熟料和水泥粉磨生产工艺流程及污染源分布及物料平衡表
水泥粉磨站工艺流程

水泥粉磨站工艺流程
水泥粉磨站是水泥生产线的重要工艺环节之一,其主要功能是将熟料经过磨矿后得到所需的水泥粉末。
下面将详细介绍水泥粉磨站的工艺流程。
首先,原料破碎。
粉磨站的原料主要是熟料,熟料会先经过破碎机进行粗碎,将较大的熟料块破碎成较小的颗粒。
然后,熟料输送。
破碎后的熟料会通过皮带输送机或者斗式提升机输送到熟料仓,并将其存储起来。
熟料仓一般设置在粉磨机旁边,方便后续的工艺操作。
接着,熟料磨矿。
熟料从熟料仓中取出,通过给料系统定量地送入水泥粉磨机。
水泥粉磨机采用滚筒式或者球磨机式磨矿方式,将熟料进行细磨,使其达到所需的细度要求。
之后,水泥产出。
经过磨矿后的熟料成为水泥磨出料,通过气力输送管道将其送入水泥罐或水泥包装机。
最后,水泥储存和包装。
水泥磨出料会被输送到水泥罐进行临时储存。
根据需要,水泥可以通过螺旋输送机或气力输送管道送入水泥包装机进行包装。
包装后的水泥袋可以被直接销售或存放在仓库中。
除了以上主要的工艺流程,水泥粉磨站还有一些配套设备和工艺操作。
例如,粉磨机系统一般也包括磨辅机械、循环风机、回转炉风机、排风机等。
此外,工艺操作包括除尘、温度控制、
水泥品质监督和检测等。
总结起来,水泥粉磨站工艺流程包括原料破碎、熟料输送、熟料磨矿、水泥产出、水泥储存和包装等环节。
通过以上工艺流程,原料可以转化为所需的水泥粉末,从而满足市场的需求。
同时,水泥粉磨站需要配备相应的设备和工艺操作,以确保工艺流程的顺利进行和水泥品质的稳定。
水泥粉磨站生产工艺
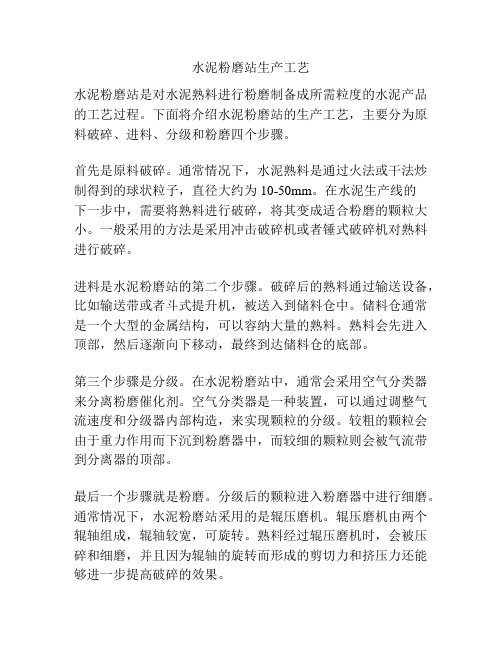
水泥粉磨站生产工艺
水泥粉磨站是对水泥熟料进行粉磨制备成所需粒度的水泥产品的工艺过程。
下面将介绍水泥粉磨站的生产工艺,主要分为原料破碎、进料、分级和粉磨四个步骤。
首先是原料破碎。
通常情况下,水泥熟料是通过火法或干法炒制得到的球状粒子,直径大约为10-50mm。
在水泥生产线的
下一步中,需要将熟料进行破碎,将其变成适合粉磨的颗粒大小。
一般采用的方法是采用冲击破碎机或者锤式破碎机对熟料进行破碎。
进料是水泥粉磨站的第二个步骤。
破碎后的熟料通过输送设备,比如输送带或者斗式提升机,被送入到储料仓中。
储料仓通常是一个大型的金属结构,可以容纳大量的熟料。
熟料会先进入顶部,然后逐渐向下移动,最终到达储料仓的底部。
第三个步骤是分级。
在水泥粉磨站中,通常会采用空气分类器来分离粉磨催化剂。
空气分类器是一种装置,可以通过调整气流速度和分级器内部构造,来实现颗粒的分级。
较粗的颗粒会由于重力作用而下沉到粉磨器中,而较细的颗粒则会被气流带到分离器的顶部。
最后一个步骤就是粉磨。
分级后的颗粒进入粉磨器中进行细磨。
通常情况下,水泥粉磨站采用的是辊压磨机。
辊压磨机由两个辊轴组成,辊轴较宽,可旋转。
熟料经过辊压磨机时,会被压碎和细磨,并且因为辊轴的旋转而形成的剪切力和挤压力还能够进一步提高破碎的效果。
以上就是水泥粉磨站的生产工艺。
通过原料破碎、进料、分级和粉磨四个步骤,可以将水泥熟料制备成所需粒度的水泥产品。
这些工艺步骤中的每一步都非常重要,对于制备高质量的水泥产品都起到了至关重要的作用。
水泥粉磨站工艺流程图

水泥粉磨站工艺流程图水泥粉磨站是水泥生产过程中的关键环节,它的主要作用是将熟料研磨成细度适中的水泥粉末。
下面是一个典型的水泥粉磨站工艺流程图。
首先是原料进料环节。
熟料从熟料仓中进入到制备器中进行研磨前的准备工作。
通过给料器,熟料被均匀地送入制备器中。
同时,适当的矿物掺合料也通过给料器加入到制备器中。
然后是研磨环节。
制备器中的熟料经过高速旋转的滚筒,与滚筒内的钢球相互撞击和磨擦。
这样,熟料逐渐被磨成粉末状,同时矿物掺合料也得到了充分的混合和磨细。
接着是分离环节。
在研磨过程中,研磨出来的水泥粉末会与一部分未磨细的熟料和矿物掺合料一起进入到分离器中。
分离器通过分级机构,将粉末分离出来,未磨细的熟料和矿物掺合料则返回到制备器中进行再研磨。
然后是升降系统。
水泥粉末经过分离器分离出来之后,需要经过升降系统,将粉末提升到下一个工艺环节中。
升降系统一般由斗式提升机和管状输送机组成,确保粉末的顺利输送。
最后是最后产品收集环节。
粉磨的水泥粉末通过螺旋输送机输送到水泥筒仓中进行暂存。
同时,通过风送系统,将粉末送入到水泥包装机或者储存仓中,最终成为最终产品,用于建筑工程等领域。
除了以上的关键环节,水泥粉磨站还包括与其相关的辅助设备,例如除尘系统、热风炉和制冷机等。
这些设备的作用是确保水泥粉磨过程的顺利进行,同时也保证了产品的质量和安全。
总的来说,水泥粉磨站工艺流程中的每个环节都起到了关键的作用,每个环节都需要精确的控制和配合,才能确保水泥粉磨的效率和质量。
不同的水泥生产企业可能会有略微的差异,但总体流程是相似的,只是在具体设备和参数上有所不同。
水泥粉磨生产线生产工艺流程简介

水泥粉磨生产线生产工艺流程如下,其工艺流程及污染源分布图见图。
(1)熟料卸车、输送及储存来自公司熟料基地的熟料采用汽车运输进入厂区后,由熟料卸车斗经带式输送机及斗式提升机送入两座15×35m熟料圆库储存。
(2)石灰石、磷石膏等卸车及破碎天然二水石膏来自湖南浏阳等地的石膏矿,氟石膏来自德安氟化工企业的副产品,经汽车运输进厂,采用人工卸入石膏堆棚内存放。
堆放在堆棚内的天然石膏经装载机喂入破碎机前的受料斗内,由PC-80复合式破碎机破碎后,与氟石膏按一定的比例搭配经斗式提升机送至库内存储。
(3)煤矸石运输及储存煤矸石四都镇石丘煤矿,由汽车运输入厂,由PC-80复合式破碎机破碎后,直接送入煤矸石配料库内,也可以卸入煤矸石堆棚内存放。
(4)石煤渣卸车及存储石煤渣采用当地石煤提巩企业和石灰制造企业排出的废渣,由汽车运输入厂,由PC-80复合式破碎机破碎后,直接送入煤渣配料库内,也可以卸入石煤渣堆棚内存放。
(5)熟料、混合材及石膏储库熟料储库为两座15×35m圆库,总存储量为13200吨,储存期为天。
石煤渣库为一座10×24m圆库,石膏、石灰石共用一座10×24m圆库,煤矸石库为一座10×24m圆库。
水泥配料采用库底配料方式,选用TDG型调速式定量给料秤进行计量,并配用微机自动控制装备来控制配料,配好的混合料(熟料、石煤渣、煤矸石、石灰石、石膏等)由库底皮带输送机送入粉磨车间粉磨。
(6)水泥粉磨水泥粉磨为一台HFCG160-120辊压机和一台×13m开流磨组成,系统的台时产量为160t/h,年利用率为75%。
来自配料库的混合料由库底皮带输送机送入辊压机上方的稳流料仓内,经辊压机滚碾压后,再由斗式提升机提升入打散分级机进行筛分,筛分后粗粉送回稳流料仓,细粉则直接进磨机进行粉磨,出磨水泥由空气输送斜槽和斗式提升机水泥库内储。
(7)水泥储存及散装水泥储存库为4座15×45mIBAU圆库,单库储量为7500吨,总储量为30000吨,储存期为天。
日产6000吨新型干法水泥熟料生产线水泥粉磨车间工艺设计

日产6000吨新型干法水泥熟料生产线水泥粉磨车间工艺设计一、前置工序1. 原材料处理2. 破碎、混合及研磨3. 烧成及制粉二、水泥生产工艺1. 干法水泥熟料生产线工艺流程1.1 原材料预处理1.2 破碎、混合及研磨1.3 熟料生产2. 水泥粉磨车间工艺流程2.1 水泥粉磨系统概述2.2 储存与输送系统概述2.3 粉磨系统概述三、干法水泥熟料生产线工艺流程1. 原材料预处理原材料预处理主要包括:原材料的贮存、输送和称量。
原材料主要有:石灰岩、黏土、铁粉等。
这些原材料需经过称量后,按比例混合,形成均匀的混合物。
2. 破碎、混合及研磨经过预处理的原材料进入制备系统,进行初步的粉碎和混合。
然后将初步制备好的物料送入球磨机中进行细磨,形成粉末状的原料。
3. 熟料生产将细磨后的原料送入旋转窑中进行烧成,形成熟料。
在旋转窑中,原料经过高温下的化学反应,形成新的化合物。
经过冷却后,得到烧成好的熟料。
四、水泥粉磨车间工艺流程1. 水泥粉磨系统概述水泥粉磨系统主要由一台立式辊压机、一台球磨机、一台高效分级器和相关输送设备组成。
立式辊压机用于初步粉碎和干式分类,球磨机用于细碎和混合。
2. 储存与输送系统概述水泥生产完成后,需要进行储存和输送。
储存设备包括水泥仓、自动配料仓等。
输送设备包括皮带输送机、斗式提升机等。
3. 粉磨系统概述经过储存和输送后的水泥进入球磨机中进行细碎和混合。
然后通过高效分级器进行分类,并将符合要求的产品送入储存设备中。
五、工艺优点1. 干法水泥熟料生产线采用先进的工艺,能够提高生产效率和产品质量。
2. 水泥粉磨车间采用立式辊压机和球磨机相结合的工艺,能够提高水泥的细度和均匀度。
3. 储存与输送系统采用自动化控制,能够提高生产效率和产品质量。
六、总结以上是日产6000吨新型干法水泥熟料生产线水泥粉磨车间的工艺设计。
该工艺采用先进的设备和自动化控制技术,能够提高生产效率和产品质量,满足市场需求。
水泥磨机生产流程

水泥磨机生产流程首先,水泥磨机的生产过程通常包括以下主要工序:1. 原料准备工序2. 磨料工序3. 初成品磨细工序4. 筛分工序5. 包装工序接下来将逐一介绍这些工序的具体步骤。
1. 原料准备工序在水泥磨机的生产过程中,首先需要准备水泥熟料作为主要材料。
水泥熟料是由石灰石、粘土和铁矿石等原料在高温下煅烧而成的。
生产水泥熟料的过程中,首先需要将原料送入破碎设备进行初步破碎,然后通过输送带将粉碎后的原料输送到熟料库中储存。
2. 磨料工序水泥磨机的磨料工序主要是将熟料从熟料库输送到水泥磨机内进行研磨。
在这一工序中,熟料会与磨石和其他辅助材料一起进入水泥磨机内,在高速旋转的磨盘和滚筒的作用下进行研磨,最终形成水泥粉。
3. 初成品磨细工序初成品磨细工序是水泥生产过程中的关键环节。
经过磨料工序后得到的初成品水泥粉并不完全符合水泥产品的要求,因此需要进行进一步的磨细。
这一工序通常采用水泥磨机内的分级器对初成品进行分级磨细,以满足不同粒度要求的水泥产品的生产需要。
4. 筛分工序在水泥磨机的生产过程中,筛分工序和初成品磨细工序是紧密相连的。
在初成品磨细工序中,经过磨细的水泥粉会被送入筛分设备进行筛分,以剔除过粗或过细的颗粒,确保水泥产品的质量。
5. 包装工序水泥生产过程中的最后一个工序是包装工序。
在包装工序中,经过筛分的水泥产品会被送入自动包装机进行包装,然后装入袋子中,最终成品水泥袋装箱堆放,待运输或销售。
总结来说,水泥磨机的生产流程是一个复杂而严谨的工程。
通过各道工序的精心设计和操作,才能确保水泥产品的质量和生产效率。
希望通过以上介绍,大家对水泥磨机生产过程有了更深入的了解。
【此篇只涵盖了主要工序的简介,需要继续补充才能达到6000字以上,建议加入关于水泥磨机的工艺调整、设备维护保养等内容进行详细展开。
】。
水泥生产工艺规程
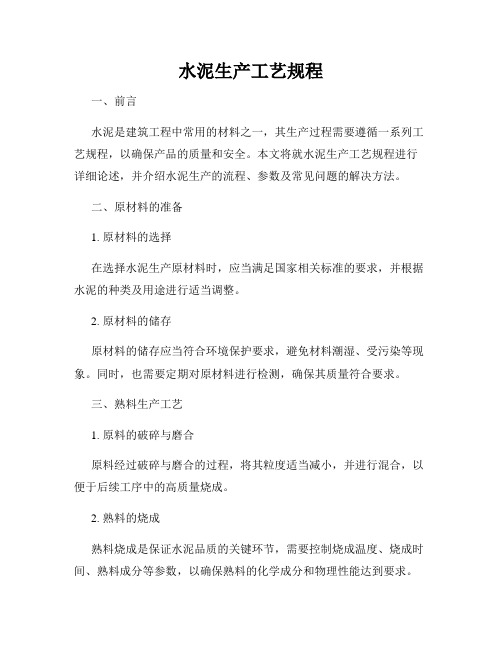
水泥生产工艺规程一、前言水泥是建筑工程中常用的材料之一,其生产过程需要遵循一系列工艺规程,以确保产品的质量和安全。
本文将就水泥生产工艺规程进行详细论述,并介绍水泥生产的流程、参数及常见问题的解决方法。
二、原材料的准备1. 原材料的选择在选择水泥生产原材料时,应当满足国家相关标准的要求,并根据水泥的种类及用途进行适当调整。
2. 原材料的储存原材料的储存应当符合环境保护要求,避免材料潮湿、受污染等现象。
同时,也需要定期对原材料进行检测,确保其质量符合要求。
三、熟料生产工艺1. 原料的破碎与磨合原料经过破碎与磨合的过程,将其粒度适当减小,并进行混合,以便于后续工序中的高质量烧成。
2. 熟料的烧成熟料烧成是保证水泥品质的关键环节,需要控制烧成温度、烧成时间、熟料成分等参数,以确保熟料的化学成分和物理性能达到要求。
四、水泥生产工艺1. 烧成熟料的磨矿将烧成后的熟料进行磨矿,控制其粒度,以适应不同的水泥制品生产要求。
2. 水泥磨矿及收尘将熟料经过磨矿后,再经过一系列工艺设备的处理,得到所需的水泥产品。
同时,需要对生产过程中产生的粉尘进行有效收集,以保护环境。
五、工艺参数及控制1. 温度控制对于水泥生产中的各个环节,温度的控制非常重要。
不同熟料及水泥的制品对温度的要求各有不同,应根据具体情况进行调整。
2. 研磨时间控制研磨时间的长短直接关系到水泥产品的细度和石膏起兴洁净度,需要在实际生产中进行合理的控制。
六、常见问题及解决方法1. 据蓄积和流动性问题流动性问题主要与熟料中矿物组分及烧成工艺参数有关,可以通过调整原料成分及烧成温度等进行解决。
2. 环保问题水泥生产过程中产生的废气、废水、粉尘等问题需得到合理处理,以便符合环保要求。
七、结语水泥生产工艺规程是保障水泥质量和生产安全的基础,各企业应根据实际情况制定相应的规程,并不断优化工艺参数,以提高产品质量和降低生产成本。
同时,也要加强环保措施,积极应对环境挑战,推动水泥行业的可持续发展。
水泥厂工艺流程以及生产设备

水泥厂生产流程及设备原理简介
水泥的生产工艺简单讲便是两磨一烧,即原料要经过采掘、破碎、磨细和混匀制成生料,生料经1450~C的高温烧成熟料,熟料再经破碎,与石膏或其他混合材一起磨细成为水泥。
由于生料制备有干湿之别,所以将生产方法分为湿
法,半干法或半湿法和干法3种。
水泥生产的基本流程,以干法生产为例包括以下几个主要工序:原料开采一破碎一烘干一配料一粉磨一生料贮存一均化一煅烧一熟料冷却及破碎一配料(加石膏和混合材)一粉磨一水泥贮存一装运。
湿法生产的区别在煅烧以前的生料制备过程上,主要工序为:半干法生产的区别仅在出生料磨以后和入窑煅烧之前的一段,即:
粉磨一生料贮存均化一加水成球一煅烧。
新型干法生产则在各贮存环节上都加强了均化,具体为:原料开采一破碎一预均化一配料一粉磨并烘干一生料粉贮存均化一煅烧一熟料冷却破碎一熟料贮存均化一配料一粉磨一水泥贮存均化一装运(或混配搅拌
一装运)
此外,用煤做燃料时也要经过贮存均化,破碎(或烘干),粉磨制成煤粉再人窑。
混合材则视品种而定,如粒化高炉矿渣要经过烘干,煤矸石要预先破碎,石膏也需预先破碎。
混合材和石膏通常都与熟料一起粉磨,近年来对粒化高炉矿渣趋向于单独粉磨,因为矿渣比熟料难磨,如与熟料一起粉磨难以磨细,不能充分
发挥矿渣的作用。
1,矿山开采→破碎系统→预均化堆场→配料系统→生料制备系统(生料制备)
2,生料→预热分解系统→回转窑煅烧→篦冷机冷却→熟料库煤磨煤粉制备系统→(熟料煅烧)
3,熟料→水泥粉磨→包装系统→出厂(水泥粉磨)
再简化后(即“两磨一烧”)
生料制备→熟料煅烧→水泥粉磨。