料量过大或窑速过快,窑内温度就不容易控制,粘挂的窑皮就不平整、不坚固。
2 几次异常窑皮的处理过程窑9.5m~14m处窑皮偏厚表现2005年8月10日中班,窑筒体9.5m~14m窑皮偏厚,筒体扫描显示此处温度平均值仅为165℃,窑尾密封圈漏料,熟料结粒偏大、黄心料较多、f-CaO偏高。
原因分析由于入窑生料的易烧性变差,f-CaO合格率低,有的操作员由于经验不足又不愿减产,为了使f-CaO合格,采取加大窑头用煤量(超出正常值h)、窑尾温度偏高控制的方法,导致此处窑皮偏厚、过渡带副窑皮比正常值厚,窑内物料填充率过高(窑速已经达到最快),影响了通风和热交换,物料预烧不好,结果熟料中黄心料更多、f-CaO仍然偏高、此处窑皮更厚、窑尾密封圈漏料更为严重。
预分解窑熟料煅烧质量的表征和欠烧的判断
预分解窑熟料煅烧质量的表征和欠烧的判断预分解窑熟料煅烧质量的表征和欠烧的判断预分解窑熟料煅烧质量的表征预分解窑熟料煅烧的好坏,包括但不仅仅是欠烧的问题,应该包括如下诸方面:1 原料化学反应的完全程度原料的各种氧化物应该尽量完全地反应,生成熟料矿物。
反应的完全程度可以用游离氧化钙、烧失量、不溶物、立升重综合反应,分述如下:1.1 游离氧化钙在熟料煅烧产过程中,CaO应该与其它氧化物全部反应,生产硅酸盐矿物,但实际上,反应不可能达到所有的反应物几乎全部消失的程度,总会有一小部分CaO不能完全反应。
在熟料冷却过程中,如果冷却速度不能达到一定数值,C3S可能分解为C2S和CaO。
这些氧化钙以游离状态存在,称为游离氧化钙。
煅烧正常的熟料中f-CaO含量在0.5%-1.5%左右。
游离氧化钙的含量与熟料的KH有密切关系,KH 高,f-CaO也会稍高。
1.2 烧失量熟料烧失量是熟料在950℃-1000℃下灼烧足够时间失去的质量。
熟料在高温下灼烧会发生一些化学反应。
化学反应包括:碳酸盐、硫酸盐的分解;有机物的燃烧(如熟料中含有的少量未燃尽炭);碱金属化合物的挥发;低价氧化物被氧化。
除低价氧化物被氧化的反应导致质量增加外,其它的过程都会导致质量减少。
烧失量是高温下水泥各种物力和化学过程质量增加和减少的代数和。
煅烧正常的熟料中烧失量在0.2%-0.4%。
1.3 不溶物熟料不溶物是熟料在一定浓度和温度的酸和碱溶液中不能溶解的部分。
熟料的不溶物是熟料煅烧质量的一项表征指标,熟料中在酸和碱溶液中不能溶解的部分主要是一些结晶较完美的SiO2,是化学惰性的,没有胶凝性。
熟料的不溶物含量与生料中的不溶物含量、生料中硅质原料的粉磨细度、熟料煅烧温度和时间有关。
如果用来表征熟料的煅烧程度,应该看熟料不溶物与生料不溶物的差值,而不是单纯看熟料不溶物的数值。
煅烧正常的熟料不溶物与生料基本接近,大约0.2%-0.4%。
1.4 立升重立升重与熟料颗粒的致密程度、各种矿物的比例、密度有关,颗粒的致密程度大概反应出熟料的煅烧化学反应程度,越致密则表明化学反应越完全。
欠烧料成因及处理
中国水泥2005.11我公司 4.3m ×64m 带五级双系列旋风预热器和N —MFC 分解炉的回转窑,设计转速为0.40~3.96r/min ,设计产量3000t/d ,配用丹麦史密斯公司四通道DBC 型多福乐燃烧器。
在试生产期间,当回转窑达到设计产量时,系统温度偏高控制时熟料还欠烧,迫不得已降低喂料量。
当fCaO 合格时,再增加喂料量至设计产量,又出现欠烧料。
周而复始,严重影响着回转窑的产质量,始终不能使系统进入良性循环状态。
鉴于此,公司各部门全力合作查找原因,并采取相应的措施,取得了良好的效果。
1欠烧料成因1.1窑头用煤量太大,温度偏低在生产过程中,当fCaO 不合格时,总是认为窑头用煤量过少,温度低,煤灰掺入量少。
于是便增加窑头用煤量,试图以此来提高烧成带温度,有时甚至出现窑头用煤量与分解炉用煤量倒置的现象,造成系统温度偏高,窑尾温度达到1200℃,C 5级筒出口温度≥500℃,窑尾废气中CO 含量高,直接威胁预热器的安全运行。
对于回转窑来说,它的容积热力强度是有一定限度的。
当容积热力强度已到极限时,增加窑头用煤量,会造成煤粉不完全燃烧,窑内还原气氛加剧,窑头温度进一步降低。
当窑温较低时,再多加煤反而更解决不了问题,因燃烧速度与温度有关,多加煤会造成火焰黑火头长,火焰温度低,窑尾温度过高。
还会引起窑内还原气氛加重,结长厚窑皮,造成预热器系统结皮堵塞,从而使工艺系统进一步恶化,热工制度紊乱。
1.2燃烧器火力不集中我公司燃烧器的中心位于回转窑端面第四象限(+30mm ,-30mm),伸入窑内300mm (见图1)。
在调整燃烧器的过程中,其具体位置固定不变,只调整内外风阀门开度及内外筒间隙。
内风为旋欠烧料成因及处理常志林,许志刚,罗霄,李玉梅(中联水泥有限责任公司南阳分公司,河南镇平474250)理而单独布石灰石或粉煤灰的现象。
3磨机产量低、吐渣多3.1原因分析(1)观察进磨皮带的料发现石灰石的粒度过大,产量低、振动大、吐渣多。
水泥厂生产过程中异常窑况的分析及处理汇总
异常窑况的分析及处理预分解窑在生产过程中由于原材料、燃料的变化,或者设备故障及操作失误等原因,引起窑外分解窑的生产受阻或波动,使整个操作系统难以控制,造成不同的异常窑况。
针对不同的异常窑况需要分析其产生的原因采取合理有效的措施进行解决,这一过程就是异常窑况的分析及处理。
有时这一过程是需要反复多次,方能将异常窑况扭转。
在实际生产中,要认真分析问题产生的原因,并果断处理,不断总结经验,提高操作水平。
预分解窑系统结皮、堵塞预分解窑在生产过程中,人窑物料的碳酸盐分解率基本达90%以上,才能满足窑内烧成的要求。
物料的分解烧成过程实际上是一个复杂的物理、化学反应过程,其中一些成分黏结在预热器、分解炉的管壁上,形成结皮而造成堵塞。
一、结皮结皮是物料在预分解窑的预热器、分解炉等管道内壁上,逐步分层黏挂,形成疏松多孔的尾状覆盖物,多发部位是窑尾下料斜坡,缩口上、下部,以及旋风预热器的锥体部位。
一般认为结皮的发生与所用的原料、燃料及预分解窑各处温度变化有关,下面就此相关的几个原因进行分析。
1、原燃材料中的有害成分的影响在预分解窑生产中,原燃材料中的有害成分主要指硫、氯、碱,生料和熟料中的碱主要源于黏土质原料及泥灰质的石灰岩和燃料,硫和氯化物主要由黏土质原料和燃料带入。
由生料及燃料带入系统中碱、氯、硫的化合物,在窑内高温下逐步挥发,挥发出来的碱、氯、硫以气相的形式与窑气混合在一起,通过缩口后,被带到预热器内,当它们与生料在一定的温度范围内相遇时,这些挥发物可被冷凝在生料表面上。
冷凝的碱、氯、硫随生料又重新回到窑内,造成系统内这些有害成分的往复遁环,逐渐积聚。
这些碱、氯、硫组成的化合物溶点较低,当它在系统内循环时,凝聚于生料颗粒表面上,使生料表面的化学成分改变,当这些物料处于较高温度下,其表面首先开始熔化,产生液相,生成部分低熔化合物。
这些化合物与温度较低的设备或管道壁接触时,便可能黏结在上面,如果碱、氯、硫含量较多而温度又较高,生成的液相多而黏,则使料粉层层黏挂,愈结愈厚,形成结成。
- 1、下载文档前请自行甄别文档内容的完整性,平台不提供额外的编辑、内容补充、找答案等附加服务。
- 2、"仅部分预览"的文档,不可在线预览部分如存在完整性等问题,可反馈申请退款(可完整预览的文档不适用该条件!)。
- 3、如文档侵犯您的权益,请联系客服反馈,我们会尽快为您处理(人工客服工作时间:9:00-18:30)。
预分解窑熟料欠烧成因及处理
--------------------------------------------------------------------------------
作者:-
作者:佚名时间:2007-4-2
1 欠烧料成因
1.1 窑头用煤量太大,温度偏低
在生产过程中,当fCaO不合格时,总是认为窑头用煤量过少,温度低,煤灰掺入量少。
于是便增加窑头用煤量,试图以此来提高烧成带温度,有时甚至出现窑头用煤量与分解炉用煤量倒置的现象,造成系统温度偏高,窑尾温度达到1 200℃,C5级筒出口温度≥500℃,窑尾废气中CO含量高,直接威胁预热器的安全运行。
对于回转窑来说,它的容积热力强度是有一定限度的。
当容积热力强度已到极限时,增加窑头用煤量,会造成煤粉不完全燃烧,窑内还原气氛加剧,窑头温度进一步降低。
当窑温较低时,再多加煤反而更解决不了问题,因燃烧速度与温度有关,多加煤会造成火焰黑火头长,火焰温度低,窑尾温度过高。
还会引起窑内还原气氛加重,结长厚窑皮,造成预热器系统结皮堵塞,从而使工艺系统进一步恶化,热工制度紊乱。
1.2 燃烧器火力不集中
我公司燃烧器的中心位于回转窑端面第四象限(+30mm,-30mm),伸入窑内300mm。
在调整燃烧器的过程中,其具体位置固定不变,只调整内外风阀门开度及内外筒间隙。
内风为旋流风,增加内风火焰粗短;外风为轴流风,增加外风火焰细长;内外筒间隙正常生产时调整范围为15mm--30mm,间隙越小火焰短,为超强火焰。
间隙越大火焰长。
另外,内外筒间隙的调整对火焰形状的影响特别大,调整不当容易烧毁窑皮及耐火砖。
在试生产期间,内风风阀臆40%,外风风阀≥80%,内外筒间隙30mm,火焰粗长,火力不集中,又不敢大幅度调整间隙。
燃烧器与煤质适应上没有大胆尝试(煤的低位发热量为20 900kJ/kg)。
当回转窑达到设计产量时,熟料欠烧,fCaO高达3.0,熟料立升重约1 100g/L。
1.3 熟料结粒过大
在试生产期间,由于窑头用煤量太大,窑速低,窑尾温度过高,导致液相提前出现,物料发黏形成大块,致使在烧成带无法烧透,造成出窑熟料结粒不均。
1.4 窑系统用风不当
(1)窑尾缩口闸板尺寸不合适,物料喷腾效应差,有落料现象,入窑内物料出现温差,加剧结粒现象的发生同时也加重了窑内的热负荷。
(2)为避免预热器温度高,不能拉大风,则易导致预热器内积料,当温度及风量波动较大时,积料突然塌落,窜入窑内,破坏窑内热工制度。
(3)篦冷机的风量偏低且风量不稳,篦速和喂料的关系掌握不好,料层厚度不能有效控制。
风量主要通过窑和三次风管两个管道导入预热器,兼顾分解炉内煤的完全燃烧和喷腾效应的产生,一味强调
某一方面,结果都会适得其反。
2 解决措施
2.1 解决煤粉燃烧问题
(1)提高进厂煤的发热量,调整头煤及尾煤比例,逐渐降低窑头用煤量,增加分解炉用煤量;使入窑物料的表观分解率控制在95%以上,减少窑内的热负荷。
(2)降低篦冷机篦速,采取厚料层操作,努力提高了二次风温和三次风温,使煤粉的燃烧更加充分,烧成带热力更加集中。
2.2 调整燃烧器参数
调整内外风的关系,使窑内火焰形状与火焰长度控制在合理的范围内,以保证窑内的热力强度。
经反复研究与试验,对燃烧器进行了大幅度的调整,内风风阀80%,外风风阀90%,内外筒间隙15mm,火焰细短,火力集中,火焰活泼有力。
窑的喂料量可达240t/h (设计喂料量206t/h),fCaO均在1.0左右,熟料立升重1 350±75g/L。
2.3 解决结粒问题
(1) 优化操作参数,严格控制C5级筒出口温度在840±10℃,分解炉出口温度870±10℃,窑尾温度1 000±50℃。
(2)严格控制生料中粉煤灰的掺加量,控制入窑生料Al2O3含量。
(3)在生产过程中,采用薄料快烧的操作方法,在窑系统稳定的情况下尽量提高窑速,窑速由原来的2.60r/min提高到3.50r/min。
(4)实践证明,所采取的措施是有效的。
熟料结粒细小均齐,直径大部分3cm,直径≥10cm的几乎没有,熟料颜色发亮尧致密尧强度高。
2.4 调整窑及炉用风比例
适当调整窑及炉用风比例及相关参数。
三次风阀门及窑尾缩口闸板调节以保持窑炉用风比例适宜,窑内通风适当为原则;总排风量调节根据喂料量大小,以满足生料悬浮需要和煤粉燃烧需要,保持适宜窑及炉过剩空气系数为原则。
通过采取上述措施后,欠烧料得到了较好的控制,窑系统热工制度趋于稳定,熟料质量和水泥质量稳步提高,熟料3天抗压强度达32MPa以上。
上传时间:2007-08-13 07:45:13 【评论】【关闭】。