新能源汽车动力电池激光清洗与焊接工艺研究应用
论激光焊接技术在新能源电池领域中的应用前景及存在的问题研究
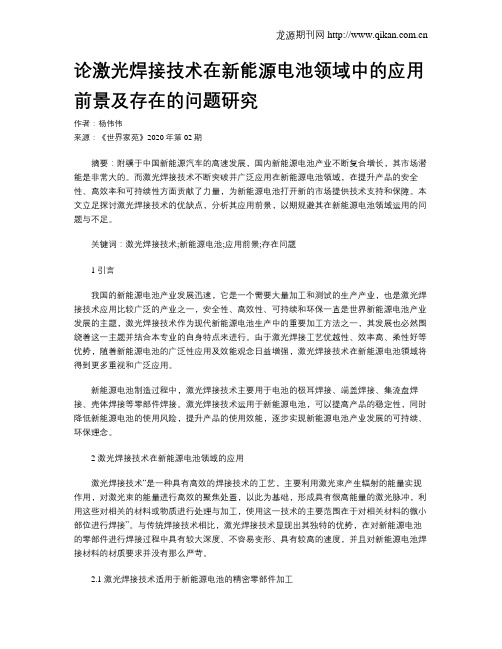
论激光焊接技术在新能源电池领域中的应用前景及存在的问题研究作者:杨伟伟来源:《世界家苑》2020年第02期摘要:附骥于中国新能源汽车的高速发展,国内新能源电池产业不断复合增长,其市场潜能是非常大的。
而激光焊接技术不断突破并广泛应用在新能源电池领域,在提升产品的安全性、高效率和可持续性方面贡献了力量,为新能源电池打开新的市场提供技术支持和保障。
本文立足探讨激光焊接技术的优缺点,分析其应用前景,以期规避其在新能源电池领域运用的问题与不足。
关键词:激光焊接技术;新能源电池;应用前景;存在问题1 引言我国的新能源电池产业发展迅速,它是一个需要大量加工和测试的生产产业,也是激光焊接技术应用比较广泛的产业之一,安全性、高效性、可持续和环保一直是世界新能源电池产业发展的主题,激光焊接技术作为现代新能源电池生产中的重要加工方法之一,其发展也必然围绕着这一主题并结合本专业的自身特点来进行。
由于激光焊接工艺优越性、效率高、柔性好等优势,随着新能源电池的广泛性应用及效能观念日益增强,激光焊接技术在新能源电池領域将得到更多重视和广泛应用。
新能源电池制造过程中,激光焊接技术主要用于电池的极耳焊接、端盖焊接、集流盘焊接、壳体焊接等零部件焊接。
激光焊接技术运用于新能源电池,可以提高产品的稳定性,同时降低新能源电池的使用风险,提升产品的使用效能,逐步实现新能源电池产业发展的可持续、环保理念。
2 激光焊接技术在新能源电池领域的应用激光焊接技术“是一种具有高效的焊接技术的工艺,主要利用激光束产生辐射的能量实现作用,对激光束的能量进行高效的聚焦处置,以此为基础,形成具有很高能量的激光脉冲,利用这些对相关的材料或物质进行处理与加工,使用这一技术的主要范围在于对相关材料的微小部位进行焊接”。
与传统焊接技术相比,激光焊接技术显现出其独特的优势,在对新能源电池的零部件进行焊接过程中具有较大深度、不容易变形、具有较高的速度,并且对新能源电池焊接材料的材质要求并没有那么严苛。
论新能源动力电池激光清洗与焊接工艺研究

论新能源动力电池激光清洗与焊接工艺研究摘要:结合当前新能源汽车发展的情况,重点探讨了如何发挥出激光清洗方式融入到新能源动力电池中,并探讨了电池极柱铝合金激光清洗实验的相关设备以及工艺试验,通过试验表明,能发挥出激光加工工艺的质量的可行性,为今后新能源动力电池发展奠定基础。
关键词:新能源汽车,动力电池,激光清洗,焊接工艺在当前新能源汽车如火如荼的发展中,我国非常重视新能源汽车产业的发展,并能从整体上合理规划以保障新能源汽车的高质量发展。
其中,新能源汽车的动力电池则是最为关键的研发内容,也是在创新发展新能源汽车中重要研发方向。
为了控制电池重量,这里都选择铝合金结构,并要求相应具有非常高的结构可靠性,在具体的处理中,传统模式大都是选择超声波焊、电弧焊、电阻焊等方案,不仅较为费力,还会存在着一定的安全隐患问题。
这里重点探讨了动力电池激光清洗与焊接相关问题,希望能有助于推动新能源动力电池的发展。
1 电池极柱铝合金激光清洗实验考虑到铝合金容易出现氧化的实际情况,这样往往会造成存在着表面硬质氧化层的情况,这样在具体的焊接环节中,为了进一步打碎则涉及到大能量,会造成能量损失且难以满足预期的焊接速度要求,容易造成存在着未熔合、未焊透以及表面不均的情况。
如果不加以重视存在的气孔问题,还会造成后期的夹渣及热裂的问题。
这里为了有效解决上述问题,应加强铝合金激光焊接中吸收率的研究工作,并发挥出激光清洗优势,进行相关的氧化层去除实验工作。
1.1设备选型在具体实践中,明确选择光纤传输的光纤激光器、碟片激光器等等,考虑到相关的激光头的参数要求,结合相应的打标控制原理来实现激光清洗的要求,这里选择相应的SCANLAB SCANcube14小型振镜的方案,并配置相应的不同焦距的场镜。
考虑到其表面较强的反光问题,应落实小光学比的场镜的要求,能满足相应的激光功率密度的要求。
经过实验,选择焦距254mm及以下的场镜符合上述要求。
1.2工艺实验落实速度的基础上,应从实际需求来进行配置优化,以便能实现预期的清洗目标。
4.11 动力电池的激光焊接讲解
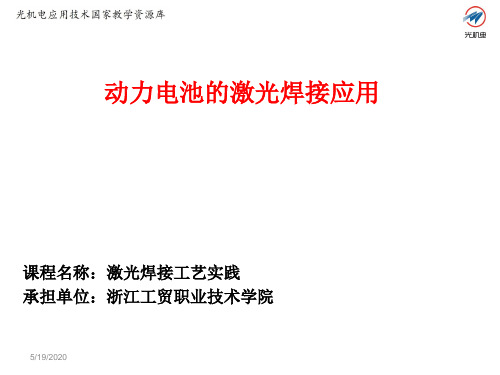
9/30/2018
2
动力电池焊接技术
2.1动力电池简介
动力电池即为工具提供动力来源的电源,多指为电动汽车、电动列车、电动自行 车、高尔夫球车提供动力的蓄电池。对于动力电池生产企业简而言之,激光焊接是一 个将正负极材料、隔膜和电解液等原材料化零为整的融合制造过程,是整个动力电池 生产流程中的关键工艺,其上下游产业链如图1所示。
9/30/2018
3. 小结
本次课介绍了新能源产业中的动力电池材料、结构和焊 接封装工艺要求,使得激光焊接成为动力电池焊接的主要选 择。
9/30/2018
4. 作业思考题
(1)工业上,动力电池主要应用在哪些领域? (2)根据动力电池的焊接封装工艺要求,说明为何激光焊
接更适合动力电池的焊接?
9/30/2018
9/30/2018
图2 动力电池生产过程涉及到的焊接部位
对多种焊接工艺比较研究发现,激光焊接优势在于焊材损耗小、被焊接工件变形小、 设备性能稳定易操作,焊接质量及自动化程度高。其工艺上的优势是其它焊接方式 无法比拟的。 以常见的圆柱形电池为例,涉及的激光焊接工序包括:(1)防爆阀焊接;(2)汇 流盘焊接;(3)正负极耳焊接;(4)壳体封口焊接;(5)注液孔焊接
9/30/2018
图1 动力电池的产业链示意图
2.2
动力电池焊接工艺
电池制造过程涉及的焊接技术十分广泛,如超声波焊、电阻焊和激光焊接等。焊 接方法与工艺的合理选用,直接影响电池的生产成本、质量的可靠性与使用的安全 性。激光焊接作为电池生产一项非常重要的工艺环节,对电池的一致性,稳定性和 安全性有很大的影响,动力电池多为薄壁铝材,激光焊接部位多,工艺难度大,对 焊接工艺要求高(图2所示动力电池的焊接位置)。
激光焊接机在汽车锂电池行业的焊接工艺技术

激光焊接机在汽车锂电池行业的焊接工艺技术随着人类社会的发展,工业化、现代化水平的不断提高,人类社会取得了巨大的经济、技术成就,同时也导致了世界环境污染日益严重和全球能源危机不断加剧。
近些年来能源和环境问题的进一步恶化跟汽车的大范围普及有很大关系。
为缓解这一问题,我国已把节能与新能源汽车列入战略性新兴产业之一,新能源汽车将逐渐替代传统燃油汽车已成为全球共识,而动力电池作为新能源汽车的核心部件,其供电性能、稳定性、安全性是决定新能源汽车性能的一个重要方面,也是消费者在选择新能源汽车时必须考虑的一方面,动力电池焊接质量对动力电池的性能起着决定性的作用。
一.动力电池分类目前电动汽车常用的动力电池主要有铅酸电池、镍镉和镍氢电池、锂离子电池、碳酸铁锂电池以及燃料电池五大类。
本文主要向大家介绍铝壳锂离子电池的激光焊接工艺。
二.激光焊接在汽车铝壳锂离子电池行业的应用激光焊接是以激光束作为能量源,利用聚焦装置使激光聚集成高功率密度的光束照射在工件表面进行加热,在金属材料的热传导作用下材料内部溶化形成特定的溶池。
激光焊接是一种新型的焊接方式,目前还处在高速发展阶段。
采用激光焊接时,工件的热影响区较小;焊点小,焊接尺寸精度高;其焊接方式属于非接触性焊接,无需加外力,产品变形小;焊接质量高;效率高,易于实现自动化生产。
一.UW激光焊接设备在汽车铝壳锂离子电池行业的应用尚拓激光是一家专业研发生产销售激光焊接机的国家级高新技术企业,是目前该领域最专业、研发力量最强、技术水准最高的激光焊接机企业。
产品类型有YAG激光焊接机、光纤激光器等,功率由5W-1000W。
尚拓激光设备涉及汽车铝壳电池的应用已长达6年之久,根据汽车铝壳锂离子电池的不同焊接部位,各部位不同的材料、不同的厚度及不同的连接方式选择不同类型不同型号的激光器。
汽车铝壳锂离子电池各部位激光焊接工艺影响激光焊接质量的因素1.激光焊接设备:光束模式、输出功率稳定性以及导光和聚焦系统;2.产品状态:焊接产品的加工精度、装配精度以及清洁程度和焊接产品的材料均匀性;3.焊接工装夹具:夹具的加工精度以及定位精度;4.焊接工艺参数:激光功率、脉冲宽度、激光波形、焊接速度、离焦量和保护气体等。
电池生产中的激光焊接应用

激光焊接在电池生产中的应用简述一、锂离子电池锂离子电池有很多种型号,在其生产过程中,需要焊接的工序包括电池组连接片焊接、外壳密封焊接、极耳焊接、安全阀焊接等。
焊接的材质主要有纯铜、镍、铝及铝合金、不锈钢等,根据材料种类和厚度不同,所用激光器主要为低频脉冲YAG固体激光器、准连续或连续光纤激光器。
1、电池组连接片焊接电池之间的串并联一般通过连接片与单体电池的焊接来完成,正负极材质不同,一般有铜和铝两种材质,由于铜和铝之间采用激光焊接后形成脆性化合物,无法满足使用要求,通常采用超声波焊接外,铜和铜、铝和铝一般均采用激光焊接。
2、电池壳体与盖板封口焊接电池的壳体材料有铝合金和不锈钢,其中采用铝合金的最多,一般为3003铝合金,也有少数采用纯铝。
不锈钢是激光焊接性最好的材质,尤其304不锈钢,无论是脉冲还是连续激光都能够获得外观和性能良好的焊缝。
铝及铝合金的激光焊焊接性能根据采用焊接方式的不同而略有差异。
除了纯铝和3系铝合金采用脉冲焊接和连续焊接都没有问题,其他系列铝合金最优选择连续激光焊接方式,以减小裂纹敏感性。
同时,根据电池壳体厚度选择合适功率的激光器,一般壳体厚度1 mm以下时,可考虑采用1000W以内单模激光器,厚度在1mm以上需使用1000W 以上单模或多模激光器。
小容量锂电池常采用比较薄的铝壳(厚度在0.25 mm 左右),也有的采用钢壳。
由于壳体厚度的关系,此类电池的焊接一般采用较低功率的激光器即可,目前最多采用的是YLR-500激光器。
根据实际焊接需要可采用连续焊接,也可以采用调制脉冲输出的脉冲激光焊接,或直接采用QCW准连续激光器进行脉冲焊接。
同时配置振镜焊接头的焊接方式也可采用。
使用连续激光器焊接薄壳锂电池,效率可以提升5~10 倍,且外观效果和密封性更好。
因此有逐渐取代脉冲激光器在这个应用领域的趋势。
3、电池极带点焊电池极带使用的材质包括纯铝带、镍带、铝镍复合带以及少量的铜带等。
电池极带的焊接一般使用脉冲焊接机,随着IPG 公司QCW 准连续激光器的出现,其在电池极带焊接上也得到了广泛的应用,同时由于其光束质量好、焊斑能够做到很小,其在应对高反射率的铝带、铜带以及窄带电池极带(极带宽度在1.5 mm 以下)的焊接有着独特的优势。
汽车动力电池的激光焊接和摩擦焊接的失效分析
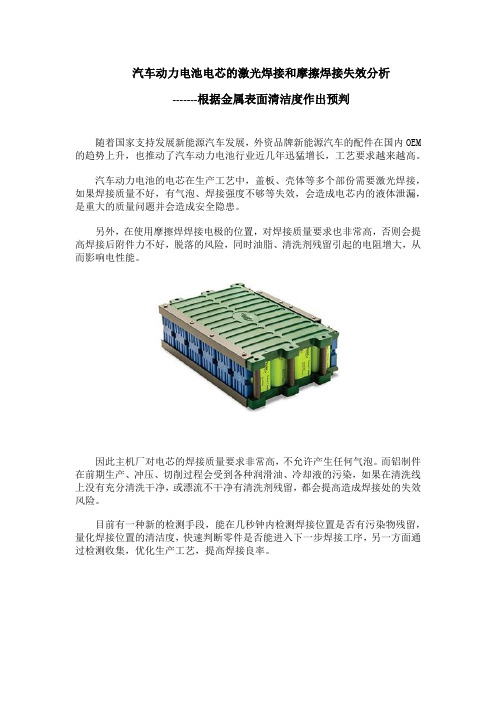
汽车动力电池电芯的激光焊接和摩擦焊接失效分析
-------根据金属表面清洁度作出预判
随着国家支持发展新能源汽车发展,外资品牌新能源汽车的配件在国内OEM 的趋势上升,也推动了汽车动力电池行业近几年迅猛增长,工艺要求越来越高。
汽车动力电池的电芯在生产工艺中,盖板、壳体等多个部份需要激光焊接,如果焊接质量不好,有气泡、焊接强度不够等失效,会造成电芯内的液体泄漏,是重大的质量问题并会造成安全隐患。
另外,在使用摩擦焊焊接电极的位置,对焊接质量要求也非常高,否则会提高焊接后附件力不好,脱落的风险,同时油脂、清洗剂残留引起的电阻增大,从而影响电性能。
因此主机厂对电芯的焊接质量要求非常高,不允许产生任何气泡。
而铝制件在前期生产、冲压、切削过程会受到各种润滑油、冷却液的污染,如果在清洗线上没有充分清洗干净,或漂流不干净有清洗剂残留,都会提高造成焊接处的失效风险。
目前有一种新的检测手段,能在几秒钟内检测焊接位置是否有污染物残留,量化焊接位置的清洁度,快速判断零件是否能进入下一步焊接工序,另一方面通过检测收集,优化生产工艺,提高焊接良率。
德国SITA CleanoSpector清洁度检测仪采用荧光原理,量化测出金属表面污染程度,读数单位为RFU(相对荧光总量,读数越大表示污染越严重)。
在某知名汽车动力电池生产厂现场实测数据如下:
在摩擦焊前测出清洁度数值,对提高摩擦焊的良品率,优化改进摩擦焊接的工艺效果显著。
动力电池激光焊接技术介绍
动力电池激光焊接技术介绍
激光焊接技术在动力电池制造领域具有重要作用,它能确保电池组件的高效、稳定和安全。
以下是关于动力电池激光焊接技术的一些介绍:
1.激光焊接原理:激光焊接是利用高能量密度的激光束在焊接区域产生局部熔化,将电池极片或隔膜等材料焊接在一起。
激光束的功率和焊接速度可调,可根据实际需求实现不同焊接效果。
2.焊接过程:激光焊接过程通常包括预处理、焊接和后续处理等步骤。
预处理目的是使焊接区域清洁、无油污,以保证焊接质量。
焊接过程中,激光束通过透镜聚焦在焊接区域,产生高温高压力,使材料熔化并连接。
后续处理主要是为了使焊接部位平滑、美观,并减小焊缝附近的应力。
3.优点:激光焊接具有焊接速度快、熔接区域小、焊缝平整、焊接质量高等优点。
此外,激光焊接还可以实现精确控制,使电池组件的尺寸和性能更加稳定。
4.应用场景:激光焊接技术广泛应用于新能源汽车动力电池的生产制造,包括电池模块、电池包、电池系统等各级别产品的焊接。
特别是对于高能量密度、轻量化、小型化的电池产品,激光焊接技术具有显著优势。
5.发展趋势:随着新能源汽车产业的快速发展,对动力电池性能和可靠性的要求不断提高。
未来,动力电池激光焊接技术将朝
着更高功率、更高速度、更精细控制等方向发展,以满足市场需求。
。
新能源汽车动力电池激光清洗与焊接工艺研究应用
新能源汽车动力电池激光清洗与焊接工艺研究应用摘要随着新能源汽车的快速发展和需求的不断扩大,其核心部件动力电池的安全性及生产效率备受瞩目。
本文针对目前新能源电池制作中焊接及焊前处理新工艺进行工艺实验研究,对铝合金动力电池模组生产中的BUSBAR片及极柱采用激光清洗、激光焊接工艺,模组端板与侧板连接中激光焊接工艺进行设备选型及工艺实验研究,推动激光新工艺在动力电池领域应用,促进新能源电池的低能耗、快速、安全、绿色生产。
关键词新能源;动力电池;激光;铝合金;清洗;焊接新能源汽车发展十多年,尤其近几年发展十分迅速,应用日趋成熟。
目前,欧美国家及日本,都把发展新能源汽车作为战略制高点来考虑,国家投入力量加强产业的发展。
尤其是欧盟一些国家不仅是提出“禁止销售燃油时间表”,而且也上升到具体是法律层面,同时应采取一些“限行”措施。
中国则是更为主动、更积极、更为系统地推动新能源汽车的发展,中央和地方两级政府在财力强力支持。
作为新能源汽车的心脏——动力电池已成为相关企业研发的重中之重。
为降低电池重量,电池结构中通常采用铝合金结构,尤其电池pack模组承重外壳、busbar电极连接片的组装对结构的可靠性要求极高,以前该部分常采用铆接、电弧焊,超声波焊,电阻焊等方式,不但费时费力,而且容易产生安全隐患。
公司对某国内巨头企业传统工艺产线升级改造中,提出激光清洗、焊接工艺,并做了大量实验研究、验证,推动激光工艺在新能源动力电池方面应用。
1 电池极柱铝合金激光清洗实验铝合金在空气中极易氧化,表面会形成硬质氧化层,由于氧化层熔点较高,在激光焊接过程中需较大能量打碎,不但消耗较大能量拖累焊接速度,而且极易形成未焊透、未熔合、表面成型不均匀,并且氧化层在熔池中反应形成气孔,熔池中未完全熔化的氧化层会形成夹渣及造成热裂。
同时为提高铝合金激光焊接中吸收率,激光清洗应具有清洗细小纹路打毛表面作用。
为高效去除铝合金表面氧化层,采用激光清洗工艺对6061铝合金氧化层去除进行了实验研究。
新能源动力电池模组激光焊接
新能源动力电池模组激光焊接新能源动力电池模组激光焊接是目前电池行业中一种常见的连接技术,它通过利用激光束将电池模组中的各个部件进行焊接,从而实现电池的组装和连接。
本文将围绕新能源动力电池模组激光焊接展开讨论,介绍其原理、应用以及优势。
一、激光焊接原理新能源动力电池模组激光焊接是利用激光束的热效应对电池模组进行焊接的一种技术。
激光束照射到电池模组的焊接接头上,通过瞬间高温的作用,使接头表面部分熔化并迅速冷却固化,从而实现焊接。
激光焊接具有高能量密度、瞬间加热、热影响区小等优点,能够实现高精度、高效率的焊接。
二、激光焊接的应用新能源动力电池模组激光焊接广泛应用于电动汽车、储能设备等领域。
在电动汽车中,电池模组是其核心组件之一,激光焊接可以将电池模组中的电芯、导电片等部件进行可靠的连接,提高电池模组的性能和寿命。
在储能设备中,激光焊接可以实现电池模组的快速组装,提高生产效率和产品质量。
三、激光焊接的优势1. 高精度:激光焊接可以实现微小焊点的精确定位和焊接,大大提高了焊接的精度和可靠性。
2. 高效率:激光焊接速度快,能够实现对多个焊点的同时焊接,提高了生产效率。
3. 无污染:激光焊接不需要使用焊剂和助焊剂,避免了对环境的污染。
4. 低热影响区:激光焊接瞬间加热,热影响区小,不会对周围材料产生热变形和热损伤。
5. 焊接强度高:激光焊接可以实现焊点的高强度连接,提高了焊接的可靠性和耐久性。
四、激光焊接的发展趋势随着新能源动力电池市场的快速发展,激光焊接技术也在不断创新和进步。
目前,一些新的激光焊接技术已经应用于电池模组的焊接,如激光超声波混合焊接、激光熔覆等。
这些新技术能够进一步提高激光焊接的效率和质量,满足不同应用场景的需求。
新能源动力电池模组激光焊接是一种高效、精确、可靠的连接技术。
它在电动汽车、储能设备等领域的应用不断拓展,为新能源产业的发展提供了有力支持。
随着技术的不断创新和进步,相信新能源动力电池模组激光焊接技术将在未来发展中发挥更加重要的作用。
新能源动力电池模组激光焊接
新能源动力电池模组激光焊接随着新能源汽车的快速发展,电池作为其重要组成部分,对其性能和安全性提出了更高的要求。
而电池模组作为电池系统的关键组件之一,其连接方式对整个电池系统的性能和寿命具有重要影响。
传统的焊接方式存在接触电阻大、焊接质量难以保证等问题,因此,激光焊接作为一种新的连接方式逐渐被应用于电池模组的生产中。
激光焊接是利用激光束对工件进行加热和熔化,通过熔化的金属材料形成焊缝的一种焊接方法。
与传统的焊接方式相比,激光焊接具有焊缝小、热影响区小、焊接速度快、焊接质量高等优点。
在电池模组的生产中,激光焊接不仅能够实现快速、高效的焊接,还能够减小焊接区域的热影响,避免对电池材料的损伤,从而提高电池的性能和寿命。
激光焊接在电池模组的生产中主要应用于电池片的连接。
电池片是电池模组的核心组件,通过将多个电池片按照一定的方式连接起来,形成电池模组。
而激光焊接可以实现电池片之间的快速、高效连接,避免了传统焊接方式中存在的接触电阻大、焊接质量难以保证等问题。
同时,激光焊接还能够减小电池片之间的接触电阻,提高电池模组的整体性能。
在电池模组的激光焊接过程中,激光参数的选择是关键。
激光参数的选择直接影响焊接质量和效率。
一般来说,激光功率、激光束直径和激光脉冲宽度是影响焊接质量的重要参数。
激光功率过大会导致焊缝过宽、热影响区过大,从而降低焊接质量;激光功率过小则会导致焊接不完全,影响焊接强度。
激光束直径和激光脉冲宽度的选择应根据电池片的材料和尺寸进行优化,以保证焊接质量和效率。
除了激光参数的选择,激光焊接还需要考虑焊接工艺的优化。
焊接工艺的优化包括焊接速度、焊接角度、焊接位置等方面的选择。
焊接速度的选择应根据电池片的材料和尺寸进行优化,以保证焊接质量和效率。
焊接角度的选择应使焊缝形状均匀、焊接强度高。
焊接位置的选择应使焊缝与电池片表面保持一定的距离,以避免焊接过程中对电池材料的损伤。
总的来说,新能源动力电池模组激光焊接作为一种新的连接方式,具有焊缝小、热影响区小、焊接速度快、焊接质量高等优点。
- 1、下载文档前请自行甄别文档内容的完整性,平台不提供额外的编辑、内容补充、找答案等附加服务。
- 2、"仅部分预览"的文档,不可在线预览部分如存在完整性等问题,可反馈申请退款(可完整预览的文档不适用该条件!)。
- 3、如文档侵犯您的权益,请联系客服反馈,我们会尽快为您处理(人工客服工作时间:9:00-18:30)。
新能源汽车动力电池激光清洗与焊接工艺研究应用作者:葛伟良黄川川来源:《科学与信息化》2018年第21期摘要随着新能源汽车的快速发展和需求的不断扩大,其核心部件动力电池的安全性及生产效率备受瞩目。
本文针对目前新能源电池制作中焊接及焊前处理新工艺进行工艺实验研究,对铝合金动力电池模组生产中的BUSBAR片及极柱采用激光清洗、激光焊接工艺,模组端板与侧板连接中激光焊接工艺进行设备选型及工艺实验研究,推动激光新工艺在动力电池领域应用,促进新能源电池的低能耗、快速、安全、绿色生产。
关键词新能源;动力电池;激光;铝合金;清洗;焊接新能源汽车发展十多年,尤其近几年发展十分迅速,应用日趋成熟。
目前,欧美国家及日本,都把发展新能源汽车作为战略制高点来考虑,国家投入力量加强产业的发展。
尤其是欧盟一些国家不仅是提出“禁止销售燃油时间表”,而且也上升到具体是法律层面,同时应采取一些“限行”措施。
中国则是更为主动、更积极、更为系统地推动新能源汽车的发展,中央和地方两级政府在财力强力支持。
作为新能源汽车的心脏——动力电池已成为相关企业研发的重中之重。
为降低电池重量,电池结构中通常采用铝合金结构,尤其电池pack模组承重外壳、busbar 电极连接片的组装对结构的可靠性要求极高,以前该部分常采用铆接、电弧焊,超声波焊,电阻焊等方式,不但费时费力,而且容易产生安全隐患。
公司对某国内巨头企业传统工艺产线升级改造中,提出激光清洗、焊接工艺,并做了大量实验研究、验证,推动激光工艺在新能源动力电池方面应用。
1 电池极柱铝合金激光清洗实验铝合金在空气中极易氧化,表面会形成硬质氧化层,由于氧化层熔点较高,在激光焊接过程中需较大能量打碎,不但消耗较大能量拖累焊接速度,而且极易形成未焊透、未熔合、表面成型不均匀,并且氧化层在熔池中反应形成气孔,熔池中未完全熔化的氧化层会形成夹渣及造成热裂。
同时为提高铝合金激光焊接中吸收率,激光清洗应具有清洗细小纹路打毛表面作用。
为高效去除铝合金表面氧化层,采用激光清洗工艺对6061铝合金氧化层去除进行了实验研究。
1.1 设备选型激光清洗设备采用机器人装载激光头进行清洗,优先选用可使用光纤传输的光纤激光器、碟片激光器等,铝合金清洗一般功率不超过200W,可选用IPG YLP-HP-1-100-200-200激光器,激光头采用振镜形式可采用SCANLAB SCANcube14小型振镜,配置南京波长不同焦距的场镜(较大焦距清洗铝合金表面不佳,焦距太小,工作距离较小且振镜扫描范围较小)首先进行选型测试。
采用打标控制原理来实现激光平面扫描清洗,控制卡控制系统选用海目激光标刻系统V1.0,板卡型号USC-1。
铝合金表面反光严重,因此必须采用小光学比的场镜来保证激光功率密度,经不同参数打点验证发现:当采用焦距254mm及以下的场镜是可以保证激光的功率密度实现铝合金氧化层的去除。
由于电池模组上有较多极柱清洗(一般18个以上),应尽可能选择大工作范围的场镜,因此配置南京波长254焦距(工作距离300.1mm)的SL-1064-174-254G场镜。
1.2 工艺实验在保证速度的前提下,经对激光线性填充、间隔、覆盖率、光斑实验,设置最佳搭接覆盖效果,调整功率、速度实现较好清洗效果。
实验发现,当采用254mm聚焦场镜(扫描范围为174*174),功率60W,扫描速度3000mm/s,频率f=200kHZ,覆盖率100%,采用A1线性填充,间隔0.05mm,光点直径50μm,离焦量为0mm,试验效果见图1。
当功率提高50%,为90瓦,而其他参数相同,试验效果见图2。
当斜置清洗平面,采用254mm聚焦场镜,功率60W,扫描速度3000mm/s,频率f=200kHZ,覆盖率100%,采用A1线性填充,间隔0.05mm,光点直径50μm,试验效果见图3。
图1中激光清洗光束搭接密度良好,功率合适可清洗出一定深度,铝合金氧化层基本被完全去除,并且表面有一定粗糙度,效果较为理想。
图2中激光清洗后,表面有发黑氧化现象,效果不佳,证明采用参数过大。
图3中清洗极柱平面斜置,有部分区域由于离焦后能量密度不足,清洗效果变化明显。
通过以上对比试验,当激光清洗铝合金时,采用254mm聚焦场镜,功率60W,扫描速度3000mm/s,频率f=200kHZ,覆盖率100%,采用A1线性填充,间隔0.05mm,光点直径50μm,离焦量为0mm,效果较为理想,达到激光焊前清洗要求[1]。
2 BUSBAR电池连接片激光焊接2.1 设备选型BUSBAR铝片和极柱材质分别为:1060及6061铝合金,BUSBAR焊接处厚度1.2mm,采用穿透焊工艺,功率预估6000瓦以内,可采用IPG YLS-6000光纤激光器,穿透焊光束质量要求较高,采用100μm光纤,为保证较大的焊接范围及预防干涉,可采用大族振镜HWSCAN30RD-001A,焦距460mm,工作距离578,光学比为3.1,有效工作范围220*180。
2.2 工艺实验经调整激光功率、速度及保护气体实验验证,为满足3.5mm熔深及3-4mm熔宽要求,激光功率采用4200W,焊接速度选用60mm/s,但焊接接头激光收光后出现明显凹坑。
实验采用功率和速度都缓降的模式增加半圈焊接收光,接头凹坑消除,整条焊缝成型一致,熔深熔宽均能达到要求。
采用一圈半的工艺(增加收弧处理)焊缝及接头焊接效果良好,参数如下:C1:P=4200W,v=60mm/s;C2:P(0%,50%,100%)=4200W,3600W,3600W;v(0%,50%,100%)=60mm/s,65mm/s,90mm/s;离焦量0mm,Ar气流量15L/min采用前道激光清洗(电池极柱和BUSBAR片表面)及不加前道激光清洗两种工艺,焊接外观前者更加光亮一致,后者焊缝凹凸一致较差见图4,5。
对焊接试件进行切片后进行分析,发现不加激光清洗工艺的试件中间存在较大气孔,而增加激光清洗工艺后气孔明显减少甚至消失(如下图6,7所示)。
从以上工艺实验发现当采用一圈半的工艺(增加收弧处理),C1:P=4200W,v=60mm/s;C2:P(0%,50%,100%)=4200W,3600W,3600W; v(0%,50%,100%)=60mm/s,65mm/s,90mm/s;离焦量0mm,Ar气流量15L/min,焊缝及接头焊接外观效果良好。
通过对该工艺在焊前采用及不用激光清洗处理两种情况的实验对比中金相实验发现,采用激光清洗工艺的焊缝气孔几乎没有,致密性良好,满足充放电致密性要求;拉力测试对比可见,采用激光清洗工艺的焊缝强度明显较高。
铝合金BUSBAR片和极柱焊接中,激光清洗对焊接质量明显提升。
该清洗及焊接工艺满足熔深、熔宽成型要求,拉力测试满足预设指标(3.5kN)要求、数值稳定并且具有较大裕量[2]。
3 电池模组端板与侧板激光焊接3.1 焊前准备采用酒精清洗铝合金表面及结合面,静止两分钟待表面酒精完全挥发。
将电池模组中电芯、端板(6061-T6铝合金型材)、侧板(5083-H24,厚度1mm)等在夹具加紧装好,保证焊缝间隙小于0.5mm(见图9)。
方案一采用激光准直聚焦头焊接方式电池模组激光焊接工艺,功率预估4000瓦以内,可采用IPG YLS-4000光纤激光器,为保证铝合金焊接熔深光束质量要求较高,采用100μm光纤,可采用HIGHYAG BIMO准直头(见图8),工作距离310mm,光学比2.1。
经实验发现,采用常规焊接速度20~60mm/s,-2~2mm离焦量,2700~3500W功率,焊接过程均不能避免焊缝裂纹产生,出现概率在75%以上。
经分析,激光热量集中,焊接速度较快,铝合金型材厚度较大导热快,在夹具刚性固定下,焊缝快速冷却过程中产生较大应力形成热裂纹。
同时电池模组端板侧板焊缝紧邻电池,且内有涂胶层外侧夹具遮挡,不能采用传统的火焰预热工艺,并且激光焊接过程中不使用焊接填料,无法采用通过焊接材料增加焊缝Mg-Si 成分的方法来控制热裂纹形成。
根据激光焊接特点,经过反复试验选用激光功率为1800W的小功率进行焊缝预处理,再紧随进行焊接,在该前道工序处理后,后道焊缝冷却速度会明显降低,在后续近百条焊缝中焊接热裂纹得以完全消除。
同时通过对起始和结尾功率缓升缓降的优化,焊缝起始和结尾平滑过渡,无焊瘤及凹坑。
具体焊接参数如下:前道预热功率为1800W,预热起始功率1200W,经70ms缓升至1800瓦,在结束前经70ms降至500W;焊接功率为3000W,焊接起始功率1500W,经70ms缓升至3000瓦,在结束前经20ms降至2000W,再经50ms降至1500瓦后关光收弧。
其中预热焊接速度均为30mm/s,为保证焊缝宽度成形采用2mm离焦量,Ar流量15L/min。
方案二采用激光振镜焊接方式电池模组激光配置,采用100μm光纤,为保证较大的焊接范围及预防干涉,可采用大族振镜HWSCAN30RD-001A,焦距460mm,工作距离578,光学比为3.1,有效工作范围220*180。
由于光学比较大,为达到较好的功率密度,功率预估6000瓦以内,可采用IPG YLS-6000光纤激光器。
在激光振镜焊接过程中为避免热裂纹产生,可在振镜丰富的设置功能中设置激光螺旋线摆动焊接方式。
经试验发现:激光螺旋波形线宽为,步长为,激光功率为,直线焊接速度为,离焦量0mm,Ar为15L/min时,焊接效果良好。
通过振镜设置合适的激光摆动工艺可消除铝合金焊接热裂纹的产生(见图13)。
对上述两种工艺进行金相测试,发现焊缝能够完全熔透,且熔合良好。
分别取10组试件,焊缝长度70mm进行拉力测试,最大拉力测试结果如表2所示。
4 结束语动力电池模组中铝合金BUSBAR片和极柱的连接技术及端板侧板连接技术为新能源电池制造的关键工艺。
铝合金BUSBAR片和极柱其连接部位会经常性通过较高电流提供动力并反复充放电及经受振动承载,要求具有可靠的力学性能及断面致密性。
端板侧板连接为电池模组的组装受力结构件,其强度及抗裂性能直接关系电池安全。
并且电池模组制造对洁净度、烟尘控制要求严格,激光工艺的开发很好地满足了以上要求,其具有较好的穿透性、致密性、烟尘极小、不需施加压力安全可靠,焊接速度较快,易于集成和自动化,可实现高效生产。
同时激光是非接触远程加工工艺,对结构的适应性及夹具设计空间提供较好条件;并且焊接过程不需要添加焊材,节省耗材成本。
本文通过对新能源动力电池极柱与BUSBAR片激光清洗、激光焊接,端板侧板激光焊接工艺的探索实验,提供了可行的工艺方案,验证了激光加工工艺的质量可靠性、先进性,为新能源动力电池制造中激光工艺应用提供技术支持。
参考文献[1] 张政,厉丹彤,冯小保,等.新能源汽车的发展现状及其展望[J].化工新型材料,2015,(3):1-3.[2] 王淳.中国新能源汽车产业发展政策研究[D].成都:西南石油大学,2015.[3] 田晋跃.现代汽车新技术概论[M]. 北京:北京大学出版社,2014, 21-22.。