模具设计指南-模温控制
塑料模具课件-温度调节

即冷却时间t与Q 成正比,为了使冷却时间缩短,可使塑 料传给模具的热量QT 减小或使塑料和模具的温差大。缩短成型
周期就是缩短冷却时间,也就是为了提高生产效率而进行温度
调节。
根据试验。塑料带给模具的热量约5%由辐射、对流散到大 气中,其余95%由冷却介质带走。因为模具的材料是钢导热系 数大约为1000千卡/米2·小时·度,传热非常快,因此一般来说 冷却水管距型腔的距离对型腔的冷却影响不大,主要影响因素 是冷却介质的流量。
确定流体的各个物性常数; – ⑷管长L与管径d之比大于50即长管。 1. 由3-8-3,3-8-4,3-8-5求出传热面积,就可求出冷却水孔
直径,水路长度及孔数。
n a
dl
– 式中:n——孔数。
3.8.3模具冷却系统设计原则
为了提高生产效率,得到变形小的制品,除了塑件 与型腔的形状设计外,冷却系统的设计也是很重要的。 一、冷却水孔数量尽量多,尺寸尽量大如图 3-8-1 。 二、冷却水孔至型腔表面距离相等。 如图 3-8-2a 所示,一般水孔边离型腔的距离大于10mm,
冲击强度高
实验表明,HDPE冲击强度受充模速度影响很大, 特别在浇口附近,高速注射的制品较低速注射的制品 在浇口附近冲击强度高1/4,但模温影响较小,以采用 较低的模温(45~50℃)为宜。
表面光洁
对塑件表面光洁度影响最大的除型腔表面加工质量外 就是模具温度,提高模温能大大改善塑件表面状态。
上述六点要求有互相矛盾的地方,在选用时应根据使用 情况偏重于满足塑件的主要要求。
;
⑷狭窄的、薄的小型制品如图 3-8-12 、图 3-8-13 。
3.8.4常用的各种冷却系统的结构
由于塑件的形状是各种各样的,必须根据型腔内的 温度分布,浇口位置等设计不同的冷却系统,下面介 绍型腔、型芯的冷却结构以及局部冷却和加热装置。 ⑴型腔冷却系统结构如图 3-8-14 3-8-15 3-8-16 ⑵型芯冷却系统结构 3-8-17 3-8-18 3-8-19
塑料注塑模具模温控制
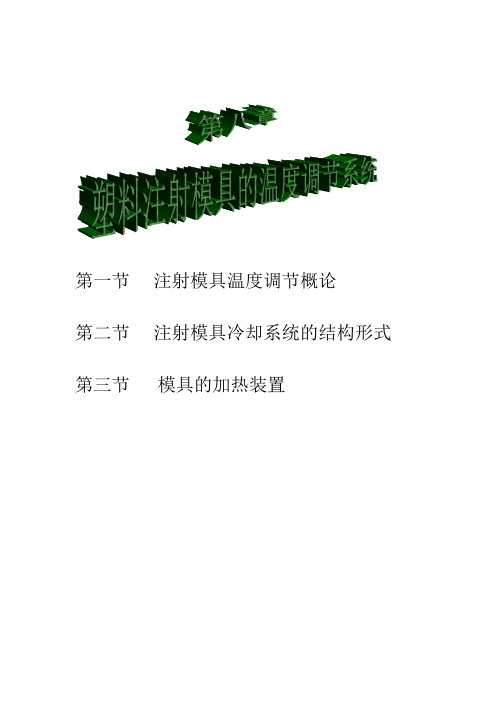
第一节注射模具温度调节概论第二节注射模具冷却系统的结构形式第三节模具的加热装置第一节注射模具温度调节概论一、模具的热传导熔融塑料传给模具的热量有三种形式1、熔融的塑料在注入模体时,将热量传导给模具,使模具温度上升,同时熔料的温度也随之下降。
2、注射完毕后,熔料和模具产生一个温差。
热量总是由高温区向低温区传递高温熔料必然向温度较低的模具传导,这个传导的热量,俗称“显热”。
3、塑料熔体在与模体热交换时,使其温度迅速降低,而产生变相固化。
这个过程产生的热量称为熔化热量。
熔融塑料在单位时间内传导给模具的总热量Q为:Q=GΔi式中Q—单位时间内熔料传导给模具的总热G—单位时间内注入模具内塑料熔体的质量△i —成型时单位质量塑料释放的热量二、调节模具温度的作用注射成型过程中,模温直接影响塑料的充模和塑件的定型以及注射周期和塑件质量。
1、缩短成型周期缩短成型周期的主要途径是缩短塑件冷却固化时间。
其表达式为:T Q k t △式中 t —冷却时间;K —系数;Q —总热量;∆T —温差。
2、调节模具温度在均衡状态,可稳定成型收缩率,提高塑件的尺寸精度。
3、在注射填充过程中,熔料保持良好的流动性和成型性。
以提高塑件的表面质量。
4、模具温度达到较好的热平衡状态,可改善塑件顺序固化成型条件有利于补缩压力的传递,避免注射缺陷。
5、调节模具温度,可均衡成型零件各部冷却速度,以减少塑件内应力引起的塑件变形。
6、在特殊情况下,可通过加热的方法,提高模具的温度。
三、冷却系统冷却效果的衡量标准冷却效果就是:塑件冷却固化过程中,在限定的时间内,冷却系统带出热量的多少和模具温度的均匀程度。
影响因素:1、冷却介质的多少;2、冷却通道与成型区域的接近程度;3、冷却水道的长度和设计布局;4、冷却通道的直径以及冷却介质的流动状态;5、从入口到出口冷冷却介质的温差;6、熔融塑料与模具的温差。
四、冷却系统的设计要点1、冷却水道与成型面各处应取相同的距离。
压铸模温度控制方法
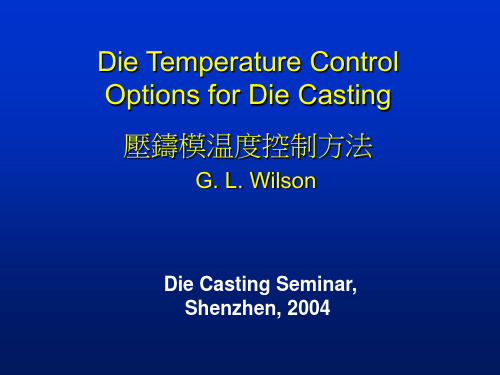
Die Temperature 模具温度
-Too Low 太低 Cold shots冷纹 Short shots填充不饱满 Porosity孔穴 Excessive contraction过度收缩
-Too High 太高
Hot tearing热裂 Warping弯翘 Blisters表面气孔 Porosity孔穴 Flashing飞边 Ejection problems顶出问题
Die temperature starts at ambient 从室温开始加热 Increase to operating temperature 加热至操作温度 Four methods available四种方式 Warm-up shots打料加热 Gas heating气体加热 Oil heating油加热 Electric heating电热
Die Temperature Range模温笵围 Range模温笵围
Optimum适当
Temperature温度 Temperature温度
Upper Limit 上限 Lower Limit 下限
Ambient环境
Die模具
Metal金属
Die Pre Heating模具预热 Heating模具预热
Die Temperature Control Options for Die Casting 压铸模温度控制方法
G. L. Wilson
Die Casting Seminar, Shenzhen, 2004
Die Temperature模具温度 Temperature模具温度
Significant process variable 重要的工艺参数 Effects casting quality 影响铸件质量 Effects production rate 影响生产效率 Effects casting cost 影响铸件成本
对模具加热或冷却

第10章模温控制模具温度对胶件的成型质量、成型效率有着较大的影响。
在温度较高的模具里,熔融胶料的流动性较好,有利于胶料充填型腔,获取高质量的胶件外观表面,但会使胶料固化时间变长,顶出时易变形,对结晶性胶料而言,更有利于结晶过程进行,避免存放及使用中胶件尺寸发生变化;在温度较低的模具里,熔融胶料难于充满型腔,导致内应力增加,表面无光泽,产生银纹、熔接痕等缺陷。
不同的胶料具有不同的加工工艺性,并且各种胶件的表面要求和结构不同,为了在最有效的时间内生产出符合质量要求的胶件,这就要求模具保持一定的温度,模温越稳定,生产出的胶件在尺寸形状、胶件外观质量等方面的要求就越一致。
因此,除了模具制造方面的因素外,模温是控制胶件质量高低的重要因素,模具设计时应充分考虑模具温度的控制方法。
概念:对模具加热或冷却,将模温控制在合理的范围内。
——模具冷却介质:水、油、铍铜、空气等;——模具的加热方式:热水,蒸气,热油、电热棒加热等。
温度控制的重要性模温对不同塑料的影响1.对流动性较好的塑料(PE、PP、HIPS、ABS等),降低模温可减小应力开裂(模温通常为60°左右);2.对流动性较差的塑料(PC、PPO、PSF等),提高模温有利于减小塑件的内应力(模温通常在80°至120°之间)。
模温对塑件成型质量的影响(1)过高:脱模后塑件变形率大,还容易造成溢料和粘模;(2)过低:则熔胶流动性差,表面会产生银丝、流纹、啤不满等缺陷;(3)不均匀:塑件收缩不均匀,导致翘曲变形。
模具温度直接影响注塑周期模具冷却时间约占注塑周期的80%。
10.1模具温度控制的原则和方式10.1.1模具温度控制的原则为了保证在最有效的时间内生产出高外观质量要求、尺寸稳定、变形小的胶件,设计时应清楚了解模具温度控制的基本原则。
(1)不同胶料要求不同的模具温度。
(2)不同表面质量、不同结构的模具要求不同的模具温度,这就要求在设计温控系统时具有针对性。
模具温度的控制
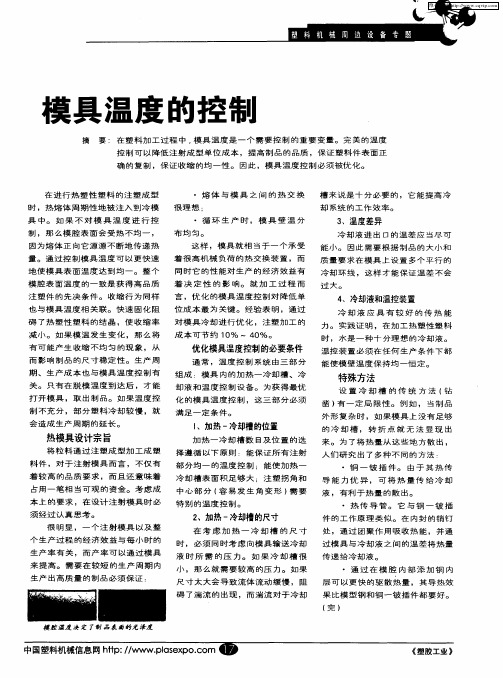
模 具温度 的控 制
摘 要 :在 塑 料 加 工 过 程 中 , 具 温度 是 一 个 需 要 控 制 的 重 要 变 量 。 完 美 的温 度 模 控 制 可 以 降低 注 射成 型 单 位 成 本 ,提 高 制 品 的 品质 ,保 证 塑 料 件 表 面 正
模 腔 表 面 温 度 的一 致 是 获 得 高 品质
注 塑 件 的 先 决 条件 。 收 缩 行 为 同 样
也 与模 具 温 度 相 关联 。 快 速 固 化 阻
4 、冷却液和温控装置
冷 却 液 应 具 有 较 好 的 传 热 能 力 。 实 践 证 明 ,在 g T . 塑 性塑 料 n  ̄ 时 ,水 是 一 种 十 分 理 想 的 冷 却 液 。
铜 一 铍 插 件 。 由 于 其 热 传
导 能 力 优 异 , 可 将 热 量 传 给 冷 却
液 ,有 利 于 热 量 的 散 出。
・
热 传 导 管。 它 与铜 一 铍 插
2 、加热 一冷却槽的尺寸
在 考 虑 加 热 一 冷 却 槽 的 尺 寸 时 ,必 须 同 时考 虑 向模 具 输 送 冷 却 液 时 所 需 的 压 力 。 如 果 冷 却 槽 很 小 ,那 么就 需 要 较 高 的压 力 。 如 果 尺 寸 太 大 会 导 致 流 体 流 动 缓 慢 , 阻 碍 了湍 流 的 出现 ,而 湍 流 对 于 冷 却
布均 匀。 这 样 ,模 具 就 相 当 于 一 个 承 受 着 很 高 机 械 负荷 的 热 交 换 装 置 ,而 同 时 它 的性 能 对 生 产 的经 济 效 益 有 着 决 定 性 的 影 响 。 就 加 工 过 程 而 言 ,优 化 的模 具 温 度 控 制 对 降 低 单 位 成 本 最 为 关 键 。 经 验 表 明 ,通 过
一体化压铸模温控方案

一体化压铸模温控方案一、为啥要温控。
咱先得明白为啥要给一体化压铸模搞个温控方案呢?你想啊,压铸这个过程就像做饭一样,温度得合适才行。
温度要是太高了,那模具就跟个暴躁的小怪兽似的,可能会变形、磨损得特别快,而且压铸出来的零件质量也不咋地,可能到处都是瑕疵,就像烤糊了的蛋糕。
温度要是太低呢,金属液就不愿意好好听话,可能流得不畅快,零件就会有缺肉的地方,就像蛋糕没发起来似的。
所以啊,温度控制是保证压铸顺利进行和产品质量的关键因素。
二、基础的温控设备。
1. 加热元件。
首先得有加热棒或者加热板这种东西。
加热棒就像一个个小火柴棍,不过是超级耐热的那种,可以插在模具里面,均匀地给模具加热。
加热板呢,就像是给模具盖了个小热毯子,从外面给模具传递热量。
这些加热元件的功率得选好,就像你选电暖器得选合适的瓦数一样,功率小了,模具热得慢;功率大了,可能会局部过热。
2. 冷却通道。
冷却通道就像是模具的小空调系统。
一般在模具里面会设计一些弯曲的通道,就像小迷宫一样。
冷水或者冷却油可以在这些通道里流动,把模具多余的热量带走。
通道的设计很有讲究,要是设计得不合理,可能有的地方冷却过度,有的地方还热着呢,就像你家空调有的房间冷得要命,有的房间还热乎乎的。
三、温控的控制策略。
1. 温度传感器。
这就像是模具的小体温计。
要在模具关键的地方装上温度传感器,比如靠近型腔的地方,因为那里的温度对压铸产品的质量影响最大。
这些传感器能实时地把温度数据传给控制系统,就像小间谍一样,时刻汇报模具的温度情况。
2. 控制系统。
控制系统就像一个聪明的大脑。
它根据温度传感器传来的数据,决定什么时候该加热,什么时候该冷却。
如果温度低了,它就指挥加热元件开始工作;如果温度高了,就打开冷却通道的阀门,让冷却液流起来。
而且这个控制系统还可以设置温度的上下限,就像给模具的温度设定了一个小范围的安全区,一旦温度超出这个范围,它就会报警,就像拉响警报一样,告诉操作人员有问题了。
10模具设计-第十章--温度调节系统PPT课件
10 . 1 模具温度及塑料成型温度关系
2)对于粘度高、流动性差的塑料,例如聚碳酸酯、聚砜、 聚甲醛、聚苯醚和氟塑料等,为了提高充型性能,考虑到 成型工艺要求较高的模具温度,必须设置加热装置对模具 进行加热。
3)一般需要用常温水或冷水对模具冷却,而对于高粘流温度 和高熔点的塑料,可用温水进行模温控制。
在模具中设置温度调节系统的目的:
就是要通过控制模具温度,使模塑成型具有良好的产品质
量和较高的生产率。
模具温度的调节是指对模具进行冷却或加热,必要时两者
兼有,从而达到控制模温的目的。
4
10 . 1 模具温度及塑料成型温度关系
注射入模具中的热塑性熔融树脂,必须在模具内冷却固化才 能成为塑件,所以模具温度必须低于模具内熔融树脂的温度, 即达到θg(玻璃化温度)以下的某一温度范围,由于树脂本身 的性能特点不同,不同的塑料要求有不同的模具温度。
3
第十章 温度调节系统
模具温度及其调节的重要性
2.模具温度对成型周期的影响
缩短模塑成型周期就是提高模塑效率。
缩短成型周期关键在于缩短冷却硬化时间,而缩短冷却时 问,可通过调节塑料和模具的温差,在保证制件质量和成 型工艺顺利进行的前提下,降低模具温度有利于缩短冷却 时间,提高生产效率。 缩短成型周期→缩短冷却硬化时间→调节塑料和模具的温差→保证 质量前提下降低模具温度→缩短冷却时间,提高生产效率
4)对于模温要求在90℃以上的,必须对模具加热。 对于流程长、壁厚较小的塑件,或者粘流温度(或熔点)虽 不高但成型面积很大的塑件,为了保证塑料熔体在充模过 程中不至温降太大而影响充型,可设置加热装置对模具进 行预热。 对于小型薄壁塑件,且成型工艺要求模温不太高时,可以 不设置冷却装置而靠自然冷却。
模具的温度控制
模具的温度控制模具是制造零件、产品的重要工具,可以制造出各种形状、尺寸、材料的产品。
而模具的温度控制是非常重要的一环,它直接影响着产品的质量、生产效率和模具寿命等因素。
下面我们来详细了解一下模具的温度控制。
一、模具温度的影响模具温度的高低对产品质量的影响是非常大的。
模具温度过高可能导致产品变形、出现开裂、缺损等问题,而模具温度过低则会导致产品表面不光滑、容易出现翘曲等问题。
因此,在生产中,需要对模具的温度进行严格控制,以确保产品的质量。
二、模具温度控制的方法1. 水流控制法这种方法是通过向模具注入冷却水或加温水来控制模具的温度。
具体来说,就是在模具上设置一个进水口和出水口,通过水流量来控制模具的温度。
这种方法简单易行,但对水的流量和温度有一定的要求,并且不适用于对温度要求比较高的产品。
2. 加热棒法这种方法是通过在模具上加装一些加热棒来控制模具的温度。
加热棒使用电阻线圈发热,可以使模具快速升温,温度控制准确性较高。
但加热棒的使用寿命有限,并且需要定期更换。
3. 空气加热法这种方法是通过空气加热来控制模具的温度。
具体来说,就是将空气加热后通过送风管送到模具内部进行加热。
这种方法可控性强,在保证模具温度均匀的情况下,还可以将时间和成本的额外消耗降至最低限度。
三、模具温度控制的注意事项1. 选择合适的控制方法在操作时,需要根据实际情况选取合适的温度控制方法。
例如,对于表面要求高、对温度要求严格的产品,应该采用空气加热法等高精度的控制方法。
而对于对温度要求不严格的产品,可以采用水流控制法等更为便捷的方法。
2. 均匀升温在升温过程中,需要确保模具温度升幅均匀。
如果模具温度不均匀,将会导致产品变形、表面不平整等问题。
3. 加强维护保养在使用过程中,需要定期对模具进行清洁、维护和保养。
特别是在使用水流控制法时,需要做好水质监测以防止水碱度过高导致模具腐蚀。
综上所述,模具的温度控制是非常重要的一环。
选取合适的控制方法、均匀升温和加强维护保养都是必不可少的。
控制模具温度的三种方法【技巧】
模温机的种类是根据使用的导热流体(水或导热油)来划分的。
用运水式模温机通常zui大出口温度95℃。
用运油式模温机用于工作温度150℃的场合。
通常情况下,带有开口水箱加热的模温机适于用水温机或油温机,zui大出口温度为90℃至150℃,这种模温机的主要特点是设计简单,价格经济。
在这种机器的基础上又衍生了一种使用高温水温机,可允许的出口温度为160℃或更高,由于在温度高于90℃的时候,水的热传导性比同温度下的油好很多,因此这种机器有着突出的高温工作能力。
除此之外,还有一种强制流动的模温机,出于安全因素,这种模温机设计工作温度为150℃以上,使用导热油。
为了防止模温机加热器里的油过热,使用了强制流动泵送系统,且加热器由一定数量的的管子堆叠组成,管子里有装有翅片的加热元件用于导流。
控制模具内的温度各点不均匀,也和注射周期中的时间点有关。
在注射以后模腔的温度升到zui高,这时热的熔体碰到模腔的冷壁,当零件移走后温度降到zui低。
模温机的作用就是防止温度差在生产过程或间隙上下波动。
我们一起看下控制模具温度的三种方法。
控制流体温度。
这是zui常用的方法,且控制精度可以满足大多数情况要求。
使用这种控制方法,显示在控制器的温度和模具温度并不一致;模具的温度波动相当大。
直接控制模具温度。
该方法是在模具内部装温度传感器,这在模具温度控制精度要求比较高的情况下才会采用。
控制器设定的温度与模具温度一致。
通常情况下,模具温度的稳定性比通过控制流体温度更好,在生产过程控制中的重复性较好。
联合控制。
联合控制是上述两种方法的综合,它能同时控制流体和模具的温度。
在联合控制中,温度传感器在模具中的位置极其重要,放置温度传感器时,必须考虑形状、结构及冷却通道的位置。
另外,温度传感器应被放置在对注塑件质量起决定性作用的地方。
模温机还可以自动控制。
模温机使用说明
模温机使用指南:如何让你的注塑成型更完
美
注塑成型是一种制造方法,常用于制造各种塑料制品。
而在注塑成型的过程中,模温机的作用是至关重要的。
以下是模温机的使用指南,帮助你达到更完美的注塑成型效果。
一、模温机是什么?
模温机是专门为注塑机设计的,通过控制模具温度,从而控制塑料熔体的温度。
模温机一般由机身、温度控制器、水路系统等部分组成。
二、如何正确使用模温机?
1.接通电源,打开模具加热器,加热至设定温度。
2.开启模温机开关,调整温度至所需温度。
3.通过模具显示屏设置需要的温度控制值及时间。
4.使用时注意观察机器运行情况,特别是压力的变化。
当模具未加热完全时,不要进行注塑成型,这样会造成不良的成型效果。
5.使用完毕后将模具温度降至室温,关闭所有开关。
同时,在使用过程中要及时清洗冷却系统和降温水。
三、模温机的优点
1.能够提高成型效率,减少废品率。
2.能够改善产品的物理性能,提高生产效果。
3.提高对工人的安全保障,提升生产效率。
四、如何选择模温机?
1.根据生产量来选择模温机容量。
2.根据要加热的模具大小来选择加热功率。
3.根据该机器的耗电情况来选择正确的电源。
4.根据产品材质选择合适的冷却流量,减少生产成本。
模温机在注塑成型中的作用是非常重要的,能够提高成型效率,减少废品率,减少生产成本,降低工人工作负担。
因此,掌握模温机的使用方法和技巧是非常有必要的。
- 1、下载文档前请自行甄别文档内容的完整性,平台不提供额外的编辑、内容补充、找答案等附加服务。
- 2、"仅部分预览"的文档,不可在线预览部分如存在完整性等问题,可反馈申请退款(可完整预览的文档不适用该条件!)。
- 3、如文档侵犯您的权益,请联系客服反馈,我们会尽快为您处理(人工客服工作时间:9:00-18:30)。
第十章模温控制
模具温度对胶件的成型质量、成型效率有着较大的影响。
在温度较高的模具里,熔融胶料的流动性较好,有利于胶料充填型腔,获取高质量的胶件外观表面,但会使胶料固化时间变长,顶出时易变形,对结晶性胶料而言,更有利于结晶过程进行,避免存放及使用中胶件尺寸发生变化;在温度较低的模具里,熔融胶料难于充满型腔,导致内应力增加,表面无光泽,产生银纹、熔接痕等缺陷。
不同的胶料具有不同的加工工艺性,并且各种胶件的表面要求和结构不同,为了在最有效的时间内生产出符合质量要求的胶件,这就要求模具保持一定的温度,模温越稳定,生产出的胶件在尺寸形状、胶件外观质量等方面的要求就越一致。
因此,除了模具制造方面的因素外,模温是控制胶件质量高低的重要因素,模具设计时应充分考虑模具温度的控制方法。
10.1模具温度控制的原则和方式
10.1.1模具温度控制的原则
为了保证在最有效的时间内生产出高外观质量要求、尺寸稳定、变形小的胶件,设计时应清楚了解模具温度控制的基本原则。
(1)不同胶料要求不同的模具温度。
参见10.1.3节
(2)不同表面质量、不同结构的模具要求不同的模具温度,这就要求在设计温控系统时具有针对性。
(3)前模的温度高于后模的温度,一般情况下温度差为20~30º左右。
(4)有火花纹要求的前模温度比一般光面要求的前模温度高。
当前模须通热水或热油时,一般温度差为40º左右。
(5)当实际的模具温度不能达到要求模温时,应对模具进行升温。
因此模具设计时,应充分考虑胶料带入模具的热量能否满足模温要求。
(6)由胶料带入模具的热量除通过热辐射、热传导的方式消耗外,绝大部分的热量需由循环的传热介质带出模外。
铍铜等易传热件中的热量也不例外。
(7)模温应均衡,不能有局部过热、过冷。
10.1.2模具温度的控制方式
模具温度一般通过调节传热介质的温度,增设隔热板、加热棒的方法来控制。
传热介质一般采用水、油等,它的通道常被称作冷却水道。
降低模温,一般采用前模通“机水”(20ºC左右)、后模通“冻水”(4ºC左右)来实现。
当传热介质的通道即冷却水道无法通过某些部位时,应采用传热效率较高的材料(如铍铜等,模具材料的传热系数详见《塑料模具技术手册》第219页),将热量传递到传热介质中去,如图10.1.1,或者采用“热管”进行局部冷却。
升高模温,一般采用在冷却水道中通入热水、热油(热水机加热)来实现。
当模温要求较高时,为防止热传导对热量的损失,模具面板上应增加隔热板。
热流道模具中,流道板温度要求较高,须由加热棒加热,为避免流道板的热量传至前模,导致前模冷却困难,设计时应尽量减少其与前模的接触面。
10.1.3常用胶料的注射温度与模具温度
下表为胶件表面质量无特殊要求(即一般光面)时常用的胶料注射温度、模具温度,模具温度指前模型腔的温度。
10.2冷却系统设计
10.2.1冷却系统设计原则
(1)冷却水道的孔壁至型腔表面的距离应尽可能相等,一般取15~25mm ,如图10.2.1所示。
(2)冷却水道数量尽可能多,而且要便于加工。
一般水道直径选用∅6.0,∅8.0,∅10.0,两平行水道间距取
40~60mm ,如图10.2.1所示。
(3)所有成型零部件均要求通冷却水道,除非无位置。
热量聚集的部位强化冷却,如电池兜、喇叭位、厚 胶位、浇口处等。
A 板,B 板,水口板,浇口部分则视情况定。
(4)降低入水口与出水口的温差。
入水,出水温差会影响模具冷却的均匀性,故设计
时应标明入水,出水方向,模具制作时要求在模坯上标明。
.运水流程不应过长,防止造成出入水温差过大。
(5)尽量减少冷却水道中“死水”(不参与流动的介质)的存在。
(6)冷却水道应避免设在可预见的胶件熔接痕处。
(7)保证冷却水道的最小边距(即水孔周边的最小钢位厚度),要求当水道长度小于150mm 时,边间距大于3mm ;当水道长度大于150mm 时,边间距大于5mm 。
(8)冷却水道连接时要由“O ”型胶密封,密封应可靠无漏水。
密封结构参见10.2.2。
(9)对冷却水道布置有困难的部位应采取其它冷却方式,如铍铜、热管等 (10)合理确定冷却水接头位置,避免影响模具安装、固定。
10.2.2“O ”型密封圈的密封结构
常用“O ”型密封圈结构如图10.2.3所示。
可参见第十五章15.5节。
图10.2.1
图10.2.2
图10.2.3
常用密封结构如图10.2.4所示。
常用装配技术要求参见列表: 密封圈规格 装配技术要求 ØD Ød
ØD1 H
W
13.0 2.5 8.0 1.8
3.2
16.0 11.0 19.0 14.0 16.0 3.5 9.0 2.7
4.7
19.0 12.0 25.0 18.0
单位:mm 10.2.3冷却实例
(1)浅模腔冷却。
前模如图10.2.5所示,后模如图10.2.6所示。
图10.2.4
此间距须≥1mm
密封圈
电池盒镶件,采用水缸冷却
图10.2.5
为了使冷却水道的孔壁至型腔表面的距离应尽可能相等 此处有“死水”存在,应隔断
图10.2.6
采用“O ”型密封圈密封
标注出水口入水口
(2)深模腔冷却。
如图10.2.7所示。
(3)较小的高、长型芯冷却。
图10.2.8采用斜向交叉冷却水道;10.2.9采用套管形式的冷却水道。
(4)无法加工冷却水道的部位采用易导热材料传出热量。
如图10.2.10所示
冷却水道采用“水缸”形式
图10.2.7
图10.2.8 图10.2.9
套管
图10.2.10
型芯用导热率较
高的铍铜制作
由铍铜将热量
传到冷却介质
由冷却介质将
热量带出模外
(5)哈夫模冷却。
如图10.2.11所示。
哈夫块上开设冷却水道,模坯上开设出水、入水管道的避空槽。
(6)成型顶块冷却。
如图10.2.12所示。
在顶块的出水、入水管道的接口处开设避空槽,避空槽的大小应满足引水管在顶块顶出时的运动空间。
模坯上的避空槽
图10.2.11
成型顶块
避空槽
图10.2.12
顶块顶出
距离。