第七章 石膏型铸造
石膏型精密铸造(石膏粉)
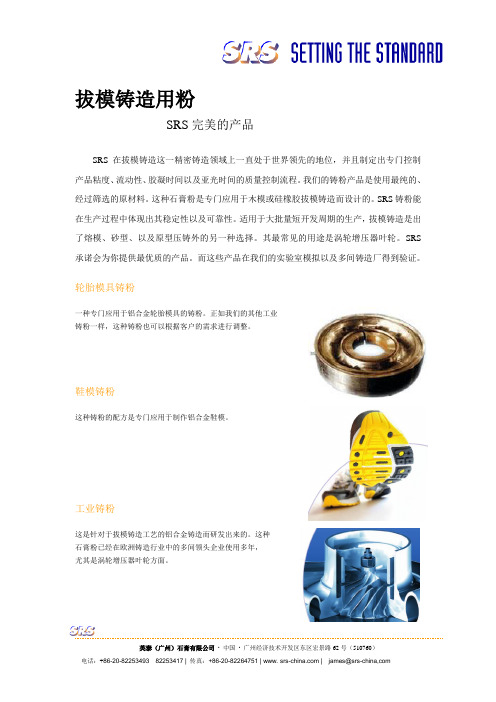
拔模铸造用粉
SRS完美的产品
SRS 在拔模铸造这一精密铸造领域上一直处于世界领先的地位,并且制定出专门控制产品粘度、流动性、胶凝时间以及亚光时间的质量控制流程。
我们的铸粉产品是使用最纯的、经过筛选的原材料。
这种石膏粉是专门应用于木模或硅橡胶拔模铸造而设计的。
SRS铸粉能在生产过程中体现出其稳定性以及可靠性。
适用于大批量短开发周期的生产,拔模铸造是出了熔模、砂型、以及原型压铸外的另一种选择。
其最常见的用途是涡轮增压器叶轮。
SRS 承诺会为你提供最优质的产品。
而这些产品在我们的实验室模拟以及多间铸造厂得到验证。
轮胎模具铸粉
一种专门应用于铝合金轮胎模具的铸粉。
正如我们的其他工业
铸粉一样,这种铸粉也可以根据客户的需求进行调整。
鞋模铸粉
这种铸粉的配方是专门应用于制作铝合金鞋模。
工业铸粉
这是针对于拔模铸造工艺的铝合金铸造而研发出来的。
这种
石膏粉已经在欧洲铸造行业中的多间领头企业使用多年,
尤其是涡轮增压器叶轮方面。
雕塑石膏实体铸型的制作工艺介绍
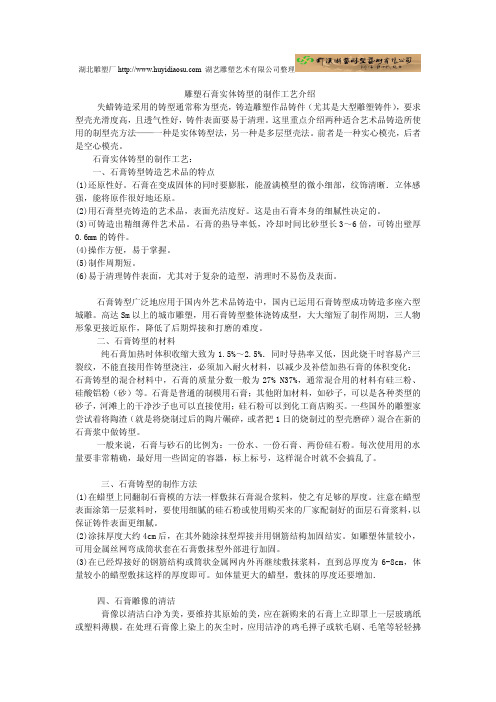
雕塑石膏实体铸型的制作工艺介绍失蜡铸造采用的铸型通常称为型壳,铸造雕塑作品铸件(尤其是大型雕塑铸件),要求型壳光滑度高,且透气性好,铸件表面要易于清理。
这里重点介绍两种适合艺术品铸造所使用的制型壳方法——一种是实体铸型法,另一种是多层型壳法。
前者是一种实心模壳,后者是空心模壳。
石膏实体铸型的制作工艺:一、石膏铸型铸造艺术品的特点(1)还原性好。
石膏在变成固体的同时要膨胀,能盈满模型的微小细部,纹饰清晰.立体感强,能将原作很好地还原。
(2)用石膏型壳铸造的艺术品,表面光洁度好。
这是由石膏本身的细腻性决定的。
(3)可铸造出精细薄件艺术品。
石膏的热导率低,冷却时间比砂型长3~6倍,可铸出壁厚0.6mm的铸件。
(4)操作方便,易于掌握。
(5)制作周期短。
(6)易于清理铸件表面,尤其对于复杂的造型,清理时不易伤及表面。
石膏铸型广泛地应用于国内外艺术品铸造中,国内已运用石膏铸型成功铸造多座六型城雕。
高达Sm以上的城市雕塑,用石膏铸型整体浇铸成型,大大缩短了制作周期,三人物形象更接近原作,降低了后期焊接和打磨的难度。
二、石膏铸型的材料纯石膏加热时体积收缩大致为1.5%~2.5%.同时导热率又低,因此烧干时容易产三裂纹,不能直接用作铸型浇注,必须加入耐火材料,以减少及补偿加热石膏的体积变化:石膏铸型的混合材料中,石膏的质量分数一般为27%N37%,通常混合用的材料有硅三粉、硅酸铝粉(砂)等。
石膏是普通的制模用石膏;其他附加材料,如砂子,可以是各种类型的砂子,河滩上的干净沙子也可以直接使用;硅石粉可以到化工商店购买。
一些国外的雕塑家尝试着将陶渣(就是将烧制过后的陶片碾碎,或者把1日的烧制过的型壳磨碎)混合在新的石膏浆中做铸型。
一般来说,石膏与砂石的比例为:一份水、一份石膏、两份硅石粉。
每次使用用的水量要非常精确,最好用一些固定的容器,标上标号,这样混合时就不会搞乱了。
三、石膏铸型的制作方法(1)在蜡型上同翻制石膏模的方法一样敷抹石膏混合浆料,使之有足够的厚度。
石膏型铸造讲义

石膏型铸造讲义
1
主要内容 概述 1、制石膏型用材料及其组成 2、石膏型精铸工艺
2
概述
1、工艺过程 石膏型精密铸造是20世纪70年代发展起来的一
种精密铸造新技术,其典型工艺过程见图0-1。 它是将熔模组装,并固定在专供灌浆用的砂箱
平板上,在真空下把石膏浆料灌入,待浆料凝结后 经干燥即可脱除熔模,再经烘干、焙烧成为石膏型, 在真空下浇注获得铸件。
3
概述
2、工艺特点
(1) 石膏浆料的流动性很好,又在真空下灌注成型, 其充型性优良,复模性优异,型精确、光洁。该工艺不 像一般熔模精密铸造受到涂挂工艺的限制,可灌注大型 复杂铸件用型。
(2) 石膏型的热导率很低,充型时合金液流动保持 时间长,适宜生产薄壁复杂件。
但铸型激冷作用差,组织粗大,当铸件壁厚差异大 时,厚大处容易出现缩松、缩孔等缺陷。
1.3
0.2
2.1-2.2 0.5 X10-6
3.25 3.1-4.3 X10-6 1.5
0.65
3.08-
5.3 X10-6
2.3
3.4
0.80
3.15
3.2-3.4 5.0 X10-6 2.6
4.6
0.85
3.95-
8.4 X10-6
2.0
3.5
0.65
4.02
5.73 7.2-10 X10-6
除石膏种类外,影响石膏强度的因素还有石膏的 细度、水固比、水温、搅拌时间等。
6
第一节 制石膏型用材料及其组成 2. 填料
为使石膏型具有良好的强度,减小其收缩和裂纹 倾向,需要在石膏中加入填料。
填料应有合适的熔点、耐火度,良好的化学稳定 性、合适的线膨胀率、发气量少,吸湿性小等性能, 常用作填料的材料及其性能见表1-1。
铸造工艺总汇-石膏型铸造与设计

图 1 石膏型精密铸造工艺过程
它是将熔模组装,并固定在专供灌浆用的砂箱平板上,在真空下把石膏浆料灌入,待浆料凝 结后经干燥即可脱除熔模,再经烘干、焙烧成为石膏型,在真空下浇注获得铸件。
7.1.2 工艺特点
1. 石膏浆料的流动性很好,又在真空下灌注成型,其充型性优良,复模性优异,型精确、光 洁。该工艺不像一般熔模精密铸造受到涂挂工艺的限制,可灌注大型复杂铸件用型。
3.2-3.4 3.95-4.02
5.73 4.7-4.9
12.5X10-6 0.5 X10-6 3.1-4.3 X10-6 5.3 X10-6
5.0 X10-6 8.4 X10-6 7.2-10 X10-6 5.1 X10-6
加入填料后石膏混合料强度 (Mpa)
7h 烘干 90℃,4h 焙烧 700℃,1h
取出母模(不可敲动),起模后应立即进行点火喷烧,否则易产生裂纹。 (五)喷烧 起模后应立刻点火并吹压缩空气进行喷烧,而使陶瓷型的表面有一定的强度和硬度。 (六)焙烧 焙烧的目的是使陶瓷型内残存的乙醇、水分和少量的有机物烧去,并使陶瓷层的强度增加。 全部由陶瓷浆料灌制的陶瓷型,焙烧温度可高达 800oC,焙烧时间 2~3h,出炉温度应在 2500C
铜器石膏型失蜡铸造法简介

铜器石膏型失蜡铸造法简介中华文明的历史进程中有很多手工艺的(璀璨发明,失蜡浇铸法就是其中之一。
失蜡浇铸法最早见于商周时代的青铜器加工中,到明清则大为盛行。
其特点:精细入微、毫厘毕现,比较适合于美感要求比较高的工艺品的加工。
到了现代,由于新的现代材料不断出现和引入,目前的失蜡铸造法除始终保持古法的目的和宗旨外,在方式方法上已不完全一样。
以下就目前常用的石膏型失蜡铸造方法作简单介绍。
石膏型失蜡铸造法的基本流程:一制阴模古法的阴模由泥土作成,然后烧制成低温陶性质的阴模,称之为“陶范”,由于烧陶过程中有很多变形的可能,所以现代已不再使用陶范的方式,而改用强度较高的石膏制作阴模:制作时在整体的阳模(现代一般是玻璃钢材质)上,按易于拆分的原则,用石膏浆制作出多块合成的套模(此时特别要注意脱模剂的使用),待石膏型固化冷却后,可将阴模拆解分开,清洁阴模内表面,用水刷7-8分潮湿后背用;二制蜡型将备好的阴模拼合成整体,使之形成需铸造的工艺品的负型(即阴模),然后将调制并加温到一定温度的液态工艺品蜡液涂刷于阴模内表面,涂刷时注意每层尽量整体一次刷完整,待整体都冷却硬化固定后再涂刷下一层,逐层加厚,直到达到所需厚度。
蜡型的厚度视加工件的大小而定,4-10毫米不等。
要求厚薄均匀,附着密实。
蜡型制作完成后,清理内表面的毛刺、将阴模的边口处修理平滑。
备用;三灌内浆将刷制完成的蜡型带石膏阴模一起倒立(大形的还需在阴模外壳加以捆扎,以防灌注时内压过大使蜡模崩裂),如有多个刷蜡口则将其他的次要开口堵住,留主口朝上,将事先混合好的耐火材料用水调制成匀质的泥浆,灌注于蜡型内,要求:灌注到位、不留空泡、操作上一气呵成、避免分层现象。
静置6小时待蜡型内的耐火材料完全硬化后方可进行下阶段的操作;四修蜡模接浇道将已灌注好耐火材料内浆的模型整体正立过来,小心去掉最外面的石膏阴模(要按拼合规律逐次拆分,不可蛮干以免损伤里面的蜡型),全部阴模拆除后用小刀修除模块之间缝隙形成的蜡毛边、毛刺,清洁蜡型表面,如有损伤则用修补软蜡修补完整。
石膏型铸造

石膏型铸造1 概述1.1 工艺过程石膏型精密铸造是用世纪70年代发展起来的一种精密铸造新技术其工艺过程见图1。
图1 石膏型精密铸造工艺过程它是将熔模组装,并固定在专供灌浆用的砂箱平板上,在真空下把石膏浆料灌入,待浆料凝结后经干燥即可脱除熔模,再经烘干、焙烧成为石膏型,在真空下浇注获得铸件。
1.2 工艺特点1. 石膏浆料的流动性很好,又在真空下灌注成型,其充型性优良,复模性优异,型精确、光洁。
该工艺不像一般熔模精密铸造受到涂挂工艺的限制,可灌注大型复杂铸件用型。
2. 石膏型的热导率很低,充型时合金液流动保持时间长,适宜生产薄壁复杂件。
但铸型激冷作用差,当铸件壁厚差异大时,厚大处容易出现缩松、缩孔等缺陷。
3. 石膏型透气性极差,铸件易形成气孔、浇不足等缺陷,应注意合理设置浇注及排气系统。
1.3 应用范围石膏型精密铸造适于生产尺寸精确,表面光洁的精密铸件,特别适宜生产大型复杂薄壁铝合金铸件,也可用于锌、铜、金、银等合金铸件。
铸件最大尺寸达1000×2000mm、重量0.03~908kg,壁厚0.8~1.5mm(局部0.5mm)。
石膏型精密铸造己被广泛应用于航空、宇航、兵器、电子、船舶、仪器、计算机等行业的零件制造上。
2 石膏型精密铸件工艺设计2.1 石膏型精密铸件工艺参数选择1)造斜度同熔模铸造。
2)加工余量(表1)。
表1 石膏型精密铸件的加工余量(mm)3)收缩率熔模收缩率0.4~0.6%、石膏型脱水收缩率0~0.5%、当金属收缩率1.1~1.3%时,综合线收缩率1.5~2.0%。
2.2 浇注系统及冒口设计1. 石膏型精密铸造的浇冒系统应满足下列要求:(1)有良好的排气能力,能顺利排出型腔中气体,在顶部和易憋气处要开设出气口。
(2)要保证合金液在型腔中流动平稳,顺利充满型胶,避免出现涡流,卷气现象。
(3)合理设置冒口,保证补缩。
(4)脱模时浇注系统应先蒋先,减小熔模对石膏型的膨胀力。
(5)浇注系统在铸件凝固过程中应尽可能不阻碍铸件收缩,以防止件变形和开裂。
石膏型铸造常用的其它填料.
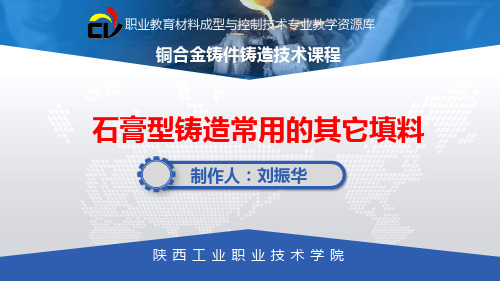
铜合金铸件铸造技术课程
石膏型铸造常用的其它填料
制作人:刘振华
陕西工业职业技术学院
绪论
适用于石膏型的填料种类较多,除上述硅酸盐类耐火材料外, 尚有锆英石粉等材料也可用作石膏型填料。下面重点介绍锆英石粉 和石墨填料的性能特点。
铜合金铸件铸造技术课程
锆英石粉
锆英石亦称锆石、锆砂,在我国山东、广东、广西沿海各地 蕴藏丰富。近年来国外在铸造方面的应用日益扩大。
铜合金铸件铸造技术课程
4.锆英石的蓄热系数较大,对铸件凝固有利。 锆英石与一些耐火材料的蓄热系数见表1。锆英石的蓄热系数 比石英大1倍,比刚玉和莫来石约大30%,作为石膏型填料能改善 石膏型的蓄热能力。由于锆英石有上述特点,对生产高熔点合金 或对铸件表面质量有较高要求时,可考虑用作石膏型填料。
耐火材料种类 蓄热系数
铜合金铸件铸造技术课程
铜合金铸件铸造技术课程
石墨在大气下加热易氧 化,如用作填料能改善石膏 型的导热性,但石膏型应在 非氧化气氛下焙烧和浇注, 使工艺复杂化,除特殊需要 外一般不宜选用。
图2 天然石墨的热传导率
1-平行于层面 2-垂直于层面
铜合金铸件铸造技术课程
THANKS FOR YOUR WATCHING
谢谢您的观看
表1 一些耐火材料的蓄热系数
锆英石
石英砂
刚玉
45-50
20-25
37
莫来石 30-38
铜合金铸件铸造技术课程
石墨
石墨的热传导率及蓄热系数均较大,石墨制品的热传导 率的大小与方向有关,颗粒成平行的方向相当于铝的热传导 率,在垂直的方向上也接近黄铜的热传导率。从天然单晶石 墨测得的数据见图2。沿层面较垂直层面约大3倍。
石膏型铸造

缓凝剂主要有三类: (a)磷酸盐、碱金属硼酸盐、硼砂、硼酸等。 (b)有机酸及可溶性盐,如柠檬酸及其盐、琥珀 酸钠、乙基酸钠、甲基酸钠、草酸等。 琥珀酸钠的缓凝作用很强,只需要加入千分之几 就有明显的效果。 (c)蛋白胶、皮胶、硅溶胶、纸浆废液等。
增强剂用来增加石膏型的湿强度、干强度、焙烧 后强度以及高温强度。一般用某些硫酸盐如 Na2SO4、K2SO4、NiSO4、MgSO4等,其中以 MgSO4的效果最好。
• 石膏型需随炉冷却,当温度降至300℃以下时才可 以出炉,否则石膏型容易开裂,对复杂型温度应低 些。
填料
α-
半水
硅
石膏 硅石粉 线
100
石
%
高 高岭 莫来 铝 土 石矾
土
工 业 氧 化 铝
锆 英 粉
石 英 玻 璃
300℃ 空冷
微裂
极轻微 裂
不 裂
不裂
不裂
不 裂
不 裂
不不 裂裂
700℃ 空冷
碎裂 微裂
4.3.2浇注系统及冒口设计
• 对于石膏型铸造,浇注系统应满足如下要求: • A良好的排气能力,能顺利排出型腔气体,在顶部和易裹
气处开设出气口。 • B保证金属液充型平稳,避免出现紊流,卷气现象。 • C合理设置冒口,保证补缩。 • D脱模时浇注系统先熔脱,减小熔模对石膏型的胀型力。 • E浇注系统在铸件凝固时尽可能不阻碍铸件收缩,以防止
650~700℃左右,加压压力0.07MPa左右。
4.2.3 石膏型应用实例
图4-6是铝合金轮胎样件模具的石膏型 铸造实例。该样件从三维实体造型,制造 LOM原型(图4-6b)、硅橡胶模(图46c)、石膏型(图4-6d)到将烘干及焙烧 完毕的石膏型温度降低至180℃,浇注铝合 金制造出模具(图4-6f),总制造周期为4 天。
- 1、下载文档前请自行甄别文档内容的完整性,平台不提供额外的编辑、内容补充、找答案等附加服务。
- 2、"仅部分预览"的文档,不可在线预览部分如存在完整性等问题,可反馈申请退款(可完整预览的文档不适用该条件!)。
- 3、如文档侵犯您的权益,请联系客服反馈,我们会尽快为您处理(人工客服工作时间:9:00-18:30)。
7.2.3 石膏型应用实例
图9-6是铝合金轮胎样件模具的石膏型
铸造实例。该样件从三维实体造型,制造
LOM原型(图9-6a)、硅橡胶模(图9-
6b)、石膏型(图9-6c)到将烘干及焙烧
完毕的石膏型温度降低至180℃,浇注铝合
金制造出模具(图9-6d),总制造周期为4
天。
图9-6 石膏型成形的轮胎模具 a) 三维实体模型 b)LOM原型 c) 硅橡胶模 d) 石膏型 e) 非占位涂层铸型 f) 铝合金轮胎模具
• • • •
• •
• (4)石膏型的浇注
• 焙烧好的石膏型在空气中很容易受
潮,必须尽快浇注。考虑到石膏型透气性
低,导热性低的特点,可采取一些措施如
如加压或负压浇注。浇注时石膏型温不高
于200℃,合金液的温度在保证流动性的情 况下,尽可能的低。如铝合金控制在650℃ 左右,加压压力0.07MPa左右。
影响见表7-2~表7-4。
表7-2
填料类型对石膏混和料抗弯强度的影响 Nhomakorabea填料
硅石 粉
硅线 石
莫来 石
高岭 土
高铝矾 土
工业氧 化铝
灌浆后2h
灌浆后7d 烘干90℃ /4h 700℃焙 烧后
0.25
0.50 1.30
0.40
1.50 2.80
0.75
2.30 3.40
0.80
2.40 3.80
1.00
第七章
石膏型铸造
7.1 概述 定义:石膏性铸造是以石膏为主要造型材料
的一种铸造工艺方法。从本质上来说是一 种以石膏为胶凝材料的实体熔模铸造法。
7.1.1 工艺简介
其基本工艺过程如图7-1所示。石膏型铸造 按脱模方法分类可分为熔模石膏型铸造和 起模石膏型铸造两类,前者是加热熔模使 其从石膏模中流出,后者是通过人力机械 方法将模样从型中拔出。起模石膏型铸造 又可分为普通石膏型和发泡石膏型。
图7-2 石膏型的工艺过程示意
7.2 石膏型铸造工艺
7.2.1 制备石膏型的各种原材料
• (1)石膏
• 制作石膏型常用α型半水石膏,也可 用β型半水石膏,前者混水量少,铸型强度 高,后者则相反。两种石膏在微观结构上 基本相似,但宏观性能上却差别较大,如 表7-1。
表7-1 铸造用石膏粉的主要性能要求
锆 英 粉
不 裂
石 英 玻 璃 不 裂
300℃ 空冷
700℃ 空冷
碎裂
不 裂
极轻 极 微裂 极轻 轻 或不 微裂 微 裂 裂
轻 微 裂
轻 微 裂
不 裂
表7-4 填料类型对石膏混和料浆体胶凝时间的影响 工业 氧化 铝 9.0 α-半水 锆英 石膏 粉 100% 10.0 8
填 料
初 凝 时 间 终 凝 时 间
凝结时间 /min 初凝 终凝 8~ 12~ 10 18 7~ 5~7 12 粒度 0.075mm (200目筛 余1%)
石膏类 型
抗压强度 /MPa
标准稠 度混水 量/%
α
β
15
8
40
50
5
5
• (2)填料 • 单纯使用α型石膏并不能用于铸型制 作,须加入耐火材料的填料。其主要目的 是减小石膏型的线收缩和裂纹倾向。常用 填料的种类较多,其中以SiO2-Al2O3系材 料应用较广泛。各种填料对石膏型性能的
2.60 4.60
0.80
2.00 3.50
0.20
0.65
0.80
0.86
0.85
0.65
表7-3
填料类型对石膏混和料裂纹倾向的影响 工 业 氧 化 铝 不 裂
填料
α- 半水 硅 石膏 硅石粉 线 100 石 % 微裂 极轻微 不 裂 裂 微裂
高 高岭 莫来 铝 土 石 矾 土 不裂 不裂 不 裂
要求和石膏原材料性能来决定。有关手册
列出了比较常用的混合浆料的配比,可供
参考。
• (2)石膏混合浆体的搅拌、灌注
• 石膏混合料吸附大量的气体,在浆料搅拌时又 会卷入大量的气,致使浆料中有大量的气泡,影响石 膏型腔表面的质量。除发泡石膏型希望有大量孔洞可 以在大气下搅拌及灌注外,普通石膏型浆料应该在真
空下搅拌,使浆料中所含的气体能够顺利外排。常用
的工艺参数为:真空度0.05~0.06MPa,搅拌时间2~ 3min,搅拌速度250~300r/min。灌浆时搅拌室的真 空度应该等于或略低于灌浆室,以加强浆体的充填能 力,但是压差不能太大以免造成浆体喷射。
• (3)石膏型的干燥、焙烧及浇注
• 石膏型需经一定的时间自然干燥后才能人 炉加热干燥和焙烧。宜在炉气可循环的炉中干燥焙 烧,也可以在箱式电炉中进行;对一般石膏其工艺 如下。 起模石膏: (80~100) ℃×8h→150℃×4h→250℃×2h→350℃×2h 熔模石膏: (80~100) ℃×8h→150℃×4h→250℃×2h→350℃×2h→ 450℃×1h→550℃×1h→(680~700)℃×2h 石膏型需随炉冷却,当温度降至300℃时才 可以出炉,否则石膏型容易开裂,对复杂型温度应 低些。
• •
• •
• (4)模样材料 • 可制作石膏型模样材料的有金属、 硬质木材、橡胶、塑料等,除橡胶外,其 它材料制作的模样为了起模方便,均需要 涂脱模剂,常用的有变压器油、凡士林、 肥皂液、经煤油稀释的石蜡硬脂酸等。
7.2.2 石膏混合浆料的制备及灌浆
• (1)石膏混合浆料的配比
• 石膏混合浆料的配制应根据铸件的
• 石膏型铸造的特点:
• 1)石膏浆料的流动性很好,凝结时有轻微 的膨胀,所制铸型轮廓清晰、花纹精细。 • 2)石膏型溃散性好,易于清除。 • 3)石膏型的导热性很差,金属浇入后散热 缓慢,流动性好,适于生产薄壁铸件。 • 4)石膏型的透气性极差,铸件易产生气孔、 浇不足等缺陷。 • 5)石膏型耐火度低,适于生产铝、锌、铜、 金、银等合金铸件。
硅石 硅线 粉 石
高岭 土
莫来 高铝矾 石 土
7.0
8.5
8.0
10.0
12.0
10.0
10.5
10.0
12.0
13.5
11.0
12.0
10
• (3)添加剂及其他
• 石膏型铸型的添加剂一般有促凝剂、缓凝 剂和增强剂等,它们的盐类,常用的有NaSiF6、 NaCl、NaF、MgCl2、MgSO4、NaNO3、KNO3 等;缓凝剂主要有三类: (a)磷酸盐、碱金属硼酸盐、硼砂、硼酸等。 (b)有机酸及可溶性盐,如柠檬酸及其盐、琥珀 酸钠、乙基酸钠、甲基酸钠、草酸等。其中琥珀 酸钠的缓凝作用很强,只需要加入千分之几就有 明显的效果。 (c)蛋白胶、皮胶、硅溶胶、纸浆废液等。 增强剂用来增加石膏型的湿强度、干强度、 焙烧后强度以及高温强度。一般用某些硫酸盐如 Na2SO4、K2SO4、NiSO4、MgSO4等,其中以 MgSO4的效果最好。