PCB选择性焊接技术难点
pcb阻焊常见缺陷原因与措施
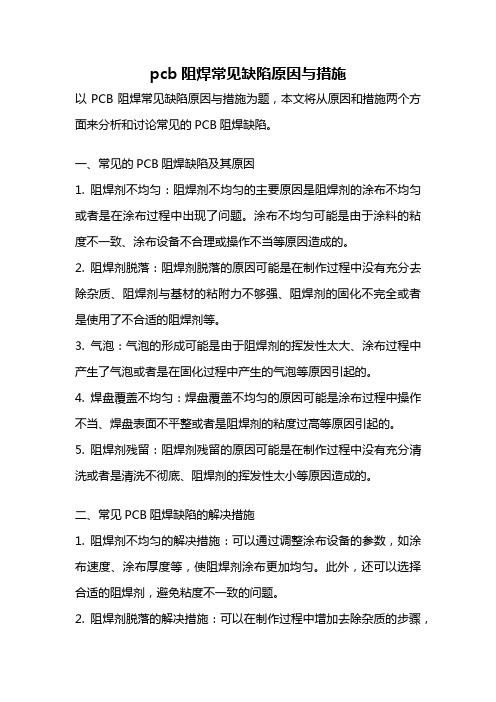
pcb阻焊常见缺陷原因与措施以PCB阻焊常见缺陷原因与措施为题,本文将从原因和措施两个方面来分析和讨论常见的PCB阻焊缺陷。
一、常见的PCB阻焊缺陷及其原因1. 阻焊剂不均匀:阻焊剂不均匀的主要原因是阻焊剂的涂布不均匀或者是在涂布过程中出现了问题。
涂布不均匀可能是由于涂料的粘度不一致、涂布设备不合理或操作不当等原因造成的。
2. 阻焊剂脱落:阻焊剂脱落的原因可能是在制作过程中没有充分去除杂质、阻焊剂与基材的粘附力不够强、阻焊剂的固化不完全或者是使用了不合适的阻焊剂等。
3. 气泡:气泡的形成可能是由于阻焊剂的挥发性太大、涂布过程中产生了气泡或者是在固化过程中产生的气泡等原因引起的。
4. 焊盘覆盖不均匀:焊盘覆盖不均匀的原因可能是涂布过程中操作不当、焊盘表面不平整或者是阻焊剂的粘度过高等原因引起的。
5. 阻焊剂残留:阻焊剂残留的原因可能是在制作过程中没有充分清洗或者是清洗不彻底、阻焊剂的挥发性太小等原因造成的。
二、常见PCB阻焊缺陷的解决措施1. 阻焊剂不均匀的解决措施:可以通过调整涂布设备的参数,如涂布速度、涂布厚度等,使阻焊剂涂布更加均匀。
此外,还可以选择合适的阻焊剂,避免粘度不一致的问题。
2. 阻焊剂脱落的解决措施:可以在制作过程中增加去除杂质的步骤,确保基材的表面干净;同时,选择具有较强粘附力的阻焊剂,并确保其固化完全。
3. 气泡的解决措施:可以选择挥发性较小的阻焊剂,减少气泡的产生;在涂布过程中要注意操作,避免气泡的形成;在固化过程中要控制好温度和时间,确保气泡能够顺利排出。
4. 焊盘覆盖不均匀的解决措施:可以通过调整阻焊剂的粘度,使其更易于涂布;此外,还可以选择合适的涂布工艺和设备,确保阻焊剂能够均匀地覆盖在焊盘表面。
5. 阻焊剂残留的解决措施:在制作过程中要充分清洗阻焊剂,确保其完全去除;可以选择具有较大挥发性的阻焊剂,加快其挥发速度,减少残留。
PCB阻焊常见缺陷的原因有阻焊剂不均匀、阻焊剂脱落、气泡、焊盘覆盖不均匀和阻焊剂残留等。
pcb板焊接注意事项
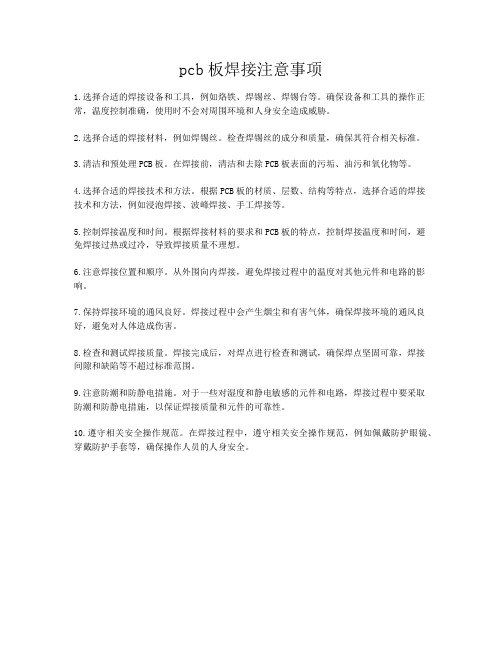
pcb板焊接注意事项
1.选择合适的焊接设备和工具,例如烙铁、焊锡丝、焊锡台等。
确保设备和工具的操作正常,温度控制准确,使用时不会对周围环境和人身安全造成威胁。
2.选择合适的焊接材料,例如焊锡丝。
检查焊锡丝的成分和质量,确保其符合相关标准。
3.清洁和预处理PCB板。
在焊接前,清洁和去除PCB板表面的污垢、油污和氧化物等。
4.选择合适的焊接技术和方法。
根据PCB板的材质、层数、结构等特点,选择合适的焊接
技术和方法,例如浸泡焊接、波峰焊接、手工焊接等。
5.控制焊接温度和时间。
根据焊接材料的要求和PCB板的特点,控制焊接温度和时间,避
免焊接过热或过冷,导致焊接质量不理想。
6.注意焊接位置和顺序。
从外围向内焊接,避免焊接过程中的温度对其他元件和电路的影响。
7.保持焊接环境的通风良好。
焊接过程中会产生烟尘和有害气体,确保焊接环境的通风良好,避免对人体造成伤害。
8.检查和测试焊接质量。
焊接完成后,对焊点进行检查和测试,确保焊点坚固可靠,焊接
间隙和缺陷等不超过标准范围。
9.注意防潮和防静电措施。
对于一些对湿度和静电敏感的元件和电路,焊接过程中要采取
防潮和防静电措施,以保证焊接质量和元件的可靠性。
10.遵守相关安全操作规范。
在焊接过程中,遵守相关安全操作规范,例如佩戴防护眼镜、穿戴防护手套等,确保操作人员的人身安全。
PCB板焊接缺陷产生的原因及解决措施
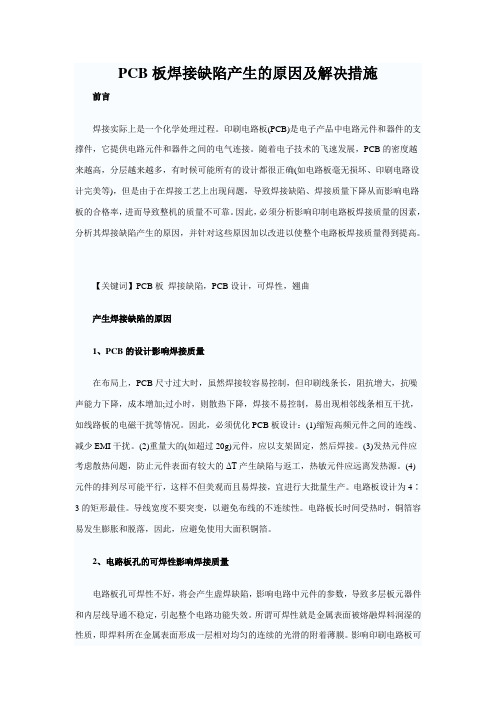
PCB板焊接缺陷产生的原因及解决措施前言焊接实际上是一个化学处理过程。
印刷电路板(PCB)是电子产品中电路元件和器件的支撑件,它提供电路元件和器件之间的电气连接。
随着电子技术的飞速发展,PCB的密度越来越高,分层越来越多,有时候可能所有的设计都很正确(如电路板毫无损坏、印刷电路设计完美等),但是由于在焊接工艺上出现问题,导致焊接缺陷、焊接质量下降从而影响电路板的合格率,进而导致整机的质量不可靠。
因此,必须分析影响印制电路板焊接质量的因素,分析其焊接缺陷产生的原因,并针对这些原因加以改进以使整个电路板焊接质量得到提高。
(|NO.1441)【关键词】PCB板焊接缺陷,PCB设计,可焊性,翘曲(|NO.1441)产生焊接缺陷的原因(|NO.1441)1、PCB的设计影响焊接质量(|NO.1441)在布局上,PCB尺寸过大时,虽然焊接较容易控制,但印刷线条长,阻抗增大,抗噪声能力下降,成本增加;过小时,则散热下降,焊接不易控制,易出现相邻线条相互干扰,如线路板的电磁干扰等情况。
因此,必须优化PCB板设计:(1)缩短高频元件之间的连线、减少EMI干扰。
(2)重量大的(如超过20g)元件,应以支架固定,然后焊接。
(3)发热元件应考虑散热问题,防止元件表面有较大的ΔT产生缺陷与返工,热敏元件应远离发热源。
(4)元件的排列尽可能平行,这样不但美观而且易焊接,宜进行大批量生产。
电路板设计为4∶3的矩形最佳。
导线宽度不要突变,以避免布线的不连续性。
电路板长时间受热时,铜箔容易发生膨胀和脱落,因此,应避免使用大面积铜箔。
(|NO.1441)2、电路板孔的可焊性影响焊接质量(|NO.1441)电路板孔可焊性不好,将会产生虚焊缺陷,影响电路中元件的参数,导致多层板元器件和内层线导通不稳定,引起整个电路功能失效。
所谓可焊性就是金属表面被熔融焊料润湿的性质,即焊料所在金属表面形成一层相对均匀的连续的光滑的附着薄膜。
影响印刷电路板可焊性的因素主要有:(1)焊料的成份和被焊料的性质。
浅析印制电路板的焊接缺陷(推荐5篇)

浅析印制电路板的焊接缺陷(推荐5篇)第一篇:浅析印制电路板的焊接缺陷浅析印制电路板的焊接缺陷【摘要】随着我国科学技术的不断发展,电子行业在我国迅速崛起,电子产品风靡全国。
印制电路板作为电子产品中的一个关键零部件,其设计和制造过程得到了电子产品制造公司的高度重视。
本文结合自己多年的工作经验,着重对印制电路板的焊接工艺缺陷进行简要分析。
【关键词】印制电路板;焊接;工艺缺陷引言焊接工艺从本质上讲属于一种典型的化学处理工艺,不同的焊接对象需要选择不同的焊接工艺,不同的焊接工艺所采用的化学原理也不相同。
印制电路板的主要作用是良好的对电子产品中所用到的电子元器件进行连接,使它们形成一个稳定、完整的系统,进而达到电子产品的设计要求。
在我国电子科技飞速发展的大背景下,印制电路板的结构变得越来越复杂,焊接工艺作为印制电路板在制造过程中的关键性工序之一,对整个电路板的整体性能起着决定性的作用,我们必须加大对印制电路板在制造过程中焊接工艺的重视,认真分析焊接缺陷,提高焊接质量,进而提高印制电路板的合格率。
1、由印制电路板的设计不合理,造成的焊接缺陷众所周知,安装在不同电子产品中的印制电路板其大小规格也各不相同,有的稍微大一点,有的则要小一点,电路板的大小会对后期制作过程中的印制电路板焊接工艺造成严重的影响,对于具体印制电路板而言,其大小和形状设计是由很多因素决定的。
当印制电路板的尺寸较大的时候,焊接工艺在执行过程中相对于较小的电路板而言容易控制并保证焊接质量,但是较大的印制电路板在焊接过程中会形成很长的焊接线条,而我们知道焊接线条的长短会直接影响印制电路板的阻抗和声抗,从而影响印制电路板的整体性能。
此外,焊接线条的增长还会加大印制电路板的生产成本,影响印制电路板生产企业的经济效益。
当印制电路板的形状较小的时候,直接的就会加大印制电路板在焊接过程中的焊接难度,在电路板的焊接过程中,一块电路板需要焊接的部位通常情况下不止一个,在这种情况下,如果印制电路板的形状较小,还会使相邻焊接线条之间形成相互干扰,影响电路板的综合性能,严重的时候会直接导致电路板报废。
pcb板焊接技巧

pcb板焊接技巧PCB(Printed Circuit Board)是电子产品中广泛应用的重要组成部分之一。
在PCB的制作过程中,焊接是关键步骤之一,对于保证电路的稳定性和可靠性至关重要。
本文将介绍一些关于PCB板焊接的技巧,帮助读者提高焊接质量和效率。
一、准备工作在进行PCB板的焊接之前,先要做好准备工作,确保焊接过程顺利进行。
首先,选用适合的焊锡丝和焊锡膏,根据电路板的要求选择合适的焊锡直径和锡量。
其次,准备好必要的焊接工具,如烙铁、焊锡笔等。
确保工具干净,尖端锐利,以便进行精确的焊接操作。
二、焊接技巧1. 温度控制焊接时的温度控制非常重要。
过高的温度可能导致焊锡迅速氧化,影响焊接质量,甚至烧毁电路板。
而过低的温度则会导致焊锡无法充分熔化,影响焊点的牢固性。
因此,在焊接过程中,要控制好烙铁的温度,确保烙铁的温度在合适的范围内。
2. 焊锡膏的使用使用适量的焊锡膏有助于提高焊接的质量。
焊锡膏可以增加焊锡的润湿性,使焊锡更容易均匀地覆盖焊点。
在使用焊锡膏时,注意不要使用过多,以免过多的焊锡膏残留在焊点附近,影响电路的正常工作。
3. 焊点的处理焊点的处理也是保证焊接质量的重要环节。
在焊接之前,要确保焊点的表面干净、无污染。
可以使用酒精擦拭焊点表面,去除表面的油污和杂质。
同时,焊点的大小也需要适度,过大的焊点可能会引起短路或不良接触,过小的焊点则可能会导致焊接不牢固。
4. 焊接技巧在焊接过程中,要掌握一些技巧,以提高焊接的效率和质量。
首先,要熟练掌握烙铁的使用方法,学会正确拿捏烙铁,保持烙铁与焊点的接触时间适中。
其次,可以使用辅助工具,如焊锡架、镊子等,来帮助焊接操作,提高精度和稳定性。
三、常见问题及解决办法1. 焊接不牢固:可能是焊锡膏使用过少、温度过低或焊点处理不当所导致。
可以尝试增加焊锡膏的使用量,提高烙铁的温度,或重新处理焊点表面。
2. 短路或断路:可能是焊点大小不合适、焊锡残留过多或焊接位置不准确所导致。
电子电路手工焊接技术焊接方法与焊接缺陷
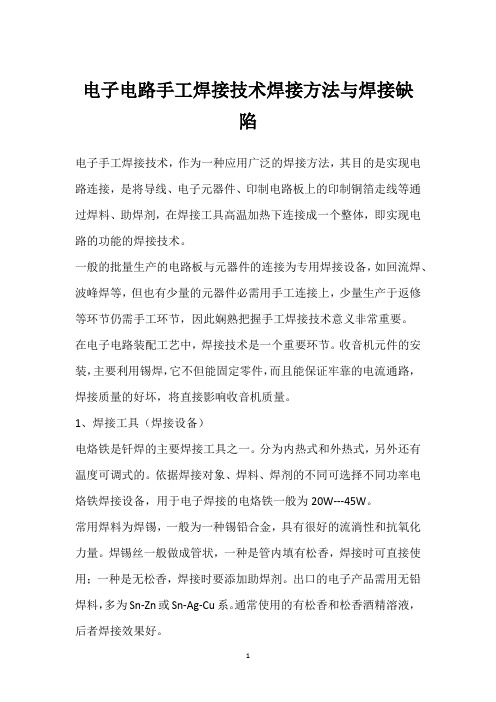
电子电路手工焊接技术焊接方法与焊接缺陷电子手工焊接技术,作为一种应用广泛的焊接方法,其目的是实现电路连接,是将导线、电子元器件、印制电路板上的印制铜箔走线等通过焊料、助焊剂,在焊接工具高温加热下连接成一个整体,即实现电路的功能的焊接技术。
一般的批量生产的电路板与元器件的连接为专用焊接设备,如回流焊、波峰焊等,但也有少量的元器件必需用手工连接上,少量生产于返修等环节仍需手工环节,因此娴熟把握手工焊接技术意义非常重要。
在电子电路装配工艺中,焊接技术是一个重要环节。
收音机元件的安装,主要利用锡焊,它不但能固定零件,而且能保证牢靠的电流通路,焊接质量的好坏,将直接影响收音机质量。
1、焊接工具(焊接设备)电烙铁是钎焊的主要焊接工具之一。
分为内热式和外热式,另外还有温度可调式的。
依据焊接对象、焊料、焊剂的不同可选择不同功率电烙铁焊接设备,用于电子焊接的电烙铁一般为20W---45W。
常用焊料为焊锡,一般为一种锡铅合金,具有很好的流淌性和抗氧化力量。
焊锡丝一般做成管状,一种是管内填有松香,焊接时可直接使用;一种是无松香,焊接时要添加助焊剂。
出口的电子产品需用无铅焊料,多为Sn-Zn或Sn-Ag-Cu系。
通常使用的有松香和松香酒精溶液,后者焊接效果好。
另一种焊剂是焊锡膏,是酸性焊剂,对金属有腐蚀作用,一般不采纳。
2、焊接方法一般采纳直径1.2—1.5mm的焊锡丝,焊接时左手拿焊锡丝,右手拿电烙铁的焊接方法进行焊接。
在烙铁接触焊点的同时送上焊锡,焊锡的量要适量。
太多易引起搭焊短路,太少元件又不坚固。
烙铁头放在焊件上后即放入焊锡丝。
焊接时焊锡在焊接面上集中达到预期范围后马上拿开焊锡丝并移开电烙铁。
焊接操作时,烙铁温度过低,烙铁与焊接点接触时间太短,热量供应不足,焊点锡面不光滑,结晶粗脆,象豆腐渣一样,那就不坚固,形成虚焊和假焊。
反之,若时间过长(一般不超过3秒),温度过高,焊锡易流散,使焊点锡量不足,也简单不牢,还可能消失烫坏电子元件及印刷电路板。
PCB缺点及产生原因介绍防焊的缺陷及成因
PCB缺点及产生原因介绍防焊的缺陷及成因PCB(Printed Circuit Board)是一种非常重要的电子组件,被广泛应用于电子产品中。
然而,尽管 PCB 有许多优点,但也存在一些缺点。
本文将介绍 PCB 的缺点及其产生原因,并重点讨论 PCB 的防焊缺陷及其成因。
首先,让我们先看一下PCB的一些常见缺点。
1.昂贵:相比于其他电子组件,制造PCB的成本相对较高。
这主要是因为PCB制造涉及到多道工序,包括涂覆、光刻、蚀刻等,需要用到昂贵的设备和材料。
2.环境影响:在PCB的制造过程中,常用的化学物质和材料可能会对环境造成污染。
例如,一些化学物质可能具有毒性,对环境和人类健康造成潜在的危害。
3.电磁干扰:由于PCB的布线是通过导线连接的,电流会产生磁场,这可能会引起电磁干扰,影响其他设备的正常运行。
4.重量和体积限制:由于PCB是一种平面结构,电子元件需要安装在PCB上,这限制了PCB在重量和体积方面的发展。
接下来,我们将重点讨论PCB的防焊缺陷及其成因。
防焊是PCB制造过程中非常重要的一步,其目的是保护PCB上的元件,使其能够正常工作。
然而,防焊过程中可能会出现一些缺陷,破坏PCB的性能和可靠性。
以下是一些常见的防焊缺陷:1.焊接剂残留:在防焊过程中使用的焊接剂可能会残留在PCB上,如果没有完全清除干净,会影响电路的连接和信号传输。
2.焊接质量不佳:焊接过程中温度、时间或压力不正确,导致焊点质量不佳。
例如,焊接温度过高会导致焊接过度,焊接温度过低则会导致焊点不牢固。
3.焊锡球或锡桥:在焊接过程中,焊锡球或锡桥可能会形成在不该存在的地方,导致焊点短路或连接不良。
这些防焊缺陷的产生原因可能有以下几个方面:1.设计问题:如果PCB的设计没有考虑到防焊的问题,如焊盘设计不合理、间距太小等,就容易导致防焊缺陷的产生。
2.操作不当:防焊过程需要严格控制温度、时间和压力等参数,如果操作人员缺乏经验或不认真执行相关操作规程,就容易导致防焊缺陷的产生。
pcb工艺技术难题
pcb工艺技术难题PCB工艺技术在电子产品制造中起着重要的作用,是电子产品的核心组件之一。
然而,随着电子产品的不断迭代更新,PCB工艺技术也面临着一些难题。
本文将就PCB工艺技术中存在的难题进行探讨。
首先,PCB工艺技术难题之一是高密度布线技术。
随着电子产品的不断小型化和功能强大化,布线的要求也越来越高。
高密度布线技术要求在有限的空间内,将尽可能多的导线精细地布置在限定的PCB板上。
这需要在PCB板上设计复杂的线路,提高PCB板上的线路密度。
然而,高密度布线技术面临着导线之间的互相干扰、信号串扰等问题,导致信号质量下降,对信号的传输效果造成影响。
其次,PCB工艺技术中还存在着材料选型的难题。
PCB板是由多种材料叠压而成,其中最重要的是基材和覆铜,而这两种材料的选用对电子产品的性能和稳定性具有重要影响。
目前市场上存在着众多不同类型的材料供选择,如FR-4、CEM-3等,但每种材料都有其特殊的特性和限制条件,如导电性、耐热性、耐磨性等。
因此,在PCB工艺技术中,如何选择合适的材料,以及如何将不同材料进行叠压,成为了制造商面临的难题。
另外,PCB工艺技术中也存在着多层板的制造难题。
多层板是利用多层基材叠加而成的,可以提供更多的布线空间,使得电路更加复杂和紧凑。
然而,制造多层板需要多次压制、复杂的布线和连接技术,因此制造成本较高。
此外,多层板还面临着层间连接与测试技术的难题,如层间间距的控制、层间故障的检测等。
最后,PCB工艺技术中也存在着封装技术的难题。
封装是将电子元器件焊接到PCB板上的过程,直接影响着电子产品的性能和可靠性。
目前,常见的封装技术有BGA、LGA、QFN 等。
这些封装技术要求将微小的引脚精确地焊接到PCB板上,保证电子元器件与PCB之间的连接可靠性。
然而,封装技术面临着引脚数量多、引脚间距小、焊接工艺复杂等问题,给制造商带来了一定的挑战。
综上所述,PCB工艺技术在电子产品制造过程中面临着高密度布线技术、材料选型、多层板制造和封装技术等难题。
PCB缺点及产生原因介绍防焊的缺陷及成因
PCB缺点及产生原因介绍-防焊的缺陷及成因防焊,又称绿漆,油墨,当然,不是所有的防焊油墨都是绿色的,也有蓝色,黑色,红色等等。
缺点名称:油墨起泡缺点图片:缺点特征:油墨与铜面分离,看去时颜色比原本的颜色淡一些规格:按客户规格无客户规格按厂内规格,即:1.相临两条线路不允许2.隔绝电性间距其缩减不可超过20%可允收3.每板面只允许三处,起泡处长10mil处理分法:造成的可能原因:1.板面不洁或残留水气(SM)2.烤板时间太长或温度太高度(SM)3.烤板时间太短或温度太低(SM)4.油墨与铜面之间热胀冷缩系数不同(HA)缺点名称:Undercut 缺点图片: 缺点特征:类似油墨起泡,即油墨与铜面分离了,看去淡淡的绿色(一般在pad四周)规格:按客户规格,无客户规格按厂内规格即:锡面板:不允许拉脱且须不可≦2mil化金(BGA)目视且≦2 mil化金(按键)目视且≦2 mil化金(SMT)目视且≦2 mil化金(其它)目视且≦2 mil造成的可能原因:处理分法:1.板面不洁或残留水气(SM)2.烤板时间太长或温度太高(SM)3.烤板时间太短或温度太低(SM)4.油墨与铜面之间热胀冷缩系数不同(SM)5.油墨附着力不好,拖锡时造成Undercur(HA/VI)缺点名称:油墨气泡缺点图片: 缺点特征:线路边上像一个个水泡一样的规格:按客户规格,无客户规格则按厂内规格,即:1.气泡不影响间距的50%2.每单面不可超过5处3.每处长40mil MAX造成的可能原因:1.油墨搅拌和放置时间不够2.印刷速度大快3.油墨粘度太高4.刮刀不锐利5.印刷和放置不够6.油墨太厚7.板面预热温度太低,使油墨中的溶剂无法完全挥发而形成气泡处理分法:超出规格报废,未超出规格可以过缺点名称:据焊下发黑缺点图片: 缺点特征:大铜箔区域,铜上面有黑的东西或氧化造成,油墨下有一快黑,看去黑黑的规格:按客户规格,无客户规格按厂内规格,即:1.长度不可超过50mil2.每面不可超过5点3.不影响附着力造成的可能原因:1.AOI测试机记号未洗掉2.板面清洁不干净或氧化3.清刷和停留太久才印刷4.蚀刻液酸气外溅5.COATING第二面放置时间过久处理分法:未超出规格可以过,超出规格可以补油墨,其余报废,超过补油墨规格报废缺点名称:油墨杂质缺点图片: 缺点特征:油墨有脏的东西印到板子上规格:按客户规格,无客户规格则按厂内规格,即:油墨杂质最大不可大于0.05",不能横跨两条线路,每面不可超过3处,残渣不允许造成的可能原因:1.前处理没处理干净2.环境不洁3.油墨中有杂物处理分法:未超出规格可以过,超出规格刮掉补油墨,但必符合补油墨规格,超出补油墨规格报废.但在实际检验中,如果杂质看起来比较不明显,即使超出两条线路也可以过(因为它对功能并没有影响)如此板也可以直接让它过缺点名称:假性露铜缺点图片: 缺点特征:油墨厚度太薄,导致板面上看去仿佛露铜一样规格:按客户规格,无客户规格则按厂内规格,即:1.不允许露铜2.须<100mil3.一面小于10点造成的可能原因:1.压力太小2.速度大快3.刮刀太浅4.刮刀角度大小5.刮刀内长度不够6.油墨浓度大高7.网板间距太大处理分法:未超出规格可以过,超出规格可以补油墨,但须符合补油墨规格,超出补油墨规格报废1.C/S面修补不可多于5处2.修补区面积长度不可大于1",宽度不可大于0.06"缺点名称:盖绿缺点图片: 缺点特征:PAD上有油墨很有规则的盖到上面去规格:按客户规格,无客户规格则按厂内规格,即:1.拒焊上环形圈至少保留0.002"未盖拒焊2.绿漆上SMD PAD,尚未侵犯到SMD长边3mil,短边2mil且不可超过长度的20%,取其小造成的可能原因:1.底片对偏2.显影未净3.底片缩拉4.因板弯造成对片偏移5.修补污染6.定位PIN松动造成印偏7.乳济脱落8.因板弯造成EP偏移处理分法:超出规格报废,未超出规格可以过缺点名称:油墨上PAD 缺点图片: 缺点特征:PAD上本来应是铜/锡/金的,现在没有了,而是一点油墨在上面规格:按客户规格,无客户规格按厂内规格,即:1.拒焊上环形圈至少保留0.002"未盖拒焊2.绿漆不许进孔但非插件焊孔则不在此限,可允收3.绿漆尚未侵犯到SMD长边3mil,短边2mil且不可超过长度的20%,取其小造成的可能原因:1.油墨反沾2.显影不净处理分法:未超出规格可以过,超出规格几个可以刮掉修补,多的就报废缺点名称: 显影未尽 缺点图片:缺点特征:PAD 上本来应是露铜,喷锡或化金的,而现在有油墨在上面,造成没有露铜,喷不上锡,化不上金规格:按客户规格,无客户规格按厂内规格,即: 不允许造成的可能原因:1.底片问题(遮亮度不够本.Spel ;3.57以上(A/W)2.曝光能量太高3.显影速度太快4.显影机喷嘴堵塞或压力不足5.显影液含水量太高(不洁)6.显影液浓度太低7.显影温度太低8.短烤抽风不对9.短烤太短,时间过长 10.印刷和放置过长 11.油墨过期 12.主剂硬化剂不对 13.稀释液不对处理分法:如果只有几个PAD 显影未净,可以把油墨刮掉拖锡(锡面板)金面板(补金水)多的就报废缺点名称:防焊污染缺点图片: 缺点特征:不该有油墨的地方有油墨不规则的污染规格:按客户规格,无客户规格按厂内规格,即:1.拒焊上环形圈至少保留0.002"未盖拒焊2.绿漆不许进孔但非插件焊孔则不在此限,可允收3.绿漆尚未侵犯到SMD长边3mil,短边2mil且不可超过长度的20%,取其小造成的可能原因:1.印完油墨后不慎碰触2.显影液不干净处理分法:未超出规格可以过,超出规格几个可以刮掉修补,多的就报废缺点名称:修补油墨污染缺点图片: 缺点特征:补油墨时,使不该有油墨的地方有油墨污染上去规格:按客户规格,无客户规格按厂内规格,即:1.拒焊上环形圈至少保留0.002"未盖拒焊2.绿漆不许进孔但非插件焊孔则不在此限,可允收3.绿漆尚未侵犯到SMD长边3mil,短边2mil且不可超过长度的20%,取其小造成的可能原因: 人为处理分法:未超出规格可以过,超出规格几个可以刮掉修补,多的就报废缺点名称:油墨未烘干缺点图片: 缺点特征:用手一刮就刮掉规格:不允许造成的可能原因:1.人为疏忽2.烘烤时间即温度不足3.烤箱通风循环不良4.烤板时间板子放置太多或油墨大厚处理分法:可以加烤,加烤不掉就报废缺点名称:拒焊线脱落缺点图片: 缺点特征:孔与孔之间的油墨掉掉了,露出铜的颜色规格:按客户规格,无客户规格按厂内规格,即:不允许造成的可能原因:1.间距太小2.油墨附着力不好3.曝光能量太强4.显影速度太慢5.显影压力太大6.显影浓度太高7.显影温度太高8.线框太小处理分法: 报废缺点名称:色泽不均缺点图片: 缺点特征:油墨有一些地方太厚,有一些地方太薄,看去颜色不一样规格:不允许造成的可能原因:1.刮刀肉太长2.底座有问题3.刮刀肉太软4.刮刀太深或太浅5.油墨太粘6.刮刀肉脱落7.电木板太低8.刮刀未研磨锋利9.网版间距太高10.速度太快11.刮刀位置距离不够12.粘板刮刀柄长短处理分法: 很明显报废。
PCB焊点焊接缺陷原因分析
Ke y wo r d Co mp o u n d ; Su r f a c e F r e e En e r g y . Ni c k e l L a y e r Co r r o s i o n ; E u t e c t i c So l d e r ; Si l v e r
连接 在 起 , 而 具仃 良好 的导 电性 能 。
鲜 活 的铜 面 焊接 效 果 较 好 但 存 放 时 问较 短 ,焊 接 后 铜 面 与焊 料锡 界面 合 金 共 化 物 ( I MC)增 长 较 快 ,严 重影 响焊 点 靠 性 !各 种P CB 表 面处 理方 式部 只有 个 H的,提 ‘ 或 保证 焊接 后焊 点可靠 性 1
PCB s o l de r we l di ng de f e c t c a us e a na l y s i s
・
C HE N Qi a n g W A N G Y i — x i o n g
Abs t r a ct Th e r e ma y b e a l o t c a u s e s o f P CB s o l d e r we l d i n g d e f e c t s .Ho we v e r i f y o u c o n s i d e r f r o m t h e
1 前 言
焊 接 足指 被焊 接 的 个 物件 ,通 过 加 热 或 加压 使 个 相 旧材质 的物 体或 同材 质 的物体达 到 原了 问
的结合 ,m J 形 成永 久性连 接 的工艺过 程称 之为焊 接 。 焊 接 过 程 巾 ,物 体 焊 料 熔 化 形 成 熔 融 区域 ,
焊 料 冷 却 凝 后便 形 成材 料 之 间 的连 接 。这 一 过
- 1、下载文档前请自行甄别文档内容的完整性,平台不提供额外的编辑、内容补充、找答案等附加服务。
- 2、"仅部分预览"的文档,不可在线预览部分如存在完整性等问题,可反馈申请退款(可完整预览的文档不适用该条件!)。
- 3、如文档侵犯您的权益,请联系客服反馈,我们会尽快为您处理(人工客服工作时间:9:00-18:30)。
PCB选择性焊接技术难点
在PCB电子工业焊接工艺中,有越来越多的厂家开始把目光投向选择焊接,选择焊接可以在同一时间内完成所有的焊点,使生产成本降到最低,同时又克服了回流焊对温度敏感元件造成影响的问题,选择焊接还能够与将来的无铅焊兼容,这些优点都使得选择焊接的应用范围越来越广。
选择性焊接的工艺特点
可通过与波峰焊的比较来了解选择性焊接的工艺特点。
两者间最明显的差异在于波峰焊中PCB的下部完全浸入液态焊料中,而在选择性焊接中,仅有部分特定区域与焊锡波接触。
由于PCB本身就是一种不良的热传导介质,因此焊接时它不会加热熔化邻近元器件和PCB区域的焊点。
在焊接前也必须预先涂敷助焊剂。
与波峰焊相比,助焊剂仅涂覆在PCB下部的待焊接部位,而不是整个PCB。
另外选择性焊接仅适用于插装元件的焊接。
选择性焊接是一种全新的方法,彻底了解选择性焊接工艺和设备是成功焊接所必需的。
选择性焊接的流程
典型的选择性焊接的工艺流程包括:助焊剂喷涂,PCB预热、浸焊和拖焊。
助焊剂涂布工艺
在选择性焊接中,助焊剂涂布工序起着重要的作用。
焊接加热与焊接结束时,助焊剂应有足够的活性防止桥接的产生并防止PCB产生氧化。
助焊剂喷涂由X/Y机械手携带PCB通过助焊剂喷嘴上方,助焊剂喷涂到PCB待焊位置上。
助焊剂具有单嘴喷雾式、微孔喷射式、同步式多点/图形喷雾多种方式。
回流焊工序后的微波峰选焊,最重要的是焊剂准确喷涂。
微孔喷射式绝对不会弄污焊点之外的区域。
微点喷涂最小焊剂点图形直径大于2mm,所以喷涂沉积在PCB上的焊剂位置精度为±0.5mm,才能保证焊剂始终覆盖在被焊部位上面,喷涂焊剂量的公差由供应商提供,技术说明书应规定焊剂使用量,通常建议 100%的安全公差范围。
预热工艺
在选择性焊接工艺中的预热主要目的不是减少热应力,而是为了去除溶剂预干燥助焊剂,在进入焊锡波前,使得焊剂有正确的黏度。
在焊接时,预热所带的热量对焊接质量的影响不是关键因素,PCB材料厚度、器件封装规格及助焊剂类型决定预热温度的设置。
在选择性焊接中,对预热有不同的理论解释:有些工艺工程师认为PCB应在助焊剂喷涂前,进行预热;另一种观点认为不需要预热而直接进行焊接。
使用者可根据具体的情况来安排选择性焊接的工艺流程。
焊接工艺
选择性焊接工艺有两种不同工艺:拖焊工艺和浸焊工艺。
选择性拖焊工艺是在单个小焊嘴焊锡波上完成的。
拖焊工艺适用于在PCB上非常紧密的空间上进行焊接。
例如:个别的焊点或引脚,单排引脚能进行拖焊工艺。
PCB以不同的速度及角度在焊嘴的焊锡波上移动达到最佳的焊接质量。
为保证焊接工艺的稳定,焊嘴的内径小于6mm。
焊锡溶液的流向被确定后,为不同的焊接需要,焊嘴按不同方向安装并优化。
机械
手可从不同方向,即0°~12°间不同角度接近焊锡波,于是用户能在电子组件上焊接各种器件,对大多数器件,建议倾斜角为10°。
与浸焊工艺相比,拖焊工艺的焊锡溶液及PCB板的运动,使得在进行焊接时的热转换效率就比浸焊工艺好。
然而,形成焊缝连接所需要的热量由焊锡波传递,但单焊嘴的焊锡波质量小,只有焊锡波的温度相对高,才能达到拖焊工艺的要求。
例:焊锡温度为275℃~300℃,拖拉速度 10mm/s~25mm/s通常是可以接受的。
在焊接区域供氮,以防止焊锡波氧化,焊锡波消除了氧化,使得拖焊工艺避免桥接缺陷的产生,这个优点增加了拖焊工艺的稳定性与可靠性。
机器具有高精度和高灵活性的特性,模块结构设计的系统可以完全按照客户特殊生产要求来定制,并且可升级满足今后生产发展的需求。
机械手的运动半径可覆盖助焊剂喷嘴、预热和焊锡嘴,因而同一台设备可完成不同的焊接工艺。
机器特有的同步制程可以大大缩短单板制程周期。
机械手具备的能力使这种选择焊具有高精度和高质量焊接的特性。
首先是机械手高度稳定的精确定位能力(±0.05mm),保证了每块板生产的参数高度重复一致;其次是机械手的 5维运动使得PCB能够以任何优化的角度和方位接触锡面,获得最佳焊接质量。
机械手夹板装置上安装的锡波高度测针,由钛合金制成,在程序控制下可定期测量锡波高度,通过调节锡泵转速来控制锡波高度,以保证工艺稳定性。
尽管具有上述这么多优点,单嘴焊锡波拖焊工艺也存在不足:焊接时间是在焊剂喷涂、预热和焊接三个工序中时间最长的。
并且由于焊点是一个一个的拖焊,随着焊点数的增加,焊接时间会大幅增加,在焊接效率上是无法与传统波峰焊工艺相比的。
但情况正发生着改变,多焊嘴设计可最大限度地提高产量,例如,采用双焊接喷嘴可以使产量提高一倍,对助焊剂也同样可设计成双喷嘴。