预分解窑熟料热耗的影响因素和降低的途径
降低水泥熟料热耗的原理及途经
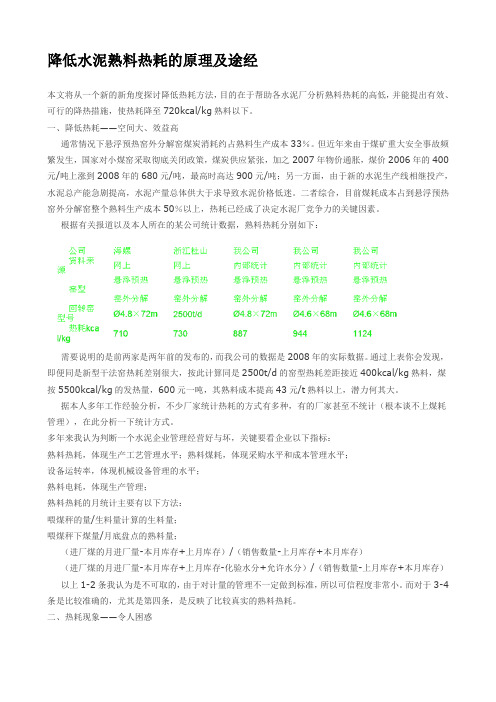
降低水泥熟料热耗的原理及途经本文将从一个新的新角度探讨降低热耗方法,目的在于帮助各水泥厂分析熟料热耗的高低,并能提出有效、可行的降热措施,使热耗降至720kcal/kg熟料以下。
一、降低热耗——空间大、效益高通常情况下悬浮预热窑外分解窑煤炭消耗约占熟料生产成本33%。
但近年来由于煤矿重大安全事故频繁发生,国家对小煤窑采取彻底关闭政策,煤炭供应紧张,加之2007年物价通胀,煤价2006年的400元/吨上涨到2008年的680元/吨,最高时高达900元/吨;另一方面,由于新的水泥生产线相继投产,水泥总产能急剧提高,水泥产量总体供大于求导致水泥价格低迷。
二者综合,目前煤耗成本占到悬浮预热窑外分解窑整个熟料生产成本50%以上,热耗已经成了决定水泥厂竞争力的关键因素。
根据有关报道以及本人所在的某公司统计数据,熟料热耗分别如下:需要说明的是前两家是两年前的发布的,而我公司的数据是2008年的实际数据。
通过上表你会发现,即便同是新型干法窑热耗差别很大,按此计算同是2500t/d的窑型热耗差距接近400kcal/kg熟料,煤按5500kcal/kg的发热量,600元一吨,其熟料成本提高43元/t熟料以上,潜力何其大。
据本人多年工作经验分析,不少厂家统计热耗的方式有多种,有的厂家甚至不统计(根本谈不上煤耗管理),在此分析一下统计方式。
多年来我认为判断一个水泥企业管理经营好与坏,关键要看企业以下指标:熟料热耗,体现生产工艺管理水平;熟料煤耗,体现采购水平和成本管理水平;设备运转率,体现机械设备管理的水平;熟料电耗,体现生产管理;熟料热耗的月统计主要有以下方法:喂煤秤的量/生料量计算的生料量;喂煤秤下煤量/月底盘点的熟料量;(进厂煤的月进厂量-本月库存+上月库存)/(销售数量-上月库存+本月库存)(进厂煤的月进厂量-本月库存+上月库存-化验水分+允许水分)/(销售数量-上月库存+本月库存)以上1-2条我认为是不可取的,由于对计量的管理不一定做到标准,所以可信程度非常小。
水泥窑煅烧工艺异常情况原因分析及处理措施
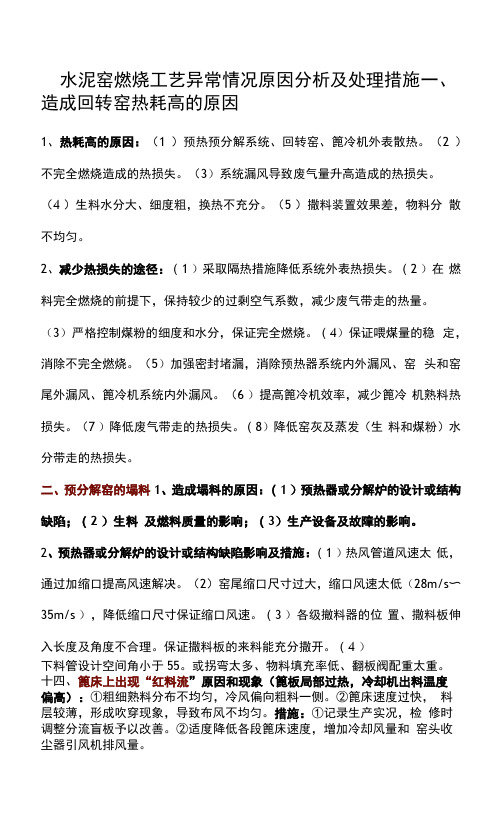
水泥窑燃烧工艺异常情况原因分析及处理措施一、造成回转窑热耗高的原因1、热耗高的原因:(1 )预热预分解系统、回转窑、篦冷机外表散热。
(2 )不完全燃烧造成的热损失。
(3)系统漏风导致废气量升高造成的热损失。
(4 )生料水分大、细度粗,换热不充分。
(5 )撒料装置效果差,物料分散不均匀。
2、减少热损失的途径:(1 )采取隔热措施降低系统外表热损失。
(2 )在燃料完全燃烧的前提下,保持较少的过剩空气系数,减少废气带走的热量。
(3)严格控制煤粉的细度和水分,保证完全燃烧。
(4)保证喂煤量的稳定,消除不完全燃烧。
(5)加强密封堵漏,消除预热器系统内外漏风、窑头和窑尾外漏风、篦冷机系统内外漏风。
(6 )提高篦冷机效率,减少篦冷机熟料热损失。
(7 )降低废气带走的热损失。
(8)降低窑灰及蒸发(生料和煤粉)水分带走的热损失。
二、预分解窑的塌料1、造成塌料的原因:(1 )预热器或分解炉的设计或结构缺陷;(2 )生料及燃料质量的影响;(3)生产设备及故障的影响。
2、预热器或分解炉的设计或结构缺陷影响及措施:(1 )热风管道风速太低,通过加缩口提高风速解决。
(2)窑尾缩口尺寸过大,缩口风速太低(28m/s〜35m/s ),降低缩口尺寸保证缩口风速。
(3 )各级撤料器的位置、撒料板伸入长度及角度不合理。
保证撒料板的来料能充分撒开。
(4 )下料管设计空间角小于55。
或拐弯太多、物料填充率低、翻板阀配重太重。
十四、篦床上出现“红料流”原因和现象(篦板局部过热,冷却机出料温度偏高):①粗细熟料分布不均匀,冷风偏向粗料一侧。
②篦床速度过快,料层较薄,形成吹穿现象,导致布风不均匀。
措施:①记录生产实况,检修时调整分流盲板予以改善。
②适度降低各段篦床速度,增加冷却风量和窑头收尘器引风机排风量。
十五、篦板温度偏高原因:①熟料粒度过细;②篦床上出现〃红料流〃;③ 风室冷却风量过大,或料层较薄,熟料层被吹穿;④风室冷却风量过小,缺乏以充分冷却熟料;⑤窑皮跨落,篦床上有大量熟料堆积,无法及时冷却所致;⑥篦床速度过快,料层过薄;⑦篦板脱落或篦绛较宽,漏料比拟严重。
预分解窑熟料欠烧成因及处理

预分解窑熟料欠烧成因及处理--------------------------------------------------------------------------------作者:-作者:佚名时间:2007-4-21 欠烧料成因1.1 窑头用煤量太大,温度偏低在生产过程中,当fCaO不合格时,总是认为窑头用煤量过少,温度低,煤灰掺入量少。
于是便增加窑头用煤量,试图以此来提高烧成带温度,有时甚至出现窑头用煤量与分解炉用煤量倒置的现象,造成系统温度偏高,窑尾温度达到1 200℃,C5级筒出口温度≥500℃,窑尾废气中CO含量高,直接威胁预热器的安全运行。
对于回转窑来说,它的容积热力强度是有一定限度的。
当容积热力强度已到极限时,增加窑头用煤量,会造成煤粉不完全燃烧,窑内还原气氛加剧,窑头温度进一步降低。
当窑温较低时,再多加煤反而更解决不了问题,因燃烧速度与温度有关,多加煤会造成火焰黑火头长,火焰温度低,窑尾温度过高。
还会引起窑内还原气氛加重,结长厚窑皮,造成预热器系统结皮堵塞,从而使工艺系统进一步恶化,热工制度紊乱。
1.2 燃烧器火力不集中我公司燃烧器的中心位于回转窑端面第四象限(+30mm,-30mm),伸入窑内300mm。
在调整燃烧器的过程中,其具体位置固定不变,只调整内外风阀门开度及内外筒间隙。
内风为旋流风,增加内风火焰粗短;外风为轴流风,增加外风火焰细长;内外筒间隙正常生产时调整范围为15mm--30mm,间隙越小火焰短,为超强火焰。
间隙越大火焰长。
另外,内外筒间隙的调整对火焰形状的影响特别大,调整不当容易烧毁窑皮及耐火砖。
在试生产期间,内风风阀臆40%,外风风阀≥80%,内外筒间隙30mm,火焰粗长,火力不集中,又不敢大幅度调整间隙。
燃烧器与煤质适应上没有大胆尝试(煤的低位发热量为20 900kJ/kg)。
当回转窑达到设计产量时,熟料欠烧,fCaO高达3.0,熟料立升重约1 100g/L。
确定三个率值和熟料的热耗
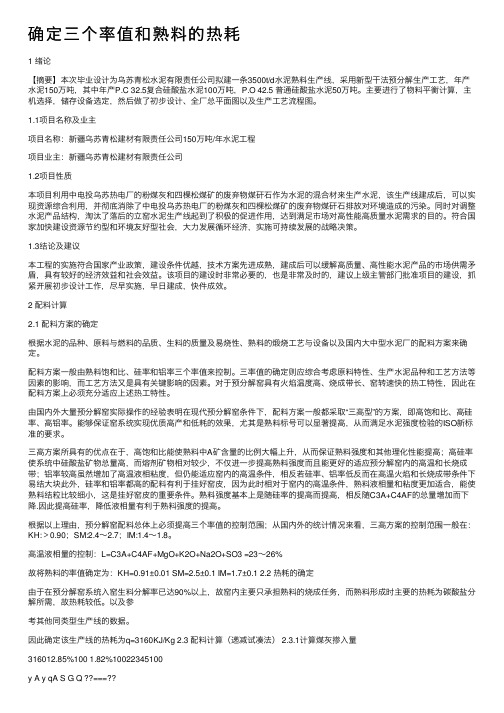
确定三个率值和熟料的热耗1 绪论【摘要】本次毕业设计为乌苏青松⽔泥有限责任公司拟建⼀条3500t/d⽔泥熟料⽣产线,采⽤新型⼲法预分解⽣产⼯艺,年产⽔泥150万吨,其中年产P.C 32.5复合硅酸盐⽔泥100万吨,P.O 42.5 普通硅酸盐⽔泥50万吨。
主要进⾏了物料平衡计算,主机选择,储存设备选定,然后做了初步设计、全⼚总平⾯图以及⽣产⼯艺流程图。
1.1项⽬名称及业主项⽬名称:新疆乌苏青松建材有限责任公司150万吨/年⽔泥⼯程项⽬业主:新疆乌苏青松建材有限责任公司1.2项⽬性质本项⽬利⽤中电投乌苏热电⼚的粉煤灰和四棵松煤矿的废弃物煤矸⽯作为⽔泥的混合材来⽣产⽔泥,该⽣产线建成后,可以实现资源综合利⽤,并彻底消除了中电投乌苏热电⼚的粉煤灰和四棵松煤矿的废弃物煤矸⽯排放对环境造成的污染。
同时对调整⽔泥产品结构,淘汰了落后的⽴窑⽔泥⽣产线起到了积极的促进作⽤,达到满⾜市场对⾼性能⾼质量⽔泥需求的⽬的。
符合国家加快建设资源节约型和环境友好型社会,⼤⼒发展循环经济,实施可持续发展的战略决策。
1.3结论及建议本⼯程的实施符合国家产业政策,建设条件优越,技术⽅案先进成熟,建成后可以缓解⾼质量、⾼性能⽔泥产品的市场供需⽭盾,具有较好的经济效益和社会效益。
该项⽬的建设时⾮常必要的,也是⾮常及时的,建议上级主管部门批准项⽬的建设,抓紧开展初步设计⼯作,尽早实施,早⽇建成,快件成效。
2 配料计算2.1 配料⽅案的确定根据⽔泥的品种、原料与燃料的品质、⽣料的质量及易烧性、熟料的煅烧⼯艺与设备以及国内⼤中型⽔泥⼚的配料⽅案来确定。
配料⽅案⼀般由熟料饱和⽐、硅率和铝率三个率值来控制。
三率值的确定则应综合考虑原料特性、⽣产⽔泥品种和⼯艺⽅法等因素的影响,⽽⼯艺⽅法⼜是具有关键影响的因素。
对于预分解窑具有⽕焰温度⾼、烧成带长、窑转速快的热⼯特性,因此在配料⽅案上必须充分适应上述热⼯特性。
由国内外⼤量预分解窑实际操作的经验表明在现代预分解窑条件下,配料⽅案⼀般都采取“三⾼型”的⽅案,即⾼饱和⽐、⾼硅率、⾼铝率。
武汉理工大学无机非金属材料工学2004

武汉理工大学2004年研究生入学考试试题代号:448 课程名称:无机非金属材料工学一、名词解释(20分)1.胶凝材料(3分)2.水泥的安定性(3分)3.高性能混凝土(4分)4.触变性(2分)5.酸度系数(写出其表达式)(2分)6.坯釉适应性(3分)7.浮法玻璃的平衡厚度(2分)8.退火温度(2分)二、填空:(每空1分,共30分)1.对于混凝土拌合物坍落度大于10mm的新拌混凝土,通常采用坍落度方法测定其流动性,而对于坍落度小于10mm的干硬性混凝土拌合物,可采用测定其稠度。
2.测定水泥ISO强度时,胶砂比,水灰比。
3.生产硅酸盐水泥的主要原料是,和。
4.水泥细度愈细,其强度,放热量。
5用碎石配制的混凝土比同条件下用卵石配制的混凝土流动性要,强度要。
6为了调节硅酸盐水泥的凝结时间,长掺入适量的。
7.水泥的主要水化产物有,,,,水化铁酸钙等。
8.根据成型方法的不同,坯料通常可分为三类:。
9.对各种坯料的基本质量要求是:。
10.施釉(glazing)的基本方法有浸釉、、三种。
11.存在于玻璃液中的气体有三种形态:。
12.根据澄清剂的不同作用机理大致可分为、硫酸盐类澄清剂和卤化物类澄清剂。
13.玻璃体的缺陷按其状态不同,可以分为三大类:。
14.耐火纤维的生产方法主要有以下几种、熔融提炼法和回转法、高速离心法、胶体法。
15.坯釉组成的表示方法有配量表示法、、示性矿物组成表示法及实验式表示法。
16.根据成型方法的不同,坯料通常可分为三类:。
17.陶瓷颜料种类很多,可以归纳三方面的用途: 、、绘制花纹图案。
18.施釉(glazing)的基本方法有浸釉、、三种。
19.对釉浆的质量要求是:一定的细度、适中的相对密度(浓度)、。
20.根据各种氧化物在玻璃结构中的作用不同可将它们分为、玻璃中间体、玻璃调整体。
21.玻璃制品的退火包括四个阶段。
22.耐火材料是耐火度不低于1580°C的无机非金属材料,不能作为制品使用温度的。
【节能】浅谈降低预分解窑熟料煤耗的措施
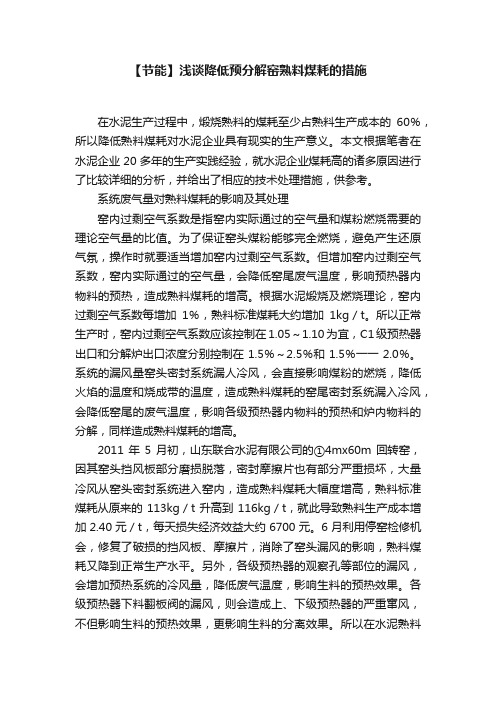
【节能】浅谈降低预分解窑熟料煤耗的措施在水泥生产过程中,煅烧熟料的煤耗至少占熟料生产成本的60%,所以降低熟料煤耗对水泥企业具有现实的生产意义。
本文根据笔者在水泥企业20多年的生产实践经验,就水泥企业煤耗高的诸多原因进行了比较详细的分析,并给出了相应的技术处理措施,供参考。
系统废气量对熟料煤耗的影响及其处理窑内过剩空气系数是指窑内实际通过的空气量和煤粉燃烧需要的理论空气量的比值。
为了保证窑头煤粉能够完全燃烧,避免产生还原气氛,操作时就要适当增加窑内过剩空气系数。
但增加窑内过剩空气系数,窑内实际通过的空气量,会降低窑尾废气温度,影响预热器内物料的预热,造成熟料煤耗的增高。
根据水泥煅烧及燃烧理论,窑内过剩空气系数每增加1%,熟料标准煤耗大约增加1kg/t。
所以正常生产时,窑内过剩空气系数应该控制在1.05~1.10为宜,C1级预热器出口和分解炉出口浓度分别控制在1.5%~2.5%和1.5%一一2.0%。
系统的漏风量窑头密封系统漏人冷风,会直接影响煤粉的燃烧,降低火焰的温度和烧成带的温度,造成熟料煤耗的窑尾密封系统漏入冷风,会降低窑尾的废气温度,影响各级预热器内物料的预热和炉内物料的分解,同样造成熟料煤耗的增高。
2011年5月初,山东联合水泥有限公司的①4mx60m回转窑,因其窑头挡风板部分磨损脱落,密封摩擦片也有部分严重损坏,大量冷风从窑头密封系统进入窑内,造成熟料煤耗大幅度增高,熟料标准煤耗从原来的113kg/t升高到116kg/t,就此导致熟料生产成本增加2.40元/t,每天损失经济效益大约6700元。
6月利用停窑检修机会,修复了破损的挡风板、摩擦片,消除了窑头漏风的影响,熟料煤耗又降到正常生产水平。
另外,各级预热器的观察孔等部位的漏风,会增加预热系统的冷风量,降低废气温度,影响生料的预热效果。
各级预热器下料翻板阀的漏风,则会造成上、下级预热器的严重窜风,不但影响生料的预热效果,更影响生料的分离效果。
降低预分解窑窑衬消耗的措施
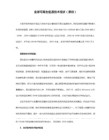
(1)熟料熔体渗入。熟料熔体主要源自窑料和燃料,渗入相主要是C2S、C4AF。其中渗入变质层中的C2S和C4AF会强烈地溶蚀镁铬砖中的方镁石和铬矿石,析出次生的CMS和镁蔷薇辉石(C3MS2)等硅酸盐矿物,有时甚至还会析出钾霞石;而熔体则会充填砖衬内气孔,使该部分砖层致密化和脆化;加之热应力和机械应力双重作用,导致砖极易开裂剥落。因C2S、C4AF在550℃以上即开始形成,而预分解窑入窑物料温度已达800℃~860℃,因此熟料熔体渗入贯穿于整个预分解窑窑内,即熟料熔体对预分解窑各带窑衬均有一定渗入侵蚀作用。
以上是预分解窑窑衬匹配的一般原则,部分大中型预分解窑窑衬的实际匹配使用情况见表1。根据这两方面的综合分析,总结出窑衬的合理匹配如表2所示。
(2)把好进货质量关和窑衬施工质量关。要严格遵守“水泥回转窑用耐火材料使用规程”中的相关要求,选购耐火材料时,应要求供货商提供产品质量担保书,并应取样送有关权威监测部门复检,以杜绝假冒伪劣产品进厂。与此同时,对施工质量亦要进行严格的监督,以确保窑衬的耐火性、密封性、隔热性、整体性、耐久性。重点应对耐火泥的配制、砖缝和膨胀缝处理等一系列技术问题严格把关。首先,更换窑衬前要编制施工方案,按砌筑要求在窑内划出纵向和横向控制线;其次,每天召开有关负责人协调会,及时解决施工中出现的问题;第三是实行项目负责制,设立专人跟班监督;最后,要求砌筑选用耐火砖,不得缺角少棱。
窑预分解系统的问题分析及改进措施

窑预分解系统的问题分析及改进措施--------------------------------------------------------------------------------作者:-作者:何文明李卫泽单位:红塔滇西水泥股份有限公司 [2007-9-3]关键字:窑-预分解摘要:我厂1号RSP窑经过6年多的运转,系统耐火材料呈现出不同程度的磨损、烧坏现象。
SB室下部掉砖,进而壳体烧损;SC室用风不良,导致边壁物料保护层不均衡,局部衬砖磨损严重;斜烟道及鹅颈管侧墙衬砖垮落,由于鹅颈管结构缺陷,经常结皮和堆料;MC室断面物料分布不均,物料稀相区炉壁烧损,直至筒体严重变形;因窑尾缩口处风速低,喷腾能力减弱而塌料;高温级旋风筒分离效率低,导致物料大量返回,内循环增加等。
本文依据热工标定结果,对该预分解系统出现的问题进行分析,并提出改进措施。
1 RSP窑系统工况分析热工标定主要参数对比见表1、表2,窑尾高温区工艺流程见图1。
表1 预热预分解系统温度变化℃表2 RSP炉的分解进程变化注:1997年数据为南京化工大学硅酸地方国营工程研究所的热工标定结果,SC室出口指斜烟道出进口等同于鹅颈管出口。
图1 窑尾高温区工艺流程1.1 三次风温度及其对SC室工况的影响由表1可见,三次风温度和入炉生料温度分别只有600℃和671℃。
入炉生料温度低主要是由于C4锥体及下料管增开人孔门较多,外漏风量和散热损失增加引起的,通过加强管理,隔热堵漏后完全可以解决;三次风温度目前基本稳定在560~580℃,提高的余地很小。
其原因是:我厂采用单筒冷却机,经过多年的运转,内部装置所遭受的磨损和腐蚀不断加剧,而且增加了砌筑耐火砖的长度,熟料停留时间短(约为30min),出机熟料温度高(~290℃),使热效率本身就不高的单筒冷却机热回收率进一步降低(1997年热工标定结果为56.6%)。
三次风温度是影响分解率和燃尽率的重要因素。
- 1、下载文档前请自行甄别文档内容的完整性,平台不提供额外的编辑、内容补充、找答案等附加服务。
- 2、"仅部分预览"的文档,不可在线预览部分如存在完整性等问题,可反馈申请退款(可完整预览的文档不适用该条件!)。
- 3、如文档侵犯您的权益,请联系客服反馈,我们会尽快为您处理(人工客服工作时间:9:00-18:30)。
预分解窑熟料热耗的影响因素和降低的途径1 系统熟料热耗高的原因分析国外水泥厂家通过采用低阻高效的多级预热器系统、新型篦式冷却机和多通道喷煤管等先进技术装备,利用窑系统的低温废气余热发电,回收使用二次能源等先进工艺,降低了水泥生产的熟料热耗。
表1、表2分别为国内外部分水泥厂家熟料热耗、预热器出口废气热损失及系统漏风量的对比。
国内生产厂家的熟料热耗较国外高出较多,以RSP预分解窑为例,G厂、C厂和F厂的热耗分别比日本RSP窑高出31%、30%和13%。
众所周知,国内生产厂家热耗高的原因有三个方面。
一是预热器出口废气热损失大。
国内厂家预热器出口废气热损失占系统熟料热耗的26%左右,有的近30%,平均比国外厂家高出约4%,而国内这些厂家在我国还算是较好的水泥企业。
造成如此高的废气热损失主要原因在于预热器出口废气量大、废气温度较高、系统存在较严重的漏风。
国外较先进的带五级预热器的预分解窑的预热器出口废气温度一般为290~310℃,如果国内厂家预热器出口废气温度能降至这个水平,则其预热器出口废气热损失可降低许多。
以G厂为例,若其预热器出口废气温度由目前的370℃降至300℃,则废气带走的热损失将由目前的每千克熟料1119kJ降至903kJ,降幅为19.3%;如果此时其出口废气量再降低,比如系统漏风量由目前的每千克熟料0.389kg降为0.195kg,即降低一半,则废气量由每千克熟料2.898kg降至2.704kg,其它条件不变,此时预热器出口废气热损失又将降到842kJ,降幅为6.7%,这种情况下系统的熟料热耗将由目前的4 031kJ/kg降为3254kJ/kg,降幅为19.3%。
表2中A厂、D厂和E厂烧成系统漏风量较少,多数厂家系统漏风量占物料总收入的比例为日本DD窑的2.5倍,有的厂家甚至高达6倍。
如果用系统漏风量占预热器出口废气量的百分比来看,多数厂家约为15%,有的竟高达23%。
由此可见系统漏风问题在部分厂家仍没有引起高度重视,但系统漏风造成的损失却是显而易见的。
一方面增大了系统废气量,增加了热损失和风机电耗,另一方面由于漏风降低了气体温度,进而降低了气固换热效率。
特别是各级预热器下部翻板阀及下料管的内、外部漏风,将使旋风筒分离效率急剧降低,从而造成高温物料向上级低温旋风筒返混,扰乱系统正常生产,其热耗必然增加。
表1 国内外部分厂家熟料热耗、预热器出口废气热损失的比较表2 国内外部分厂家预热器出口废气量及系统漏风量的比较当然,国内厂家预热器出口废气量即使扣除系统漏入的空气量,其数值也多在2.1kg/kg左右,而日本DD窑扣除后仅为1.7kg/kg。
国内预热器出口废气量大的主要原因除热耗高、燃烧产生的烟气量大外,系统用风量方面仍值得深入的探讨。
国内厂家熟料热耗高的第二个方面是烧成系统的散热损失较大。
数据对比如表3所示。
表3 国内外部分厂家烧成系统的散热损失(kJ/kg)注:1.E厂测定的散热损失数据受到天气影响较大;2.F厂冷却机为单筒冷却机,其余各厂为篦式冷却机。
由表3可见,就系统各部分散热损失大小而言,回转窑最大,以下依次为预热器、三次风管、分解炉、冷却机(篦式冷却机),其中回转窑、预热器两者散热损失之和要占系统总散热量的80%~90%。
除去二者的外表面积较大的原因外,设备的表面温度较高也不容忽视,特别是回转窑。
造成国内水泥生产厂家烧成系统散热损失高不仅有内衬材料选择的原因,而且有生产操作上的原因。
如耐火材料的选择不当,使用时间较长,隔热效果不够理想以及窑头、分解炉两把火用煤量不尽合理,使烧成系统的整体温度普遍较高等。
在耐火材料配套设计和施工、窑速变化及碱等挥发性组分的侵蚀对耐火材料的影响等方面重视也不够〔1〕。
另外还有设备设计选型上的原因。
国内在设计中小型预分解窑系统时,可能本着设备留有适当富余能力、缓冲操作上的困难等种种原因,设备选型往往偏大,以回转窑为例,国内外部分厂家的比较如表4所示。
通过对比可以看出,就窑的单位容积产量而言,国内回转窑明显要低于国外厂家,从某种程度上来说,也就意味着国内回转窑(超短窑除外)规格的设计仍值得探讨。
以Φ4m×60m的回转窑为例,印度Visaka水泥公司的窑的设计生产能力为2500t/d,而国内只有2 000t/d,两者差值竟然高达25%。
生产实践指出,对于同一规格的回转窑,会因预热器与分解炉等的规格匹配、原燃料的品质种类、窑炉燃料的用量比、配料的率值、化学成分的稳定性及操作而影响其台时产量〔2〕,但当热负荷的主体碳酸盐分解,部分或大部分从窑内移到窑外时,决定系统能力的因素也理应由回转窑移到预热器和分解炉系统〔3〕。
目前国外厂家在保证预分解程度高且稳定,回转窑具有一定潜力的基础上,纷纷在缩小窑的规格,比如超短窑。
这样可适当降低窑的散热损失,减小耐火材料的用量,有利于节能。
与国外相比,国内在这方面还存在提高认识的问题。
在设计新的水泥生产线时,应具体考虑到工厂使用的原、燃料品质,操作管理水平等,充分做到设备选型合理、优化,功能匹配得当,否则生产中产量的提高会使窑系统平衡变得极为敏感,有时遇到小小的波动亦难以调整。
表4 国内外部分厂家回转窑的规格及产量注:表中国内厂家窑单位容积产量和窑单位截面积产量均是按照窑的有效尺寸来进行计算的。
由表3可以发现,分解炉的散热损失占系统总散热损失的比例较小,适当增大分解炉的有效容积,对系统散热损失影响不大,但可延长粉料在炉内停留时间,对煤粉燃烧与生料分解反应有利。
目前新型分解炉的设计,除了注重改变燃料入口位置、燃料、生料、三次风分布方式外,还存在着增大炉体体积的趋势。
通过表4还可以看出,规模大的厂家的窑的单位截面积产量大于规模小的厂家。
同时研究也表明,对于不同规模的预分解窑,规模大的预分解窑的单位容积的耐火材料用量比规模小的预分解窑要少,而且在国内各种规模的预分解窑系统中,没有达产达标的以中小型窑居多。
因此,本着工厂的技术经济指标考虑,国内在新建预分解窑时,在资金允许的条件下以采用大中型预分解窑为佳,日本、东南亚一些国家纷纷建造大型的水泥预分解生产线也足以证明这一点。
冷却机余风带走热量较大也是导致系统热耗高的一个原因,如表5所示。
表5 各厂冷却机的热回收效率、出冷却机熟料温度及二次风温等的比较注:表中二次风温为各厂的测定值,因二次风温测量误差较大,故仅供参考。
由表5可知,若从出冷却机余风风量、风温两项指标来看,国内厂家与国外水平还比较接近。
但国内厂家冷却机热回收效率、入窑二次风温明显偏低,出冷却机熟料温度偏大,这些都说明了国内的篦式冷却机与国外厂家相比,在冷却风利用率、提高窑系统二次风温等方面尚存在较大差距。
2 降低系统熟料热耗的途径从前面叙述中可以知道,国内厂家熟料热耗高的原因虽主要在于预热器出口废气热损失、系统散热损失及冷却机余风热损失三大热损失较高,但具体到各项热损失仍有其根本原因。
目前,降低系统热耗的途径有多方面,本文归结如下。
2.1 优化系统设计和生产操作2.1.1 优化原料配方原料的性质及其配料方案对水泥生料易烧性有着重要的影响,它与烧成系统设备如分解炉等的设计、操作密切相关。
生产中理应对不同的原料,通过优化配比,为实现节能降耗打下基础〔4〕。
2.1.2 采用多级新型旋风预热器系统造成预热器出口废气热损失较高的原因有预热器系统换热效率不高,厂家忽视了系统漏风对水泥生产的影响等。
实践证明只有选用多级低阻高效旋风预热器系统,彻底改进预热器本身的性能,才能提高预热器系统的换热效率,降低预热器出口废气温度,生产中还应严格注意设备的密封堵漏,从而降低系统的熟料热耗。
但对目前已建成投产的预分解窑,还可以针对其较高的预热器出口废气温度和出冷却机余风温度,通过低温废气余热发电,从而为降低系统熟料热耗做出贡献〔5〕,这在鲁南、琉璃河、宁国等厂已取得了成功。
2.1.3 应用新型高效的篦式冷却机新型篦式冷却机应力求以最少的冷却风冷却尽可能多的热熟料,使冷却风与热熟料充分地进行热交换,提高入窑系统的二、三次风的温度,从而达到高效、低耗的目的〔6〕。
1990年新型的控流式篦式冷却机投放市场以来,很快以其节省熟料热耗、提高窑系统的运转率和可靠性,以及延长篦板寿命与减少维修量等优点,在国外得到了广泛的运用,获得了显著的效益〔7〕。
目前,我国水泥工业也正积极推广带阻力篦板空气梁垫的新型高效篦式冷却机。
当然,除上述三点之外,正确合理地选择耐火材料和保温材料对水泥生产也至关重要,水泥生产中理应引起高度重视,以求实现窑系统及不同部位衬里的长寿命和低散热。
2.2 开发新型水泥烧成工艺,发展高性能水泥英国、美国、法国及日本等国已率先利用工业可燃废料来生产水泥。
他们通过水泥工业可以回收利用的可燃废料和含可燃质的原料作为二次燃料,结合循环流化床技术,进行水泥新烧成工艺的开发,业已取得了初步成功〔7,8〕。
国内在此方面尚未见到报导,但国内已着手进行新型干法窑燃无烟煤生产水泥技术的研究开发,同时不少单位已从节能降耗和环保角度出发,开展对具有低的钙硅比、低的烧成温度和高的水硬活性、高的水化率的高性能水泥的研究,以期达到降低生产能耗、减少资源消耗、减轻环境负荷的目的,促进我国水泥工业的结构性调整。
3 结论1)国内水泥厂家熟料热耗高的原因主要在于三大热损失较高,其中预热器出口废气量大、废气温度高、系统漏风严重、耐火材料使用不尽合理、冷却机热回收效率低等原因是导致系统热耗高的直接原因。
同时回转窑规格的设计等也值得进一步探讨。
2)降低系统热耗的途径有多方面。
一是从原料入手,优化原料配方。
二是优化系统设计和生产操作,通过采用多级低阻高效旋风预热器系统,或充分利用预热器出口废气热量和出冷却机余风热量,通过低温废气余热发电技术,为降低熟料热耗做贡献。
三是应用新型高效的篦式冷却机,通过提高冷却风的利用率,降低出冷却机的熟料温度,以此降低系统热耗。
3)耐火材料和保温材料的正确合理的配套选择、使用和管理等对降低系统热耗至关重要。
4)最大限度地将水泥工业可以回收利用的可燃废料和含可燃质的原料,乃至人类社会活动中排出的工业废弃物和生活废弃物作为二次燃料,加以有效利用,积极开发新型水泥烧成工艺,发展高性能水泥,实现我国水泥工业的可持续发展战略,并使水泥工业成为环境协调型产业体系。