3.2.2 缩孔、缩松的形成及防止方法
铸件中缩孔与缩松的防止方法
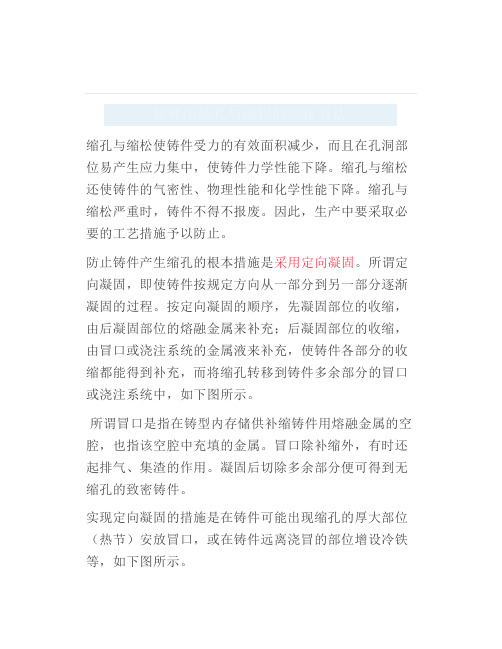
铸件中缩孔与缩松的防止方法缩孔与缩松使铸件受力的有效面积减少,而且在孔洞部位易产生应力集中,使铸件力学性能下降。
缩孔与缩松还使铸件的气密性、物理性能和化学性能下降。
缩孔与缩松严重时,铸件不得不报废。
因此,生产中要采取必要的工艺措施予以防止。
防止铸件产生缩孔的根本措施是采用定向凝固。
所谓定向凝固,即使铸件按规定方向从一部分到另一部分逐渐凝固的过程。
按定向凝固的顺序,先凝固部位的收缩,由后凝固部位的熔融金属来补充;后凝固部位的收缩,由冒口或浇注系统的金属液来补充,使铸件各部分的收缩都能得到补充,而将缩孔转移到铸件多余部分的冒口或浇注系统中,如下图所示。
所谓冒口是指在铸型内存储供补缩铸件用熔融金属的空腔,也指该空腔中充填的金属。
冒口除补缩外,有时还起排气、集渣的作用。
凝固后切除多余部分便可得到无缩孔的致密铸件。
实现定向凝固的措施是在铸件可能出现缩孔的厚大部位(热节)安放冒口,或在铸件远离浇冒的部位增设冷铁等,如下图所示。
所谓冷铁是指为增加铸件局部的冷却速度,在砂型、砂芯表面或型腔中安放的金属物。
图中所示铸件中可能产生缩孔的厚大部分不止一个,若仅靠顶部冒口,难以向底部凸台补缩,如果在该凸台的型壁上安放两个外冷铁,加快了该处的冷却速度,使厚壁凸台反而最先凝固,从而实现了由下而上的定向凝固。
定向凝固与逐层凝固是两个不同的概念。
定向凝固是指铸件各部分的凝固顺序;逐层凝固是指铸件某截面上的凝固顺序。
逐层凝固的合金表层先凝固,然后逐渐向铸件中心增厚,铸件中心最后凝固。
冒口的补缩通道能长时间保持畅通,有利于实现铸件的定向凝固。
对于纯金属、共晶成分的合金,工艺上一般都采用定向凝固的原则,来提高铸件的致密性。
相反,倾向于糊状凝固的合金,结晶的固体骨架较好地布满整个铸件的截面,使冒口的补缩通道堵塞,难以实现定向凝固。
铸钢件缩孔和缩松的形成与预防

F铸造oundry热加工热处理/锻压/铸造2011年第15期69铸钢件缩孔和缩松的形成与预防宁夏天地奔牛实业集团有限公司(石嘴山753001)王福京缩孔和缩松从本质上来说,是因为型内的金属产生收缩而引起的,但是不同种类的金属,其形成缩孔和缩松的机理有所不同。
1.产生机理从铸钢件角度来分析,钢液注满型腔后,由于型壁的传热作用,型内钢液形成自型壁表面至铸件壁厚中心温度逐渐升高的温度梯度。
随着型壁传热作用不断地进行,型内钢液温度不断降低。
当与型壁表面接触的钢液温度降至凝固温度时,铸件的表面就开始凝固,并形成一层固体状态的硬壳。
如果这时浇注系统已经凝固,那么硬壳内处于液体状态的钢液就与外界隔绝。
当型内钢液温度进一步降低时,硬壳内的钢液一方面因温度降低而产生液态收缩,另一方面由于硬壳的传热作用,使与硬壳接触的钢液不断结晶凝固,从而出现凝固收缩。
这两种收缩的出现,将使硬壳内钢液液面下降。
与此同时,处于固体状态的硬壳,也因温度的降低而产生固态收缩,对于铸钢件来说,由于液态收缩和凝固收缩的总和是大于固态收缩的,因此在重力作用下,硬壳内钢液液面将下降,并且与上部硬壳脱离接触。
随着型内钢液温度不断地降低和硬壳内钢液不断地凝固,硬壳越来越厚,而钢液越来越少。
当铸件内最后的钢液凝固后,铸件上部的硬壳下面就会出现一个孔洞,这个孔洞即为缩孔。
虽然凝固后的铸件自高温状态冷却至室温时,还将产生固态收缩,从而使整个铸件和其内部缩孔的体积稍有减小,但并不会改变缩孔体积与铸件体积的比值。
由于凝固层厚度的增加和钢液的减少是不断进行的,因而从理论上来说,缩孔的形状是漏斗状的。
并且因残存的钢液凝固时不能得到补缩,所以在产生缩孔的同时,往往也伴随着缩松的出现。
用肉眼能直接观察到的缩孔为宏观缩孔,而借助于放大镜或将断面腐蚀以后才能发现的缩孔为微观缩孔。
一般情况下,宏观缩孔可以用补焊的手段来解决,而微观缩孔就无法处理了,一般都是成片出现的微小孔洞。
缩孔和缩松及其控制方法

缩孔和缩松及其控制方法缩孔和缩松是在材料加工和制造过程中常见的问题,对于产品的质量和性能有着重要影响。
本文将分别介绍缩孔和缩松的概念、原因以及控制方法。
一、缩孔缩孔指的是材料加工或制造过程中产生的孔洞或空隙,一般是由于材料内部气体无法完全排除或者材料收缩不均匀而引起的。
缩孔问题会导致产品的力学性能下降、密封性能降低以及外观质量不佳等问题。
造成缩孔的原因有多种,主要包括以下几个方面:1. 材料本身的问题:一些材料由于其特殊的化学成分或物理性质,容易产生气泡或者孔洞。
这些材料在加工或制造过程中容易出现缩孔问题。
2. 加工工艺的问题:加工过程中,如果温度、压力或者速度等参数控制不当,都有可能导致缩孔问题的发生。
例如,如果温度过高或者加热速度过快,就容易在材料内部产生气泡或者孔洞。
3. 设备的问题:加工设备的性能和状态也会影响材料的缩孔情况。
如果设备的密封性不好或者加工条件不能满足要求,就有可能导致缩孔问题。
针对缩孔问题的控制方法主要包括以下几个方面:1. 材料选择:选择合适的材料对于缩孔问题的控制非常重要。
一些具有较低缩孔倾向的材料可以有效地减少缩孔问题的发生。
2. 加工工艺优化:通过合理调整加工工艺参数,如温度、压力、速度等,可以减少缩孔问题的发生。
例如,采用适当的加热温度和加热时间可以降低材料内部气泡的产生。
3. 设备改进:改进加工设备的密封性能和控制能力,能够有效地减少缩孔问题。
定期检查和维护设备,确保其处于良好的工作状态也是很重要的。
二、缩松缩松是指在材料加工或制造过程中,由于材料的收缩不均匀而导致的形状尺寸偏差。
缩松问题会导致产品的尺寸不准确,甚至无法满足设计要求。
造成缩松的原因主要包括以下几个方面:1. 材料本身的问题:一些材料由于其特殊的物理性质,在加工或制造过程中容易出现收缩不均匀的情况,从而导致缩松问题的发生。
2. 加工工艺的问题:加工过程中,如果温度、压力或者速度等参数控制不当,都有可能导致材料收缩不均匀,出现缩松问题。
缩孔的防止措施

缩孔的防止措施1. 背景介绍在工程领域中,缩孔是一种常见的问题,指的是混凝土浇筑过程中未能填满模板或者未完全充实的空洞或空隙。
缩孔可能会导致混凝土结构的强度和稳定性受到影响,从而影响到工程的质量和安全性。
为了防止缩孔问题的发生,在混凝土浇筑过程中需要采取一些防止措施。
2. 防止缩孔的措施以下是防止缩孔问题发生的几种常用措施:2.1 混凝土配合比设计混凝土配合比设计是防止缩孔的关键因素之一。
合理的配合比设计可以确保混凝土的流动性和可塑性,从而减少浇筑过程中的空隙和空洞。
在设计配合比时,需要考虑到使用的材料种类和质量、水胶比、粉料含量以及外加剂的使用等因素。
2.2 浇筑技术控制控制好混凝土的浇筑技术也是防止缩孔的重要措施之一。
以下是几个浇筑技术控制的要点:•振捣方式和时间:使用适当的振捣方式和时间可以帮助混凝土充实模板中的空隙和空洞。
振捣应该均匀地分布在整个浇筑区域,并且持续时间应该足够长,确保混凝土能够流动并充分充实。
•浇注方式:采用合适的浇注方式可以有效地减少缩孔的发生。
例如,在梁柱节点处可以采用低压喷射的方式进行浇注,将混凝土均匀地注入模板中,避免产生空洞。
2.3 加大修补措施如果在施工过程中发现缩孔问题,需要及时采取修补措施,以确保施工质量。
以下是一些常用的修补措施:•补丁修复:针对小面积的缩孔,可以使用混凝土补丁进行修复。
补丁的混凝土需要与原混凝土具有相同的成分和性能。
•重新浇筑:对于大面积的缩孔,需要重新浇筑混凝土。
在重新浇筑之前,需要清理和处理好原混凝土表面,确保新旧混凝土之间能够良好的结合。
重新浇筑时需要遵循之前提到的浇筑技术控制措施。
3. 缩孔的影响如果缩孔问题得不到有效的控制和修复,可能会带来以下几个方面的不良影响:•结构强度丧失:缩孔可能导致混凝土结构的强度丧失,从而影响到整个工程的安全性和稳定性。
•结构变形:缩孔也可能导致混凝土结构的变形增大,使得结构整体的稳定性下降。
•耐久性下降:缩孔会导致混凝土中的空隙增多,从而影响到混凝土的耐久性。
分析铸造缩松缺陷形成原因及对策

分析铸造缩松缺陷形成原因及对策铸造缩孔缺陷是在铸造过程中常见的一种问题,它会给制造业带来很多麻烦和损失。
本文将分析铸造缩孔缺陷的形成原因,并提出相应的对策,以期为相关行业提供帮助和指导。
一、铸造缩孔缺陷的形成原因分析1.1 完全凝固不均匀在铸造过程中,铸件凝固是逐渐进行的,如果凝固速度不均匀,就会导致缩孔缺陷的形成。
常见的原因包括铸件的凝固时间过短、冷却速度不均匀、局部温度过高等。
1.2 金属液收缩过大铸造过程中,金属液在凝固过程中会收缩,如果收缩过大,就容易形成缩孔。
这主要是由于铸件材料的物理性质不合理,或者是铸型的设计不合理所导致的。
1.3 铸造材料含有气体铸造材料中含有气体会在凝固过程中释放出来,如果释放过快,就会形成孔洞。
常见的原因是铸造材料中含有气体的含量过高,或者是在铸造过程中没有采取有效的排气措施。
1.4 基材与液态金属的相容性差如果铸件的基材与液态金属的相容性差,就容易在凝固过程中产生裂纹和缩孔。
一般来说,基材与液态金属的相容性差会导致界面张力增大,从而影响凝固过程。
二、对策提出2.1 优化铸造工艺参数通过优化铸造工艺参数,可以降低缩孔缺陷的发生概率。
具体来说,可以调整金属液的浇注温度和速度,控制铸件的凝固时间,改进冷却系统等措施。
2.2 优化铸造材料选择合适的铸造材料也是减少缩孔缺陷的关键。
应选择具有较低的收缩率和较好的流动性的材料,以确保凝固过程中的收缩程度可控。
2.3 采取有效的排气措施在铸造过程中,采取有效的排气措施可以减少气体对铸件凝固过程的干扰,从而降低缩孔缺陷的风险。
排气措施可以包括加入剂、提高浇注温度、采取适当的连续浇注等。
2.4 提高基材与液态金属的相容性为了减少缩孔缺陷的形成,可以通过提高基材与液态金属的相容性来增加界面的稳定性。
可以通过改变基材化学成分、调整金属液的配方等方式来实现。
三、结语以上是对铸造缩孔缺陷形成原因及对策的分析。
通过优化铸造工艺、材料选择、排气措施以及提高基材与液态金属的相容性等方法,可以有效降低缩孔缺陷的发生概率,提高铸件的质量和产能。
铸铁件缩松、缩孔、凹陷缺陷的原因分析与防止方法
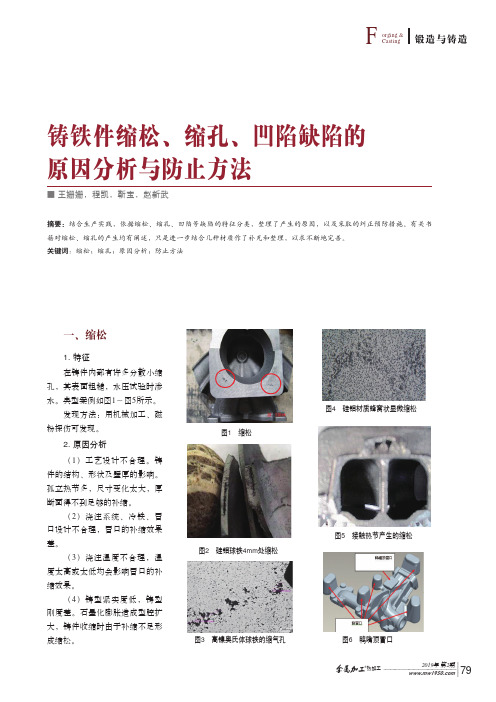
2019年第2期热加工79F锻造与铸造orging &Casting铸铁件缩松、缩孔、凹陷缺陷的原因分析与防止方法■王姗姗,程凯,靳宝,赵新武摘要:结合生产实践,依据缩松、缩孔、凹陷等缺陷的特征分类,整理了产生的原因,以及采取的纠正预防措施。
有关书籍对缩松、缩孔的产生均有阐述,只是进一步结合几种材质作了补充和整理,以求不断地完善。
关键词:缩松;缩孔;原因分析;防止方法一、缩松1. 特征在铸件内部有许多分散小缩孔,其表面粗糙,水压试验时渗水。
典型案例如图1~图5所示。
发现方法:用机械加工、磁粉探伤可发现。
2. 原因分析(1)工艺设计不合理。
铸件的结构、形状及壁厚的影响。
孤立热节多,尺寸变化太大,厚断面得不到足够的补缩。
(2)浇注系统、冷铁、冒口设计不合理,冒口的补缩效果差。
(3)浇注温度不合理,温度太高或太低均会影响冒口的补缩效果。
(4)铸型紧实度低,铸型刚度差。
石墨化膨胀造成型腔扩大,铸件收缩时由于补缩不足形成缩松。
图1 缩松图2 硅钼球铁4mm处缩松图4 硅钼材质蜂窝状显微缩松图3 高镍奥氏体球铁的缩气孔图5 接触热节产生的缩松图6 鸭嘴顶冒口2019年 第2期 热加工80F锻造与铸造orging &Casting(5)碳、硅含量低,磷含量较高;凝固区间大。
硅钼和高镍球墨铸铁对碳、硅含量和氧化铁液的敏感性特大,铁液严重氧化或碳、硅量低时,易出现显微缩松。
即便在薄壁处也容易出现缩松(见图2、图3、图4)。
(6)孕育不充分,石墨化效果差。
(7)残余镁量和稀土量过高。
钼含量较高时也会增加显微缩松。
(8)浇注速度太快。
(9)炉料锈蚀,氧化铁多。
(10)铁液在电炉内高温停放时间太长,俗称“死铁水”,造成严重氧化。
(11)冲天炉熔炼时底焦太底,风量太大,元素烧损大,铁液严重氧化。
(12)冒口径处形成接触热节产生缩松(见图5)。
(13)压箱铁不够(或箱卡未锁紧,箱带断裂等),浇注后由于涨箱造成缩松。
304不锈钢熔模铸造中缩孔、缩松的几种防止措施

熔模铸造中缩松的几种特有解决方案
缩松是铸造最常见的缺陷之一,是铸件在冷却过程中热节或远浇口部位得不到有效的补缩而产生的细小分散的孔洞。
熔模铸造因为热壳浇注的特点,在浇注系统设计时大大地限制了冒口、冷铁对于缩松的处理,但是却有一系列独特的解决方案。
1、型壳底部淬水
部位:铸件浇注位置底部。
铸件浇注位置底部远离浇冒口,补缩通道过长,如果铸件较高或底部有热节,就容易产生缩松。
原理:通过淬水使型壳底部温度迅速降低,对铸件起到底部激冷的作用。
操作:热壳浇注后,型壳立刻淬水,视铸件薄厚在水中停顿1-3秒,深度为易缩松的位置。
案例1圆环产品,材质304不锈钢,浇注温度1640℃
此产品组树后高度方向尺寸较大,见图1和图2,浇注后于圆环浇注位置的下半圆A处容易出现缩松,如图1,经分析认为补缩通道过长导致下半圆凝固时钢水得不到有效补缩,从而产生缩松。
工艺改进为型壳底部淬水,深度如图2所示,效果良好,基本解决下半圆的缩松问题。
图1 圆环剖面图图2 圆环组树淬水示意图
2、喷水激冷
3、局部补砂泥
4、中空型壳
5、加保温棉
6、工艺散热冷铁
7、冷铁、热贴。
二、铸件中的缩孔和缩松讲解

1、缩孔与缩松的形成 (1)缩孔(又称集中缩孔)
• 形成 • 形状:倒锥形 • 形成部位最后凝固处 • 易形成缩孔的合金:纯金属,共晶成分
的合金→逐层凝固
图2-4 缩孔形成过程
Fig.2-4 The formation of Shrinkage Void
The formation of Thermal Stress
Internal Stress,Deformation and
Crack of Casting
• 结论:铸件中厚的部分最后冷却,总是 受拉应力,反之,薄的部分受压应力。
• 热应力的预防:采用同时凝固的方法 (不管壁厚如何,同时一起收缩,可避 免热应力的产生)。
Internal Stress,Deformation and Crack of Casting
铸造内应力:铸件冷却时因固态收缩受 阻碍,在铸件内部产生的应力。
一、内应力的形成
类型— 热应力、机械应力 1、热应力
• 热应力的形成 • 形成原因—铸件的壁厚不均匀,冷却和
收缩先后不一致造成内应力。
图2-8 热应力的形成
• 适用的合金:普通灰口铸铁(缩孔缩松 倾向小),锡青铜
2、机械应力
二、铸件的变形与预防
Deformation of the Cast and Its Prevention
具有内应力的铸件处在一种不稳定的状 态— 它会通过适当的变形来减缓自身的 内应力,趋于一种稳定状态。
例1 T型型材的变形 例2 机架的变形 例3 机床床身
顺序凝固法的总体思路:合金的收缩不 可避免,可使缩孔形成在铸件外部的冒 口内(该处为最后凝固处)。
- 1、下载文档前请自行甄别文档内容的完整性,平台不提供额外的编辑、内容补充、找答案等附加服务。
- 2、"仅部分预览"的文档,不可在线预览部分如存在完整性等问题,可反馈申请退款(可完整预览的文档不适用该条件!)。
- 3、如文档侵犯您的权益,请联系客服反馈,我们会尽快为您处理(人工客服工作时间:9:00-18:30)。
缩孔、缩松的形成及防止方法
副教授:陈云
铸件中的缩孔与缩松
液态金属在铸型内凝固过程中,由于液态收缩和凝固收缩导致体积缩小,若其收缩得不到补充,就在铸件最后凝固的部分形成孔洞。
大而集中的孔洞称为缩孔,细小而分散的孔洞称为缩松。
(a)铝合金缩孔、缩松(b)金相显微镜下缩松(c)扫描电镜下缩松
一、缩孔的形成
纯金属、共晶成分和凝固温度范围窄的合金,浇注后在型腔内是由表及里的逐层凝固。
在凝固过程中,如得不到合金液的补充,在铸件最后凝固的地方就会产生缩孔。
缩孔形成的条件:铸件呈逐层凝固方式凝固,成分为纯金属或共晶成分的
合金。
缩孔产生的基本原因:是合金的液态收缩和凝固收缩值大于固态收缩值,且得不到补偿。
缩孔产生的部位在铸件最后凝固区域,如壁较厚大的上部或铸件两壁相交处,这些地方称为热节。
热节位置可用画内接圆的方法确定。
用画内切圆法确定缩孔位置
二、缩松的形成
铸件最后凝固的收缩未能得到补充,或者结晶温度范围宽的合金呈糊状凝固,凝固区域较宽,液、固两相共存,树枝晶发达,枝晶骨架将合金液分割开的小液体区难以得到补缩所致。
缩松形成的条件:铸件主要呈糊状凝固方式凝固,成分为非共晶成分或有较宽结晶温度范围的合金。
形成缩松的基本原因:是合金的液态收缩和凝固收缩值大于固态收缩值。
缩松一般出现在铸件壁的轴线区域、冒口根部、热节处,也常分布在集中缩孔的下方。
三、影响缩孔和缩松形成的因素
1、合金成分
结晶温度范围越小的合金,产
生缩孔的倾向越大;结晶温度范围
越大的合金,产生缩松的倾向越大。
铁碳合金成分和体积收缩的关系
V总—总体积收缩容积;V孔—缩孔容积;V松—缩松容积
2、浇注条件
提高浇注温度时,合金的总体积收缩和缩
孔倾向增大。
浇注速度很慢或向冒口中不断补浇高温合
金液,使铸件液态和凝固收缩及时得到补偿,
铸件总体积收缩减小,缩孔容积也减小。
V 总—总体积收缩容积;V 孔—缩孔容积;V 松—缩松容积
铁碳合金成分和体积收缩的关系
3、铸型材料
铸型材料对铸件冷却速度影响很大 。
湿型比干型的冷却能力大,使凝固区域
变窄,缩松减少。
金属型的冷却能力更大,
故缩松更显著减少。
四、缩孔和缩松的防止方法
缩孔和缩松都使铸件的力学性能下降,缩松还可使铸件因渗漏而报废。
因此,必须根据技术要求,采取适当的工艺措施予以防止。
1、控制铸件的凝固过程
实践证明,只要能使铸件实现“顺序凝固”(定
向凝固)或“同时凝固”,尽管合金的收缩较大,也
可获得没有缩孔的致密铸件。
“顺序凝固”原则是让铸件远离冒口的地方先凝
固,靠近冒口的地方次凝固,最后才是冒口本身凝
固,实现以厚补薄,将缩孔转移到冒口中去。
“顺序凝固”适用于收缩大或壁厚差别较大,易产生缩孔的合金铸件,如铸钢、高强度灰口铸铁和可锻铸铁等。
“同时凝固”原则,就是从工艺上采取必要
的措施,使铸件各部分的冷却速度尽量相等,以达
到铸件各部分几乎同时凝固完结。
“同时凝固”原则,适用于碳、硅含量较高
的灰口铸铁和球墨铸铁。
采用“顺序凝固”时,尽管冒口补缩作用好,但冷却速度不一致,易产生铸造应力、变形及裂纹等缺陷;冒口消耗金属多,降低了铸件的出品率,并且,冒口切割较为困难。
采用“同时凝固”时,铸件出现裂纹、应力和变形的倾向性小,不必设置冒口,使工艺简化,又能节省金属材料,而且,提高了铸造的出品率。
2、合理应用冒口、冷铁等工艺措施
冒口一般设置在铸件厚壁处和热节部位,是防止缩孔、缩松最有效的措施,冒口的尺寸应保证冒口比铸件补缩部位凝固得晚,并有足够的金属液供给。
冷铁通常是用铸铁、钢和铜等金属材料制成
的激冷物。
放入铸型内,用以加大铸件某一部分
的冷却速度,调节铸件的凝固顺序。
阀体铸件的冒口和冷铁位置
1—浇口;2—明冒口;3—暗冒口(或边冒口);4—冷铁
谢谢观看。