自卸车通用检验规范
自卸车通用检验标准
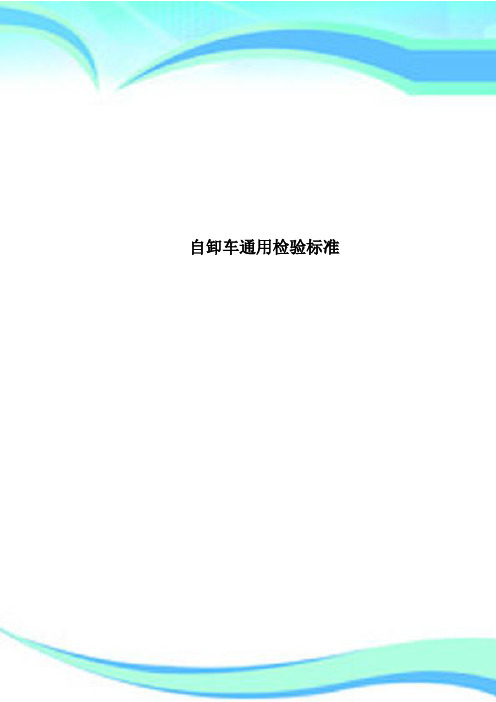
自卸车通用检验标准————————————————————————————————作者:————————————————————————————————日期:文件编号:受控状态发放号自卸车通用制造检验规范编制:审核:批准:2006年月日发布2006年月日实施前言自卸车通用制造检验规范1 范围本标准规定了自卸车的技术要求、制造检验规范,试验方法。
本标准适用于本公司生产的各种型号自卸车(上装)的制造及最终检验。
2 规范性引用文件下列文件中的条款通过本规范的引用而成为本规范的条款。
凡是注日期的引用文件,其随后所有的修改单(不包括勘误的内容)或修订版均不适用于本规范,然而,鼓励根据本规范达成协议的各方研究是否可使用这些文件的最新版本。
凡是不注日期的引用文件,其最新版本适用于本规范。
GB7258-2004 机动车运行安全技术条件GB1589-2004 道路车辆外廓尺寸、轴荷及质量限值GB/T 3766 液压系统通用技术条件QC/T 223-1997 自卸车性能试验方法QC/T 252-1998 专用汽车定型试验规程QC/T 319-1999 自卸汽车取力器技术条件QC/T 460-1999 自卸汽车液压缸技术条件QC/T 460-1999 自卸汽车栏板锁紧装置技术条件3 技术要求及检验规范3.1 整车要求3.1.1 自卸汽车整车必须符合本规范要求,并按照规定程序批准的图样及技术文件制造。
3.1.2 自卸汽车外廓尺寸应符合GB1589-2004《道路车辆外廓尺寸、轴荷及质量限值》的规定,货箱内部尺寸等必须符合产品公告和图纸要求。
3.1.3 自卸汽车上装按质心,轴荷设计要求计算,严格按图纸及公告尺寸施工。
3.1.4 照明及信号系统应符合GB4785-1998《汽车及挂车外部照明和信号装置的安装规定》的要求。
a)自卸车应安装两只红色后示廓灯,安装在后立柱上部;b)自卸车应安装两只红色前示廓灯,安装在前立柱上部;c)自卸车应安装侧标志灯和侧回复反射器,琥珀色,安装位置高度距地面不得小于900,不得大于1500,最好是车架边纵梁处,整车纵向位置是距前部小于3000,距后部小于900,两灯中间位置相距小于3000,最大不能超过3500;d)后转向灯、后位灯离地高度不得小于900,大于1200,后位灯距外廓侧面不得小于400;e)车辆后部必须安装一只红色后雾灯,不能与后位灯干涉,二者相距至少200;f)车辆后部必须安装后回复反射器,三角形红色2只,安装在保险杠上或后尾板上,距车辆左右侧不得小于400,并且对称安装。
自卸车出厂检验规范

自卸车出厂检验规范
摘自QC/T222-2010
自卸汽车通用技术条件附录B
试验条件:自卸汽车在空载状态下,停止在平坦、硬实场地上
外观
1.外廓尺寸符合图纸规定
2.焊缝应无裂缝、焊坑、焊穿、焊渣、漏焊等现象
3.所有外露的黑色金属件应采取防腐防锈处理,油漆色泽鲜艳,无皱皮、污痕
4.所有管路排列平直、整齐,所有零件装配位置正确
5.将上述情况目测记录
性能要求
1.车厢最大举升角 QC/T223-2010(4.3.2)
在倾卸方向两侧栏板的外侧各安装一个角度仪并调整到0°,然后将车箱举升到最大角,分别观察角度仪上的指示值并记录。
2.车厢举升时间 QC/T223-2010(4.
3.3)
液压泵在额定转速下,用秒表(精确到0.1s)测量空载车厢从与车架贴合位置举升到最大举升角的时间。
根据倾卸方向各进行3次。
3.车厢下降时间 QC/T223-2010(
4.3.4)
用秒表(精确到0.1s)测量车厢从最大举升角度下降到车架贴合位置所需的时间。
按倾卸方向,各进行3次。
4.制动性能
空载初速度30km/h时,制动距离不大于9m,车辆任何部位不得超过试车道3m。
委托外测机构
1.噪声测定 GB1495-1979 机动车辆允许噪声
2.有害气体排放测定
详细参照QC/T223-2010 自卸车性能试验方法。
自卸车整车装配检验规范-ok
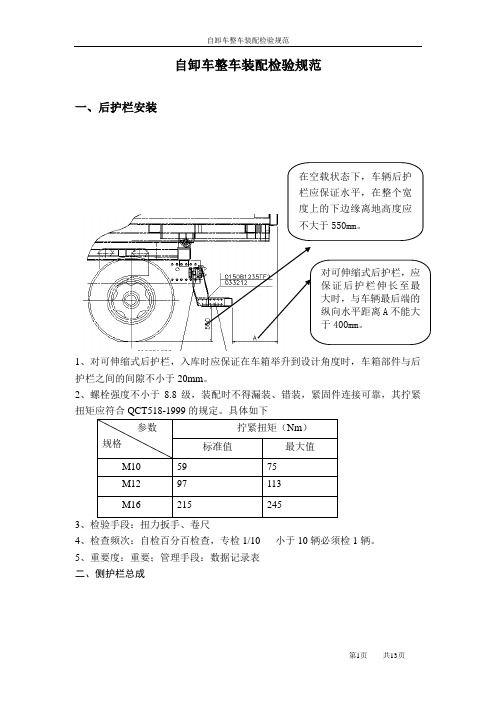
自卸车整车装配检验规范一、后护栏安装1、对可伸缩式后护栏,入库时应保证在车箱举升到设计角度时,车箱部件与后护栏之间的间隙不小于20mm 。
2、螺栓强度不小于8.8级,装配时不得漏装、错装,紧固件连接可靠,其拧紧扭矩应符合QCT518-1999的规定。
具体如下参数 规格 拧紧扭矩(Nm )标准值最大值M10 59 75 M12 97 113 M162152453、检验手段:扭力扳手、卷尺4、检查频次:自检百分百检查,专检1/10 小于10辆必须检1辆。
5、重要度:重要;管理手段:数据记录表 二、侧护栏总成在空载状态下,车辆后护栏应保证水平,在整个宽度上的下边缘离地高度应不大于550mm 。
对可伸缩式后护栏,应保证后护栏伸长至最大时,与车辆最后端的纵向水平距离A 不能大于400mm 。
1、护装置固定地安装在副车架上时,所有连接件应与底盘车辆上的各种设施,如备胎、蓄电池架、储气筒、燃油箱、灯具、工具箱、液化气罐等保留至少10mm 间隙。
2、支架分为支架总成、带撑杆的支架总成、缩短的支架总成(如图),其中带撑杆的支架下端撑杆L 型板必须与主车架贴紧,并有预紧的2mm 余量。
3、前、后支架总成时,距横杆前、后边缘的距离原则上为200mm ,如受空间所限(如与空气滤清器、电瓶、车箱限位、主副车架连接座、侧置备胎、副车架外侧工艺孔等位置发生重叠),允许布置情况在100mm 范围内调整。
4、强度不小于8.8级,装配时不得漏装、错装,紧固件连接可靠,其拧紧扭矩应符合QCT518-1999的规定。
具体如下参数 规格 拧紧扭矩(Nm )标准值最大值M8 23 26 M12971135、检验手段:扭力扳手、卷尺6、检查频次:自检百分百检查,专检1/10 小于10辆必须检1辆。
7、重要度:重要;管理手段:数据记录表 三、备胎升降系统总成通用技术要求1、部件安装、焊接牢固可靠,备胎安装后,必须锁紧固定支架。
2、装侧置备胎时,备胎与主传动轴及周边相关部件的间距不小于50mm 。
自卸车检验指导书

1.生产过程检验1.1副车架总成检验规范1.1.1.检验项目及标准1.1.1.1车架长度公差±5mm,宽度公差负1-3毫米。
用钢卷尺测量。
1.1.1.2车架下平面平面度≤4mm。
1.1.1.3两纵梁直线度任意5米内≤4mm。
5-7米≤6mm。
7米以上≤8mm。
1.1.1.4翻转轴孔中心相对于纵梁底平面误差≤1mm。
1.1.1.5翻转轴孔轴向与总量垂直度≤1度。
1.1.1.6翻转轴套两端相对于两纵梁中心线对称度≤2mm。
1.1.1.7油缸支座中心与两纵梁中心左右偏差不大于2mm。
1.1.1.8油缸支座至后翻转轴套两端距离差不大于5mm。
1.1.1.9底架对角线差≤5mm。
1.1.1.10外观要求:平整;清洁;无焊丝头、氧化铁;无扭曲变形、锤痕、凹陷等外观缺陷。
焊缝应美观,洁净不得有焊瘤、咬边、气孔、夹渣、假焊、偏焊、漏焊,焊缝标准应达到厂标二级以上标准。
1.1.2.对以上检验项目的说明1.1.2.1以上检验项目由生产班组先进行自检,然后由检验员进行专检。
1.1.2.2以上检验项目的检查必须采用全检的方法.有一项不合格就不能进行下道工序。
1.1.2.3检验员必须做到认真检验,严格要求,并做好检验记录。
1.1.2.4以上检验项目用250×500mm直角弯尺;5米、20米钢卷尺。
1.2底架总成检验规范1.2.1.检验项目及标准1.2.1.1板材厚度符合国家GB/T1222-1989规定标准。
底架总长度±5mm,底板宽度±3mm。
两纵梁宽度公差负2-4mm。
1.2.1.2两纵梁纵向中心与底板纵向中心错移量≤3mm。
1.2.1.3底架总体6米以内平面度≤3mm。
6米以上平面度≤5mm。
1.2.1.4焊后变形允许有一定上拱,上拱高度≤2mm。
不允许下塌。
1.2.1.5两纵梁下端平面到底板两侧距离差≤5mm。
1.2.1.6底架对角线差≤5mm。
1.2.1.7主托架工作面距纵梁下表面距离±1mm。
_《金属非金属露天矿山在用矿用自卸汽车安全检验规范》(AQ2027-)
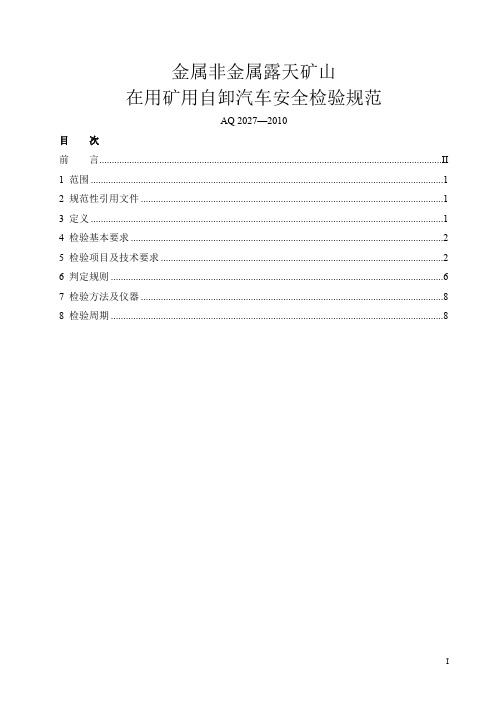
金属非金属露天矿山在用矿用自卸汽车安全检验规范AQ 2027—2010目次前言 (II)1 范围 (1)2 规范性引用文件 (1)3 定义 (1)4 检验基本要求 (2)5 检验项目及技术要求 (2)6 判定规则 (6)7 检验方法及仪器 (8)8 检验周期 (8)前言本标准为强制性标准。
本标准由国家安全生产监督管理总局提出。
本标准由全国安全生产标准化技术委员会非煤矿山安全分技术委员会归口。
本标准负责起草单位:国家安全生产长沙矿山机电检测检验中心。
本标准主要起草人:贺建国、翟守忠、李春娟、骆拓、袁乐安、龚文、周建、邓宇、周振华、王四现、季光洲、罗振兴。
本标准为首次发布。
金属非金属露天矿山在用矿用自卸汽车安全检验规范1 范围本标准规定了金属非金属露天矿山在用矿用自卸汽车安全检验的项目、技术要求、检验方法、判定规则和检验周期。
本标准适用于金属非金属露天矿山在用矿用自卸汽车现场检验。
2 规范性引用文件下列文件中的条款通过本标准的引用而成为本标准的条款。
凡是注日期的引用文件,其随后所有的修改单(不包括勘误的内容)或修订版均不适用于本标准,然而,鼓励根据本标准达成协议的各方研究是否可使用这些文件的最新版本。
凡是不注日期的引用文件,其最新版本适用于本标准。
GB 7258—2004 机动车运行安全技术条件GB 16423—2006 金属非金属矿山安全规程3 术语和定义下列术语和定义适用于本标准。
3.1 金属非金属露天矿山metal and nonmetal opencast mines在地表开挖区通过剥离围岩、表土或砾石,采出供建筑业、工业或加工业用的金属或非金属矿物的采矿场及其附属设施。
3.2 矿用自卸汽车mining dump trucks矿山用载重10 t 以上,以柴油机为动力的自卸汽车,包括电传动矿用自卸汽车。
3.3 最小转弯直径minimum turning diameter汽车前轮处于最大转角状态行驶时,车体离转向中心最远点形成的轨迹圆直径。
自卸汽车通用技术条件
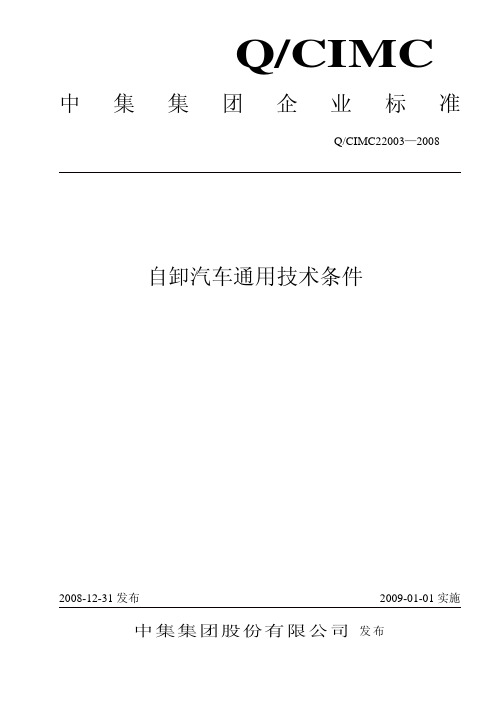
Q/CIMC 中集集团企业标准Q/CIMC22003—2008自卸汽车通用技术条件2008-12-31发布 2009-01-01实施中集集团股份有限公司发布目次前言 (II)1 范围 (3)2 规范性引用文档 (3)3 技术要求 (4)4 检验规则 (6)5 标志、使用说明书 (6)6 随车文件、运输和储存 (7)7 质量保证 (7)8 附录A (8)前言本标准是规范集团内各企业生产的自卸车的依据、标准。
修订本标准的依据是GB1589-2004《道路车辆外廓尺寸 轴荷及质量限值》、GB7258-2004《机动车运行安全技术条件》,QC/T222《自卸汽车通用技术条件》。
本标准由集团技术管理部提出。
本标准由集团技术管理部归口。
本标准由中集车辆(集团)有限公司起草。
本标准主要起草人: 朱爱平、徐国红、胡志鹏。
自卸汽车通用技术条件1 范围本标准依据国家相关标准,规定了中集集团股份有限公司生产的各类自卸汽车的要求、检验规则及标志、使用说明书、随车文件、运输、贮存及质量保证。
本标准适应于定型自卸汽车底盘、允许最大总质量小于31t、以液压倾卸的自卸汽车(包括后卸自卸汽车、侧卸自卸汽车)。
本标准不适用于三轮自卸车和矿用自卸汽车和半挂自卸汽车。
2 规范性引用文档下列标准所包含的条款,通过在本标准中引用而构成本标准的条款。
凡是不注日期的引用文件,其最新版本适用于本标准。
凡是注日期的引用文件,其随后所有的修改单或修订版本不适用于本标准。
标准都会被修订,使用本标准的各方应探讨使用下列标准最新版本的可能性。
GB1495 汽车加速行驶车外噪声限值及测量方法GB1589 道路车辆外廓尺寸、轴荷及质量限值GB/T 3181 漆膜颜色标准GB3766 液压系统通用技术条件GB/T3847 车用压燃式发动机和压燃式发动机汽车排气烟度排放限值及测量方法GB4094 汽车操纵件、指示器及信号装置的标志GB4785 汽车及挂车外部照明和信号装置的安装规定GB7258 机动车运行安全技术条件GB9969.1 工业产品使用说明书 总则GB11567.1 汽车和挂车侧面防护要求GB11567.2 汽车和挂车后下部防护要求GB15741 汽车和挂车号牌板(架)及其位置GB16737 道路车辆 世界制造厂识别代号(WMI)GB16735 道路车辆 车辆识别代号(VIN)GB17509 汽车和挂车转向信号灯配光性能GB/T18411 道路车辆 产品标牌GA406 车身反光标识JB/T5943 工程机械 焊接件通用技术条件QC /T222 自卸汽车通用技术条件QC/T252 专用汽车定型试验规程QC/T319 自卸汽车取力器技术条件QC/T460 自卸汽车液压缸技术条件QC/T461 自卸汽车-换向阀技术条件QC/T 484 汽车油漆涂层QC/T29015 自卸汽车栏板锁紧装置技术条件QC/T29104 专用汽车液压系统液压油固体污染度限值3 技术要求3.1 整车3.1.1 自卸汽车应符合本标准规定,并按经规定程序审核批准的产品图样和技术文件制造。
煤矿自卸汽车检测标准

煤矿自卸汽车检测标准一、外观检测1.车辆外观应整洁,无严重磨损、锈蚀、凹陷、变形等情况。
2.车身各部件(包括车灯、后视镜、门锁、车门气动杆等)应完整,无损坏。
3.车辆标识(包括车牌、车辆识别码、安全警示标志等)应清晰、完整。
二、尺寸检测1.车辆的长、宽、高应符合设计要求,允许偏差不超过±5%。
2.车辆的轴距、轮距应符合设计要求,允许偏差不超过±3%。
3.车辆的整备质量、满载质量应符合设计要求,允许偏差不超过±5%。
三、重量检测1.车辆的总重量应符合设计要求,允许偏差不超过±5%。
2.车辆的轴荷分布应符合设计要求,允许偏差不超过±3%。
四、载重检测1.车辆的最大载重应符合设计要求,允许偏差不超过±5%。
2.车辆的额定载重应符合设计要求,允许偏差不超过±3%。
3.车辆在额定载重下的行驶性能应稳定,无跑偏、飘逸等现象。
五、性能检测1.车辆的动力性能应符合设计要求,发动机功率、扭矩应达到额定值,加速性能良好。
2.车辆的制动性能应符合设计要求,制动距离、制动效能稳定可靠。
3.车辆的操控性能应符合设计要求,转向灵敏、稳定,无跑偏、振荡等现象。
4.车辆的通过性能应符合设计要求,对不同地形、路况的适应能力强。
5.车辆的燃油经济性能应符合设计要求,百公里油耗应达到较低水平。
六、安全性检测1.车辆的安全设施(如刹车防抱死系统、防滑系统、安全带、应急逃生门等)应工作正常,无故障。
2.车辆的稳定性应良好,在满载及复杂路况下应能保持稳定行驶。
3.车辆的灯光系统(包括前照灯、后尾灯、转向灯等)应工作正常,无故障。
4.车辆的安全警示标志(如危险品标志、放大号牌等)应清晰可见。
七、可靠性检测1.车辆的主要部件(如发动机、变速箱、车桥等)应工作正常,无异响、无泄漏。
2.车辆的电气系统(包括电源、用电设备等)应工作稳定,无故障。
3.车辆的液压系统(如液压倾卸机构)应工作稳定,无泄漏。
自卸车检验作业指导书1

自卸车检验作业指导书检验项目图片检验标准检验方法副车架总成检验车架长度公差±5mm,宽度公差负1-3mm 钢卷尺车架下平面平面度≤4mm 直角尺两纵梁直线度任意5M内≤4mm,5-7M≤6mm,7M以上≤8mm钢卷尺翻转轴孔中心相对于纵梁底平面误差≤1mm 钢卷尺翻转轴孔轴向与纵梁垂直度≤1度直角尺翻转轴套两端相对于两纵梁中心线对称度≤2mm 钢卷尺油缸支座中心与两纵梁中心摆布偏差≤2mm 钢卷尺油缸支座至后翻转轴套两短距离差≤5mm 钢卷尺底架对角线误差≤5mm 钢卷尺外观平整;清洁;无焊丝头、氧化铁;无扭曲变形、锤痕、凹陷等外观缺陷。
焊缝美观,不得有焊瘤、咬边、气孔、夹渣、假焊、偏焊、漏焊等,焊缝标准应达到相关标准。
目测编制校对标准化审核批准检验项目图片检验标准检验方法底架总成检验板材厚度符合国家GB/T1222-1989规定标准。
底架总长度±5mm,底板宽度±3mm,两纵梁宽度公差负2-4mm。
钢卷尺两纵梁纵向中心与底板纵向中心错移量≤3mm。
钢卷尺底架总体6米以内平面度≤3mm,6米以上平面度≤5mm。
钢卷尺焊后变形上拱高度≤2mm,不允许有下塌。
钢卷尺两纵梁下端平面到底板两侧距离差≤5mm。
钢卷尺底架对角线差≤5mm。
钢卷尺主托架工作面距纵梁下表面距离±1mm。
钢卷尺主托架中心道后翼梁距离±3mm。
钢卷尺主托架与纵梁焊接坚固、可靠。
目测底架纵梁、底架横梁与底板焊接角高度8mm、为100mm断续焊,其他部位焊角高6mm、全方位焊接。
钢卷尺、目测底架尾部横梁外侧打印字码,标记生产编号目测编制校对标准化审核批准检验项目图片检验标准检验方法底架总成检验外观平整;清洁;无焊丝头、氧化铁;无扭曲变形、锤痕、凹陷等外观缺陷。
焊缝美观,不得有焊瘤、咬边、气孔、夹渣、假焊、偏焊、漏焊等,焊缝标准应达到相关标准。
目测编制校对标准化审核批准检验项目图片检验标准检验方法货箱检验厢板宽(长)度方向误差允许负0-3mm,高度方向允许误差±3mm,板材厚度符合国家GB/T1222-1989规定标准。
- 1、下载文档前请自行甄别文档内容的完整性,平台不提供额外的编辑、内容补充、找答案等附加服务。
- 2、"仅部分预览"的文档,不可在线预览部分如存在完整性等问题,可反馈申请退款(可完整预览的文档不适用该条件!)。
- 3、如文档侵犯您的权益,请联系客服反馈,我们会尽快为您处理(人工客服工作时间:9:00-18:30)。
可编辑自卸车通用制造检验规范编制:审核:批准:前言自卸车通用制造检验规范1 范围本标准规定了自卸车的技术要求、制造检验规范,试验方法。
本标准适用于本公司生产的各种型号自卸车(上装)的制造及最终检验。
2 规范性引用文件下列文件中的条款通过本规范的引用而成为本规范的条款。
凡是注日期的引用文件,其随后所有的修改单(不包括勘误的内容)或修订版均不适用于本规范,然而,鼓励根据本规范达成协议的各方研究是否可使用这些文件的最新版本。
凡是不注日期的引用文件,其最新版本适用于本规范。
GB7258-2004 机动车运行安全技术条件GB1589-2004 道路车辆外廓尺寸、轴荷及质量限值GB/T 3766 液压系统通用技术条件QC/T 223-1997 自卸车性能试验方法QC/T 252-1998 专用汽车定型试验规程QC/T 319-1999 自卸汽车取力器技术条件QC/T 460-1999 自卸汽车液压缸技术条件QC/T 460-1999 自卸汽车栏板锁紧装置技术条件3 技术要求及检验规范3.1 整车要求3.1.1 自卸汽车整车必须符合本规范要求,并按照规定程序批准的图样及技术文件制造。
3.1.2 自卸汽车外廓尺寸应符合GB1589-2004《道路车辆外廓尺寸、轴荷及质量限值》的规定,货箱内部尺寸等必须符合产品公告和图纸要求。
3.1.3 自卸汽车上装按质心,轴荷设计要求计算,严格按图纸及公告尺寸施工。
3.1.4 照明及信号系统应符合GB4785-1998《汽车及挂车外部照明和信号装置的安装规定》的要求。
a)自卸车应安装两只红色后示廓灯,安装在后立柱上部;b)自卸车应安装两只红色前示廓灯,安装在前立柱上部;c)自卸车应安装侧标志灯和侧回复反射器,琥珀色,安装位置高度距地面不得小于900,不得大于1500,最好是车架边纵梁处,整车纵向位置是距前部小于3000,距后部小于900,两灯中间位置相距小于3000,最大不能超过3500;d)后转向灯、后位灯离地高度不得小于900,大于1200,后位灯距外廓侧面不得小于400;e)车辆后部必须安装一只红色后雾灯,不能与后位灯干涉,二者相距至少200;f)车辆后部必须安装后回复反射器,三角形红色2只,安装在保险杠上或后尾板上,距车辆左右侧不得小于400,并且对称安装。
3.1.5 焊接件应按JB/ZQ3011-1983《工程机械焊接通用技术条件》的规定施焊。
焊缝均匀、光滑,焊接要牢固、可靠,不得有裂纹、夹渣、焊穿、漏焊现象,咬肉处每米不得多于3处。
3.1.6 油漆涂层应符合JB/Z111-1986《汽车油漆涂层》的规定,油膜应能自然干燥。
3.1.7 自卸车外观质量3.1.7.1 自卸车外观不应有图样未规定的凸起、凹陷和其它损伤。
各栏板,车架,侧防护栏、后防护杠应平整、匀称,无翘曲变形。
3.1.7.2 零部件外露结合面的边缘应整齐、均匀,不应有明显的错位,其错位量不得超过规定值。
3.1.7.3 刹车管路和电器管路应布置紧凑,排列整齐、美观,应该用管卡固定牢靠。
3.1.7.4 自卸车各连接部分的零件不应有损坏,永久变形等现象,各部连接销轴要可靠且转动自如,所有螺栓联结都要采用防松措施,被紧固件为薄板件时还要加平垫圈。
3.1.7.5 所有外露黑色金属表面均应作防锈处理。
外表面装饰漆应美观大方,色泽鲜明,分界整齐,无漏喷、流挂、起皱、起泡、针孔、脱漆、发花、反粘、颗粒、夹杂、倒光等缺陷,漆膜附着牢固,坚硬,光滑平整、厚薄均匀,干净无尘。
漆膜下不允许出现红丝和透过漆膜的锈斑。
相互接触的非配合装配面在装饰前要喷防锈漆,由于加工或焊接损坏的底漆要重新涂装。
3.1.8 自卸车应设置防护装置,侧后防护装置的尺寸,强度及安装位置应符合GB11567.1-2001《汽车和挂车侧面防护要求》和GB11567.2-2001《汽车和挂车后下部防护要求》的要求。
3.1.8.1 侧面防护装置要求。
a)自卸车左右侧必须安装横杆结构的侧面防护装置;b)侧面防护装置不应增加车辆的总宽,外表面的主要部分位于车辆最外侧以内不大于120mm的位置,装置后端有300mm位于后轮胎最外侧以内不大于30mm的位置。
c)侧面防护装置外表面应光滑且连续,尽量采用横杆结构,横杆间距不大于300mm,横杆截面高度不小于100mm,最好为δ3×100×40的折槽。
d)后缘与最靠近它的轮胎外圆距离小于300mm。
e)侧面防护装置的下缘最大离地高度为550mm,全长方向上不得有凸出超过5mm的物体。
f)上缘距车辆上部构件的距离,即距车架边纵梁的距离不得大于350mm,且离地高不得小于950mm。
g)侧面防护装置前缘要光滑倒圆,圆角半径大于5mm。
3.1.8.2 后下部防护装置要求a)后防装置下边缘的离地高度应不大于550mm;b)后防装置的宽度不得大于车辆后轴两侧车轮最外点的距离,且任一端最外边缘与这一侧车辆后轴车轮最外端的水平横向距离不大于100mm,后防装置宽度一般应为2320mm;c)后防装置截面一般应为矩形管140×100×8,但也可为[14槽钢。
3.1.9 自卸车应至少设置一个备胎和相应的备胎架,尽量满足用户要求。
3.2 副车架3.2.1 副车架主纵梁a)副车架主纵梁材质必须符合图纸要求,保证主纵梁拼焊后的尺寸;b)副车架主纵梁拼焊后需要矫查,校查方法和要求见下表:校正按以下内容进行:1)目视或拉线确定变形部位2)根据变形大小确定加热区域,作标记线3)采用火焰校正,水冷法4)加热温度不超过650℃5)加热温度与颜色见下表钢材表面颜色及相关温度6)加热法如图示7)检查主纵梁在全长范围内直线度在高度方向上小于2mm,且只允许上凸,宽度方向小于2.5mm,全长内小于5mm。
3.2.2 副车架组装3.2.2.1 副车架的组装有车架组焊平台,完成各横梁,纵梁、边梁的组对和后翻转铰链的组装。
保证的关键尺寸为:后翻转铰链相对车架中心线垂直度2mm。
3.2.2.2 副车架在制作过程中保证总长度不大于8000mm范围内,其长度极限偏差为±5mm,长度每增加1000mm时,(不足1000mm的,按1000mm计算),长度极限偏差增加1mm。
宽度极限偏差增加±4mm。
3.2.2.3 副车架在制作过程中保证,车架纵梁上平面在长度不大于5000mm范围内,其平面度公差为5mm,长度每增加1000mm时,(不足1000mm的,按1000mm计算),其平面度公差增加1mm。
3.2.2.4 副车架对角线长度差不大于10mm。
3.2.2.5 副车架只允许冷校正。
3.3 车厢3.3.1 对厢式或有栏板的自卸车,车门及栏板闭锁装置应设置在离地面高度不超过1900mm的位置。
3.3.2 车厢底板对角线长度差不大于10mm。
3.3.3 所有栏板与底板间隙不大于4mm,各栏板、立柱之间间隙不大于5mm。
3.3.4 各栏板对角线长度公差不大于5mm。
3.4 液压系统安装3.4.1 安技术图样要求安装液压举升机构。
3.4.2 车厢完全下降后,油缸的缸杆伸出长度应在15-50mm之间。
3.4.3 油缸的上下支架与油缸之间的最大距离不大于2mm,必须使用M16的细螺纹螺栓连接,且螺栓的精度等级不小于Q8.8级,扭紧力矩力矩210Nn。
3.4.4 所有液压软管必须妥善保管以防刮伤和磨损。
3.4.5 正确安装油泵,油泵与传动轴及底盘之间的间隙大于5mm,传动轴夹角小于5度。
4 电气4.1 发电机在运转期间,不允许松开、取下或置换交流发电机的电线和蓄电池连接线。
4.2 蓄电池充电时要与汽车的电气设备断开。
4.3 汽车搭铁连接有变动时,必须重新形成完全有效的接地。
4.4 电线因更改被切断时,必须使用防水连接件。
4.5 更改导线位置时必须套上绝缘胶皮,并用夹子牢固的固定在车架上。
4.6 在汽车上电焊时,为避免对交流发电机调节器造成损害,必须拆除蓄电池连接线,并将电缆捆在一起。
4.7 电气元件在装配前一定要进行严格检查或实验筛选,合格者进行装配。
4.8 按装配图布线连接,不得随意更改。
4.9 导线的载流量和颜色必须符合设计规定。
4.10 装配按钮和指示灯严格按设计的颜色。
4.11 所有导线的绝缘层必须完好无损,导线剥头处的细铜丝必须拧紧,需要时应搪锡。
4.12 焊点必须牢固,不得有脱焊和虚焊现象。
焊点应光滑、均匀。
4.13 电线必须拉直,多余的折叠后用卡子卡住。
4.14 电气系统装配后,应按设计规定的电压和电流范围进行试运行检查。
4.15 在试运行开始前,所有选择的开关都应置于开始位置。
试运行过程中应检查各开关、按钮、旋钮是否灵活可靠,各个灯是否亮。
4.16 如需直接从底盘电路中连接电源,应校核底盘采用的发动机功率。
4.17 需延长或减短线束时,应将整根线束更换,如需增加线束,线束应采用同原车型号、颜色相同的导线,通过连接件或接线柱连接。
4.18 电路不能打褶,多余的线用卡子卡住。
5 改主车5.1 底盘尼龙管5.1.1 在塑料管和尼龙管附近进行焊接、钻孔磨削等工作时,应采取防护措施,将其拆下或覆盖。
5.1.2 制动装置更改,管路连接件和软管等需符合设计要求,和底盘厂家要求。
5.1.3 安装尼龙管时不要与车架的刃边、撑杆、螺栓头和支架等接触。
若不可避免,则需利用保护管子装置。
5.1.4 安装尼龙管不要过分的拉伸和压缩。
5.1.5 若尼龙管与其他部件平面接触,应将其固定以防止管子抖动或擦伤。
尼龙管架的间距不超过600mm。
5.1.6 应保证尼龙管与排气管等发热部件有足够的间隙,以避免尼龙管损坏,若不能保证,应设置绝缘和隔热挡板。
5.1.7 尼龙管不允许接触有害液体,尼龙管不要涂漆。
5.1.8 进行蒸汽冲洗、防锈处理或红外线烘烤油漆等工作时,保护尼龙管不受热损害。
5.1.9 应使用摺边的或有橡胶涂层的夹子来固定尼龙管。
5.1.10 尼龙管不能与钢管夹在一起。
5.1.11 尼龙管的使用温度在-40°—90°。
5.2 主车车架及其他5.2.1 尽量借用主车大梁上的各孔,尽量避免在主车大梁上采用气割、气焊工艺,特殊情况除外。
5.2.2 对车架高度应力区以外钻孔时尽量满足下表:5.2.3 在大梁翼面高应力区外的其他部位钻孔时,只能在中心处钻一个孔。
5.2.4 在纵梁的边角区禁止钻孔,图示部位禁止钻孔:5.2.5 腹板上的新钻孔必须远离原有的孔位和焊缝,否则腹板可能出现裂纹。
5.2.6 禁止采用粗糙的钻孔,禁止气割割孔。
5.2.7 车架无法避免采用气焊切割,则在气割后再修磨,以消除割痕,做到表面平整无缺。
5.2.8 尽量避免装置件在紧固前先临时点焊在车架上,点焊处往往诱发裂纹,出现早期损坏。