品质检验程序
品质检验标准检验流程

品质检验标准检验流程
品质检验标准是指在生产过程中,为了保证产品质量符合预期标准,需要进行的一系列检验措施和方法。
以下是一般的品质检验标准检验流程:
1. 制定品质检验标准:根据产品的特性和要求,制定品质检验标准,包括外观、尺寸、性能等方面的指标和要求。
2. 样品准备:从生产批次或批次中随机选择一部分样品,以代表整个批次的质量情况。
3. 检验设备准备:根据不同的检验项目和要求,准备相应的检验设备和工具,如显微镜、计量器具、试验机等。
4. 检验项目确认:根据品质检验标准,确认需要进行的具体检验项目,包括外观检验、尺寸检验、物理性能检验等。
5. 选择合适的检验方法:根据不同的检验项目,选择合适的检验方法,如目测、测量、试验等。
6. 进行检验:按照品质检验标准和检验方法,对样品进行逐一检验,记录检验结果。
7. 判定结果:根据检验结果和品质检验标准,判定样品是否符合标准要求。
8. 评估检验结果:对检验结果进行评估,分析不符合要求的原
因,确定改进措施。
9. 检验报告和记录:根据检验结果,生成检验报告和记录,记录样品的检验情况和评估结果。
10. 处理不合格品:对于不符合标准要求的样品,按照内部程序进行处理,如返工、报废等。
11. 追踪和反馈:对检验结果进行追踪和反馈,确保问题得到及时解决,并作为改进质量控制措施的依据。
以上是一般的品质检验标准检验流程,具体的流程和步骤可能会因不同的产品和行业而有所差异。
三检制制度及质量检验程序
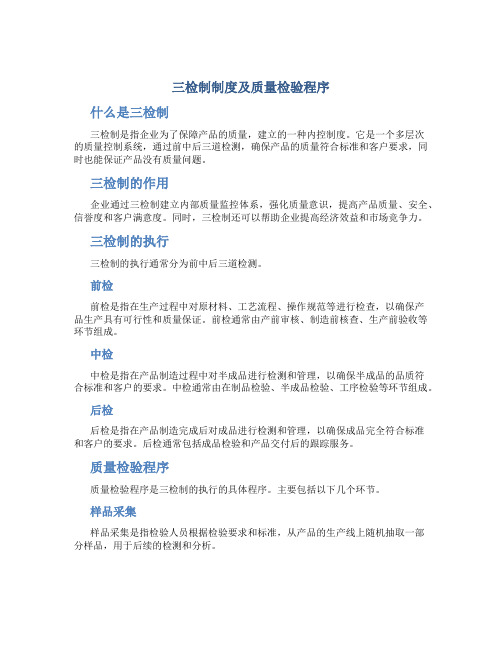
三检制制度及质量检验程序什么是三检制三检制是指企业为了保障产品的质量,建立的一种内控制度。
它是一个多层次的质量控制系统,通过前中后三道检测,确保产品的质量符合标准和客户要求,同时也能保证产品没有质量问题。
三检制的作用企业通过三检制建立内部质量监控体系,强化质量意识,提高产品质量、安全、信誉度和客户满意度。
同时,三检制还可以帮助企业提高经济效益和市场竞争力。
三检制的执行三检制的执行通常分为前中后三道检测。
前检前检是指在生产过程中对原材料、工艺流程、操作规范等进行检查,以确保产品生产具有可行性和质量保证。
前检通常由产前审核、制造前核查、生产前验收等环节组成。
中检中检是指在产品制造过程中对半成品进行检测和管理,以确保半成品的品质符合标准和客户的要求。
中检通常由在制品检验、半成品检验、工序检验等环节组成。
后检后检是指在产品制造完成后对成品进行检测和管理,以确保成品完全符合标准和客户的要求。
后检通常包括成品检验和产品交付后的跟踪服务。
质量检验程序质量检验程序是三检制的执行的具体程序。
主要包括以下几个环节。
样品采集样品采集是指检验人员根据检验要求和标准,从产品的生产线上随机抽取一部分样品,用于后续的检测和分析。
检测与分析检测与分析是指对采集的样品进行各项检测和分析,如物理检测、化学检测、功能检测、可靠性检测等等。
结果评价结果评价是指根据检测结果和标准要求,对检测的样品进行评价和分类,如合格、不合格、让步接收等等。
记录与报告记录与报告是指将检测过程中产生的数据、信息和进行记录和汇总,生成检验报告和检测清单。
检验报告是质量检测的重要成果之一,也是质量管理的重要依据。
三检制是企业为保证产品质量而实施的一种内部控制系统,通过前中后三道检测,确保产品符合标准和客户要求,同时也能提高企业的经济效益和市场竞争力。
质量检验程序是三检制的具体实施程序,它包括样品采集、检测与分析、结果评价和记录与报告等环节。
一个完整的质量检验程序不仅能够提高产品的质量,还能够让企业更好地满足客户需求和市场竞争需求。
品质部岗位职责及检验流程

质量部岗位职责及检验内容目录管理:AZL—01-2017—18目的:IQC/IPQC/FQC/OQC检验方法原材料检验(IQC )原进厂检验包括三个方面:①库检:原材料品名规格、型号、数量等是否符合实际,一般由仓管人员完成.②质检:检验原材料物理,化学等特性是否符合相应原材料检验规定,一般采用抽检方式.③试检:取小批量试样进行生产,检查生产结果是否符合要求。
来料不合格的处理:①标识:在外包装上标明“不合格”,堆置于“不合格区”或挂上“不合格”标识牌等。
②处置:退货或调货或其他特采。
③纠正措施:对供应商提供相关要求或建议防止批量不合格的再次出现。
2紧急放行:因生产急需,在检验报告出来前需采用的物资,为紧急放行。
需留样检验,并对所放行物资进行特殊标识并记录,以便需要时进行追踪。
3特采:从非合格供应商中采购物资--加强检验。
②检验不合格而采用的物资-—挑选或修复后使用。
4应特别关注不合格品所造成的损失:①投入阶段发现,损失成本为1元。
②生产阶段发现,损失成本为10元。
③在客户手中发现,损失成本为100元。
二、过程检验(IPQC )lPQC 的检验范围包括:①产品:半成品、成品的质量。
②人员:操作员工艺执行质量,设备操作技能差。
③设备:设备运行状态,负荷程度。
④工艺、技术:工艺是否合理,技术是否符合产品特性要求.⑤环境:环境是否适宜产品生产需要。
2工序产品检验:对产品的检验,检验方式有较大差异和灵活性,可依据生产实际情况和产品特性,检验方式更灵活。
质检员全检:适用于关键工序转序时,多品种小批量,有致命缺陷项目的工序产品。
工作量较大,合格的即准许转序或入库,不合格则责成操作员工立即返工或返维。
质检员抽检:适用于工序产品在一般工序转序时,大批量,单件价值低,无致命缺陷的工序产品.员工自检:操作员对自己加工的产品先实行自检,检验合格后方可发出至下道工序。
可提高产品流转合格率和减轻质检员工作量,不易管理控制,时有突发异常现象。
品质检验程序
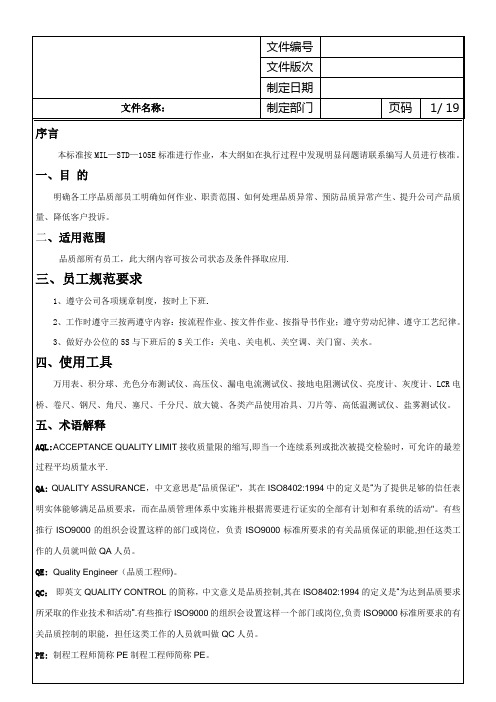
2、工作时遵守三按两遵守内容:按流程作业、按文件作业、按指导书作业;遵守劳动纪律、遵守工艺纪律。
3、做好办公位的5S与下班后的5关工作:关电、关电机、关空调、关门窗、关水。
四、使用工具
万用表、积分球、光色分布测试仪、高压仪、漏电电流测试仪、接地电阻测试仪、亮度计、灰度计、LCR电桥、卷尺、钢尺、角尺、塞尺、千分尺、放大镜、各类产品使用冶具、刀片等、高低温测试仪、盐雾测试仪。
8、良好的英文阅读与理解能力。
2、各岗位职责
质检员:根据检验标准(指导书\文件),对每批次产品进行检验或抽检,做好检验记录,汇总后反馈给上级;对工厂产品的质量工艺提出合理化建议;完成本部门领导交办的任务。
品质技术员:根据检验标准(指导书\文件),对每批次产品进行检验或抽检,做好检验记录,汇总后反馈给上级;对工厂产品的质量工艺提出合理化建议;完成本部门领导交办的任务。对区域组的质检员进行工作安排,对质检员的异常进行筛选处理。
品质工程师:1、负责生产现场异常件质量问题的分析、判断,并做出处理的决定,提出纠正和预防措施,确保生产在受控、稳定的状态下进行;
2、制订检验作业指导书,确保质量检验方法正确,检验结果可靠;
3、负责对配套件和生产原料的进厂、入库验收工作、确保进厂物料符合规定要求,并对供应商进行质量监控;
4、做好工序检验工作、半成品和成品检验工作,保证不合格品不流入下道工序和出厂,确保产品符合规定要求;
BOM:物料清单(BillofMaterialBOM).
SPC:是Statistical Process Control的简称统计过程控制。它是一种借助数理统计方法的过程控制工具.它对生产过程进行分析评价,根据反馈信息及时发现系统性因素出现的征兆,并采取措施消除其影响,使过程维持在仅受随机性因素影响的受控状态,以达到控制质量的目的.
质量检查方案

质量检查方案(1)初步检验程序1)货物送达到采购人指定的地点后,由业主方组成相关验收人员对货物进行初步检验。
检验内容:即对货物的数量、外观情况及供应商向采购人出具的使用说明书、权威机构的检验证明、质量保证书、质量合格证等相关单据进行目测检验。
2)货物经业主方验收人员初步检验后,在数量齐全、外观情况符合且上述单据齐全的情况下,验收人员在《货物收货情况检验表》上签字。
3)货物经过初步检验后,若有其中一项以上不符合要求或单据欠缺的,即认为是不合格的产品,业主方验收人员在收货情况检验表上签字、注明“不合格”的原因向我方反映,我方将积极采取更换或修理的措施。
(2)专业检验程序1)货物经初步检验合格后,由质量检验部门的专业技术人员对该批货物的质量进行详细的检测检验,包括但不限于上述第一步初步检验中的检测项目,必要时可以采取高科技手段进行检验或送检。
2)若专业技术人员经检验后,均认为该批货物符合要求,则在收货情况检验总表上签字并注明“合格”,并及时将该表送交予采购人和我方。
3)若专业技术人员在检验过程中对货物质量的鉴定发生争议或无法评断的,则向质量检验部门的主管作出书面报告,必要时可以请权威质量鉴定部门进行鉴定检验。
4)若专业技术人员经检验后,均认为该批货物不符合要求,则在收货情况检验总表上签字、注明“不合格”的原因并将该情况向采购人提交书面报告。
由采购人通知我方,我方将积极采取应对措施,由商务人员联系生产厂商,双方协商解决方案,在协商过程中做好资料、证据的收集作业,如合同文书的备份、技术人员的书面鉴定说明、权威鉴定机构的鉴定报告、与生产厂商会议的录音等,向采购人做出合理、及时的解决方案。
(3)入库前的最后检验1)货物经初步检验合格且经专业检验合格后,专业技术人员及时将收货情况检验表送达至业主方,由采购方进行入库前的最后检验。
2)业主方详细检查收货情况检验总表上的初步检验程序及专业检验程序的签字情况及货物的使用说明书、权威机构的检验证明、质量保证书、质量合格证等相关单据。
品质管理部门品质检验与异常处理流程

品质管理部门品质检验与异常处理流程在现代企业管理中,品质管理是一个至关重要的环节。
品质管理部门负责确保产品或服务达到预期的标准,并及时处理可能出现的品质异常问题。
本文将详细介绍品质管理部门的品质检验与异常处理流程。
一、品质检验流程1. 品质标准设定:品质管理部门首先根据产品或服务的特性和客户的需求,制定相应的品质标准。
这些标准可以包括外观要求、性能参数、质量指标等等。
2. 抽样检验:在生产过程中,品质管理部门根据设定的抽样方案,进行抽样检验。
抽样方案可以采用随机抽样或定期抽样的方式。
3. 检验方法选择:品质管理部门根据产品或服务的特性,选择合适的检验方法。
常见的检验方法包括外观检查、物理性能测试、化学分析等。
4. 检验记录:品质管理部门对每一次的检验都应该进行记录,包括检验日期、抽样数量、检验结果等信息。
这些记录有助于追溯问题的根源和及时纠正。
5. 数据分析:品质管理部门定期对检验结果进行数据分析,以了解产品或服务的品质状况。
通过对数据的分析,可以确定潜在的问题并采取相应的措施进行改进。
二、异常处理流程1. 异常发现:在品质检验中,品质管理部门可能会发现一些异常问题,如产品不合格、服务存在缺陷等。
这些异常问题可以通过检验记录或客户投诉等渠道得到。
2. 异常评估:品质管理部门需要对异常问题进行评估,确定其影响范围和严重程度。
评估过程可以包括对异常样品的再检验、对相关数据的分析等。
3. 异常分类:根据异常问题的性质和根源,品质管理部门将其进行分类。
常见的异常分类可以包括技术问题、材料问题、人为问题等。
4. 异常处理措施制定:品质管理部门根据异常问题的分类和评估结果,制定相应的处理措施。
处理措施可以包括返工、报废、供应商调整等。
5. 异常处理记录:品质管理部门应对每一次的异常处理都进行详细记录,包括处理措施、处理结果等信息。
这些记录有助于追溯问题的解决过程,以及提供可借鉴的经验教训。
6. 持续改进:品质管理部门需要对异常处理流程进行持续改进。
质量检验管理制度
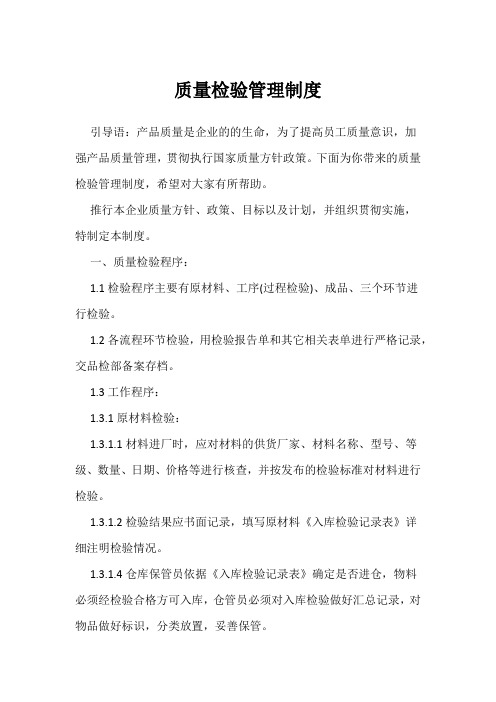
质量检验管理制度引导语:产品质量是企业的的生命,为了提高员工质量意识,加强产品质量管理,贯彻执行国家质量方针政策。
下面为你带来的质量检验管理制度,希望对大家有所帮助。
推行本企业质量方针、政策、目标以及计划,并组织贯彻实施,特制定本制度。
一、质量检验程序:1.1检验程序主要有原材料、工序(过程检验)、成品、三个环节进行检验。
1.2各流程环节检验,用检验报告单和其它相关表单进行严格记录,交品检部备案存档。
1.3工作程序:1.3.1原材料检验:1.3.1.1材料进厂时,应对材料的供货厂家、材料名称、型号、等级、数量、日期、价格等进行核查,并按发布的检验标准对材料进行检验。
1.3.1.2检验结果应书面记录,填写原材料《入库检验记录表》详细注明检验情况。
1.3.1.4仓库保管员依据《入库检验记录表》确定是否进仓,物料必须经检验合格方可入库,仓管员必须对入库检验做好汇总记录,对物品做好标识,分类放置,妥善保管。
1.3.2工序检验(过程检验):1.3.2.1生产员工接受到生产任务的同时,必须要了解产品的型号、规格、数量、设计图纸以及工艺要求,按要求生产。
不能随便改变流程和要求。
1.3.2.2生产人员领取材料时,注意观察材料是否合格。
未经检验或检验不合格的材料,车间不得投入生产使用,并及时反馈。
1.3.2.3机具车间主要原材料上总装线前必须100%全检。
1.3.2.4制造部、产品检测部负责对各工序的质量进行控制和监督,按照产品工序质量检验要求进行检验和监督。
对各工序进行巡查和抽样检查,并作好记录。
1.3.2.5各工序生产人员严格进行首检、自检、交接检,如发现质量问题,立即停止生产,及时上报有关负责人,进行检验隔离,作好工序检验记录,保证各工序生产质量。
1.3.3成品检验1.3.3.1产品组装完成后,将成品放至待检验区,质检员按照成品质量标准及检测方法进行检验。
品检部随着成品的生产批次,随出随检。
1.3.3.2成品全部检验,检验结果要求书面记录,填写“成品检验记录表”,并出具检验结论。
产品质量检验管理程序(含流程图)
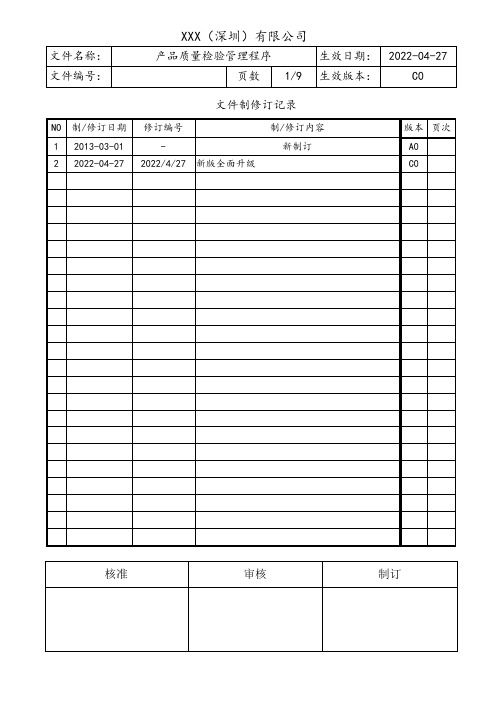
文件制修订记录1.0目的为了有效测量与监控产品从进料、制程、成品及出货各阶段检验作业能始终符合产品工程规范的各项要求。
2.0范围:适用于品管IQC、IPQC、QA过程作业。
3.0权责:3.1品管部:负责各阶段品质检验的执行、标识、追溯的管理、实际验货。
3.2工程部:产品作业标准的制定与检查。
3.3生产部:依生产计划、工程标准、验收标准执行生产作业。
3.4业务部:依订单需求验收出货数量。
3.5资材部:采购物料的外部联络。
4.0定义:无5.0作业内容:5.1进料检验5.1.1收料5.1.1.1供应商依据采购订单交货到公司仓库。
5.1.1.2仓管依据采购订单核对送货单是否一致,如若不符则退货并要求供应商重新交货,符合则点收数量并开出[进货单]。
5.1.1.3仓管将[进货单]连同要求供应商提供的相关文件(如材质报告、检验报告、测试报告等)交品管部,通知IQC进行检验。
5.1.1.4检验参照依据AQL表或依客户端需求作抽样检验。
5.1.1.5品管部IQC接到[进货单]后对供应商所提供的文件进行验证,(有法规环保类要求的产品必须依客户指定或经国家认可有检测能力机构出具的测试报告,如“SGS报告”等);品管部可以根据批量大小、价值贵重程度来对供应商所提供产品的材质进行一次确认。
5.1.1.5下列几项物料必须由品管部进料检验:a)生产性原材料。
b)外发加工产品。
c)包装材料等。
5.1.2需应用下列一种或多种方法进行验收、检验5.1.2.1接收检验及测试:a)核对材质证明(限自购原材料,样品或来料加工产品可不需要提供材质证明),核对供应商提供的相关文件。
b)依《检验标准书》逐项检验与填写[进料检验报告],无《检验标准书》时,依图面求或样板检验,检验结果可直接记录于[进料检验报告]上。
c)凡属客户提供来料进行加工,如无图面,依据客户提供的规格进行检验;如既无规格又无图面,IQC只针对其外观进行检验并记录于[进料检验报告]上。
- 1、下载文档前请自行甄别文档内容的完整性,平台不提供额外的编辑、内容补充、找答案等附加服务。
- 2、"仅部分预览"的文档,不可在线预览部分如存在完整性等问题,可反馈申请退款(可完整预览的文档不适用该条件!)。
- 3、如文档侵犯您的权益,请联系客服反馈,我们会尽快为您处理(人工客服工作时间:9:00-18:30)。
序言本标准按MIL-STD-105E标准进行作业,本大纲如在执行过程中发现明显问题请联系编写人员进行核准。
一、目的明确各工序品质部员工明确如何作业、职责范围、如何处理品质异常、预防品质异常产生、提升公司产品质量、降低客户投诉。
二、适用范围品质部所有员工,此大纲内容可按公司状态及条件择取应用。
三、员工规范要求1、遵守公司各项规章制度,按时上下班。
2、工作时遵守三按两遵守内容:按流程作业、按文件作业、按指导书作业;遵守劳动纪律、遵守工艺纪律。
3、做好办公位的5S与下班后的5关工作:关电、关电机、关空调、关门窗、关水。
四、使用工具万用表、积分球、光色分布测试仪、高压仪、漏电电流测试仪、接地电阻测试仪、亮度计、灰度计、LCR电桥、卷尺、钢尺、角尺、塞尺、千分尺、放大镜、各类产品使用冶具、刀片等、高低温测试仪、盐雾测试仪。
五、术语解释AQL:ACCEPTANCE QUALITY LIMIT接收质量限的缩写,即当一个连续系列或批次被提交检验时,可允许的最差过程平均质量水平。
QA: QUALITY ASSURANCE,中文意思是“品质保证”,其在ISO8402:1994中的定义是“为了提供足够的信任表明实体能够满足品质要求,而在品质管理体系中实施并根据需要进行证实的全部有计划和有系统的活动”。
有些推行ISO9000的组织会设置这样的部门或岗位,负责ISO9000标准所要求的有关品质保证的职能,担任这类工作的人员就叫做QA人员。
QE: Quality Engineer(品质工程师)。
QC: 即英文QUALITY CONTROL的简称,中文意义是品质控制,其在ISO8402:1994的定义是“为达到品质要求所采取的作业技术和活动”。
有些推行ISO9000的组织会设置这样一个部门或岗位,负责ISO9000标准所要求的有关品质控制的职能,担任这类工作的人员就叫做QC人员。
PE: 制程工程师简称PE制程工程师简称PE。
NG: NG的全称就是NO GOOD(不好;无用的,没有价值的;次品)。
OK: 好的;认可;同意。
SOP: 是标准操作程序(Standard Operating Procedure) 的英文首字母缩写。
IQC: Incoming Quality Control意思为来料质量控制.目前IQC的侧重点在来料质量检验上,来料质量控制的功能较弱.IQC的工作方向是从被动检验转变到主动控制,将质量控制前移,把质量问题发现在最前端,减少质量成本,达到有效控制,并协助供应商提高内部质量控制水平。
MRB: 全称是Material Review Board,中文意思是材料审查会议。
它是针对所有检验工作站发现产品异样状态暂时不能确定是否为缺陷的一种处理办法。
这里的工作站包括进料检验,过程检验,出货检验以及客户退回的产品。
根据不确定缺陷发现的位置,MRB会议可由不同的人召集。
SQE: 供货商管理工程师(Supplier Quality Engineer)。
BOM:物料清单( Bill of Material BOM)。
SPC:是Statistical Process Control的简称统计过程控制。
它是一种借助数理统计方法的过程控制工具。
它对生产过程进行分析评价,根据反馈信息及时发现系统性因素出现的征兆,并采取措施消除其影响,使过程维持在仅受随机性因素影响的受控状态,以达到控制质量的目的。
CPK:Complex Process Capability index 的缩写,是现代企业用于表示制程能力的指标。
制程能力强才可能生产出质量、可靠性高的产品。
PMC:Product Material Control 生产控制或生产管制(台、日资公司俗称生管)主要职能是生产的计划与生产的进度控制。
IPQC: In Put Process Quality Control中文意思为制程控制,是指产品从物料投入生产到产品最终包装过程的品质控制。
MIL-STD-105E II 抽样标准:MIL-STD-105E抽样计划又称计数值的调整型抽样计划,二次大战期间美军军方采购军需武器装备时,对于供货商均以验收检验、制程检验、产品检验、出货检验等方式进行严格的检验以确保武器装备的品质,但由于产品与种类的急遽增多,且制程日益复杂庞大,先前的监督检验制度无法因应此同一趋势,而改用稽查检验方式所开发出来的抽样计划。
严重品质特性 Critical characteristic:该特性不符合要求时,则在使用与维护的过程中将造成人员危害或不安全。
关键不合格件 Critical nonconforming unit:不符合严重品质特性要求的不合格件,不符合事项中包含一项以上的重要品质特性。
主要品质特性 Major characteristic:该特性不符合要求时,将导致产品失效或者降低使用性。
主要不合格件 Major nonconforming unit:符合所有严重品质特性,但不符合主要品质特性要求的不合格件,不符合事项中包含一项以上的主要品质特性。
次要品质特性 Minor characteristic:该特性若不符合要求时,不会造成产品失效或者降低产品使用性。
次要不合格件 Minor characteristic unit:符合关键与主要品质特性,但不符合次要品质特性的不合格件,不符合事项中包含一项以上的次要品质特性。
生产期间 Production interval:在同一生产期间,其产品品质必须具有均一性,通常属常态性偏移,一般以单班生产的时间为定义,但亦可将生产期间订为一天(最大值不超过一天),期间所产生偏移量的改变,并不影响产品品质。
品质计划 Quality program:产品从研发到生产期间,利用成本分析手法有效的规划、组织及管理各项活动或计划,使产品达成品质目标。
六、品质系统管理要求品质系统的建立首先要要求供应商应建立以预防为主的品质系统,除了当作另一个可接受的方法外,亦展示供应商持续不断品质改进的决心。
再者要求公司全员参与全员了解,过程需要技术人员要进行大量实验。
1、影响品质的工作者必须了解品质系统的运作程序。
2、产品必须符合或超越顾客需求。
3、强调预防性的过程差异分析与不良率分析。
4、当疵病发生时,必须立即寻找失效的产生原因与疵病来源,并且采取有效的纠正措施。
5、使用统计分析方法与问题解析手法,用以降低过程变异量,改善过程能力与产品品质。
6、保存记录,用以证实品质计划与过程控制的有效性。
7、利用制造程序图规划重要控制点,用以阻止或侦测疵病之产生。
8、过程不良原因的分析工具,如PDCA 循环(Plan-Do-Check-Action)、FMEA(Failure Modes andEffects Analysis)、柏拉图分析(Plato Analysis)及要因分析(Cause and Effect Analysis)等。
9、过程改善过程的评估工具,如趋势分析、品质成本、生产效率、不良品率及6个标准差(6-sigma)的能力。
10、利用实验计划,降低变异源产生之机率,改善生产力。
11、确认过程控制技术的使用范围,如统计过程品管(SPC)、自动化、量具、预防保养、目视检验等。
12、过程控制计划(Process control plan)必须包括SPC。
13、通过资料分析,显示供应商过程控制措施是有效性的。
14、根据工作的需要,执行适宜的教育训练。
15、确认各单位在SPC 相互作用上的权责与工作内容。
16、使用控制图之前,必须先行确定每次抽样数与抽样频率,并建立修正控制界线的作业程序与律定超出控制范围的准则。
17、确认所指定品质特性的关键参数,并找出影响关键参数的生产程序。
18、律定过程改进的权责,对纠正措施进行追踪,直至失效原因被消除为止。
19、执行量测系统分析(MSA Measurement System Analysis),了解量仪具的变异量。
包括使用控制图,利用记录与纠正及预防措施,执行过程能力分析(如 CPK),或通过过去统计资料进行趋势分析,最后则100%检验。
七、岗位技能要求1、技能要求质检员:1、熟悉公司的工艺工序、工作原理与机理,具备亲自动手操作能力。
2、熟练办公软件的基本操作。
3、熟练掌握公司产品及生产工艺技术应用方面的知识。
ISO9001、TS16949等质量管理体系的运行与应用能力;熟悉国际质量体系专业知识。
4、工作态度认真,积极负责,具有较强的创新意识。
品质技术员:熟悉公司的ISO规定;清楚品质的基本理论知识;检查仪器使用的方法;了解产品的原理及制作工序与检查方法;善于人际沟通。
品质工程师:1、熟悉公司的工艺工序、工作原理与机理,具备亲自动手操作能力。
2、熟练掌握公司产品及生产工艺技术应用方面的知识。
3、ISO9001、TS16949等质量管理体系的运行与应用能力;熟悉国际质量体系专业知识。
4、从事该行业的各种标准、IEC,GB,ISO等产品质量标准等品质标准的判断能力。
5、CPAR、PDCA、TS五大工具(APQP&CP、FMEA、MSA、SPC、PPAP)、品质七大手法等品质改善工具的运用能力。
6、具有较强的学习、分析、理解、沟通和协调能力。
7、工作态度认真,积极负责,具有较强的创新意识。
8、良好的英文阅读与理解能力。
2、各岗位职责质检员:根据检验标准(指导书\文件),对每批次产品进行检验或抽检,做好检验记录,汇总后反馈给上级;对工厂产品的质量工艺提出合理化建议;完成本部门领导交办的任务。
品质技术员:根据检验标准(指导书\文件),对每批次产品进行检验或抽检,做好检验记录,汇总后反馈给上级;对工厂产品的质量工艺提出合理化建议;完成本部门领导交办的任务。
对区域组的质检员进行工作安排,对质检员的异常进行筛选处理。
品质工程师:1、负责生产现场异常件质量问题的分析、判断,并做出处理的决定,提出纠正和预防措施,确保生产在受控、稳定的状态下进行;2、制订检验作业指导书,确保质量检验方法正确,检验结果可靠;3、负责对配套件和生产原料的进厂、入库验收工作、确保进厂物料符合规定要求,并对供应商进行质量监控;4、做好工序检验工作、半成品和成品检验工作,保证不合格品不流入下道工序和出厂,确保产品符合规定要求;5、运用统计技术,负责对现场质量问题进行收集、统计、分析和反馈;6、负责内部质量信息的传递、对外质量信息的反馈、顾客反馈问题的处理和改进工作;7、负责质量问题的跟踪解决,进行质量攻关,督促和协调各部门解决质量问题的进度;8、参与新产品、新工艺、新材料的试验工作,出具试验结果,并针对试验过程及结果提出质量改进建议;9、制定公司质量指标并进行统计、考核工作,确保公司质量目标的完成;10、负责公司质量体系的推动工作、公司内审、第三方审核工作,负责质量手册、程序文件的宣传、贯彻工作,建立、完善和维护分厂质量管理体系;制定质量控制计划,监控现场工艺执行情况,定期组织质量分析会。