第十篇 轴承下瓦开轴向槽消除油膜振荡
汽轮机轴承油膜油膜振荡介绍
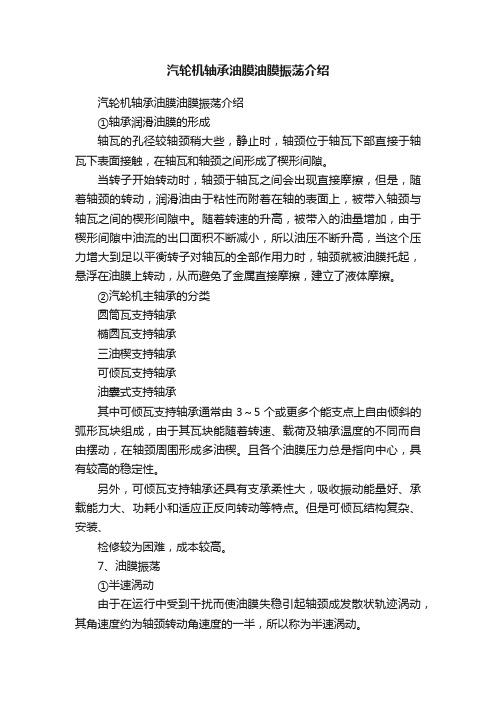
汽轮机轴承油膜油膜振荡介绍汽轮机轴承油膜油膜振荡介绍①轴承润滑油膜的形成轴瓦的孔径较轴颈稍大些,静止时,轴颈位于轴瓦下部直接于轴瓦下表面接触,在轴瓦和轴颈之间形成了楔形间隙。
当转子开始转动时,轴颈于轴瓦之间会出现直接摩擦,但是,随着轴颈的转动,润滑油由于粘性而附着在轴的表面上,被带入轴颈与轴瓦之间的楔形间隙中。
随着转速的升高,被带入的油量增加,由于楔形间隙中油流的出口面积不断减小,所以油压不断升高,当这个压力增大到足以平衡转子对轴瓦的全部作用力时,轴颈就被油膜托起,悬浮在油膜上转动,从而避免了金属直接摩擦,建立了液体摩擦。
②汽轮机主轴承的分类圆筒瓦支持轴承椭圆瓦支持轴承三油楔支持轴承可倾瓦支持轴承油囊式支持轴承其中可倾瓦支持轴承通常由3~5个或更多个能支点上自由倾斜的弧形瓦块组成,由于其瓦块能随着转速、载荷及轴承温度的不同而自由摆动,在轴颈周围形成多油楔。
且各个油膜压力总是指向中心,具有较高的稳定性。
另外,可倾瓦支持轴承还具有支承柔性大,吸收振动能量好、承载能力大、功耗小和适应正反向转动等特点。
但是可倾瓦结构复杂、安装、检修较为困难,成本较高。
7、油膜振荡①半速涡动由于在运行中受到干扰而使油膜失稳引起轴颈成发散状轨迹涡动,其角速度约为轴颈转动角速度的一半,所以称为半速涡动。
②油膜振荡及其特点典型的油膜振荡发生在汽轮机启动升速过程中,转子的第一阶临界转速越低,其支持轴承在工作转速范围内发生油膜振荡的可能性就越大,油膜振荡的振幅比半速涡动要大的多,转子跳动剧烈,往往不是一个轴承和相邻轴承,而是机组的所有轴承都出现强烈振动,机组附近有“咚咚”的撞击声,油膜振荡一旦发生,转子始终保持着等于临界转速的涡动速度,而不再随转速的升高而升高,这一现象成为油膜振荡的惯性效应。
所以遇到油膜振荡发生时,不能象过临界转速那样,借提高转速冲过去的办法来消除油膜振荡的产生:轴颈带动润滑油高速流动时,高速油流反过来激励轴颈,使其发生强烈振动的一种自激振动现象。
防止油膜振荡的措施

防止油膜振荡的措施为了预防和消除抽膜振荡,可以根据转子系统的实际情况采取以下若千措施:(1)消除油a振荡的诱发因素:①改善转子的平衡状态,限制振幅放大因子;②消除转子不对中故障。
限制低次谐波分蛋;③消除动静间除不均匀,限制非线性激振力.(2)改变轴承参数:①提高轴承比压,减小轴承宽度,抬高轴承标高,在下瓦中部开环形枯等,但不超过轴承允许的最大承载能力;②降低润滑油粘度,将枯度较高的油换成粘度较低的油,提高进油沮度.以不发生干雄徐、小地磅油质劣化为限;(3)选择合适的轴承形式:根据轴承类型和结构尺寸的不同,每种轴承有其稳定工作的范围。
一般认为各种轴承的稳定性从优到劣可按下列次序排列:可倾瓦,偏盆三油叶、对称三油叶、椭圆、三油楔、圆柱轴承。
(4)增加转了系统刚度,提高转子系统的临界转速.转子固有频率越高,发生油膜振荡的失稳转速也越高,系统失稳转速应在工作转速的125买以上。
其他常见典型故障1.转抽果纹导致转轴裂纹最重要的原因是高周期疲劳、低周期疲劳、蠕变和应力腐蚀开裂,此外也与转子工作环境中含有腐蚀性化学物质等有关,而大的扭转和径向载荷,加上复杂的转子运动.造成了恶劣的机械应力状态,最终也将导致轴裂纹的产生.裂纹在转子旋转的动态应力下,始终处于”开“和”闭”的周期变化过程中。
裂纹转子的监测和诊断方法有:(1)稳态响应法:对裂纹转子的监侧和诊断要着眼于各阶谐波分量幅值1X,2X和3X的大小以及防时间的变化。
1X.2X和3X分盆幅值随时间稼定增长的趋势表明转子可能存在裂纹。
(2)滑停法:此法将机组从工作转速滑降至零转速,在降速过程中测盆振动响应并进行谱分析。
若转子产生裂纹或裂纹有进一步的扩展,则在转速过临界及1/2,1/3临界转速时.振动响应将有明显的改变。
(3)溢度瞬间法;此法原理是快速降低燕汽温度.使转子表面产生拉伸的热应力.如果有裂纹存在,拉应力将使裂纹张开,使转子振动瞬间增大。
通过快速降温或快速升温的办法可以发现转子是否有裂纹.裂纹故障的特征为:〔1)各阶临界转速较正常时要小,尤其在裂纹严重时.(2)由于裂纹造成刚度变化且不对称.转子的共振转速扩展为一个区;(3)裂纹转子轴系在强迫响应时一阶分it的分散度比无裂纹时大,(4)转速超过临界转速后,一般各高阶请波振幅较未超过时小;(5)恒定转速下.各阶请波幅值1X,2X和3X及其相位不德定.且尤以2X突出;(6)裂纹引起刚度不对称,使转子动平衡发生困难.往往多次试重也达不到所要求的平衡精度。
汽轮发电机机组油膜振荡综合诊断与处理建议

汽轮发电机机组油膜振荡综合诊断与处理建议一、机组油膜振荡的主要原因1.机组结构与工作环境汽轮发电机机组具有复杂的结构和特殊的工作环境,机组内部存在着各种摩擦和振动,这些因素都会对机组油膜振荡产生影响。
2.润滑油机组润滑油的粘度、温度和油料质量等因素,都会对油膜振荡产生直接的影响。
如果润滑油的粘度过高或过低,都会导致机组油膜不稳定,从而引起振荡。
3.轴承磨损轴承在长时间工作过程中,难免会出现磨损和松动现象。
如果轴承运行时有松动,就会引起机组的振动,从而引起油膜振荡。
机组油膜振荡的检测方法很多,包括现场检测和实验室检测两种。
具体方法如下:1.现场检测现场检测是指利用现场技术手段,对机组进行振动、噪声等参数的测量和分析。
2.实验室检测实验室检测是指将机组的润滑油送到实验室进行检测。
实验室检测可以检测润滑油的粘度、杂质、酸值等物理和化学指标,进一步分析机组油膜振荡的原因和性质。
机组油膜振荡的处理方法应该根据具体情况进行综合分析和处理。
如果机组油膜振荡是由于润滑油的质量不好或者是油料粘度过低或过高引起的,就需要更换润滑油。
换一种合适的润滑油,可以很好地解决油膜振荡问题。
2.多次加油为了保证机组正常运行,可以进行多次加油。
多次加油可以确保机组内部的润滑油充足,避免机组因为润滑不良而引起的油膜振荡问题。
如果机组油膜振荡是由于轴承松动引起的,就需要更换轴承。
更换完好的轴承可以确保机组稳定运行,避免机组因为松动而导致的振荡问题。
1.定期检查机组油膜振荡问题的预防,最关键的是要做到定期检查。
定期检查可以发现机组问题的早期迹象,及时进行处理,避免问题不断扩大。
2.保养维护保养维护是预防机组油膜振荡问题的另一个重要方法。
机组的保养维护工作必须要做好,可以重点关注润滑油的保养、轴承的保养以及机组的清理和维护等。
综上所述,汽轮发电机机组油膜振荡对机组的运行稳定性和生产效益都会产生极大的影响。
因此,我们必须要注重机组油膜振荡的综合诊断和处理,并且加强管理,采取有效的预防措施,确保机组的正常运行和生产效益。
滑动轴承油膜振荡的原因和对策
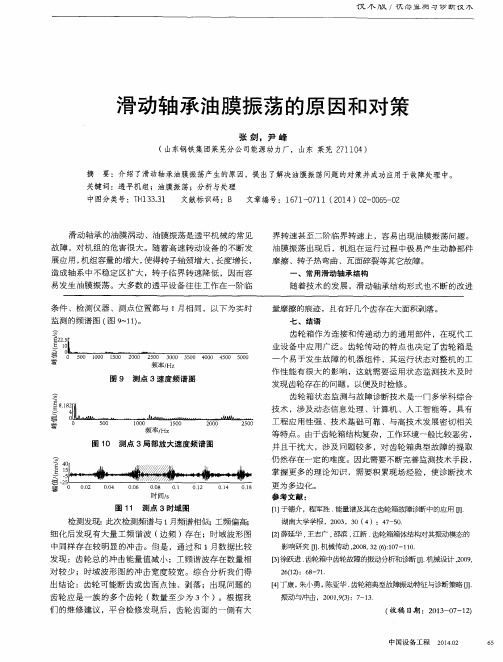
仅
小
/恹 忿 监
- ' 7
町仪 7 卜
滑 动轴承油膜振 荡的原 因和对 策
张 剑 。尹 峰
( 山东钢铁集 团莱 芜分公 司能源动力厂, 山东 莱芜 2 7 1 1 0 4)
摘 要:介绍 了滑 动轴承 油膜振 荡产 生的原因,提 出了解决 油膜振 荡 问题 的对策并成功应用 于故障处理 中。 关键词 :透平机组 ;油膜振 荡;分析 与处理
频率 / H z
个易 于发 生 故障 的机 器 组件 ,其 运行 状 态对 整机 的 工
图 9 测点 3速 度 频 谱 图
1  ̄8i 8 2 5 4 j 型
.
作性 能 有很 大 的影 响 ,这就 需要 运 用状 态监 测技 术 及时 发现 齿轮存 在 的问题 ,以便 及时检 修 。 齿轮 箱状 态 监测 与故 障诊 断技 术 是一 门多 学科 综合 技术 ,涉 及 动态 信 息处 理 、计 算机 、人 工智 能 等 ,具有
[ 3 ] 徐跃进 . 齿轮 箱中齿轮故障 的振动分析和诊 断 U 】 _ 机 械设计 , 2 0 0 9
2 6 ( 1 2 ) :6 8 — 7 1 .
[ 4 】 丁康 , 朱小 勇, 陈亚华 . 齿轮箱典型故障振动特征与诊断策略 Ⅱ 】 . 振动与冲击 ,2 0 0 1 , 9 ( 3 ) :7 - 1 3 . ( 收 稿 日期 :2 0 1 3 - 0 7 - 1 2 )
油膜振荡实验报告

一、实验目的本次实验旨在通过模拟油膜振荡现象,探究油膜振荡的产生机制、影响因素以及危害,为实际工程应用中预防和控制油膜振荡提供理论依据。
二、实验原理油膜振荡是指旋转轴颈在滑动轴承中带动润滑油高速流动,在一定条件下,高速油流反过来激励轴颈,产生一种强烈的自激振动现象。
其主要原因是在轴颈与轴瓦之间的间隙中形成的油膜,其承载力与外载荷平衡时,轴颈处于平衡位置;当转轴受到某种外来扰动时,轴颈中心就会在静平衡位置附近发生涡动,其振动频率约为转子回转频率的一半,称为半速涡动。
当转速达到比第一阶临界转速的2倍稍高以后,半速涡动的涡动速度与转轴的第一阶临界转速相重合,产生共振,振动幅度剧烈增加,称为油膜振荡。
三、实验仪器与材料1. 实验台:用于放置实验装置,确保实验过程稳定;2. 轴承:模拟实际工程中的轴承,提供支撑和承载;3. 轴颈:模拟实际工程中的轴颈,承受油膜振荡带来的振动;4. 润滑油:模拟实际工程中的润滑油,提供润滑和承载;5. 传感器:用于测量振动信号;6. 数据采集系统:用于实时采集振动数据;7. 电脑:用于数据处理和分析。
四、实验步骤1. 将轴承安装在实验台上,确保轴承与轴颈的配合精度;2. 将润滑油加入轴承中,确保油膜形成;3. 启动轴颈,逐渐提高转速,观察振动信号;4. 记录不同转速下的振动数据;5. 分析振动数据,判断是否存在油膜振荡现象;6. 通过改变轴承间隙、润滑油种类、转速等参数,研究油膜振荡的影响因素。
五、实验结果与分析1. 实验结果表明,当转速达到一定值时,振动信号出现约转速频率0.35~0.49倍的频率成分,表明半速涡动现象的存在;2. 当转速继续升高,半速涡动的频率成分保持不变,说明半速涡动现象稳定;3. 当转速达到比第一阶临界转速的2倍稍高时,振动幅度急剧增加,表明油膜振荡现象发生;4. 通过改变轴承间隙、润滑油种类、转速等参数,发现轴承间隙过小、润滑油粘度过高、转速过高等因素容易引发油膜振荡。
汽轮发电机机组油膜振荡综合诊断与处理建议

汽轮发电机机组油膜振荡综合诊断与处理建议汽轮发电机机组油膜振荡是指在润滑油膜的作用下,轴承产生的振动现象。
油膜振荡对机组的安全运行和设备的寿命造成了严重威胁,因此如何进行综合诊断和有效处理是非常重要的。
本文将对汽轮发电机机组油膜振荡的综合诊断与处理进行建议。
一、油膜振荡的诊断1. 振动检测振动检测是最直观的诊断手段,通过振动传感器对轴承振动情况进行监测。
正常情况下,振动应该是稳定的,若出现频繁的振动异常,则说明可能存在油膜振荡问题。
2. 油膜监测油膜监测是通过监测轴承的润滑油膜情况来判断是否存在振荡问题。
当润滑油膜不稳定时,往往会引起振动异常。
3. 温度检测由于油膜振荡会导致摩擦增加,从而使轴承温升,因此可以通过监测轴承温度来初步判断是否存在振荡问题。
4. 润滑油分析通过对润滑油的化学成分和污染物进行分析,可以了解润滑油是否存在异常情况,从而判断是否存在振荡问题。
二、油膜振荡的处理建议1. 调整轴承间隙轴承间隙对油膜的稳定起着至关重要的作用,因此可以通过调整轴承间隙来减轻油膜振荡的情况。
2. 改进润滑系统改进润滑系统可以采用更高性能的润滑油、改进润滑油供给系统等方式,从根本上解决油膜振荡的问题。
3. 增加油膜稳定性可以通过增加油膜的黏性或者加强润滑油的供给,来增加油膜的稳定性,减轻振荡的出现。
4. 检修轴承如果油膜振荡已经严重影响机组的运行,建议进行轴承的检修,彻底清洁和更换润滑油,并对轴承进行维护保养。
5. 定期维护及时清理设备表面和检查润滑油情况,可以防止因为摩擦增加而导致油膜振荡。
汽轮发电机机组油膜振荡是一种常见但危害严重的问题,需要及时进行综合诊断和处理。
合理的诊断手段和处理建议可以有效的帮助企业解决油膜振荡问题,提高机组的可靠性和安全性。
也需要加强对机组设备的定期维护和维修工作,减少油膜振荡的发生。
油膜振荡分析与处理
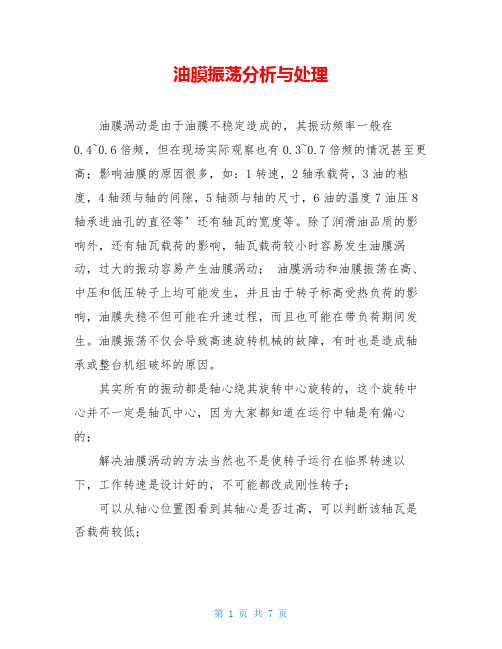
油膜振荡分析与处理油膜涡动是由于油膜不稳定造成的,其振动频率一般在0.4~0.6倍频,但在现场实际观察也有0.3~0.7倍频的情况甚至更高;影响油膜的原因很多,如:1转速,2轴承载荷,3油的粘度,4轴颈与轴的间隙,5轴颈与轴的尺寸,6油的温度7油压8轴承进油孔的直径等’还有轴瓦的宽度等。
除了润滑油品质的影响外,还有轴瓦载荷的影响,轴瓦载荷较小时容易发生油膜涡动,过大的振动容易产生油膜涡动;油膜涡动和油膜振荡在高、中压和低压转子上均可能发生,并且由于转子标高受热负荷的影响,油膜失稳不但可能在升速过程,而且也可能在带负荷期间发生。
油膜振荡不仅会导致高速旋转机械的故障,有时也是造成轴承或整台机组破坏的原因。
其实所有的振动都是轴心绕其旋转中心旋转的,这个旋转中心并不一定是轴瓦中心,因为大家都知道在运行中轴是有偏心的;解决油膜涡动的方法当然也不是使转子运行在临界转速以下,工作转速是设计好的,不可能都改成刚性转子;可以从轴心位置图看到其轴心是否过高,可以判断该轴瓦是否载荷较低;解决油膜涡动,一个是检查油的质量使其合格,保证油温在设计范围内,还有就是增加该轴瓦的载荷,比如抬高轴瓦,增加轴瓦的轴径比等。
油膜涡动:油膜的楔形按油的平均流速绕轴瓦中心运动的现象称为油膜涡动,因其平均速度为轴颈圆周速度的一半,故又称为半速涡动。
机理:油润滑滑动轴承工作时,以薄的油膜支承轴颈。
在轴瓦表面的油膜速度为零(轴瓦静止),而在轴颈表面的油膜速度与轴颈表面相同(轴颈高速旋转)。
因此,不论在圆周上的任何剖面,油膜的平均速度均为轴颈圆周速度的一半。
轴颈高速旋转时,油膜厚度随楔形变化,但油的平均流速却相对不变。
由于油的不可压缩性,多出的油将从轴承两端流出,或者油膜的楔形按油的平均流速绕轴瓦中心运动。
如何诊断油膜涡动引起的振动?诊断油膜涡动可从以下的振动特征来判断:(1)油膜涡动的特征频率为略小于转子转速的1/2,并随转速的升高而升高,常伴有1倍频;(2)振动较稳定,次谐波振幅随工作转速的升高而升高;(3)相位较稳定;(4)轴心轨迹为双环椭圆,进动方向为正进动;(5)对轴承润滑油的温度、粘度和压力变化敏感。
大型汽轮机气流激振问题的分析与处理
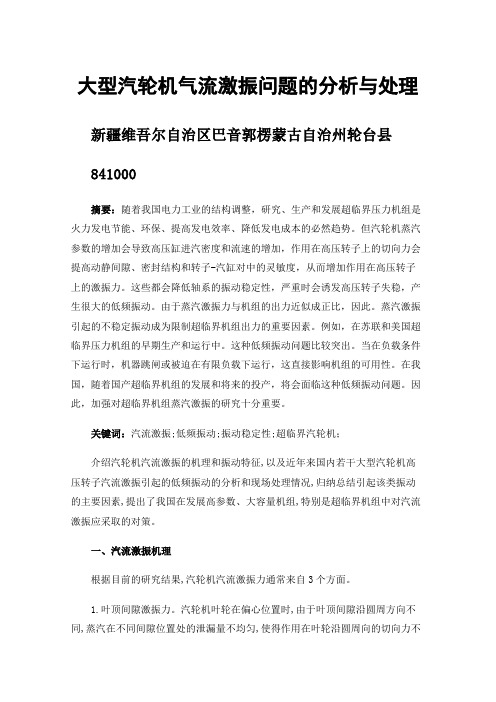
大型汽轮机气流激振问题的分析与处理新疆维吾尔自治区巴音郭楞蒙古自治州轮台县841000摘要:随着我国电力工业的结构调整,研究、生产和发展超临界压力机组是火力发电节能、环保、提高发电效率、降低发电成本的必然趋势。
但汽轮机蒸汽参数的增加会导致高压缸进汽密度和流速的增加,作用在高压转子上的切向力会提高动静间隙、密封结构和转子-汽缸对中的灵敏度,从而增加作用在高压转子上的激振力。
这些都会降低轴系的振动稳定性,严重时会诱发高压转子失稳,产生很大的低频振动。
由于蒸汽激振力与机组的出力近似成正比,因此。
蒸汽激振引起的不稳定振动成为限制超临界机组出力的重要因素。
例如,在苏联和美国超临界压力机组的早期生产和运行中。
这种低频振动问题比较突出。
当在负载条件下运行时,机器跳闸或被迫在有限负载下运行,这直接影响机组的可用性。
在我国,随着国产超临界机组的发展和将来的投产,将会面临这种低频振动问题。
因此,加强对超临界机组蒸汽激振的研究十分重要。
关键词:汽流激振;低频振动;振动稳定性;超临界汽轮机;介绍汽轮机汽流激振的机理和振动特征,以及近年来国内若干大型汽轮机高压转子汽流激振引起的低频振动的分析和现场处理情况,归纳总结引起该类振动的主要因素,提出了我国在发展高参数、大容量机组,特别是超临界机组中对汽流激振应采取的对策。
一、汽流激振机理根据目前的研究结果,汽轮机汽流激振力通常来自3个方面。
1.叶顶间隙激振力。
汽轮机叶轮在偏心位置时,由于叶顶间隙沿圆周方向不同,蒸汽在不同间隙位置处的泄漏量不均匀,使得作用在叶轮沿圆周向的切向力不相等,就会产生一作用于叶轮中心的横向力(合力),也称为间隙激振力。
该横向力趋向于使转子产生自激振动。
在1个振动周期内,当系统阻尼消耗的能量小于该横向力所做的功,这种振动就会被激发起来。
叶顶间隙不均匀产生的间隙激振力大小与叶轮的级功率成正比,与动叶的平均节径、高度和工作转速成反比。
因此,间隙激振容易发生在大功率汽轮机及叶轮直径较小和短叶片的转子上,即大型汽轮机的高压转子上。
- 1、下载文档前请自行甄别文档内容的完整性,平台不提供额外的编辑、内容补充、找答案等附加服务。
- 2、"仅部分预览"的文档,不可在线预览部分如存在完整性等问题,可反馈申请退款(可完整预览的文档不适用该条件!)。
- 3、如文档侵犯您的权益,请联系客服反馈,我们会尽快为您处理(人工客服工作时间:9:00-18:30)。
轴承下瓦开轴向槽治理油膜振荡的方法研究黄海舟1,2徐华1朱均1(1西安交通大学润滑理论及轴承研究所西安,710049)(2湖北省电力试验研究院武汉,430077)摘要:对汽轮发电机组轴承油膜振荡的治理方法进行了试验研究,实验结果表明:现场对轴承下瓦开轴向槽,能使轴承失稳转速提高而保证温升增加不多,且工艺简单易行,比现场调整轴承载荷的方法更能取得振动治本的效果。
关键词:汽轮发电机组;油膜振荡;轴瓦开槽SS热电厂NO.7汽轮发电机组,汽轮机(背压式)和发电机型号分别为B25-90/10-1和QF2-25-3,北京重型电机厂制造,1986年投产。
机组于1993年、1995年和1999年3次发生油膜振荡,引起发电机后轴承及整个轴系强烈振动,改变运行参数一般不能抑制振动。
机组前两次发生油膜振荡时,停机检修主要是采取逐步增大轴承载荷,每次使振动恢复正常均要经过两次以上的检修反复,经济损失可观。
目前,国内与本机组同型的在役机组有20多台,据制造厂反映无一例发生过油膜振荡。
从历史经验看,适当增大轴承载荷可以在一段时间内消除油膜振荡。
如1995年曾两次尝试调整轴承载荷:第一次将4号轴承标高抬高0.05mm、顶隙减小为1.6‰D、接触角减小为55︒,不能抑制油膜振荡;而第二次将4号轴承标高抬高0.5mm、将发电机对轮中心比原始抬高0.19mm,油膜振荡一时得到控制,直至机组顺利运行了4年。
实践证明,仅靠增大轴承载荷不能保证机组在下次检修后油膜振荡不再发生,而及时换用稳定性更好的轴承,对现场往往不很实际。
因此,当油膜振荡在1999年8月、机组小修后启动再度出现后,对发电机后轴承采取了下瓦开槽和抬高安装标高的综合措施,提高了轴承稳定性,消除了油膜振荡。
带大负荷运行时各轴承座振动(以下简称瓦振)均小于30 μm 。
本文针对所试验的机组1999年接连出现油膜振荡的问题,介绍了轴系载荷的调整措施,重点阐述了现场对轴承下瓦开轴向槽、从治本上消除油膜振荡的途径。
1 机组油膜振荡的现象特征及原因分析本机组汽轮机和发电机的前、后支撑轴承编号依次为1~4号轴承,励磁机只有一个支撑轴承。
发电机 3、4号轴承为4垫块、固定式圆柱轴承,其中4号轴承直径D=240 mm,宽度L=240 mm,设计比压Pm=1.15 MPa,采用32号汽轮机润滑油。
4号轴承为水平中分面两侧进油,一部分油在轴颈与上瓦内表面中间的宽度为120 mm的环向油槽之间经过,冷却轴颈,并使油流易于向两侧扩散至整个轴瓦表面;另一部分油在轴颈与下瓦之间经过后向轴瓦两侧泄出。
1.1 振动现象与特征1999年7月28日至8月4日,机组进行了一次小修。
与振动有关的检修工作只有:为核准轴向位移发生器零位撬动过4号轴承前转子上的台肩,处理了4号轴承油档漏油问题,调整了5号轴承紧力,对冷油器清洗后重新滤油。
轴系中心数据未作调整。
机组启动后,8月6日4号轴承第一次发生强烈振动,水平瓦振超过170 μm,是时运行工况为有功12.5MW、无功18MVar、润滑油温度39.7 ︒C 。
运行人员将有功降到10.3MW、无功降到10MVar、润滑油温度升到44.4 ︒C,大幅振动消失。
而将有功升到10.6MW时,振动再次出现,以后不论怎样调整运行工况都不能控制振动,机组被迫停机检查。
停机对4号轴承作了翻瓦检查,将轴瓦前后不均匀的顶隙0.43~0.56 mm减小为0.43 mm,瓦盖紧力适当增加。
8月13日再次开机,机组启动过程中振动尚好,但次日带负荷运行中再次出现了剧烈的振动。
如在有功15.9MW和较高的润滑油温度41.7 ︒C时,4号水平瓦振达到153 μm。
经数小时工况调整,降低振动无效果,机组不得不再次停机检查、检修。
第二次发生振动时,电厂采用随机配备的振动监测在线系统获得了部分有意义的振动数据。
由于4号轴承轴振测点损坏,从临近轴承振动和4号垂直瓦振故障信息中,分析了振动原因。
表1是在线系统采集的列表数据,半频分量振动占通频振动比例较高,而高频分量较小。
表2是现场测得的瓦振数据。
图1是在线系统给出的2X、3X轴振的三维谱图,低频振动中心频率约为22.8Hz,尤其在3X轴振三维谱图上22.8Hz低频振动分量已超过其基频振动值。
表1 油膜振荡发生时在线系统的振动谱分量列表数据 /μm谱分量/测点2X轴振3X轴振3垂直瓦振4垂直瓦振通频56 287 45 520.5x 6 54 6 81.0x 27 63 15 192.0x 6 11 2 43.0x 2 4 1 2表2 油膜振荡发生时现场瓦振数据/ μm方向/轴承号 1 2 3 4 5垂直 5 11 30 59 10水平15 15 36 170 19轴向17 10 10 28 22图1 油膜振荡发生时2X、3X轴振三维谱图2.2 振动原因分析2.2.1 运行中轴承载荷降低引起油膜振荡经查实,本机组历史上三个年份发生油膜振荡的季节,均是7-8月间的高温季节。
从振动的幅值分析,4号轴承是油膜振荡发起部位并波及整个轴系。
其实质是运行中4号轴承载荷发生了较大降低,而直接原因或外因是2、3号轴承箱的温度过高。
从本机组的轴系结构分析,2、3号轴承共用一个轴承箱,每到炎热季节,由于对轮的鼓风生热和汽机轴封蒸汽泄漏,轴承箱较细的排气管排不及箱体内的热量和油烟,轴承箱的外表温度一般高达60℃以上, 2、3号轴承因热影响标高升高,导致4号轴承载荷减轻,容易发生失稳。
2.2.2 4号轴承抗失稳能力较弱4号轴承为上瓦开周向槽的圆柱轴承,槽宽比为50%,轴承预载荷降低,本身抗失稳能力较弱,这是4号瓦每次首先发生油膜振荡的内因。
3 机组油膜振荡治理措施研究据前述分析,要从提高4号轴承稳定性方面入手,治理机组油膜振荡。
3.1 调整轴系中心及轴承载荷调整轴系中心增大轴承载荷抑制油膜振荡,是现场最常见的作法。
从理论上讲,提高轴承承载能力系数,将增大轴承偏心率,提高失稳转速。
对4号轴承初步计算表明[1],当承载能力系数由0.763变到1.15,偏心率由0.25变到0.50,失稳转速增大约8 % 。
本次轴系调整,将3、4和5号轴承标高分别抬高0.12mm、0.50mm和0.92mm,汽轮机轴承不动,形成发电机比汽轮机对轮中心高约0.1mm(低发对轮错位值规范为≤0.02mm),3、4号轴承载荷有不同程度增加。
3.2 轴承下瓦开轴向槽3.2.1 开槽方案的拟定在不更换轴承的前提下,现场适当改变轴瓦结构、提高轴承的抗失稳能力有多种方法,常见的有:(1)调整轴瓦间隙,如减小顶隙、加大侧隙、扩大油楔深度、扩大阻油边间隙;(2)减小轴瓦长径比,如阻油边内移、截短轴瓦,在轴瓦上开设沟槽、加油坝等。
其实质是增大轴承的相对偏心率和降低润滑油在轴承中的周向平均流速。
由于4号轴承供油结构的特点,没有采用最初提出的将阻油边内移的方案,而最终采取在4号轴承下瓦宽度中间、周向相隔56︒位置、对称地开设了两个轴向槽,槽的尺寸:长⨯宽⨯深=40⨯25⨯1.8(mm)。
由于这一作法在汽轮发电机组轴承故障的现场处理中报道较少,本次选取的开槽部位及槽尺寸,出于对瓦温不利影响的考虑,偏于保守。
3.2.2 开槽方案计算分析用有限元法计算了4号轴承下瓦开轴向槽后,压力分布和失稳转速的变化。
发电机转子重量13500kg,计算中轴承载荷按平分转子重量考虑,轴瓦间隙取实际值。
图2给出了下瓦开轴向槽后轴承宽度中心的压力分布。
计算表明:(1)轴承下瓦开轴向槽后,轴向槽部位无量纲油膜压力图2 4号轴承下瓦开轴向槽后宽度中心的压力分布将基本建立不起动压,使轴承承载力降低,最小油膜厚度减小,而偏心率和油膜刚度增加。
(2)轴向槽还会使润滑油周向流动平均速度降低。
这两个有利因素将使轴承的失稳转速提高。
通过对失稳转速进行搜索计算,轴承失稳转速大于4000r/min。
(3)4号轴承下瓦开轴向槽后,由于上瓦周向槽的存在,计算温升只增加2-3℃。
3.3 轴承其它增稳措施检修还将4号轴承顶隙和单边侧隙分别调整为0.35mm和0.25mm,使轴瓦由园柱瓦变为有0.3的椭圆度,但由于上瓦环向油槽的存在和根据前两次的处理效果,此措施只会起辅助性作用。
4 效果验证1999年8月22日上述措施实施后机组启动,检测发电机轴承升速振动,确定发电机转子一阶临界转速为1350~1400 r/min。
显然,与8月14日4号轴承发生油膜振荡的故障频率一致。
机组整个升速和带负荷过程中,4号轴承及其它轴承低频分量振动消失,经过一个多月带大负荷观察,4号轴承水平瓦振稳定在30 μm以下,其它轴承振动也有改善,4号轴承及其它轴承回油温度正常,见表3数据。
表3 最终振动和回油温度(振动/ m,回油温度 /℃)4号轴承在下瓦开槽和抬高标高后,其轴承回油温度升高小于3 ℃,离报警温度还有较大的富余,故更好地根除油膜振荡,还可以将4号轴承下瓦的轴向槽适当加长、加宽和更接近接触区。
5 结束语(1)对于频发油膜振荡的机组,现场仅进行轴承载荷调整难以避免油膜振荡重演,而结合轴承结构改造可取得满意效果、勿需更换轴承。
(2)在轴承下瓦开轴向槽,可同时起到增大轴承相对偏心率和降低润滑油周向流动平均速度的作用,从而提高轴承的抗失稳能力,轴承金属温度升高很小。
(3)在所讨论的机组上至少有两次现场试验说明,对于上瓦具有宽环向油槽的圆柱轴承,仅改变轴承的椭圆度,对抑制油膜振荡效果不甚显著。
参考文献[1] 朱均,虞烈,龚汉声等.汽轮机径向滑动轴承性能计算(JB/Z 209-84). 北京:机械工业出版社,1986.[2] Cameron,A. The Principles of Lubrication. Longmans Green & Co.,1966.。