脱硫工艺流程图
醇胺法脱硫工艺流程图
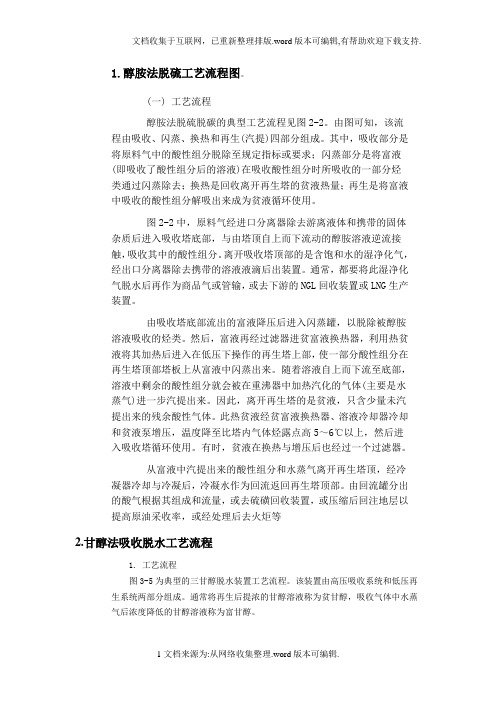
1.醇胺法脱硫工艺流程图。
(一) 工艺流程醇胺法脱硫脱碳的典型工艺流程见图2-2。
由图可知,该流程由吸收、闪蒸、换热和再生(汽提)四部分组成。
其中,吸收部分是将原料气中的酸性组分脱除至规定指标或要求;闪蒸部分是将富液(即吸收了酸性组分后的溶液)在吸收酸性组分时所吸收的一部分烃类通过闪蒸除去;换热是回收离开再生塔的贫液热量;再生是将富液中吸收的酸性组分解吸出来成为贫液循环使用。
图2-2中,原料气经进口分离器除去游离液体和携带的固体杂质后进入吸收塔底部,与由塔顶自上而下流动的醇胺溶液逆流接触,吸收其中的酸性组分。
离开吸收塔顶部的是含饱和水的湿净化气,经出口分离器除去携带的溶液液滴后出装置。
通常,都要将此湿净化气脱水后再作为商品气或管输,或去下游的NGL回收装置或LNG生产装置。
由吸收塔底部流出的富液降压后进入闪蒸罐,以脱除被醇胺溶液吸收的烃类。
然后,富液再经过滤器进贫富液换热器,利用热贫液将其加热后进入在低压下操作的再生塔上部,使一部分酸性组分在再生塔顶部塔板上从富液中闪蒸出来。
随着溶液自上而下流至底部,溶液中剩余的酸性组分就会被在重沸器中加热汽化的气体(主要是水蒸气)进一步汽提出来。
因此,离开再生塔的是贫液,只含少量未汽提出来的残余酸性气体。
此热贫液经贫富液换热器、溶液冷却器冷却和贫液泵增压,温度降至比塔内气体烃露点高5~6℃以上,然后进入吸收塔循环使用。
有时,贫液在换热与增压后也经过一个过滤器。
从富液中汽提出来的酸性组分和水蒸气离开再生塔顶,经冷凝器冷却与冷凝后,冷凝水作为回流返回再生塔顶部。
由回流罐分出的酸气根据其组成和流量,或去硫磺回收装置,或压缩后回注地层以提高原油采收率,或经处理后去火炬等2.甘醇法吸收脱水工艺流程1. 工艺流程图3-5为典型的三甘醇脱水装置工艺流程。
该装置由高压吸收系统和低压再生系统两部分组成。
通常将再生后提浓的甘醇溶液称为贫甘醇,吸收气体中水蒸气后浓度降低的甘醇溶液称为富甘醇。
氨法脱硫工艺流程图

氨法脱硫工艺流程图氨法脱硫是一种常用的烟气脱硫工艺,适用于煤炭、燃油等含硫燃料的燃烧排放中的硫化物的去除。
下面是一个典型的氨法脱硫工艺流程图。
工艺流程图中包括以下几个步骤:1. 烟气净化塔:烟气从锅炉或其他燃烧设备中产生后,进入烟气净化塔。
此处主要是进行粉尘的去除,通过喷洒水雾或其他净化剂,将烟气中的颗粒物捕集下来。
2. 双碱喷射吸收塔:烟气从烟气净化塔底部进入到双碱喷射吸收塔。
在吸收塔内,喷射进入的溶液与烟气进行充分接触,吸收烟气中的二氧化硫。
溶液一般是由氨水和碱液混合而成,主要成分为氨和氢氧化钠。
3. 溶液处理:吸收塔中的溶液会随着烟气中的硫化物被吸收而变得含有高浓度的硫酸盐和亚硫酸盐。
这些溶液需要经过处理进行脱硫产物的分离和再生。
首先是通过过滤和沉淀等方法,将产生的固体脱硫产物分离出来。
然后,将溶液进行再生处理,通常是经过氧化和还原反应,将硫酸盐还原为硫化物,并与新鲜的溶液混合,构成新的脱硫吸收溶液。
4. 脱硫产物处理:通过上述的溶液处理过程,产生的固体脱硫产物需要进行处理。
一般来说,这些产物中含有一定量的硫酸钙和硫酸钠,可以用于制备化肥或者其他产品;同时,可以通过煅烧工艺将其转化为硫酸盐,再继续加工利用。
5. 精制液处理:脱硫产物处理后的精制液,需要进行再次处理,以达到排放标准。
该处理一般包括过滤、吸附和中和等步骤,以置除残留的硫化物、硫酸盐和废液中的酸。
6. 污水处理:氨法脱硫工艺中,产生的废液属于含有某些浓度硫酸盐的废水,需要进行处理。
废水处理工艺一般包括初沉、生化处理、沉淀等步骤,以绞尽脱硫工艺中产生的滞后固体和溶解物质。
以上即为氨法脱硫工艺流程图的主要内容。
这个流程图展示了氨法脱硫工艺的主要步骤,以及每个步骤中的关键处理过程。
通过该工艺,能够有效地去除烟气中的硫化物,达到减少燃煤燃气排放对环境的污染的目的。
各脱硫工艺简介及对比
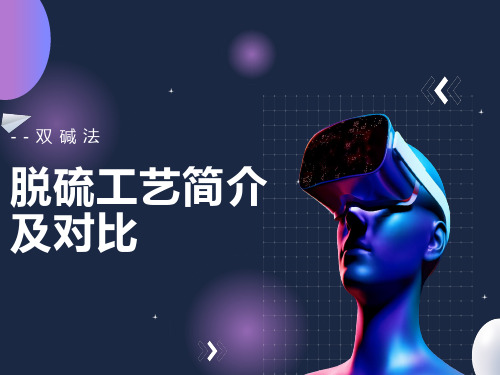
(4)石膏脱水系统
工艺水系统 工艺水系统负责提供FGD足够的水量,补充系统运行期间水的散失,以保证FGD系统的正常功能。工艺水通常采用循环水排水作为水源,一般设置两台工艺水泵(一用一备),一个工艺水箱。 工艺水的主要用水如下: 系统的补充水,主要有:除雾器冲洗水、石灰浆液补充水、泵的循环水等。 不定期对系统的一些管路进行冲洗,水量不定。主要有:循环管路冲洗水、石灰浆液管路冲洗水,石膏排放管路冲洗水、污泥管路冲洗水等。
3、脱硫系统说明
脱硫系统的工艺流程图见下页图。 整套系统由六大部分组成: 烟气系统;(2)SO2吸收系统;(3)吸收剂制备及供给系统;(4)石膏脱水系统;(5)工艺水系统;(6)电控系统。
(1)烟气系统
烟气从锅炉引风机后的烟道上引出,进入吸收塔。在吸收塔内脱硫净化,经除雾器除去水雾,送入锅炉引风机后的总烟道,经然后烟囱排入大气。在烟道上设一段旁路烟道,并设置旁路挡板门,当锅炉启动、进入FGD的烟气超温和FGD装置故障停运时,烟气由旁路挡板经烟囱排放。 烟气系统主要包括FGD进出口烟道,进出口挡板门,旁路挡板门以及与挡板门配套的执行机构。
脱硫工艺简介及对比
--双碱法
一、脱硫工艺
不同脱硫工艺之间的比较 ,具体见下表。
双碱法脱硫工艺介绍
烟气脱硫原理 湿式石灰/石灰石法技术工成熟,脱硫率高,但其主要缺点之一是容易结垢造成吸收系统的堵塞,而双碱法则是先用可溶性的碱性清液作为吸收剂吸收SO2,然后再用电石渣或石灰浆液对吸收液进行再生,由于在吸收和吸收液处理中,使用了两种不同类型的碱,故称为双碱法。双碱法的明显优点是,由于采用液相吸收,从而不存在结垢和浆料堵塞等问题。 针对公司的实际情况,因此本工程选用钠-钙双碱法工艺。
(6)电控系统
石膏法脱硫工艺流程图
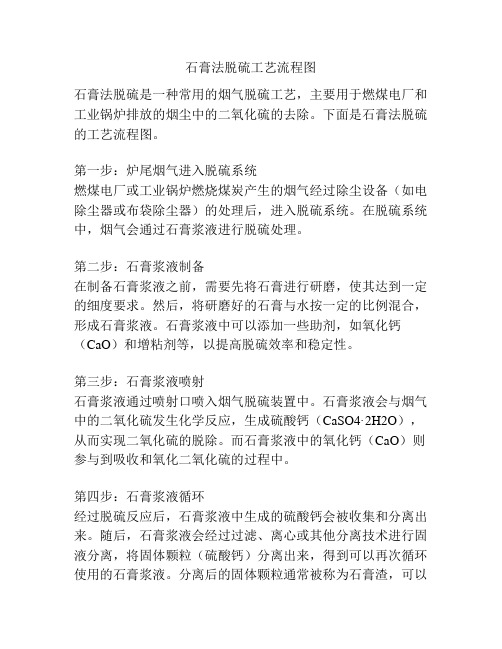
石膏法脱硫工艺流程图石膏法脱硫是一种常用的烟气脱硫工艺,主要用于燃煤电厂和工业锅炉排放的烟尘中的二氧化硫的去除。
下面是石膏法脱硫的工艺流程图。
第一步:炉尾烟气进入脱硫系统燃煤电厂或工业锅炉燃烧煤炭产生的烟气经过除尘设备(如电除尘器或布袋除尘器)的处理后,进入脱硫系统。
在脱硫系统中,烟气会通过石膏浆液进行脱硫处理。
第二步:石膏浆液制备在制备石膏浆液之前,需要先将石膏进行研磨,使其达到一定的细度要求。
然后,将研磨好的石膏与水按一定的比例混合,形成石膏浆液。
石膏浆液中可以添加一些助剂,如氧化钙(CaO)和增粘剂等,以提高脱硫效率和稳定性。
第三步:石膏浆液喷射石膏浆液通过喷射口喷入烟气脱硫装置中。
石膏浆液会与烟气中的二氧化硫发生化学反应,生成硫酸钙(CaSO4·2H2O),从而实现二氧化硫的脱除。
而石膏浆液中的氧化钙(CaO)则参与到吸收和氧化二氧化硫的过程中。
第四步:石膏浆液循环经过脱硫反应后,石膏浆液中生成的硫酸钙会被收集和分离出来。
随后,石膏浆液会经过过滤、离心或其他分离技术进行固液分离,将固体颗粒(硫酸钙)分离出来,得到可以再次循环使用的石膏浆液。
分离后的固体颗粒通常被称为石膏渣,可以用于其他用途,如建材工业等。
第五步:废石膏处理在石膏法脱硫工艺中,除去硫酸钙的石膏浆液中可能还含有其他的杂质和重金属离子。
因此,废石膏需要经过处理才能符合环境保护要求。
常用的处理方法有湿法脱硫石膏综合利用和中间贮存等。
第六步:排放烟气经过脱硫处理后,烟气中的二氧化硫含量已大幅降低。
经过除尘装置的处理,烟气中的颗粒物也被有效地去除,达到了环境排放标准要求。
最后,处理后的烟气可以经过烟囱或烟气处理设施排放到大气中。
以上就是石膏法脱硫的工艺流程图,通过该工艺可以有效地去除燃煤电厂和工业锅炉烟尘中的二氧化硫,降低对环境的污染。
同时,脱硫薄膜的制备方法和脱硫薄膜的应用也在不断进步中,以提高脱硫效率和降低能耗。
石灰石-石膏湿法脱硫技术的工艺流程、反应原理及主要系统
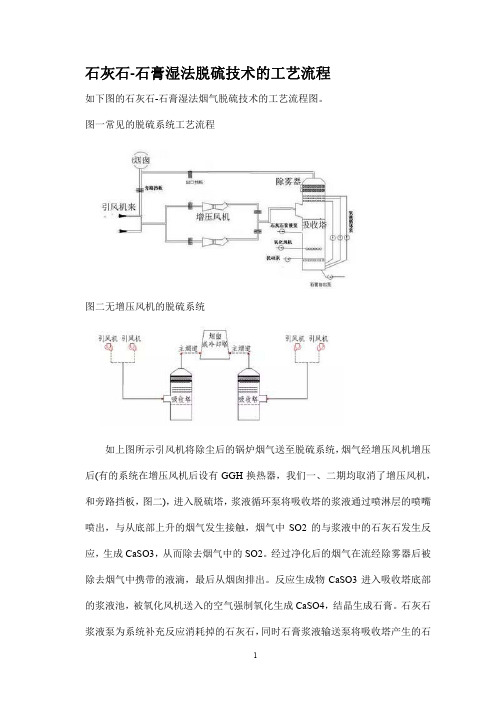
石灰石-石膏湿法脱硫技术的工艺流程如下图的石灰石-石膏湿法烟气脱硫技术的工艺流程图。
图一常见的脱硫系统工艺流程图二无增压风机的脱硫系统如上图所示引风机将除尘后的锅炉烟气送至脱硫系统,烟气经增压风机增压后(有的系统在增压风机后设有GGH换热器,我们一、二期均取消了增压风机,和旁路挡板,图二),进入脱硫塔,浆液循环泵将吸收塔的浆液通过喷淋层的喷嘴喷出,与从底部上升的烟气发生接触,烟气中SO2的与浆液中的石灰石发生反应,生成CaSO3,从而除去烟气中的SO2。
经过净化后的烟气在流经除雾器后被除去烟气中携带的液滴,最后从烟囱排出。
反应生成物CaSO3进入吸收塔底部的浆液池,被氧化风机送入的空气强制氧化生成CaSO4,结晶生成石膏。
石灰石浆液泵为系统补充反应消耗掉的石灰石,同时石膏浆液输送泵将吸收塔产生的石膏外排至石膏脱水系统将石膏脱水或直接抛弃。
同时为了防止吸收塔内浆液沉淀在底部设有浆液搅拌系统,一期采用扰动泵,二期采用搅拌器。
石灰石-石膏湿法脱硫反应原理在烟气脱硫过程中,物理反应和化学反应的过程相对复杂,吸收塔由吸收区、氧化区和结晶区三部分组成,在吸收塔浆池(氧化区和结晶区组成)和吸收区,不同的层存在不同的边界条件,现将最重要的物理和化学过程原理描述如下:(1)SO2溶于液体在吸收区,烟气和液体强烈接触,传质在接触面发生,烟气中的SO2溶解并转化成亚硫酸。
SO2+H2O<===>H2SO3除了SO2外烟气中的其他酸性成份,如HCL和HF也被喷入烟气中的浆液脱除。
装置脱硫效率受如下因素影响,烟气与液体接触程度,液气比、雾滴大小、SO2含量、PH值、在吸收区的相对速度和接触时间。
(2)酸的离解当SO2溶解时,产生亚硫酸,同时根据PH值离解:H2SO3<===>H++HSO3-对低pH值HSO3-<===>H++SO32-对高pH值从烟气中洗涤下来的HCL和HF,也同时离解:HCl<===>H++Cl-F<===>H++F-根据上面反应,在离解过程中,H+离子成为游离态,导致PH值降低。
各种烟气脱硫工艺介绍及其工艺流程图汇总

各种脱硫工艺介绍及其流程图汇总脱硫技术简介通过对国内外脱硫技术以及国内电力行业引进脱硫工艺试点厂情况的分析研究,目前脱硫方法一般可划分为燃烧前脱硫、燃烧中脱硫和燃烧后脱硫等3类。
其中燃烧后脱硫,又称烟气脱硫(Flue gas desulfurization,简称FGD),在FGD技术中,按脱硫剂的种类划分,可分为以下五种方法:以CaCO3(石灰石)为基础的钙法,以MgO为基础的镁法,以Na2SO3为基础的钠法,以NH3为基础的氨法,以有机碱为基础的有机碱法。
世界上普遍使用的商业化技术是钙法,所占比例在90%以上。
按吸收剂及脱硫产物在脱硫过程中的干湿状态又可将脱硫技术分为湿法、干法和半干(半湿)法。
湿法FGD技术是用含有吸收剂的溶液或浆液在湿状态下脱硫和处理脱硫产物,该法具有脱硫反应速度快、设备简单、脱硫效率高等优点,但普遍存在腐蚀严重、运行维护费用高及易造成二次污染等问题。
干法FGD技术的脱硫吸收和产物处理均在干状态下进行,该法具有无污水废酸排出、设备腐蚀程度较轻,烟气在净化过程中无明显降温、净化后烟温高、利于烟囱排气扩散、二次污染少等优点,但存在脱硫效率低,反应速度较慢、设备庞大等问题。
半干法FGD技术是指脱硫剂在干燥状态下脱硫、在湿状态下再生(如水洗活性炭再生流程),或者在湿状态下脱硫、在干状态下处理脱硫产物(如喷雾干燥法)的烟气脱硫技术。
特别是在湿状态下脱硫、在干状态下处理脱硫产物的半干法,以其既有湿法脱硫反应速度快、脱硫效率高的优点,又有干法无污水废酸排出、脱硫后产物易于处理的优势而受到人们广泛的关注。
按脱硫产物的用途,可分为抛弃法和回收法两种。
烧结烟气脱硫工艺海水脱硫技术烟气脱硫-脱硫工艺石灰石石膏湿法烟气脱硫技术氧化镁法烟气脱硫工艺典型双碱法脱硫技术石膏湿法烟气脱硫工艺流程图半干法工艺流程图脱硫脱硝除尘一体化设备半干法脱硫工艺流程带炉内煅烧的烟气循环流化床脱硫技术半干法烟气脱硫系统工艺流程图氢氧化镁浆液制备系统-镁法脱硫工艺流程Ⅳ湿法粗粉脱硫生产流程图石灰石/石灰石膏法烟气脱硫工艺1脱硫工艺流程图烟气脱硫工艺流程石灰石-石膏湿法脱硫工艺流程图循环流化床脱硫技术工艺流程图-工艺流程-双碱法脱硫系统烧结脱硫工程。
脱硫废水处理工艺流程图
脱硫废水处理工艺流程图
脱硫废水处理工艺流程图如下:
首先,脱硫废水处理工艺流程图包含了脱硫废水处理的一系列环节,主要包括药剂投加、反应、沉淀、过滤、浓缩、再利用等步骤。
首先是药剂投加环节。
在该环节,脱硫废水经过储水池后,药剂会被投入到废水中,药剂的种类会根据废水中硫的浓度来选择,一般有氧化剂、还原剂等。
接着是反应环节。
药剂与废水中的硫进行化学反应,形成不溶性的沉淀物。
反应的时间会根据废水中硫的浓度来调节,一般需要几十分钟到几个小时不等。
然后是沉淀环节。
在该环节,反应后的废水会静置,其中的沉淀物会逐渐沉淀下来。
通常会有一个沉淀池来进行沉淀,沉淀时间一般为几十分钟到几个小时不等。
接下来是过滤环节。
通过过滤设备,废水中的沉淀物会被去除掉,得到相对干净的废水。
过滤设备可以是过滤器、压滤机等。
然后是浓缩环节。
通过蒸发或其他浓缩方式,将废水中的水分蒸发掉,使废水浓缩,从而减小体积。
浓缩后的废水可以减少后续处理的成本。
最后是再利用环节。
浓缩后的废水可以进行再利用,例如循环
使用,或者用于其他工艺。
这样可以减少废水的排放,节约水资源。
需要注意的是,脱硫废水处理工艺流程图是一个简化的示意图,实际的处理工艺可能会因废水的性质和工艺要求而略有不同。
在实际应用中,还需要考虑废水的前处理、中间处理和后处理等环节,以及相关的设备和控制系统。
CFB脱硫工艺
表2 4种脱硫工艺的主要经济指标及比较
项 目 CFB WCFB GSA 湿法抛弃 工程总投资/万元 3 500 3 400 3 800 5 802 单位容量投资/元· (kWh)-1 350 340 380 580.2 年运行费用/万元 1 079 1 039 1 098 1 766 寿命期内脱除SO2的成本/元· t-1 714.9 688.4 727.5 1 170.1 脱硫增加电价/元· (kWh)-1 0.008 3 0.008 0 0.008 5 0.014 0 工程总投资或单位容量投资 0.603 0.586 0.655 1 脱除SO2的成本或脱硫增加电价 0.611 0.588 0.622 1
(3) 反应塔布置在锅炉除尘器(指捕集锅炉原烟气 中烟尘的除尘器)和新建的脱硫除尘器之间,并在 反应塔前增加脱硫风机; (4) 反应塔和新建的脱硫除尘器(指捕集脱硫副产 物专用的除尘器)均布置在烟囱之后,并在新建的 脱硫除尘器后增加脱硫风机。 (5) 反应塔和新建的脱硫除尘器均布置在锅炉房 的顶部,并在新建的脱硫除尘器后增加脱硫风机
GSA工艺
GSA工艺特点
GSA工艺的工艺流程见图3。其主要特点是: (1) 吸收剂以石灰浆液的形式从反应塔底部 的中心喷入,属半干法脱硫工艺; (2) 采用高位布置的旋风分离器作为预除尘 器; (3)可在较低的趋近绝热饱和温度(ΔT=3~6 ℃)下运行。
3 CFB工艺原理
目前,烟气循环流化床脱硫工艺已达到工 业化应用的主要有3种工艺流程: (1) 德国LLB公司开发的烟气循环流化床脱硫 工艺,(CFB); (2) 德国Wulff公司的回流式烟气循环流化床 脱硫工艺,(RCFB ); (3) 丹麦F.L.Smith公司研究开发的气体悬浮吸 收烟气脱硫工艺,(GSA)
MDEA天然气脱硫工艺流程
《仪陇天然气脱硫》项目书目录1总论 (3)1.1项目名称、建设单位、企业性质 (3)1.2编制依据 (3)1.3项目背景和项目建设的必要性 (3)1、4设计范围 (5)1、5编制原则 (5)1.6遵循的主要标准、规范 (8)1.7 工艺路线 (8)2 基础数据 (8)2.1原料气和产品 (8)2.2 建设规模 (9)2.3 工艺流程简介 (9)2.3.1醇胺法脱硫原则工艺流程: (9)2.3.2直流法硫磺回收工艺流程: (10)3 脱硫装置 (11)3.1 脱硫工艺方法选择 (11)3.1.1 脱硫的方法 (11)3.1.2醇胺法脱硫的基本原理 (12)3.2 常用醇胺溶液性能比较 (13)3.1.2.1几种方法性质比较 (14)3.2醇胺法脱硫的基本原理 (17)3.3主要工艺设备 (18)3.3.1主要设备作用 (18)3.3.2运行参数 (19)3.3.3操作要点 (20)3.4乙醇胺降解产物的生成及其回收 (21)3.5脱硫的开、停车及正常操作 (22)3.5.1乙醇胺溶液脱硫的开车 (22)3.5.2保证乙醇胺溶液脱硫的正常操作 (22)3.6胺法的一般操作问题 (23)3.6.1胺法存在的一般操作问题 (23)3.6.2操作要点 (24)3.7选择性脱硫工艺的发展 (25)4 节能 (25)4.1装置能耗 (25)装置中主要的能量消耗是在闪蒸罐、换热器和再生塔。
(25)4.2节能措施 (25)5 环境保护 (26)5.1建设地区的环境现状 (26)5.2、主要污染源和污染物 (26)5.3、污染控制 (26)6 物料衡算与热量衡算 (28)6.1天然气的处理量 (28)7.天然气脱硫工艺主要设备的计算 (33)7.1MDEA吸收塔的工艺设计 (33)7.1.1选型 (33)7.1.2塔板数 (33)7.1.3塔径 (34)7.1.4堰及降液管 (36)7.1.5浮阀计算 (37)7.1.6 塔板压降 (37)7.1.7塔附件设计 (39)7.1.8塔体总高度的设计 (40)7.2解吸塔 (41)7.2.1 计算依据 (41)7.2.2塔板数的确定 (41)7.2.3解吸塔的工艺条件及有关物性的计算 (42)7.2.4解吸塔的塔体工艺尺寸计算 (43)8参数校核 (44)8.1浮阀塔的流体力学校核 (44)8.1.1溢流液泛的校核 (44)8.1.2液泛校核 (44)8.1.3液沫夹带校核 (45)8.2塔板负荷性能计算 (45)8.2.1漏液线(气相负荷下限线) (45)8.2.2 过量雾沫夹带线 (45)8.2.3 液相负荷下限 (46)8.2.4 液相负荷上限 (46)8.2.5 液泛线 (46)9 附属设备及主要附件的选型和计算 (47)10.心得体会 (49)11.参考文献 (50)1总论1.1项目名称、建设单位、企业性质项目名称:天然气脱硫建设单位:中石油仪陇净化厂企业性质:国营企业1.2编制依据天然气可分为酸性天然气和洁气。
脱硫工段工艺流程图
脱硫工段工艺流程图
脱硫工段是热电厂燃煤发电过程中的重要环节,其主要目的是减少燃煤产生的二氧化硫排放,保护环境。
下面我将详细介绍脱硫工段的工艺流程图。
首先,燃煤进入燃烧室,与空气进行充分的燃烧反应,产生大量的烟尘和废气。
废气中含有二氧化硫,需要进行脱硫处理。
第一步是氧化反应。
废气经过预处理后,进入净化塔顶部分布的喷头区域,与一定比例的含氧气体进行接触。
氧化剂主要有空气和二氧化氯等,能够将二氧化硫氧化为二氧化硫酸。
第二步是吸收反应。
氧化后的废气经过喷头区域,进入喷雾层。
在喷雾层中,废气与喷雾液体进行接触,喷雾液体是一种含有吸收剂的溶液,一般为石灰石浆液。
在此过程中,二氧化硫与液滴中的吸收剂发生吸收反应,生成硫酸。
第三步是分离反应。
经过吸收的废气与喷头层中的液滴一起下沉,进入喷雾塔的下部,此处设有分离装置。
在分离过程中,废气和液滴发生反向冲刷,液滴中的硫酸被回收下来,而废气中的烟尘和其它颗粒物被截留,净化后的废气从塔顶排放。
第四步是脱水处理。
分离后的液滴中含有大量水分,需要进行脱水处理。
液滴进入脱水装置,通过旋流器等装置将水分与液滴分离,脱水后的液滴进入再生系统。
最后,通过再生系统,将脱水后的液滴进行再利用。
具体的再
生方式受到多种因素的影响,一般采用高温回归的方法,将液滴中的硫酸分解为二氧化硫和水,再经过氧化反应转化为硫酸,用于循环再利用。
以上就是脱硫工段的工艺流程图。
通过该流程,热电厂能够有效地减少燃煤产生的二氧化硫排放,保护环境,同时实现废气中的硫酸回收和再利用。
- 1、下载文档前请自行甄别文档内容的完整性,平台不提供额外的编辑、内容补充、找答案等附加服务。
- 2、"仅部分预览"的文档,不可在线预览部分如存在完整性等问题,可反馈申请退款(可完整预览的文档不适用该条件!)。
- 3、如文档侵犯您的权益,请联系客服反馈,我们会尽快为您处理(人工客服工作时间:9:00-18:30)。
图例:
工艺水 烟气 氧化空气Biblioteka 压缩空气 石灰粉、浆液、滤液水
机组循环水排污水
锅炉
石灰石-石膏湿法烟气脱硫系统工艺流程图
工艺水池
工艺水泵
净烟气
除 雾 器 冲 洗 水
吸 收 塔
事激 故冷 喷烟 淋气
除雾器喷嘴
二级折流式除雾器
喷淋层
单元制喷淋总管
烟气插板门
原烟气
锅炉烟气
除尘器
锅炉引风机
喷嘴
氧化空气 石灰粉罐车来 空压机来压缩空气
滤液水泵
浆液循环泵
悬浮泵 石膏排出泵
M
事 故 浆 液 箱
搅 拌 器
石 膏 旋 流 器
M
真空脱水皮带机
事 故 浆 液 箱
事故浆液返回泵
滤液水
石膏外运
吸收塔地坑搅拌器 M
吸收塔地坑泵
氧化罗茨风机
布袋除尘器
配
CEMS反吹用气
置
浆
石灰粉仓
液
事故喷淋水阀仪用气
螺旋输送机
星型给料机
石灰浆液箱 储气罐
M 石灰浆液箱 搅拌器
滤液水至石灰浆液箱 供浆再循环管线
供浆泵
吸收塔地坑
废水处理系统
滤液水返回塔
废 水 旋 流 气动纠偏 器
汽 水 分 离 器
真空泵 滤液水池搅拌器 M 滤液水池