铸钢件缩孔及缩松缺陷的消除
10步解决解决球墨铸铁件缩孔、缩松问题
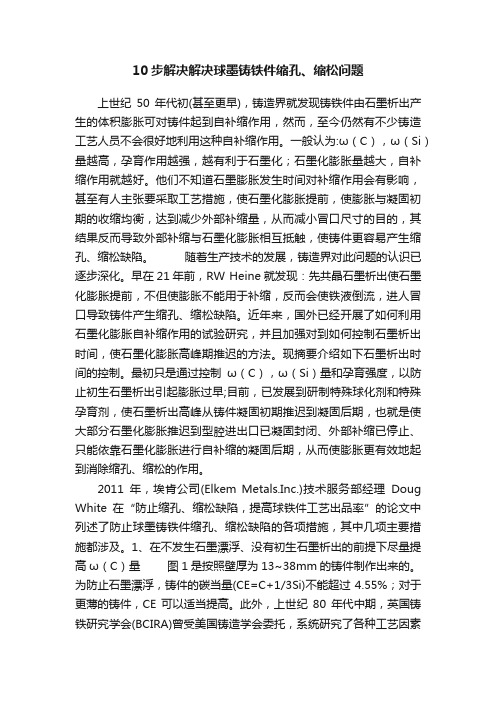
10步解决解决球墨铸铁件缩孔、缩松问题上世纪50年代初(甚至更早),铸造界就发现铸铁件由石墨析出产生的体积膨胀可对铸件起到自补缩作用,然而,至今仍然有不少铸造工艺人员不会很好地利用这种自补缩作用。
一般认为:ω(C),ω(Si)量越高,孕育作用越强,越有利于石墨化;石墨化膨胀量越大,自补缩作用就越好。
他们不知道石墨膨胀发生时间对补缩作用会有影响,甚至有人主张要采取工艺措施,使石墨化膨胀提前,使膨胀与凝固初期的收缩均衡,达到减少外部补缩量,从而减小冒口尺寸的目的,其结果反而导致外部补缩与石墨化膨胀相互抵触,使铸件更容易产生缩孔、缩松缺陷。
随着生产技术的发展,铸造界对此问题的认识已逐步深化。
早在21年前,RW Heine就发现:先共晶石墨析出使石墨化膨胀提前,不但使膨胀不能用于补缩,反而会使铁液倒流,进人冒口导致铸件产生缩孔、缩松缺陷。
近年来,国外已经开展了如何利用石墨化膨胀自补缩作用的试验研究,并且加强对到如何控制石墨析出时间,使石墨化膨胀高峰期推迟的方法。
现摘要介绍如下石墨析出时间的控制。
最初只是通过控制ω(C),ω(Si)量和孕育强度,以防止初生石墨析出引起膨胀过早;目前,已发展到研制特殊球化剂和特殊孕育剂,使石墨析出高峰从铸件凝固初期推迟到凝固后期,也就是使大部分石墨化膨胀推迟到型腔进出口已凝固封闭、外部补缩已停止、只能依靠石墨化膨胀进行自补缩的凝固后期,从而使膨胀更有效地起到消除缩孔、缩松的作用。
2011年,埃肯公司(Elkem Metals.Inc.)技术服务部经理Doug White在“防止缩孔、缩松缺陷,提高球铁件工艺出品率”的论文中列述了防止球墨铸铁件缩孔、缩松缺陷的各项措施,其中几项主要措施都涉及。
1、在不发生石墨漂浮、没有初生石墨析出的前提下尽量提高ω(C)量图1是按照壁厚为13~38mm的铸件制作出来的。
为防止石墨漂浮,铸件的碳当量(CE=C+1/3Si)不能超过4.55%;对于更薄的铸件,CE可以适当提高。
分析铸造缩松缺陷形成原因及对策

分析铸造缩松缺陷形成原因及对策铸造缩孔缺陷是在铸造过程中常见的一种问题,它会给制造业带来很多麻烦和损失。
本文将分析铸造缩孔缺陷的形成原因,并提出相应的对策,以期为相关行业提供帮助和指导。
一、铸造缩孔缺陷的形成原因分析1.1 完全凝固不均匀在铸造过程中,铸件凝固是逐渐进行的,如果凝固速度不均匀,就会导致缩孔缺陷的形成。
常见的原因包括铸件的凝固时间过短、冷却速度不均匀、局部温度过高等。
1.2 金属液收缩过大铸造过程中,金属液在凝固过程中会收缩,如果收缩过大,就容易形成缩孔。
这主要是由于铸件材料的物理性质不合理,或者是铸型的设计不合理所导致的。
1.3 铸造材料含有气体铸造材料中含有气体会在凝固过程中释放出来,如果释放过快,就会形成孔洞。
常见的原因是铸造材料中含有气体的含量过高,或者是在铸造过程中没有采取有效的排气措施。
1.4 基材与液态金属的相容性差如果铸件的基材与液态金属的相容性差,就容易在凝固过程中产生裂纹和缩孔。
一般来说,基材与液态金属的相容性差会导致界面张力增大,从而影响凝固过程。
二、对策提出2.1 优化铸造工艺参数通过优化铸造工艺参数,可以降低缩孔缺陷的发生概率。
具体来说,可以调整金属液的浇注温度和速度,控制铸件的凝固时间,改进冷却系统等措施。
2.2 优化铸造材料选择合适的铸造材料也是减少缩孔缺陷的关键。
应选择具有较低的收缩率和较好的流动性的材料,以确保凝固过程中的收缩程度可控。
2.3 采取有效的排气措施在铸造过程中,采取有效的排气措施可以减少气体对铸件凝固过程的干扰,从而降低缩孔缺陷的风险。
排气措施可以包括加入剂、提高浇注温度、采取适当的连续浇注等。
2.4 提高基材与液态金属的相容性为了减少缩孔缺陷的形成,可以通过提高基材与液态金属的相容性来增加界面的稳定性。
可以通过改变基材化学成分、调整金属液的配方等方式来实现。
三、结语以上是对铸造缩孔缺陷形成原因及对策的分析。
通过优化铸造工艺、材料选择、排气措施以及提高基材与液态金属的相容性等方法,可以有效降低缩孔缺陷的发生概率,提高铸件的质量和产能。
铸钢缩孔和缩松产生的原因及预防措施!
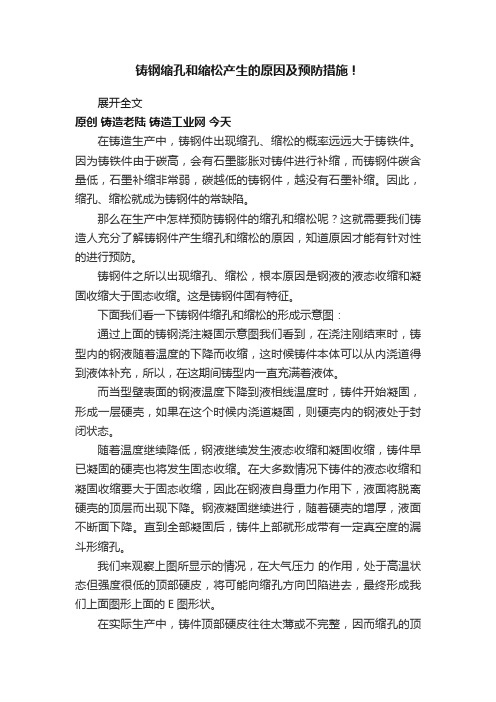
铸钢缩孔和缩松产生的原因及预防措施!展开全文原创铸造老陆铸造工业网今天在铸造生产中,铸钢件出现缩孔、缩松的概率远远大于铸铁件。
因为铸铁件由于碳高,会有石墨膨胀对铸件进行补缩,而铸钢件碳含量低,石墨补缩非常弱,碳越低的铸钢件,越没有石墨补缩。
因此,缩孔、缩松就成为铸钢件的常缺陷。
那么在生产中怎样预防铸钢件的缩孔和缩松呢?这就需要我们铸造人充分了解铸钢件产生缩孔和缩松的原因,知道原因才能有针对性的进行预防。
铸钢件之所以出现缩孔、缩松,根本原因是钢液的液态收缩和凝固收缩大于固态收缩。
这是铸钢件固有特征。
下面我们看一下铸钢件缩孔和缩松的形成示意图:通过上面的铸钢浇注凝固示意图我们看到,在浇注刚结束时,铸型内的钢液随着温度的下降而收缩,这时候铸件本体可以从内浇道得到液体补充,所以,在这期间铸型内一直充满着液体。
而当型壁表面的钢液温度下降到液相线温度时,铸件开始凝固,形成一层硬壳,如果在这个时候内浇道凝固,则硬壳内的钢液处于封闭状态。
随着温度继续降低,钢液继续发生液态收缩和凝固收缩,铸件早已凝固的硬壳也将发生固态收缩。
在大多数情况下铸件的液态收缩和凝固收缩要大于固态收缩,因此在钢液自身重力作用下,液面将脱离硬壳的顶层而出现下降。
钢液凝固继续进行,随着硬壳的增厚,液面不断面下降。
直到全部凝固后,铸件上部就形成带有一定真空度的漏斗形缩孔。
我们来观察上图所显示的情况,在大气压力的作用,处于高温状态但强度很低的顶部硬皮,将可能向缩孔方向凹陷进去,最终形成我们上面图形上面的E图形状。
在实际生产中,铸件顶部硬皮往往太薄或不完整,因而缩孔的顶部通常和能大气相通。
铸件凝固后期,在其最后凝固部分的残余钢液中,由于温度梯度小,金属液将同时凝固,即在钢液中出现许多细小的晶粒,当晶粒长大互相连接后,将剩余的钢液分割成互不相通的小熔池。
这些小熔池在进一步冷却和凝固时得不到液体的补缩,会产生许多细小的孔洞,这就是缩松。
缩松按糨的分布情况一般分为三种:一、弥散缩松,这种缩松是指细小的孔洞均匀分布在铸件的大部分体积内,易在结晶温度范围宽的合金铸件的冷却缓慢的厚大部位处产生。
铸件缩孔和缩松缺陷十点分析

铸件缩孔和缩松缺陷十点分析缩孔和缩松都是铸造生产中常见的铸件缺陷。
缩孔是铸件在冷凝过程中收缩,得不到金属溶液的补充而产生的孔洞,形状不规则,孔壁粗糙,一般位于铸件的热节处。
缩孔和气孔在外表上往往极为相似,经常容易混淆。
一般来说,气孔的内壁是平滑的,而缩孔的内壁则呈枝状结晶的末梢状。
缩松是铸件最后凝固的区域没有得到金属溶液的补缩而形成分散和细小的小孔,常出现在铸件的较厚截面以及厚薄截面交接处或热节点上。
缩松的分布面积要比缩孔大得多,往往隐藏于铸件的内部,有时肉眼察觉不到。
缩孔和缩松在铸件废品中占有较大的比例,必须引起足够的重视,以提高铸件合格率。
笔者结合多年的生产实践经验,谈谈铸件缩孔和缩松的产生原因及其防止措施。
1.铸件和模样设计(1)铸件截面尺寸变化过大。
如果在设计中铸件截面尺寸变化过大,薄截面的冷却速度比相邻厚截面的冷凝速度要快得多,这样就很难实现铸件的顺序凝固,同时也难于进行补缩。
设计时要尽量避免这种情况,否则应采用冷铁,以实现铸件的顺序凝固并利于补缩。
(2)铸件断面过厚,如果没有采取相应措施对其进行补缩,会因补缩不良形成缩孔。
(3)圆角太小。
铸件的凹角圆角半径太小,会导致型砂传热能力降低,凝固速度下降,同时由于该处型砂受热作用强,发气压力大,析出的气体可向未凝固的金属液渗入,导致铸件产生气缩孔。
(4)圆角太大。
圆角太大,则圆角部分就成了厚截面,如果相邻的截面较薄,就难以得到有效的补缩,造成补缩不良2.模样(1)模样或芯盒磨损致使铸件截面减薄,导致铸件截面厚度减薄而妨碍补缩。
(2)模样尺寸不当或模样结构不当,导致铸件截面过厚或过薄。
设计时应注意控制模样的厚度,尽量使邻近较厚截面的薄截面保持最大的厚度。
3.砂箱(1)上箱太浅。
生产中为了节省型砂用量或为了降低砂箱和造型成本而使用高度不够的上箱,这是造成缩松缺陷的常见原因。
上箱太浅,会降低金属液的静压力,以致难以进行补缩,补缩压力不够,会导致产生缩松或缩孔,或二者兼有之。
不锈钢铸件缩孔吐酸处理
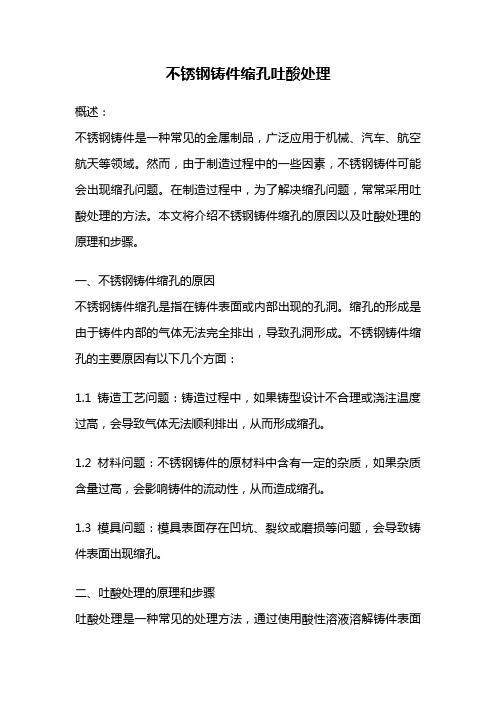
不锈钢铸件缩孔吐酸处理概述:不锈钢铸件是一种常见的金属制品,广泛应用于机械、汽车、航空航天等领域。
然而,由于制造过程中的一些因素,不锈钢铸件可能会出现缩孔问题。
在制造过程中,为了解决缩孔问题,常常采用吐酸处理的方法。
本文将介绍不锈钢铸件缩孔的原因以及吐酸处理的原理和步骤。
一、不锈钢铸件缩孔的原因不锈钢铸件缩孔是指在铸件表面或内部出现的孔洞。
缩孔的形成是由于铸件内部的气体无法完全排出,导致孔洞形成。
不锈钢铸件缩孔的主要原因有以下几个方面:1.1 铸造工艺问题:铸造过程中,如果铸型设计不合理或浇注温度过高,会导致气体无法顺利排出,从而形成缩孔。
1.2 材料问题:不锈钢铸件的原材料中含有一定的杂质,如果杂质含量过高,会影响铸件的流动性,从而造成缩孔。
1.3 模具问题:模具表面存在凹坑、裂纹或磨损等问题,会导致铸件表面出现缩孔。
二、吐酸处理的原理和步骤吐酸处理是一种常见的处理方法,通过使用酸性溶液溶解铸件表面的氧化物和杂质,从而改善铸件表面的质量。
在不锈钢铸件缩孔问题中,吐酸处理可以有效地清除铸件表面的缩孔,并提高铸件的整体质量。
2.1 吐酸处理的原理吐酸处理的原理是利用酸性溶液对铸件表面进行腐蚀,溶解表面的氧化物和杂质。
酸性溶液中的酸可以与氧化物反应生成可溶性盐类,从而清除铸件表面的缩孔。
2.2 吐酸处理的步骤吐酸处理的步骤主要包括以下几个方面:2.2.1 清洗铸件:首先需要将铸件进行清洗,去除表面的油污和杂质,以便酸性溶液能够更好地与铸件表面反应。
2.2.2 酸性溶液处理:将铸件浸泡在酸性溶液中,使酸性溶液充分接触到铸件表面。
酸性溶液的浓度和处理时间可以根据具体情况进行调整,以达到最佳的处理效果。
2.2.3 中和处理:在酸性溶液处理后,需要对铸件进行中和处理,以防止进一步的腐蚀。
中和处理可以通过用碱性溶液冲洗铸件表面来完成。
2.2.4 清洗和干燥:最后,需要对铸件进行清洗和干燥,以去除残留的酸性溶液和水分,确保铸件表面的干净和质量。
铸件产生缩孔、疏松的型壳补救措施
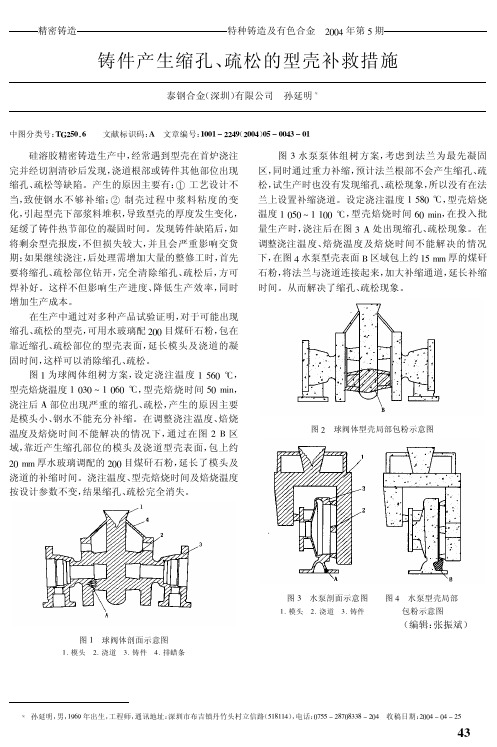
图 ’ 水泵泵体组树方案, 考虑到法兰为最先凝固 区, 同时通过重力补缩, 预计法兰根部不会产生缩孔、 疏 松, 试生产时也没有发现缩孔、 疏松现象, 所以没有在法 兰上设置补缩浇道。设定浇注温度 # $0" & , 型壳焙烧 型壳焙烧时间 %" )*+, 在投入批 温度 # "$" ( # #"" & , 量生产时, 浇注后在图 ’ , 处出现缩孔、 疏松现象。在 调整浇注温度、 焙烧温度及焙烧时间不能解决的情况 下, 在图 / 水泵型壳表面 - 区域包上约 #$ )) 厚的煤矸 石粉, 将法兰与浇道连接起来, 加大补缩通道, 延长补缩 时间。从而解决了缩孔、 疏松现象。
精密铸造
特种铸造及有色合金
!""/ 年第 $ 期
铸件产生缩孔、 疏松的型壳补救措施
泰钢合金 (深圳) 有限公司 孙延明!
中图分类号: !"#$% & ’
文献标识码: (#%%+) ( 文章编号: )%%) * ##+, %$ * %%+- * %)
硅溶胶精密铸造生产中, 经常遇到型壳在首炉浇注 完并经切割清砂后发现, 浇道根部或铸件其他部位出现 缩孔、 疏松等缺陷。产生的原因主要有: ! 工艺设计不 当, 致使钢水不够补缩; " 制壳过程中浆料粘度的变 化, 引起型壳下部浆料堆积, 导致型壳的厚度发生变化, 延缓了铸件热节部位的凝固时间。发现铸件缺陷后, 如 将剩余型壳报废, 不但损失较大, 并且会严重影响交货 期; 如果继续浇注, 后处理需增加大量的整修工时, 首先 要将缩孔、 疏松部位钻开, 完全清除缩孔、 疏松后, 方可 焊补好。这样不但影响生产进度、 降低生产效率, 同时 增加生产成本。 在生产中通过对多种产品试验证明, 对于可能出现 缩孔、 疏松的型壳, 可用水玻璃配 !"" 目煤矸石粉, 包在 靠近缩孔、 疏松部位的型壳表面, 延长模头及浇道的凝 固时间, 这样可以消除缩孔、 疏松。 图 # 为球阀体组树方案, 设定浇注温度 # $%" & , 型壳焙烧时间 $" )*+, 型壳焙烧温度 # "’" ( # "%" & , 浇注后 , 部位出现严重的缩孔、 疏松, 产生的原因主要 是模头小、 钢水不能充分补缩。在调整浇注温度、 焙烧 温度及焙烧时间不能解决的情况下, 通过在图 ! - 区 域, 靠近产生缩孔部位的模头及浇道型壳表面, 包上约 延长了模头及 !" )) 厚水玻璃调配的 !"" 目煤矸石粉, 浇道的补缩时间。浇注温度、 型壳焙烧时间及焙烧温度 按设计参数不变, 结果缩孔、 疏松完全消失。
铸钢件缩孔及缩松缺陷的消除
铸钢件缩孔及缩松缺陷的消除【摘要】通过分析铸钢件缩孔及缩松产生的机理,总结出铸件产生缩孔及缩松缺陷的部位,提出从改进浇注系统、改变铸件结构、适当提高浇注温度及控制浇注速度等几个方面消除铸件中的缩孔及缩松。
缩孔及缩松缺陷是铸钢件生产中的一大难题,长期以来困扰着广大铸造工作者。
这两种缺陷多发生在铸件内部,通过机械加工或X 射线检查可以发现,要进行挽救比较困难,也有发生在表面上的,通过安放冒口可以消除。
这两种缺陷很相似,危害都很大,可以归为一类。
由于缩孔及缩松缺陷的消除需要综合考虑浇注系统、浇注温度、铸件结构、冒口及冷铁等工艺因素,在实际生产中难以控制。
本文拟对铸钢件生产中出现的缩孔、缩松缺陷的消除作一探讨,供有关人员参考。
一、缩孔及缩松缺陷产生的机理铁液在铸型内冷凝的过程中,体积要发生三次收缩:第一次是合金液从浇注温度冷却到开始凝固的温度,称为液态收缩; 第二次是从开始凝固的温度冷却到金属液全部凝固的温度,称为凝固收缩; 第三次是从全部凝固的温度冷却到室温,称为固态收缩。
液态收缩的大小与浇注温度有关,铁液每降低100 ℃,体积约缩小0. 78 % ~1. 2 % ,因此浇注温度越高,液态收缩越大。
一般情况下,在能保证流动性的前提下,应尽量降低铁液的浇注温度。
液态及凝固收缩受合金成分的影响较大,比如,在其他成分相同的情况下,碳、硅含量越大,收缩就越小; 而锰、硫含量越多,则收缩量越大。
一般铸钢件在凝固收缩阶段的线收缩率为2.0 % ~3. 5 % ,因此在砂型铸造中制造模样时,除了加放一定的加工余量外,还要按铸造合金的收缩特性,加上一定量的合金收缩率。
当金属液进入型腔后,靠近型壁的金属液散热快,冷却速度快,而后向铸件中心逐次凝固。
铸件在冷却凝固的过程中,一般液态收缩时可以得到浇包中液态金属的补缩,这个阶段的收缩对铸件质量影响不大; 固态收缩对形成缩孔、缩松缺陷的影响也不大,但如果在凝固收缩时得不到补缩,就会在铸件最后凝固的部位( 如温度最高的中心处) 形成细小或分散的孔洞,即缩孔、缩松缺陷。
压铸件缩孔缩松的原因及解决办法
1.压铸件缩孔缩松现象存在的原因压铸件缩孔缩松现象产生的原因只有一个,那就是由于金属熔体充型后,由液相转变成固相时必然存在的相变收缩.由于压铸件的凝固特点是从外向内冷却,当铸件壁厚较大时, 内部必然产生缩孔缩松问题。
所以,就压铸件来说,特别是就厚大的压铸件来说,存在缩孔缩松问题是必然的,是不可以解决的。
640.webp (1).jpg2.解决压铸件缩孔缩松缺陷的唯一途径压铸件缩孔缩松问题,不能从压铸工艺本身得到彻底解决,要彻底解决这个问题,只能超越该工艺,或者说是从系统外寻求解决的办法。
这个办法又是什么呢?从工艺原理上说,解决铸件缩孔缩松缺陷,只能按照通过补缩的工艺思想进行.铸件凝固过程的相变收缩,是一种自然的物理的现象,我们不能逆这种自然现象的规律,而只能遵循它的规律,解决这个问题。
3.补缩的两种途径对铸件的补缩,有两种途径,一是自然的补缩,一是强制的补缩. 要实现自然的补缩,我们的铸造工艺系统中,就要有能实现“顺序凝固”的工艺措施.很多人直觉地以为,采用低压铸造方法就能解决铸件的缩孔缩松缺陷,但事实并不是这么回事.运用低压铸造工艺,并不等于就能解决铸件的缩孔缩松缺陷,如果低压铸造工艺系统没有设有补缩的工艺措施,那么,这种低压铸造手段生产出来的毛坯,也是可能百分之一百存在缩孔缩松缺陷的。
由于压铸工艺本身的特点,要设立自然的“顺序凝固”的工艺措施是比较困难的,也是比较复杂的.最根本的原因还可能是, ”顺序凝固”的工艺措施,总要求铸件有比较长的凝固时间,这一点,与压铸工艺本身有点矛盾。
强制凝固补缩的最大特点是凝固时间短,一般只及”顺序凝固”的四分之一或更短,所以,在压铸工艺系统的基础上,增设强制的补缩工艺措施,是与压铸工艺特点相适应的,能很好解决压铸件的缩孔缩松问题。
4.强制补缩的两种程度挤压补缩和锻压补缩实现铸件的强制补缩可以达到有两种程度.一种是基本的可以消除铸件缩孔缩松缺陷的程度,一种是能使毛坯内部达到破碎晶粒或锻态组织的程度.如果要用不同的词来表述这两种不同程度话,那么,前者我们可以用“挤压补缩”来表达,后者,我们可以用“锻压补缩”来表达。
铸铁件缩孔和缩松缺陷防止方法及应用实例
DOI 1. 6  ̄i n10 - 3 52 1.1 1 :03 9 .s. 3 84 . 20 . 2 9 s 0 0 0
M e h d o Pr v n h i k g v t n o o i  ̄e fI o si sa d Th i p ia i n Ex mp e t o s t e e t r n a e Ca i a d P r st De to r n Ca t S y y ng n er Ap l to a c ls
而 由于 Mg 大 铁液 的收缩 倾 向 , 防止 缩松 考 增 从
虑 , Mg 量应越 低越好 ; ( 残) 兼顾 到工 艺控 制 的难
采用冷却筋 、 散热片和导热率高 的型砂 、 芯砂局 部加速冷却等。 以下是笔者公司使用这些方法解
决缩 孔缩 松缺 陷 的实例 。
度 , 际生产 中一 般采 用 的控制 范 围为 005 实 .3%~
决 。要 注 意 的是 , 种方 法 只适用 于缩 松 或者 显 这
微缩松 比较轻微 , x射线检查没有发现每个铸件
都 有这种 缺 陷 , 就是 出现 缩松 缺陷 的铸 件 比例 也
不 高时 。 21 化 学成分 方面 的控 制 .
( ) 当提 高 C C 1适 E。 E高 , 铁液 凝 固过程 中石
与x射线 相 结合 的检 测 方法 ; 批量 生 产过 程 中一
关键部位有一定大小 的缩松缺陷存在 , 而在关键
部位 则仍 然 不允许 有 缩 松缺 陷 。例 如 , 动钳 壳 制 体 的活塞 缸部 位是 不 允许 有 缩孔 缺 陷 的 , 否则 使 用过 程 中会 出现 制 动漏 油等 致命 问题 , 而在 背脊 部位 可 以 出现 一定 大 小 的缺 陷 , 不 能影 响 产 品 但
解决铸件缩松缺陷的方法
解决铸件缩松缺陷的方法大型铸件:解决铸件缩松缺陷的方法,最根本的着眼点就是“热平衡”。
其方法是:(1)在机床铸件结构形成的厚处与热节处,实行快速凝固,人为地造成机床铸件各处温度场的基本平衡。
(2)合理的工艺设计。
内浇道设在机床铸件相对溥壁处,数时多且分散。
使最早进入厚壁处的金属液率先凝固,薄壁处后凝固,使各处基本达到均衡凝固。
对于壁厚均匀的机床铸件,采用多个内浇道和出气孔。
(3)选用蓄热量大的造型材料,这对用消失模生产抗磨产品极为重要!铬铁矿砂取代石英砂等蓄热量小的其它砂种,会取得良好的效果,浇毕微震更优!(4)球铁的机床铸型强度大,表面硬度≧90,砂箱刚性大,对消除缩松有利。
(5)需要冒口时,当首迁热冒口,且离开热节。
若将冒口置于热节上,必将加大冒口尺寸,形成“热上加热”。
弄不好,非但缩松难除,还会产生集中性缩孔,又降低了工艺出品率。
(6)。
大型铸件的材料铸件的材料不同,铸造收缩率也不同。
例如,铸钢的收缩率比灰铸铁大;灰铸铁中硫多时,收缩率增大,硅多时收缩率减小。
(7)大型铸件优先采用砂型铸造,材质为优质的高强度铸铁HT250-300,可承接单件60吨左右的铸件,抗拉力强、制造合理、结构稳定、精度高、耐磨损、使用寿命长。
(8)大型铸件的铸造方法常用的是砂型铸造,其次是特种铸造方法,如:金属型铸造、熔模铸造、石膏型铸造等。
而砂型铸造又可以分为粘土砂型、有机粘结剂砂型、树脂自硬砂型、消失模等等。
大型铸件的铸造采用砂型铸造是因为铸造方法成本低、生产工艺简单、生产周期短。
(9)大型铸铁的分类:大型床身、机床床身铸件、龙门铣床身铸件、端面铣床、T型槽地轨、基础垫铁、床身立柱、床身铸件。
- 1、下载文档前请自行甄别文档内容的完整性,平台不提供额外的编辑、内容补充、找答案等附加服务。
- 2、"仅部分预览"的文档,不可在线预览部分如存在完整性等问题,可反馈申请退款(可完整预览的文档不适用该条件!)。
- 3、如文档侵犯您的权益,请联系客服反馈,我们会尽快为您处理(人工客服工作时间:9:00-18:30)。
"
( $ ) 对于形状复杂,有多个热节的铸件,一般采用
内浇口与冒口相结合的方法来进行补缩,浇注系统设计 多采用底注式或侧注式,即将铸件较小热节放置在浇注 系统底部或侧面,内浇口设置在这些热节处,浇注时金 属从铸型底部平稳注入, 使铸型中气体和杂质容易排 出,在铸件顶部较大热节处设置冒口进行补缩。 如图 & 所示为某铸件的浇注系统。
图 )" 工艺补贴的应用
对于铸件上的某些局部热节,为使其早凝固或整个 铸件同时凝固,冷铁放置于热节部位或热节附近。在不 宜安放冒口的厚大部位一般均应放冷铁。由于冷铁没有 补缩作用,铸件和热节的补缩仍由冒口供给,通常冷铁 位置的确定应和冒口位置同时考虑,使铸件凝固时沿着 从安放冷铁部位向冒口方向顺序凝固。 在断面过于突 出,既不易放外冷铁,又不能安放冒口的地方,可以考 虑使用内冷铁。内冷铁的大小与铸件质量有很大关系, 太小不起作用,太大则不能完全与铁液熔合在一起,影 响铸件力学性能。另外,内冷铁与浇注的金属液材质应 相同且应洁净。
三、缩孔及缩松缺陷的防止措施
要使铸钢件在凝固过程中不产生缩孔及缩松缺陷, 必须将铸件最后凝固的部位引出铸件本体,这就需要在 铸件内形成顺序凝固的温度梯度,使金属液从较低温度 开始凝固,而最后凝固的部位在冒口中。生产中常用的 方法有以下几种。 $% 使用冒口 在浇注一般的小铸钢件或结构简单的小型铸件时, 有无冒口影响不大, 因为铸钢件自身有一定的补缩能 力。而当铸钢件较复杂时,冒口的作用就比较明显。 冒口有明冒口和暗冒口两种。 明冒口暴露在空气 中,冷却速度快,浇注一段时间后就凝固了,使冒口中 的金属液与外界隔离,降低了冒口的补缩效率,对此可
热加工
-’ !""# 年第 $ 期 !!!! "#$%&’&()! $*"! $’"
铸" " 造 !"#$%&’
在浇注的最后阶段,将一部分金属液由冒口浇入,以强 化冒口的补缩效果。冒口的位置需根据铸件壁厚和冷却 的情况而定,应设置在铸件最后凝固的部位。冒口的断 面一般为被补缩断面的 #! $ % & 倍, 冒口的高度应为其 直径的 #! $ % &! $ 倍,才能保证补缩效果。 实际上,冒口的计算是一个很复杂的问题,铸造工 作者提出了多种不同的方法,各有利弊,需要有一定的 实践经验。 !% 选择合适的内浇口位置 内浇口的位置对铸件是否产生缩孔及缩松缺陷的影 响很大,因为合适的内浇口位置能够形成顺序凝固,避 免缺陷的产生。 ( # ) 铸件高度较小而水平尺寸较大时,导入位置一 般应保证铸件横向的顺序凝固, 内浇口应设于铸件厚 处,使合金液从厚处导入。 ( & ) 铸件壁厚较大且均匀时,为了保证铸件整体的 同时凝固和避免浇不足,合金液应从铸件四周通过较多 内浇口均匀地导入,在铸件各区域的最后凝固处设置冒 口,以便补缩。 ( ’ ) 铸件有一定高度时,则应首先保证自下而上的 顺序凝固,而水平方向上同时凝固,内浇口位置应尽可 能使水平方向的温度分布均匀,通常把内浇口设置在铸 件的薄壁处,且在厚壁部分放置冷铁。另外,在不破坏 铸件顺序凝固的前提下, 内浇口数量宜多些且均匀分 布,以避免局部过热。 ( ( ) 对于熔模铸造中的小型简单铸钢件,应尽量选 择通过内浇口补缩铸件, 以提高浇注系统的金属利用 率,即将内浇口设置在铸件热节部位,以利于补缩。浇 注系统一般采用顶注式或侧注式, 如某铸件采用图 #) 方案时,热节 ( 处产生缩松,而采用图 #* 方案时, 通 过内浇口向热节 ( 处补缩,消除了缩松。
ห้องสมุดไป่ตู้
缩对形成缩孔、缩松缺陷的影响也不大,但如果在凝固 收缩时得不到补缩,就会在铸件最后凝固的部位 ( 如温 度最高的中心处) 形成细小或分散的孔洞,即缩孔、缩 松缺陷。
二、缩孔及缩松缺陷产生的部位
实际生产中,有时候要区分是缩孔还是气孔或是夹 渣缺陷,并不是很容易,需要综合考虑铸件的结构因素 来判断。总结起来,缩孔及缩松缺陷在铸件上产生的部 位肯定是最后凝固的地方,而导致最后凝固主要有以下 两种情况: ( $ ) 最常见是发生在铸件断面突增或铸件几何热节 的部位,因为这些地方金属液的散热最慢,最后凝固而 形成缺陷。 ( + ) 并非是铸件的几何热节,而是因为金属液长时 间流经某处,使该处过热,也会产生缩孔及缩松缺陷, 通常称之为物理热节。
图 &" 底注式浇注系统
&% 控制浇注速度 从理论上讲,金属液进入砂型时,热量的散失和金 属液与型壁接触的时间长短成正比,且与金属液的表面 积和体积的比率成正比。浇注速度影响金属液接触型壁 的时间,因此控制浇注速度可改变铸件内的温度差,浇 注速度越慢,铸件内的温度差越大。但速度不能太慢, 否则容易形成冷隔、浇不满等缺陷。而大平面的铸件不 宜慢浇,否则会导致上型由于长时间受热出现落砂缺陷。 ’% 修改铸件结构 对于结构比较复杂、铸造工艺性差的铸钢件,仅靠 从浇注系统设计方面出发,无法完全消除缩孔与缩松, 为了获得高质量的铸件,可与机械加工单位协商,适当 改变铸件结构,从而改善铸件的工艺性能。主要方法有 以下两种: ( # ) 增加工艺补贴" 为了保证顺序凝固,有利于冒 口补缩,在冒口与热节之间增加工艺补贴,一般在机械 加工时被切除。 由于工艺补贴的存在, 加大了补缩通 道,使补缩通道迟于热节部位凝固,使铸件实现顺序凝 固。如图 ’) 所示,该铸件为均匀厚壁,在工艺试制时, 虽采取多种方案,都因冒口无法对铸件中部热节 ( 处进 行有效补缩,而在此处产生缩孔。后在冒口与热节之间 ,从而彻底 增加了 &+,, 宽的工艺补贴( 如图 ’* 所示 )
中因为补缩铸件下部而产生缩孔与缩松。对于壁厚不均 匀的铸件,只要浇注位置选择合适,浇注系统工艺参数 设计合理,可以实现铸件的自补。 ’& 选择合适的浇注温度 提高浇注温度能在一定条件下提高金属液的补缩能 力,但要根据铸件的具体情况分析。对于熔模铸造,温 , 均可 度的提高( 包括提高浇注温度和型壳焙烧温度 ) 使热节前方的补缩通道推迟凝固,延长了补缩距离,因 而有利于消除缩孔。但是,提高浇注温度,可能会使内 浇口处过热而产生缩松,所以要辩证地看待提高浇注温 度。在熔模铸造中减缓铸件的冷却,也是消除缩孔的一 个有效途径,一般采用填砂造型的方法,这样可使补缩 通道凝固较缓慢,补缩能力更强。但由于填砂造型后, 金属冷却较慢,铸件中位于同时结晶的区域较宽,易在 铸件表面形成分散缩松,故对填砂造型铸件,应选择合 适的浇注系统来避免这种情况。 #& 合理使用冷铁 固体金属吸收热量的性能比型砂或型壳快得多,因 此在铸件的转角及断面突增处常放置冷铁。冷铁使用的 方法有两种:一种放置在铸件外部,称为外冷铁;另一 种放在铸件的内部与金属液凝结在一起,称为内冷铁。
" " 缩孔及缩松缺陷是铸钢件生产中的一大难题,长期 以来困扰着广大铸造工作者。这两种缺陷多发生在铸件 内部,通过机械加工或 # 射线检查可以发现,要进行挽 救比较困难,也有发生在表面上的,通过安放冒口可以 消除。这两种缺陷很相似, 危害都很大, 可以归为一 类。由于缩孔及缩松缺陷的消除需要综合考虑浇注系 统、浇注温度、铸件结构、冒口及冷铁等工艺因素,在 实际生产中难以控制。本文拟对铸钢件生产中出现的缩 孔、缩松缺陷的消除作一探讨,供有关人员参考。
四、结语
图 $" 加工余量的应用
( & ) 铸钢件缩孔与缩松缺陷产生的部位有两种情 况,一是铸件的厚大部位及几何热节得不到补缩;二是 由于铸件某部位长时间过热。 ( # ) 防止铸钢件产生缩孔、 缩松缺陷可从浇注系 统、浇注温度、铸件结构等几个方面来完善。"
( #--’-.&- )
%& 铸件的自补 对于大型厚壁铸钢件,在浇注系统设计时,应充分 利用铸件的自补。这类铸件多采用顶注式浇注系统,钢 液从铸件上部流到下部要经过较长的流程,因浇注温度 与室温的差异,当钢液进入下部厚壁处时,其温度已接 近凝固温度,而铸件上部依然温度较高,这样就形成了 自下而上的顺序凝固,不会使铸件厚大部位在凝固过程
!"#$%&’
铸" " 造
铸钢件缩孔及缩松缺陷的消除
南昌航空工业学院材料科学与工程学院 ! ( 江西! ""##"$ ) ! 聂小武
" " 【 摘要】 " 通过分析铸钢件缩孔及缩松产生的机理,总结出铸件产生缩孔及缩松缺陷的部位,提出从改
进浇注系统、改变铸件结构、适当提高浇注温度及控制浇注速度等几个方面消除铸件中的缩孔及缩松。
热加工
/. !""# 年第 $ 期 !!!! "#$%&’&()! $*"! $’"
一、缩孔及缩松缺陷产生的机理
铁液在铸型内冷凝的过程中, 体积要发生三次收 缩:第一次是合金液从浇注温度冷却到开始凝固的温 度,称为液态收缩;第二次是从开始凝固的温度冷却到 金属液全部凝固的温度,称为凝固收缩;第三次是从全 部凝固的温度冷却到室温,称为固态收缩。 液态 收 缩 的 大 小 与 浇 注 温 度 有 关, 铁 液 每 降 低 $%%& ,体积约缩小 %! ’() * $! +) , 因此浇注温度越 高,液态收缩越大。一般情况下,在能保证流动性的前 提下,应尽量降低铁液的浇注温度。液态及凝固收缩受 合金成分的影响较大, 比如, 在其他成分相同的情况 下,碳、硅含 量 越 大, 收 缩 就 越 小; 而 锰、 硫 含 量 越 多,则收缩量越大。一般铸钢件在凝固收缩阶段的线收 缩率为 +! %) * ,! -) , 因此在砂型铸造中制造模样时, 除了加放一定的加工余量外,还要按铸造合金的收缩特 性,加上一定量的合金收缩率。 当金属液进入型腔后,靠近型壁的金属液散热快, 冷却速度快,而后向铸件中心逐次凝固。铸件在冷却凝 固的过程中,一般液态收缩时可以得到浇包中液态金属 的补缩,这个阶段的收缩对铸件质量影响不大;固态收