【产品管理】产品标准工时计算实例
标准工时计算方法

标准工时计算方法一、目的:规范标准工时制定与修改作业,使标准工时具有完整性,使ERP系统运行之排程合理和成本准确。
二、名词定义:2.1、标准工时:在特定的工作环境条件下,用规定的作业方法和设备,以普通熟练工作者的正常速度完成一定质量和数量的工作所必需的时间。
2.2、宽放时间:指作业员除正常工作时间之外必须的停顿及休息的时间。
包括操作者个人事情引起的延迟,疲劳或无法避免的作业延迟等时间。
对于没有规定发生时间、发生频率、所需时间的不规则要素作业,并不在正常时间范围之内,而属于宽放时间。
2.3、标准速度:没有过度体力和精神疲劳状态下,每天能连续工作,只要努力就容易达到标准作业成果的速度。
三、标准工时的构成:3.1、标准时间=正常时间+宽放时间=观测时间*(1+熟练修正数+努力修正数)+观测时间*宽放率3.2、正常时间:3.2.1、主体作业时间:按照作业目的进行的作业。
指能创造价值的作业,如改变产品外形,改变产品性能等。
3.2.2、副作业时间:与主体作业同步发生,起附属作用。
如取放工具、检查等。
正常时间设定方法如下:直接观测法:秒表观测法;摄影分析法;work sampling法。
优点:比较简单;任何人都可以做。
缺点:难于跟标准速度相比较,需要评价标准速度;生产之前不能设定。
合成法:动作分析法、历史数据法。
优点:信赖程度和一贯性高;客观性和普遍性高;不需要评价标准速度;可在生产之前设定;容易消除不必要动作。
缺点:需要教育和训练。
3.3、宽放时间:3.3.1、私事宽放时间:作业过程中,满足生理要求的宽放时间,如上厕所,喝水,擦汗。
3.3.2、疲劳宽放时间:为了补偿工作过程中体力和精神疲劳,采取的休息或操作速度减弱的宽放时间。
3.3.3、特殊宽放:学习宽放、机械干涉宽放、奖励宽放、工厂宽放、其它宽放.作业宽放时间:补偿作业过程中发生不规则的要素作业。
如用处理不良品等。
3.3.4、集体宽放时间:集体作业时,对于个体差异产生损失的补偿。
标准工时怎么算
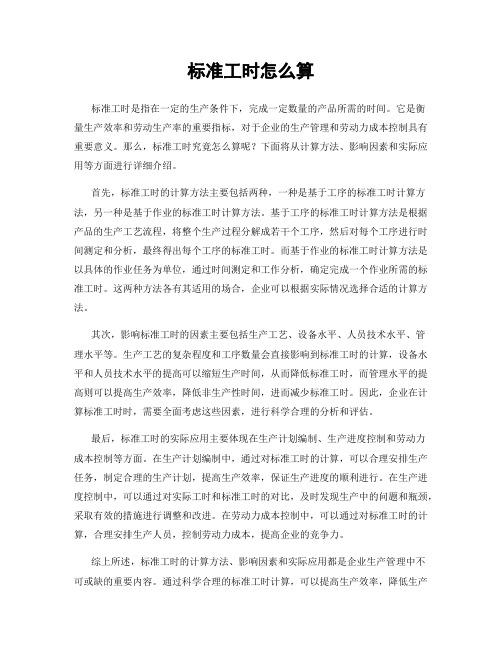
标准工时怎么算标准工时是指在一定的生产条件下,完成一定数量的产品所需的时间。
它是衡量生产效率和劳动生产率的重要指标,对于企业的生产管理和劳动力成本控制具有重要意义。
那么,标准工时究竟怎么算呢?下面将从计算方法、影响因素和实际应用等方面进行详细介绍。
首先,标准工时的计算方法主要包括两种,一种是基于工序的标准工时计算方法,另一种是基于作业的标准工时计算方法。
基于工序的标准工时计算方法是根据产品的生产工艺流程,将整个生产过程分解成若干个工序,然后对每个工序进行时间测定和分析,最终得出每个工序的标准工时。
而基于作业的标准工时计算方法是以具体的作业任务为单位,通过时间测定和工作分析,确定完成一个作业所需的标准工时。
这两种方法各有其适用的场合,企业可以根据实际情况选择合适的计算方法。
其次,影响标准工时的因素主要包括生产工艺、设备水平、人员技术水平、管理水平等。
生产工艺的复杂程度和工序数量会直接影响到标准工时的计算,设备水平和人员技术水平的提高可以缩短生产时间,从而降低标准工时,而管理水平的提高则可以提高生产效率,降低非生产性时间,进而减少标准工时。
因此,企业在计算标准工时时,需要全面考虑这些因素,进行科学合理的分析和评估。
最后,标准工时的实际应用主要体现在生产计划编制、生产进度控制和劳动力成本控制等方面。
在生产计划编制中,通过对标准工时的计算,可以合理安排生产任务,制定合理的生产计划,提高生产效率,保证生产进度的顺利进行。
在生产进度控制中,可以通过对实际工时和标准工时的对比,及时发现生产中的问题和瓶颈,采取有效的措施进行调整和改进。
在劳动力成本控制中,可以通过对标准工时的计算,合理安排生产人员,控制劳动力成本,提高企业的竞争力。
综上所述,标准工时的计算方法、影响因素和实际应用都是企业生产管理中不可或缺的重要内容。
通过科学合理的标准工时计算,可以提高生产效率,降低生产成本,提高企业的竞争力,实现可持续发展。
因此,企业应该重视标准工时的计算和应用,不断优化和改进管理,提高生产效率,实现经济效益和社会效益的双丰收。
标准工时计算案例

标准工时计算案例
标准工时的计算方法因国家和行业而异,但通常都基于工作分析和经验数据。
以下是一个简单的标准工时计算案例:
案例背景:
假设某公司生产一款产品,该产品由A、B、C三个零件组成,生产流程如下:
1. 零件A的加工时间为5分钟,生产100个需要500分钟。
2. 零件B的加工时间为7分钟,生产100个需要700分钟。
3. 零件C的加工时间为10分钟,生产100个需要1000分钟。
4. 组装三个零件需要8分钟/个,生产100个需要800分钟。
基于上述流程,我们可以计算出生产100个产品的总工时:
500分钟(零件A)+ 700分钟(零件B)+ 1000分钟(零件C)+ 800
分钟(组装)= 3000分钟。
将总工时转换为小时:3000分钟 / 60 = 50小时。
因此,生产100个产品需要50小时的标准工时。
需要注意的是,这个案例非常简单,实际生产中可能会有更复杂的工艺流程和影响因素,如设备故障、员工休息、材料准备等。
因此,标准工时的计算需要综合考虑各种因素,并进行详细的工作分析。
产品工时额定标准
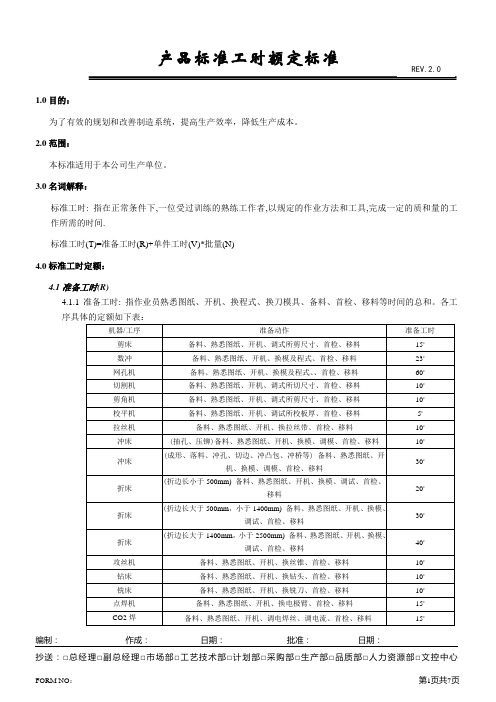
1.0目的:为了有效的规划和改善制造系统,提高生产效率,降低生产成本。
2.0范围:本标准适用于本公司生产单位。
3.0名词解释:标准工时: 指在正常条件下,一位受过训练的熟练工作者,以规定的作业方法和工具,完成一定的质和量的工作所需的时间.标准工时(T)=准备工时(R)+单件工时(V)*批量(N)4.0标准工时定额:4.1准备工时(R)4.1.1准备工时: 指作业员熟悉图纸、开机、换程式、换刀模具、备料、首检、移料等时间的总和。
各工4.1.2在工时定额时,可根据实际情况对以上的准备工时作以适当的调整。
4.2 单件工时(V)4.2.1 单件工时(V): 一位熟练工作者以规定的作业方法和工具完成一件合格料品所需的时间.单件工时(V)=上下料时间(Ts)+机器/人加工效率(Vr)*(1+宽放率(Aw))+辅助时间(F)4.2.24.2.34.2.4各工序/机器单件工时具体定额4.2.4.1剪床:(均以标准板材(4尺,8尺)计算,则有剪条料单件工时=(材料长/条料宽+1)*12"/N剪净料单件工时V=[(A+1)*12”+(C+1)*Vr]/N*(1+Aw) B DA=材料长B=工件长C=材料宽D=工件宽N=一张板加工工件数量Vr=单刀时间(当工件L<5000时,Vr=0.1’; 当工件500>L>1000时,Vr=0.15’;当工件L>1000时,Vr=0.2’)4.2.4.2数冲:a. V=Ts+ [(C+D)/*Vr+E*H+F*K]*(1+Aw)C=工件外周长D=工件内孔周长(孔径大于60mm)E=换刀次数F=孔数(孔径等于或小于60mm)Vr=切边速度0.15'/1000mm(按刀长为60算)H=自动换刀速度0.15'/次K=冲孔速度(松散孔1”/下冲一次,密集孔1”/下冲6次(液压AMADA))b. 覆膜与去毛刺时间=数冲单件工时(V)。
c. 当加工工件板材厚度大于2.0时,其单件工时须乘以1.2的系数.4.2.4.3切割机:a.平台切割机:V=Ts+Vr*N*(1+Aw)+F (可根据材料截面的大小对其机器工效率作以适当的调整)N=下切刀数b.等离子切割机:V=Vr*L*(1+Aw)+FL=切割缝长4.2.4.4网孔机:V=Ts+Vr*N*(1+Aw)+FN=下冲次料=孔总数一次冲孔数4.2.4.5冲床:a.抽孔、压铆:V=Ts+Vr*N*(1+Aw)+FN=压铆数量或抽孔数量当N>15时,其单件工时(V)须乘以0.8系数;b.成形、落料、冲孔、切边、冲凸包、冲桥等:V=Ts+Vr*N*(1+Aw)+FN=下冲次数剪条料后落料的单件时间须乘以0.6系数;c.当料件长大于1200mm,宽大于500mm时,其机床加工效率应乘以2。
标准工时和计算标准管理规范(含表格)
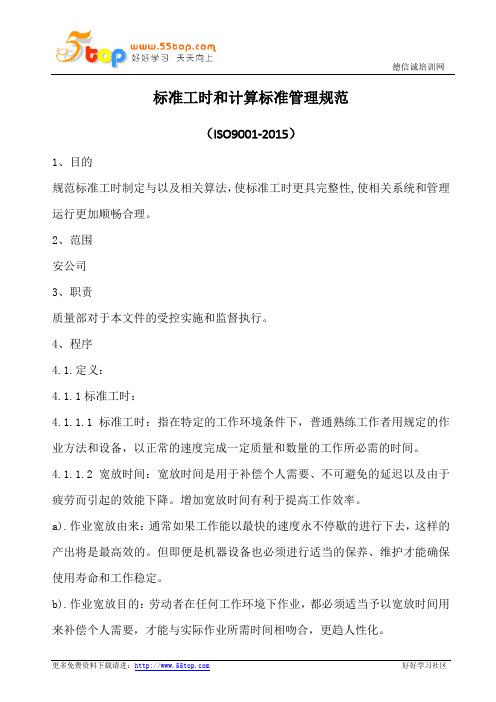
标准工时和计算标准管理规范(ISO9001-2015)1、目的规范标准工时制定与以及相关算法,使标准工时更具完整性,使相关系统和管理运行更加顺畅合理。
2、范围安公司3、职责质量部对于本文件的受控实施和监督执行。
4、程序4.1.定义:4.1.1标准工时:4.1.1.1标准工时:指在特定的工作环境条件下,普通熟练工作者用规定的作业方法和设备,以正常的速度完成一定质量和数量的工作所必需的时间。
4.1.1.2宽放时间:宽放时间是用于补偿个人需要、不可避免的延迟以及由于疲劳而引起的效能下降。
增加宽放时间有利于提高工作效率。
a).作业宽放由来:通常如果工作能以最快的速度永不停歇的进行下去,这样的产出将是最高效的。
但即便是机器设备也必须进行适当的保养、维护才能确保使用寿命和工作稳定。
b).作业宽放目的:劳动者在任何工作环境下作业,都必须适当予以宽放时间用来补偿个人需要,才能与实际作业所需时间相吻合,更趋人性化。
4.1.1.3标准速度:没有过度体力和精神疲劳状态下,每天能连续工作,只要努力就容易达到标准作业成果的速度。
4.1.2员工定义:4.1.2.1直接人员:指生产产线上从事生产操作人员。
包括装配、调整、检查检测和不良品维修人员。
他们是生产线上直接从事生产劳动的人员。
4.1.2.2间接人员:指不直接从事生产操作的人员,此处包括车间班长,物料配送人员、设备保养人员、工具保养人员。
间接员工虽然不从事直接的生产操作,但对于提升生产效率具有很大的影响。
4.1.3时间定义:4.1.3.1正常作业时间:指以每天8小时为基准的作业时间,其单位为分钟。
正常作业时间包括“前准备时间”和“净作业时间”。
4.1.3.1.1前准备时间(95分钟):a).早会(早会,交接班)10分钟b).清洁(工治具、设备、车间、更衣)30分钟c).中餐时间15分钟d).间隙时间(上午15分钟,下午15分钟)30分钟e).首检时间10分钟4.1.3.1.2净作业时间:指对作业对象作业的内容,规则地、周期性地重复进行的作业部分的时间。
产品标准工时计算实例

1次印刷 3.13
8.49
烘烤 0.95
卸網版 清潔 1.79
架網版 調墨 2.38
2次印刷 1.79
5.96
烘烤 0.95
卸網版 清潔 1.79
架網版 調墨 20 min
C
3次印刷 1.66
架網版 調墨 2.38
3次印刷 1.66
5.83
烘烤 8 min
卸網版 清潔 15 min
清潔
人員 1
印刷
人員2
架網版 調墨
人員 1-5
清潔
人員 1
印刷
人員2
架網版 調墨
人員 1-5
清潔
人員 1
印刷
人員2
網版印刷製程
每片需重覆之動作
檢查
人員3、4
取料
人員5
烘烤
人員5
卸網版 清潔
人員 1-5
檢查
人員3、4
取料
人員5
烘烤
人員5
卸網版 清潔
人員 1-5
檢查
人員3、4
取料
人員5
烘烤
人員5
卸網版 清潔
22
情況B
網版印刷製程
1. 網印機台 1 台
2. 需先烘烤 30 min
3. 網版架設 20 min
(含定位與試印)
4. 網版拆卸與清洗 15 min
人員 1-5
18
三次印刷瓶頸時間
網版印刷製程
Raw material
Seq Operation
1 1次印刷 2 2次印刷 3 3次印刷
Work Time (sec/pc)
3.13
1.79
1.66
工厂标准工时计算方法
工厂标准工时计算方法
工厂标准工时是指完成一定数量的产品所需的标准时间,通常用小时为单位。
工厂标准工时的计算方法如下:
1. 确定生产计划中的产品数量和种类。
2. 对生产过程进行分解,确定每个工序所需的时间和人工费用。
3. 将每个工序的时间和费用相加,得到整个生产过程的标准时间和人工费用。
4. 根据生产计划中的产品数量,计算出每种产品的标准时间和人工费用。
5. 将每种产品的标准时间和人工费用相加,得到整个生产计划的标准时间和人工费用。
6. 将整个生产计划的标准时间和人工费用除以生产计划中的产品数量,得到每个产品的标准工时和标准人工费用。
7. 根据标准工时和标准人工费用,制定相应的生产计划和生产成本预算。
以上是工厂标准工时计算方法的基本步骤,但实际计算中还需要考虑诸多因素,如工艺水平、设备性能、人力资源等。
因此,要制定合理的工厂标准工时计算方法,需要结合实际情况进行分析和调整。
- 1 -。
标准工时计算方法【范本模板】
标准工时计算方法一、目的:规范标准工时制定与修改作业,使标准工时具有完整性,使ERP系统运行之排程合理和成本准确。
二、名词定义:2。
1、标准工时:在特定的工作环境条件下,用规定的作业方法和设备,以普通熟练工作者的正常速度完成一定质量和数量的工作所必需的时间。
2.2、宽放时间:指作业员除正常工作时间之外必须的停顿及休息的时间.包括操作者个人事情引起的延迟,疲劳或无法避免的作业延迟等时间。
对于没有规定发生时间、发生频率、所需时间的不规则要素作业,并不在正常时间范围之内,而属于宽放时间.2.3、标准速度:没有过度体力和精神疲劳状态下,每天能连续工作,只要努力就容易达到标准作业成果的速度.三、标准工时的构成:3。
1、标准时间=正常时间+宽放时间=观测时间*(1+熟练修正数+努力修正数)+观测时间*宽放率3.2、正常时间:3。
2。
1、主体作业时间:按照作业目的进行的作业。
指能创造价值的作业,如改变产品外形,改变产品性能等。
3。
2。
2、副作业时间:与主体作业同步发生,起附属作用。
如取放工具、检查等。
正常时间设定方法如下:直接观测法:秒表观测法;摄影分析法;work sampling法.优点:比较简单;任何人都可以做.缺点:难于跟标准速度相比较,需要评价标准速度;生产之前不能设定.合成法:动作分析法、历史数据法.优点:信赖程度和一贯性高;客观性和普遍性高;不需要评价标准速度;可在生产之前设定;容易消除不必要动作。
缺点:需要教育和训练。
3.3、宽放时间:3。
3。
1、私事宽放时间:作业过程中,满足生理要求的宽放时间,如上厕所,喝水,擦汗。
3.3.2、疲劳宽放时间:为了补偿工作过程中体力和精神疲劳,采取的休息或操作速度减弱的宽放时间。
3.3。
3、特殊宽放:学习宽放、机械干涉宽放、奖励宽放、工厂宽放、其它宽放。
作业宽放时间:补偿作业过程中发生不规则的要素作业。
如用处理不良品等.3。
3。
4、集体宽放时间:集体作业时,对于个体差异产生损失的补偿.如熟练度的差异,工位编排产生的损失等。
精益管理之标准工时
3.0 标准工时的运用 3.1.1 生产效率的计算公式 1 效率=产出/投入; 2 生产效率=产出工时/直接出勤工时 3 工作效率=产出工时/总出勤工时 4 产出工时=产出数量*标准工时/PCS 5 直接出勤工时=直接作业人员的投入工时; 6 总出勤工时=(直接+间接)人员的投入工时;
3.1.2 生产效率的计算案例
标准工时的结构图
标准工时的计算公式
标准工时 = [平均实操工时 *(1+评比系数) ] + (正常时间*宽放系数)
评比系数需要根据测量对象每次确认、宽放系数在 劳动条件和劳动环境不变的情况下只需确认一次.
关键词:评比系数、宽放系数
为什么要进行评比?
所谓“评比”:就是时间研究人员将所观测到 的操作者的操作速度与自己所认为的理想速度 (正常速度)作比较。
2.6 标准工时审核与发行的四个步骤
2.6.1 标准工时测试记录表(IE制作\班组长会签); 2.6.2 工序别标准工时总表(IE课长\制造课长会签); 2.6.3 产品别标准工时总表(工程经理\生产经理会签); 2.6.4 《产品别标准工时总表》经文控统一发行;
目录
什么是标准工时 如何测定标准工时 标准工时的应用
产出工时=? 需求工时=? 需求人数=?
产出工时=1000*20/60=333.33
需求工时=333.3/60%=555.55
需求人数=55.55/2*10=27.53 ≈28人
3.4 设备需求的计算依据
1 设备产出工时=产出数量*设备加工周期时间/PCS; 2 需求工时=设备产出工时/设备稼动率; 3 需求设备=需求工时/出货期限*工作时间; 4 出货期限:24小时之后(1天之后); 5 工作时间:22小时/每天; 6 设备稼动率现状:70%;
标准工时计算
标准工时计算 Revised by Liu Jing on January 12, 2021标准工时计算一、目的:为了更好地控制生产的人员及产量,使之处于最佳配置状态,真正达到“高产、低消耗”之目的。
“ρ”(以单位产量计)。
1、标准工时的计算方法:标准工时的定义:2.1.1 所有产品的标准工时,都是由产品原料加工,组装测试、检查及包装等各道工序所消耗的时间总计,而所谓公司标准则是参照国际标准局有关对人体研究而得出的人类平均劳动强度值,以结合本公司的实际状况(即以公司的一个中等熟练程度的操作工人的操作时间为基础)而定出的标准。
2.1.2 公司的标准工时,最主要由下列几大工序的标准工时组成,即:零件加工、SMT、手插机、过波峰炉、执锡、PCB检测、组立预加工、装配、检查测试、包装这十大工序的标准时间所组成。
而这几大工序的标准工时,又建立在单件标准时间的基础上。
2、基本公式及相关公式:标准工时=实际时间×(1+宽裕率)(一般宽裕率为实际时间的18%~24%)宽裕时间宽裕率= ×100%实际时间工位平均时间:记为“T平”计划内有效工作时间=T平生产计划数生产工位数,记为“N”标准工时N=工位平均时间生产性:当天产量×标准工时×100%生产性=当天工作时间×出勤人数编程效率记作“ρ”实际生产时间(单位产品)×100%ρ=标准工时各操作者过程时间之总和平衡率= ×100%(平衡误差±秒)最大过程时间×操作人数ε完成台数生产达成率= ×100%ε生产预定台数生产线不平衡损失率=1-生产线平衡率不平衡率损失最高的工位时间×合计人数-各工序时间的合计节拍时间TC=实际作业时间/生产量直通良品台数直通良品率= ×100%完成台数当日出勤人员出勤率(就劳率)= ×100%LINE在籍人员标准工时×计划日产量PAC-1(计划人数)= ×(1+宽裕率)(宽裕率设定为15%)日稼动时×有效率×就劳率计划日产量人均日产量=PAC-1。
- 1、下载文档前请自行甄别文档内容的完整性,平台不提供额外的编辑、内容补充、找答案等附加服务。
- 2、"仅部分预览"的文档,不可在线预览部分如存在完整性等问题,可反馈申请退款(可完整预览的文档不适用该条件!)。
- 3、如文档侵犯您的权益,请联系客服反馈,我们会尽快为您处理(人工客服工作时间:9:00-18:30)。
4
表單填寫
成型製程
成型速率測定表
本單使用於:□第一次訂定 ●再修訂
案例:導光板成型Gemini IRDA Lens
成型效率訂定
8月23日 2005 年
說明:測定結果
1. 成型機台:
50 TON
GP-07 GP-59 GP-88 GP-89
2. 料
號: SMT580501J
核
准:
審
核:
初
核:
製 表: 簡益平
保存期限:一年
表單編號:IT03F09(04)
文件等級:密件
5
計算公式
一般加工製程
工序1
工序2
工序3
工序4
工序5
1人
27 sec/pc
A 27 sec/pc
1人
25 sec/pc
B 25 sec/pc
1人
30 sec/pc
C 30 sec/pc
3人
72 sec/pc
上下治具 檢查,擦拭
上下治具
T2
T3
人員週期
設備週期 = T1 + T2 人員週期 = T2 + T3 作業週期 = Max( T1 + T2 , T2 + T3 ) 每時產能 = 3600 / [Max(T1 + T2 , T2 + T3 )]
7
注意事項
一般加工製程
必須將所有之作業考量在內,特別是非 每pc執行之作業,但不含不正常作業部 份.
來料單 位(大片)
第一次 銑切單 位(中片)
第二次 銑切單 位(小片)
8
補充說明
一般加工製程
1. 多人一機 案例: 螺帽埋置需有2人以上放置螺帽.
設備 人員A 人員B
熱熔
人工
熱熔
人工
T1 取出 置放螺帽 T2 T3
檢查 取出 置放螺帽 T4
置放螺帽 放入
T5
T6
置放螺帽 放入
設備週期 = T1 + Max( T2 + T3 , T5 + T6 ) 人員A週期 = T2 + T3 + T4 人員B週期 = T5 + T6 作業週期 = Max( T1 , T4 ) + Max( T2 + T3 , T5 + T6 )
人工台 人工開關門
人工台 手臂取出,但人員控 制手臂將螺帽置入
成型製程
自動台 手臂取出,人 員隨台作業
自動台 360度手臂取出
自動台 手臂取出
1
自動台
成型製程
定義:無人隨台顧台,產品為頂出,手臂夾取等方式取出
開模 取出 關模
T1
T2
T3
注塑
T4
完整週期
開模 取出 關模
T1
T2
T3
完整週期
注塑
T4
標準工時(循環時間) = T1 + T2 + T3 + T4
5 T3
關門 剪膠
2
4
T4
T8
檢包
6 T9
開門
2 T1
人機比 = 人時 : 機時 = 22 : 40 = 1 : 1.81 人時 = T1 + T2 + T3 + T4 + T8 + T9 = 22 機時 = T1 + T2 + T3 + T4 + T5 + T6 + T7 = 40
此時,人員閒置時間過長,需加以改善,改善方式有兩個方向: 1. 縮短機器時間 : 重點在於縮短開模,關模,注塑之時間. 2. 增加人員作業時間 : 下製程之作業可拉至成型(CFM),.
10
補充說明
一般加工製程
3. 無需人員操作 案例:人員只需設定參數,或運送至該處. A). 只需運送:將運送時間攤換成每pc所需之時間,並將時間 加到上一站之作業時間.(有時可能為後一站) B). 需設定參數:將設定與運送時間攤換成每pc所需之時間, 並將時間加到上一站之作業時間.(有時可能為後一站)
一般加工製程
EX:Tray盤每盤20pc,作業時間 10 sec; 取放Tray盤時間 20 sec (動作可能包含移動空Tray盤到旁邊, 取新Tray到面前)
3. 循環時間: 42.7
4. 標準速率: 84.3 *4
秒 只/時
請將前述所提之 標準工時計算結
果填入此欄
※5. 成型速率: 75.9 *4
只/時 (標準速率╳90%╳良率權數)
6. 修訂次數:第
2
次
※7.良率權數:
1
(本次修訂前的成型速率:197.6 * 4 只/時.前次修訂日期:2004年 9 月13 日)
有時入庫單位並非以最終成品之單位 來計算. (舉例說明,薄膜先裁切成兩大 片,這時是以中片入庫還是小片.)
檢驗部分需確認是否為破壞性檢驗. (舉例說明,Hard Coating需進行百格 檢驗,其每盤有60pc,每爐5盤,每盤需 抽 2 pc測試,則其每爐之產出應為290 pc,而非 300 pc,每爐工時需用 290 pc 來分擔計算.)
9
補充說明
一般加工製程
2. 多機一人 案例:壓合時, 一人同時操作兩台機台.
設備A 設備B 人員
取放 T1
取放 T1
壓合 T2 取放 T1
檢查 取放 T3 T1
取放
壓合 T2
檢查 取放 T3
壓合 取放
檢查 取放
壓合 檢查
設備週期 = T1 + Max(T2, T3+T1+T3) 人員週期 = T1 + T3 作業週期 = Max( 人員週期 , 設備週期/2 )
D 24 sec/pc
1人
26 sec/pc
E 26 sec/pc
標準工時 = Max(A,B,C,D,E) * 總投入人數 = 30 * 7 = 210 sec/pc
6
有使用設備狀況
一般加工製程
機台作業時間 上下治具 機台作業時間 上下治具 機台作業時間 上下治具
T1
T2
設備週期
檢查,擦拭
上下治具 檢查,擦拭
T4
Hale Waihona Puke T8T9T1
有同步工時產生,需進 行人機配合分析
標準工時(循環時間)=T1+T2+T3+T4+Max(T5+T6+T7,T8+T9)
3
人機配合分析
成型製程
開模開門 取出
22
3
T7 T1 T2
置入
5 T3
關門 關模
22 T4 T5
注塑
24 T6
開模 開門
22 T7 T1
開門 取出
2
3
T1 T2
置入
4. 需分模號:需將分模號之時間分攤到每pc. 案例:銑膠有分模號之情形 EX:每盤24pc,銑膠時間 5 sec;分模號時間 24 sec/盤 銑膠C/T = 銑膠時間 + 分模號時間 / 數量
= 5 + 24 / 24 = 6 sec/pc
11
補充說明
5. 元件是用載具承裝時(或類似情況): 需將拿取與放置載具之時間分攤
2
人工台
成型製程
定義:有人員隨台顧台,產品為人工方式取出,人員需進行開 關門之動作,置入皮革,螺帽等元件,通常成型機台作業時,人 員會伴隨進行其他作業.
開模 開門 取出 置入 關門 關模 注塑 開模 開門
T7 T1 T2 T3
T4 T5
T6
T7 T1
開門 取出 置入 關門 剪膠 檢包
開門
T1 T2 T3