第2章冲裁模设计-4_凹模尺寸计算
凸、凹模刃口尺寸的计算
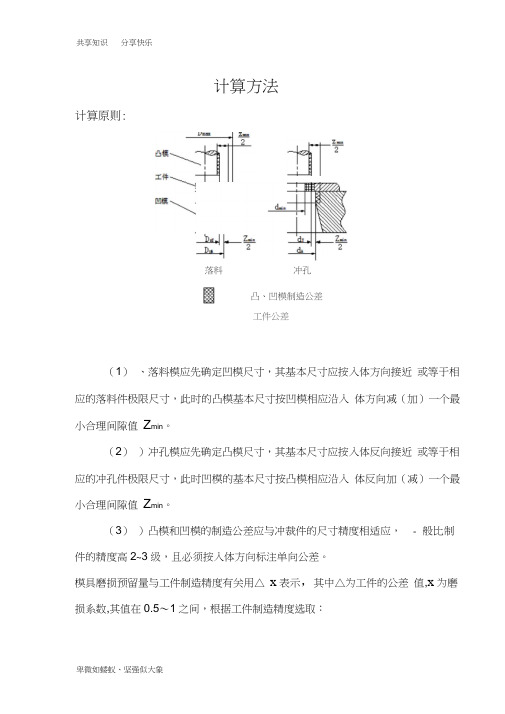
工件公差(1) 、落料模应先确定凹模尺寸,其基本尺寸应按入体方向接近 或等于相应的落料件极限尺寸,此时的凸模基本尺寸按凹模相应沿入 体方向减(加)一个最小合理间隙值 Z min 。
(2) )冲孔模应先确定凸模尺寸,其基本尺寸应按入体反向接近 或等于相应的冲孔件极限尺寸,此时凹模的基本尺寸按凸模相应沿入 体反向加(减)一个最小合理间隙值 Z min 。
(3) )凸模和凹模的制造公差应与冲裁件的尺寸精度相适应, - 般比制件的精度高2~3级,且必须按入体方向标注单向公差。
模具磨损预留量与工件制造精度有关用△ x 表示,其中△为工件的公差 值,x 为磨损系数,其值在0.5〜1之间,根据工件制造精度选取:计算原则:计算方法落料 冲孔凸、凹模制造公差工件精度IT10级以上X =1.0工件精度IT11〜13X =0.75工件精度IT14X =0.5规则形状冲裁模凸模、凹模制造偏差51、分别加工法§凸+ §凹W Z max- Z min落料D凹=(D max - X △0D凸=(D凹-Z min )二凸=(D max - X △Z min )」凸冲孔d凸=(d min + X △) 1凸d凹=(d凸+ Z min ) 0 = ( d min + X△Z min ) 0孔心距孔心距属于磨损后基本不变的尺寸,在同一工步中,在工件上冲出的孔距为L±2/2两个孔时,其凹模型孔心距L d可按下式确定。
L d =L+ —■-8:凸、「•凹一一凸、凹模制造公差,可按IT6〜IT7级来选取,或取、•凸W0.4 ( Z max- Z min ) , '•凹W0.6 ( Z max" Z min )2、单配加工法单配加工法是用凸模和凹模相互单配的方法来保证合理间隙的一种方法。
此方法只需计算基准件(冲孔时为凸模,落料时为凹模)基本尺寸及公差,另一件不需标注尺寸,仅注明“相应尺寸按凸模(或凹模)配做,保证双面间隙在Z max〜Z min之间”即可。
冲压模具设计——第二章

弱区先变形,变形区为弱区
9
第三节 冲压变形理论基础
五、冲压材料及其冲压成形性能
1.冲压成形性能 材料的冲压成形性能:材料对各种冲压加工方法的适应能力。
冲压加工的依据。 成形极限高 材料的冲压性能好 成形质量好 便于冲压加工
成形极限高 冲压成形性能是一个综合性的概念
29
3、间隙对模具寿命的影响
模具寿命分为刃磨寿命和模具总寿命。 失效原因:磨损、变形、崩刃、折断和胀裂。
小间隙将使磨损增加,甚至使模具与材料之间产生粘 结现象,并引起崩刃、凹模胀裂、小凸模折断、凸凹 模相互啃刃等异常损坏。
为了延长模具寿命,在保证冲裁件质量的前提下
1)采用适当或较大的间隙值;
2)减缓间隙不均匀的影响; 3)采用小间隙时必须提高模具硬度与光洁度、精度; 4)改善润滑条件,减少磨损。
3
冲压变形理论基础
一、塑性变形的基本概念
变形:
弹性变形、塑性变形。
塑性:
表示材料塑性变形能力。它是指固体材料在外力作用下发 生永久变形而不破坏其完整性能力。
塑性指标:
衡量金属塑性高低的参数。常用塑性指标为延伸率δ和断
面收缩率ψ。
Lk L0 100 % L0
F0 Fk 100 % F0
成形质量好
10
第三节 冲压变形理论基础
五、冲压材料及其冲压成形性能(续)
2.冲压成形性能的试验方法 间接试验和直接试验
3.板料的机械性能与冲压成形性能的关系
板料的强度指标越高,产生相同变形量的力就越大; 塑性指标越高,成形时所能承受的极限变形量就越大; 刚度指标越高, 成形时抵抗失稳起皱的能力就越大。
c= (DA-dT)/2
冲裁及冲裁模设计
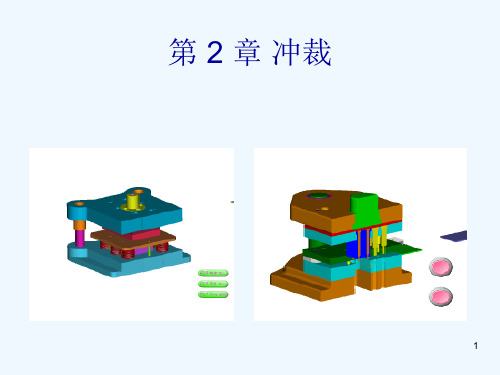
第 2 章 冲裁
2 -2 冲裁模具间隙
2.2.1 间隙对冲裁件质量的影响
冲裁件的质量:断面质量、尺寸精度 a 间隙对断面质量的影响 小间隙、合理间隙、大间隙情况下的剪切过程 断面特征值与间隙的关系图。
17
第 2 章 冲裁
2-2 冲裁模间隙
间隙对断面质量的影响
18
第 2 章 力、变形和冲裁件正常的断面状况 a)冲孔件 b)落料件
第 2 章 冲裁
2 -2 冲裁模具间隙
间隙的概念 模具凸凹模刃口缝隙间的距离。 单边间隙c、双边间隙z。 间隙对冲裁件的质量、模具寿命、冲裁力都有很大 的影响,是冲裁工艺和模具设计中的最重要的工艺参数。 2.2.1 间隙对冲裁件质量的影响 2.2.2 间隙对冲裁力的影响 2.2.3 间隙对模具寿命的影响 2.2.4 间隙的确定
12
第 2 章 冲裁
2-1 冲裁变形机理
2.1.5 断面特征
1)圆角带:冲裁过程中,纤维的弯曲与拉伸形成, 软材料圆角大。 2)光亮带:塑剪变形时,由于相对移动,凸凹模侧 压力将毛料压平形成的光亮垂直断面。
3)断裂带:刃口微裂纹受拉应力不断扩展形成的撕 裂面,导致断面粗糙并有斜度。 4)毛刺:由微裂纹位置与冲裁间隙等引起,是金属 拉断而形成的金属刺残留在冲裁件上
板 坯
F v 1
F v 2
F h 2
F h 2
F v 2
凹 模
板坯受力简图 Diagram of sheet metal under load
10
第 2 章 冲裁
2-1 冲裁变形机理
2.1.3 裂纹的形成与发展 裂纹产生的条件:当变形区的应变达到极限塑性应变值时, 就产生微裂纹 裂纹扩展的方向:沿着最大剪切应变速度的方向扩展 裂纹的成长过程:裂纹首先在低应力区产生,由于变形过 程中最大剪切应变的速度方向发生变化,使得新的裂纹不断产 生,旧裂纹的扩展不断停止,然后在旧裂纹的前端附近重新产 生新的裂纹,不断产生的微裂纹的根部汇成了一条主裂纹 极限塑性应变值除和材质外,还和应力状态、变形历史(损 伤程度)有关。
凸、凹模刃口尺寸计算
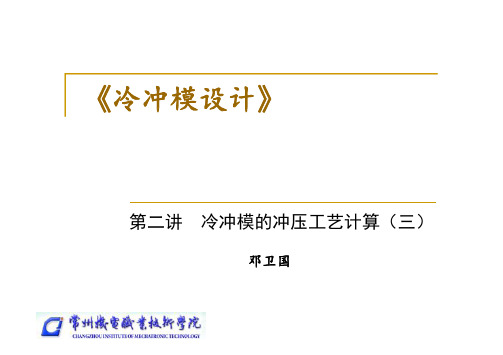
《冷冲模设计》第二讲冷冲模的冲压工艺计算(三)邓卫国第二讲冷冲模的冲压工艺计算(三)第三部分凸、凹模刃口尺寸的确定凹模与凸模的刃口尺寸计算定义:什么叫刃口尺寸:刃口尺寸指在凹模和凸模零件图上分别标注尺寸及公差值,这个值与冲压产品尺寸精度有关。
⏹学习目标☐掌握凸、凹模刃口计算作用☐掌握凸、凹模刃口尺寸计算的依据和原则☐掌握凸、凹模刃口尺寸计算的方法二、冲裁模凸、凹模刃口尺寸的确定1、冲裁模凸、凹模刃口计算的作用冲裁件的尺寸精度主要取决于凸、凹模的刃口部分尺寸。
并且合理的冲裁间隙也靠凸、凹模刃口尺寸保证。
凸模刃口尺寸示意图所以冲裁模刃口设计是冲裁模设计的重点。
凹模刃口尺寸示意图二、冲裁模凸、凹模刃口的确定2、凸、凹模刃口尺寸计算的依据在生产实践中发现:a.由于凸凹模之间存在间隙,冲裁件断面都带有锥度。
依据:①光亮带是冲压件测量和使用部位;②落料件的光亮带,是因凹模刃口挤切材料产生的;③冲孔件的光亮带,是因凸模刃口挤切材料产生的;④落料件的大端(光亮带)尺寸等于凹模尺寸;⑤冲孔件的小端(光亮带)尺寸等于凸模尺寸。
b.凸模轮廓越磨越小,凹模轮廓越磨越大,结果使间隙越用越大。
结论:在计算冲裁模刃口尺寸时,应按落料、冲孔两种情况分别进行计算。
二、冲裁模凸、凹模刃口尺寸确定3、冲裁模凸、凹模刃口计算的原则(一)(1)设计落料模先确定凹模刃口尺寸以凹模为基准,间隙取在凸模上,即冲裁间隙通过减小凸模刃口尺寸来取得;设计冲孔模先确定凸模刃口尺寸以凸模为基准,间隙取在凹模上,冲裁间隙通过增大凹模刃口尺寸来取得。
二、冲裁模凸、凹模刃口尺寸的确定4、冲裁模凸、凹模刃口计算的原则(二)(2)根据冲模在使用过程中的磨损规律:设计落料模时:凹模基本尺寸应取接近或等于零件的最小极限尺寸;设计冲孔模时:凸模基本尺寸则取接近或等于冲件孔的最大极限尺寸。
理由:凸、凹模在磨损到一定程度时,仍能冲出合格的零件。
二、冲裁模凸、凹模刃口尺寸确定5、冲裁模凸、凹模刃口计算的原则(三)(3)凹模和凸模制造公差主要与冲裁件的精度有关①一般冲模精度较零件精度高3~4级;②形状简单的圆形、方形刃口,其制造偏差值可按IT6~IT7级来选取,或查表;③形状复杂的刃口制造偏差可按零件相应部位公差值的1/4来选取;④刃口尺寸磨损后无变化的制造偏差值可取冲件相应部位公差值的l/8并冠(±);⑤若零件没有标注公差,则可按IT14级取值。
冲裁模凸模与凹模刃口尺寸的计算

冲压工艺与模具设计冲裁模凸模与凹模刃口尺寸的计算落料件大端尺寸冲孔件小端尺寸1、 基准件的确定 落料件尺寸由凹模尺寸决定,以凹模为基准,间隙取在凸模上; 冲孔件尺寸由凸模尺寸决定;以凸模为基准, 间隙取在凹模上。
2.3.1 凸模、凹模刃口尺寸计算的依据和原则2、考虑冲模的磨损规律 落料模:凹模基本尺寸应取落料件公差范围的较小尺寸; 冲孔模:凸模基本尺寸应取冲孔件公差范围的较大尺寸。
冲裁间隙采用最小合理间隙值3、制件和冲模刃口尺寸偏差应按“入体”原则标注“入体”原则:向材料实体方向单向标注落料件和凸模上偏差为零,下偏差为负;冲孔件和凹模上偏差为正,下偏差为零。
2.3.2 凸、凹模刃口尺寸的计算方法图 2.3.1冲模的制造公差与冲裁间隙之间关系图 a)落料;b)冲孔 1、凸模与凹模分别加工计算模具刃口尺寸分开加工:是指凸模和凹模分别按图纸标注的尺寸和公差进行加工特点:制造周期短,互换性好,但是间隙受模具制造影响,适合于简单形状的冲压件。
冲模的制造公差与冲裁间隙之间应满足:∣δp∣+ ∣δd∣≤2c max-2c minδp ——凸模下偏差;δd——凹模上偏差。
若:∣δp∣+ ∣δd∣>2c max-2c min取δp = 0.4(2c max-2c min) ;δd = 0.6(2c max-2c min)(1)落料(以凹模为基准,先确定凹模尺寸)落料凹模的尺寸:D d=(D max-xΔ)0+ δd落料凸模的尺寸:D p=(D d- 2c min)0-δp(2)冲孔(以凸模为基准,先确定凸模尺寸)冲孔凸模的尺寸:d p=(d min+ xΔ)0-δp冲孔凹模的尺寸:d d=(d p+2c min)0+ δd(3)凹模型孔中心距:L d=(L min+0.5Δ)±0.125Δ2、凸模和凹模配制加工计算刃口尺寸按尺寸和公差制造出凹模或凸模其中一个(基准件),然后依此为基准再按最小合理间隙配作另一件。
2.3.1-2.3.2工作部分尺寸计算

Z mt
式中:Z——合理冲裁间隙; t——板料厚度; m——记忆系数,参考数据见书。
第2章计算
2.3.2冲裁模工作部分尺寸的计算 冲裁模凸模和凹模工作部分的尺寸直接决 定冲裁件的尺寸和凸—凹模间隙的大小,是冲 裁模上的最重要尺寸。 1.计算的原则 由冲裁过程和生产实践可知:落料件的光 面是因凹模刃口挤切材料产生的,而孔的光面 是凸模刃口挤切材料产生的,落料件的大端尺 寸等于或接近于凹模刃口尺寸,冲孔件的小端 尺寸等于或接近于凸模刃口尺寸。
2.3.1 冲裁间隙的选择(续) 1.间隙对冲裁件断面质量的影响 提高断面质量的主要措施是将模具凹、凸 模之间的间隙控制在合理范围内,并使间隙均 匀分布。同时,对硬质材料,冲裁加工前要进 行退火处理,以提高材料的塑性。 2.间隙对冲裁件精度的影响 冲裁间隙对冲裁件的尺寸精度也有一定影 响。 3.间隙对冲裁力的影响
第2章 冲裁工艺与冲裁模具设计 2.3 冲裁模的工艺计算
2.3.2冲裁模工作部分尺寸的计算(续) (2) 凸模与凹模配作加工 凸、凹模配作加工是指先按图样设计尺寸加 工好凸模或凹模中的一件作为基准件(一般落料 时以凹模为基准件,冲孔时以凸模为基准件), 然后根据基准件的实际尺寸按间隙要求配作另一 件。此方法适合于复杂形状及薄料的冲裁件。
第2章 冲裁工艺与冲裁模具设计
表2-16 磨损系数X
板料厚度 t/mm <1 1~2 2~4 >4 ≤0.16 ≤0.20 ≤0.24 ≤0.30
制件公差Δ/mm
0.17~0.35 0.21~0.41 0.25~0.49 0.31~0.59 非圆形x值
≥0.36 ≥0.42 ≥0.50 ≥0.60
第2章 冲裁工艺与冲裁模具设计
表2-17
第2章 冲裁工艺与冲裁模(用)

2.2 冲裁件尺寸精度及结构工艺性
一、冲裁件尺寸精度和表面粗糙度
1、金属冲裁件的内、外形的经济精度不高于ITll级,如表2-1。 一般落料精度最好低于IT10级,冲孔精度最好低于IT9级。冲裁剪切 面的近似表面粗糙度值件见表2-2。
2、非金属冲裁件的内外形的经济精度为IT14、IT15级。 3、冲裁尺寸标注应符合冲压工艺要求。例如下图2-5所示的冲裁件, 其中图a的尺寸标注方法就不合理,因为,两孔中心距会随模具的磨 损而增大。如改为图b的标注方式,则两孔中心距与模具磨损无关。
⒊ 把握好刃口制造精度与工件精度的关系。 形状简单的刃口制造偏差:按IT6~IT7级; 形状复杂的刃口制造偏差:取冲裁件相应部位公差的1/4; 对刃口尺寸磨损后无变化的制造偏差: 取冲裁件相应部位公差的1/8并冠以(±); 详见表2-8
0 绪论 一、冲压概念
二、刃口尺寸计算方法
根据凸、凹模的加工工艺方法的不同,刃口尺寸的计算方法可分 为两种类型:凸模与凹模分别单独加工、凸模与凹模配合加工。 1. 凸模与凹模分别加工 (如图2-10) 凸模与凹模分别加工是指凸模与凹模分别按各自的图纸加工至最后 的尺寸,凸模、凹模图纸要分别标注凸模、凹模刃口尺寸及公差。
模具寿命受各种因素的综合影响,冲裁间隙是主要影响因素之一。
间隙越小,摩擦越严重,所以过小的冲裁间隙对模具寿命极为不
利。
较大的冲裁间隙可使模具与材料之间的摩擦减小,在一定程度上
还可以减小间隙分布不均匀的不利影响。从而提高模具寿命。
⒊ 冲裁间隙对冲裁工艺力的影响 正常情况下,冲裁间隙对冲裁力的影响不是很大。 冲裁间隙对卸料力、推件力的影响比较显著。间隙增大后,从凸 模上卸下零件和从凹模中推出零件都比较省力。但间隙太大,引起毛 刺增加,反而又使卸料力和推件力迅速增加。
第二章-冲裁工艺与冲裁模具设计PPT课件

都有搭边。材料利用率低,但能保证冲裁件质量,
模具寿命较高。
少废料排样
模具只沿工件部分外形轮廓冲裁,只有局部有
搭边。废料较少,工件质量不高,模具摩损快。
无废料排样
工件间、工件与条料间均没有搭边的存在。模具刃口
沿板料依次切下获取工件。材料利用率高,工件质量差,
模具易损坏。
裁板
纵裁
联合裁
横裁
21
冲压工艺力和压力中心的计算
概 念:
~是冲裁时压力机应具有的最小压力,是完成分离
所必需的力和其它附加力(卸料力、推料力、顶料力)的
总和。它是设计模具、选择压力机的重要依据。
冲裁力的计算
使板料发生分离的力称为冲裁力。一般平刃冲裁模的冲裁
力P可用下式计算:
= KLt
(K-系数,取1.3)
合理冲裁间隙值的确定:
❖ 工件断面质量无严格要求时,应取大间隙值;
❖ 工件的断面质量和制造精度较高时,应取较小间隙值;
❖ 在设计冲模刃口尺寸时,应考虑模具摩损因素,冲裁
间隙应取最小值。
6
方法1:理论确定法
如右图所示,可得冲裁间隙为:
= 2( − ℎ0 )tan = 2(1 − ℎ0 Τ)tan
能与其冲压时定位 基准重合 ,
并选择在冲裁过程中基本上下
不变动的面或线上。
9
凸、凹模刃口尺寸的计算
重要性:
冲模刃口处的尺寸及制造公差直接影响工件的尺寸
精度,合理的冲裁间隙也靠其保证。
前提:
尺寸
计算
的原
则:
因冲裁间隙的存在,落下的料和冲出的孔都带有锥
度,且落料件的大端尺寸与凹模刃口尺寸相近,冲出
- 1、下载文档前请自行甄别文档内容的完整性,平台不提供额外的编辑、内容补充、找答案等附加服务。
- 2、"仅部分预览"的文档,不可在线预览部分如存在完整性等问题,可反馈申请退款(可完整预览的文档不适用该条件!)。
- 3、如文档侵犯您的权益,请联系客服反馈,我们会尽快为您处理(人工客服工作时间:9:00-18:30)。
(2)凹模外形尺寸(外形及紧固孔布置)
1. 外形尺寸
(1) 厚度尺寸
)(=理mm LP H 6225.0
值)修磨量(表=理实h H H 52−+
小型 H 实际=10~25mm
大型 H 实际≤50mm ,时加固理mm H 50>
(2) 长宽尺寸(图2-28)
,,,理理理H W H W H W 0.25.12.1321≥≥≥两形孔之间最小壁厚不得小于5mm 。
注:W1平滑曲线到凹模边界距离,W2直线到凹模边界距离,W3复杂情况或尖端到凹模边界距离。
2. 紧固件(螺钉、圆柱销)尺寸
(1) 直径与配合长度
1)直径d 表2-2,通常取理H 3
1 2)配合长度 通常取d 5.1≥
(2) 位置尺寸
1)孔心-外部边距离,一般可取1.5d
2)孔心-(光滑)孔边距离,一般可取1.5d 。
3)螺孔间距 一般约等于10d
例题一
已知某冲件如图,求凹模结构尺寸
解:求外廓尺寸
1. 冲裁周长L =20+20+20+10π=91.416
2. 冲裁力P =1.3×91.416×1×200=
23768.160(P =1.3lt τ)
3. 厚度H
(取整数进一位)
===理1626.1525.062LP H 考虑刃磨量,据表2-5,刃口厚度h =5,21516==实+H
4. 长宽尺寸
(1) 边宽 W 1=1.2×16=19.2,W 2=1.5×16=24
(2) 压力中心 X 0=0,Y 0=-6.6
(压力中心6.656.64
32144332211−≈−=++++++=
l l l l y l y l y l y l y c ) (3) 长度尺寸
20-6.6+W 2=37.4,10+6.6+W 1=35.8
压力中心定为凹模几何中心,则凹模长度为2×37.4=74.8=75(进一位取整数)
(4) 宽度尺寸
20+2W 2 =68
∴凹模外形尺寸为75×68×21
注:通常凹模板外廓尺寸应按标准选取,可加大取为:
80×80×22
求紧固孔尺寸 料厚=1
抗剪强度
200
16=5.3进一位取6
1. 紧固件直径:由d≈H理/3=3
如内六角螺钉GB70-85 M6×L
圆柱销GB119-86 A6×L A表示过度配合B表示间隙
2. 紧固件长度L 紧固件配合长度L’应大于1.5d
3. 紧固件位置及数量
(1)距边尺寸,取1.5d=9
(2)螺孔间距75-2×9=57
68-2×9=50
(3)销孔位置:销孔边距螺孔中心≥1.5d=9
销孔中心距螺孔中心≥2d=12
销孔中心距57-2×12=33。