昆明理工大学机电系统设计模块PLC实验报告
电动机PLC实验报告

实验报告班级:机械一班学号:姓名:日期: 4.17实验二、电动机PLC实验一、实验目的1.熟悉S7-200PLC的逻辑指令2.根据已有的控制线路,改变成PLC程序3.进一步掌握编程软件的使用方法和调试方法二、实验设备1.装有V4.0 STEP 7 MicroWIN SP3的PC机一台2.装有模拟软件S7_200三、控制要求分析正转:当按下正转开关SF2,降压启动,当速度V达到一定,速度继电器BS1闭合,电阻短接,电动机稳定工作,按下停车按钮SF1,反接制动,V下降,一定时,速度继电器断开,KF1断电,QA2释放,反接制动过程结束。
反转:反转开关SF3闭合,V上升,速度达到一定时,速度继电器BS2导通,然后稳定运行,当按下SF1停车按钮,反接制动,当V下降到一定时,速度继电器断开,反接制动过程结束。
四、PLC的I/O分析紧急停车:I0.0停车:I0.1正转:I0.2反转:I0.3KFI:M0.1KF2:M0.2KF3: M0.3KF4:M0.4QA1:Q0.1QA2:Q0.2QA3:Q0.3五、PLC梯形图程序及指令表程序语句表:LDN I0.0 AN I0.1 LD I0.2 O M0.3 ALDAN I0.3 AN M0.4 = M0.3 Network 2 LDN I0.0 LDN I0.1 A M0.3 O M0.2 ALDAN Q0.2 = Q0.1 Network 3 LDN I0.0 AN I0.1 LD M0.4 O I0.3 ALDAN I0.2 AN M0.3= M0.4 Network 4 LDN I0.0 LDN I0.1 A M0.4 O M0.1 ALDAN Q0.1 = Q0.2 Network 5 LDN I0.0 A I0.4 LD Q0.1 O M0.1 ALD= M0.1 Network 6 LDN I0.0 A I0.5 LD Q0.2 O M0.2 ALD= M0.2 Network 7 LDN I0.0 LD M0.1 A M0.3 LD M0.2 A M0.4 OLDALD= Q0.3六、电气原理图七、实验过程记录及分析1.根据已有的控制电路,改成PLC梯形图2.输入PC机进行调试3.直到获得所需结果八、时序分析正转:I0.2:正转Q0.1:降压启动I0.4:速度继电器Q0.3:电阻短接,稳定运行I0.1:停车Q0.2:反接制动反转:I0.3:反转启动Q0.2:降压启动I0.5:速度继电器Q0.3:电阻短接,稳定运行I0.1:停车Q0.1:反接制动九、实验心得和体会经过这次试验,学会了如何将一个已有的控制电路,改成PLC梯形图语言,同时也了解了具有反接制动电阻的电动机得正反转启动停止的控制过程,对试验软件的调试过程有进一步的了解。
plc实习报告范文6篇
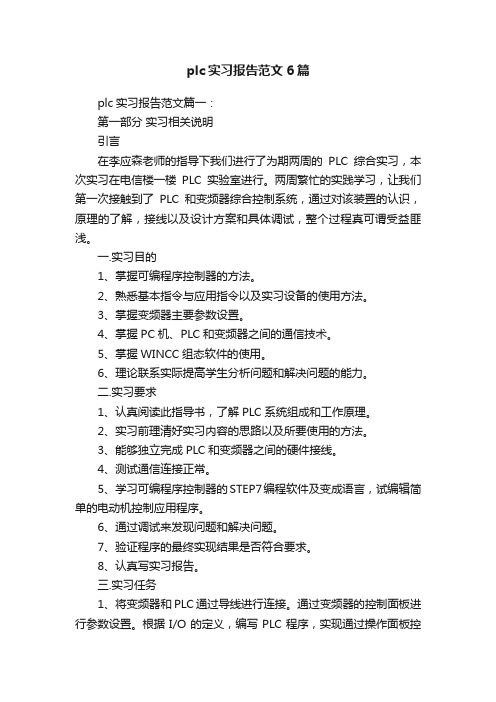
plc实习报告范文6篇plc实习报告范文篇一:第一部分实习相关说明引言在李应森老师的指导下我们进行了为期两周的PLC综合实习,本次实习在电信楼一楼PLC实验室进行。
两周繁忙的实践学习,让我们第一次接触到了PLC和变频器综合控制系统,通过对该装置的认识,原理的了解,接线以及设计方案和具体调试,整个过程真可谓受益匪浅。
一.实习目的1、掌握可编程序控制器的方法。
2、熟悉基本指令与应用指令以及实习设备的使用方法。
3、掌握变频器主要参数设置。
4、掌握PC机、PLC和变频器之间的通信技术。
5、掌握WINCC组态软件的使用。
6、理论联系实际提高学生分析问题和解决问题的能力。
二.实习要求1、认真阅读此指导书,了解PLC系统组成和工作原理。
2、实习前理清好实习内容的思路以及所要使用的方法。
3、能够独立完成PLC和变频器之间的硬件接线。
4、测试通信连接正常。
5、学习可编程序控制器的STEP7编程软件及变成语言,试编辑简单的电动机控制应用程序。
6、通过调试来发现问题和解决问题。
7、验证程序的最终实现结果是否符合要求。
8、认真写实习报告。
三.实习任务1、将变频器和PLC通过导线进行连接。
通过变频器的控制面板进行参数设置。
根据I/O的定义,编写PLC程序,实现通过操作面板控制交流异步电动机起动,停止,正反转切换,并监视电动机的故障和运行状态。
2、做WINCC画面,将WINCC与PLC相连,实现在WINCC上对变频器的监控。
除了控制电动机起动,停止,正反转切换,监视电动机的故障和运行状态外,还要在WINCC画面上进行频率给定以及对实际频率的监视。
四.实习方法1、通信方式有两种:(1)通过MPI通信实现。
(2)通过Profibus-DP实现。
2、控制方式有两种:(1)本地的操作面板控制。
(2)远程的Wincc画面监控。
五.实习地点校内PLC实习基地,即在电信学院一楼PLC实验室。
六.安全注意事项1、电动机很危险,注意在电动机运行期间要远离电动机。
plc实验报告总结
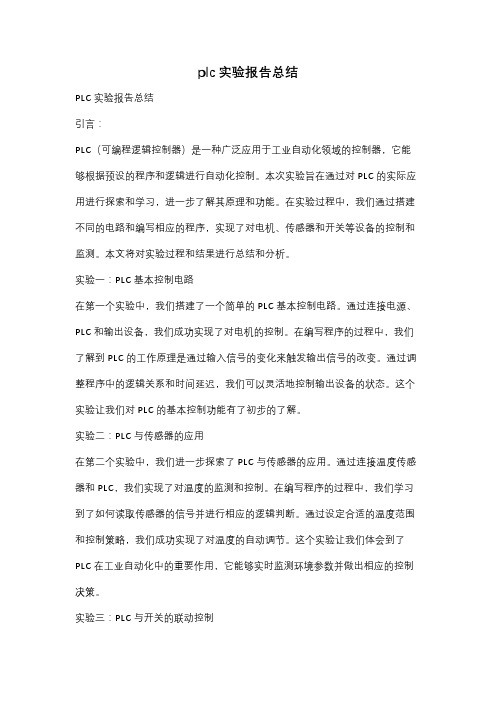
plc实验报告总结PLC实验报告总结引言:PLC(可编程逻辑控制器)是一种广泛应用于工业自动化领域的控制器,它能够根据预设的程序和逻辑进行自动化控制。
本次实验旨在通过对PLC的实际应用进行探索和学习,进一步了解其原理和功能。
在实验过程中,我们通过搭建不同的电路和编写相应的程序,实现了对电机、传感器和开关等设备的控制和监测。
本文将对实验过程和结果进行总结和分析。
实验一:PLC基本控制电路在第一个实验中,我们搭建了一个简单的PLC基本控制电路。
通过连接电源、PLC和输出设备,我们成功实现了对电机的控制。
在编写程序的过程中,我们了解到PLC的工作原理是通过输入信号的变化来触发输出信号的改变。
通过调整程序中的逻辑关系和时间延迟,我们可以灵活地控制输出设备的状态。
这个实验让我们对PLC的基本控制功能有了初步的了解。
实验二:PLC与传感器的应用在第二个实验中,我们进一步探索了PLC与传感器的应用。
通过连接温度传感器和PLC,我们实现了对温度的监测和控制。
在编写程序的过程中,我们学习到了如何读取传感器的信号并进行相应的逻辑判断。
通过设定合适的温度范围和控制策略,我们成功实现了对温度的自动调节。
这个实验让我们体会到了PLC在工业自动化中的重要作用,它能够实时监测环境参数并做出相应的控制决策。
实验三:PLC与开关的联动控制在第三个实验中,我们探索了PLC与开关的联动控制应用。
通过连接多个开关和PLC,我们实现了对多个输出设备的控制。
在编写程序的过程中,我们学习到了如何根据不同的开关状态来触发相应的输出信号。
通过合理设置开关的逻辑关系和输出设备的联动关系,我们成功实现了对多个设备的协同工作。
这个实验让我们认识到了PLC在复杂控制系统中的灵活性和可靠性。
实验四:PLC与人机界面的交互在第四个实验中,我们探索了PLC与人机界面的交互应用。
通过连接触摸屏和PLC,我们实现了通过触摸屏对设备进行控制和监测。
在编写程序的过程中,我们学习到了如何设计人机界面,包括按钮、指示灯和数据显示等元素。
plc实训报告实训总结

plc实训报告实训总结第一篇:《PLC实训,那些事儿》这周我们专业课上了一个关于PLC编程的实训,说真的,一开始我是挺抗拒的,因为编程这玩意儿对我来说就像天书一样。
不过,后来发现其实也没那么难嘛,关键是得找对方法。
实训的第一天,老师先给我们讲解了PLC的基本概念,然后就让我们自己动手了。
我跟我的小伙伴小张一组,刚开始的时候,我们俩对着电脑屏幕发呆,不知道从何下手。
还好,老师很耐心地一步步指导我们,慢慢地,我们就摸到了门道。
小张还开玩笑说:“这不就跟咱们小时候玩的电子游戏差不多嘛,只不过现在是让机器按我们的想法动起来。
”最有趣的是我们尝试控制一个小型传送带的时候,第一次编程完成后,传送带怎么也不动,我们都快急死了。
后来检查了好几遍代码,才发现原来是一个小小的语法错误。
修正之后,当传送带顺利运转起来那一刻,我们俩激动得差点跳起来,感觉比拿到满分还要开心。
这次实训让我意识到,其实学习新东西并不像想象中那么可怕,只要肯花时间和精力去钻研,总能有所收获。
而且,团队合作真的很重要,遇到难题大家一起解决,效率高多了。
最重要的是,这个过程真的挺好玩的,感觉自己好像解锁了一项新技能,对未来充满了期待。
第二篇:《PLC实训,不只是编程》提到PLC实训,很多人第一反应可能是“枯燥”、“难”。
但实话说,这次实训给我的印象远不止于此。
它不仅仅是一次技术上的练习,更是一次心灵上的成长之旅。
实训开始前,我对PLC编程一窍不通,心里没底得很。
不过,当真正接触到实际操作后,我发现这其实是一门艺术。
通过编写代码,可以让冰冷的机器按照自己的意志工作,这种感觉太酷了。
我和搭档小李一起合作,他负责查资料,我则负责编写代码。
我们互相鼓励,遇到问题共同解决,那种成就感是难以言喻的。
最难忘的是我们尝试模拟工厂自动化生产线的那个项目。
为了实现这个目标,我们几乎天天泡在实验室里,从早到晚。
有时候,为了调试一个功能,我们能连续好几个小时盯着屏幕,眼睛都快花了。
PLC可编程逻辑控制短后报告文斯
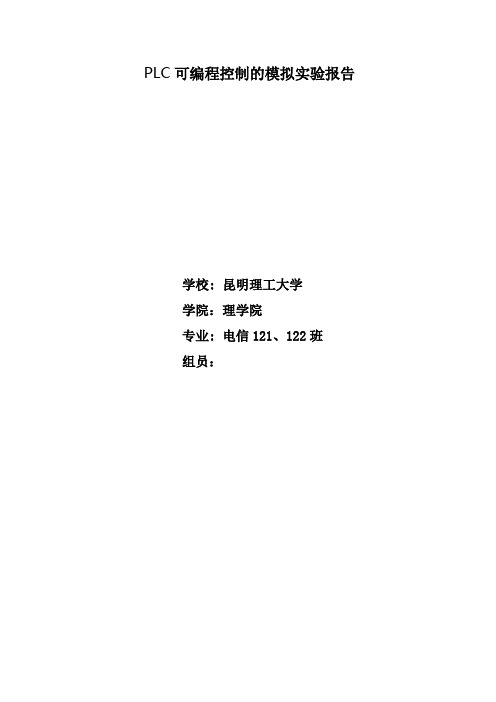
PLC可编程控制的模拟实验报告学校: 昆明理工大学学院:理学院专业: 电信121、122班组员:目录第一部分第一章可编程控制器简介第二章 S7-200可编程序控制器第三章编程元件及程序知识第四章 S7-200基本逻辑指令第二部分实验一装配流水线的模拟控制实验二四节传送带的模拟控制实验三液体混合的模拟控制实验四水塔水位控制第三部分实验总结第一部分第一章可编程控制器简介可编程序控制器,英文称Programmable Controller,简称PC。
但由于PC容易和个人计算机(Personal Computer)混淆,故人们仍习惯地用PLC作为可编程序控制器的缩写。
它是一个以微处理器为核心的数字运算操作的电子系统装置,专为在工业现场应用而设计,它采用可编程序的存储器,用以在其内部存储执行逻辑运算、顺序控制、定时/计数和算术运算等操作指令,并通过数字式或模拟式的输入、输出接口,控制各种类型的机械或生产过程。
第二章S7-200可编程序控制器S7系列PLC有S7-200、S7-300、S7-400。
SIMATIC S7-200系列小型可编程序控制器具有价格低廉、结构小巧、可靠性高、运行速度快的特点,具有丰富的指令集,强大的多种集成功能和实时特性,可单机运行,也可进行输入/输出和功能模块的扩展。
在规模不太大的控制领域是较为理想的控制设备。
硬件系统基本构成系统基本构成1. 硬件(1)基本单元又称做CPU模块,有的称为主机或本机。
包括CPU、存储器、基本输入输出点和电源等。
(2)扩展单元主机I/O点数量不能满足控制系统的要求时,用户可根据需要扩展各种I/O 模块。
(3)特殊功能模块完成某种特殊控制任务的装置。
(4)相关设备为充分和方便地利用系统的硬件和软件资源而开发和使用的设备。
2. 工业软件工业软件是为更好地管理和使用这些设备而开发的与之相配套的程序、文档及其规则的总和,它主要由标准工具、工程工具、运行软件和人机接口等几大类构成。
PLC 实验报告

PLC 实验报告《PLC 实验报告》一、实验目的本次 PLC 实验的主要目的是熟悉 PLC(可编程逻辑控制器)的基本工作原理和操作方法,通过实际编程和运行,掌握 PLC 在工业控制中的应用,提高对自动化控制技术的理解和实践能力。
二、实验设备1、 PLC 实验箱实验箱内包含 PLC 主机、输入输出模块、电源模块等。
2、编程软件使用了_____品牌的 PLC 编程软件,用于编写和调试 PLC 程序。
3、连接线缆用于连接 PLC 主机与计算机,实现程序的下载和上传。
4、实验对象实验中使用了_____作为被控对象,例如电机、灯光等。
三、实验原理PLC 是一种专门为在工业环境下应用而设计的数字运算操作的电子装置。
它采用可编程序的存储器,用来在其内部存储执行逻辑运算、顺序控制、定时、计数和算术运算等操作的指令,并通过数字式或模拟式的输入和输出,控制各种类型的机械或生产过程。
PLC 的工作原理大致分为三个阶段:输入采样阶段、程序执行阶段和输出刷新阶段。
在输入采样阶段,PLC 依次读取输入端口的状态,并将其存储在输入映像寄存器中;在程序执行阶段,PLC 按照用户编写的程序,对输入映像寄存器和输出映像寄存器中的数据进行逻辑运算和算术运算,并将结果存储在输出映像寄存器中;在输出刷新阶段,PLC 将输出映像寄存器中的数据传送到输出端口,从而控制外部设备的运行。
四、实验内容1、基本指令实验熟悉 PLC 的基本指令,如常开触点、常闭触点、线圈、定时器、计数器等。
通过编写简单的程序,实现对灯光的开关控制、电机的正反转控制等。
2、顺序控制实验掌握 PLC 的顺序控制编程方法,使用顺序功能图(SFC)编写程序,实现对生产流水线的控制,例如物料的输送、加工、分拣等过程。
3、模拟量处理实验学习 PLC 对模拟量的采集和处理,通过模拟量输入模块采集外部传感器的信号,如温度、压力等,并在程序中进行数据转换和处理,实现对被控对象的精确控制。
昆理工机电一体化实习报告
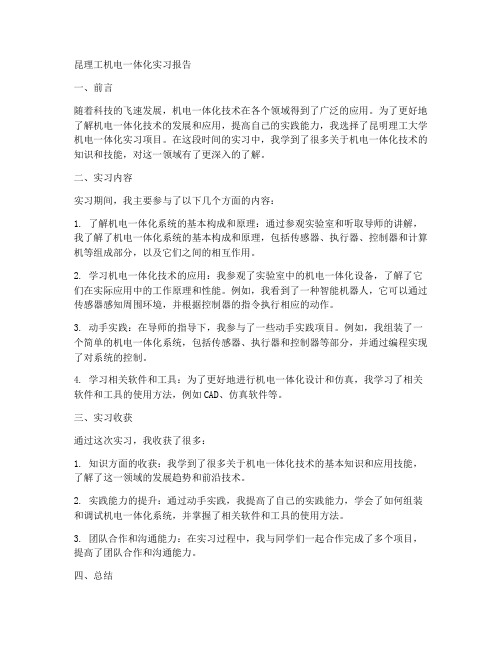
昆理工机电一体化实习报告一、前言随着科技的飞速发展,机电一体化技术在各个领域得到了广泛的应用。
为了更好地了解机电一体化技术的发展和应用,提高自己的实践能力,我选择了昆明理工大学机电一体化实习项目。
在这段时间的实习中,我学到了很多关于机电一体化技术的知识和技能,对这一领域有了更深入的了解。
二、实习内容实习期间,我主要参与了以下几个方面的内容:1. 了解机电一体化系统的基本构成和原理:通过参观实验室和听取导师的讲解,我了解了机电一体化系统的基本构成和原理,包括传感器、执行器、控制器和计算机等组成部分,以及它们之间的相互作用。
2. 学习机电一体化技术的应用:我参观了实验室中的机电一体化设备,了解了它们在实际应用中的工作原理和性能。
例如,我看到了一种智能机器人,它可以通过传感器感知周围环境,并根据控制器的指令执行相应的动作。
3. 动手实践:在导师的指导下,我参与了一些动手实践项目。
例如,我组装了一个简单的机电一体化系统,包括传感器、执行器和控制器等部分,并通过编程实现了对系统的控制。
4. 学习相关软件和工具:为了更好地进行机电一体化设计和仿真,我学习了相关软件和工具的使用方法,例如CAD、仿真软件等。
三、实习收获通过这次实习,我收获了很多:1. 知识方面的收获:我学到了很多关于机电一体化技术的基本知识和应用技能,了解了这一领域的发展趋势和前沿技术。
2. 实践能力的提升:通过动手实践,我提高了自己的实践能力,学会了如何组装和调试机电一体化系统,并掌握了相关软件和工具的使用方法。
3. 团队合作和沟通能力:在实习过程中,我与同学们一起合作完成了多个项目,提高了团队合作和沟通能力。
四、总结通过这次昆理工机电一体化实习,我对机电一体化技术有了更深入的了解,并提高了自己的实践能力。
我认识到,机电一体化技术在现代社会中起着重要的作用,将为我们的生活和工作带来更多的便利和机遇。
在今后的学习和工作中,我将继续努力学习和应用机电一体化技术,为我国的发展做出自己的贡献。
plc实训报告2篇
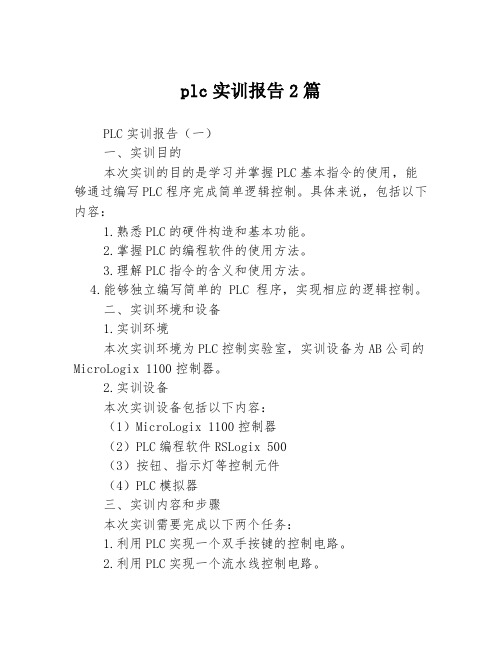
plc实训报告2篇PLC实训报告(一)一、实训目的本次实训的目的是学习并掌握PLC基本指令的使用,能够通过编写PLC程序完成简单逻辑控制。
具体来说,包括以下内容:1.熟悉PLC的硬件构造和基本功能。
2.掌握PLC的编程软件的使用方法。
3.理解PLC指令的含义和使用方法。
4.能够独立编写简单的PLC程序,实现相应的逻辑控制。
二、实训环境和设备1.实训环境本次实训环境为PLC控制实验室,实训设备为AB公司的MicroLogix 1100控制器。
2.实训设备本次实训设备包括以下内容:(1)MicroLogix 1100控制器(2)PLC编程软件RSLogix 500(3)按钮、指示灯等控制元件(4)PLC模拟器三、实训内容和步骤本次实训需要完成以下两个任务:1.利用PLC实现一个双手按键的控制电路。
2.利用PLC实现一个流水线控制电路。
下面分别介绍实现过程:1.实现双手按键的控制电路(1)控制要求制作一个可以通过双手按键控制的电路,要求按下左手按键时电路闭合,点亮左侧绿色指示灯;按下右手按键时电路闭合,点亮右侧红色指示灯;同时按下左右手按键时电路闭合,点亮中间黄色指示灯。
(2)实现步骤①将左手按键接在PLC的输入口I0/0上,右手按键接在输入口I0/1上,接线方式如图1所示。
②打开PLC编程软件RSLogix 500,新建工程,选择MicroLogix 1100控制器型号。
③编写程序,如图2所示,将I0/0和I0/1定义为输入端口,O0/0、O0/1、O0/2定义为输出端口,分别对应左侧绿色、右侧红色、中部黄色指示灯。
BEGINXIC I0/0OTE O0/0ENDBEGINXIC I0/1OTE O0/1ENDBEGINXIC I0/0XIC I0/1OTE O0/2END④将程序下载到PLC控制器中。
⑤按下左手按键,点亮左侧绿色指示灯;按下右手按键,点亮右侧红色指示灯;同时按下左右手按键,点亮中间黄色指示灯。
- 1、下载文档前请自行甄别文档内容的完整性,平台不提供额外的编辑、内容补充、找答案等附加服务。
- 2、"仅部分预览"的文档,不可在线预览部分如存在完整性等问题,可反馈申请退款(可完整预览的文档不适用该条件!)。
- 3、如文档侵犯您的权益,请联系客服反馈,我们会尽快为您处理(人工客服工作时间:9:00-18:30)。
三、验证型实验1、电动机Y/△降压起动控制(1)工作原理按下启动按钮SB1,KM1、KM3、时间继电器通电并自保,电动机接成Y型起动,2s后,时间继电器动作,使KM3断电,KM2通电吸合,电动机接成△型运行。
按下停止按扭SB1,电动机停止运行。
图1电动机Y/△减压起动控制主电路(2)I/O分配(3)梯形图图2 梯形图程序(3)程序说明按下启动按钮SB2,触点I0.1闭合内部辅助线圈M0.0通电常开触点M0.0闭合,形成自锁常开触点M0.0闭合,线圈Q0.0通电常开触点M0.0闭合,线圈Q0.2通电,定时器T38通电开始计时常闭触点Q0.2断开,形成互锁2s后,T38断开,Q0.2断电;T38闭合,Q0.1通电并自锁(4)语句表图3 语句表程序(5)仿真结果图4 状态表图5 工程图2、用PLC构成交通灯控制系统(1)控制要求如图所示,起动后,南北红灯亮并维持25s。
在南北红灯亮的同时,东西绿灯也亮,1s后,东西车灯即甲亮。
到20s时,东西绿灯闪亮,3s后熄灭,在东西绿灯熄灭后东西黄灯亮,同时甲灭。
黄灯亮2s后灭东西红灯亮。
与此同时,南北红灯灭,南北绿灯亮。
1s后,南北车灯即乙亮。
南北绿灯亮了25s后闪亮,3s后熄灭,同时乙灭,黄灯亮2s后熄灭,南北红灯亮,东西绿灯亮,循环。
图6 十字路口交通灯(2)I/O分配(3)程序设计图7十字路口交通信号灯的时序图(4)梯形图图8 基本逻辑指令设计的信号灯控制的梯形图(5)程序说明1、按下启动按钮SB1,I0.0闭合,M0.0接通闭合并自锁。
网络2中的M0.0常开触点闭合,计时器T37接通并计时;网络4中的T43接通并计时,网络20、21中的T59、T60组成1s的时钟脉冲;南北红灯工作;由于Q0.0的接通,网络12中的Q0.5接通,东西绿灯亮。
2、由于Q0.0的接通,计时器T49接通并计时,1s后Q0.7接通,东西车灯亮。
3、经过20s后,网络4中的T43动作,网络12的计时器T43常闭触点断开,Q0.5断电;网络5中的T43常开触点闭合,使得当T59的常开触点闭合时Q0.5接通,T59的常开触点断开时Q0.5断开,此时东西绿灯闪烁。
4、由于网络4中的T43动作,网络5中的T43常开触点闭合,因而计时器T44接通并计时,经过3s后,T44动作;T44在网络12中的常闭触点T44断开,东西绿灯闪烁结束,在网络14中的常闭触点T44断开,Q0.7失电,东西车灯停止工作;同时网络15的T44常开触点闭合,Q0.4接通,东西黄灯工作;网络6的T44常开触点闭合,计时器T42接通并计时;经过2s后,T42动作,网络15的T42常闭触点断开,Q0.4失电,东西黄灯停止工作。
5、当东西黄灯停止工作时,网络2中的计时器T37正好经过25s计时动作,网络10中的T37常闭触点断开,南北红灯熄灭;网络11的T37常开触点闭合,Q0.3接通,东西红灯工作;由于Q0.3的接通,因而网络16中的Q0.3常开触点闭合,南北绿灯工作。
6、由于Q0.3的接通,因而网络17的计时器T50接通并计时,1s后,网络18的T50常开触点闭合,Q0.6接通,南北车灯亮。
7、T37动作后,网络7中的T37常开触点闭合,T38接通并计时,网络3中的T37常开触点闭合,T41接通并计时。
8、经过25s后,网络7的T38动作,网络16的T38常闭触点断开,Q0.2断电;网络16中的T38常开触点闭合,使得当T59的常开触点闭合时Q0.2接通,T59常开触点断开时Q0.2断开,此时南北绿灯闪烁。
9、由于网络7的T38动作,因而网络8的T38常开触点闭合,计时器T39接通并计时,经过3s后,T39动作;T39在网络16中的常闭触点断开,南北绿灯闪烁结束,在网络18的T39常闭触点断开,Q0.6失电,南北车灯停止;同时网络19的T39常开触点闭合,Q0.1接通,南北黄灯工作;网络9的T39常开触点闭合,计时器T40接通并计时;经过2s后,T40动作,网络19中的T40常闭触点断开,Q0.1失电,南北黄灯停止工作。
10、当南北黄灯停止工作时,正好东西红灯工作了30s,即网络3中的T41计时30s,此时T41动作,网络2中的T37复位,且使得常开触点复位,进入下一次循环。
(6)语句表图9 语句表程序(7)仿真结果图10 状态表图11 工程图3、运料小车往返运行(顺序控制指令)(1)控制要求小车的示意图如图所示,设小车在初始位置时停在左边,限位开关I0.2为1状态。
按下启动按钮I0.0后,小车向右运动(简称右行),碰到限位开关I0.1后,停在该处,3s后开始左行,碰到I0.2后返回初始步,停止运动。
图12 小车运动示意图其控制结构图如图所示图13 控制结构图(2)I/O分配(3)梯形图图14 梯形图(4)程序说明1、按下按钮SB1,I0.0闭合,S0.1置位1,Q0.0通电,小车开始向右运动;2、运行至行程开关ST1处,撞击行程开关ST1,常开触点I0.1闭合,S0.2置位1,小车停止运动,T37通电并计时;3、3s后,T37的常开触点闭合,S0.3置位1,Q0.1通电,小车向左运动;4、当小车运动至行程开关ST2处时,撞击行程开关ST2,常开触点I0.2闭合,小车停止运动,并为下一次运动做准备。
(5)语句表图15语句表程序(6)仿真结果图16状态表四、设计型实验1、摇臂钻床控制系统设计(1)控制方案及流程设计1)主轴电动机1M随时都可以启停,并保持,启动按钮是SB2,停止按钮是SB1,接触器是KM1,热继电器是FR1;2)摇臂的升降控制:SB3是摇臂上升按钮,SB4是下降按钮,SQ1U是上升终端限位开关,SQ1D是下降终端限位开关,KM2是上升接触器,KM3是下降接触器。
3)假设想使摇臂上升,就要按SB3按钮,这时如果摇臂是处在抱住立柱的位置,那么SQ2限位开关的常开触点是断开的,常闭触点就是闭合的;这样控制油泵放松的接触器KM4与电磁铁YA就先得电,使摇臂与立柱松开,当放松到位时,SQ2动作,常开闭合,常闭断开,这样摇臂就可以上升了,下降也是同样的过程。
当上升结束时,松开SB3按钮,KT、KM2、KM3、KM4全部失电,经过时间继电器延时闭合的常闭触点的延时后,油泵夹紧方向的接触器KM5得电吸合。
同时YA继续得电吸合直到夹紧到位,SQ3限位开关动作,KM5与YA全部失电。
主轴与立柱箱的夹紧与放松:SB5是立柱放松按钮,SB6是立柱夹紧按钮。
(2)I/O分配(3)I/O连接图图17 I/O接线图)梯形图图18梯形图程序(5)语句表图19语句表程序(6)程序说明1、按下按钮SB2,I0.1闭合,Q0.0闭合并自锁,主轴电动机M1启动运转;2、当需要摇臂上升时,按下按钮SB3,I0.3闭合,M0.0接通。
由于网络3中的I1.1是闭合的,因此Q0.3接通闭合,液压泵电动机M3正转,松开摇臂。
摇臂松开后,网络3中的I0.7常闭触点断开,网络4中的I0.7常开触点闭合,液压泵电动机M3停转,而摇臂升降电动机M2正转,带动摇臂上升。
当摇臂上升到一定高度时,松开按钮SB3,I0.3复位,M0.0断开,网络6中的M0.2闭合一个扫描周期宽的时间,使得网络7中的M3闭合并自锁,同时T37接通,开始计时。
经过2s后T37动作,网络8中的M0.4闭合一个扫描周期宽的时间,使网络5中的M0.4闭合,接通Q0.4液压泵电动机M3反转,夹紧摇臂。
当摇臂夹紧后,SQ2、SQ3恢复初始状态,且I1.0断开,Q0.4失电,液压泵电动机M3停转,完成摇臂上升的控制过程。
3、对于摇臂下降的控制过程与摇臂上升的控制过程相同。
4、当需要对立柱或主轴箱松开或夹紧时,选择SA至适当的挡位,按下按钮SB5或SB6,网络9中的I1.2或I1.3闭合,接通M0.5及T38,网络3或网络6中的M0.5、T38闭合,接通Q0.3或Q0.4,使得立柱、主轴箱松开或夹紧。
(7)仿真结果图20状态表图21工程图2、组合机床的控制两工位钻孔、攻丝组合机床,能自动完成工件的钻孔和攻丝加工,自动化程度高,生产效率高。
两工位钻孔、攻丝组合机床如图所示。
图22 两工位钻孔、攻丝组合机床示意图(1)控制方案及流程设计系统通电,自动起动液压泵电动机M1。
若机床各部分在原位(工作台在钻孔工位SQ1动作,钻孔滑台在原位SQ2动作,攻丝滑台在原位SQ3动作),并且液压系统压力正常,压力继电器PV 动作,原位指示灯HL1亮。
将工件放在工作台上,按下起动按钮SB,夹紧电磁阀YV1得电,液压系统控制夹具将工件夹紧,与此同时控制凸轮电动机M2得电运转。
当夹紧限位SQ4动作后,表明工件已被夹紧。
起动钻孔动力头电动机M3,且由于凸轮电动机M2运转,控制凸轮控制相应的液压阀使钻孔滑台前移,进行钻孔加工。
当钻孔滑台到达终点时,钻孔滑台自动后退,到原位时停,M3同时停止。
等到钻孔滑台回到原位后,工作台右移电磁阀YV2得电,液压系统使工作台右移,当工作台到攻丝工位时,限位开关SQ6动作,工作台停止。
起动攻丝动力头电机M4正转,攻丝滑台开始前移,进行攻丝加工,当攻丝滑台到终点时(终点限位SQ7动作),制动电磁铁DL得电,攻丝动力头制动,0.3s后攻丝动力头电机M4反转,同时攻丝滑台由控制凸轮控制使其自动后退。
当攻丝滑台后退到原位时,攻丝动力头电机M4停,凸轮正好运转一个周期,凸轮电机M2停,延时3s后左移电磁阀YV3得电,工作台左移,到钻孔工位时停。
放松电磁阀YV4得电,放松工件,放松限位SQ8动作后,停止放松。
原位指示灯亮,取下工件,加工过程完成。
两个滑台的移动,是通过控制凸轮来控制滑台移动液压系统的液压阀实现的,电气系统不参与,只需起动控制凸轮电机M2即可。
在加工过程中,应起动冷却泵电机M5,供给冷却液。
(2)I/O分配(3)I/O连接图图23 I/O接线图(4)梯形图图24 梯形图程序(5)程序说明1、系统通电后,S0.1置位1,Q0.1置位,自动启动液压系统M1。
机床各部分处于原位,即工作台在钻孔工位SQ1;钻孔滑台在原位SQ2;攻丝滑台在原位SQ3;液压系统压力正常,压力继电器PV动作,此时S0.2置位1,Q2.4接通,原位指示灯HL1亮;2、将工件放在工作台上,按下启动按钮SB,常开触点I1.1闭合,则S0.3置位1,此时:1)Q2.0置位,夹紧电磁阀YV1得电;2)Q0.2置位,启动凸轮电动机M2得电运行;3、夹紧限位SQ4得电,常开触点I0.4闭合,S0.4置位1,表明工件被夹紧,此时:1)Q0.3置位,启动钻孔动力头M3,由于凸轮电动机M2正在运行,此时钻孔滑台前移,进行钻孔加工;2)Q0.6置位,启动冷却泵电动机M5;4、钻孔到终点时SQ5动作,常开触点I0.5闭合,S0.5置位1,Q0.3复位,钻孔动力头回位;5、钻孔滑台自动后退,压住SQ2时停止,常开触点I0.2闭合,S0.6置位1,Q2.1得电接通,工作台右移电磁阀YV2得电;6、工作台到攻丝工位时,SQ6动作,常开触点I0.6闭合,S0.7置位1,Q0.4接通,攻丝动力头电动机M4正转,攻丝滑台前移,开始攻丝加工;7、攻丝到终点时,SQ7动作,常开触点I0.7闭合,S1.0置位1:1)Q0.0接通,制动电磁铁DL得电,攻丝动力头制动;2)定时器T37得电并接通;8、延时0.3秒后,常开触点T37闭合,S1.1置位1,Q0.5接通,攻丝电动机M4反转,同时攻丝滑台后退至原位(压住SQ3);9、当攻丝滑台回到原位时,S1.2置位1:1)攻丝动力头电动机M4停止,凸轮正好运转一个周期;2)定时器T38接通计时;3)冷却泵停止;10、延时3秒后,S1.3置位1:1)Q0.2复位,凸轮电动机M2停止;2)Q2.2接通,左移电磁阀YV3得电;3)Q2.0复位,停夹紧电磁阀;11、工作台左移,到钻孔工位时SQ3压下,常开触点I0.1闭合,S1.4置位1:1)Q2.3接通,放松电磁阀YV4得电,放松工件;2)Q0.1复位,液压泵电动机M1停止;12、放松限位SQ8动作时,常开触点I1.0闭合,方式结束;13、原位指示灯亮,取下工件,加工过程结束。