装配后车辆性能检测与转毂试验台
浅谈重型卡车和轿车转鼓试验台的异同

172研究与探索Research and Exploration ·智能检测与诊断中国设备工程 2021.02 (上)近年来,中国的汽车产业得到了快速发展,国产车质量进步已经赢得了更多人群的青睐,汽车的销量也在逐年攀升,我国已经成为全球最大的汽车市场。
随着汽车饱有量不断增大,国家对汽车安全、环保方面的规定也日益严格,汽车厂家为了达到国家规定都纷纷添置汽车性能检测设备,加强对汽车性能的检验与质量控制。
汽车综合转鼓试验台(试验台)是重要的汽车性能检测设备,这里简单的根据车型的不同划分为重型卡车转鼓试验台和轿车转鼓试验台,本文主要对重型卡车和轿车转鼓试验的异同进行讨论。
1 国内汽车转鼓试验开展现状目前,国内汽车转鼓试验开展的比较多的是轿车企业,由于轿车的销量大、生产速度快,采用大量路试显然不能满足产量的需求。
重型卡车企业为市场提供承载力更高的车辆底盘以满足货物运输、特种汽车等领域的需要,但汽车产量要比家用轿车小很多,国内的一些知名重卡品牌还在沿用传浅谈重型卡车和轿车转鼓试验台的异同周祥(上汽依维柯红岩商用车有限公司,重庆 404100)摘要:重型卡车与轿车对转鼓试验台有着不同的要求,重型卡车对实验台空间和结构强度要求都比较高。
本文对重型卡车和轿车的转鼓试验台系统结构的异同进行讨论,最后,对转鼓试验检测内容与发动机功率测试进行介绍,可供相关人员参考。
关键词:转鼓试验;两驱和四驱车辆;功率测试中图分类号:U467 文献标识码:A 文章编号:1671-0711(2021)02(上)-0172-02统的路试方式对下线车辆进行性能测试,上汽红岩重卡在2009年、2020年分别引进了2套意大利HPA 的三轴、四轴转鼓试验台和美国“宝克BEP”的1套四轴综合转鼓台。
老式的转鼓试验台采用机械测量系统 ,是将每个转鼓组通过多组皮带连接起来,使四个转鼓组可以同步运行。
皮带轮和转鼓组连接是依靠离合器来实现的,通过控制离合器的通断来控制每个转鼓组的连接与脱开。
弹性轮胎转鼓试验台的设计

要
汽车是人类社会重要的交通运输工具,在国民经济中发挥着举足轻重的作用,构 成汽车的每一个部件是否正常工作是决定汽车行驶状态的影响因素,而汽车轮胎是汽 车重要的部件之一。轮胎的性能对汽车的牵引力、制动性、行驶的平稳性、平顺性、 越野性和燃料经济性都有直接的影响,所以说轮胎的性能直接影响汽车的使用性能。 轮胎转鼓试验台是根据车轮的实际工作状态,开发可以模拟汽车实际使用状态的 摩擦系数测定系统,探讨了转鼓试验台的结构特点,建立了车辆行驶阻力在道路上和 转鼓试验台上等值转换的试验方法,阐述了转鼓试验台的总体设计。系统采用电动机 输入动力,制动电机消耗功率,并能通过转速转矩传感器准确测量输入和输出的转矩 参数,进而通过运算得到滚动阻力系数的准确值。为研制开发滚动阻力系数试验装置 提供理论参考。
1.1 课题的目的和意义.......................................................................................1 1.2 轮胎转鼓试验台的功用................................................................................ 1 1.3 轮胎转鼓试验台的发展情况......................................................................... 2 1.4 研究内容.....................................................................................................2
Keywords:Tyre; Turn Roller Tester; Sensor; Roll Resistance
综合转鼓试验台技术规格书
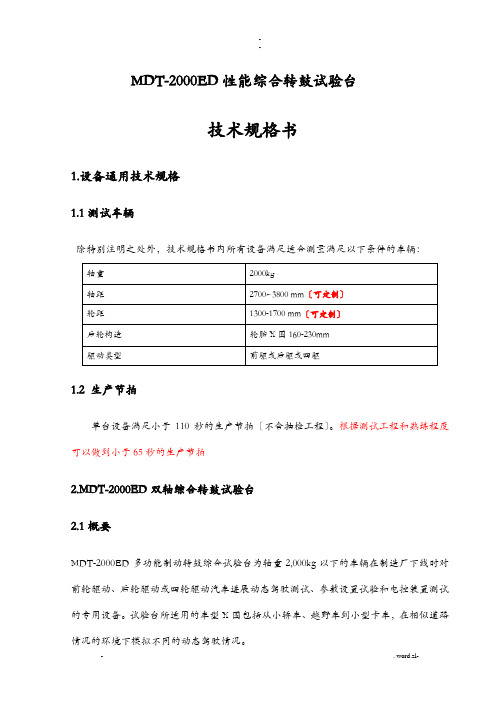
显示器采用24英寸LCD显示器,采用立柱式方法安装在试验台的侧前方。
在试验台的左侧方各安装一套试验和设定车型用操作开关〔无线遥控〕。
控制柜采用独立式安装在试验台的侧方。
2.2设备名称、型号、数量、产地
设备包含4套侧向限制挡轮:防止汽车在试验台上侧向移动对轮胎和轮圈造成损坏〔机械式〕。
设备包含平安设施:试验台应有所有必要的平安设备和平安功能保护操作者的平安以及防止车辆和试验台的损坏。
设备包含1套气动系统:气动系统与用户的压缩空气网络连接。
设备包含1套操作者操作面板:在地面上位于左侧前轴附近。
设备包含1套废气收集装置:位于后滚筒组件后面,随轴距调整装置一起移动,保持与车尾的距离不变。该装置与设备主控制器通讯,保证只有在试验中自动升起,其余时间降入地下,整车开过时不与其干预。尾气收集装置分左、右两局部,以适应排气管位置不同的车辆。
试验台主要包括4套滚筒组用以支撑车轮。每套滚筒组与一个向量控制交流电机连接。这些电机由变频器控制并且以驱动电机或发电机模式单独工作。一套中央控制单元探测电机独立同步运行所需的参数 (转速/扭矩)。数据传输通过总线系统进展,具有快速响应、恒转速、恒扭矩的控制模式及较强的过载能力。
4套交流向量控制电机:交流向量电机能实现每套滚筒组组的电控离合、制动和加速。在试验时交流电机带动滚筒组驱动汽车,也可被车驱动发电。所发电能输送给非驱动轴处电机,剩余的电能须反应给用户工厂电网,节能但不影响工厂电网正常工作。配备电能反应给工厂电网所需的变频器。
设备名称:综合转鼓试验台
设备型号:MDT-2000ED
产地:XX弥荣〔CKD组装〕
转鼓实验台——试验方法

转鼓实验台试验方法1、组成与功能1.1转鼓实验台概述汽车动力性室内台架试验的方式,主要是用无外载测功仪检测发动机功率,底盘测功机检测汽车的最大输出功率、最高车速和加速能力。
室内台架试验不受气候、驾驶技术等客观条件的影响,只受测试仪本身测试精度的影响,测试条件易于控制,所以汽车检测站广泛采用汽车动力性室内台架试验方式。
1.2转鼓实验台应具有下述主要测试功能:1)车速表、里程表检测;2)滑行性能检测;3)加速性能检测;4)底盘输出功率和扭矩的检测;5)制动性能检验。
1.3转鼓实验台可具有下述测试功能:1)油耗检测时的加载功能;2)排气污染物检测时的加载功能。
1.4转鼓实验台配备反拖装置,应能检测汽车动力传动系统的损耗功率。
2、评价指标2.1检测参数汽车动力性采用驱动轮输出功率作为检测参数。
驱动轮输出功率用底盘转鼓实验台检测。
2.2评价指标汽车动力性采用汽车发动机在额定扭矩(最大扭矩)和额定功率(最大功率)时的驱动轮输出功率作为评价指标。
2.3检测工况检测工况采用汽车额定扭矩和额定功率的工况。
即发动机全负荷与额定扭矩转速和额定功率转速所对应的直接档(无直接档时指传动比最接近1的档)车速构成的工况。
2.4限值在上述检测工况下,采用校正驱动轮输出功率与相应的发动机输出总功率的百分比作为驱动轮输出功率的限值。
M VOM VM P P /=η (1) e VOP VP P P /=η (2)式中:VM η一汽车在额定扭矩工况下的校正驱动轮输出功率与额定扭矩功率的百分比,%;VP η一汽车在额定功率工况下的校正驱动轮输出功率与额定功率的百分比,%;VOM P 一汽车在额定扭矩工况下的校正驱动轮输出功率,kW ;VPO P 一汽车在额定功率工况下的校正驱动轮输出功率,kW ;M P 一发动机在额定扭矩工况下的输出功率,kW ; e P 一发动机的额定功率,kW 。
2.5汽车动力性合格的条件Ma VM ηη≥ (3)或 Pa VP ηη≥ (4)式中:Ma η一汽车在额定扭矩工况下的校正驱动轮输出功率与额定扭矩功率的百分比的允许值,%;η一汽车在额定功率工况下的校正驱动轮输出功率与额定功率的百分比的允许Pa值,%;汽车的校正驱动轮输出功率的限值列于下表。
多功能转鼓试验台25页PPT
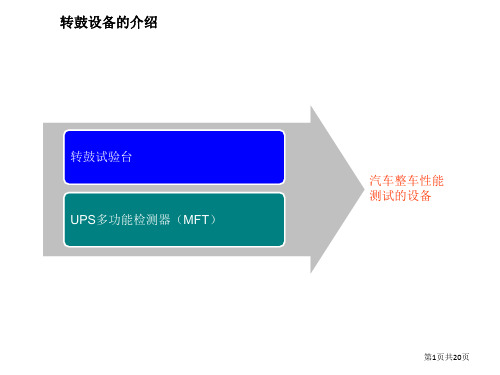
后轮刹车力测试与前轮类似。转鼓还是运行在模式4(即 转鼓由变频马达驱动),首先保持后轮行进在5Km/h(前轮 静止),MFT提示操作员不要踩刹车以便设备测量后轮阻滞 力。然后MFT提示操作员踩刹车直至后轴左右轮刹车力达标 。
第15页共20页
转鼓测试准备
车辆开进时,注意尽量不要太偏向一边,同时停车 时前轮最好紧靠后排转鼓,挡位放空挡。一切就序后按 回车键。MFT通过红外线接口控制转鼓台测试开始,转 鼓台对轴距进行调整(在轴距不对的情况下),放下提 升杆,升起尾气罩和防返杆,关闭隔音室前后门,车轮 降到转鼓表面。若车子对中十分不好,MFT会提示开动 车子对中(若车子上来就对中,就可省去此步骤)。
作为测试过程主控(Master)的MFT设备,属于UPS 系统
第12页共20页
转鼓测试功能概述
1、设备状态监控画面示例 2、转鼓测试准备 3、转鼓动态驾驶测试 4、转鼓刹车测试 5、转鼓ABS测试 6、转鼓稳态测试
第13页共20页
汽车整车UPS测试 (转鼓试验台)
整车ABS性能检测
防
车轮各轮的阻滞力≦5%
防返杆位于后轴转鼓的后部,升起时可以 防止车轮因刹车等因素脱离转鼓
第5页共20页
转鼓设备主要电气部件-超声波车辆识别装置
超声波传感器,每个转鼓台共有4个超声波传感器,其中前鼓两个超声波传感 器属于模拟量传感器,用于测量车轮到传感器的距离,提醒驾驶员对中。后两个超 声波传感器属于数字量传感器(0和1两个高低位),用来检测有无车辆驶入。
汽车变速器性能检测试验台毕业设计说明书
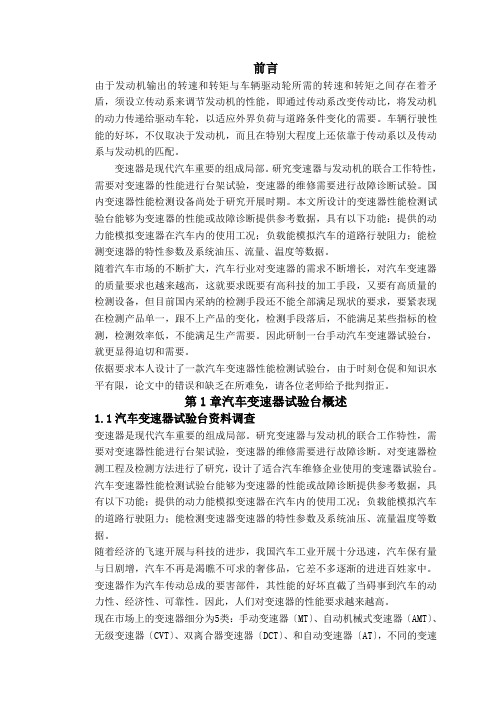
前言由于发动机输出的转速和转矩与车辆驱动轮所需的转速和转矩之间存在着矛盾,须设立传动系来调节发动机的性能,即通过传动系改变传动比,将发动机的动力传递给驱动车轮,以适应外界负荷与道路条件变化的需要。
车辆行驶性能的好坏,不仅取决于发动机,而且在特别大程度上还依靠于传动系以及传动系与发动机的匹配。
变速器是现代汽车重要的组成局部。
研究变速器与发动机的联合工作特性,需要对变速器的性能进行台架试验,变速器的维修需要进行故障诊断试验。
国内变速器性能检测设备尚处于研究开展时期。
本文所设计的变速器性能检测试验台能够为变速器的性能或故障诊断提供参考数据,具有以下功能:提供的动力能模拟变速器在汽车内的使用工况;负载能模拟汽车的道路行驶阻力;能检测变速器的特性参数及系统油压、流量、温度等数据。
随着汽车市场的不断扩大,汽车行业对变速器的需求不断增长,对汽车变速器的质量要求也越来越高,这就要求既要有高科技的加工手段,又要有高质量的检测设备,但目前国内采纳的检测手段还不能全部满足现状的要求,要紧表现在检测产品单一,跟不上产品的变化,检测手段落后,不能满足某些指标的检测,检测效率低,不能满足生产需要。
因此研制一台手动汽车变速器试验台,就更显得迫切和需要。
依据要求本人设计了一款汽车变速器性能检测试验台,由于时刻仓促和知识水平有限,论文中的错误和缺乏在所难免,请各位老师给予批判指正。
第1章汽车变速器试验台概述1.1汽车变速器试验台资料调查变速器是现代汽车重要的组成局部。
研究变速器与发动机的联合工作特性,需要对变速器性能进行台架试验,变速器的维修需要进行故障诊断。
对变速器检测工程及检测方法进行了研究,设计了适合汽车维修企业使用的变速器试验台。
汽车变速器性能检测试验台能够为变速器的性能或故障诊断提供参考数据,具有以下功能;提供的动力能模拟变速器在汽车内的使用工况;负载能模拟汽车的道路行驶阻力;能检测变速器变速器的特性参数及系统油压、流量温度等数据。
汽车排放性能四驱转鼓系统
汽车排放、性能四驱转鼓系统货物需求一览表及技术规格编制:___________________审核:__________________批准:__________________重庆力帆乘用车有限公司2011年7月20日1 设备名称及数量:汽车排放、性能四驱转鼓系统试验台一套。
2 概述2.1★主要用途2.1.1 该设备用于最大总质量不超过3.5吨的M1、M2、N1类车辆(由标准GB/T15089-2001规定,下同)的欧III、欧Ⅳ、欧Ⅴ及更高排放法规工况法排放和燃油经济性试验过程中模拟车辆行驶道路阻力。
2.1.2 该设备用于整备质量不超过5吨的车辆的环境模拟及性能试验。
2.1.3该设备可用于3.5-5.4吨中型汽车的排放和燃油消耗试验。
2.1.4 该设备用于汽车的动力性和经济性测试以及其他的性能开发试验。
2.2 ★可以满足前驱、后驱、四驱三种车辆的试验要求。
2.3 ★设备能够完全满足规格书条款5规定的工作条件。
2.4 ★投标人在投标文件中应对本招标文件的要求逐条进行详细回应,如仅在投标文件中对所有要求注明满足/符合而无相应的说明,则作为废标。
2.5 投标人投标总价应为交钥匙工程价格,在合同执行过程中,如果发现有漏项,需要增加供货范围的内容,由此产生的一切费用应当由投标人承担。
3 招标范围4 ★适用标准设备必须能够满足下列整车性能试验及相关标准的要求。
中国汽车排放第三阶段、第四阶段标准的要求,GB18352.3-2005欧洲汽车排放第三、四、五阶段标准的要求,70/220/EEC(98/69/EC)、EC 715/2007美国汽车低排放、超低排放标准以及SAE J2711的要求日本汽车排放标准JC085 ★工作条件这套设备将被安装在环境模拟仓内。
5.1 工作环境温度: -40℃~70℃。
5.2 工作环境湿度: 5% ~ 95% RH。
5.3 设备控制系统环境温度:5~45℃。
5.4 可使用的电源:三相,AC380∨(+15%,-10%),50Hz±2%单相,AC220∨(+15%,-10%),50Hz±2%5.5 可使用的压缩空气: 600kPa~ 1000kPa 。
使用动力总成台架实现实车转鼓台架测量项目的测试方法与制作流程
图片简介:本技术介绍了使用动力总成台架实现实车转鼓台架测量项目的测试方法,具体包括以下步骤:S1、首先将汽车整车通过外部转移设备转移至动力总成台架上,并且汽车的每个车轮置于独立可旋转平台上的两个辊轴之间,本技术涉及汽车测试技术领域。
该使用动力总成台架实现实车转鼓台架测量项目的测试方法,通过动力总成台架可以快速、精准地控制动力总成所处的运行环境,完美的代替并且实现转鼓测试台架整车测试中不能加速或减速并转弯操作,还能快速模拟行驶过程中,其他车辆对于测试车辆汽车的反应速度,车身姿态等,提高模拟汽车在道路形式时的状态,配合相应的软件操作系统,为车辆及自动驾驶车辆的开发提供更加优秀的测试服务。
技术要求1.使用动力总成台架实现实车转鼓台架测量项目的测试方法,其特征在于:具体包括以下步骤:S1、首先将汽车整车通过外部转移设备转移至动力总成台架上,并且汽车的每个车轮置于独立可旋转平台上的两个辊轴之间,根据汽车的型号大小,可以通过升降调节支架对独立可旋转平台的高度进行调整,使得车轮的轮毂能够与万向球笼工装对准;S2、车轮的轮毂通过万向球笼工装连接在动力总成台架的测功机上,辊轴用轴承座支撑后,固定在独立可旋转平台上,测试装配完成后,开始进行测试,测功机的扭矩以及转速控制特性好,精确快速的跟踪扭矩以及转速命令,模拟发动机扭矩转速和车轮端负载扭矩转速,从而对发动机的性能进行测试;S3、当测试要求车身姿态进行转变时,转动汽车方向盘,使得车轮转向,此时启动转向电机,转向电机带动独立可旋转平台进行转动,使得车轮与测功机之间的角度发生变化,同时转向电机按照车轮转向的加速度同步进行转向,在车轮转向时,车轮同测功机的角度由万向球笼工装实现,并且通过万向球笼工装传递扭矩,即可实现对整车进行加速或减速并转弯操作的测试,还能快速模拟行驶过程中,其他车辆对于测试车辆汽车的反应速度的测试。
2.根据权利要求1所述的使用动力总成台架实现实车转鼓台架测量项目的测试方法,其特征在于:所述步骤S1中独立可旋转平台设置有四个,汽车的四个车轮分别位于动力总成台架上的四个独立可旋转平台上。
四轮定位大灯仪、转毂试验台原理与维修
资料范本本资料为word版本,可以直接编辑和打印,感谢您的下载四轮定位大灯仪、转毂试验台原理与维修地点:__________________时间:__________________说明:本资料适用于约定双方经过谈判,协商而共同承认,共同遵守的责任与义务,仅供参考,文档可直接下载或修改,不需要的部分可直接删除,使用时请详细阅读内容美国宝克公司四轮定位、大灯仪、转毂试验台原理与维修维修技术培训资料陈刚2006-5/2008-2目录本课程申报48课时。
以专题式进行讲解,计划讲解如下专题:第一部分:四轮定位仪第一节:四轮定位仪的工艺任务及工作流程(专题1)第二节:四轮定位仪的构成(专题2)第三节:四轮定位仪测试原理分析(专题3)第四节:新车型激光头重新定位方法(专题4)第五节:激光系统初始化与标定——开发区设备(专题5)第六节:激光系统初始化与标定——红旗事业部设备(专题6)第七节:方向盘基准仪校准(专题7)第八节:设备常规操作方法及显示(专题8)第九节:车型的修改与设置(专题9)第十节:激光系统与成像分析(专题10)第十一节:四轮定位仪车辆连续跑偏质量问题的解析(专题11)第十二节:四轮定位的工艺参数修改(专题12)第十三节:工艺参数解析(专题13)第十四节:VME总线板卡概述——红旗事业部设备(专题14)第十五节:检测线DOS系统(专题15)第二部分:灯光测试仪第一节:灯光测试仪的任务第二节:灯光测试仪的构成第三节:灯光测试仪的测试原理第四节:照相机调整第五节:光轴偏转校准——开发区设备第六节:光轴偏转校准——红旗事业部设备第七节:灯箱方向性标定第八节:光强度标定——开发区设备第九节:光强度标定——红旗事业部设备第十节:增加车型。
第十一节:参数系统解析第十二节:使用与维护相关补充说明第三部分:转毂试验台第一节:转毂试验台的工艺任务及工作流程第二节:转毂试验台的构成第三节:转毂试验台的测试原理第四节:设备操作方法第五节:阻滞力标定第六节:手刹、脚刹车标定第七节:轮距修改第八节:声级标定第九节:人机接口界面第十节:参数系统解析第十一节:使用与维护相关提示前言我们公司的整车检测线是从美国宝克公司定货的设备。
汽车在转鼓实验台的性能测试及测试分析
式中: ~ M 为制动 台 的滚筒摩 擦力 矩, 试验 台标 定时候 得到 :r 为制动 台的 滚 筒半径 。 测量后 轮制动力 时操作 工移动汽 车将后轮 定位在 制动筒上, 前轮 自然 和地 面 接触 , 复上面 的操 作 。 筒 反力式 制动 试验 台测量 时前轮 和后 轮 的制动力 重 滚 是 两次制 动 分别测 量, 测量 时制动 踏板被 踩 到底, 测量得 到 的是汽 车的最 大制 动力 F 。 … 3制 动 力 F 和最 大 制动 力 F 的测 试 分析 … 由于 转鼓测 试 实际得 到 的是部分 制动 负荷 下的制 动力 F, 一 要满足 G 7 5 B 28 的要求 需要将 它对 应转化 为汽 车 的最大 制动力 F 考 虑通 过转鼓 测试 制动力 …, 和 滚筒反 力式制动 台对 同一类车 型的一 系列车辆 进行 制动力测 试试验, 试验 对 结果进 行 测试 分析 从而 建立 F 和 F 的关系 。 … 3 1 转鼓 台和 滚筒反 力式 制动 台制动 试验 对 比 试验 设备 : 宝克转 鼓试 验 台和滚 筒反 力式试 验 台。试验 车 型 :Q X X 该 E 7X , 车整备 质量 参数 为前 70 k / 4 5 k : 0 g 后 2 g 试验 过程 : 一辆 合格 的商 品车先在 转鼓 测试 台上按 照程序 测量制 动力 , 将 分 别记 录下 各轮 的制动 力大 小, 测试 完毕后, 马上 将它 由 同一人将 车转 移到滚 筒 反力 式制 动测试 台测试 , 记录 下各 车轮 的制动力 大 小 : 车辆 同此 方法进 其他
前言 新 车 出厂 前汽 车 的制 动性 能必 须满 足 G 7 5 的要 求 , 动性 能的检 查有 B2 8 制 两种方 法, 路试 法和 台试 法 。汽车 装配 厂一 般采 用台试 法 , 国内很 多轿车 厂使 用 的台试设 备是转 鼓试 验 台, 鼓试 验台是 一种 多功 能汽 车性 能测试 台, 转 用于 汽车制 动性 能、A S B 功能 、传 动系 性能检 测 。转 鼓测试 汽 车制动 力 时, 车在 汽 高速运 转, 能实现 部分 负荷制 动, 以测试 得到 的实 际制动 力是 部分 制动 负 只 所 荷 下的制 动力 , 不是 汽车 的最 大制动 力, 还不 能满 ̄G 75 对制 动力 检测 的要 =B 28 求。 本文通 过一 组试验 , 对转鼓 台测 试得 到 的制 动力 和滚 筒反 力式制 动 台测试 的制动力 进行测试 分析, 决 了转 鼓测试 部分负 荷制动 力转化 为最大 制动力 的 解 问题 。
- 1、下载文档前请自行甄别文档内容的完整性,平台不提供额外的编辑、内容补充、找答案等附加服务。
- 2、"仅部分预览"的文档,不可在线预览部分如存在完整性等问题,可反馈申请退款(可完整预览的文档不适用该条件!)。
- 3、如文档侵犯您的权益,请联系客服反馈,我们会尽快为您处理(人工客服工作时间:9:00-18:30)。
装配后车辆性能检测与转毂试验台
汽车的出厂检测项目很多,如何在生产中采用高效精确的检测设备是汽车厂家面临的难题。
通过制定合理的测试工艺流程,将转毂试验台用于装配后车辆性能的检测是一个不错的选择。
转毂试验台的结构和工作原理
转毂试验台主要由4对转毂组成,每对转毂与一个矢量调节的三相交流电机相连(见图1)。
通过变频器个别受到电机驱动(“驱动”)或电机制动(“制动”)。
“驱动”与“制动”电机通过直流中间电路进行能源交流,多余能源反馈回试验台。
不同的行驶状况可通过与转毂组连接马达来实现,操作者与试验台控制之间的通信通过不同的显示器及操作元件来实现。
转毂与制动力的计算
静态(近匀速状态)测量是通过变频器测量出交流电机的电流。
借助扭矩测量轴可以比较电机电流与扭矩之间的关系。
这个过程是通过分段式的增加力(电机电流的数值)来实现的。
这个扭矩会被换算成转毂表面的切向力(F切)。
通过这个测量出的切向力及事先给出的标称力并借助最小二乘法计算出“最贴近的模拟曲线”。
考虑到发动机转数和转毂转数之间的对应关系和已知的转毂直径,我们就可以根据以下算式计算转毂表面上切向力与电机电流之间的关系:?
F切= -Imot×kc×km×i/rrolle
式中? Imot——发动机转数和转毂转数之间的对应关系;
kc——在X-road这里可以使用扭矩测量轴获得;
km——电机生产商给出的系数;
i——电机标称扭矩/电机标称电流;
rrolle——转毂半径。
动态测量的测量原理是:通过变频器,转毂的延迟和加速都借助于石英控制的实时系统测量。
借助于降低转毂对的质量可以计算出转毂质量的反力(F反)。
F反=mred×a
式中mred——转毂降低的质量(使用x-cal 获得);
a——转毂的加速度/延迟。
各车轮损耗力F1、净拖力Fd和净制动力F2的计算如下:
Fd=拖力-F1=(I/R)×Ad- F1
式中? I——转毂转动惯量;
R——转毂直径;
I/R——转毂因子;
Ad——车轮拖动时的转毂角减速度。
F2=制动力-Fd-F1=(I/R)×Af-(I/R)×Ad
式中? Af——车轮制动时的转毂角减速度。
转毂试验台测试工艺
1.传统制动性能测试
按照GB7258的测试要求,传统制动性能的测试有空转阻滞力、行车制动及驻车制动3个项目。
(1)空转阻滞力测试。
进行该测试时,汽车在低速运行(<10km/h),挂空档,转毂开始测试汽车空转阻滞力。
各车轮阻滞力应≤5%该车轮所在轴的轴荷。
(2)行车制动测试。
此时设备测试的是真实的制动力数据,而不受系统防抱死算法的影响。
此测试的输入和输出与无ABS 的动态制动测试相同,即输入参数为前轴制动力限制值、总制动力限制值、前后轴制动力平衡限制值及左右制动力平衡限制值;输出结果为各项制动力指标是否符合要求。
判断标准如下(在产某车型):
用65~200N的制动踏板力检测整车制动:
①前轴制动力和≥60%轴荷,左右差≤20%。
②后轴制动力和≥20%轴荷,当后轴制动力和≥60%轴荷时,左右差≤24%;当后轴制动力和<60%轴荷时,左右差≤8%;
③制动力总和与整车重量的百分比≥60%;
(3)驻车制动力测试。
转毂运转时,设备提示“拉起手刹”,驾驶员用50~200N的拉力拉手刹,数敲击齿数(驻车制动器行程标准:5~9齿),驻车制动力≥20%整备质量(整车)。
2.ABS性能测试
ABS 测试分为ABS静态测试、ABS轮速传感器测试、动态ABS测试和轮速传感器交叉测试。
ABS静态测试包括:试验机与ABS电控单元模块进行通信,并使之退出工作模式进入诊断模式;验证ABS 电控单元的识别号是否正确;清除测试前在装配和加注等阶段产生的故障代码;启动ABS 电控单元的自检程序;再次建立与ABS 电控单元的通信并使之进入诊断模式;阅读重新出现的故障代码。
此测试的主要目的是避免带故障代码进行测试而引起汽车损坏。
对于ABS轮速传感器测试,首先从ABS 电控单元中下载轮速传感器测试程序,然后电动机驱动惯性转毂,检测是否接收到轮速传感器的信号,并且将测量到的速度数据与限制值相比较。
此测试的主要目的是测试ABS 轮速传感器的装配和连接是否正确,以及轮速传感器的质量和精度。
图2为公司某车型单轮轮速传感器信号,表1为轮速传感器测试方式。
动态ABS测试阶段,试验机模拟ABS 工作时电控单元的所有动作:依次向每个车轮的泄压阀和增压阀发出控制命令,评价其制动力的衰减百分比的上限和每个增压阀恢复百分比的下限。
图3为装有BOSCH 8.0 ABS的某轿车在转毂试验台上测得的制动力曲线。
在轮速传感器交叉测试阶段中,试验机首先使惯性转毂以不同的转速转动,并读取和验证各轮速传感器的转速数据;查询在制动测试期间电控单元检测到的故障代码;发出控制命令使电控单元退出诊断模式。
此测试的主要目的是测试每个轮速传感器的装配和连接是否有交叉,这种交叉会使制动性能恶化。
表2为某车型的电磁阀功能测试和阀体关系。
3.空调制冷性能测试
该测试在汽车静止时完成,转毂试验台读取空调系统温度传感器的数值,并与设定值比较,确认是否合格。
需要注意的是,开始测试前汽车需要开启空调运转2min以上,以确保空调进入稳定工作状态。
4.速度表校验测试
将汽车加速,当汽车仪表板显示车速在40km/h时开始测试,确认汽车仪表显示速度是否在32.8~40km/h范围内。
车速表指示车速V1与实际车速V2之间应符合下列关系式:
0≤V1-V2≤(V2/10)+4。
5.自动巡航功能测试
将汽车加速到80km/h启动巡航开始测试,确认巡航功能正常。
6.测试流程
通过详细分析转毂试验项目,制定如下转毂性能测试的工艺流程:测试汽车编码输入-空调制冷功能测试-ABS静态测试-轮速传感器测试-汽车空转阻力测试-速度表校核测试-巡航测试-汽车传动系测试-传统行车制动性能测试-ABS动态测试-倒档测试-驻车制动测试-系统判断测试结果并打印。
小结
文中针对ABS 制动性能所采用的测试设备和程序能很好地满足汽车出厂的质量要求,在提高工艺的柔性、技术的先进性和可扩充性等方面具有优势。