计算凹模外形尺寸、选择典型组合
计算凸凹模尺寸

孔4×Ф5.5凸、凹模尺寸计算:凸模: d 凸=(d m in + x ∆)0凸δ-=(5.5+0.5⨯0.3)002.0-=5.65002.0-凹模: d 凹=(d 凸+ Z m in )凹δ0=(5.65+0.64)02.00+=6.2902.00+ 孔Ф26凸凹模尺寸计算:凸模: d 凸=(d m in + x ∆)0凸δ-=(26+0.5⨯0.52)002.0-=26.26002.0- 凹模: d 凹=(d 凸+ Z m in )凹δ0=(26.26+0.64)02.00+=26.9025.00+ 外形凸凹模尺寸的计算(落料):根据零件的形状,凹模磨损后其尺寸变化都为第一类A (磨损后尺寸增大) 由教材表3—6查得 1x =0.5 2x =0.5凹A =凹(δ)∆+x A 式 ( 1—2 ) 式中: A —工件基本尺寸(mm) △—工件公差(mm ) 凹δ-凹模制造公差(mm )1凹A =025.0045.1705.17015.0170-∆--==⨯+凹)(δ025.005.15415.01542--=⨯+=凹)(凹δA凹模的外形一般有矩形与原形两种。
凹模的外形尺寸应保证凹模有足够的强度与刚度。
凹模的厚度还应包括使用期内的修磨量。
凹模的外形尺寸一般是根据材料的厚度和冲裁件的最大外形尺寸来确定的。
查《冲压工艺及模具设计》万战胜主编中国铁道出版社表2—22 凹模外形尺寸得凹模最小壁厚C=52mm 凹模厚度H=36mm故凹模板的外形尺寸:长 L=L1+2C=170+52×2=274mm宽 B=L2+2C=154+52×2=258mm故L×B×H=274×258×36 mm又查《模具手册之四—冲模设计手册》编写组编著机械工业出版社表14-6 矩形和圆形凹模外行尺寸(GB2858-81)将上述尺寸改为315×250×40mm。
冲压模具课程设计指导
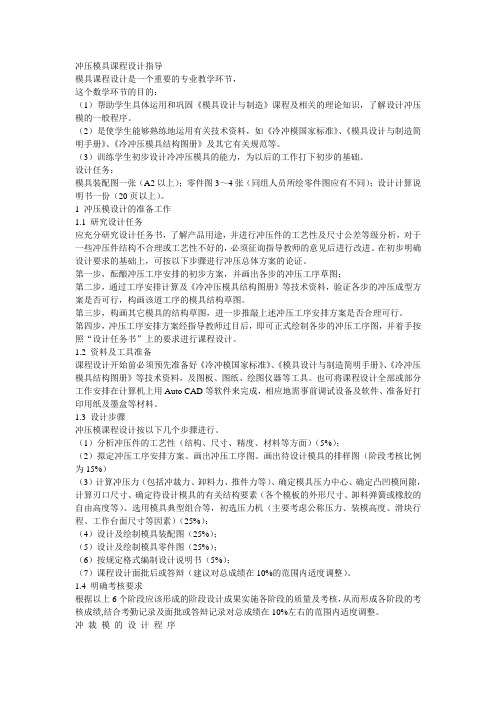
冲压模具课程设计指导模具课程设计是一个重要的专业教学环节,这个数学环节的目的:(1)帮助学生具体运用和巩固《模具设计与制造》课程及相关的理论知识,了解设计冲压模的一般程序。
(2)是使学生能够熟练地运用有关技术资料,如《冷冲模国家标准》、《模具设计与制造简明手册》、《冷冲压模具结构图册》及其它有关规范等。
(3)训练学生初步设计冷冲压模具的能力,为以后的工作打下初步的基础。
设计任务:模具装配图一张(A2以上);零件图3~4张(同组人员所绘零件图应有不同);设计计算说明书一份(20页以上)。
1 冲压模设计的准备工作1.1 研究设计任务应充分研究设计任务书,了解产品用途,并进行冲压件的工艺性及尺寸公差等级分析,对于一些冲压件结构不合理或工艺性不好的,必须征询指导教师的意见后进行改进。
在初步明确设计要求的基础上,可按以下步骤进行冲压总体方案的论证。
第一步,酝酿冲压工序安排的初步方案,并画出各步的冲压工序草图;第二步,通过工序安排计算及《冷冲压模具结构图册》等技术资料,验证各步的冲压成型方案是否可行,构画该道工序的模具结构草图。
第三步,构画其它模具的结构草图,进一步推敲上述冲压工序安排方案是否合理可行。
第四步,冲压工序安排方案经指导教师过目后,即可正式绘制各步的冲压工序图,并着手按照“设计任务书”上的要求进行课程设计。
1.2 资料及工具准备课程设计开始前必须预先准备好《冷冲模国家标准》、《模具设计与制造简明手册》、《冷冲压模具结构图册》等技术资料,及图板、图纸、绘图仪器等工具。
也可将课程设计全部或部分工作安排在计算机上用Auto CAD等软件来完成,相应地需事前调试设备及软件、准备好打印用纸及墨盒等材料。
1.3 设计步骤冲压模课程设计按以下几个步骤进行。
(1)分析冲压件的工艺性(结构、尺寸、精度、材料等方面)(5%);(2)拟定冲压工序安排方案、画出冲压工序图、画出待设计模具的排样图(阶段考核比例为15%)(3)计算冲压力(包括冲裁力、卸料力、推件力等)、确定模具压力中心、确定凸凹模间隙,计算刃口尺寸、确定待设计模具的有关结构要素(各个模板的外形尺寸、卸料弹簧或橡胶的自由高度等)、选用模具典型组合等,初选压力机(主要考虑公称压力、装模高度、滑块行程、工作台面尺寸等因素)(25%);(4)设计及绘制模具装配图(25%);(5)设计及绘制模具零件图(25%);(6)按规定格式编制设计说明书(5%);(7)课程设计面批后或答辩(建议对总成绩在10%的范围内适度调整)。
冲裁模凸凹模尺寸计算

第四章 冲裁
一、冲裁件的工艺性分析
3.冲裁件尺寸标注 冲裁件尺寸的基准应尽可能 与其冲压时定位 基准重合 ,并选 择在冲裁过程中基本上下 不变动
的面或线上。
第四章 冲裁
二、冲裁工艺方案的确定
1.冲裁工序的组合 (1)根据生产批量来确定 (2)根据冲裁件尺寸和精度等级来确定 (3)根据对冲裁件尺寸形状的适应性来确定 (4)根据模具制造安装调整的难易和成本的高低来确定 (5)根据操作是否方便与安全来确定
第四章 冲裁
一、凸、凹模刃口尺寸计算原则(续)
计算原则: 1.设计落料模先确定凹模刃口尺寸。以凹模为基准,间隙取 在凸模上,即冲裁间隙通过减小凸模刃口尺寸来取得。 设计冲孔模先确定凸模刃口尺寸。以凸模为基准,间隙取 在凹模上,冲裁间隙通过增大凹模刃口尺寸来取得。 2.根据冲模在使用过程中的磨损规律,设计落料模时,凹模 基本尺寸应取接近或等于工件的最小极限尺寸; 设计冲孔模时,凸模基本尺寸则取接近或等于工件孔的最 大极限尺寸。 模具磨损预留量与工件制造精度有关。
第四章 冲裁
二、冲裁工艺方案的确定
2、冲裁顺序的安排 (1)级进冲裁顺序的安排 1)先冲孔或冲缺口,最后落料或切断,将冲裁件与条料分离。 2)采用定距侧刃时,定距侧刃切边工序安排与首次冲孔同时进 行,以便控制送料进距。 (2)多工序冲裁件用单工序冲裁时的顺序安排 1)先落料使坯料与条料分离,再冲孔或冲缺口。 2)冲裁大小不同、相距较近的孔时,为减少孔的变形,应先冲 大孔后冲小孔。
+δ A
0 0
DT = (D A − Z min )−δ T = (Dmax − x∆ − Z min )−δ T
(2)冲孔 0 d T = (d min + x∆ )−δ T
圆形缺口垫片课程设计说明书

3.2.4材料及技术要求...................................12
3.2.5凹模零件图.......................................13
1.4.2卸料力...........................................7
1.4.3顶件力..................................ቤተ መጻሕፍቲ ባይዱ........7
1.4.4总冲压力.........................................7
第二节 冲压工艺性分析...................................5
1.2.1冲压件材料.......................................6
1.2.2冲压件结构.......................................6
1.2.3冲压件尺寸精度...................................6
前 言
冲压是使板料经分离或成形而得到制件的加工方法。冲压利用冲压模具对板料进行加工。常温下进行的板料冲压加工称为冷冲压。冷冲压模具在工业生产中的地位:是大批生产同形产品的工具,同时也是工业生产的主要工艺装备。模具工业是国民经济的基础工业。
模具可保证冲压产品的尺寸精度和质量稳定,而且在加工中不破坏产品表面。用模具生产零件可以采用冶金厂大量生产的廉价的轧制钢板或钢带为坯料,且在生产中不需要加热,具有生产效率高、质量好、重量轻、成本低且节约能源和原材料等一系列优点,是其它加工方法所不能比拟的。使用模具已成为当代工业生产的重要手段和工艺发展方向。现代制造工业的发展和技术水平地提高,在很大程度上取决于模具工业的发展。
各种冲压模具结构形式与设计
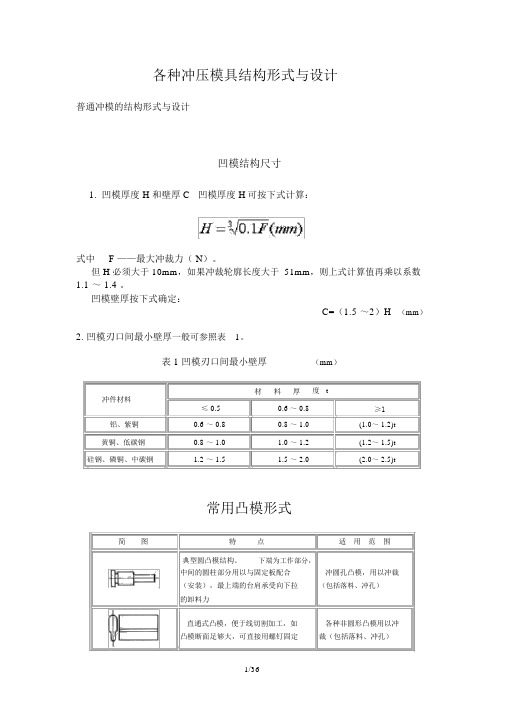
各种冲压模具结构形式与设计普通冲模的结构形式与设计凹模结构尺寸1.凹模厚度 H 和壁厚 C 凹模厚度 H可按下式计算:式中 F ——最大冲裁力( N)。
但 H 必须大于 10mm,如果冲裁轮廓长度大于 51mm,则上式计算值再乘以系数1.1 ~ 1.4 。
凹模壁厚按下式确定:C=(1.5 ~2)H(mm)2.凹模刃口间最小壁厚一般可参照表1。
表 1 凹模刃口间最小壁厚(mm)材料厚度 t冲件材料≤ 0.50.6 ~ 0.8≥1铝、紫铜0.6 ~ 0.80.8 ~ 1.0(1.0~ 1.2)t 黄铜、低碳钢0.8 ~ 1.0 1.0 ~ 1.2(1.2~ 1.5)t 硅钢、磷铜、中碳钢 1.2 ~ 1.5 1.5 ~ 2.0(2.0~ 2.5)t常用凸模形式简图特点适用范围典型圆凸模结构。
下端为工作部分,中间的圆柱部分用以与固定板配合冲圆孔凸模,用以冲裁(安装),最上端的台肩承受向下拉(包括落料、冲孔)的卸料力直通式凸模,便于线切割加工,如各种非圆形凸模用以冲凸模断面足够大,可直接用螺钉固定裁(包括落料、冲孔)断面细弱的凸模,为了增加强度和凸模受力大,而凸模相刚度,上部放大对来说强度、刚度薄弱凸模一端放长,在冲裁前,先伸入单面冲压的凸模凹模支承,能承受侧向力整体的凸模结构上部断面大,可直单面冲压的凸模接与模座固定节省贵重的工具钢或硬凸模工作部分组合式质合金组合式凸模,工作部分轮廓完整,圆凸模。
节省工作部分与基体套接定位的贵重材料冲裁凹模的刃壁形式简特点适用范围图刃壁带有斜度,冲件或废料不易滞留在刃孔内,因而减轻对刃壁的磨适用于冲件为任何形状、各损,一次刃磨量较少。
刃口尺寸随刃种板厚的冲裁模(但料太薄不磨变化宜采用)凹模工作部分强度好α一般取5′~ 30 ′刃壁带有斜度,漏料畅通,但由于适用于材料厚度小于3mm 刃壁与漏料孔用台肩过渡,因此凹模的冲裁模工作部分强度较差凹模厚度即有效刃壁高度。
刃壁带有斜度,冲件或废料不易滞留在刃孔内,因而刃壁磨损小,一次刃磨量少。
整体式凹模轮廓尺寸的

二班六组
三,整体式凹模轮廓尺寸的确定
凹模的尺寸指凹模的高度、长度、与宽度 (矩形凹模)或高度与外径(圆形凹模) 冲裁时凹模承受冲裁力和侧向挤压力的作 用。由于凹模结构形式和固定方法的不同, 受力情况又比较复杂,目前尚不用理论计算 方法确定凹模轮廓尺寸。在生产中,通常根 据冲裁的板料厚度和冲件的轮廓尺寸,或者 凹模孔口刃壁间距离,按经验公式来确定。
• 通过观察上式,发现上 式仅根据冲裁件的厚度 取值,并没有考虑到材 料力学性能的差异,由 此可以得出:只要材料 厚度和排样图相同,不 论冲裁何种材料,凹模 的尺寸都是相同的,这 显然是不合理的,说明 上式有局限性。
凸凹模:复合模中同时缘之间的壁厚决定于冲裁件 的孔边距,所以当冲裁孔边距较小时必须考虑凹凸模强度。 为保证凹凸强度,其壁厚不应小于允许的最小值。如果小于 允许的最小值,就不宜采用复合膜进行冲裁。 最小壁厚: 倒装复合膜的冲孔废料容易积存在凹凸模型孔内,所受胀力 大,凹凸模最小壁厚要大些。 正装复合膜的冲孔废料由装在上模的打料装置推出,凹凸模 型孔内不积存废料,胀力小,最小壁厚可小于倒装复合模的 凹凸模最小壁厚值。 目前复合膜的凹凸模最小壁厚值按经验公式确定,倒装式复 合膜的最小壁厚见表3-14,正装可比倒装较小。
凹模厚(高)度:H=ks(>=8) ① s----垂直送料方向的凹模刃壁间最大距离 (mm)
凹模厚度系数k 见课本表3-13
K-----系数,参考板料厚度的影响 由材料厚度和b1决定
送料方向的凹模长度:L=s1+2s2 S1-----送料方向的凹 模刃壁最大距离 (mm) S2-----送料方向的凹 模刃壁至凹模边缘的 最小距离(mm)其 值查表3-12
新第二章冲裁模的典型结构三部分

2.10.3硬质合金块的固定
1.焊接固定法 这种方法操作方便,模具结构简单.
2.机械固定法(如图2.10.5) 此法牢固可靠,配合面的精度较高.
3.热套(或冷压)固定法 4.黏结固定法
a)、f)、h)、i )螺钉固定;b)、c)压板固定;d)斜面固定; e)冷鉚固定;g)销钉固定
图2.10.5 硬质合金的机械固定
为保证送料精度使条料紧靠一侧的导料板送进,可采用测压
装置(如图2.8.23)
2.8.5卸料与推件装置的设计
1.卸料零件 ⑴刚性卸料(如图2.8.24) ⑵弹性卸料(如图2.8.25)
2.推件和顶件装置 推件和顶件的目的是将制件从凹模中推出或顶出(如图
2.8.26)。 刚性推件装置(如图2.8.27) 弹性推件装置(如图2.8.28) 弹性顶件装置 (如图2.8.29)
1—顶件块;2—顶杆;3—支承板;4—橡胶块 图 2.8.29
2.8.6 标准模架及导向零件
按导柱在模架上的固定位置不同,导柱模架的基本形式有: 对角导柱模架、后侧导柱模架、中间导柱模架、四导柱模架。 按导柱导套导向方式的不同模架又分为:
滑动导向模架(如图2.8.30) 滚动导向模架(如图2.8.31) 滑动式导柱导套(图 2.8.32) 滚珠式导柱导套(图2.8.33 )
2.硬质合金的牌号与性能 一般硬质合金是以碳钨和碳化钛为基,以钴、镍或铁做
粘结剂,经烧结而成。
2.10.2硬质合金冲裁模的结构设计特点
1.排样要求 级进模中大部分采用侧刃定位,侧刃位置要适当 (图2.10.1)。 排样时应避免凸凹模单边工作,在不浪费材料的前提下,可
将交错排样改为并列排样,消除单边冲裁(如图2.10.2)。
(4)合理的选用精冲模具材料、热处理方法和模具零件 的加工工艺性;
冲裁模设计

冲裁模设计一、分析本例的工艺性1.(1)该零件形状简单、对称。
(2)该零件圆弧与直线相切处有尖角,但图纸上无特殊要求,用线切割钼丝半径加单边放电间隙代替尖角是允许的。
(3)冲件上无悬臂和狭槽。
(4)最小孔边距为(14-6)/2=4>t ,最小孔间距为(28-2×5-2×2-6)/2 = 4 > t = 1.2 。
(5)该冲件端部带圆弧,用落料成形是允许的。
(6)检查最小孔的刚度和强度。
由Q235查得τ= 304~373MPa 。
再由表2-1查得b ≥ 0.8t=0.8×1.2=0.96,该件上的最窄孔为4,远远大于b =0.96的要求。
2、分析公差和粗糙度 (1)公差该件的最小公差的尺寸为075.006+Φ, 查得精度等级为IT11,低于冲孔可以达到的精度等级为IT10。
(2)粗糙度 本例未作特殊要求。
3、被冲材料为Q235,冲裁性能很好。
根据以上分析,本例的冲裁工艺性好。
二、确定基本冲压工序1.由图2-1可得,该件外形为落料,内形为冲孔,冲孔有一圆孔和两长圆形孔。
2. 确定的冲裁工艺方案方案一:先落料、后分三次冲孔,采用四付单工序模 方案二:先落料、后同时冲三孔,采用二付单工序模 方案三:先冲孔、后落料,采用级进模冲裁方案四:先冲孔、后切断,采用少废料级进模冲裁 方案五:同时冲孔、落料,采用复合工序模方案一和方案二的模具结构简单,生产率低,既不能满足产量要求又不经济;方案四最大的特点是省料,但冲件精度低,若按长度方向送进零件尺寸可以保证但料窄,送料步距大,不方便;若按宽度方向送进,冲件圆弧与直边吻接不好。
方案五冲件精度高但操作不方便,生产率不高;方案三既能满足冲件精度要求,模具数量少,操作方便,生产率高,若采用侧刃定距还便于实现自动送料。
通过以上分析,采用方案三较好。
排样设计 确定本例的排样方法,查出搭边、计算料宽和材料利用率一、确定本例的排样方法1、由确定的工艺方案得出,本例采用的是冲孔、落料、级进模冲裁,侧刃定距2、该零件是窄长件采用单直排3、因为两长圆孔与中间圆孔的孔边距4<5mm,故采用冲长圆孔与冲圆孔分步冲裁的方法。
- 1、下载文档前请自行甄别文档内容的完整性,平台不提供额外的编辑、内容补充、找答案等附加服务。
- 2、"仅部分预览"的文档,不可在线预览部分如存在完整性等问题,可反馈申请退款(可完整预览的文档不适用该条件!)。
- 3、如文档侵犯您的权益,请联系客服反馈,我们会尽快为您处理(人工客服工作时间:9:00-18:30)。
L=2(L1+L2) L1∥=15.2+15.2+3=33.4 L1⊥=67/2=33.5 L2按表2.5-1查得为30 L∥=2(L1∥+L2)=2×(33.4+30)=126.8 L⊥=2(L1⊥+L2)=2×(33.5+30)=127 (3)判断送料方向 ∵ L1∥ =126.8≤L1⊥=127
2.5 计算凹模外形尺寸、选择典型组合
2.5.3 本例凹模外形尺寸的计算,确定典型组合 (1)由排样图确定各凹模型孔位置如图2-19所示。
(在排样图上有两侧刃孔)。
图2-19 凹模型孔位置
2.5 计算凹模外形尺寸、选择典型组合
(2)确定凹模外形尺寸,在本例中已计算压力中心在距落 料型孔中心6.6mm处。 外形尺寸按下式计算
计算凹模外形尺寸、选择典型组合
2.5.1计算凹模外形尺寸 凹模的外形一般按下述的步骤进行。
1)确定凹模的几何中心。凹模的几何中心一般也 是模柄的中心。要求凹模的几何中心与压力中心 重合。如受模具结构限制或工件的精度低、冲裁 间隙大时,可允许凹模的几何中心与压力中心稍 有偏离,能不但超出模柄的投形面积的范围。否 则应采用置偏模柄的办法,使模柄中心与压力中 心重合。
2.5 计算凹模外形尺寸、选择典型组合
2)初步计算外型尺寸。
L=2(L1+L2)
(2-14)
式中 L-凹模的长度或宽度方向的尺寸;
L1-凹模几何中心到最远型孔孔壁的距离。
L2-凹模几何中心最远型孔孔壁到凹模边 缘的距离。查表2-9选用
3)选取标准值,确定凹模厚度。
2.5 计算凹模外形尺寸、选择典型组合
2.5.2 选择典型组合 选择典型组合时应考虑如下几方面的问题。 确定模具类型:是级进模(单工序模)还是复合模。
(1)级进模(单工序模) ① 有无导向 ② 有导向时是固定导板导向还是弹压导板导向或导柱导 套导向 ③ 卸料方式:弹压卸料还是固定卸料。 ④ 横向送料还是纵向送料。
(2)复合模 ① 倒装还是顺装(顺装在国标中无标准) ② 凹模外形是圆形还是矩形 ③ 是薄凹模还是厚凹模. 根据这些条件就可以选定典型的组合。
送料
∴为纵向
(4)选择典型组合: 由弹压卸料、纵向送料,选择典型组合为:
125×125×120 -150GB2872.1-81 凹模外形尺寸为125×125×16