精镗C6150机床尾座体Φ75+0.030 0孔夹具课程设计说明书
尾座套筒课程设计说明书
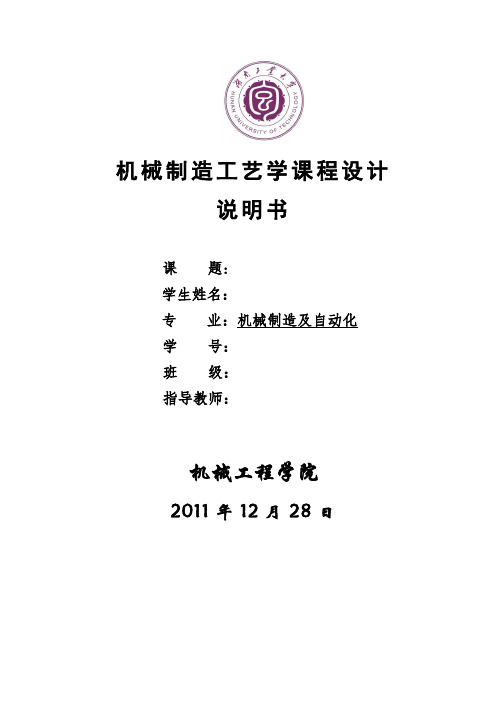
机械制造工艺学课程设计说明书课题:学生姓名:专业:机械制造及自动化学号:班级:指导教师:机械工程学院2011年12月28日车床尾座套筒是车床的主要零件,其结构合理与否、质量的好坏对加工过程、加工精度等有很大的影响,因此,在机床零件设计的过程中为主要考虑对象。
车床尾座在轴类工件的加工、端面钻孔等工序中经常应用,其工作状况好坏对工件加工质量有着较大的影响。
车床尾座的主要作用是为轴类零件定心,同时具有辅助支撑和夹紧的功能。
尾座顶尖的定位精度直接影响机床加工工件的径向尺寸精度,以及圆度、圆柱度、同轴度等形位精度。
而套筒是直接用来装夹顶尖的,由此可见,车床套筒的加工质量将直接影响到机床的工作精度和使用寿命。
所以,研究车床套筒的成形工艺是非常重要的。
此篇课程设计主要内容是对套筒零件的材料选用以及成形方法的研究及设计。
首先,简述了车床套筒的作用与工艺分析,然后对成形工艺作了详细的研究与设计。
这其中包括如何选材及热处理要求,分析了毛坯的制造方案与选用原则,分析了基准面的选取,叙述了切削用量对加工精度的影响以及如何选用。
在此基础上,制定了加工工艺路线与工艺规程设计,进行了各道工序的加工方法,机床、刀具、夹具、辅具、量具的选择,最后编制了机械加工工艺过程卡片与典型的工序卡片。
由于能力所限,经验不足,设计中还有许多不足之处,希望各位老师多加指导。
第一章机械制造工艺学课程设计任务书 (4)第二章零件分析 (5)第三章工艺规程设计 (9)3.1 选择毛坯 (9)3.2 基准的毛坯 (9)3.3 零件加工方法的选择 (10)3.4 确定工艺路线 (11)3.5 工艺分析 (14)第四章工序设计 (16)4.1 确定加工余量、工序尺寸及公差 (16)4.2 工艺装备选择 (19)4.3 确定各工序的切削余量 (23)第五章机械加工工艺过程卡 (35)第六章机械加工工序卡片 (36)第七章收获及心得体会 (37)致谢 (39)参考文献 (40)第一章机械制造工艺学课程设计任务书课程设计题目车床套筒工艺规程设计学院机械工程学院专业机械制造及自动化年级2009级已知参数:1、零件图(见附件)。
夹具设计,车床CA6140后托架课程设计说明书
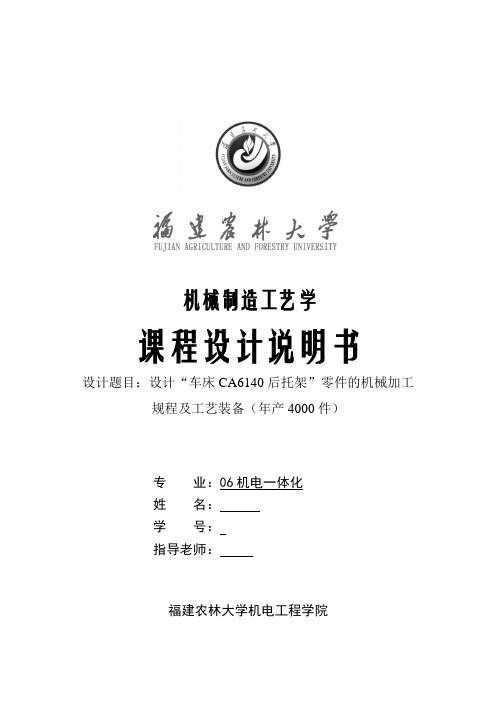
机械制造工艺学课程设计说明书设计题目:设计“车床CA6140后托架”零件的机械加工规程及工艺装备(年产4000件)专业:06机电一体化姓名:学号:指导老师:福建农林大学机电工程学院序言机械制造工艺学课程设计是在我们学完了大学的全部基础课;技术基础课以及大部分专业课之后进行的。
这是我们在进行毕业设计之前对所学课程的一次深入的综合性的总复习。
也是一次理论联系实际的训练,因此,它在我们大学四年生活中占有重要的地位。
由于能力所限,设计尚有许多不足之处,恳请各位老师给与请教。
一.零件的分析(一)零件的作用题目所给的是机床CA6140车床的后托架,是机床的附件,对加工零件超出车身长度的细长杆零件时,用来支撑工件,防止其偏移或松动。
(二)零件的工艺分析由零件图可得后托架主要加工底面,侧面三孔,顶面四孔,以及左视图上的螺纹孔。
⑴.以底面为主要加工的表面,有底面的铣加工,其底面的粗糙度要求是6.1=Ra ,平面度公差要求是0.03。
(2)精加工孔mm 025.0040+φ, mm 02.002.30+φ,mm 03.005.25+φ要求达到的精度等级为8~7IT IT 。
粗糙度为um Ra 6.1=,且以底平面为基准,要求平行度公差为07.0。
⑶.以顶面为住加工面的四个孔,分别是以132φ-和202φ-为一组的阶梯空,这组孔的表面粗糙度要求是50Rz ,3.6=Ra ,以及以132φ-和102φ-的阶梯孔,其中102φ-是装配铰孔,其中132φ-孔的表面粗糙度要求是50Rz ,3.6=Ra ,102φ-是装配铰孔的表面粗糙度的要求是3.6=Ra 。
(4) 其余未注要求的加工表面为不去除材料加工。
二.工艺规程设计(一)确定毛坯的制造形式零件的材料为HT200,由于零件形状规范,可以直接用铸造,属于中批生产。
(二)基面的选择基面选择是工艺规程设计中的重要工作之一。
基面选择得正确与合理,可以使加工质量得到保证,生产率得以提高。
新机构CK6150数控车床使用说明书(通用)
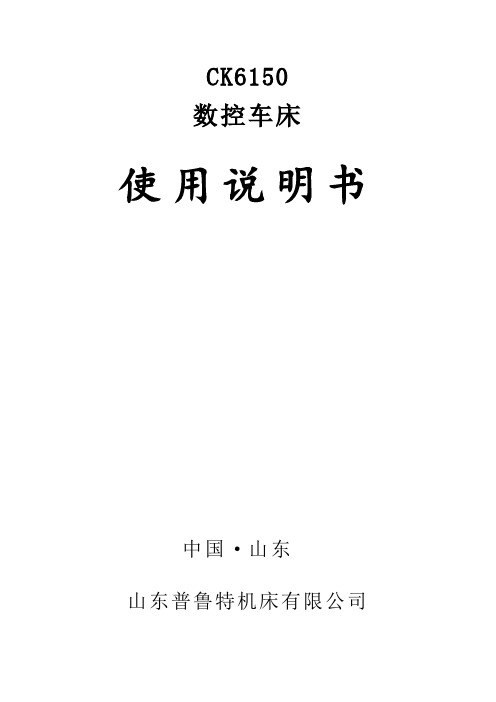
CK6150数控车床使用说明书中国·山东山东普鲁特机床有限公司目录1概述 (1)1.1 产品的主要用途 (1)1.2 机床的精度 (1)1.3 机床的使用环境 (1)1.4 机床对环境的影响 (1)2安全防护须知 (2)2.1 对上机操作、维修人员的要求 (2)2.2 基本操作要求 (2)2.3 接通电源之前的要求 (2)2.4 接通电源之后的要求 (3)2.5 常规检查 (3)2.6 温升 (3)2.7 开机前的准备工作 (4)2.8 工作中注意事项 (4)2.9 中断加工 (5)2.10 完成加工之后 (5)2.11 安全保护装置 (5)2.12 维修前的准备工作 (5)2.13 维修操作 (5)2.14 维修后的处理 (6)3 吊运与安装 (7)3.1 机床的运输与存放 (7)3.2 安装前的准备工作 (7)3.3 机床吊运 (7)3.4 机床安装 (7)3.5 内部装置连接的检查 (8)3.6 操作前的检查 (8)3.7 床身水平的最终调整 (9)3.8 安装后的维护和内部装置连接的检查 (9)5 机床结构 (11)5.1 机床布局 (11)5.2 机床部件简介 (11)6 机床的使用和安全防护 (13)6.1 机床的使用 (13)6.2 安全防护 (13)6.3 设置必要的安全警告标牌 (13)7 检查与维修 (14)7.1 常规检查 (14)7.2 定期检查 (15)7.3 润滑、冷却 (15)7.4 机床的调整和维修 (16)7.5 常见故障排除 (18)8 机床电气概述 (20)8.1 电气设备配置图 (20)8.2 机床电气主要参数 (21)8.3 机床电气的检查 (21)8.4机床送电 (22)8.5 机床电气维护和调整 (22)8.6 电气原理图(附图1) (23)8.7 控制面板接线图(附图2) (24)8.8线路板接线、布局图(附图3) (25)使用须知➢在使用本机床之前,请仔细阅读本《使用说明书》及《车床数控系统产品说明书》,并完全理解说明书全部内容,才能使本机床安全地运转。
机床夹具设计课程设计说明书(铣床或加工中心夹具设计)

摘要夹具制造的主要特点是在机械制造过程中用来固定加工对象,使之占有正确的位置,已接受加工或检测并保证加工要求的机床附加装置,简称为夹具,在我们实际生产夹具的作用是将工件定位,已使加工工件获得相对于机床和刀具的正确位置,并把工件可靠的夹紧。
在现代制造技术迅猛发展的今天,机床夹具无论在传统的机床上还是在数控机床上,加工中心上,仍是必不可少的重要工艺装备。
通过机床夹具设计,不仅可以培养分析运用已学知识的能力,而且可以得到工程设计的初步训练。
首先,对零件进行分析,主要是零件作用的分析和工艺分析,通过零件作用分析可以了解零件的基本情况,而工艺分析可以知道零件的加工表面和加工要求。
根据零件图提出的加工要求,确定毛坯的制造形式和尺寸的确定。
其次,进行基面的选择,确定加工过程中的粗基准和精基准。
根据选好的基准,制订工艺路线,通常制订两种以上的工艺路线,通过工艺方案的比较与分析,再选择可以使零件的几何形状、尺寸精度及位置精度等技术要求得到合理的保证的一种工序。
再次,根据已经选定的工序路线,确定每一步的切削用量及基本工时,并选择合适的机床和刀具。
对于粗加工,还要校核机床功率。
最后,提出设计问题,再选择定位基准,然后开始切削力、夹紧力的计算和定位误差的分析。
然后把设计的过程整理为图纸。
通过以上的概述 整个设计基本完成。
关键词:机械加工工艺、夹具设计、工序、定位目录摘要 (I)1设计任务 (1)2 零件的装夹 (1)2.1零件的工艺和精度分析 (3)2.2 定位设计 (4)2.3对刀引导装置 (6)2.4夹紧方案 (6)2.5 分度对定机构设计 (8)2.6 夹具体设计 (8)3夹具加工精度分析 (9)3.1 定位精度 (9)3.2 对刀精度 (9)3.3安装精度 (10)3.4夹具精度 (10)总结 (11)参考文献 (12)1设计任务1、明确设计任务每个学生按指导教师提供的夹具设计题目自己选题目。
课程设计分组进行,每组2个零件,设计出2种机床夹具;明确生产要求,确定零件的加工工艺,明确加工机床。
最新ca6140车床手柄座说明书及铣槽夹具设计
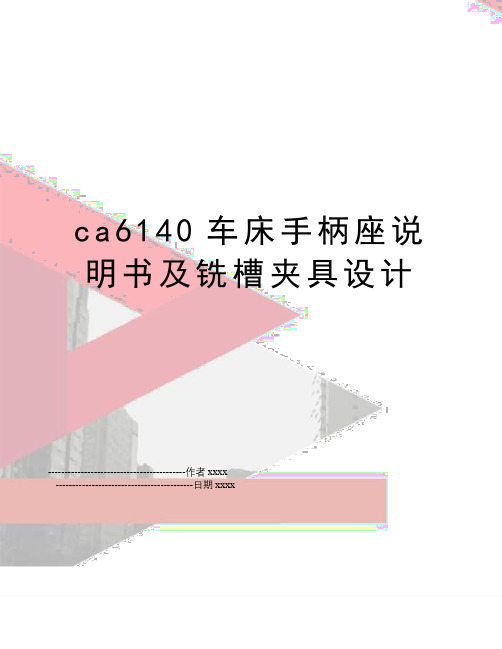
c a6140车床手柄座说明书及铣槽夹具设计------------------------------------------作者xxxx------------------------------------------日期xxxx第1章、零件的分析 01。
1。
零件的功用及结构分析 01.2. 零件的工艺分析 0第2章、手柄座的机械加工工艺规程设计 (2)2.1. 毛坯的选择 (2)2。
2. 基准的选择 (2)(1)粗基准的选择 (2)(2)精基准的选择 (3)2。
3。
工艺路线的拟定 (3)2.4. 加工余量、工序尺寸及毛坯尺寸的确定 (4)2。
5. 切削用量及工时定额的确定 (5)第3章、加工铣槽夹具设计 (17)3.1. 任务的提出 (17)3.2. 定位方案及定位装置的设计计算 (17)3.2。
1. 定位方案的确定 (17)3。
2。
2。
定位元件及装置设计 (17)3。
2。
3. 定位误差的分析计算 (17)3。
3. 对刀或导引元件(装置)设计 (18)3.4. 夹紧方案及装置的设计计算 (19)2 / 263。
4。
1。
夹紧方案的确定 (19)3.4。
2. 夹紧力大小的分析计算 (19)3.4.3. 夹紧机构及装置设计 (20)3。
5。
连接元件及夹具体设计 (20)3.6. 夹具操作及维护简要说明 (20)参考文献 (21)附录Ⅰ机械加工工艺过程卡片 (20)附录Ⅱ机械加工工序卡片 (21)评语 (22)3 / 26第1章、零件的分析1.1.零件的功用及结构分析题目所给的零件是CA6140车床的手柄座。
它位于车床操作机构中,可同时操纵离合器和制动器,即同时控制主轴的开、停、换向和制动.操作过程如下:当手把控制手柄座向上扳动时,车床内部的拉杆往外移,则齿扇向顺时针方向转动,带动齿条轴往右移动,通过拨叉使滑套向右移,压下羊角形摆块的右角,从而使推拉杆向左移动,于是左离合器接合,主轴正转;同理,当手把控制手柄座向下扳动时,推拉杆右移,右离合器接合,主轴反转。
机床夹具设计课程设计说明书(含内容和排版简要说明)
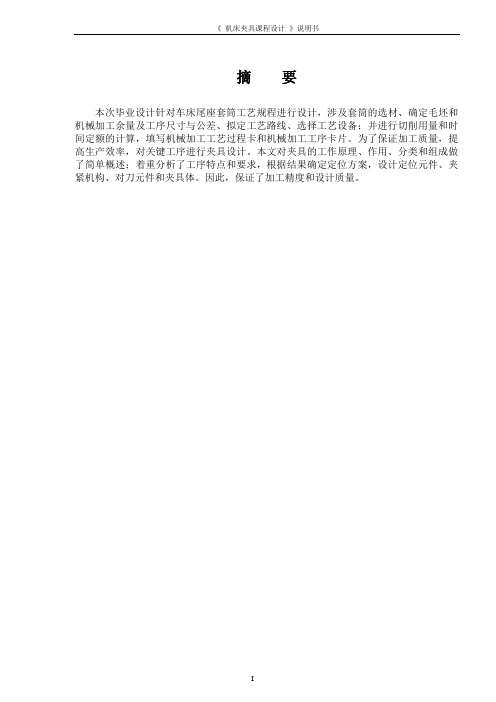
《机床夹具课程设计》说明书摘要本次毕业设计针对车床尾座套筒工艺规程进行设计,涉及套筒的选材、确定毛坯和机械加工余量及工序尺寸与公差、拟定工艺路线、选择工艺设备;并进行切削用量和时间定额的计算,填写机械加工工艺过程卡和机械加工工序卡片。
为了保证加工质量,提高生产效率,对关键工序进行夹具设计。
本文对夹具的工作原理、作用、分类和组成做了简单概述;着重分析了工序特点和要求,根据结果确定定位方案,设计定位元件、夹紧机构、对刀元件和夹具体。
因此,保证了加工精度和设计质量。
目录摘要 (I)1设计任务 (1)2 零件的装夹 (2)2.1零件的工艺和精度分析 (2)2.2 定位设计 (2)2.3对刀引导装置 (3)2.4夹紧方案 (3)2.5 夹具体设计 (4)3夹具加工精度分析 (5)3.1 定位精度 (5)3.2 对刀精度 (5)3.3安装精度 (5)3.4夹具精度 (5)总结 (6)参考文献 (7)1设计任务分析对比综合现有车床尾座套筒加工工艺的基础上,设计出高效的加工工艺规程和夹具设计方案,达到降低成本,提高生产效率的目的。
车床尾座套筒需求量大,所编写的工艺规程主要适用于大量生产的情况使用。
在加工过程中主要有一下问题:(1)车床尾座套筒属于回转件在以内圆为基准加工半精加工和精加工外圆面时装夹固定必须使用夹具实现定心,因此在进行半精加工和精加工前必须分别设计一套夹具;(2)由于套筒是回转件,在铣床上铣键槽时没有夹具无法实现定心和夹紧,所以在铣键槽前也要设计一套夹具;(3)国内车床尾座套筒生产工艺基本成型,要在前人基础上提出一套更加优化的方案也是一个很大的挑战。
图1-1车床尾座套筒零件简图2 零件的装夹2.1零件的工艺和精度分析在选定了车床尾座套筒主要表面的加工方法以后,还需要进一步确定这些加工方法在工艺路线中的安排顺序,这就涉及到加工阶段的划分。
对于精度要求较高的表面,总是先粗加工后精加工,但工艺过程划分成几个阶段是对整个加工过程而言的,不能拘泥于某一表面的加工。
CK6150数控车床液压尾架设计
目录1 绪论 (1)1.1数控机床的产生 (1)1.2数控机床的组成及分类 (2)1.3数控机床的发展趋势 (4)1.4国内研究状况 (5)2 CK6150数控车床液压尾架 (7)2.1尾架的功用 (7)2.2尾架的结构 (7)2.3采用液压尾架的原因 (8)3.1设计任务 (10)3.2负载分析 (10)3.3液压缸参数的确定 (10)3.4液压缸参数的校核 (12)4 数控车床液压尾架的液压泵站设计 (14)4.1拟定液压系统图 (14)4.2液压元、辅件的选择 (17)5 液压系统的性能验算205.1验算回路中的压力损失 (20)5.2验算油液温升 (21)6 PLC控制系统的设计 (22)6.1分析控制对象,确定控制要求 (22)6.2分析控制要求,确定I/O点数 (22)6.3绘制PLC的实际(I/O端子)接线图 (22)6.4设计PLC控制的梯形图 (23)6.5编写PLC控制程序 (24)7 液压系统的维护和常见故障 (25)结束语 (27)致谢 (28)参考文献 (29)1 绪论1.1 数控机床的产生随着社会生产与科学技术的迅速发展,机械产品日趋精密、复杂,改型也日益频繁。
这不仅对机床设备的生产提出了提高精度与效率的要求,也提出了增加通用性与灵活性的要求,特别是宇航、造船、武器生产部门,它们的零件具有精度高、形状复杂、批量较小、经常变动的特点,使用普通车床去加工这类零件,不仅劳动强度大、生产效率低,还难以保证精度,有些零件甚至无法加工。
同时,随着市场竞争的日益加剧,企业生产也迫切需要进一步提高其生产效率,提高产品质量及降低生产成本。
于是一种新型的生产设备——数控机床就应运而生了。
数控机床是在机械制造技术和控制技术的基础上发展起来的,其过程大致如下:1948年,美国帕森斯公司接受美国空军委托,研制直升飞机螺旋桨叶片轮廓检验用样板的加工设备。
由于样板形状复杂多样,精度要求高,一般加工设备难以适应,于是提出采用数字脉冲控制机床的设想。
CA6140车床床身加工工艺及夹具设计说明书.
前言CA6140车床是普通精度级万能车床,它运用加工各种轴类,套筒类和盘类零件上的回转表面,以及车削端面等,是应用最广泛的车床。
CA6140车床床身是机床的基础构件,机床的各个主要部件和零件都装在床身或床身的导轨上作相对运动。
在切削中,刀具与工件的相互作用力传递到床身上而使床身变形床身的变形和振动直影响到被加工零件的精度和表面粗糙度,因此,床身是车床上极为重要的一个部件。
而导轨,则是床身上极为重要的一个部分,床身上共有四条导轨,其中,有两条导轨是拖板用的导轨,另外两条导轨为尾座导轨,其作用为导向和承载,所以,以导轨要求有较高的的导向精度,结构简单,工艺好等特点。
本次的设计主要就是针对加工床身导轨而进行设计的,为了保证导轨的精度,降低工人的劳动强度,床身导轨的加工基准选用导轨本身即“自为基准”原则。
本次设计的主要内容是设计一个调节装置,其作用就是在加工床身时对床身在空间的各个位置进行调节,限于目前的水平有限,希望各位老师给予指正。
第1章零件的分析1.1零件的作用题目所给的零件是CA6140机床床身,它是机床的基础构件。
机床的各个主要部件和零件都装在床身上或在床身导轨上作相对运动。
床身是机床的支承件,装左床腿和右床腿并支承在地基上。
床身上安装着机床的各部件,并保证它们之间具有要求的相互准确位置。
在床身上安装有刀架、尾座、床头箱等零件。
在切削中,刀具与工件相互作用力传递到床身上而床身变形,床身的变形和振动直接影响到被加工零件的精度和表面粗糙度。
因此,床身是机床上极为重要的构件。
1.2 零件的工艺分析该零件主要有四组加工表面,该三组加工表面都要求有较小的表面粗糙度值。
现述如下:1.2.1床鞍与床身的结合面。
该平面是床鞍与床身的结合面,负责纵向进给运动。
所以,要求该平面的表面粗糙度值不得超过1.6,以保证纵向进给的精度。
1.2.2导轨面。
床身上有四条导轨,其中有两条上安装拖板,另两条安装尾架,导轨面是床身的的一个重要表面,刀架负责安装车刀,直接影响到工件的切削精度,尾座可以安装钻头进行钻削等工作,因此,要求导轨面有较小的表面粗糙度值和好的直线度,以保证零件的加工精度。
机床夹具设计课程设计说明书
摘要机床夹具设计课程设计是在全部学完机械制造工艺学及机床夹具设计,并进行了生产实习的基础是进行的一个教学环节.它要求学生全面地综合运用本课程及其有关先修课的理论和实践知识进行工艺及结构的设计,也为以后进行一次预备训练。
此课程设计的目的:(1)能根据被加工零件的技术要求,运用夹具设计的基本原理和方法,学会,拟订夹具设计方案,完成夹具结构设计,初步具备设计出高效、省力、经济合理并能保证加工质量的专用夹具的能力.(2)培养学生熟悉并运用有关手册、标准、图表等技术资料的能力。
(3)进一步培养学生识图、制图、运算和编写技术文件等基本技能。
此次是对一种大批量生产的拨叉类零件进行铣槽。
所设计的夹具必须保证这个通槽的各种尺寸精度,并且以最经济、最省时省力的方法来设计此套夹具。
通过对定位误差的分析,确定出采用大端面小心轴定位,夹紧装置采用螺旋压板夹紧机构。
对于我本人来说,希望能通过本次课程设计学习,学会将所学理论知识和工艺课程实习所得的实践知识结合起来,并应用于解决实际问题之中,从而锻炼自己分析问题和解决问题的能力.关键字:夹具设计、制图、机械目录摘要 (I)1 设计任务 (1)2 零件的定位 (2)2。
1 零件的工艺和精度分析 (2)2。
2 定位设计 (2)2.3 定位元件的选择 (3)3 零件的夹紧装置 (4)3。
1 夹紧方式的选择 (4)3.2 工件拆装 (4)3.3 钻床夹具 (4)3。
4 夹具精度 (5)3。
5 夹具体设计 (5)4对刀导向装置 (6)4。
1 定位误差 (6)4。
2 对刀装置 (6)4.3 对刀精度 (6)4.4 安装精度 (6)4。
5 导向装置 (7)总结 (8)参考文献 (9)1 设计任务对下图零件钻φ11H7的通孔这道工序进行夹具设计图1—1夹具设计零件图能根据被加工零件的技术要求,运用夹具设计的基本原理和方法,学会,拟订夹具设计方案,完成夹具结构设计,初步设计出高效、省力、经济合理并能保证加工质量的专用夹具.2 零件的定位2。
镗床主轴专用夹具说明书(DOC)
中北大学课程设计说明书学生姓名:学号:学院:专业:题目:指导教师:职称:中北大学课程设计任务书2016~2017 学年第一学期学院:专业:学生姓名:学号:课程设计题目:数控镗床主轴起迄日期:12月19 日~12月30 日课程设计地点:中北大学指导教师:学科部副主任:下达任务书日期: 年月日课程设计任务书目录第1章零件分析 (2)1.1 零件的作用 (2)1.2 生产纲领的计算 (2)第2章夹具介绍 (2)2.1夹具概述 (2)2.2机床夹具的功能 (3)第3章铣槽夹具设计 (3)3.1设计要求 (3)3.2夹具设计 (4)3.2.1 定位基准的选择 (4)3.2.2 切削力及夹紧力的计算 (4)3.3定位误差的分析 (5)3.4 定向键与对刀装置设计 (6)3.5 夹具设计及操作的简要说明 (8)3.6 确定夹具体结构尺寸和总体结构 (8)结论 (10)参考文献 (11)第1章零件分析1.1 零件的作用镗床主要是用镗刀在工件上镗孔的机床,通常,镗刀旋转为主运动,镗刀或工件的移动为进给运动。
它的加工精度和表面质量要高于钻床。
镗床是大型箱体零件加工的主要设备。
主要用镗刀对工件已有的预制孔进行镗削的机床。
通常,镗刀旋转为主运动,镗刀或工件的移动为进给运动。
它主要用于加工高精度孔或一次定位完成多个孔的精加工,此外还可以从事与孔精加工有关的其他加工面的加工。
使用不同的刀具和附件还可进行钻削、铣削、切它的加工精度和表面质量要高于钻床。
镗床是大型箱体零件加工的主要设备。
螺纹及加工外圆和端面等。
1.2 生产纲领的计算该产品年产量为6000台,其备品率5%,机械加工废品率1%,现制定该零件的机械加工工艺规程。
年件年件)(6360%1 %511 6000%) %1(=++⨯=++=βαQNN冷却套的年产量为6360件,现已知该产品属于轻型机械,由机械制造工艺设计简明手册表1.1-2生产类型与生产纲领的关系,可确定其生产类型为大批生产。
- 1、下载文档前请自行甄别文档内容的完整性,平台不提供额外的编辑、内容补充、找答案等附加服务。
- 2、"仅部分预览"的文档,不可在线预览部分如存在完整性等问题,可反馈申请退款(可完整预览的文档不适用该条件!)。
- 3、如文档侵犯您的权益,请联系客服反馈,我们会尽快为您处理(人工客服工作时间:9:00-18:30)。
机电及自动化学院《制造工艺学》夹具设计课程设计精镗C6150机床尾座体Φ75+0.030 0孔姓名:学号:0811114011专业:机械电子届别:2008级2011 年12 月23日—2012年01月13日前言尾座体的用途尾座体有以下作用:1.对工件进行正确定位;2.增强加工时工件的强度;3.可以利用尾座进行钻铰内孔以及攻丝套牙。
尾座的组成主要有尾座体、尾座套筒、丝杆、压块等。
机床配件尾座的作用是用于钻孔、铰孔加工中的辅助支撑。
为了保证尾座顶尖套伸缩精度,应保证尾座顶尖套与尾座体之间的配合间隙在合理的范围内.保证顶尖套在尾座体孔内伸缩灵活且不松动。
此外,还要保证顶尖套在伸缩行程范围内其中心线对于床身导轨的平行度要求。
为了保证整个部件的精度,主要零件的性能要求较高。
零件为中批量生产,设计的夹具应适应批量生产。
目录摘要 (1)一、夹具设计任务及要求1.1 机床尾座体的重要技术要求 (1)1.2 精度及批量分析 (1)二、夹具设计方案的确定 (2)2.1 基准面的选择 (2)2.2 定位原理及定位方案的选择及实现 (2)2.3 夹紧方式及元器件的选择 (3)2.4 夹具总装结构 (4)三、定位误差及夹紧分析与计算 (4)3.1 影响加工精度的因素 (4)3.2 保证加工精度 (7)3.3 夹紧方式 (8)3.4 夹紧力的数值计算 (8)3.5 确定夹紧力时应考虑的计算系数 (8)3.6 确定夹紧力 (10)3.7 夹紧点的数目及位置 (12)四、夹具的主要零件结构设计 (13)4.1 立柱的螺纹设计 (13)4.2 定位板定位销校核 (14)五、结束语 (14)参考文献 (15)摘要本设计的内容是设计精镗Φ75+0.030 0mm孔的夹具,零件材料为HT200。
选用的镗刀为方形镗刀,镗刀材料为硬质合金,镗杆的直径为Φ60mm,所用镗刀尺寸为12mm×12mm。
一、夹具设计任务及要求1.机床尾座体的重要技术要求:Φ75+0.030 0mm孔与底面的平行度公差为0.02mm;Φ75+0.030 0mm孔与导轨槽的垂直度公差为0.08mm;Φ75+0.030 0mm孔的圆柱度公差为0.012mm;Φ75+0.030 0mm孔的位置度公差为0.008mm。
2.精度及批量分析(1)本工序有一定位置精度要求,属于批量生产,使用夹具加工是适当的。
(2)考虑到生产批量不是很大,因而夹具结构应尽可能的简单,以减少夹具的制造成本。
尾座体的用途及说明:尾座体有以下作用:1.对工件进行正确定位;2.增强加工时工件的强度;3.可以利用尾座进行钻铰内孔以及攻丝套牙。
尾座的组成主要有尾座体、尾座套筒、丝杆、压块等。
机床配件尾座的作用是用于钻孔、铰孔加工中的辅助支撑。
为了保证尾座顶尖套伸缩精度,应保证尾座顶尖套与尾座体之间的配合间隙在合理的范围内.保证顶尖套在尾座体孔内伸缩灵活且不松动。
此外,还要保证顶尖套在伸缩行程范围内其中心线对于床身导轨的平行度要求。
为了保证整个部件的精度,主要零件的性能要求较高。
二、夹具设计方案的确定2.1.基准面的选择(夹具体方式的确定)夹具体是夹具的基本件,它既要把夹具的各种元件、机构、装置连接成一个整体,而且还要考虑工件装卸的方便。
因此,夹具体的形状和尺寸主要取决于夹具各组成件的分布位置、工件的外形轮廓尺寸以及加工的条件等。
在设计夹具体时应满足以下基本要求。
具有足够的强度和刚度。
结构简单、轻便,在保证强度和刚度前提下结构尽可能简单紧凑,体积小、质量轻和便于工件装卸。
安装稳定牢靠。
结构的工艺性好,便于制造、装配和检验尺寸要稳定且具有一定精度。
清理方便。
达到零件所须的技术要求故本方案的基准面以导轨槽的左侧面及尾座体底面做为基准面2.2 定位原理及定位方案的选择及实现1.工件的定位原理自由物体在空间直角坐标系中有六个自由度,即沿OX,OY,OZ三个轴向的平动自由度和三个绕轴的转动自由度。
要使工件在夹具体中具有准确和确定不变的位置,则必须限制六个自由度。
工件的六个自由度均被限制的定位叫做完全定位;工件被限制的自由度少于六个,但仍然能保证加工要求的定位叫不完全定位。
根据零件的技术要求:定位方案确定为两面一孔定位。
2.定位方案的选择及实现由分析知,零件的定位方案有如下两种:方案一:采用尾座体底面,导轨槽侧面及Φ22mm孔定位方案二:采用尾座体底座,导轨槽侧面及Φ20H7+0.021 0孔定位比较两种定位方案:方案A的夹紧需要用压板夹紧,批量生产时,需频繁的拆卸夹紧装置,增加工时和工人的工作量;方案B的夹紧可用启动装置在Φ22mm 孔内部夹紧,实现自动化夹紧,适应批量生产和减少工人的工作量。
故选用方案B更合理。
2.3.夹紧方式及元器件的选择夹紧机构的三要素是夹紧力方向的确定、夹紧力作用点的确定、夹紧力大笑的确定。
对夹紧机构的基本要求如下:夹紧作用准确,处于夹紧状态时应能保持自锁,保证夹紧定位的安全可靠。
夹紧动作迅速,操作方便省力,夹紧时不应损害零件表面质量夹紧件应具备一定的刚性和强度,夹紧作用力应是可调节的。
结构力求简单,便于制造和维修。
故本方案采用液压夹紧装置。
2.4.夹具总装结构根据被加工零件的结构特征,选择六点定位原理。
夹具体底座的支承块限制3个自由度,导轨槽的定位块限制2个自由度,Φ22mm 孔的菱形销限制1个自由度。
总装图参见附件。
三、定位误差与夹紧分析及计算3.1影响加工精度的因素一批工件依次在夹具中进行定位时,由于工序基准的变动对加工表面尺寸所造成的极限值之差称为定位误差。
产生定位误差的原因是工序基准与定位基准不相重合或工序基准自身在位置上发生偏移或位移所引起的。
用夹具装夹工件进行机械加工时,其工艺系统中影响工件加工精度的因素很多,与夹具有关的因素有:定位误差ΔP 、对刀误差ΔT 、夹具在机床上的安装误差ΔA 和夹具误差ΔE ,在机械加工工艺系统中,影响加工精度的其它因素综合称为加工方法误差ΔG 。
上述各项误差均导致刀具相对工件的位置不精确而形成总的加工误差∑Δ。
a.定位误差ΔD①第一类误差第一类误差是指工件在夹具上定位时所产生的那部分定位误差。
基准不重合误差是由于定位基准和工序基准不重合而产生的那部分定位误差。
在本设计中,由于定位基准和工序基准是重合的,所以基准不重合误差为0。
②第二类误差第二类误差是定位元件对夹具基准面的尺寸误差及位置度所产生的那一部分定位误差。
当支承面与工件底面对夹具的安装基准(底面)有平行度误差及支承面对夹具的对刀基准(镗套轴线)有位置误差,菱形销与定位块安装有误差,被加工孔的定位误差为移动误差: J L L 1'1δ=∆ (3-1)J L L 2'2δ=∆J L L 3'3δ=∆故定位误差为J DW L L L 1'11)(δ=∆=∆ (3-3) J DW L L L 2'22)(δ=∆=∆J DW L L L 3'33)(δ=∆=∆按标注的测量尺寸:0321===J J J L L L δδδ75/030.0=∆=∆=∆γϕφ将上述数值代入定位误差计算公式,则得:mm L DW 010.075/010.0750)(1=⨯+=∆mm L DW 010.075/010.0750)(2=⨯+=∆mm L DW 010.075/010.0750)(3=⨯+=∆b.对刀误差ΔT因为刀具相对于对刀或导向装置不精确造成的加工误差,称为对刀误差。
本工序中镗刀是采用镗套进行导向,镗床镗孔时导向误差计算公式为: lb h d d p me d d K d d K L +-±±-±-±∂±)(221123' (3-4) 即得导向误差016.0=∆T mmc.夹具在机床上的安装误差ΔA因为夹具在机床上的安装不精确而造成的加工误差,称为夹具的安装误差。
一般取:Δ水A =0.2mm Δ垂A=0mm d.夹具误差ΔE因夹具上定位元件,对刀或导向元件及安装基面三者之间(包括导向元件与导向元件之间)的位置不精确而造成的加工误差,称为夹具误差,夹具误差大小取决于夹具零件的加工精度的夹具装配时的调整和修配精度。
一般取ΔE=0.02mme.加工方法误差ΔG因机床精度,刀具精度,刀具与机床的位置精度,工艺系统受力变形和受热变形等因素造成的加工误差,统称为加工方法误差,因该项误差影响因素很多,又不便于计算,所以常根据经验为它留出工件公差的31。
计算时可设ΔG=3k δ。
k δ——工件位置公差取0.008ΔG=mm k002.0008.0313=⨯=δ (3-5)3.2. 保证加工精度工件在夹具中加工时,总加工误差∑Δ为上述各项误差之和。
由于上述误差均为独立随机误差,应用概率法加,因此,保证工件加工精度条件是:22222g e a t p ∆+∆+∆+∆+∆=∆∑ (3-6) 202.0002.002.0016.0010.02.022222=++++= 即工件总加工误差∑Δ应不大于工件的加工尺寸公差,由以上得知,本夹具完全可以保证加工精度。
为保证夹具有一定的使用寿命,防止夹具因磨损而过早报废,在分析计算工件加工精度时需留出一定精度储备量c J ,因此将上式改为:∆∑ ≤k δ-c J → c J =k δ-∆∑ (3-7)当c J ≥0时夹具能满足加工要求,根据以上c J =k δ-∆∑=0.30-0.202=0.098≥0所以夹具完全可以满足加工要求。
3.3 夹紧方式夹紧装置中产生源动力的部分叫做力源装置,常用的力源装置有气动、液压、电动等夹紧装置中直接与工件的被夹压面接触并完成压夹作用的元件称为夹紧元件,本设计采用了液压夹紧,解决了手动夹紧是夹紧力不一致,误差大,精度低,工人劳动强度大等缺点。
由于油液的不可压缩性,能传递较大的压力,一般工作压力可达551065~1050⨯⨯pa,比气压大10多倍,因此,在产生同样作用力的情况下,油缸直径可以小许多倍,使夹具结构更为紧凑。
3.4 夹紧力的数值计算选择夹紧力的作用点和方向应注意:a) 夹紧力应朝向主要限位面;b) 夹紧力的作用点应落在定位元件支承范围内;c) 夹紧力的作用点,应落在工件刚性较好的方向和部位;d) 夹紧力作用点应靠近工件的加工表面;夹紧力大小主要取决于切削力和重力的大小和方向。
夹紧力作用点和方向的选择,通常应与工件定位基准的选择同时考虑,因此这两个参数在制定机床工艺方案时已确定,这里仅作重点叙述的是确定夹紧力的大小的问题。
3.5 确定夹紧力时应考虑的计算系数a.摩擦系数ƒ在许多情况下,并不是由夹具的定位支承机构或夹紧机构本身直接承受工件所受切削力,而是由工件在紧急状态下,工件与定位支承机构及夹紧机构之间所产生的摩擦力来防止工件产生平移或转动,因此在确定夹紧力时,需要考虑各种接触表面之间的摩擦系数。