大连石化公司储运罐区“8.29”火灾事故报告
大连石化四次事故学习体会材料
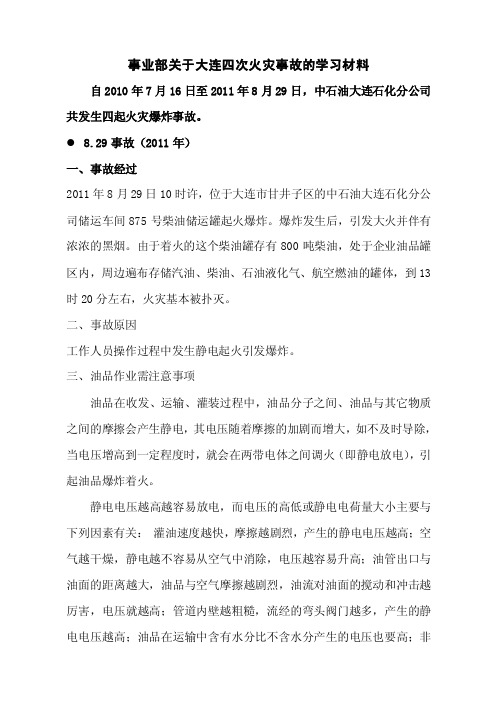
事业部关于大连四次火灾事故的学习材料自2010年7月16日至2011年8月29日,中石油大连石化分公司共发生四起火灾爆炸事故。
8.29事故(2011年)一、事故经过2011年8月29日10时许,位于大连市甘井子区的中石油大连石化分公司储运车间875号柴油储运罐起火爆炸。
爆炸发生后,引发大火并伴有浓浓的黑烟。
由于着火的这个柴油罐存有800吨柴油,处于企业油品罐区内,周边遍布存储汽油、柴油、石油液化气、航空燃油的罐体,到13时20分左右,火灾基本被扑灭。
二、事故原因工作人员操作过程中发生静电起火引发爆炸。
三、油品作业需注意事项油品在收发、运输、灌装过程中,油品分子之间、油品与其它物质之间的摩擦会产生静电,其电压随着摩擦的加剧而增大,如不及时导除,当电压增高到一定程度时,就会在两带电体之间调火(即静电放电),引起油品爆炸着火。
静电电压越高越容易放电,而电压的高低或静电电荷量大小主要与下列因素有关:灌油速度越快,摩擦越剧烈,产生的静电电压越高;空气越干燥,静电越不容易从空气中消除,电压越容易升高;油管出口与油面的距离越大,油品与空气摩擦越剧烈,油流对油面的搅动和冲击越厉害,电压就越高;管道内壁越粗糙,流经的弯头阀门越多,产生的静电电压越高;油品在运输中含有水分比不含水分产生的电压也要高;非金属管道,如帆布、橡胶、石棉、水泥、塑料等管道比金属管道更容易产生静电。
1、静电接地。
油品生产和储运设施、管道等必须进行有效静电接地,静电导体其接地电阻值不得大于4Ω。
对于船岸之间的静电连接要做到“一先一后”,即船靠好后先接静电接地线,船离泊时最后再拆静电接地线。
2、改善工艺操作条件。
在生产工艺的操作上,应控制油品处于流速范围内;应避免混入其他不相容的第二物相杂质,如水等;宜采用管道或部件;用软管作业时,要注意对软管的支撑和固定,防止滑动、摩擦产生静电;严禁向塑料容器里倒装轻质燃料油。
3、采用静电消除器。
进入码头前,必须先触摸入口处的静电释放器。
大连火灾 悲剧为何重演

着火 的 1 3号罐 体再 次发 生火灾 ,所 幸 0 没有造 成人 员伤 亡及 海水 污染 。作 为高
危 企 业 ,大 连 中 石 油 国 际 储 运 有 限 公 司
部分, 具有相 互依赖 性和关联 性 。 我们 要
从 系 统 性 的 眼 光 来 认 识 关 键 性 基 础 设 施
运输 、 能源等 方面 。 它们 往往是 高技术 局
再 次 , 发 事 件 发 生 后 , 们 必 须 认 突 我
26 《 全 与 健 康》2 1 .2上 安 001.
1 条 生命 敲响 9
文 / 海 鹰 孟
吉 林 商 业 大 厦 “ 一 ・ ” 灾 无 情 一 五 火 地 夺去 了 1 生 命 。 故 的 具 体 原 因 仍 9条 事 在 调 查 之 中 ,但 暴 露 出 的 单 位 消 防 安 全 责 任 制 不 落 实 、 消 防 设 施 维 护 保 养 不 到 位 等 问题 , 然 为冬 季 消 防 敲 响 警 钟 。 仍 一
油 泄 漏 后 极 易 导 致 环 境 污 染 , 能 源 的 生 产 、 存 、 输 应 与 环 保 部 门 实 现 应 急 预 储 运
案 的 兼 容 , 高 协 同 应 急 、 成 应 急 的 能 提 合
力。
其次 ,大连 中石 油国 际储 运 有 限公
司的事故 警示我们 : 急 管理 重在预 防 , 应
些在 事发 现场的群 众 , 过互助 、 通 自救 逃
“ 今天 早晨 珲春 街通 车 了。” 吉林 市
昌 邑 区 市 民 刘 先 生 说 。 火 时 , 先 生 恰 起 刘 在火 灾现场 警戒线 外的街 对面 。 说 , 他 当 时 见 不 到 什 么 明 火 , 是 烟 , 到 的 消 防 都 赶
大连石化公司储运罐区“”火灾事故报告.docx
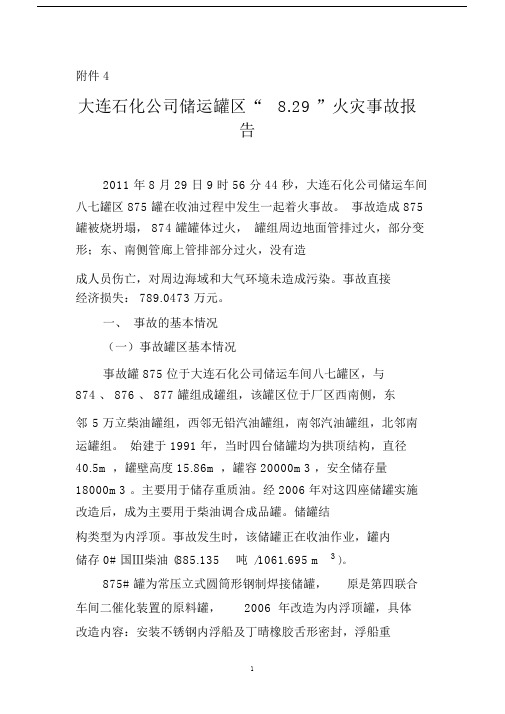
附件 4大连石化公司储运罐区“ 8.29 ”火灾事故报告2011 年 8 月 29 日 9 时 56 分 44 秒,大连石化公司储运车间八七罐区 875 罐在收油过程中发生一起着火事故。
事故造成 875 罐被烧坍塌, 874 罐罐体过火,罐组周边地面管排过火,部分变形;东、南侧管廊上管排部分过火,没有造成人员伤亡,对周边海域和大气环境未造成污染。
事故直接经济损失: 789.0473 万元。
一、事故的基本情况(一)事故罐区基本情况事故罐 875 位于大连石化公司储运车间八七罐区,与874 、 876 、 877 罐组成罐组,该罐区位于厂区西南侧,东邻5 万立柴油罐组,西邻无铅汽油罐组,南邻汽油罐组,北邻南运罐组。
始建于 1991 年,当时四台储罐均为拱顶结构,直径40.5m ,罐壁高度 15.86m ,罐容 20000m3 ,安全储存量18000m3 。
主要用于储存重质油。
经 2006 年对这四座储罐实施改造后,成为主要用于柴油调合成品罐。
储罐结构类型为内浮顶。
事故发生时,该储罐正在收油作业,罐内储存 0# 国Ⅲ柴油 (885.135吨/1061.695 m 3 )。
875# 罐为常压立式圆筒形钢制焊接储罐,原是第四联合车间二催化装置的原料罐,2006 年改造为内浮顶罐,具体改造内容:安装不锈钢内浮船及丁晴橡胶舌形密封,浮船重量为 17.193 吨;罐壁开通气孔( 12 个)、收付油口、搅拌器开口等;罐组立相关工艺管线改造;罐内做内防腐处理,防腐部位为底板、拱顶、 1 米以下的壁板罐顶包边角钢、 1 米处的壁板刷导静电涂料,干膜厚度 300 微米;罐内增上旋转循环喷头。
(二)事故部位工艺流程说明柴油组份主要来自以下装置:400万吨 / 年柴油加氢精制装置;300万吨 / 年渣油加氢脱硫装置;360万吨 / 年加氢裂化装置;200万吨 / 年煤油加氢;450 万吨 / 年常减压蒸馏B2 (常 2)、 B3(常 3)、 C1(减 1)线 (以下简称二蒸馏B2 、 B3 、 C1 线 );80万吨 / 年柴油加氢精制装置。
大连石化公司“2011.8.29”火灾事故
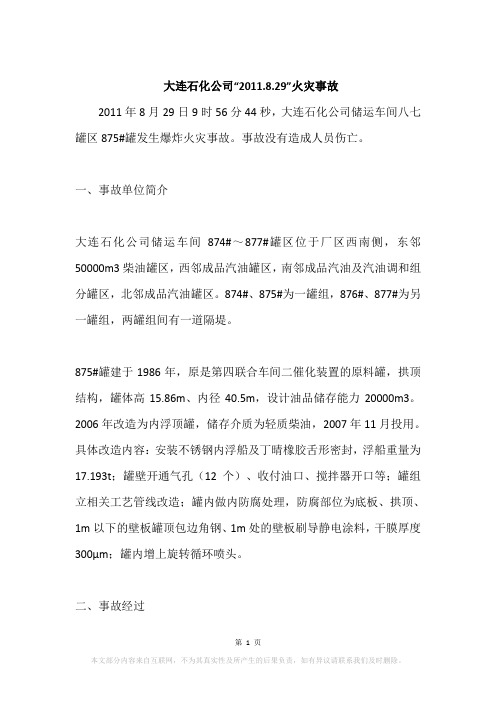
大连石化公司“2011.8.29”火灾事故2011年8月29日9时56分44秒,大连石化公司储运车间八七罐区875#罐发生爆炸火灾事故。
事故没有造成人员伤亡。
一、事故单位简介大连石化公司储运车间874#~877#罐区位于厂区西南侧,东邻50000m3柴油罐区,西邻成品汽油罐区,南邻成品汽油及汽油调和组分罐区,北邻成品汽油罐区。
874#、875#为一罐组,876#、877#为另一罐组,两罐组间有一道隔堤。
875#罐建于1986年,原是第四联合车间二催化装置的原料罐,拱顶结构,罐体高15.86m、内径40.5m,设计油品储存能力20000m3。
2006年改造为内浮顶罐,储存介质为轻质柴油,2007年11月投用。
具体改造内容:安装不锈钢内浮船及丁晴橡胶舌形密封,浮船重量为17.193t;罐壁开通气孔(12个)、收付油口、搅拌器开口等;罐组立相关工艺管线改造;罐内做内防腐处理,防腐部位为底板、拱顶、1m以下的壁板罐顶包边角钢、1m处的壁板刷导静电涂料,干膜厚度300µm;罐内增上旋转循环喷头。
二、事故经过2011年8月29日8时10分左右,大连石化公司储运车间大班长吴某接到公司生产运行处徐某的调度指令,要求将柴油调合一线从877#罐改至875#罐。
在与车间工艺员尤某核实确认后,8时30分左右,吴某通知一班班长周某准备做此项工作,周某通知内操员多某让她联系上游装置操作员等相关人员;9时30分左右,多某通知周某切换的准备工作已经做好,于是,周某赶到875#罐组立确认收油流程,并在现场用对讲机通知多某可以切换,多某随后开始切换作业;9时52分40秒,875#罐入口电动阀开启,液面从静置状态的0.969m逐渐上升;9时56分44秒,875#罐突然发生爆燃,罐底撕裂,并引起火灾。
三、事故原因1.直接原因875#罐在浮盘未浮起的情况下,收油管出口流速达4.34m/s,超过1m/s 的安全界限,产生大量静电并发生放电,在浮盘下引燃油雾、可燃性气体与空气形成的混合气体(80万t柴油加氢装置波动,造成较多轻组分进入875#罐),发生爆炸。
大连新港中石油“ ”输油管道爆炸火灾等 起事故调查处理报告

大连所属企业“7·16”输油管道爆炸火灾4起事故调查处理结果的通报安委办〔2011〕44号各省、自治区、直辖市及新疆生产建设兵团安全生产委员会,国务院安委会各成员单位,有关中央企业:2010年7月16日,位于辽宁省大连市保税区的大连中石油国际储运有限公司原油库输油管道发生爆炸,引发大火并造成大量原油泄漏,导致部分原油、管道和设备烧损,另有部分泄漏原油流入附近海域造成污染。
事故造成1名作业人员轻伤、1名失踪;在灭火过程中,1名消防战士牺牲、1名受重伤。
事故造成的直接财产损失为22330.19万元。
其后,中国石油天然气集团公司在大连地区的企业又相继发生了3起火灾事故,即2010年发生的大连中石油国际储运有限公司“10·24”火灾事故、2011年发生的中石油大连石化分公司“7·16”火灾事故和“8·29”爆炸火灾事故。
近日,国务院批复同意国务院事故调查组提出的对该4起事故的调查处理意见,认定这4起事故均为责任事故。
其中,大连中石油国际储运有限公司“7·16”输油管道爆炸火灾事故(以下简称“7·16”事故)是一起特别重大责任事故。
根据《国务院关于进一步加强企业安全生产工作的通知》(国发〔2010〕23号,以下简称《国务院通知》)关于“事故查处结案后,要及时予以公告,接受社会监督”的要求,现将事故调查处理结果通报如下:一、“7·16”事故简要情况大连中石油国际储运有限公司在大连保税区的原油库建有20个原油储罐,总库容185万立方米。
2010年5月26日,中油燃料油股份有限公司与中国联合石油有限责任公司(与中石油国际事业有限公司合署办公)签订了事故涉及原油的代理采购确认单。
在原油运抵大连港一周前,中油燃料油股份有限公司得知此批原油硫化氢含量高,需要进行脱硫化氢处理,于7月8日与天津辉盛达石化技术有限公司(以下简称天津辉盛达公司)签订协议,约定由天津辉盛达公司提供“脱硫化氢剂”,由上海祥诚商品检验技术服务有限公司(以下简称上海祥诚公司)负责加注作业。
大连石化公司储运罐区“8.29”火灾事故报告

附件4大连石化公司储运罐区“8.29”火灾事故报告2011年8月29日9时56分44秒,大连石化公司储运车间八七罐区875罐在收油过程中发生一起着火事故。
事故造成875罐被烧坍塌,874、877存量后,3)。
船及丁晴橡胶舌形密封,浮船重量为17.193吨;罐壁开通气孔(12个)、收付油口、搅拌器开口等;罐组立相关工艺管线改造;罐内做内防腐处理,防腐部位为底板、拱顶、1米以下的壁板罐顶包边角钢、1米处的壁板刷导静电涂料,干膜厚度300微米;罐内增上旋转循环喷头。
(二)事故部位工艺流程说明柴油组份主要来自以下装置:400万吨/年柴油加氢精制装置;300万吨/年渣油加氢脱硫装置;360万吨/年加氢裂化装置;200万吨/年煤油加氢;450万吨/年常减压蒸馏B2(常2)、B3(常3)、C1(减1)线(以下简称二蒸馏B2、B3、C1线);氢、馏B3(管径万加氢8产运行处调度徐锋通知,将柴油馏出油从877罐切换到875罐收油。
当时,877罐液位6.612米,温度40℃;875罐液位0.969米,温度37.6℃。
8时30分左右,吴胜指令操作员刘长青和多玮进行转油操作。
9时50分左右,内操多玮通过DCS将馏出油从877罐转875罐收,整个切换过程为自动操作。
此时,当班班长周铁在现场检查电动阀门状态是否正常。
在确认875罐调合一线阀门打开正常,并与多玮确认875罐液位上升正常后,准备确认877罐调合一线阀门是否已经关闭。
9时56分44秒左右,当班长周铁行至875罐至877罐走梯位置时,听到875罐“嘭”的一声,出现闪爆,随即着火。
现场操作人员立即报警,并进行转油、关阀等应急处理。
事故发生后,公司立即启动应急预案,下达调度指令,紧急切断了相关, Array左右的875罐含硫量小于350PPm,主要为有机硫,不易生成硫化亚铁。
硫化亚铁在与空气接触后,一般在几分钟内(最长时间不超过30分钟)就会发生自燃,875罐停止付油到开始进油,间隔9个小时23分钟,已远远超过硫化亚铁自燃时间。
大连油罐1122事故
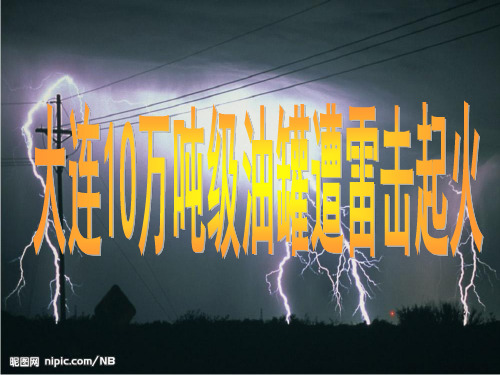
2010.7.16 大连中石油输油管道爆炸 2010年7月16日晚18时50分左右,大连市大 连新港一艘30万吨级外籍货轮在卸油的过程 当中,发生操作不当引发的爆炸。引发输油 管线爆炸,并引发原油泄漏。
2010.10.24 大连7.16爆炸油罐拆除时再 次引发火情 2010年10月24日下午,大连新港码头油 库7.16爆炸事故现场拆除曾着火油罐时, 引燃罐体内残留原油,再次发生火情。事 故没有造成人员伤亡。
各部室车间,要在日常检查中对设备设施的 防雷防静电设施进行检查,确保各防雷防静电接 地设施良好,以防类似事故的发生。
安全环保部 2011年11月23日
2011.7.16 减压蒸馏装置泄漏并引起大火 7月16日电16日14时25分,中国石油大连 石化公司厂区内1000万吨常减压蒸馏装 置换热器发生泄漏并引起大火。消防官兵 及时赶到现场灭火,事故没有人员伤亡。
2011.8.29 中石油大连油罐起火 8月29日10时06分,中石油大连石化分公司875 号柴油罐发生火灾,具体原因尚不清楚。目前, 尚无人员伤亡,情况可控。
2011年11月22日18点30分,大连的大港 集团罐区31号和32号两个十万吨级的油 罐起火。
大连消防接报之后迅速出动了700 多名官兵,180辆消防车,迅速的赶往现 场,经过了1个多小时的紧急扑救,大火 已经基本扑灭,目前没有人员伤亡报告。
据大连公安称,今晚18时35分,大连港 油品码头海滨北罐区31、32号原油罐因 雷击密封圈着火,一个小时后,火情扑 灭,无人员伤亡。
油库特大火灾事故案例分析

油库特大火灾事故案例分析一、事故案例2005年7月16日,中国大连庄河一石化公司的油库发生了一起特大规模的火灾事故。
据当地媒体报道,事故现场火光冲天,浓烟滚滚,燃烧了近16个小时才得以基本控制。
整个油库区域内的油罐液化气储罐相继爆炸,爆炸威力之大不仅炸碎了现场的钢筋水泥建筑,还影响了两公里外的居民区,造成了巨大的人员伤亡和财产损失。
这一次特大油库火灾事故在当时震惊了全国,并引起了社会各界的关注与讨论。
二、事故原因1. 设备老化事故发生的油库属于一石化公司的老旧设备,距离建成已有近30年的历史,油罐、管道等设施的老化程度较为严重。
在长期的使用过程中,由于设备维护保养不到位、更新换代不及时等原因,导致了设备老化速度加快,设备安全隐患增多。
2. 安全管理不到位据调查,一石化公司在日常的生产管理中存在安全管理不到位的问题。
对于油库设备的定期检查与维护保养工作,公司并未严格执行,导致了设备故障风险的大幅度提升。
同时,公司管理层对于员工的安全培训和教育力度不足,没有形成健全的安全防护制度,也是事故发生的重要原因之一。
3. 管理体系薄弱据相关报道,一石化公司的管理体系存在一定程度的薄弱之处,企业内部的监管体系不完善,导致了一些重要的管理环节缺失。
而这些缺失,正是导致了油库特大火灾事故发生的深层次原因。
三、事故影响1. 人员伤亡这次特大火灾事故共造成了35人死亡,196人受伤,其中有多名消防队员在扑救火灾时不幸遇难。
这一次特大火灾事故给灾区居民带来了巨大的生命安全和财产损失,也让全国人民再次深切感受到了火灾对人们生命财产带来的威胁。
2. 环境污染特大火灾事故导致了大量的油类和化学物质泄漏,不仅给事故现场周边的环境造成了巨大的污染,而且对附近居民的生活带来了极大的影响,其中还包括大量家畜的死亡。
这次特大火灾事故对环境的破坏之大让人们感受到了环境保护的重要性。
3. 经济损失特大火灾事故导致了巨大的经济损失,不仅包括了直接受灾的企业和民众,还包括了各种相关的资源浪费,比如灭火救援的人力物力资源等。
- 1、下载文档前请自行甄别文档内容的完整性,平台不提供额外的编辑、内容补充、找答案等附加服务。
- 2、"仅部分预览"的文档,不可在线预览部分如存在完整性等问题,可反馈申请退款(可完整预览的文档不适用该条件!)。
- 3、如文档侵犯您的权益,请联系客服反馈,我们会尽快为您处理(人工客服工作时间:9:00-18:30)。
大连石化公司储运罐区“8.29”火灾事故报告附件4大连石化公司储运罐区“8.29”火灾事故报告2011年8月29日9时56分44秒,大连石化公司储运车间八七罐区875罐在收油过程中发生一起着火事故。
事故造成875罐被烧坍塌,874罐罐体过火,罐组周边地面管排过火,部分变形;东、南侧管廊上管排部分过火,没有造成人员伤亡,对周边海域和大气环境未造成污染。
事故直接经济损失:789.0473万元。
一、事故的基本情况(一)事故罐区基本情况事故罐875位于大连石化公司储运车间八七罐区,与874、876、877罐组成罐组,该罐区位于厂区西南侧,东邻5万立柴油罐组,西邻无铅汽油罐组,南邻汽油罐组,北邻南运罐组。
始建于1991年,当时四台储罐均为拱顶结构,直径40.5m,罐壁高度15.86m,罐容20000m3,安全储存量18000m3。
主要用于储存重质油。
经2006年对这四座储罐实施改造后,成为主要用于柴油调合成品罐。
储罐结构类型为内浮顶。
事故发生时,该储罐正在收油作业,罐内储存0#国Ⅲ柴油(885.135吨/1061.695 m3)。
875#罐为常压立式圆筒形钢制焊接储罐,原是第四联合车间二催化装置的原料罐,2006年改造为内浮顶罐,具体改造内容:安装不锈钢内浮船及丁晴橡胶舌形密封,浮船重量为17.193吨;罐壁开通气孔(12个)、收付油口、搅拌器开口等;罐组立相关工艺管线改造;罐内做内防腐处理,防腐部位为底板、拱顶、1米以下的壁板罐顶包边角钢、1米处的壁板刷导静电涂料,干膜厚度300微米;罐内增上旋转循环喷头。
(二)事故部位工艺流程说明柴油组份主要来自以下装置:400万吨/年柴油加氢精制装置;300万吨/年渣油加氢脱硫装置;360万吨/年加氢裂化装置;200万吨/年煤油加氢;450万吨/年常减压蒸馏B2(常2)、B3(常3)、C1(减1)线(以下简称二蒸馏B2、B3、C1线);80万吨/年柴油加氢精制装置。
200万煤油加氢、400万柴油加氢、360万加氢裂化、300万渣油加氢、80万吨柴油加氢和部分二蒸馏B2、B3、C1线直馏柴油(其中二蒸馏B3、C1两个组分在西油槽罐区合走一条线去八七罐区),从装置出来专线至八七罐区柴油在线调合头,每个组分和调合总管设油品在线分析仪,通过软件控制每个组分进入调合头的比例,然后经过静态混合器混合后进入成品罐,其中调合头有两条,调合一线(管径DN450)和调合二线(管径DN300)。
当成品罐收至规定液位,按工艺规定进行循环搅拌,然后静止取样分析,分析合格后出厂。
事故发生时400万加氢柴油、300万渣油加氢柴油、部分80万加氢柴油和二蒸馏B2、B3、C1调合组分同时向875储罐输送柴油,油品调合工艺情况如下:二、事故经过8月29日上午8时10分左右,储运车间八七罐区工段长吴胜接到生产运行处调度徐锋通知,将柴油馏出油从877罐切换到875罐收油。
当时,877罐液位6.612米,温度40℃;875罐液位0.969米,温度37.6℃。
8时30分左右,吴胜指令操作员刘长青和多玮进行转油操作。
9时50分左右,内操多玮通过DCS将馏出油从877罐转875罐收,整个切换过程为自动操作。
此时,当班班长周铁在现场检查电动阀门状态是否正常。
在确认875罐调合一线阀门打开正常,并与多玮确认875罐液位上升正常后,准备确认877罐调合一线阀门是否已经关闭。
9时56分44秒左右,当班长周铁行至875罐至877罐走梯位置时,听到875罐“嘭”的一声,出现闪爆,随即着火。
现场操作人员立即报警,并进行转油、关阀等应急处理。
事故发生后,公司立即启动应急预案,下达调度指令,紧急切断了相关管线物料,对关联的上下游装置进行了循环处理。
及时启动了三级防控系统,防止污染物入海。
并在第一时间向集团公司总值班室和大连市委值班室报送了事故情况,在着火和灭火后两次向新闻媒体发布了新闻通稿。
公司消防支队和大连市消防局共出动69台消防车辆,对着火点周边的储罐、管排进行喷淋冷却、隔离、降温处理。
13时06分,现场明火全部扑灭。
三、事故原因分析(一)事故的直接原因1. 助燃物事故发生前,875罐正在收油作业,罐内储存850多吨0#国Ⅲ柴油,液面高度0.963m 。
浮船高度1.8m ,在浮船与油面之间有0.837m 左右的气相空间,体积约1000 m 3,浮船呼吸阀处于开启状态,在浮船与油面之间进入大量空气。
罐罐收油线(φ24液浮189697252. 点火源分析1)现场施工作业情况经调查,由于预报29日有雨,当天没有签发任何作业票,现场也无人员施工作业。
可排除明火因素。
2)硫化亚铁自燃分析875罐含硫量小于350PPm,主要为有机硫,不易生成硫化亚铁。
硫化亚铁在与空气接触后,一般在几分钟内(最长时间不超过30分钟)就会发生自燃,875罐停止付油到开始进油,间隔9个小时23分钟,已远远超过硫化亚铁自燃时间。
经现场观察,875罐内壁光滑,无明显腐蚀。
可排除硫化亚铁自燃因素。
3)雷电火源分析8月29日2时至3时大连石化公司上空有雷雨,但事故后对875罐进行了“剩磁”检测,检测结果为零,说明875罐没有落雷。
可排除雷击造成起火爆炸的可能性。
4)罐体设备故障分析874-877柴油储罐从2006年完成改造以来,875、876、877储罐用于柴油调合的搅拌器由于电机电流超负荷,一直处于停用状态,总电源已经切断。
可排除搅拌器原因产生火源。
5)静电分析(1)875罐收油流速调合头实时入罐流量(DCS数据)时间总流量(m3/h)平均值(m3/h)9:54 721.91718.179:57 714.44875罐调合一线入口流速测算注:以877罐液位及调合头平均流量数据为准计算管道流速(2)液位低于浮盘下的流速限制。
①国家标准《液体石油产品静电安全规程》(GB 13348-2009)5.1.4条款规定:对于电导率低于50pS/m 的液体石油产品,在注入口未浸没前,初始流速不应大于1m/s,当注入口浸没200mm后,可逐步提高流速,但最大流速不应超过7m/s。
如采用其他有效防静电措施,可不受上述限制。
注:本次柴油电导率小于1pS/m。
②美国(API)健康与环境事务部、安全和消防分会、美国石油学会《防止因静电、闪电和杂散电流引起火灾的保护措施》(2003年推荐方法、1998年9月第6版)第4.5.2 条款规定:在进油管浸入两倍于管径或61厘米(2英尺)的深度(以较小值为准)前,要将进油管线入罐流速限制在1m/s以内。
如果采用浮顶式的油罐,要遵守1m/s以下的速度极限,直至浮盘浮起。
③石油行业推荐标准(SY/T6319-2008)《防止静电、闪电和杂散电流引燃的措施》第4.5.2 条款对静电电荷的控制规定:“限制填充线和入射液流的填充速度1m/s直到填充管浸没油中2倍管径或是61mm(取二者较小值)。
当使用内浮顶储罐,要遵守1m/s的极限速度直到顶浮起来”。
依据上述规定:事故发生前,柴油流速超过了规定的限制安全流速(1m/s以下)。
(2)油罐油表面静电电位以3.82m/s进油流速计算,875罐爆炸前油面静电电位为21.59kv-32.39kv。
1987年~1988年北京劳动保护研究所实验结果:油面静电电位35kV时的放电能量为0.2mJ,可以引燃汽柴油油气(最小点火能量为0.2mJ)。
油面静电电位15kV时的放电能量为0.02mJ,引燃不了柴油油气,但可以引燃氢气(最小点火能量为0.019 mJ)。
此流速下静电可以引燃氢气,但引燃柴油油气的可能性较小。
3. 可燃物分析1)火灾前875罐收付油情况8月25日4时至26日6时,875罐完成收油作业,收油量为14161.423吨,油品组成如下:8月28日9时50分至29日0时30分,由875罐向新码头“兴池”轮装付柴油,付出量13146.381吨,罐内剩0.963m,油量885.135吨。
8月29日9时50分,875罐内温度为38.6℃(闪点为67℃)。
2)上游装置异常状态排查情况(1)400万吨柴油加氢精制装置、300万吨/年渣油加氢脱硫装置8月25日-29日DCS数据显示,事故发生前,400万吨/年柴油加氢精制装置和300万吨/年渣油加氢脱硫装置操作正常,处于平稳运行状态,质量环保检测中心采样化验数据表明馏出口质量合格。
(2)450万吨/年蒸馏装置2011年8月27日-2011年8月29日的DCS数据显示,450万吨/年蒸馏装置B2、B3、C1线流量稳定, 泵运转正常,可以排除轻烃、氮气、蒸汽等介质由出装置柴油线窜入罐区。
(3)360万吨/年加氢裂化装置8月28日10时40分,360万加氢裂化反应系统引氢气充压;8月29日10时,压力上升至2.3MPa。
8月28日10时,主汽提塔投用氢气汽提,汽提塔塔顶气去火炬;14时30分,建立分馏系统循环。
调阅8月28日至8月29日DCS记录趋势,显示主汽提塔液面、预闪蒸罐液面、分馏塔压力、航煤和柴油汽提塔液面等平稳,无异常。
事故发生时,该装置处于开工初期阶段,界区馏出口采用两道手阀隔离,无产品外送到罐区。
(4)200万吨/年煤油加氢装置200万吨/年煤油加氢装置在28日至29日期间,处于停工阶段,系统充氮气保压,干燥塔液面、压力稳定。
因装置准备开工(原计划8月31日),界区馏出口采用两道手阀隔离,无产品外送至罐区。
(5)80万吨/年柴油加氢装置80万吨/年柴油加氢装置始建于1998年3月,投产于1999年7月,装置设计年加工能力为80万吨。
2002年10月,通过更换催化剂提高空速,使装置加工能力达到100万吨/年。
该装置“初步设计”的设计原则指出:“汽提塔汽提方式以水蒸汽汽提为主,并预留氢气汽提方式”,工艺技术方案明确“汽提塔采用过热水蒸汽汽提方案,同时考虑氢气汽提的可能性”。
该装置投产初期,使用过蒸汽汽提,由于生产的柴油含水率高,便采用氢气气提方式。
8月29日7时40分时,该装置的汽提塔进料温度为230.23℃,塔底温度为223.85℃,汽提氢气一直维持在1200Nm3/h左右,塔顶压力为0.480MPa。
8时20分,因反应热源减少,汽提塔进料温度降低至216.58℃,塔底温度降至210.86℃,塔顶温度降低,回流量减少,装置开始提汽提氢气量,9时00分汽提氢气量达到1304Nm3/h,增加了约100Nm3/h,塔顶压力从0.489MPa升高到0.496MPa 。
10时25分汽提氢气量开始从1300Nm 3/h 降低,10时39分降至1206Nm 3/h 。
(6)事故后取样分析情况9月1日临时采样分析结果(用注射器从采样瓶中直接抽取气相进行分析) 采样地点 油温(℃)氢气含量% 烃含量% 877罐 280.2 0.1 390.5 0.27 490.34 0.4 80万柴油加氢 270.74 0.43 400.82 0.58 510.47 0.71 400万柴油加氢27 0 0.02 柴油出装置流汽提氢气进料温塔底温注:表明875罐内有氢气及轻烃,不能反映875号罐油面与浮船空间内气相组成。