金属的焊接及无损检测
焊接工艺中的射线检测与无损检测

焊接工艺中的射线检测与无损检测焊接是一种常见的金属连接方法,广泛应用于建筑、制造业、航空航天等领域。
然而,焊接过程中常常存在焊缝质量问题,这对于相关产品的安全性和可靠性产生了重要影响。
为了确保焊缝的质量,射线检测与无损检测成为了必不可少的方法。
本文将重点讨论焊接工艺中的射线检测与无损检测。
一、射线检测在焊接工艺中的应用射线检测是一种利用射线通过被测对象来获取材料内部结构信息的方法。
在焊接工艺中,射线检测主要用于检测焊缝的质量,包括焊接接头的缺陷、孔洞、裂纹等问题。
常用的射线检测方法包括X射线检测和γ射线检测。
1. X射线检测X射线检测是利用X射线通过被测对象后形成的透射或散射图像来判断焊缝的质量。
这种方法具有迅速、高效的特点,能够有效发现焊缝中的各类缺陷。
X射线检测设备主要包括射线源、探测器和显像设备。
在进行X射线检测时,需要严格遵守相关的安全操作规程,以避免对人体造成伤害。
2. γ射线检测γ射线检测是利用γ射线通过被测对象后形成的透射或散射图像来检测焊缝的质量。
与X射线检测相比,γ射线的穿透能力更强,可以检测更厚的金属焊缝。
γ射线检测设备与X射线检测设备类似,但射线源的选择以及防护措施会有所不同。
二、无损检测在焊接工艺中的应用无损检测是一种在不破坏被测对象外部结构的前提下,通过检测技术来获取内部缺陷信息的方法。
在焊接工艺中,无损检测主要用于检测焊缝的质量以及焊接接头的可靠性。
1. 超声波检测超声波检测是利用超声波在材料中传播时受到材料内部结构变化的影响而产生回波信号的方法。
在焊接工艺中,超声波检测可以检测焊缝中的各类缺陷,如焊缝结构不均匀、气孔、裂纹等。
该方法非常灵敏,可以检测出微小的缺陷,并可定量评估焊缝的可靠性。
2. 磁粉检测磁粉检测是利用磁场在被测对象表面形成漏磁场,从而检测材料内部缺陷的方法。
在焊接工艺中,磁粉检测可以发现焊缝中的裂纹、缺陷等问题。
该方法操作简单,适用性广泛,并且对于表面缺陷的检测效果较好。
无损检测基本知识
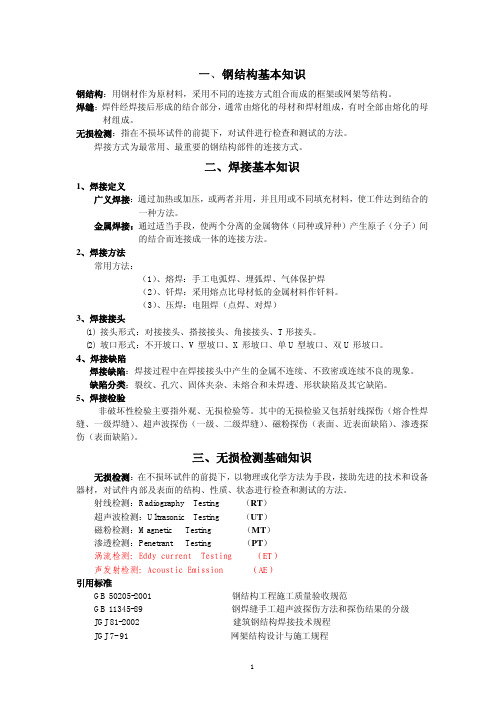
一、钢结构基本知识钢结构:用钢材作为原材料,采用不同的连接方式组合而成的框架或网架等结构。
焊缝:焊件经焊接后形成的结合部分,通常由熔化的母材和焊材组成,有时全部由熔化的母材组成。
无损检测:指在不损坏试件的前提下,对试件进行检查和测试的方法。
焊接方式为最常用、最重要的钢结构部件的连接方式。
二、焊接基本知识1、焊接定义广义焊接:通过加热或加压,或两者并用,并且用或不同填充材料,使工件达到结合的一种方法。
金属焊接:通过适当手段,使两个分离的金属物体(同种或异种)产生原子(分子)间的结合而连接成一体的连接方法。
2、焊接方法常用方法:(1)、熔焊:手工电弧焊、埋弧焊、气体保护焊(2)、钎焊:采用熔点比母材低的金属材料作钎料。
(3)、压焊:电阻焊(点焊、对焊)3、焊接接头(1) 接头形式:对接接头、搭接接头、角接接头、T形接头。
(2) 坡口形式:不开坡口、V型坡口、X形坡口、单U型坡口、双U形坡口。
4、焊接缺陷焊接缺陷:焊接过程中在焊接接头中产生的金属不连续、不致密或连续不良的现象。
缺陷分类:裂纹、孔穴、固体夹杂、未熔合和未焊透、形状缺陷及其它缺陷。
5、焊接检验非破坏性检验主要指外观、无损检验等。
其中的无损检验又包括射线探伤(熔合性焊缝、一级焊缝)、超声波探伤(一级、二级焊缝)、磁粉探伤(表面、近表面缺陷)、渗透探伤(表面缺陷)。
三、无损检测基础知识无损检测:在不损坏试件的前提下,以物理或化学方法为手段,接助先进的技术和设备器材,对试件内部及表面的结构、性质、状态进行检查和测试的方法。
射线检测:Radiography Testing (RT)超声波检测:Ultrasonic Testing (UT)磁粉检测:Magnetic Testing (MT)渗透检测:Penetrant Testing (PT)涡流检测:Eddy current Testing (ET)声发射检测:Acoustic Emission (AE)引用标准GB 50205-2001 钢结构工程施工质量验收规范GB 11345-89 钢焊缝手工超声波探伤方法和探伤结果的分级JGJ 81-2002 建筑钢结构焊接技术规程JGJ 7- 91 网架结构设计与施工规程JG/T 3034.1-1996 焊接球节点钢网架焊缝超声波探伤及质量分级法JG/T 3034.2-1996 螺栓球节点钢网架焊缝超声波探伤及质量分级法ZBY 230- 84(JB/T10061-1999)A型脉冲反射式超声探伤仪通用技术条件ZBY 231-84(JB/T10062-1999) 超声探伤用探头性能测试方法ZBY 232-84(JB/T10063-1999) 超声探伤用1号标准试块技术条件ZB J04 001- 87(JB/T9214-1999) A型脉冲反射式超声探伤系统工作性能测试方法(一)、射线检测(RT)射线探伤是利用射线可穿透物质和在穿透物质时能量有衰减的特性来发现缺陷的一种探伤方法。
金属焊接检验管理规定

附件五金属焊接检验管理规定5.1金属焊接5.1.1合金材料检验范围5.1.1.1对所有含合金成分(包括16Mn)的设备元部件(制造厂文件明令严禁解体的除外)、组合件(外围公用系统所有合金部件也包括在内)必须做100%的光谱复查,可解体或散装设备,要逐一零件复查,组合件的所有焊口两侧母材及焊缝100%光谱复查。
并将复检报告,逐一存档。
5.1.1.2现场用合金材料,安装前必须100%光谱检验,安装后连同焊缝一起必须做100%的光谱复查(对于≥M30的高温螺栓,施工单位做安装前的检验、技术监督单位进行安装后检验)。
光谱复查要求监理全程旁站,签证验收。
合金材料安装前的光谱分析应做好标识,材料下料后必须移植光谱标识。
5.1.1.3主蒸汽管道、再热蒸汽管道及中、大口径管道焊缝应每隔90度光谱分析一点,光谱分析必须进行定量分析。
汽机本体零部件、紧固件、未提供原始材质及有怀疑的合金部件光谱分析应采用直读式数字合金分析仪。
5.1.1.4所有光谱检验要做好标识,高合金钢光谱检验后要磨去灼烧点。
对细晶马氏体钢材质部件及其焊缝光谱分析后要磨去灼烧点且此部位要做PT检查。
5.1.1.5高压管道、压力容器、钢结构上的所有临时焊点(包括热电偶的临时焊点),清除后此部位要做PT检查。
5.1.2设备检验范围5.1.2.1对设备厂家焊口100%外观检查,水冷壁鳍片切割后100%进行检查,并做好记录。
膜式壁及蛇形管管排制造厂焊口及两侧各200mm范围内PT检验比例:合金总含量>10%的合金钢材质(T91、T92、不锈钢等)按100%;合金总含量3~10%的合金钢材质按50%、合金总含量<3%的合金钢材质按25%、碳钢材质按10%比例做PT检验。
异种钢焊缝按高材质端的检验比例检验。
5.1.2.2过热器、再热器、省煤器等蛇形管排的R(弯管半径)≤1.8D(管子直径)弯头:进行100%的厚度检验和不圆度检查,厚度、不圆度不合格的(低于设计壁厚),必须联系制造厂家予以更换。
焊接无损检测标准

焊接无损检测标准一、检测方法焊接无损检测主要采用以下方法:1. 射线检测(RT)2. 超声检测(UT)3. 磁粉检测(MT)4. 渗透检测(PT)5. 涡流检测(ET)根据焊接结构和材料的不同,选择合适的检测方法。
二、检测时机焊接无损检测时机一般分为:1. 焊接完成后立即进行初检,以确保焊接质量稳定。
2. 焊接完成后的24小时内进行复检,以发现可能出现的延迟性缺陷。
3. 在某些重要工程中,可在关键部位焊接完成后进行实时监测,以确保焊接质量。
三、检测比例焊接无损检测的比例一般按照以下原则进行:1. 对关键部位和结构应进行100%检测。
2. 对其他部位和结构可采用抽样检测,抽样比例根据实际情况和规范要求进行。
四、检测结果判定根据无损检测结果,对焊接质量进行判定:1. 合格:无缺陷或缺陷轻微,不影响焊接结构安全性和使用性能。
2. 不合格:存在明显缺陷,需要进行返修或补焊。
五、检测设备焊接无损检测设备应符合以下要求:1. 设备精度和灵敏度应满足检测要求。
2. 设备应定期进行校准和维护,确保设备性能稳定。
3. 设备应有相应的安全保护装置,以保障操作人员和设备安全。
六、检测人员资质焊接无损检测人员应具备以下资质:1. 经过专业培训并取得相应的资格证书。
2. 熟悉各种无损检测方法和规范要求。
3. 具有丰富的实践经验和操作技能。
4. 了解焊接结构的基本知识和安全操作规程。
5. 能够准确判断焊接缺陷的类型和程度,并出具相应的检测报告。
七、检测报告格式1. 标题:应清晰地表明检测报告的主题或名称。
2. 引言:简要介绍被检测的焊接结构和材料,以及相关的工程背景信息。
3. 检测方法:详细说明所采用的焊接无损检测方法和流程。
4. 检测结果:列出所有的检测数据和分析结果,以及相应的图片和图表。
5. 结论:根据检测结果进行总结和评价,并给出相应的建议和措施。
6. 签名和日期:应有检测单位负责人或授权人员的签名,并注明报告的日期。
焊接无损检测
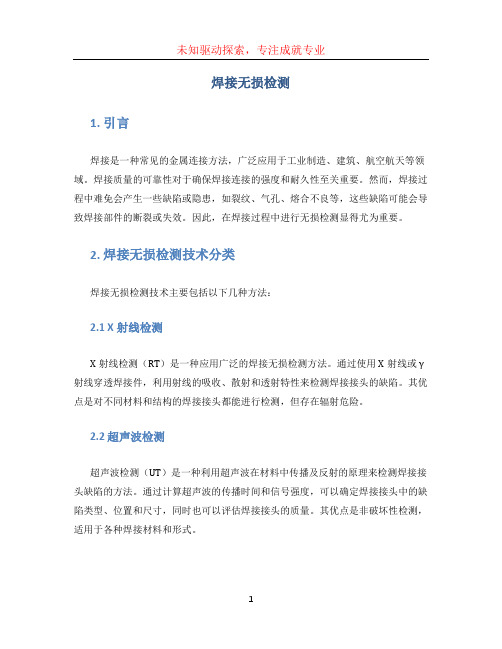
焊接无损检测1. 引言焊接是一种常见的金属连接方法,广泛应用于工业制造、建筑、航空航天等领域。
焊接质量的可靠性对于确保焊接连接的强度和耐久性至关重要。
然而,焊接过程中难免会产生一些缺陷或隐患,如裂纹、气孔、熔合不良等,这些缺陷可能会导致焊接部件的断裂或失效。
因此,在焊接过程中进行无损检测显得尤为重要。
2. 焊接无损检测技术分类焊接无损检测技术主要包括以下几种方法:2.1 X射线检测X射线检测(RT)是一种应用广泛的焊接无损检测方法。
通过使用X射线或γ射线穿透焊接件,利用射线的吸收、散射和透射特性来检测焊接接头的缺陷。
其优点是对不同材料和结构的焊接接头都能进行检测,但存在辐射危险。
2.2 超声波检测超声波检测(UT)是一种利用超声波在材料中传播及反射的原理来检测焊接接头缺陷的方法。
通过计算超声波的传播时间和信号强度,可以确定焊接接头中的缺陷类型、位置和尺寸,同时也可以评估焊接接头的质量。
其优点是非破坏性检测,适用于各种焊接材料和形式。
2.3 磁粉检测磁粉检测(MT)是一种利用电磁感应原理来检测焊接接头缺陷的方法。
通过在焊接接头周围施加磁场,并在表面涂覆磁粉,当存在裂纹或表面缺陷时,磁粉会在缺陷处形成磁通量漏磁,通过观察磁粉的聚集情况可以确定焊接接头的缺陷。
其优点是简单易行,适用于各种材料和形状的焊接接头。
2.4 渗透检测渗透检测(PT)是一种利用液体渗透性的原理来检测焊接接头缺陷的方法。
通过在焊接接头表面施加渗透液,待一定时间后擦拭干净,再施加显像液,缺陷处的渗透液会被显像液吸收,形成可见的缺陷信号。
其优点是适用于各种形状和材料的焊接接头,但不能检测到深藏在焊接接头内部的缺陷。
3. 焊接无损检测的应用焊接无损检测在工业制造、建筑、航空航天等领域都有广泛的应用,具体包括以下几个方面:•工业制造:焊接无损检测可以确保工业制造过程中的焊接质量,检测焊接接头的缺陷,避免因焊接质量不合格而造成的产品失效。
•建筑:焊接无损检测可用于建筑结构的焊接缺陷检测和评估,确保建筑物的结构强度和安全性。
焊接检测方法及应用

焊接检测方法及应用焊接是一种连接金属的常用方法,但在焊接过程中可能会出现一些问题,如未完全熔化、缺陷等。
为了保证焊接质量和产品的安全性,需要对焊接进行检测。
以下是常用的焊接检测方法及其应用。
1. 目测检测:目测是一种简单直观的检测方法,通过肉眼观察焊缝以及周围区域,识别焊接缺陷。
这种方法适用于大型零件焊接检测,可以快速识别明显的缺陷,如气孔、裂纹等。
2. 渗透检测(PT):渗透检测是一种液体浸渗的方法,通过表面缺陷与表面张力的作用,将液体渗入缺陷并通过显色剂显示缺陷位置。
这种方法可以检测出裂纹、夹渣等表面缺陷,适用于焊缝表面的检测。
3. 磁粉检测(MT):磁粉检测是利用电磁感应原理,通过施加电磁场和散射磁粉来检测材料表面和近表面的缺陷。
这种方法适用于检测磁性金属材料的缺陷,如裂纹和气孔等。
4. 超声波检测(UT):超声波检测是一种利用超声波在材料中的传播特性来检测焊缝缺陷的方法。
通过发射超声波并接收回波,可以分析回波特性,如幅值、时间和频谱等,来识别焊缝中的缺陷。
这种方法适用于焊缝内部的检测。
5. X射线检测(RT):X射线检测是一种利用X射线穿透材料并通过接收器接收衰减信号来检测焊缝缺陷的方法。
通过分析接收到的信号,可以识别焊缝中的缺陷,如裂纹、夹渣和气孔等,适用于较厚的金属焊接检测。
这些焊接检测方法在不同的应用领域有着广泛的应用。
在航空航天领域,焊接质量对于飞行器的安全至关重要。
采用超声波检测和X 射线检测方法,可以对飞行器的焊接连接进行全面无损检测,确保焊接质量。
在汽车制造领域,焊接被广泛应用于车身制造。
通过目测和渗透检测方法,可以检测出车身焊接的裂纹和气孔等缺陷,保证汽车制造的质量。
在核工业领域,焊接质量对于核设施的安全至关重要。
采用X射线检测和超声波检测方法,可以对核设施中的焊接连接进行无损检测,确保焊接质量和工作安全。
在建筑领域,焊接被广泛应用于钢结构的制造。
采用目测和磁粉检测方法,可以检测出结构焊缝的裂纹和气孔等缺陷,确保建筑结构的安全稳定。
焊接质量的检验方法
焊接质量的检验方法引言:焊接是将金属材料通过加热或压力使其熔化并连接在一起的常用工艺,广泛应用于制造业。
焊接质量的好坏直接影响到焊接件的性能和安全可靠性。
因此,对焊接质量进行有效的检验是非常重要的。
本文将介绍一些常用的焊接质量检验方法,以帮助确保焊接件的质量符合标准要求。
一、外观检验法外观检验法是通过肉眼观察焊接件的表面特征来评估焊缝的质量。
该方法适用于简单的焊接结构,如焊缝表面是否平整、无明显裂纹、气孔、夹杂物等。
二、无损检测法无损检测法是通过使用无损检测设备,如超声波、射线、液体渗透等技术对焊接件进行检测。
这些技术可以检测到焊接件内部的缺陷,如焊缝中的气孔、夹杂物、裂纹等。
无损检测法适用于对焊接质量要求较高的关键部位。
三、拉伸试验法拉伸试验法是通过在焊接件上施加拉力来评估其强度和韧性。
焊接件通常以拉伸试样的形式制备,并在拉伸试验机上进行拉伸。
根据断裂模式和拉伸值,可以评估焊接件的强度和延展性。
拉伸试验法适用于对焊接件机械性能要求较高的情况。
四、硬度测试法硬度测试法是通过在焊接件表面进行硬度测试来评估其力学性能。
硬度测试法可以检测焊缝区域的硬度变化,根据硬度值可以判断焊接区域的强度和韧性。
硬度测试法适用于对焊接部位的材料性能要求较高的情况。
五、金相检验法金相检验法是通过制备焊接件的金属切片,并在显微镜下观察和分析焊缝的金属组织结构。
金相检验法可以评估焊接件的晶粒尺寸、晶界结构、相变等特征,从而评估焊接质量的好坏。
金相检验法适用于对焊接质量较高的精细结构。
六、破坏性检测法破坏性检测法是通过对焊接件进行破坏性试验,并观察试验后的断裂面来评估焊接质量。
常用的破坏性试验方法有冲击试验、弯曲试验等。
通过观察断口的形态和裂纹的分布,可以评估焊接件的韧性和抗冲击性能。
结论:焊接质量的检验是确保焊接件性能和安全的重要环节。
本文介绍的外观检验法、无损检测法、拉伸试验法、硬度测试法、金相检验法和破坏性检测法是常用的焊接质量检验方法。
焊缝等级分类及无损检测要求
焊缝等级分类及无损检测要求焊接是制造过程中最常用的连接方法之一,焊接质量的好坏直接关系到产品的性能和寿命。
为了确保焊接接头的质量,需要进行焊缝的等级分类检测,以及无损检测来评估焊接接头的质量。
按照国际标准ISO5817-2024《焊接工艺的质量评定—焊接的焊缝形态在钢、镍、钴合金中的分类》对焊缝质量分类,焊接接头的质量可分为4个等级:1.A级:焊缝形态完好,焊盖有紧密的覆盖,有均匀的焊渣分布。
在金属基材上,焊接扩展处有不连续缺陷(如气孔、夹杂物、裂纹)数量较少。
2.B级:焊缝形态良好,有无酸洗或其他方法清除焊渣。
金属基材上有适量的不连续缺陷,但与所给定的金属基材和焊接技术的特性相符。
3.C级:焊盖紧密,能够完全覆盖焊缝,但可以有较多的焊渣。
但在金属基材上可以有多个连续缺陷,但缺陷的长度和深度有限。
4.D级:有紧密焊盖,但可能略有不完全覆盖焊缝而有部分内部缺陷。
这些缺陷可能不完全显示出来,可以通过无损检测方法进行评定。
无损检测要求:为了评估焊缝的质量,常常采用无损检测方法来检测焊接接头的缺陷。
无损检测是通过不破坏工件的情况下对材料、制品、构件等进行内部缺陷的检测和评定。
1.超声波检测:通过超声波传感器对焊缝进行扫描,检测焊接缺陷如气孔、夹杂物、裂纹等。
2.X射线检测:通过使用X射线或γ射线照射焊缝,利用与焊缝中缺陷发生反射的X射线或γ射线进行检测。
3.磁粉检测:通过在焊缝附近施加磁场,再将可视的磁粉(常见为铁粉)撒在焊缝上,当磁力线遇到焊缝中的缺陷时,磁粉会聚集在缺陷上,从而发现缺陷的位置和大小。
4.渗透检测:将渗透剂涂在焊缝上,通过渗透剂的极性和粘性吸入焊缝中的缺陷,再用显像剂使渗透剂显影出来,从而发现焊缝中的缺陷。
以上无损检测方法可以针对不同类型的焊缝进行评定,满足焊接接头等级分类中所要求的质量标准。
无损检测不仅可以检测出焊缝中的缺陷,还可以评估缺陷的大小和对焊缝的影响程度,从而为后续的焊缝处理提供指导。
金属焊接检验管理规定
金属焊接检验管理规定5.1金属焊接5.1.1合金材料检验范围5.1.1.1对所有含合金成分(包括16Mn)的设备元部件(制造厂文件明令严禁解体的除外)、组合件(外围公用系统所有合金部件也包括在内)必须做100%的光谱复查,可解体或散装设备,要逐一零件复查,组合件的所有焊口两侧母材及焊缝100%光谱复查。
并将复检报告,逐一存档。
5.1.1.2现场用合金材料,安装前必须100%光谱检验,安装后连同焊缝一起必须做100%的光谱复查(对于≥M30的高温螺栓,施工单位做安装前的检验、技术监督单位进行安装后检验)。
光谱复查要求监理全程旁站,签证验收。
合金材料安装前的光谱分析应做好标识,材料下料后必须移植光谱标识。
5.1.1.3主蒸汽管道、再热蒸汽管道及中、大口径管道焊缝应每隔90度光谱分析一点,光谱分析必须进行定量分析。
汽机本体零部件、紧固件、未提供原始材质及有怀疑的合金部件光谱分析应采用直读式数字合金分析仪。
5.1.1.4所有光谱检验要做好标识,高合金钢光谱检验后要磨去灼烧点。
对细晶马氏体钢材质部件及其焊缝光谱分析后要磨去灼烧点且此部位要做PT检查。
5.1.1.5高压管道、压力容器、钢结构上的所有临时焊点(包括热电偶的临时焊点),清除后此部位要做PT检查。
5.1.2设备检验范围5.1.2.1对设备厂家焊口100%外观检查,水冷壁鳍片切割后100%进行检查,并做好记录。
膜式壁及蛇形管管排制造厂焊口及两侧各200mm范围内PT检验比例:合金总含量>10%的合金钢材质(T91、T92、不锈钢等)按100%;合金总含量3~10%的合金钢材质按50%、合金总含量<3%的合金钢材质按25%、碳钢材质按10%比例做PT检验。
异种钢焊缝按高材质端的检验比例检验。
5.1.2.2过热器、再热器、省煤器等蛇形管排的R(弯管半径)≤1.8D(管子直径)弯头:进行100%的厚度检验和不圆度检查,厚度、不圆度不合格的(低于设计壁厚),必须联系制造厂家予以更换。
《焊接和无损检测》课件
目录
• 焊接技术概述 • 焊接工艺与设备 • 无损检测技术概述 • 无损检测技术与方法 • 焊接与无损检测的应用案例
01
CATALOGUE
焊接技术概述
焊接的定义与特点
焊接定义
焊接是通过加热或加压,或两者 并用,使分离的工件产生原子间 结合力,从而将金属材料永久连 接成一个整体的过程。
多层多道焊接有利于减小焊接变形,提高 焊缝质量。
焊接设备与工具
01
02
03
电弧焊机
常用的电弧焊机包括手工 弧焊机、埋弧焊机和气体 保护焊机等。
焊接辅助工具
包括焊条保温筒、焊接夹 具、角磨机和砂轮等。
焊接电源
提供稳定的焊接电流和电 压,保证电弧稳定燃烧。
焊接材料的选择与使用
01
02
03
04
焊条选择
高效化
提高焊接生产效率和降 低成本是焊接技术的重
要发展方向。
自动化与智能化
随着机器人技术、自动 化控制技术的发展,焊 接过程自动化、智能化
已成为趋势。
环保与节能
焊接技术应符合环保要 求,减少能耗和污染排
放,实现绿色制造。
新材料与新工艺
随着新材料和先进工艺 的出现,焊接技术也在
不断创新和发展。
02
CATALOGUE
详细描述
磁粉检测技术利用铁磁性材料在磁场作用下产生磁性现象,当材料存在表面或近表面缺陷时,磁场会 发生畸变,吸附磁粉形成磁痕,通过观察磁痕可以判断材料表面和近表面缺陷的位置和大小。
涡流检测
总结词
利用电磁感应原理在导体中产生涡流来 检测材料表面和近表面缺陷的方法。
VS
详细描述
- 1、下载文档前请自行甄别文档内容的完整性,平台不提供额外的编辑、内容补充、找答案等附加服务。
- 2、"仅部分预览"的文档,不可在线预览部分如存在完整性等问题,可反馈申请退款(可完整预览的文档不适用该条件!)。
- 3、如文档侵犯您的权益,请联系客服反馈,我们会尽快为您处理(人工客服工作时间:9:00-18:30)。
其他的焊接技术还有1887年,美国的汤普森发明电阻焊,并用于薄板的点焊和缝焊;缝焊是压焊中最早的半机械化焊接方法,随着缝焊过程的进行,工件被两滚轮推送前进;二十世纪20年代开始使用闪光对焊方法焊接棒材和链条。至此电阻焊进入实用阶段。1956年,美国的琼斯发明超声波焊;苏联的丘季科夫发明摩擦焊;1959年,美国斯坦福研究所研究成功爆炸焊;50年代末苏联又制成真空扩散焊设备。
四、拟解决的关键问题
用焊接方法加工的结构易产生较大的焊接变形和焊接残余应力,从而影响结构的承载能力、加工精度和尺寸稳定性。在焊接接头中存在着一定梳理的缺陷,如裂纹、气孔、夹渣、未焊透、未熔合等,这些缺陷的存在会降低焊件强度,引起应力集中,造成焊接结构破坏。同时,焊缝成分及金相组织与母材不同,接头部位经历热循环不同,使接头不同区域的性能不同。以上三部分均会影响焊接结构的完整性及安全性,所以选择怎样的焊接方式或无损检测方法焊接和检测怎样的金属能有利于保证焊接结构安全性及可靠性。
焊接技术就是高温或高压条件下,使用焊接材料(焊条或焊丝)将两块或两块以上的母材(待焊接的工件)连接成一个整体的操作方法。焊接是通过加热、加压,或两者并用,使同性或异性两工件产生原子间结合的加工工艺和联接方式。焊接应用广泛,既可用于金属,也可用于非金属。焊接技术是随着金属的应用而出现的,古代的焊接方法主要是铸焊、钎焊和锻焊。中国商朝制造的铁刃铜钺,就是铁与铜的铸焊件,其表面铜与铁的熔合线蜿蜒曲折,接合良好。春秋战国时期曾侯乙墓中的建鼓铜座上有许多盘龙,是分段钎焊连接而成的。经分析,所用的与现代软钎料成分相近。古代焊接技术长期停留在铸焊、锻焊和钎焊的水平上,使用的热源都是炉火,温度低、能量不集中,无法用于大截面、长焊缝工件的焊接,只能用以制作装饰品、简单的工具和武器。
2、邓洪军、焊接结构生产、机械工业出版社、2012-01-16
3、中国标准出版社,全国无损检测标准化技术委员会、无损检测标准汇编、中国标准出版社、2011
4、索科洛夫、材料探伤法、中国工业出版社、1963.07
5、李荣雪、焊接检验、机械工业出版社、2007-4-11
指导教师意见
指导教师(签名):
年月日
所在系(所)意见
负责人(签章):
年月日
19世纪初,英国的戴维斯发现电弧和氧乙炔焰两种能局部熔化金属的高温热源;1885~1887年,俄国的别纳尔多斯发明碳极电弧焊钳;1900年又出现了铝热焊。
20世纪初,碳极电弧焊和气焊得到应用,同时还出现了薄药皮焊条电弧焊。电弧比较稳定,焊接熔池受到熔渣保护,焊接质量得到提高,使手工电弧焊进入实用阶段,电弧焊从20年代起成为一种重要的焊接方法。
六、本课题的进度安排
1、第1~4周现场实习调查阶段
2、第5周确定毕业论文题目及提纲
3、第6周进行相关资料查阅与检索
3、第7~8周完成毕业论文开题报告
4、第9~12周完成毕业论文初稿撰写
5、第13~14周交付指导教师审查,修改完善毕业论文
七、参考文献
1、芮树祥,忻鼎乾编、焊接工工艺学、哈尔滨工程大学出版社、1998-09-01
在此期间,美国的诺布尔利用电弧电压控制焊条送给速度,制成自动电弧焊机,从而成为焊接机械化、自动化的开端。1930年美国的罗宾诺夫发明使用焊丝和焊剂的埋弧焊,焊接机械化得到进一步发展。
40年代,为适应铝、镁合金和合金钢焊接的需要,钨极和熔化极惰性气体保护焊相继问世。1951年苏联953年,苏联的柳巴夫斯基等人发明二氧化碳气体保护焊,促进了气体保护电弧焊的应用和发展,如出现了混合气体保护焊、药芯焊丝气渣联合保护焊和自保护电弧焊等。
五、研究思路和方法
首先焊接结构的无损性检测,是针对结构的非损害性检测,即在保证机械机构的原有结构和性能的前提下,获取被检测对象的缺陷或者潜在缺陷资料信息而所采用的检测方法。针对焊接结构的典型缺陷类型运用适合的无损检测技术,并分析目前无损检测技术在实际运用中存在的优缺点进行对比研究探讨。在前辈的经历中吸取经验,利用网络查找有关金属的焊接及无损检测技术,分析各种金属的特性,找到最适合的方法。
无损检测就是发现这类安全隐患的直接而有效的手段之一。所谓的无损检测,就是指不损及其将来使用和使用可靠性,对材料或制件进行宏观缺陷检测、几何特性测量、化学成分、组织结构和力学性能的评定。无损检测的运用广泛到涉及民航、铁道、石油、锅容管特等关系到人民的生命安全和生产安全的重要部门。
无损检测技术是在第二次世界大战后迅速发展起来的一门综合工程技术,它主要是根据物质的各种物理特性变化,在不损伤被检物使用性能与形状的条件下可以实现百分之百检查,从而判断被检物的质量状况。因此,它的应用已经在工业生产、物理研究和生物工程等广大科技领域获得极大的重视和迅猛发展,已经成为控制产品质量、保证设备安全运行等方面的极为重要的技术手段。不仅如此,它已经从单纯的检测技术发展为无损评价技术,不仅包含了无损检查与测试,还涉及以断裂力学为基础的损伤容限设计而对产品及设备的安全使用寿命作出评估,因此尽管无损检测技术本身并非是一种生产技术,但其技术水平却能反映该部门、该行业、该地区甚至该国的工业技术水平。在机械制造业以及军事工业中它已经占据了相当重要的地位,在许多重要的大型设备安全保障体系中都发挥着重要作用。然而,在一般设备或者普通民用设备的诊断维护工程中则尚未受到足够的重视和广泛应用。
理论研究
其它
√
一、本课题的研究目的和意义
1、选题目的:
随着社会主义市场经济的蓬勃发展,我国的工业化程度有了大幅度的提高,各种机械设备装置在各行业的应用越来越普及。伴随着各种机械设备装置的大量应用,其潜在的安全隐患也建逐渐显露了出来,尤其是近年来的锅炉爆炸、管道泄漏等安全事故频繁发生,不禁给我们敲响了警钟。是什么原因导致这些安全事故发生的呢?难道在事故发生之前没有不能查出这些安全隐患防患于未然吗?那么查出安全隐患的手段又是什么呢?
二、本课题的主要研究内容(提纲)
(1)金属材料在焊接过程中,其内部结构受高温因素的影响,易出现劣化损伤的现象,导致金属材料整体焊接性下降,如何提高金属材料焊接检测能力。
(2)金属焊接的残余应力分布。
(3)焊接结构的生产质量以及焊接检测技术。
三、文献综述(国内外研究情况及其发展)
焊接技术发明至今已有百余年的历史,工业生产中的大量重要产品,如航空、航天及核能工业中产品的生产制造都离不开焊接技术。当前,新兴工业的发展迫使焊接技术不断前进,就如何提高焊接生产率是目前焊接技术发展的重要研究对象。选择合适的焊接工艺参数,对提高焊接质量和提高生产效率非常重要.,焊接工艺参数(焊接规范)是指焊接时,为保证焊接质量而选定的诸多物理量.,典型的有焊接电流、焊接电压(通常用电弧长)、焊接速度、电源种类极性、坡口形式等等。对于不同的焊接方法,又有着不同的焊接参数,如焊条电弧焊焊条直径,钨极氩弧焊中钨极直径,埋弧焊中焊丝直径等等。工厂中常用TIG打底焊和TIG焊两种焊接工艺对中厚板进行对接和堆接焊接,本课题研究焊接工艺参数对接头组织和使用性能的影响,调整出最佳的焊接工艺参数以供工厂实际操作选用。
重庆邮电大学移通学院
本科毕业设计(论文)开题报告
题目金属的焊接及无损检测
学院名称重庆邮电大学移通学院
专业班级机械设计制造及其自动化05141203
学生姓名舒波
学号**********
指导教师雷建勇
2016年03月06日
设计(论文)
题目
金属的焊接及无损检测
设计(论文)
类型(划“√”)
工程实际
科研项目
实验室建设
70年代主要用于焊接薄壁材料和低速焊接,焊接过程属于热传导型,即激光辐射加热工件表面,表面热量通过热传导向内部扩散,通过控制激光脉冲的宽度、能量、峰值功率和重复频率等参数,使工件熔化,形成特定的熔池。由于激光焊接作为一种高质量、高精度、低变形、高效率和高速度的焊接方法,它已成功地应用于微小型零件焊接中。