滑动轴承的故障诊断分析 (DEMO)
柴油机滑动轴承故障机理分析和对策 (1)

华中科技大学硕士学位论文柴油机滑动轴承故障机理分析和对策姓名:李红申请学位级别:硕士专业:动力工程指导教师:张宗杰20040509摘要滑动轴承是柴油机的重要组成部分,它的工作质量直接影响柴油机的可靠性,甚至寿命。
国内柴油机普遍存在烧连杆瓦故障,本文主要针对康明斯B系列柴油机出现的此类故障进行研究。
首先叙述柴油机滑动轴承的常见故障、材料、结构设计。
B系列柴油机连杆轴承主要故障表现为粘着磨损和磨料磨损,其次是疲劳磨损和少量的腐蚀磨损,最终在用户中体现的故障模式是连杆烧瓦或抱瓦。
论文论证滑动轴承故障产生的机理,进行滑动轴承负荷计算、流体动力润滑分析以及轴心轨迹计算,采用荷氏计算法,将康明斯B柴油机连杆轴承相关数据导入程序,得到轴承的负荷图、轴心轨迹图以及连杆大头磨损图。
对轴承的最大负荷区域、轴心轨迹进行分析,并比较了故障形态的统计数据,确定故障主要集中在用户使用的早期500公里到5000公晕期间,故障形态为轴承润滑不良,温度过高。
确定B系列柴油机连杆烧瓦故障的主要控制参数….润滑系统的清洁度、连杆轴承的最小间隙值、连杆大端的刚度和曲轴、连杆制造精度等。
通过对现有生产工艺加工的曲轴和连杆零件数据分析,发现实际加工零件尺寸存在偏态分布,配合间隙偏小,加工表面粗糙度偏大,找到了产生故障的根源,通过概率分析法,调整和改进生产工艺参数,同时辅之以公差中心控制图对现场加工过程进行控制,有效提高了孔轴的配合率,改进后的发动机在用户使用情况跟踪结果,连杆烧瓦故障从1999年单台赔偿44.05元下降到目前单台赔偿4.7元。
关键词:柴油机滑动轴承故障分析对策AbstractSlidebearingsareimportantintegralpartofthediesels.Theirworkwilldirectlyimpactonthereliability,eventhelifeofthediesels.Amongthedomesticdiesels.connectingrodbearingfailuresexistatlarge.ThispapermainlystudiessuchfailuresoccurredinCumminsBseriesdieselengines.Firstly,thefrequentfailures,material,designofslidebearingsaleintroduced.ThemainfailuresofconnectingrodbeatingsinBseriesenginesarepresentedasadheredwear,andabrasivewear.secondly,fatiguewear.andslightlycorrosionweal',thefailuremodesappearedinfinalcustomersareconnectingrodbearingburntorceased.Inordertodemonstratethemechanismofthefailures,theslidebearingloadcalculationandfluiddynamiclubricationanalysisandaxiscenteruackcalculationareproposed.He’Scalculationisdeterminedbyusingthetheory,inputtherelateddataofconnectingrodbearingsofBseriesenginesintotheHe’Sprogram,bearingloadchart,axiscentertrackchartandwearchartofbigendofconnectingrodscanbeoutputted.Byanalyzingmaximumloadareaofbearings,andaxiscentertrack,andcomparingthestatisticaldataofoccurredfailuremode,thefailuresaremainlyoccurredintheearlykilometersof500-5000.Thefailuremodesarebadlubricationandtemperatureriseofthebearings.ThisiStodeterminethemaincontrolparametersofbearingfailuresofBseriesengines一一cleanlinessoflubricationsystem,minimumclearanceofrodbearings,rigidityandbendofbigendofconnectingrod,andtheprocessingaccuracyofconnectingrodetc.Byanalyzingthedataofcrankshaftsmadebycurrenttechnology,andprocessingaccuracyofconnectingrods.It’Sfoundthatdeflectiondistributionexistedintheactualmachinedparts.Thematchingclearancearesmall,theroughnessonsurfacearebig,rootcausesofthefailurearefound.Byprobabilityanalysismethod,theproductionprocessingparametersareadjustedandimproved,andhavebeenmonitoredbycontrolchart,iteffectivelyimprovedthematchrateofholeandaxis.Trackingtheresultsafterimprovements,theclaimfortherodbearingfailureperenginewentdownto4.7Yuannow,comparedwith44.05in1999.Keywords:dieselengine,slidebearing,failure,analysis,countermeasures独创性声明本人声明所呈交的学位论文是我个人在导师指导下进行的研究工作及取得的研究成果。
叙述柴油机滑动轴承早期损坏的原因分析与对策

滑动轴承早期损坏的常见形式1.机械损伤滑动轴承机械损伤是指轴承的合金表面出现不同程度的沟痕,严重时在接触表面发生金属剥离以及出现大面积划伤。
一般情况下,接触面损伤与烧蚀现象同在。
造成轴承机械损伤的主霉原因是轴承表面难以形成油膜或油膜被严重破坏。
2.轴承穴蚀滑动轴承在气缸压力冲击载荷的反复作用下,表面层发生塑性变形和冷却硬化,局部丧失变形能力,逐步形成裂纹并不断扩展,随着磨屑的脱落,在受载表面层形成空穴。
一般发生穴蚀时,先出现陷坑,然后这种陷坑逐步扩大引起合金层界面开裂,裂纹沿着界面平行方向扩展,直到剥落为止。
滑动轴承穴蚀的主要原因是油槽和油孔等结构的横断面突然改变引起油液流动紊乱,在油流紊乱的真空区形成气泡,随后由于压力升高,气泡溃灭产生穴蚀。
穴蚀一般发生在轴承的高载区,比如曲轴主轴承下的轴瓦。
3.疲劳点蚀轴承疲劳点蚀是由于发动机超负荷工作,使轴承工作过热及轴承间隙过大,造成轴承中部疲劳损伤、疲劳点蚀或者疲劳脱落。
这种损伤的原因大多是因为超载、轴承间隙过大或者润滑油不清洁,混有异物所致,因此:使用时应该注意避免轴承超载工作,不要以过低或过高的转速运转;发动机怠速要调整到平稳状态;确保正常的轴承间隙,防止发动机转速过高或过低。
4.轴承合金腐蚀轴承合金腐蚀一般是因为润滑油不纯,受润滑油所含的化学杂质(酸性氧化物等)氧化轴承合金生成酸性物质,引起轴承合金部分脱落,形成无规则的微小裂孔或小陷坑。
5.轴承饶熔轴颈和轴承的摩擦副之间有微小的突起金属面直接接触,形成局部高温,在润滑不足、冷却不良的情况下,轴承合金发黑或局部烧熔。
造成轴承合金发黑或局部烧熔常为轴颈与轴承配合过紧所致,润滑油压力不足也容易烧毁轴承。
6.轴承走外圆轴承走外圆就是轴承在座孔内有相对的转动。
轴承走外圆,不仅影响轴承的散热,容易使轴承内表面合金烧蚀,而且会使轴承背面损伤,严重时烧毁轴承。
其主要原因是轴承过短、加工或者安装不符合规范等。
滑动轴承早期损坏的原因分析1.颗粒物造成的早期损坏1)微小颗粒异物导致的轴承早期损坏是由微小颗粒杂质进人轴承合金层的运动表面造成的,虽然对轴承没有造成严重的损伤,但是此类现象若继续展下去,不但导致轴承早期损坏,轴也会受到严重的损伤,所以必须根据故障的原因及时排除,避免造成零件损坏。
发动机滑动轴承损坏原因汇总,有用

发动机滑动轴承损坏原因汇总,有用法律顾问:赵建英律师轴承是当代机械设备中一种重要零部件。
用于支撑机械旋转体,降低其运动过程中的摩擦系数。
按照摩擦性质的不同轴承可分为滚动轴承和滑动轴承两大类,发动机上的滑动轴承在在使用过程中由于设计参数、制造工艺和使用环境的不同,经常出现各种形式的失效而使其过早损坏。
那么它们到底是怎么损坏的呢?下面我们来详细分析一下。
1、机械损伤滑动轴承机械损伤是指轴瓦的合金表面出现不同程度的沟痕,严重时在接触表面发生金属剥离以及出现大面积的杂乱划伤;一般情况下,接触面损伤与烧蚀现象同时存在。
造成轴承机械损伤的主要原因是轴承表面难以形成油膜或油膜被严重破坏。
2、轴承穴蚀滑动轴承在气缸压力冲击载荷)的反复作用下,表面层发生塑性变形和冷作硬化,局部丧失变形能力,逐步形成纹并不断扩展,然后随着磨屑的脱落,在受载表面层形成穴。
一般轴瓦发生穴蚀时,是先出现凹坑,然后这种凹坑逐步扩大并引起合金层界面的开裂,裂纹沿着界面的平行方向扩展,直到剥落为止。
滑动轴承穴蚀的主要原因是,由于油槽和油孔等结构要素的横断面突然改变引起油流强烈紊乱,在油流紊乱的真空区形成气泡,随后由于压力升高,气泡溃灭而产生穴蚀。
穴蚀一般发生在轴承的高载区,如曲轴主轴承的下轴瓦上。
3、疲劳点蚀轴承疲劳点蚀是指,由于发动机超负荷工作,使得轴承工作过热及轴承间隙过大,造成轴承中部疲劳损伤、疲劳点蚀或者疲劳脱落。
这种损伤大多是因为超载、轴承间隙过大,或者润滑油不清洁、内中混有异物所致。
因此,使用时应该注意避免轴承超载工作不要以过低或过高的转速运转;怠速时要将发动机调整到稳定状态;确保正常的轴承间隙,防止发动机转速过高或过低;检查、调整冷却系统的工作情况,确保发动机的工作温度适宜。
4、轴承合金腐蚀轴承合金腐蚀一般是区为润滑油不纯,润滑油中所台的化学杂质(酸性氧化物等)使轴承合金氧化而生成酸性物质,引起轴承合金部分脱落,形成无规则的微小裂孔或小凹坑。
轴承故障分析报告

轴承故障分析报告一、背景介绍轴承是各种旋转机械中重要的部件之一,它承受了机械旋转运动的负载和传动力,起到支撑和减少摩擦的作用。
然而,由于各种原因,轴承可能会出现故障,导致机械设备的运行不稳定甚至完全停止。
本报告旨在对轴承故障进行深入分析,以便于找到准确的故障原因,并提出有效的解决方案。
二、故障现象描述轴承故障表现为摩擦、振动、噪音、过热等现象,严重时会引发机械设备的停机。
根据收集到的数据和实验观测,我们对轴承故障的主要表现进行了详细描述和分析。
1. 摩擦:轴承故障常会导致摩擦增加,表现为机械设备运行时需要更大的驱动力,摩擦力增大,导致设备运转困难。
2. 振动:轴承在故障时容易产生振动,振动幅度与故障严重程度相关。
振动会产生共振效应,进一步损坏轴承及周围零部件。
3. 噪音:轴承故障还会引起设备噪音的增加,噪音的音量和频率可能随故障类型和程度而变化。
噪音不仅影响设备正常运行,还会给操作者带来不适。
4. 过热:当轴承故障时,摩擦产生的热量不容易散发,会导致轴承和周围零部件温度升高。
长时间高温运行会导致轴承材料变形、润滑油变质等,从而进一步加速轴承的损坏。
三、故障原因分析根据现场检查、数据分析和历史经验,我们对轴承故障的原因进行了深入分析。
1. 润滑不良:当轴承润滑不足时,摩擦增大,易引发故障。
例如,润滑油过少、过期或污染严重,都会导致润滑效果下降,增加轴承故障的风险。
2. 轴承安装不当:轴承安装时若不符合规范,也容易引发故障。
例如,轴承严重偏心、过紧或过松的安装都会导致轴承运行不稳,容易损坏。
3. 轴承质量问题:低质量轴承在生产、选配或运输过程中可能出现各种缺陷,加速了其寿命的衰减。
因此,轴承质量问题可能是轴承故障的主要原因之一。
4. 过载运行:当机械设备长时间以及超过设计负荷运行时,轴承容易承受过大的力,造成轴承过早磨损和故障。
四、解决方案提议针对轴承故障的原因,我们提出以下解决方案以预防和解决轴承故障。
轴承故障诊断 PPT
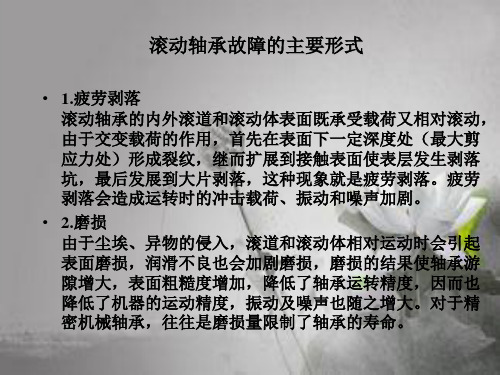
诊断特征
• 1、频谱和波形特征 • (1)径向振动在轴承故障特征频率(见下面说明部分)
及其低倍频处有峰。若有多个同类故障(内滚道、外滚道、 滚子……),则在故障特征频率的低倍频处有较大的峰。 • (2)内滚道故障特征频率处有边带,边带间隔为1×RPM。 • (3)滚动体故障特征频率处有边带,边带间隔为保持架 故障特征频率。 • (4)在加速度频谱的中高频区域若有峰群突然生出(下 图所示),表明有疲劳故障。 • (5)径向振动时域波形有重复冲击迹象(有轴向负载时, 轴向振动波形与径向相同),或者其波峰系数大于5,表 明故障产生了高频冲击现象。
• 由表7-9可知,3号机测点①处振动大,比1号机 和2号机相同部位大得多,初步估计测点①处轴 承有问题。
• 对测点①振动波形的包络信号作功率谱分析(图 7-25),分析频率500Hz,400谱线,功率谱。计 算该测点轴承特征频率(R=1480r/min, D=122.5mm,d=22mm,N=11,α=10°)为:
–(1)轴承外圈一阶径向固有振动,其频带在(1-8 ) kHz范围类。如离心泵、风机、轴承试验机这类简单机 械的滚动轴承故障诊断中,这是一种方便的诊断信息。
–(2)轴承其他元件的固有振动。其频带在(20-60) kHz范围内,能避开流体动力噪声,信噪比高。
–(3)加速度传感器的一节固有频率,合理利用加速度 传感器(安装)系统的一节谐振频率作为监测频带,常 在轴承故障信号提取中受到良好效果,其频率范围通常 选择在10kHz左右。
滚动轴承故障的主要形式
• 1.疲劳剥落 滚动轴承的内外滚道和滚动体表面既承受载荷又相对滚动, 由于交变载荷的作用,首先在表面下一定深度处(最大剪 应力处)形成裂纹,继而扩展到接触表面使表层发生剥落 坑,最后发展到大片剥落,这种现象就是疲劳剥落。疲劳 剥落会造成运转时的冲击载荷、振动和噪声加剧。
滑动轴承的失效分析概论(写的很好)
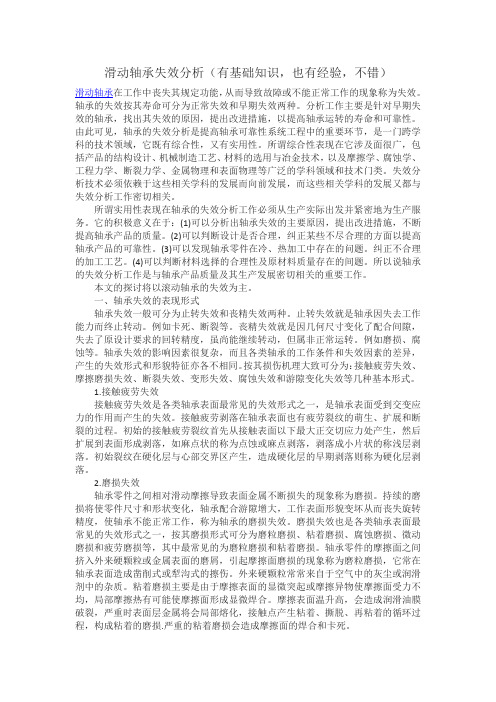
滑动轴承失效分析(有基础知识,也有经验,不错)滑动轴承在工作中丧失其规定功能,从而导致故障或不能正常工作的现象称为失效。
轴承的失效按其寿命可分为正常失效和早期失效两种。
分析工作主要是针对早期失效的轴承,找出其失效的原因,提出改进措施,以提高轴承运转的寿命和可靠性。
由此可见,轴承的失效分析是提高轴承可靠性系统工程中的重要环节,是一门跨学科的技术领域,它既有综合性,又有实用性。
所谓综合性表现在它涉及面很广,包括产品的结构设计、机械制造工艺、材料的选用与冶金技术,以及摩擦学、腐蚀学、工程力学、断裂力学、金属物理和表面物理等广泛的学科领域和技术门类。
失效分析技术必须依赖于这些相关学科的发展而向前发展,而这些相关学科的发展又都与失效分析工作密切相关。
所谓实用性表现在轴承的失效分析工作必须从生产实际出发并紧密地为生产服务。
它的积极意义在于:(1)可以分析出轴承失效的主要原因,提出改进措施,不断提高轴承产品的质量。
(2)可以判断设计是否合理,纠正某些不尽合理的方面以提高轴承产品的可靠性。
(3)可以发现轴承零件在冷、热加工中存在的问题。
纠正不合理的加工工艺。
(4)可以判断材料选择的合理性及原材料质量存在的间题。
所以说轴承的失效分析工作是与轴承产品质量及其生产发展密切相关的重要工作。
本文的探讨将以滚动轴承的失效为主。
一、轴承失效的表现形式轴承失效一般可分为止转失效和丧精失效两种。
止转失效就是轴承因失去工作能力而终止转动。
例如卡死、断裂等。
丧精失效就是因几何尺寸变化了配合间隙,失去了原设计要求的回转精度,虽尚能继续转动,但属非正常运转。
例如磨损、腐蚀等。
轴承失效的影响因素很复杂,而且各类轴承的工作条件和失效因素的差异,产生的失效形式和形貌特征亦各不相同。
按其损伤机理大致可分为:接触疲劳失效、摩擦磨损失效、断裂失效、变形失效、腐蚀失效和游隙变化失效等几种基本形式。
1.接触疲劳失效接触疲劳失效是各类轴承表面最常见的失效形式之一,是轴承表面受到交变应力的作用而产生的失效。
滑动轴承常见故障及解决方法
滑动轴承常见故障及解决方法【摘要】滑动轴承是机器中应用很广泛的一种传动,其工作平稳、可靠、无噪声。
但在运行过程中常见故障很多,影响设备的正常运行。
因此,总结故障原因,找出消除故障的解决方案和预防措施,从而可以达到设备正常运行,降低维修率,提高企业的经济效益。
【关键词】异常磨损;巴氏合金;轴承疲劳;轴承间隙巴氏合金是滑动轴承常用材料之一,因其独特的机械性能,很多旋转机械广泛采用为滑动轴承材料。
在日常工作中发现因滑动轴承故障导致停产,造成很大损失的情况时常发生。
总结积累经验,参考有关书目知识,对巴氏合金轴承故障因素及解决方法作以简要论述。
一、巴氏合金松脱巴氏合金松脱原因多产生于浇注前基体金属清洗不够,材料挂锡,浇注温度不够。
当巴氏合金与基体金属松脱时,轴承就加速疲劳,润滑油窜入松脱分离面,此时轴承将很快磨损。
解决方法:重新挂锡,浇注巴氏合金。
二、轴承异常磨损轴径在加速启动跑合过程中,轻微的磨合磨损和研配磨损都属正常。
但是当轴承存在下列故障时,将出现不正常或严重磨损。
1、轴承装配缺陷。
轴承间隙不适当,轴瓦错位,轴径在轴瓦中接触不良,轴径在运行中不能形成良好油膜,这些因素可引起转子振动和轴瓦磨损。
解决方法:更换轴承或重新修刮并做好标记,重新装配,使其达到技术要求。
2、轴承加工误差。
圆柱轴承不圆,多油楔轴承油楔大小和分布不当,轴承间隙过大或过小,止推轴承推力盘端面偏摆量超差、瓦块厚薄不均,都能引起严重磨损。
解决方法:采用工艺轴检测修理轴承瓦不规则形状。
3、转子振动。
由于转子不平衡、不对中,油膜振荡、流体激进等故障,产生高振幅,使轴瓦严重磨损、烧伤、拉毛。
解决方法:消除引起振动因素,更换已磨损轴承。
4、供油系统问题。
供油量不足或中断,引起严重摩擦、烧伤及抱轴。
解决方法:解决供油系统问题,清洁或更换油液,修理或加大冷却器,以降低油温。
三、轴承疲劳引起轴承疲劳有以下原因:1、轴承过载,使承载区油膜破裂,局部地区产生应力集中,局部接触裂纹,扩展后产生疲劳破坏。
轴承损坏形式及原因分析
浅的坑痕,呈结晶壮的破坏壮。这是 由于润滑不良所致。例如;少油或由 于温升所造成的黏度改变,使油膜无 法将接触面分离,表面有瞬间的接触。 办法:改善润滑。
精选可编辑ppt
10
9) 微动腐蚀
轴承环与轴或轴承箱之间有相对 运动才发生的现象。这是由于太松的 配合或轴承座变形所致。
由的旋转。
精选可编辑ppt
23
10.具有两个或多个轴承的轴心耦合时,产生不正确的直线偏差或角度 歪斜。 对策;由调整片来调整正确的对位,确保轴心耦合在一条直线上, 尤其是当轴上同时有三个或多个轴承运转时,更得注意。
11.轴的直径过大,导致内环膨胀过多,减少轴承间隙。 对策: 1)研磨轴径,使轴与轴承内环之间获得一适当的配合。 2) 改用径向间隙大的轴承。
7.安装轴承前轴承箱内的碎片,异物没有清除干净。 对策:仔细清洗轴承箱和轴承本身。
8.(交叉定位) 同一轴上有两个定位轴承,而引起的不对正或由于轴热膨胀而导致 轴承内部间隙不足。 对策:调整轴承箱与端盖之间的调整垫片,使轴承箱与外环之间有 一定的间隙。
9. 轴肩摩擦到轴承密封盖,轴肩部直径不正确与保持架摩擦。 对策:重新加工轴肩,检查肩部直径及圆角。
精选可编辑ppt
26
10.外环与轴承箱扭曲,轴与内环扭曲。是由于箱孔圆角过大;没有足 够的支撑。轴肩圆角过大,没有足够支撑,两端面靠不实。 对策:重新加工箱孔圆角和轴肩的圆角。
11.不正确的安装方式,用锤直接敲到轴承上,导致轴承工作表面有磕 伤。 对策:选择正确的安装方法:套筒法、加热法、油压法等。
精选可编辑ppt
2
3、轴承的受力痕迹
通常轴承在运转工作一段时间后,在工作表面都会有明显的 受力痕迹,并非所有的痕迹的出现就表示轴承坏掉了,轴承在正常
滑动轴承性能分析和检测方法
滑动轴承性能分析和检测方法滑动轴承是工程机械上的重要部件之一,安装不佳会影响其使用效果,甚至造成工程机械设备的故障。
在轴承安装上了之后,如果不仔细进行调准,校直可能导致TIMKEN轴承遭受另外的载荷,摩擦和振动。
这些可能加速疲劳和减少轴承的使用寿命,并且可能会损坏其它机器零件的使用期限。
此外,增加的振动和摩擦可能极大增加能源消耗和过早的失效风险。
如果轴承内有铁屑、毛刺、灰尘等异物进入,将使轴承在运转时产生噪声与振动,甚至会损伤滚道和滚动体。
所以在安装轴承前,必须确保安装表面和安装环境的清洁。
润滑对滑动轴承的运转及寿命有极为重要的影响。
润滑脂由基础油、增稠剂及添加剂制成。
润滑脂的性能主要由基础油决定。
一般低粘度的基础油适用于低温、高速;高粘度的适用于高温、高负荷。
增稠剂也关系着润滑性能,增稠剂的耐水性决定润滑脂的耐水性。
原则上,牌子不同的润滑脂不能混合,而且,即使是同种增稠剂的润滑脂,也会因添加剂不同相互带来坏影响。
轴承表面涂有防锈油,必须用清洁的汽油或煤油仔细清洗,再涂上干净优质或高速高温的润滑油脂方可安装使用。
全封闭轴承不须清洗加油。
在使用期间,要经常对轴承运行的基本外部条件进行监测,譬如温度,振动和噪音的测量等等。
这些有规律的检查将及早发现潜在的问题并将防止出现意想不到的机器中止现象,使生产计划得以实现,提高的工厂生产力和效率。
在运作过程中,轴承要求有正确的再次润滑,完美它的表现。
滑动轴承润滑的方法,分为脂润滑和油润滑。
为了使轴承很好地发挥机能,首先,要选择适合使用条件、使用目的的润滑方法。
若只考虑润滑,油润滑的润滑性占优势。
但是脂润滑有可以简化轴承周围结构的特长。
当我们在使用滑动轴承的时候,如果发现其温度很高的情况下,则赶紧停止设备运转,然后找出其原因,并按照上述提供的解决方案进行处理,但是可能因轴承发热的原因不同,所以解决的方式也不同,所以还是要具体情况具体对待,在技术人员的帮助下完成。
滑动轴承的检修
二、滑动轴承的检修工艺
2.轴瓦的刮研
轴瓦的刮研就是根据轴瓦与轴颈的配合要求来对轴瓦表面 进行刮研加工。重新浇铸乌金的轴瓦在车削之后、使用前 要进行刮研。
(1)检查轴瓦与轴颈的配合情况。将轴瓦内表面和轴颈擦 干净,在轴颈上涂薄薄一层红油(红丹粉与机油的混合物), 然后把轴瓦扣放在轴颈处,用于压住轴瓦, 同时周向对轴颈 做往复滑动,往复数次后将轴瓦取下,查看瓦面。此时瓦表 面有的地方有红油点,有的地方有黑点,有的地方呈亮光。 无红油处表明轴瓦与轴颈没有接触,间隙较大;红点表明二 者虽无接触,但间隙较小;黑点表明它比红点高,轴瓦与轴略 有接触;而亮点表明接触最重,亦即最高点,经往复研磨,发 出了金属光泽。
二、滑动轴承的检修工艺
一、轴瓦的检查及刮研
1.轴瓦缺陷的检查
轴承解体后,用煤油、毛刷和破布将轴瓦表面清洗干净, 然后对轴瓦表面做外观检查,看乌金层有无裂纹、砂眼、重 皮和乌金剥落等缺陷。 将手指放到乌金与瓦壳结合处,用小锤轻轻敲打轴瓦,如结 合处无振颤感觉且敲打声清脆无杂音,则表明乌金与瓦亮无 分离。还可用渗油法进行检查,即将轴瓦浸于煤油中3~ 5min,取出擦干后在乌金与瓦衬结合缝处涂上粉笔末,过一 会儿观察粉末处是否有渗出的油线,如无则表明结合良好, 钨金与瓦壳没有分离。
二、滑动轴承的检修工艺
(2)根据配合情况刮削轴瓦。现场多用手工方法对轴瓦进行 刮削,使用工具为柳叶刮刀或三角刮刀。刮削是针对瓦面上 的亮点、黑点及红点,无红油瓦无须刮削。对亮点下刀要重 而不僵,刮下的乌金厚且呈片状;对黑点下刀要轻,刮下的乌 金片薄且细长;对红点则轻轻刮挑,挑下的乌金薄且小刮刀 的刀痕下一遍要与上一遍呈交叉状态,形成网状,使轴承运 行时润滑油的流动不致倾向一方,这就完成轴瓦的第一次刮 削。
- 1、下载文档前请自行甄别文档内容的完整性,平台不提供额外的编辑、内容补充、找答案等附加服务。
- 2、"仅部分预览"的文档,不可在线预览部分如存在完整性等问题,可反馈申请退款(可完整预览的文档不适用该条件!)。
- 3、如文档侵犯您的权益,请联系客服反馈,我们会尽快为您处理(人工客服工作时间:9:00-18:30)。
滑动轴承的故障诊断分析一、滑动轴承的分类及其特点1、静压轴承静压轴承的间隙只影响润滑油的流量,对承载能力影响不大,因此、静压轴承可以不必调整间隙,静压轴承在任何转速下都能保证液体润滑,所以理论上对轴颈与轴瓦的材料无要求。
实际上为防止偶然事故造成供油中断,磨坏轴承轴承,轴颈仍用45#,轴瓦用青铜等。
2、动压轴承动压滑动轴承必须在一定的转速下才能产生压力油膜。
因此、不适用于低速或转速变化范围较大而下限转速过低的主轴。
轴承中只产生一个压力油膜的单油楔动压轴承,当载荷、转速等条件变化时,单油楔动压轴承的油膜厚度和位置也随着变化,使轴心线浮动,而降低了旋转精度和运动平稳性。
多油楔动压轴承一定的转速下,在轴颈周围能形成几个压力油楔,把轴颈推向中央,因而向心性好。
异常磨损:由于安装时轴线偏斜、负载偏载、轴承背钢与轴承座孔之间有硬质点和污物,轴或轴承座的刚性不良等原因,造成轴承表面严重损伤。
其特征为:轴承承载不均、局部磨损大,表面温度升高,影响了油膜的形成,从而使轴承过早失效。
二、常见的滑动轴承故障●轴承巴氏合金碎裂及其原因1.固体作用:油膜与轴颈碰摩引起的碰撞及摩擦,以及润滑油中所含杂质(磨粒)引起的磨损。
2.液体作用:油膜压力的交变引起的疲劳破坏。
3.气体作用:润滑膜中含有气泡所引起的汽蚀破坏。
●轴承巴氏合金烧蚀轴承巴氏合金烧蚀是指由于某种原因造成轴颈与轴瓦发生摩擦,使轴瓦局部温度偏高,巴氏合金氧化变质,发生严重的转子热弯曲、热变形,甚至抱轴。
当发生轴承与轴颈碰摩时,其油膜就会被破坏。
摩擦使轴瓦巴氏合金局部温度偏高,而导致巴氏合金烧蚀,由此引起的轴瓦和轴颈的热胀差,进一步加重轴瓦和轴颈的摩擦,形成恶性循环。
当轴瓦温度T大于等于230°C时,轴承巴氏合金就已烧蚀。
三、机理分析大多滑动轴承由于运行过程中处于边界润滑状态所以会产生滑动摩擦现象,同时又居有一定的冲击能量和势能,所以存在与产生滑动摩擦和碰摩相同的故障机理。
由于故障振动频率特征不明显,往往容易与其它的故障相混淆,如部件松动等。
而且会随着故障的不同阶段和产生主要故障因素的不同而有所区别。
它的故障状态与多种故障的形式相似,故障严重时同时会有不平衡、不对中、松动、碰摩、共振(低频、高频)等故障特征现象显示。
但其特征频率多与工频及其谐波有关,其主要振动特征为频谱的非线性表现。
转子与轴瓦发生摩擦时,在径向接触瞬间,转子的刚度增大,被轴瓦反弹后脱离接触,转子刚度减小,并且发生横向自由振动。
因此,转子刚度在接触与非接触两者之间变化,变化的频率就是转子的涡动频率。
转子横向自由振动与强迫的旋转运动、涡动运动叠加在一起就会产生一些特有的,复杂的振动响应的频率。
随着摩擦副的间隙增大,将产生更大的冲击和轴旋转中心的偏移。
所以利用与正常时的标准频谱对比,对于判断故障发展过程极其有利。
四、滑动轴承的振动诊断方法1、通频(相对较宽频率范围,下同)振动总值的越线诊断检测积累正常状态下的滑动轴承振动信号,计算其通频的振动总值的的门限值,当此值大于某一门栏时,将被检轴承判断为有故障。
2、特征频率诊断对检测得到的滑动轴承振动信号进行频谱分析,根据此频谱和滑动轴承正常时的振动频谱(标准谱)之间的差异,和差异处的频率成分与振源频率之间的对应关系确定故障的有无、程度、类别和原因。
一般滑动轴承特征为工频及其谐波占主导位置,工频较大说明有较大的偏心(非质量不平衡原因),若时域波形同时存在不对称,说明有碰摩或产生比较连续的摩擦现象。
连续的偏摩会显示很大的工频,同时也会有一些谐波存在。
有轴承不对中时还会随着温度的上升,振动值也同时升高,由于约束条件的不同,尤其在设备的非驱动端轴承反映明显。
振动值一般水平方向较垂直方向大。
(由于支承刚度的不同)3、振动形态诊断观察变速过程中的滑动轴承振动信号的通频幅值随转速的变化的规律,从而区别被检轴承的振动究竟是受迫振动(包括共振)还是自激振动。
振动形态诊断法常作为特征频率诊断法的一种辅助诊断手段。
4、轴心轨迹诊断时域波形中的直流成分显示的为轴心的位置。
连续的直流成分的改变即为旋转轴的轴心位置轨迹图。
5、滑动轴承其它说明引起较大振动的滑动轴承存在的问题通常是轴承间隙过大,松动(轴承体内巴氏合金松动)或摩擦等等。
间隙过大的滑动轴承,可能出现小的不平衡、不同轴或其它某些振动力,引起机械松动或冲击。
大量实践经验表明:已经磨损的轴承,通过对在水平和垂直方向上测得的振幅进行比较,可以识别出来。
当轴承磨损之后,通常其垂直方向的振幅很少比水平方向的振幅大。
滑动轴承磨损的最后阶段将会产生轴频的及其谐波振动。
五、滑动轴承的故障分析故障诊断过程实际上是一个从状态信号中提取故障信息特征形成待检模式与基准模式(故障档案)进行比较的模式或分类过程。
由此可知,建立滑动轴承各种常见故障档案库(即各类故障的基准模式库)自然就成为滑动轴承故障诊断技术研究中的首要工作。
而弄清滑动轴承的各种失效及故障形式以及与之相应的状态特征,则是建立滑动轴承故障档案库的基础。
滑动轴承偏离、轴承不对中会引起偏摩或偏摆现象,产生与摩擦相同的现象。
连续摩擦会以工频为主,间断摩擦会产生碰摩特征。
在大中型机械设备上,一般采用滑动轴承的较多,其主要故障是磨损与松动。
由于轴系的不平衡,不对中以及轴承本身安装不良而导致轴承的承压不均匀,油膜破裂等。
滑动轴承磨损是由运动表面的相对摩擦造成的。
摩擦激发一种高频振动和噪声,对其信号作频谱分析时,会发现整个频带的分量均被提高了,并且在高频段上出现峰值,这些峰值的大小与摩擦的严重程度成正比。
一般滑动轴承的摩擦与松动和轴不平衡,不对中等故障状态有密切的关系。
因此在振动的频谱图上常出现转频的一阶、二阶、三阶以及高阶分量。
滑动轴承由于摩擦引起的振动类似于有缺陷的滚动轴承引起的振动。
当出现摩擦引起的振动特征时,依次检查润滑、润滑系统和轴承间隙。
这种状态也可出现在轴承间隙过大或间隙不足的情况。
轴系弯曲、轴承不对中会在轴的非驱动端产生更大的冲击,这是因为驱动端相对来讲能够受的更大的约束,而非驱动端相对小些,振动能量只能在非驱动端释放。
所以一般非驱动端容易损坏轴承因考虑是否存在轴的弯曲现象或轴承不对中。
滑动轴承的破坏是由于轴系不对中,轴承载荷的变化,油膜振荡等引起轴承座的振动。
这些振动可导致油膜的破坏,轴瓦烧损和碎裂,轴承座产生裂纹等。
对于两端轴承有比较严重的不对中会对转子产生比较大的交变应力,容易使转子产生疲劳破坏。
滑动轴承不对中转子振动的非线性特性:由于不对中,滑动轴承的静油膜力与轴颈的偏心率存在非线性关系。
此外附加力和力矩是轴颈位移和速度的非线性函数。
在简谐激振力F cosωt 作用下的非线性系统,受迫振动的响应除同步响应外,还有高次谐波与分数谐波响应。
高次谐波响应在非线性系统中或多或少地存在,而分数谐波响应则只在一定条件下才能产生。
含有基频和高次谐波的成分,又含有ω/2 次谐波是典型轴承失稳特例.六、轴承不对中的特性1、由于轴承不对中造成各轴承负荷分配变化和轴承的动态特性变化,从而影响整个转子—轴承系统的稳定性。
2、由于支承负荷变化,造成轴承临界转速的变化,激发结构共振。
3、轴承不对中会导致高压汽轮机汽封间隙不均匀诱发间隙激振。
4、在不对中的一对轴承中,负荷大的轴承油膜呈现较大的非线性,在不平衡扰动力作用下,在一定条件下,可导致转子振动出现分数谐波和高次谐波响应。
5、轴承不对中,使转轴受外部预载,通过联轴器施加于转轴的力严重时,可使联轴器截面突变处产生疲劳裂纹。
6、由于轴承不对中导致转子产生低频涡动,轴心的涡动位移与转子的周期性弯曲产生交变应力,此交变应力的频率等于转动频率与涡动频率之差。
当变形超过某个值,转轴弯曲最大处就会产生疲劳裂纹。
7、由于支承负荷变化造成工作转速下轴承振型的变化。
松动一般不应有明显的冲击现象,而碰摩有明显的冲击,两者可从时域波形中加以区别。
碰摩在时域波形中应是逐渐衰减的。
摩擦会激励零部件共振,产生有色噪声,没有大的冲击波形;而随机噪声为白噪声信号。
动压滑动轴承间隙过大诊断要点a)确认频谱中有稳定的1、2或3倍频分量占优势。
垂直方向比水平振动更大。
相对较小的4-10倍频分量,可能也会较明显。
b)检查轴向振动,可能与径向频谱类似。
如果轴向振动与径向振动大小相近,表明问题严重。
c)径向和轴向时域波形为稳定的周期波形占优势,每转一周有1、2或3个峰值。
没有大的加速度冲击。
提示:间隙过大与不对中的区分可以根据以下两点:i.间隙过大时垂直振动比水平振动更大;而不对中时垂直与水平振动基本相同。
轴瓦松动时转子振幅增大,振动频率为二倍频。
ii. 间隙过大时4-10倍频分量比较显著,类似于机械松动的现象;而不对中时高次谐波较小。
间隙过大与机械松动的区分可以根据以下两点:i.隙过大时,其时域波形为稳定的周期波形占优势,没有大的加速度冲击现象;而机械松动时其时域波形较为杂乱,有明显的非周期信号使波形很不稳定。
ii.间隙过大时轴向振动可能较大,特别是止推轴承;而机械松动时一般轴向振动较小。