防止缩松缩孔
铸件中缩孔与缩松的防止方法
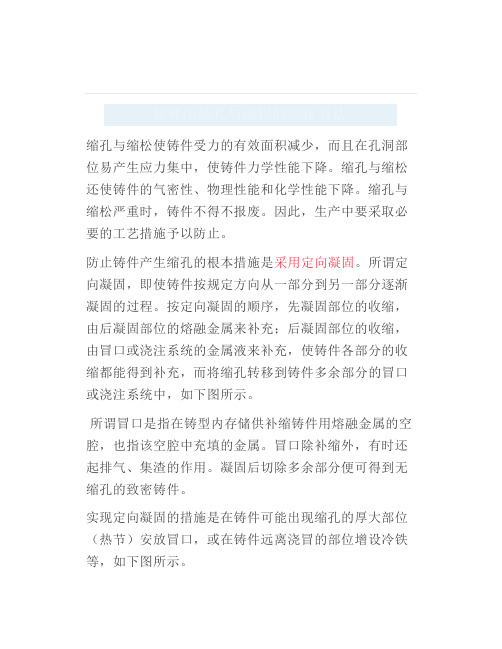
铸件中缩孔与缩松的防止方法缩孔与缩松使铸件受力的有效面积减少,而且在孔洞部位易产生应力集中,使铸件力学性能下降。
缩孔与缩松还使铸件的气密性、物理性能和化学性能下降。
缩孔与缩松严重时,铸件不得不报废。
因此,生产中要采取必要的工艺措施予以防止。
防止铸件产生缩孔的根本措施是采用定向凝固。
所谓定向凝固,即使铸件按规定方向从一部分到另一部分逐渐凝固的过程。
按定向凝固的顺序,先凝固部位的收缩,由后凝固部位的熔融金属来补充;后凝固部位的收缩,由冒口或浇注系统的金属液来补充,使铸件各部分的收缩都能得到补充,而将缩孔转移到铸件多余部分的冒口或浇注系统中,如下图所示。
所谓冒口是指在铸型内存储供补缩铸件用熔融金属的空腔,也指该空腔中充填的金属。
冒口除补缩外,有时还起排气、集渣的作用。
凝固后切除多余部分便可得到无缩孔的致密铸件。
实现定向凝固的措施是在铸件可能出现缩孔的厚大部位(热节)安放冒口,或在铸件远离浇冒的部位增设冷铁等,如下图所示。
所谓冷铁是指为增加铸件局部的冷却速度,在砂型、砂芯表面或型腔中安放的金属物。
图中所示铸件中可能产生缩孔的厚大部分不止一个,若仅靠顶部冒口,难以向底部凸台补缩,如果在该凸台的型壁上安放两个外冷铁,加快了该处的冷却速度,使厚壁凸台反而最先凝固,从而实现了由下而上的定向凝固。
定向凝固与逐层凝固是两个不同的概念。
定向凝固是指铸件各部分的凝固顺序;逐层凝固是指铸件某截面上的凝固顺序。
逐层凝固的合金表层先凝固,然后逐渐向铸件中心增厚,铸件中心最后凝固。
冒口的补缩通道能长时间保持畅通,有利于实现铸件的定向凝固。
对于纯金属、共晶成分的合金,工艺上一般都采用定向凝固的原则,来提高铸件的致密性。
相反,倾向于糊状凝固的合金,结晶的固体骨架较好地布满整个铸件的截面,使冒口的补缩通道堵塞,难以实现定向凝固。
铸钢件缩孔和缩松的形成与预防

F铸造oundry热加工热处理/锻压/铸造2011年第15期69铸钢件缩孔和缩松的形成与预防宁夏天地奔牛实业集团有限公司(石嘴山753001)王福京缩孔和缩松从本质上来说,是因为型内的金属产生收缩而引起的,但是不同种类的金属,其形成缩孔和缩松的机理有所不同。
1.产生机理从铸钢件角度来分析,钢液注满型腔后,由于型壁的传热作用,型内钢液形成自型壁表面至铸件壁厚中心温度逐渐升高的温度梯度。
随着型壁传热作用不断地进行,型内钢液温度不断降低。
当与型壁表面接触的钢液温度降至凝固温度时,铸件的表面就开始凝固,并形成一层固体状态的硬壳。
如果这时浇注系统已经凝固,那么硬壳内处于液体状态的钢液就与外界隔绝。
当型内钢液温度进一步降低时,硬壳内的钢液一方面因温度降低而产生液态收缩,另一方面由于硬壳的传热作用,使与硬壳接触的钢液不断结晶凝固,从而出现凝固收缩。
这两种收缩的出现,将使硬壳内钢液液面下降。
与此同时,处于固体状态的硬壳,也因温度的降低而产生固态收缩,对于铸钢件来说,由于液态收缩和凝固收缩的总和是大于固态收缩的,因此在重力作用下,硬壳内钢液液面将下降,并且与上部硬壳脱离接触。
随着型内钢液温度不断地降低和硬壳内钢液不断地凝固,硬壳越来越厚,而钢液越来越少。
当铸件内最后的钢液凝固后,铸件上部的硬壳下面就会出现一个孔洞,这个孔洞即为缩孔。
虽然凝固后的铸件自高温状态冷却至室温时,还将产生固态收缩,从而使整个铸件和其内部缩孔的体积稍有减小,但并不会改变缩孔体积与铸件体积的比值。
由于凝固层厚度的增加和钢液的减少是不断进行的,因而从理论上来说,缩孔的形状是漏斗状的。
并且因残存的钢液凝固时不能得到补缩,所以在产生缩孔的同时,往往也伴随着缩松的出现。
用肉眼能直接观察到的缩孔为宏观缩孔,而借助于放大镜或将断面腐蚀以后才能发现的缩孔为微观缩孔。
一般情况下,宏观缩孔可以用补焊的手段来解决,而微观缩孔就无法处理了,一般都是成片出现的微小孔洞。
缩孔和缩松及其控制方法

缩孔和缩松及其控制方法缩孔和缩松是在材料加工和制造过程中常见的问题,对于产品的质量和性能有着重要影响。
本文将分别介绍缩孔和缩松的概念、原因以及控制方法。
一、缩孔缩孔指的是材料加工或制造过程中产生的孔洞或空隙,一般是由于材料内部气体无法完全排除或者材料收缩不均匀而引起的。
缩孔问题会导致产品的力学性能下降、密封性能降低以及外观质量不佳等问题。
造成缩孔的原因有多种,主要包括以下几个方面:1. 材料本身的问题:一些材料由于其特殊的化学成分或物理性质,容易产生气泡或者孔洞。
这些材料在加工或制造过程中容易出现缩孔问题。
2. 加工工艺的问题:加工过程中,如果温度、压力或者速度等参数控制不当,都有可能导致缩孔问题的发生。
例如,如果温度过高或者加热速度过快,就容易在材料内部产生气泡或者孔洞。
3. 设备的问题:加工设备的性能和状态也会影响材料的缩孔情况。
如果设备的密封性不好或者加工条件不能满足要求,就有可能导致缩孔问题。
针对缩孔问题的控制方法主要包括以下几个方面:1. 材料选择:选择合适的材料对于缩孔问题的控制非常重要。
一些具有较低缩孔倾向的材料可以有效地减少缩孔问题的发生。
2. 加工工艺优化:通过合理调整加工工艺参数,如温度、压力、速度等,可以减少缩孔问题的发生。
例如,采用适当的加热温度和加热时间可以降低材料内部气泡的产生。
3. 设备改进:改进加工设备的密封性能和控制能力,能够有效地减少缩孔问题。
定期检查和维护设备,确保其处于良好的工作状态也是很重要的。
二、缩松缩松是指在材料加工或制造过程中,由于材料的收缩不均匀而导致的形状尺寸偏差。
缩松问题会导致产品的尺寸不准确,甚至无法满足设计要求。
造成缩松的原因主要包括以下几个方面:1. 材料本身的问题:一些材料由于其特殊的物理性质,在加工或制造过程中容易出现收缩不均匀的情况,从而导致缩松问题的发生。
2. 加工工艺的问题:加工过程中,如果温度、压力或者速度等参数控制不当,都有可能导致材料收缩不均匀,出现缩松问题。
3.2.2 缩孔、缩松的形成及防止方法

缩孔、缩松的形成及防止方法副教授:陈云铸件中的缩孔与缩松液态金属在铸型内凝固过程中,由于液态收缩和凝固收缩导致体积缩小,若其收缩得不到补充,就在铸件最后凝固的部分形成孔洞。
大而集中的孔洞称为缩孔,细小而分散的孔洞称为缩松。
(a)铝合金缩孔、缩松(b)金相显微镜下缩松(c)扫描电镜下缩松一、缩孔的形成纯金属、共晶成分和凝固温度范围窄的合金,浇注后在型腔内是由表及里的逐层凝固。
在凝固过程中,如得不到合金液的补充,在铸件最后凝固的地方就会产生缩孔。
缩孔形成的条件:铸件呈逐层凝固方式凝固,成分为纯金属或共晶成分的合金。
缩孔产生的基本原因:是合金的液态收缩和凝固收缩值大于固态收缩值,且得不到补偿。
缩孔产生的部位在铸件最后凝固区域,如壁较厚大的上部或铸件两壁相交处,这些地方称为热节。
热节位置可用画内接圆的方法确定。
用画内切圆法确定缩孔位置二、缩松的形成铸件最后凝固的收缩未能得到补充,或者结晶温度范围宽的合金呈糊状凝固,凝固区域较宽,液、固两相共存,树枝晶发达,枝晶骨架将合金液分割开的小液体区难以得到补缩所致。
缩松形成的条件:铸件主要呈糊状凝固方式凝固,成分为非共晶成分或有较宽结晶温度范围的合金。
形成缩松的基本原因:是合金的液态收缩和凝固收缩值大于固态收缩值。
缩松一般出现在铸件壁的轴线区域、冒口根部、热节处,也常分布在集中缩孔的下方。
三、影响缩孔和缩松形成的因素1、合金成分结晶温度范围越小的合金,产生缩孔的倾向越大;结晶温度范围越大的合金,产生缩松的倾向越大。
铁碳合金成分和体积收缩的关系V总—总体积收缩容积;V孔—缩孔容积;V松—缩松容积2、浇注条件提高浇注温度时,合金的总体积收缩和缩孔倾向增大。
浇注速度很慢或向冒口中不断补浇高温合金液,使铸件液态和凝固收缩及时得到补偿,铸件总体积收缩减小,缩孔容积也减小。
V 总—总体积收缩容积;V 孔—缩孔容积;V 松—缩松容积铁碳合金成分和体积收缩的关系3、铸型材料铸型材料对铸件冷却速度影响很大 。
缩孔的防止措施

缩孔的防止措施1. 背景介绍在工程领域中,缩孔是一种常见的问题,指的是混凝土浇筑过程中未能填满模板或者未完全充实的空洞或空隙。
缩孔可能会导致混凝土结构的强度和稳定性受到影响,从而影响到工程的质量和安全性。
为了防止缩孔问题的发生,在混凝土浇筑过程中需要采取一些防止措施。
2. 防止缩孔的措施以下是防止缩孔问题发生的几种常用措施:2.1 混凝土配合比设计混凝土配合比设计是防止缩孔的关键因素之一。
合理的配合比设计可以确保混凝土的流动性和可塑性,从而减少浇筑过程中的空隙和空洞。
在设计配合比时,需要考虑到使用的材料种类和质量、水胶比、粉料含量以及外加剂的使用等因素。
2.2 浇筑技术控制控制好混凝土的浇筑技术也是防止缩孔的重要措施之一。
以下是几个浇筑技术控制的要点:•振捣方式和时间:使用适当的振捣方式和时间可以帮助混凝土充实模板中的空隙和空洞。
振捣应该均匀地分布在整个浇筑区域,并且持续时间应该足够长,确保混凝土能够流动并充分充实。
•浇注方式:采用合适的浇注方式可以有效地减少缩孔的发生。
例如,在梁柱节点处可以采用低压喷射的方式进行浇注,将混凝土均匀地注入模板中,避免产生空洞。
2.3 加大修补措施如果在施工过程中发现缩孔问题,需要及时采取修补措施,以确保施工质量。
以下是一些常用的修补措施:•补丁修复:针对小面积的缩孔,可以使用混凝土补丁进行修复。
补丁的混凝土需要与原混凝土具有相同的成分和性能。
•重新浇筑:对于大面积的缩孔,需要重新浇筑混凝土。
在重新浇筑之前,需要清理和处理好原混凝土表面,确保新旧混凝土之间能够良好的结合。
重新浇筑时需要遵循之前提到的浇筑技术控制措施。
3. 缩孔的影响如果缩孔问题得不到有效的控制和修复,可能会带来以下几个方面的不良影响:•结构强度丧失:缩孔可能导致混凝土结构的强度丧失,从而影响到整个工程的安全性和稳定性。
•结构变形:缩孔也可能导致混凝土结构的变形增大,使得结构整体的稳定性下降。
•耐久性下降:缩孔会导致混凝土中的空隙增多,从而影响到混凝土的耐久性。
铸件缩孔、缩松有何区别?如何解决?

铸件缩孔、缩松有何区别?如何解决?在铸造生产中,铸件气孔和铸件缩孔有时是伴生的,有时是独立存在。
当出现气孔和缩孔时,我们要快速的判断出缺陷是气孔还是缩孔对于解决问题十分必要。
气孔类缺陷与防治方法在铸造生产中,孔洞类缺陷是常见缺陷,也是给铸造厂造成损失比较大的缺陷之一。
孔洞类缺陷分为气孔和缩孔。
气孔多为由于金属液中侵入、裹入、卷入气体所至。
铸件气孔出现在铸件上的位置不同,其产生的原因也不同。
这就要求我们的铸造技术员在判断气孔缺陷病因时,要掌握各类气孔发生的原理,具有什么样的特征。
只有如此才能对症下药,将出现的气孔缺陷解决掉。
气孔特征:(1)卷入气孔:金属液在充型过程中因卷入气体而在铸件内形成气孔,多呈孤立存在的圆形或椭圆形大气孔,位置不固定,一般偏铸件中上部。
(2)侵入气孔:由型、芯、涂料、芯撑、冷铁产生的气孔侵入铸件表层而形成气孔,多呈梨形或椭圆形,尺寸较大,孔壁光滑,表面多呈氧化色。
(3)反应气孔:由金属液内部某些成分之间或金属液与型、芯在界面上发生化学反应而形成群分布的气孔。
位于铸件表层的针头形或腰圆形反应气孔称为表面针孔与皮下气孔,由金属液与型、芯涂料发生界面反应所至;分散或成群分布在铸件整个断面上或某个局部区域的针头反应气孔。
形成原因:(1)由于炉料潮湿、锈蚀、油污、气候的潮湿,熔练工具和浇包未烘干,金属液成分不当,合金液为精炼与精炼不足,使金属液中含有大量气体或气体物质,导致在铸件中析出气孔或反应气孔。
(2)型、芯未充分烘干,透气性差,通气不良,含水分和发气物质过多,涂料未烘干或含发气成分过多,冷铁、芯撑有锈斑、油污或未烘干,金属型排气不良,在铸件中形成侵入气孔。
(3)浇注系统不合理,浇注和充型速度过快,金属型排气不良,使金属液在浇注和充型过程中产生紊流、涡流或断流而卷入气体,在铸件中形成卷入性气孔。
(4)合金液易可吸气,在熔炼和浇注过程中未采取有效的精炼、保护和净化措施,使金属液中含有大量气体、夹渣和夹气成分,在充型和凝固过程中形成析出气孔和反应气孔。
铸钢缩孔和缩松产生的原因及预防措施!
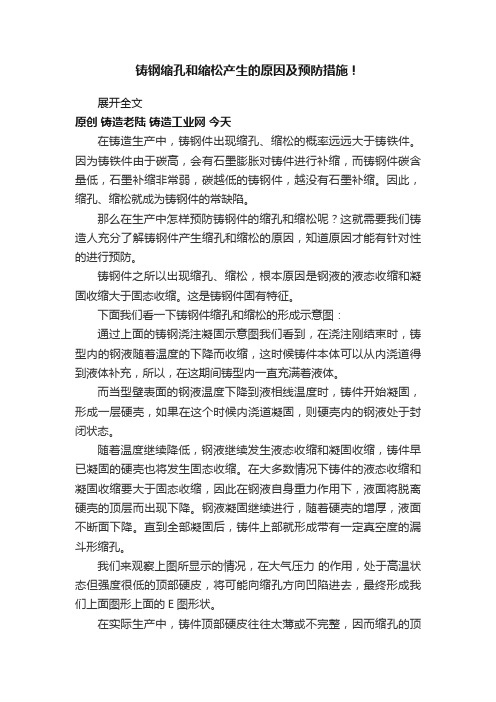
铸钢缩孔和缩松产生的原因及预防措施!展开全文原创铸造老陆铸造工业网今天在铸造生产中,铸钢件出现缩孔、缩松的概率远远大于铸铁件。
因为铸铁件由于碳高,会有石墨膨胀对铸件进行补缩,而铸钢件碳含量低,石墨补缩非常弱,碳越低的铸钢件,越没有石墨补缩。
因此,缩孔、缩松就成为铸钢件的常缺陷。
那么在生产中怎样预防铸钢件的缩孔和缩松呢?这就需要我们铸造人充分了解铸钢件产生缩孔和缩松的原因,知道原因才能有针对性的进行预防。
铸钢件之所以出现缩孔、缩松,根本原因是钢液的液态收缩和凝固收缩大于固态收缩。
这是铸钢件固有特征。
下面我们看一下铸钢件缩孔和缩松的形成示意图:通过上面的铸钢浇注凝固示意图我们看到,在浇注刚结束时,铸型内的钢液随着温度的下降而收缩,这时候铸件本体可以从内浇道得到液体补充,所以,在这期间铸型内一直充满着液体。
而当型壁表面的钢液温度下降到液相线温度时,铸件开始凝固,形成一层硬壳,如果在这个时候内浇道凝固,则硬壳内的钢液处于封闭状态。
随着温度继续降低,钢液继续发生液态收缩和凝固收缩,铸件早已凝固的硬壳也将发生固态收缩。
在大多数情况下铸件的液态收缩和凝固收缩要大于固态收缩,因此在钢液自身重力作用下,液面将脱离硬壳的顶层而出现下降。
钢液凝固继续进行,随着硬壳的增厚,液面不断面下降。
直到全部凝固后,铸件上部就形成带有一定真空度的漏斗形缩孔。
我们来观察上图所显示的情况,在大气压力的作用,处于高温状态但强度很低的顶部硬皮,将可能向缩孔方向凹陷进去,最终形成我们上面图形上面的E图形状。
在实际生产中,铸件顶部硬皮往往太薄或不完整,因而缩孔的顶部通常和能大气相通。
铸件凝固后期,在其最后凝固部分的残余钢液中,由于温度梯度小,金属液将同时凝固,即在钢液中出现许多细小的晶粒,当晶粒长大互相连接后,将剩余的钢液分割成互不相通的小熔池。
这些小熔池在进一步冷却和凝固时得不到液体的补缩,会产生许多细小的孔洞,这就是缩松。
缩松按糨的分布情况一般分为三种:一、弥散缩松,这种缩松是指细小的孔洞均匀分布在铸件的大部分体积内,易在结晶温度范围宽的合金铸件的冷却缓慢的厚大部位处产生。
焊接缩孔与缩松的机理及因素及防止措施
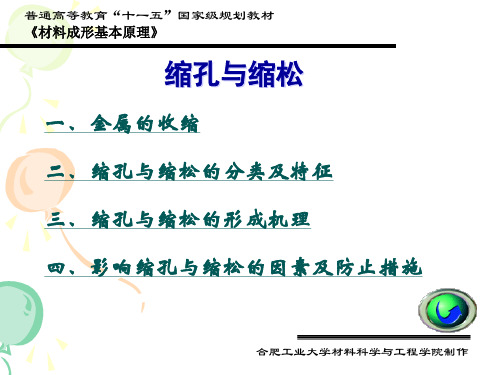
合肥工业大学材料科学与工程学院制作
普通高等教育“十一五”国家级规划教材 《材料成形基本原理》
温度 /℃ 温度 温度 m = ( 100 % n ( T ) L S ) V( LS) 0 L S V 液 V 液 浇 V 凝 S 固 V ( L V 固 /℃ /℃
合肥工业大学材料科学与工程学院制作
普通高等教育“十一五”国家级规划教材 《材料成形基本原理》
a)明缩孔
b)凹角缩孔
c)芯面缩孔
d)内部缩孔
合肥工业大学材料科学与工程学院制作
普通高等教育“十一五”国家级规划教材 《材料成形基本原理》
缩 孔 特 点
常出现于纯金属、共晶成分合金和结晶温度范围 较窄的以层状凝固方式凝固的铸造合金中; 多集中在铸件的上部和最后凝固的部位;铸件厚 壁处、两壁相交处及内浇口附近等凝固较晚或凝 固缓慢的部位(称为热节),也常出现缩孔; 缩孔尺寸较大,形状不规则,表面不光滑。
金属从浇注温度冷却到室温所产生的体收缩为液
态收缩、凝固收缩和固态收缩之和,即:
εV总=εV液+εV凝+εV固
其中,液态收缩和凝固收缩是铸件产生缩孔
和缩松的基本原因 。而固相收缩对应力、变形
与裂纹影响较大。
合肥工业大学材料科学与工程学院制作
普通高等教育“十一五”国家级规划教材 《材料成形基本原理》
二、缩孔与缩松的分类及特征 缩孔 缩松
普通高等教育“十一五”国家级规划教材 《材料成形基本原理》
(一)影响缩孔与缩松的因素
金属的性质 铸型的冷却能力 (收缩系数α大) (蓄热系数b小)
浇注温度与浇注速度 (高,快) 铸件尺寸 补缩能力 (大) (弱)
例:铸铁的缩孔、缩松倾向
- 1、下载文档前请自行甄别文档内容的完整性,平台不提供额外的编辑、内容补充、找答案等附加服务。
- 2、"仅部分预览"的文档,不可在线预览部分如存在完整性等问题,可反馈申请退款(可完整预览的文档不适用该条件!)。
- 3、如文档侵犯您的权益,请联系客服反馈,我们会尽快为您处理(人工客服工作时间:9:00-18:30)。
第四节防止缩孔缩松的途径
一、缩孔和缩松的相互转化
对于一定成分的合金,浇注温度一定时合金的收缩体积满足以下关系:总收缩体积=液态收缩体积+凝固收缩体积=缩孔体积+缩松体积=常数。
但是,缩孔和缩松体积可以相互转化,造成转化的根本原因是凝固方式的改变:即体积凝固还是逐层凝固。
表8-2给出了影响缩孔和缩松体积相互转化的因素。
表8-2 缩孔、缩松互相转换的影响因素
二、防止缩孔和缩松的途径
防止铸件中产生缩孔和缩松的基本原则是针对该合金的收缩和凝固特点制定正确的铸造工艺,使铸件在凝固过程中建立良好的补缩条件,尽可能地使缩松转化为缩孔,并使缩孔出现在铸件最后凝固的地方。
这样,在铸件最后凝固的地方安臵一定尺寸的冒口,使缩孔集中于冒口中,或者把浇口开在最后凝固
的地方直接补缩,即可获得健全的铸件。
使铸件在凝固过程中建立良好的补缩条件,主要是通过控制铸件的凝固方向使之符合“顺序凝固原则”或“同时凝固原则”。
1、顺序凝固(progressive solidification)
铸件的顺序凝固原则,是采用各种措施保证铸件结构上各部分,按照远离冒口的部分最先凝固,然后是靠近冒口部分,最后才是冒口本身凝固的次序进行,亦即在铸件上远离冒口或浇口的部分到冒口或浇口之间建立一个递增的温度梯度,如图8-8所示。
铸件按照顺序凝固原则进行凝固,能保证缩孔集中在冒口中,获得致密的铸件。
逐层凝固是指铸件某一断面上,先在铸件表面形成硬壳,然后它逐渐向铸件中心长厚,铸件中心最后凝固。
因此,顺序凝固和逐层凝固是两个不同的概念。
铸件的结构,以及由铸造条件所形成的温度场,是决定铸件凝固方向的主要因素,可用下例说明。
图8-9a是带冒口的板状铸件,厚度为δ,金属液从冒口浇入,即上注式。
右图是铸件纵截面上中心线的温度曲线及随时间变化情况。
因为金属液是从冒口
浇入的,所以中心线上A、B、C三点的温度依次向冒口方向递增,t
液—t
固
是
合金的凝固温度范围。
图8-9b表示该铸件A、B、C三点的横截面上径向温度分布及随时间变化情况。
横坐标为铸件厚度δ,纵坐标为温度。
横截面中心线上各点的温度,就是纵截面中心线上相应各点的温度。
由于铸件表面冷却快,横截面上内外有温度差,外表温度低。
可以近似地认为各点同一时刻的温度分布曲线是平行的。
在时刻I,A1、B1、C1三点温度都高于液相线温度t
液。
但在横截面B上,距铸件表面δB1处的温度已降至液相线C1温度;横截面C上,δC1处的温度降至液相线温度。
将δB1和δC1移植到图8-9c所表示的铸件纵截面上,并联接起来,即可得到时刻I的“等液相线”,以此类推,则得到不同时刻的“等液相线”。
同样方法可绘出各时刻的“等固相线”。
同一时刻的“等液相线”和“等固相线”之间的区域,是该时刻铸件的凝固区域。
“等液相线”之间的夹角称作“补缩通道扩张角φ”,也随时间变化。
向着冒口张开的φ
角范围内金属液都处于液态,形成“楔形”补缩通道,使冒口中的金属液有可能补缩到凝固区域中,φ角越大,则补缩通道越宽。
因此,顺序凝固的实质是采取各种措施,保证铸件在整个凝固过程中始终存在着和冒口连通的“补缩通道”,使冒口能发挥补缩作用(图8—9c)。
在铸件中,液固两相区与铸件壁热中心相交的线段为“补缩困难区μ”。
液固两相区越宽,扩张角φ越小,补缩困难区就越长(见图8—10)。
在液固两相区中,尤其在补缩困难区μ中,液相与固相之间的附着力往往大于液体本身的重量,而且存在于晶体骨架之间的液体以其附加压力反作用于补缩力,致使合金液在凝固终了以前便失去补缩能力。
因此,倾向于逐层凝固的共晶成分合金和结晶温度范围较小的合金,其等液相线和等固相线之间的凝固区域较窄,容易实现补缩。
相反,在相同的φ角条件下,结晶温度范围较宽的合金就不容易补缩。
在这种情况下,有时缩松不能完全转化为缩孔而集中到冒口中去。
顺序凝固的优点是,冒口补缩作用好,可以防止缩孔和缩松,铸件致密。
因此,对凝固收缩大,结晶温度范围较小的合金,常采用这个原则以保证铸件质量。
顺序凝固的缺点是,由于铸件各部分有温度差,在凝固期间容易产生热裂,凝固后也容易使铸件产生应力和变形。
顺序凝固原则需加冒口和补贴,工艺出品率较低,且切割冒口费工。
如果采取底注式浇注系统,由于铸件底部金属液流动时间长,金属液的温度最高,而上升到冒口中去的金属液温度最低。
因此,形成的纵向温度分布是远离冒口部分温度最高,冒口温度最低,形成反向的温度差,为“反顺序凝固”,如图8-11所示。
从图中可以看出,“补缩通道扩张角φ”在底注的情况下,是对着内浇口张开的。
所以补缩通道和浇口相通,而冒口和补缩通道之间充塞着凝固区域。
在这种情况下,凝固过程中液体可能被分割成两部分或更多部分,在铸件壁的热中心线上产生轴线缩松或区域性缩松。
根据以上分析,决定角φ方向、大小和变化速度的是铸件的纵向温度梯度。
据实验,对于板状铸钢件,纵向温度梯度应大于0.2~0.4℃/cm;对杆状铸钢件应为1.5~2℃/cm;对于某些宽结晶温度范围的有色合金铸件应为5.5~3℃/cm,可以消除缩松。
2、同时凝固(simultaneous solidification)
同时凝固原则是采取工艺措施保证铸件结构上各部分之间没有温差或温差尽量小,使各部分同时凝固。
在同时凝固条件下,扩张角φ等于零,没有补缩通道。
同时凝固原则的优点是,凝固时期铸件不容易产生热裂,凝固后也不易引起应力、变形;由于不用冒口或冒口很小,而节省金属,简化工艺、减小劳动量。
缺点是铸件中心区域往往出现缩松,铸件不致密。
因此,这种原则一般用
于以下情况:
(1)碳硅含量高的灰铸铁,其体收缩较小,甚至不收缩,合金本身就不易产生缩孔和缩松。
(2)结晶温度范围大,容易产生缩松的合金,(如锡青铜)对气密性要求不高时,可采用同时凝固原则,使工艺简化。
事实上,这种合金即使加冒口也很难消除缩松。
(3)壁厚均匀的铸件,尤其是均匀薄壁铸件,倾向同时凝固,消除缩松有困难,应采用同时凝固原则。
(4)球铁铸件利用石墨化膨胀力实现自身补缩时,则必须采用同时凝固原则。
(5)从合金性质看适宜采用顺序凝固原则的铸件,当热裂、变形成为主要矛盾时,也可以采用同时凝固原则。
以上介绍了两种凝固原则及其适用范围。
对于某一具体铸件,则要根据合金的特点、铸件的结构及其技术要求,以及可能出现的其它缺陷,如应力,变形、裂纹等综合考虑,找出主要矛盾,合理地确定采用哪种凝固准则。
应该指出,两种凝固方式在凝固顺序上虽然是对立的,但是在某个具体铸件上又可以将两者结合起来。
铸件结构一般比较复杂,例如,从整体看某个铸件壁厚均匀,但个别部位有热节。
所以,不能简单地采用顺序凝固或同时凝固方式,而往往是采用复合的凝固方式,亦即从整体上是同时凝固,为了个别部位的补缩,铸件局部是顺序凝固,或者相反。