流化床反应器的设计
流化床反应器的设计概论讲解
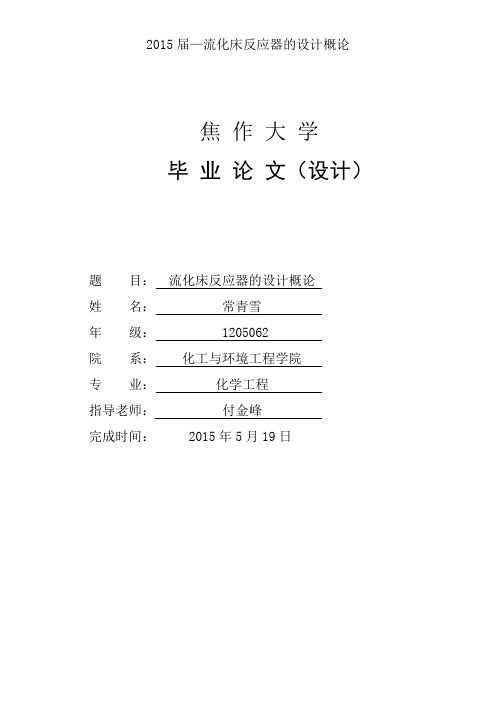
焦作大学毕业论文(设计)题目:流化床反应器的设计概论姓名:常青雪年级: 1205062院系:化工与环境工程学院专业:化学工程指导老师:付金峰完成时间: 2015年5月19日目录第一章概述 (2)1.1 流态化基本概念 (2)1.1.1 概念 (2)1.1.2流态化现象 (4)1.1.3散式流态化和聚式流态化 (5)1.1.4流化态过程中的不正常现象 (7)第二章流化床反应器的结构、参数及其工艺计算 (9)2.1 理想流体的流化床的流化速度 (9)2.1.1临界硫化速度 (9)2.1.2操作流化速度 (9)2.1.2流化床反应器结构 (11)2.2 流化床反应器的床型 (13)3.1 传质概率与传质微分方程 (16)3.1.1 混合物组成的表示方法 (16)3.1.2 传质的通量 (17)3.2质量传递的基本方式 (18)3.2.1 分子传质 (18)3.2流化床的传热 (21)第四章数据处理及结论 (23)4.1数据处理 (23)4.1.1 质量衡算 (23)4.1.2能量衡算 (23)4.2.2流化床反应器的开发与放大 (25)致谢 (30)参考文献 (31)第一章概述流化床反应器比较适用于强烈放热、催化剂易于失活的有机反应过程。
在流化床反应器中工业催化剂除具有良好的活性、产品选择性和稳定性外,还必须满足一定的粒度分布要求并具有良好的硫化性能和耐磨性。
流化床反应器的传质、传热效果好,升温降温时温度分布稳定,催化剂可以连续再生,反应器单位产量大,单位投资抵等优点。
1.1 流态化基本概念1.1.1 概念一般指固体流态化,又称假液化,简称流化,它是利用流动流体的作用,将固体颗粒群悬浮起来,从而使固体颗粒具有某些流体表观特征,利用这种流体与固体间的接触方式实现生产过程的操作,称为流态化技术,属于粉体工程的研究范畴。
流态化技术是一种强化流体(气体或液体)与固体颗粒间相互作用的操作,如在直立的容器内间歇地或连续地加入颗粒状固体物料,控制流体以一定速度由底部通入,使其压力降等于或略大于单位截面上固体颗粒的重量,固体颗粒即呈悬浮状运动而不致被流体带走。
流化床反应器的设计25

精心整理mf U R =1000p d ep ρμ>mf U R =20p d ep ρμ<吨烯烃流化床反应器设计年产3.5万1操作工艺参数反应温度为:450℃ 反应压力为:0.12MPa(绝压) 操作空速为:1~5h -1MTO 成型催化剂选用Sr-SAPO-34 催化剂粒径范围为:30~80μm 催化剂平均粒径为60μm 催化剂颗粒密度为1500kg/m 3 催化剂装填密度为750kg/m 3催化性能:乙烯收率,67.1wt%;丙烯收率,22.4wt%;总收率,89.5wt%。
水醇质量比为0.2甲醇在450℃下的粘度根据常压下气体粘度共线图查得为24.3μPa.s 甲醇450℃下的密度根据理想气体状态方程估算为0.54kg/m 3甲醇处理量:根据催化剂的催化性能总受率为89.5wt%,甲醇的用量=烯烃质量×(32/14)/0.895 烯烃的生产要求是35000t/a ,甲醇的量为89385/a 。
2操作气速2.1最小流化速度计算当流体流过颗粒床层的阻力等于床层颗粒重量时,床层中的颗粒开始流动起来,此时流体的流速称为起始流化速度,记作U mf 起始流化速度仅与流体和颗粒的物性有关,其计算公式如下式所示: 对于的小颗粒()2U 1650p p mf d gρρμ-=(1)对于的大颗粒()1/2d U 24.5p p mfg ρρρ⎡⎤-=⎢⎥⎢⎥⎣⎦(2)式中:d p 为颗粒的平均粒径;ρp ,ρ分别为颗粒和气体的密度;μ为气体的粘度假设颗粒的雷诺数R ep <20,将已知数据代入公式(1), 校核雷诺数:将U mf 带入弗鲁德准数公式作为判断流化形式的依据散式流化, F rmf <0.13;聚式流化,F rmf >0.13。
代入已知数据求得根据判别式可知流化形式为散式流化。
2.2颗粒的带出速度Ut床内流体的速度等于颗粒在流体中的自由沉降速度(即颗粒的重力等于流体对颗粒的曳力)时,颗粒开始从床内带出,此时流体的速度成为颗粒的带出速度U t 其最大气速不能超过床层最小颗粒的带出速度U t ,其计算公式如下式所示:当U R =0.4d p tepρμ<时,2U 18d g p p t ρρμ⎛⎫- ⎪⎝⎭=(3)当U 0.4<R=500d p tepρμ<时,221/34U d225g p t p ρρρμ⎡⎤⎛⎫- ⎪⎢⎥⎝⎭⎢⎥=⎢⎥⎢⎥⎣⎦(4)当U R=500d p tepρμ>时,1/23.1d U g p p t ρρρ⎡⎤⎛⎫- ⎪⎢⎥⎝⎭=⎢⎥⎢⎥⎢⎥⎣⎦(5)流化床正常操作时不希望夹带,床内的最大气速不能超过床层平均粒径颗粒的带出速度U t ,因此用d p =60μm 计算带出速度。
气固流化床反应器的设计与优化
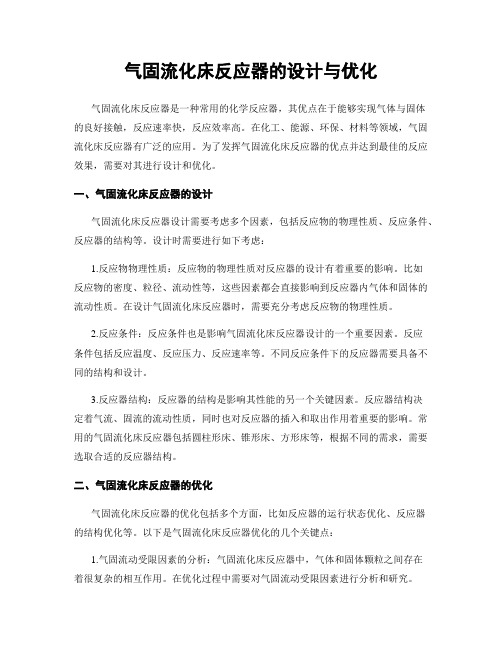
气固流化床反应器的设计与优化气固流化床反应器是一种常用的化学反应器,其优点在于能够实现气体与固体的良好接触,反应速率快,反应效率高。
在化工、能源、环保、材料等领域,气固流化床反应器有广泛的应用。
为了发挥气固流化床反应器的优点并达到最佳的反应效果,需要对其进行设计和优化。
一、气固流化床反应器的设计气固流化床反应器设计需要考虑多个因素,包括反应物的物理性质、反应条件、反应器的结构等。
设计时需要进行如下考虑:1.反应物物理性质:反应物的物理性质对反应器的设计有着重要的影响。
比如反应物的密度、粒径、流动性等,这些因素都会直接影响到反应器内气体和固体的流动性质。
在设计气固流化床反应器时,需要充分考虑反应物的物理性质。
2.反应条件:反应条件也是影响气固流化床反应器设计的一个重要因素。
反应条件包括反应温度、反应压力、反应速率等。
不同反应条件下的反应器需要具备不同的结构和设计。
3.反应器结构:反应器的结构是影响其性能的另一个关键因素。
反应器结构决定着气流、固流的流动性质,同时也对反应器的插入和取出作用着重要的影响。
常用的气固流化床反应器包括圆柱形床、锥形床、方形床等,根据不同的需求,需要选取合适的反应器结构。
二、气固流化床反应器的优化气固流化床反应器的优化包括多个方面,比如反应器的运行状态优化、反应器的结构优化等。
以下是气固流化床反应器优化的几个关键点:1.气固流动受限因素的分析:气固流化床反应器中,气体和固体颗粒之间存在着很复杂的相互作用。
在优化过程中需要对气固流动受限因素进行分析和研究。
2.反应器结构优化:反应器结构是影响其性能的另一个重要因素,选择合适的反应器结构可以优化其性能,加强其固体和气体之间的接触。
例如改变反应器的高宽比,调节反应器锥度等,都可以对反应器的性能进行优化。
3.气固流动数值模拟:使用CFD(计算流体动力学)软件对反应器进行数值模拟,可以帮助了解反应器内的流动性质和固体颗粒的分布情况。
对反应器运行状态进行数值模拟,可以有效地指导优化过程。
化学工程中的反应器设计和流体力学

化学工程中的反应器设计和流体力学在化学工程中,反应器是重要的核心设备之一。
反应器的设计是化学生产工艺优化的关键环节,而流体力学是反应器设计中需要充分考虑的因素之一。
本文将从反应器设计与流体力学的角度,探讨化学工程中反应器的设计与优化过程。
一、反应器设计的基础知识反应器是化学反应的重要设备,它是将化学反应物料转化为所需的化学反应产物的核心设备。
在反应器中,反应物料按照一定比例混合后,根据反应式进行化学反应,最终获得所需的化学产物。
反应器的通用设计需要考虑多个因素,如反应物料的物理和化学性质,反应器的结构设计和设备操作条件,以及反应器的生产能力和可靠性等。
在反应器的设计中,必须深入了解化学反应的各种条件和技术特点,从而准确地计算反应器的生产能力,提高产量和质量。
二、反应器的类型和特点反应器的设计应该根据不同的用途和反应条件选择不同的反应器类型。
常见的反应器包括:均相反应器、搅拌反应器、流动床反应器、固定床反应器和反应器堆等。
不同反应器的特点和适用范围不同,在选择反应器时需要充分考虑化学反应的反应特点和工艺要求。
均相反应器,是指反应物和反应物、反应物和反应物产生反应时处于同种物理状态形成的反应器。
均相反应器包括:罐式反应器、反应蒸气合成器、管式反应器和流化床反应器等。
罐式反应器适用于反应物料型态稳定,反应过程无需搅动的情况。
反应蒸气合成器常用于高压情况下的合成和重要有机合成反应中。
管式反应器常用于液态或气态有机小分子的锁定反应,一般情况下常采用管式管状反应器,尺寸一般较小。
流化床反应器的主要特点是平均流速大,温度较均匀,反应物料分散均匀,应用于液态化学反应和气相催化反应。
搅拌反应器主要应用于液态反应,反应混合好均匀,反应速率增加,反应物料充分接触,反应物料反应活性显著提高。
搅拌反应器中,搅拌器可以将反应物料分散均匀,促进反应物料在反应器中均匀混合,提高反应速率和反应效果。
此种反应器不仅适用于多相反应,还适用于反应物料量较少、反应过程水平度较低的情况。
流化床反应器 设计计算
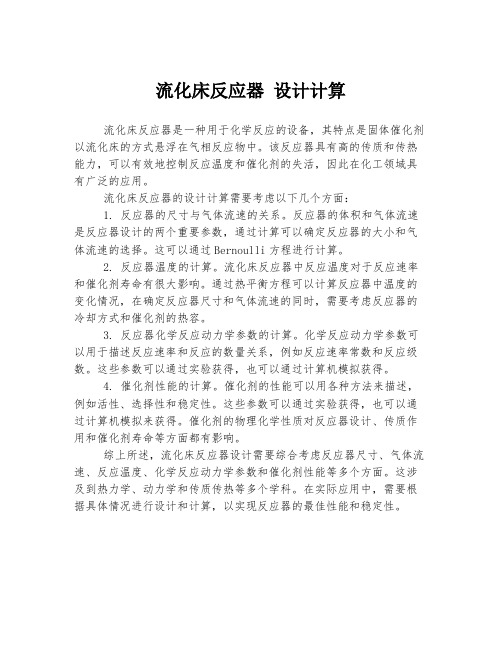
流化床反应器设计计算
流化床反应器是一种用于化学反应的设备,其特点是固体催化剂以流化床的方式悬浮在气相反应物中。
该反应器具有高的传质和传热能力,可以有效地控制反应温度和催化剂的失活,因此在化工领域具有广泛的应用。
流化床反应器的设计计算需要考虑以下几个方面:
1. 反应器的尺寸与气体流速的关系。
反应器的体积和气体流速是反应器设计的两个重要参数,通过计算可以确定反应器的大小和气体流速的选择。
这可以通过Bernoulli方程进行计算。
2. 反应器温度的计算。
流化床反应器中反应温度对于反应速率和催化剂寿命有很大影响。
通过热平衡方程可以计算反应器中温度的变化情况,在确定反应器尺寸和气体流速的同时,需要考虑反应器的冷却方式和催化剂的热容。
3. 反应器化学反应动力学参数的计算。
化学反应动力学参数可以用于描述反应速率和反应的数量关系,例如反应速率常数和反应级数。
这些参数可以通过实验获得,也可以通过计算机模拟获得。
4. 催化剂性能的计算。
催化剂的性能可以用各种方法来描述,例如活性、选择性和稳定性。
这些参数可以通过实验获得,也可以通过计算机模拟来获得。
催化剂的物理化学性质对反应器设计、传质作用和催化剂寿命等方面都有影响。
综上所述,流化床反应器设计需要综合考虑反应器尺寸、气体流速、反应温度、化学反应动力学参数和催化剂性能等多个方面。
这涉及到热力学、动力学和传质传热等多个学科。
在实际应用中,需要根据具体情况进行设计和计算,以实现反应器的最佳性能和稳定性。
流化床反应器的操作与控制—流化床反应器的工艺计算

A组分总消失量 dCAb dt
dl dt
dCAb dl
ub
dCAb dl
流化床反应器内的传热
流化床反应器具有温度分布均匀和传热速率高的特点,特别适于产生大量反 应热的化学反应,同时换热器的传热面积可以减小,结构更紧凑。
传热的三种基本形式:
• 固体颗粒与固体颗粒之间的传热 • 固体颗粒与流体间的传热 • 床层与器壁或换热器表面的传热
这三种传热的基本形式中,前两种传热速度比后一种要大得多,所以要提 高整个流化床的传热速度,关键就在于提高后一种传热速度。
1.844 102 C 1
Re0.23
Pr 0.43
CP P
CP
0.8
P
0.66
0.43
• 注意: 是有单位的,其单位为[s.cm-2]
• 床层与横放的换热器器壁之间传热时,给热系数计
算式为
Nu
0.66 Re0.44
Pr 0.3
P
1
0.44
流化床传热小结
• 水平管的给热系数比垂直管低5-15%,因此倾向 于使用垂直管。
• u:气流的空塔流速[m.s-1]
可见,流化床的内径取决于气流的空塔气速,而流化床的空塔气速应介
于初始流化速度(也称临界流化速度)与逸出速度之间。即维持流化状态的最 低气速与最高气速之间。
例8-1 计算萘氧化制苯酐的微球硅胶钒催化剂的起始流化 速度和逸出速度
已知催化剂粒度分布如下:
目 >1 100 80- 60 40 < 数 20 - 10 - - 4
d p gumf
2
流化床反应器的设计
丙烯腈流化床反应器的设计学院:化工与药学院班级: 2012化学工程与工艺1、2班学生:翟鹏飞肖畅裴一歌徐嘉星廖鹏飞田仪长指导教师: 丽丽完成日期:2015年12月10日指导教师评语:_______________________________________________ ________________________________________________ ________________________________________________成绩:教师签名:目录1 设计生产能力及操作条件 (1)2 操作气速的选择 (1)3 流化床床径的确定 (1)3.1 密相段直径的确定 (1)3.2 稀相段直径的确定 (2)3.3 扩大段直径的确定 (2)4 流化床床高 (2)4.1 流化床的基本结构 (2)4.2 催化剂用量及床高 (3)5 床层的压降 (4)6 选材及筒体的设计 (4)7 封头的设计 (5)8 裙座的选取 (5)9 水压试验及其强度校核 (5)10 旋风分离器的计算 (5)11 主反应器设计结果 (6)丙烯腈流化床反应器的设计1设计生产能力及操作条件反应温度为:440℃反应压力为:1atm丙烯腈氨氧化法催化剂选用:sac-2000催化剂粒径围为:44~88μm催化剂平均粒径为:50μm催化剂平均密度为:1200kg/m3催化剂装填密度为:640kg/m3催化性能:丙烯腈单收>78.0%;乙腈单收<4.0%;氢氰酸单收<7.0% 耐磨强度<4.0wt%接触时间:10s流化床反应器设计处理能力:420.5kmol/h2操作气速的选择流化床的操作气速U0=0.6m/s,为防止副反应的进行,本流化床反应器设计密相和稀相两段,现在分别对其直径进行核算。
3 流化床床径的确定3.1 密相段直径的确定本流化床反应器设计处理能力为420.5kmol/h 原料气体,根据公式:pt n V U V D T 1013.02732734.2240⨯+⨯⨯==πV-气体体积流量,m 3/s U 0-流化床操作气速,m/ss m h m V /83.6/33.246001013.01013.027********.225.42033==⨯+⨯⨯=m U V D T 81.36.014.383.64401=⨯⨯==π 即流化床反应器浓相段的公称直径为DN=3.9m3.2 稀相段直径的确定稀相段直径和密相段直径一样,即D T1=3.81m 即流化床反应器稀相段的公称直径为DN=3.9m3.3扩大段直径的确定在该段反应器中,扩大反应器的体积,可以减缓催化剂结焦,以及抑制副反 应的生产,可采用经验把此段操作气速取为稀相段操作气速的一半。
流化床反应器 设计计算
流化床反应器设计计算
流化床反应器是一种常见的化工反应器,其设计计算对于反应过程的安全和效率具有重要作用。
在流化床反应器的设计计算中,需要考虑反应器的尺寸、流体动力学、传热传质等多个因素,以确保反应器能够满足反应条件和产量要求。
首先,流化床反应器的尺寸设计需要考虑反应物料的特性和反应条件,如反应温度、压力、反应物料的粒度分布等。
根据这些因素,可以选择合适的反应器容积、高度和截面积等参数。
其次,流体动力学是流化床反应器设计计算的重要部分。
流化床反应器中的反应物料通常被气体流体化,形成气固两相流。
在反应过程中,需要控制气体流速、气固两相流的压降和流化床的液化等问题,以确保反应物料的均匀分布和传递效率。
最后,传热传质是流化床反应器设计计算中的另一个关键因素。
在反应过程中,需要通过床层和气体流动实现反应物料的传热传质。
设计合理的流化床反应器结构和操作条件,可以实现反应物料的高效传递和转化。
总之,流化床反应器的设计计算需要综合考虑反应条件、流体动力学和传热传质等多个因素,以实现反应过程的高效、稳定和安全。
- 1 -。
循环流化床催化反应器的设计及应用
循环流化床催化反应器的设计及应用石油、化工、能源等领域需要大量使用催化剂来完成各种反应过程,而催化剂的性质和反应器设计对反应的效率、产品质量、能源利用率等方面有着至关重要的影响。
循环流化床催化反应器是近年来发展起来的一种反应器,具有较高的催化活性、良好的固液、固气分离效果、易于大规模生产等优点,在各种反应过程中得到了广泛应用。
本文将介绍循环流化床催化反应器的设计原理、工艺流程及其应用领域。
一、循环流化床催化反应器的设计原理循环流化床催化反应器是由一个床层和循环管路组成,床层内有固体催化剂颗粒和反应物,反应物在催化剂颗粒上发生反应,产生的物质被带走,床层中的固体催化剂颗粒通过循环管路回到床层中,形成循环的反应过程。
循环床内催化剂颗粒的流动形式通常分为两种:快速流态和扩散流态,具有类似于流体的性质,称为流化床。
循环流化床催化反应器的主要特点是采用了循环流化床技术,可实现高效的催化反应,相较于传统催化反应器具有更高的传质速率、更高的反应速率、更高的容积效率、更好的固液分离效果等优点。
循环流化床催化反应器的设计原理基于以下三点:一、气固两相流动性能好,能大大提高传质速度、反应速度;二、催化剂颗粒稳定悬浮于流态床层内,具备良好的固液分离性能;三、在反应转化率逐渐上升的情况下,床内流体总体压降呈现下降趋势,从而能提高床层容积利用率。
二、循环流化床催化反应器的工艺流程循环流化床催化反应器的工艺流程一般分为预处理、进料、反应和产物处理四个部分。
首先是预处理,包括催化剂的活化、干燥、筛分等,催化剂的品质直接影响反应器的效果。
其次是进料,反应前要将气体、液体和固体物料进行混合,由气体或液体泵泵入床层,在床层底部设置多个喷嘴形成均匀的气流,使催化剂颗粒悬浮于流态床层内,形成循环流动。
进一步是反应,催化剂表面通过高速传质实现了吸附、反应和解吸三个基本过程,产生的物质通过流态床固液分离器分离,颗粒状态的催化剂流回反应器床层内循环利用,形成了床内催化反应循环过程。
第六章 流化床反应器
当: Rep 2 10 时 CD 0.43 500
5
这样,可得到ut计算式:
当Rep 0.4时 ut
2 gd p ( s f )
18
0.5 ep
2d p ( s f ) gR 当0.4 Rep 500时 ut 15 f
流化床反应器的缺点
由于流态化技术的固有特性以及流化过程影响因素的 多样性,对于反应器来说,流化床又存在粉明显的局限性: ①由于固体颗粒和气泡在连续流动过程中的剧烈循环和搅动, 无论气相或固相都存在着相当广的停留时间分布,物料的 流动更接近于理想混合流,返混较严重。导致不适当的产 品分布,降低了目的产物的收率;为了限制返混,常采用 多层流化床或在床内设置内部构件。反应器体积比固定床 反应器大,并且结构复杂。对设备精度要求较高; ②反应物以气泡形式通过床层,减少了气-固相之间的接触机 会,降低了反应转化率; ③由于固体催化剂在流动过程中的剧烈撞击和摩擦,使催化 剂加速粉化,加上床层顶部气泡的爆裂和高速运动、大量 细粒催化剂的带出,造成明显的催化剂流失; ④床层内的复杂流体力学、传递现象,使过程处于非定常条 件下,难以揭示其统一的规律,也难以脱离经验放大、经 验操作。
式中:Lmf—临界流化床高;εmf—临界流化床的空隙率;
ρp和ρg—分别为颗粒及流体的密度
二、特征流速
1、临界流化速度 也称起始流化速度、最低流化速度, 是指刚刚能够使颗粒流化起来的气体空床流速(也叫表观速 度)。也即颗粒层由固定床转为流化床时流体的气体空床流 速,用umf表示。实际操作速度常取临界流化速度的倍数(又 称流化数)来表示。临界流化速度对流化床的研究、计算与 操作都是一个重要参数,确定其大小是很有必要的。确定临 界流化速度最好是用实验测定,也可用经验公式计算。
- 1、下载文档前请自行甄别文档内容的完整性,平台不提供额外的编辑、内容补充、找答案等附加服务。
- 2、"仅部分预览"的文档,不可在线预览部分如存在完整性等问题,可反馈申请退款(可完整预览的文档不适用该条件!)。
- 3、如文档侵犯您的权益,请联系客服反馈,我们会尽快为您处理(人工客服工作时间:9:00-18:30)。
mf U R =
1000
p d ep ρ
μ
> 年产3.5
万吨烯烃流化床反应器设计
1 操
作工艺参数
反应温度为:450℃ 反应压力为:0.12MPa(绝压) 操作空速为:1~5h -1
MTO 成型催化剂选用Sr-SAPO-34 催化剂粒径范围为:30~80μm 催化剂平均粒径为60μm 催化剂颗粒密度为1500kg/m 3 催化剂装填密度为 750kg/m 3
催化性能:乙烯收率,67.1wt%;丙烯收率,22.4wt%;总收率,89.5wt%。
水醇质量比为0.2
甲醇在450℃下的粘度根据常压下气体粘度共线图查得为24.3μPa.s 甲醇450℃下的密度根据理想气体状态方程估算为0.54kg/m 3
甲醇处理量:根据催化剂的催化性能总受率为89.5wt%,甲醇的用量=烯烃质量×(32/14)/0.895
烯烃的生产要求是35000t/a ,甲醇的量为89385/a 。
2 操作气速
2.1 最小流化速度计算
当流体流过颗粒床层的阻力等于床层颗粒重量时,床层中的颗粒开始流动起来,此时流体的流速称为起始流化速度,记作U mf 起始流化速度仅与流体和颗粒的物性有关,
mf U R =20p d ep ρμ<其计算公式如下式所示:
对于的小颗粒
()2
U 1650p p mf d g
ρρμ
-=
(1)
对于的大颗粒
()1/2
d U 24.5p p mf
g ρρρ⎡⎤-=⎢⎥
⎢⎥⎣⎦ (2)
式中:d p 为颗粒的平均粒径;ρp ,ρ分别为颗粒和气体的密度;μ为气体的粘度假设颗粒的雷诺数R ep <20,将已知数据代入公式(1), 校核雷诺数:
将U mf 带入弗鲁德准数公式作为判断流化形式的依据散式流化, F rmf <0.13;聚式流化,F rmf >0.13。
代入已知数据求得
根据判别式可知流化形式为散式流化。
2.2 颗粒的带出速度Ut
床内流体的速度等于颗粒在流体中的自由沉降速度(即颗粒的重力等于流体对颗粒的曳力)时,颗粒开始从床内带出,此时流体的速度成为颗粒的带出速度U t 其最大气速不能超过床层最小颗粒的带出速度U t ,其计算公式如下式所示:
当U R =
0.4
d p t
ep
ρ
μ
<时,
2U 18d g p p t ρρμ⎛⎫- ⎪⎝⎭= (3)
当
U 0.4<R
=500
d p t
ep ρμ
<时,
2
21/34U d
225g p t p ρρρμ⎡⎤⎛⎫- ⎪⎢⎥
⎝⎭⎢⎥=⎢⎥⎢⎥⎣⎦ (4)
当
U R =500
d p t
ep ρ
μ
>时,
1/2
3.1d U g p p t ρρρ⎡⎤⎛⎫- ⎪⎢⎥⎝⎭=⎢⎥⎢⎥⎢⎥⎣⎦ (5)
流化床正常操作时不希望夹带,床内的最大气速不能超过床层平均粒径颗粒的带出速度U t ,因此用d p =60μm 计算带出速度。
代入已知数据求得 校核雷诺数:
R ep =0.532(0.4 <R ep <500)
2.3 流化床操作气速
如上所述,已知颗粒的临界流化速度U mf 和催化剂的小颗粒的带出U t ,对于采用高流化速度,其流化数(流化数=气体表观速度/临界流化速度)可以选着300-1000,本装置设计使用流化数为1000,带入计算 故本装置的操作气速为1.3m/s
为防止副反应的进行,本流化床反应器设计密相和稀相两段,现在分别对其直径进行核算。
3 床径的确定 3.1 密相段直径确定
本流化床反应器设计处理能力为13.4t/h 。
体积流量为24829.3m 3/h 甲醇气体,即6.9m 3/s 。
根据公式
T D (6) 即流化床反应器密相段的公称直径为DN=2.6m
3.2 稀相段直径的确定
在该段反应器中,扩大反应器的体积,可以减缓催化剂结焦,以及抑制副反应的生产,本厂设计稀相段流化数为700,计算过程如下: 将流速带入公式(6)中
即流化床反应器稀相段的公称直径为DN=3.1m
4流化床床高
床高分为三个部分,即反应段,扩大段,以及锥形段高度。
甲醇处理量为M=13.4t/h
取质量空速为2h -1,则催化剂的量为6.7吨。
由催化剂的装填密度为750kg/m 3,所以静床高度的确定
2
2
4
67004
1.7750 3.14
2.6mf T m H m
D ρπ⋅⨯=
=
=⨯⨯催化剂,
考虑到床层内部的内部构件,取静床层高度为2.0m 。
流化时的流化比取2,因此床层高度H 1=2H mf =3.4m 。
扩大段高度取扩大段直径的三分之一,H 2=1.1m 。
反应段与扩大段之间的过渡部分过度角为120°,由三角函数,过渡段高度 锥形段取锥底角为40°,取锥高为H 4=1.2m ,其锥底直径为1.5m 。
由此可得,流化床总高H=H 1+H 2+H 3+H 4=5.92m 其长径比为5.92/2.6=2.3。
5床层的压降
流化床在正常操作时具有恒定的压降,其压降计算公式为
6流化床壁厚
流化床反应器的操作温度为450摄氏度,操作压力为0.12Mpa ,设计温度为500摄氏度,设计压力为0.2Mpa ,由于温度较高,因此选择0Cr18Ni9材料,该种材料在设计温度下的许用应力为100Mpa ,流化床体采用双面对接焊,局部无损探伤,取流化床体焊接接头系数为φ=0.85,壁厚的附加量取c=2mm 。
流化床壁厚:
考虑到流化床较高,风载荷有一定影响,取反应器的设计壁厚为6mm , 流化床体的有效厚度为t e =t n -c 1-c 2=3.4mm 。
筒体的应力按下式进行计算
()()
0.22600 3.476.5722 3.4e t e p D t Mpa t σ+⨯+=
==⨯。
许用应力[σ]t φ=100x0.85=85Mpa>76.57Mpa,应力校核合格。
对于扩大段,
[]d 0.23100
t =
2 5.721000.850.2
2i t
pD c mm
p
σφ⨯+=
+=⨯⨯--
考虑到扩大段,过渡段压力略有减小,并且扩大段温度较低,因此均选取扩 大段、过渡段壁厚为6mm 。
锥形段阶段为反应气体的预分布阶段,未发生反应,温度较低直径较小,因 此壁厚更小,但为考虑选材与安装的方便性,其壁厚也选取为6mm 。
6椭圆封头
由于反应器压力较低,封头承压不大,故选用应用最为广泛的椭圆形封头, 设计压力为0.15Mpa ,设计温度为500摄氏度,腐蚀裕量为2mm ,封头焊缝系 数为0.85。
封头高度取1m 。
选择材料为0Cr18Ni9材料,在设计温度下,其许用应力为100Mpa 。
形状系数为K=1.0
封头厚度按下式进行计算
考虑到便于焊接,故选取封头厚度为6mm。
7裙座
裙座的厚度按经验选取为20mm,,高度为1m。
8水压试验及其强度校核
水压试验的试验压力有p T=p+0.1=0.3Mpa, p T=1.25p=0.25Mpa,取两者中大
值,即pt=0.3Mpa。
水压试验时壁内应力
已知0Cr18Ni9材料在常温下的屈服强度为σs=137Mpa,计算
0.9σs=123.3Mpa
可以知道水压试验时筒体壁内应力小于0.9σs,水压试验安全。
9旋风分离器
在流化床顶部,为防止小粒径催化剂颗粒随气体被带出,故在流化床扩大
段设立二级旋风分离器,根据旋风分离器的规格,选用CLG型旋风分离器,其中一级旋风分离器的直径为640mm,二级旋风分离器的直径为540mm。
旋风分离器的布置和结构:一级旋风分离器的料腿下伸到床底部,下料腿
端部安装锥形堵头,使催化剂能够随自下而上的气流进入下料管内。
二级旋风分离器下料腿置入床层稀相区,下料腿端部安装挡风帽和翼阀。
10 主反应器设计结果
主反应器最终设计结果如下:
表4-1 主反应器R101设计表。