纺丝工艺参数
静电纺丝评价标准

静电纺丝评价标准全文共四篇示例,供读者参考第一篇示例:静电纺丝技术是一种通过高电压静电场将高分子流体加工成纤维的方法。
它具有快速、高效、省时、易操作的特点,广泛应用于纺织、医疗、生物材料等领域。
由于静电纺丝技术的复杂性,评价其性能的标准也相对复杂。
本文将介绍静电纺丝技术的评价标准,希望能为相关领域的研究人员和工程师提供一些帮助。
一、纤维质量评价标准1. 纤维直径纤维的直径是评价静电纺丝产品质量的一个重要指标。
通常情况下,纤维直径越细,产品的性能越好。
通过测量纤维直径的分布情况,可以评估产品的均匀性和稳定性。
3. 纤维形态纤维的形态包括直线度、曲率等。
直线度越好的纤维产品,其使用性能和品质也就越好。
测量纤维的形态参数可以评估产品的加工性能和使用寿命。
4. 纤维结构纤维的结构包括表面形貌、孔隙率、结晶度等。
这些参数直接影响产品的力学性能、透气性和吸湿性等性能。
评估静电纺丝产品的结构特征是评价其质量的重要依据。
二、工艺参数评价标准1. 电场强度静电纺丝技术是通过高电压静电场将高分子流体加工成纤维的方法,因此电场强度是影响产品性能的一个重要参数。
合适的电场强度可以提高纤维的质量和产量,同时避免产品出现缺陷。
2. 喷丝速度喷丝速度是指高分子流体从喷嘴中喷出的速度。
过高或过低的喷丝速度都会影响纤维的形态和质量。
通过调节喷丝速度,可以获得理想的纤维产品。
3. 收集器距离收集器的距离是指纺丝喷嘴与纤维收集器之间的距离。
调节收集器的距离可以改变纤维的拉伸程度和排列密度,从而影响产品的性能和外观。
4. 加热温度加热温度是指高分子流体在静电场中受热之后的温度。
合适的加热温度可以使得高分子流体更容易被拉伸成纤维,并且有助于改善纤维的结晶度和强度。
三、应用性能评价标准1. 机械性能静电纺丝产品的机械性能包括拉伸强度、弹性模量等参数。
通过测量这些参数,可以评估产品的耐磨性、拉伸性和抗拉断性等性能。
2. 吸湿性能吸湿性能是一种评价纤维产品适用性的重要性能之一。
聚乙烯醇湿法纺丝 天津工业大学

实验参数设计第一纺丝盘纤度的计算由于喷丝头拉伸率应为1030选取20为本实验喷丝头拉伸率喷丝头拉伸率第一纺丝盘线速度喷出速率110002因为第一纺丝盘的线速度12m15s48mmin代入上述公式所以喷丝头速度6mmin因为每分钟喷出量等于供料量所以10000041066081063768rmin所以供料量3768rmin08mlr3014mlmin第一纺丝盘纤度100003014102016481000102dtex拉伸倍数的计算拉伸倍数第一纺丝盘纤度经拉伸后纤度62因为根据实验要求第一导丝盘拉伸一般在室温空气介质中进行拉伸率控制在80以下拉伸倍数18
因为 每分钟喷出量等于供料量 所以 1000*∏*(0.04)2*10-6*6/0.8*10-6=37.68 r/min 所以 供料量=(37.68 r/min)*(0.8ml/r)=30.14ml/min 第一纺丝盘纤度=10000*(30.14*1.02*0.16/4.8*1000)=10.2dtex
52[1].5dtex36f锦纶6POY试纺工艺
![52[1].5dtex36f锦纶6POY试纺工艺](https://img.taocdn.com/s3/m/ddde7d661ed9ad51f01df2ec.png)
! 统计数据#
世界产业用纺织品的最终消费预测
用 途
汽车用 产业用 家庭用 医疗用 建设用 农业用 衣料用 包装用 土木用 体育用 环境用 保护用 合 计
消费量 k t
1995 年
2005 年
1 918 1 523 1 439 1 177
849 741 647 423 251 237
2 483 2 344 2 259 1 652 1 266 1 021
速 0. 35 m s。
表 1 两种产品的纺丝组件压力及喷丝板对比
2 结果与讨论
2. 1 切片质量 由于在纺制多孔细旦锦纶 6 PO Y 时, 应相应提高纺
丝温度, 切片中可萃取物含量偏高时, 会严重影响板面清
规格 毛细孔径 (dtex f) mm
52. 5 12 0. 35 52. 5 36 0. 20
(长沙锦纶厂, 湖南, 410013)
摘 要: 介绍了在进口锦纶高速纺生产线上试纺锦纶 6 多孔细旦 PO Y 的生产工艺, 试生产证明调整和 稳定切片质量, 提高纺丝温度, 适当缩短喷丝板与上油嘴之间的距离, 采用合适的组件装配方式, 降低侧 吹风速度, 提高纺丝上油量等是生产锦纶 6 细旦丝的工艺技术关键。 主题词: 聚己内酰胺纤维 细旦纤维 预取向丝 纺丝
项 目
纤维原料 对苯二甲酸 乙二醇 对苯二甲酸二甲酯 己内酰胺 己二胺 丙烯腈 纤维聚合物 聚酯 聚酰胺 聚乙烯醇 合成纤维 涤纶 腈纶 丙纶
1997 年产量 k t
2 316 1 180
535 235
52 38 270 930 793 12 81 707 377 273 21
b. 严格控制锦纶 6 切片质量, 纺丝温度相应提高 5℃, 采取较低的侧吹风风速, 适当提高上油量, 缩短喷油 嘴与喷丝板之间的距离, 降低卷绕张力, 可以改善 PO Y 质量及卷绕成形。
静电纺丝技术

静电纺丝技术静电纺丝技术是利用高压静电作用使聚合物溶液或熔体带电并发生形变,在喷头末端处形成悬垂的锥状液滴,当液滴表面静电斥力大于其表面张力时,液滴表面就会喷射出高速飞行的射流,并在较短的时间内经电场力拉伸、溶剂挥发、聚合物固化形成纤维。
所获得的静电纺纤维直径小、比表面积大,同时纤维膜还具有孔径小、孔隙率高、孔道连通性好等优势,在过滤、传感、医疗卫生以及自清洁等领域具有广泛的应用。
1静电纺丝的起源与发展静电纺丝起源于200多年前人们对静电雾化过程的研究。
1745年,Bose通过对毛细管末端的水表面施加高电势,发现其表面将会有微细射流喷出,从而形成高度分散的气溶胶,并得出该现象是由液体表面的机械压力与电场力失衡所引起的。
1882年,Rayleigh指出当带电液滴表面的电荷斥力超过其表面张力时,就会在其表面形成微小的射流,并对该现象进行理论分析总结,得到射流形成的临界条件。
1902年,Cooley与Morton申请了第一个利用电荷对不同挥发性液体进行分散的专利。
随后Zeleny研究了毛细管端口处液体在高压静电作用下的分裂现象,通过观察总结出几种不同的射流形成模型,认为当液滴内压力与外界施加压力相等时,液滴将处于不稳定状态。
基于上述的基础研究,1929年,Hagiwara公开了一种以人造蚕丝胶体溶液为原料,通过高压静电制备人造蚕丝的专利。
1934年,Formhals设计了一种利用静电斥力来生产聚合物纤维的装置并申请了专利,该专利首次详细介绍了聚合物在高压电场作用下形成射流的原因,这被认为是静电纺丝技术制备纤维的开端。
从此,静电纺丝技术成为了一种制备超细纤维的有效可行方法。
1966年,Simons发明了一种生产静电纺纤维的装置,获得了具有不同堆积形态的纤维膜。
20世纪60年代,Taylor在研究电场力诱导液滴分裂的过程中发现,随着电压升高,带电液体会在毛细管末端逐渐形成一个半球形状的悬垂液滴,当液滴表面电荷斥力与聚合物溶液表面张力达到平衡时,带电液滴会变成圆锥形;当电荷斥力超过表面张力时,就会从圆锥形聚合物液滴表面喷射出液体射流。
DTY生产工艺及参数设定
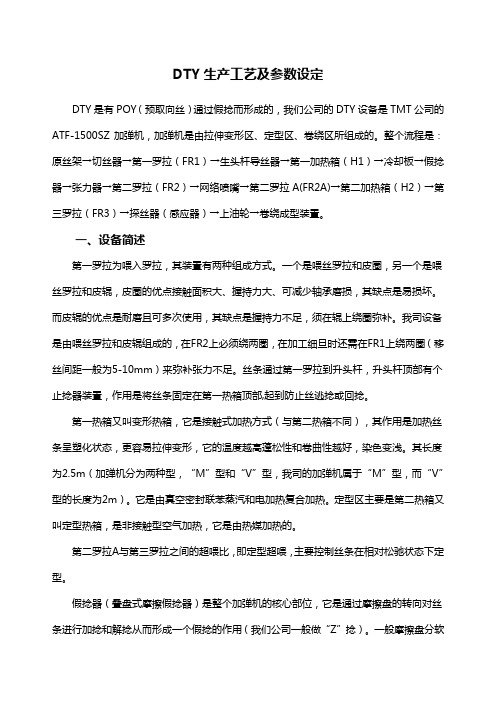
DTY生产工艺及参数设定DTY是有POY(预取向丝)通过假捻而形成的,我们公司的DTY设备是TMT公司的ATF-1500SZ加弹机,加弹机是由拉伸变形区、定型区、卷绕区所组成的。
整个流程是:原丝架→切丝器→第一罗拉(FR1)→生头杆导丝器→第一加热箱(H1)→冷却板→假捻器→张力器→第二罗拉(FR2)→网络喷嘴→第二罗拉A(FR2A)→第二加热箱(H2)→第三罗拉(FR3)→探丝器(感应器)→上油轮→卷绕成型装置。
一、设备简述第一罗拉为喂入罗拉,其装置有两种组成方式。
一个是喂丝罗拉和皮圈,另一个是喂丝罗拉和皮辊,皮圈的优点接触面积大、握持力大、可减少轴承磨损,其缺点是易损坏。
而皮辊的优点是耐磨且可多次使用,其缺点是握持力不足,须在辊上绕圈弥补。
我司设备是由喂丝罗拉和皮辊组成的,在FR2上必须绕两圈,在加工细旦时还需在FR1上绕两圈(移丝间距一般为5-10mm)来弥补张力不足。
丝条通过第一罗拉到升头杆,升头杆顶部有个止捻器装置,作用是将丝条固定在第一热箱顶部,起到防止丝逃捻或回捻。
第一热箱又叫变形热箱,它是接触式加热方式(与第二热箱不同),其作用是加热丝条呈塑化状态,更容易拉伸变形,它的温度越高蓬松性和卷曲性越好,染色变浅。
其长度为2.5m(加弹机分为两种型,“M”型和“V”型,我司的加弹机属于“M”型,而“V”型的长度为2m)。
它是由真空密封联苯蒸汽和电加热复合加热。
定型区主要是第二热箱又叫定型热箱,是非接触型空气加热,它是由热媒加热的。
第二罗拉A与第三罗拉之间的超喂比,即定型超喂,主要控制丝条在相对松驰状态下定型。
假捻器(叠盘式摩擦假捻器)是整个加弹机的核心部位,它是通过摩擦盘的转向对丝条进行加捻和解捻从而形成一个假捻的作用(我们公司一般做“Z”捻)。
一般摩擦盘分软盘(聚氨酯PU盘等)和硬盘(陶瓷盘、砂盘等),软盘摩擦系数高、表面柔软、对丝条损伤小、“雪花少”但使用寿命短成本贵;而硬盘与软盘反之。
化纤公司纺丝部纺丝主要的工艺参数
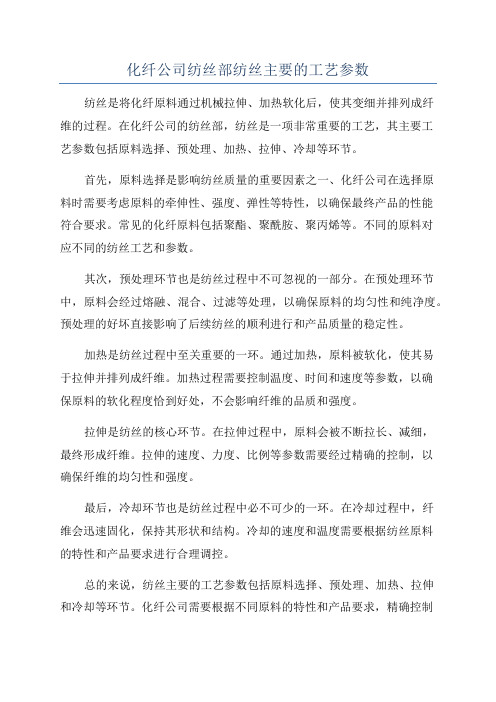
化纤公司纺丝部纺丝主要的工艺参数纺丝是将化纤原料通过机械拉伸、加热软化后,使其变细并排列成纤维的过程。
在化纤公司的纺丝部,纺丝是一项非常重要的工艺,其主要工艺参数包括原料选择、预处理、加热、拉伸、冷却等环节。
首先,原料选择是影响纺丝质量的重要因素之一、化纤公司在选择原料时需要考虑原料的牵伸性、强度、弹性等特性,以确保最终产品的性能符合要求。
常见的化纤原料包括聚酯、聚酰胺、聚丙烯等。
不同的原料对应不同的纺丝工艺和参数。
其次,预处理环节也是纺丝过程中不可忽视的一部分。
在预处理环节中,原料会经过熔融、混合、过滤等处理,以确保原料的均匀性和纯净度。
预处理的好坏直接影响了后续纺丝的顺利进行和产品质量的稳定性。
加热是纺丝过程中至关重要的一环。
通过加热,原料被软化,使其易于拉伸并排列成纤维。
加热过程需要控制温度、时间和速度等参数,以确保原料的软化程度恰到好处,不会影响纤维的品质和强度。
拉伸是纺丝的核心环节。
在拉伸过程中,原料会被不断拉长、减细,最终形成纤维。
拉伸的速度、力度、比例等参数需要经过精确的控制,以确保纤维的均匀性和强度。
最后,冷却环节也是纺丝过程中必不可少的一环。
在冷却过程中,纤维会迅速固化,保持其形状和结构。
冷却的速度和温度需要根据纺丝原料的特性和产品要求进行合理调控。
总的来说,纺丝主要的工艺参数包括原料选择、预处理、加热、拉伸和冷却等环节。
化纤公司需要根据不同原料的特性和产品要求,精确控制这些参数,以确保纺丝过程的顺利进行和产品质量的稳定性。
只有做到这些,才能生产出符合市场需求的高质量化纤产品。
化纤公司纺丝部纺丝主要的工艺参数

化纤公司纺丝部纺丝主要的工艺参数化纤公司的纺丝部是进行化纤纺丝生产的重要部门之一,其主要工艺参数包括纺丝温度、纺丝速度、纺丝压力、纺丝张力、喷丝气压等。
下面将详细介绍这些工艺参数。
首先,纺丝温度是纺丝工艺中的一个关键参数。
纺丝温度的控制能够影响纺丝质量和纺丝速度。
通常情况下,纺丝温度较高可以提高纺丝速度,但过高的温度会引起纤维熔化或起糊化现象,降低纺丝质量。
因此,在确定纺丝温度时需要进行适当的调整和控制。
其次,纺丝速度是指纺丝过程中纤维经过纺丝机头的速度。
纺丝速度对纺丝质量和产量起着重要的影响。
纺丝速度较高时,可以提高生产效率,但也容易产生纤维断裂或其他质量问题。
因此,纺丝速度需要在一定范围内进行调整和控制。
纺丝压力是纺丝过程中纤维在纺丝机头内部受到的压力。
纺丝压力的大小决定了纤维在纺丝机头内部的受力情况,进而影响纤维的拉伸程度和纺丝质量。
通常情况下,纺丝压力较高可以提高纤维的拉伸程度,但过高的压力会导致纤维断裂或其他质量问题。
因此,在确定纺丝压力时需要进行适当的调整和控制。
纺丝张力是指纺丝过程中纤维受到的张力大小。
纺丝张力对纺丝质量和产量也有重要的影响。
纺丝张力较大时,可以提高纤维的拉伸程度,但过大的张力会导致纤维断裂或其他质量问题。
因此,在确定纺丝张力时需要进行适当的调整和控制。
喷丝气压是指喷丝装置通过喷嘴向纺丝机头注入的气体压力。
喷丝气压的大小会影响纤维在纺丝机头内部的流动情况和纺丝质量。
通常情况下,喷丝气压较大可以提高纤维的流动性,但过大的气压会引起纺丝乱流或其他质量问题。
因此,在确定喷丝气压时需要进行适当的调整和控制。
综上所述,化纤公司纺丝部的纺丝主要工艺参数包括纺丝温度、纺丝速度、纺丝压力、纺丝张力、喷丝气压等。
这些参数的合理控制和调整,对于保证化纤纺丝质量和提高生产效率具有重要意义。
芳纶纺丝关键技术
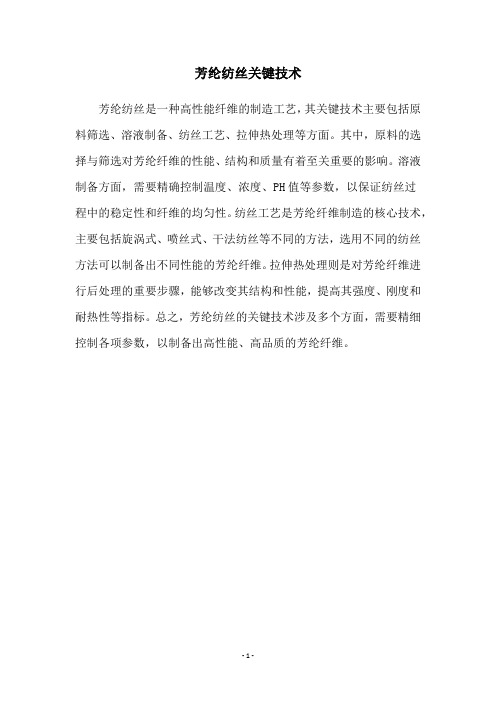
芳纶纺丝关键技术
芳纶纺丝是一种高性能纤维的制造工艺,其关键技术主要包括原料筛选、溶液制备、纺丝工艺、拉伸热处理等方面。
其中,原料的选择与筛选对芳纶纤维的性能、结构和质量有着至关重要的影响。
溶液制备方面,需要精确控制温度、浓度、PH值等参数,以保证纺丝过
程中的稳定性和纤维的均匀性。
纺丝工艺是芳纶纤维制造的核心技术,主要包括旋涡式、喷丝式、干法纺丝等不同的方法,选用不同的纺丝方法可以制备出不同性能的芳纶纤维。
拉伸热处理则是对芳纶纤维进行后处理的重要步骤,能够改变其结构和性能,提高其强度、刚度和耐热性等指标。
总之,芳纶纺丝的关键技术涉及多个方面,需要精细控制各项参数,以制备出高性能、高品质的芳纶纤维。
- 1 -。
- 1、下载文档前请自行甄别文档内容的完整性,平台不提供额外的编辑、内容补充、找答案等附加服务。
- 2、"仅部分预览"的文档,不可在线预览部分如存在完整性等问题,可反馈申请退款(可完整预览的文档不适用该条件!)。
- 3、如文档侵犯您的权益,请联系客服反馈,我们会尽快为您处理(人工客服工作时间:9:00-18:30)。
纺丝工艺参数
1. 1 熔体输送温度
涤纶长丝生产的可纺性要求熔体黏度降越小越好, 所以熔体输送温度不能控制得太高, 太高会形成较大的黏度降, 影响纺丝生产;但纺制超粗旦丝熔体流量较大, 输送温度太低会使熔体输送管内层与外层温度差异增大, 影响熔体输送的流动均匀性, 从而会影响纺丝加工及产品质量。
所以要在保证熔体输送良好的前提下, 尽量降低熔体输送温度, 控制熔体黏度降。
可以通过降低熔体输送管线及热交换器的保温热媒温度来降低熔体输送温度, 达到减小黏度降的目的。
1. 2 纺丝温度
对于超粗旦纤维, 纺丝温度的控制至关重要。
可以通过纺丝温度的调节来有效改变熔体的流变性能, 同时纺丝温度对可纺性影响也较明显。
较高的温度有利于纺丝, 但会增加纺丝的毛丝和断头。
在工艺调试中发现, 在纺丝温度高于287 ℃时, 纺丝飘丝会增加, 铲板困难( 粘板严重) 。
同时组件压力的大小也会影响到熔体的流变性能, 所以纺丝温度要结合组件压力的情况调整。
较高的组件压力可适当降低黏度, 改善熔体的流变性能。
本工艺就是选择较高的组件压力( 17MP a ) 进行生产。
试验证明, 在较高的组件压力下, 纺丝温度控制在284 ℃较为合理。
1. 3 冷却条件和集束点的确定
冷却条件对超粗旦涤纶长丝影响较大, 粗旦纤维要求冷却均匀。
而超粗纤维DP F 较大, 冷却太快会使单丝冷却产生差异, 造成皮芯结构, 染色均匀性变差, 影响产品质量。
超粗旦纤维采用侧吹风冷却, 靠近整流屏的纤维冷却较快,
远离整流屏的纤维冷却较慢, 纤维之间会形成差异。
本工艺在纺丝缓冷区采用弧形板技术, 有效地减少了野风对缓冷区的干扰, 同时使丝层内外冷却更均匀一致。
超粗旦纤维冷却相对较慢, 所以集束点不应靠上, 防止丝条未完全冷却而过早集束, 从而影响纺丝生产及产品质量。
经过试验论证, 集束点选在1 500 mm较为理想。
1. 4 上油
由于纤维总纤度较大, 需要上油量较大, 生产时发现油嘴处会出现滴油、溅油等现象, 同时还发现油嘴发烫, 影响上油的均匀性。
经过查找发现, 在线使用的油嘴宽度较小, 出油孔较小,造成了上述异常。
更换大油嘴( 京瓷、杜塞拉姆等) 进行试验, 解决了难题。
1. 5 合股位置的选择
加工合股丝, 合股位置是关键。
本工艺调试时进行了多次实验, 丝束过了第二导丝盘合股,加工稳定, 毛丝等外观降等少。
但由于是单股网络后合股, 两束丝间抱合不好, 后加工时容易分散, 影响产品质量。
丝束在第一导丝盘前合股时, 会产生少量毛丝等外观异常情况, 但纤维抱合性较好, 能形成较好的预网络, 退绕成功率高。