缺陷与无损检测方法对照表
金属材料缺陷检测与无损评估方法研究

金属材料缺陷检测与无损评估方法研究近年来,金属材料作为工业生产中不可或缺的材料,在各个领域广泛应用。
然而,金属材料在使用过程中可能会出现各种缺陷,如裂纹、腐蚀、疲劳等,这些缺陷会对金属材料的性能和寿命产生严重影响,甚至会引发事故。
因此,对金属材料的缺陷进行准确的检测和无损评估就显得尤为重要。
一、金属材料缺陷检测方法1. 目测检测方法:目测检测方法是最简单、直观的检测方法之一,适用于一些表面缺陷的检测。
通过肉眼观察金属材料的外观,如表面颜色、形状等,来判断是否存在缺陷。
这种方法操作简单、成本低,但只适用于检测一些比较明显的缺陷。
2. 超声波检测方法:超声波检测是一种常用的无损检测方法,能够全面、有效地检测金属材料内部的缺陷。
在超声波检测中,通过超声波发射和接收器件,对金属材料进行扫描,根据超声波在材料内部的传播速度和反射强度来判断是否存在缺陷。
这种方法具有高灵敏度、高准确性的特点,可以检测到微小的缺陷。
3. 磁粉检测方法:磁粉检测是一种常用的金属材料缺陷检测方法,适用于检测表面和近表层存在的裂纹、焊接缺陷等。
在磁粉检测中,通过在金属材料表面施加磁场,再撒上带有磁粉的粉末,通过观察磁粉在缺陷处的分布情况,来判断是否存在缺陷。
这种方法操作简单、成本较低,但只适用于表面和近表层的缺陷检测。
二、金属材料缺陷无损评估方法1. 声发射检测方法:声发射检测是一种通过检测材料在受力后产生的声波信号来评估缺陷的方法。
在金属材料受力或变形时,缺陷会引起局部应力集中,从而产生声波信号。
通过对这些声波信号的分析,可以评估材料的缺陷性质、位置和严重程度。
与其他方法相比,声发射检测具有非接触、实时、高灵敏度等优点。
2. 磁记忆检测方法:磁记忆检测是一种通过检测材料的磁矩分布变化来评估缺陷的方法。
在金属材料中存在缺陷时,缺陷会引起磁矩分布的变化,通过在材料表面布置磁传感器,可以监测磁场的变化,从而评估缺陷的位置和严重程度。
这种方法具有快速、高效、无损伤的特点,适用于对金属材料进行在线无损评估。
表7.6五种常用无损检测方法的对照表

表7.6五种常用无损检测方法的对照表
在压力容器制造过程中,各种无损检测方法的选择,首先要满足国家的有关规程,标准的要求.也必须按照有关技术文件,如:图纸和技术协议的要求,满足其探伤的比例.合格等级检测时的检测时机等.
无损检测责任工程师在制造和检修工作中,除完成上述必要的检测项目外,有时必须根据工作需要增加检测方法和手段来进一步对缺陷进行判断.我们除应掌握常规无损检测方法各自的特点及其适应性,而且也必须了解其他检测方法和手段特点帮助我们来提高检测结果的可靠性.
无损检测所利用的基本原理都可以归纳为材料内部组织的不连续性和几何形状发生变化,会引起各种物理量的变化.反过来根据物理量的变化大小来推断试件内部组织的不连续性和几何形状的变化.然而,物理量的变化的原因很复杂,往往与试件内部的变化无法一一应对.所以我们必须综合考虑几种物理量的变化.才能对试件内部的异常作出正确的判断.我们有时应根据几种无损检测方法检测的结果进行综合分析判断,最终来确定缺陷,并对缺陷进行定性.
定量.定位分析.。
焊缝内部缺陷无损检测方法的应用对比研究
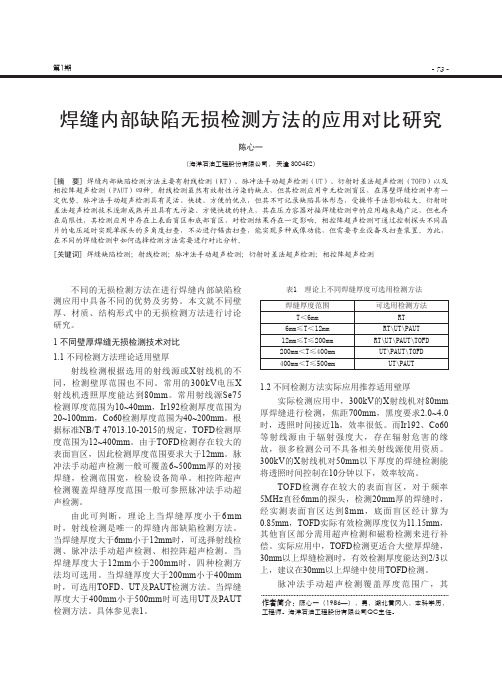
- 73 -第1期焊缝内部缺陷无损检测方法的应用对比研究陈心一(海洋石油工程股份有限公司, 天津 300452)[摘 要] 焊缝内部缺陷检测方法主要有射线检测(RT)、脉冲法手动超声检测(UT)、衍射时差法超声检测(TOFD)以及相控阵超声检测(PAUT)四种。
射线检测虽然有放射性污染的缺点,但其检测应用中无检测盲区,在薄壁焊缝检测中有一定优势。
脉冲法手动超声检测具有灵活、快捷、方便的优点,但其不可记录缺陷具体形态,受操作手法影响较大。
衍射时差法超声检测技术逐渐成熟并且具有无污染、方便快捷的特点,其在压力容器对接焊缝检测中的应用越来越广泛,但也存在局限性,其检测应用中存在上表面盲区和底部盲区,对检测结果存在一定影响。
相控阵超声检测可通过控制探头不同晶片的电压延时实现单探头的多角度扫查,不必进行锯齿扫查,能实现多种成像功能,但需要专业设备及扫查装置。
为此,在不同的焊缝检测中如何选择检测方法需要进行对比分析。
[关键词] 焊缝缺陷检测;射线检测;脉冲法手动超声检测;衍射时差法超声检测;相控阵超声检测作者简介:陈心一(1986—),男,湖北黄冈人,本科学历,工程师。
海洋石油工程股份有限公司QC主任。
不同的无损检测方法在进行焊缝内部缺陷检测应用中具备不同的优势及劣势。
本文就不同壁厚、材质、结构形式中的无损检测方法进行讨论研究。
1 不同壁厚焊缝无损检测技术对比1.1 不同检测方法理论适用壁厚射线检测根据选用的射线源或X 射线机的不同,检测壁厚范围也不同。
常用的300kV 电压X 射线机透照厚度能达到80mm 。
常用射线源Se75检测厚度范围为10~40mm ,Ir192检测厚度范围为20~100mm ,Co60检测厚度范围为40~200mm 。
根据标准NB/T 47013.10-2015的规定,TOFD 检测厚度范围为12~400mm 。
由于TOFD 检测存在较大的表面盲区,因此检测厚度范围要求大于12mm 。
常见焊接缺陷及X射线无损检测

前言船舶制造业自20世纪初开始研究焊接应用技术,并于1920年以英国船厂首次采用焊接技术建造远洋船为标志,焊接技术逐渐在船厂得到推广应用,并迅速取代铆接技术。
由于焊接过程中各种参数的影响,焊缝中有时候不可避免地会出现裂纹、气孔、央渣、未熔合和未焊透等缺陷。
为了保证焊接构件的产品质量,必须对其中的焊缝进行有效的检测和评价,尤其是在船舶压力管道、分段大接缝、外板及水密与强力接点等部位进行质量检测是十分必要的。
众所周知,船舶结构件发生焊接裂纹对结构强度和航行安全危害极大,特别是一些隐性裂纹不易发现,一旦船舶出厂,这些隐性裂纹后患无穷。
因此,船舶在建造焊接过程中产生的裂纹一经发现,就必须立即查明原因并采取果断的措施彻底根除。
焊接质量的检验方法,一般分无损检验和破坏检验两大类,采用何种方法,主要根据产品的技术要求和有关规范的规定。
无损探伤分渗透检验、磁粉探伤、超声波探伤和射线照相探伤。
破坏检验方法是用机械方法在焊接接头(或焊缝)上截取一部分金属,加工成规定的形状和尺寸,然后在专门的设备和仪器上进行破坏试验。
依据试验结果,可以了解焊接接头性能及内部缺陷情况,判断焊接工艺正确与否。
经检验,船体结构焊缝超过质量允许限值时,应首先查明产生缺陷的原因,确定缺陷在工件上的部位。
在确认允许修补时,再按规定对焊缝进行修补。
一、船舶焊接缺陷及无损探伤技术简介1、船舶焊接中的常见缺陷分析船舶焊接是保证船舶密性和强度的关键,是保证船舶质量的关键,是保证船舶安全航行和作业的重要条件。
如果焊接存在着缺陷,就有可能造成结构断裂、渗漏,甚至引起船舶沉没。
因此,在船舶建造中焊接质量是重点验收工作之一,规范也明确规定,焊缝必须进行外观检查,外板对接焊缝必须进行内部检查。
船体焊缝内部检查,可采用射线探伤与超声探伤等办法。
射线探伤能直接判断船体焊缝中存在的缺陷的种类、大小、部位及分布情况,直观可靠,重复性好,容易保存,当前船厂普遍采用X射线探伤来进行船体焊缝的内部质量检查。
复合材料缺陷及无损检测技术

常见的复合材料缺陷
夹芯结构以及蜂窝芯子
面板 胶接层 蜂窝芯子
常见的复合材料缺陷
纤维断裂、树脂富集和孔洞
常见的复合材料缺陷
面芯脱胶
常见的复合材料缺陷
芯间脱胶
常见的无损检测方法
1. 无损检测(NDT):应用于制造过程、成品检验
和在役检测等各个阶段
2. 无损检测:在不破坏的前提下,检查工件宏观缺陷
复合材料缺陷、无损检测 及性能测试
常见的复合材料缺陷
1. 针对纤维增强层合板和夹芯板而言 2. 产生领域:生产、运输和使用过程 3. 类型:孔洞(voids, porosity)
脱胶 (debonds) 分层 (delaminatioБайду номын сангаасs) 撞击 (impact damage) 纤维断裂 (broken fibres) 树脂裂纹 (resin cracks)
状况的无损检测方法称为涡流检测
2. 原理:
常见的无损检测方法
涡流检测
常见的无损检测方法
涡流检测
常见的无损检测方法
非常规检测方法
声发射 光全息成像 红外热成像 微波检测 机械阻抗 泄漏检测 Acoustic Emission (AE) Optical Holography Infrared Thermography Microwave Testing Mechanical Impedance Leak Testing (LT)
激光全息成像
常见的无损检测方法
红外热成像:借助物体热辐射得到热气像的检测技术 特点:非接触
实时 高效 直观
常见的无损检测方法
红外热成像
常见的无损检测方法
红外热成像
铝蜂窝芯子
无损检测射线常见缺陷图集及分析.
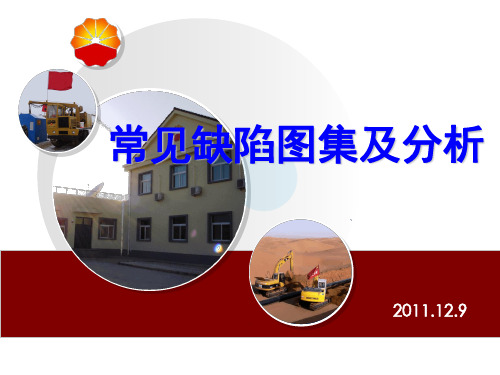
折 痕 曝 光 前
1、折痕的表面现象是什么? 折痕(曝光前)的表征为白月牙状显示,其密度低于邻近的胶片区域(黑度较低)。 2、它们产生的原因是什么? 曝光前弯曲胶片用力过大或过猛都会导致这种类型的折痕。 3、这些现象何时可能发生? 通常出现在从包装盒取出胶片或在曝光前装入暗袋时处理不当的情况下。 4、如何检验曝光前的折痕? 有意识地将某些胶片卷曲或扭折,使其曝光,然后按正常方法冲洗。检验胶片,这时您可 能会在胶片处理不当的地方风到一些颜色较淡的折痕。 5、如何可以避免它们? 严格遵守暗室操作规程,始终小心处理胶片,特别避免手指对胶片施以任何类型的压力。
未融合
边缘未融合
注意:砂轮片磨伤痕迹(不是未融合)
5、裂纹
定义:裂纹是指材料局部断裂形成的缺陷。 影像特征:底片上裂纹和典型影像是轮廓分明的黑线或黑丝。其细节 特征包括:黑线或黑丝上有微小的锯齿,有分叉,粗细和黑度有时有 变化,有些裂纹影像呈较粗的黑线与较细的黑丝相互缠绕状;线的端 部尖细,端头前方有时有丝状阴影延伸。
纵向裂纹
根部裂纹
横向裂纹
6、咬边
一、常见缺陷及示意图
二、其他几种缺陷 三、常见伪缺陷
表 面 内 边
内 咬 边
错 口
接 头 凹 坑
一、常见缺陷及示意图
二、其他几种缺陷 三、常见伪缺陷
1、压痕
1、压痕的表面现象是什么? 压痕的表征为密度明显低于邻近区域的密度。 2、它们产生的原因是什么? 在曝光前某个胶片区域局部受力严重。 3、这些现象何时可能发生? 产生压痕的主要原因在于暗袋准备过程中胶片处理的 方式不当。在处理过程中,胶片某处可能被压(夹)紧 在暗袋中。掉落到暗袋上的物体同样可能造成压痕。 4、如何检验压痕? 直接从同一包装盒中小心准备另一暗袋胶片,曝光并冲 洗胶片,如果未见到与第一次所见一样的暇疵,则第一次所 见的斑痕很可能就是压痕。 5、如何可以避免压痕? 严格遵守暗室操作规程,始终小心处理胶片,避免对胶 片施以任何类型的压力。
混凝土缺陷检测的无损检测方法
混凝土缺陷检测的无损检测方法混凝土是建筑结构中最常用的材料之一,但它也容易出现缺陷,如裂缝、空洞、气孔等。
这些缺陷会影响混凝土的强度和耐久性,因此需要及时检测和修复。
无损检测是一种非破坏性的检测方法,可以有效地检测混凝土缺陷,本文将介绍混凝土缺陷检测的无损检测方法。
一、超声波检测法超声波检测法是一种常用的混凝土缺陷检测方法。
它利用超声波在混凝土中的传播和反射来检测混凝土中的缺陷。
具体方法如下:1.准备设备:超声波检测仪、探头、计算机等。
2.选择合适的探头:根据混凝土的厚度和要检测的缺陷深度选择合适的探头。
3.设置超声波检测仪:根据混凝土的特性和要检测的缺陷类型设置超声波检测仪的参数。
4.检测混凝土:将探头放在混凝土表面,通过超声波检测仪发送超声波,然后接收反射波,并将数据传输到计算机进行处理和分析。
5.分析结果:根据计算机显示的结果判断混凝土中是否存在缺陷,并确定缺陷的位置和大小。
二、雷达检测法雷达检测法是一种利用电磁波来检测混凝土缺陷的无损检测方法。
具体方法如下:1.准备设备:雷达检测仪、天线、计算机等。
2.选择合适的天线:根据混凝土的厚度和要检测的缺陷深度选择合适的天线。
3.设置雷达检测仪:根据混凝土的特性和要检测的缺陷类型设置雷达检测仪的参数。
4.检测混凝土:将天线放在混凝土表面,通过雷达检测仪发送电磁波,然后接收反射波,并将数据传输到计算机进行处理和分析。
5.分析结果:根据计算机显示的结果判断混凝土中是否存在缺陷,并确定缺陷的位置和大小。
三、红外热像检测法红外热像检测法是一种利用红外热像仪来检测混凝土缺陷的无损检测方法。
它通过检测混凝土表面的温度差异来判断混凝土中是否存在缺陷。
具体方法如下:1.准备设备:红外热像仪、计算机等。
2.设置红外热像仪:根据混凝土的特性和要检测的缺陷类型设置红外热像仪的参数。
3.检测混凝土:将红外热像仪对准混凝土表面,记录混凝土表面的温度分布情况,并将数据传输到计算机进行处理和分析。
风电叶片的主要缺陷与无损检测技术评价
叶片整体是一种复杂的层合板结构 ,由于各种干扰因素会产生分层现象。叶片的分层 主 要指纤维层合板间的分层 、芯材与纤维层合板间的分层 。 分层形成 的原因有 : 树脂用量不够 、
布层污染 、真空泄压、二次பைடு நூலகம்型。 夹杂指叶片生产过程中引入非结构材料。夹杂的产生主要是主观因素,如 :布层铺设 时
其质量可靠性是保证机组正常稳定运行的决定因素。纤维增强复合材料 ( F R P) 因其轻质 、
耐腐蚀和高拉伸模量一直是风 电叶片最常用 的材料 。由于风电叶片外型庞大 、质量重, 一旦
出现事故 ,会造成极其严重的后果 。为 了保证叶片产品质量可靠性和安全性 ,叶片须经权威
机构检验和认证 ,以考察结构设计和安全性是否符合 I E C和其它相关标准, 取得相应资质后
关 键 词 :风电叶片; 缺陷; 性能;无损检测
1 引 言
风力发电具有资源再生 、容量巨大、无污染 、综合治理成本低等优点, 是未来电力的先
进生产方向。从 2 0 世纪 7 0 年代至今 ,国内外风电事业得以蓬勃发展 ,装机容量越大 ,发电 效率越高, 技术难度越大。 风 电叶片是捕获风能的最主要部件 , 也是风力发电机的关键部件 ,
操作以及使用不当的原因,如外力冲击、与其它物体碰撞和刮擦等。对缺陷产生原因进行准
确分析, 可以有针对性地采取预防与控制措施 , 减少缺陷形成的概率 , 保证结构质量和性能
满足要求。
孔隙是指叶片在成型过程 中形成的孔洞 ,包括布层内纤维束内的孔隙、纤维束与纤维束 之间的孔隙以及布层层间的孔隙。产生的原因可以归纳为以下几点 :①工艺方面 :叶片灌注
2 . 2 . 2 夹杂对性能的影响
M. Z h a n g和s . E . Ma s o n  ̄经用蒸馏水和海水作为夹杂进行过试验研究 , 铺层时在每层 间刷
焊缝内部缺陷探伤,无损检测方法
焊缝内部缺陷探伤,无损检测方法焊接缺陷是指焊接接头部位在焊接过程中形成的缺陷。
焊缝的内部缺陷有:1、气孔气孔是指焊接时,熔池中的气体未在金属凝固前逸出,残存于焊缝之中所形成的空穴。
其气体可能是熔池从外界吸收的,也可能是焊接冶金过程中反应生成的。
2、夹渣夹渣是指焊后溶渣残存在焊缝中的现象。
3、裂纹焊缝中原子结合遭到破坏,形成新的界面而产生的缝隙称为裂纹。
4、未焊透未焊透指母材金属未熔化,焊缝金属没有进入接头根部的现象。
5、未熔合未熔合是指焊缝金属与母材金属,或焊缝金属之间未熔化结合在一起的缺陷。
按其所在部位,未熔合可分为坡口未熔合、层间未熔合、根部未熔合三种。
无损检测(NDT或无损探伤)是在不损害或不影响被检测对象使用性能的前提下,采用射线、超声、红外、电磁等原理技术并结合仪器对材料、零件、设备进行缺陷、化学、物理参数检测的技术。
1、超声波探伤是利用超声能透入金属材料的深处,并由一截面进入另一截面时,在界面边缘发生反射的特点来检查零件缺陷的一种方法,当超声波束自零件表面由探头通至金属内部,遇到缺陷与零件底面时就分别发生反射波,在荧光屏上形成脉冲波形,根据这些脉冲波形来判断缺陷位置和大小。
2、射线探伤是利用某种射线来检查焊缝内部缺陷的一种方法。
常用的射线有X射线和γ射线两种。
X射线和γ射线能不同程度地透过金属材料,对照相胶片产生感光作用。
利用这种性能,当射线通过被检查的焊缝时,因焊缝缺陷对射线的吸收能力不同,使射线落在胶片上的强度不一样,胶片感光程度也不一样,这样就能准确、可靠、非破坏性地显示缺陷的形状、位置和大小。
3、磁粉探伤利用工件缺陷处的漏磁场与磁粉的相互作用,它利用了钢铁制品表面和近表面缺陷(如裂纹,夹渣,发纹等)磁导率和钢铁磁导率的差异,磁化后这些材料不连续处的磁场将发生畸变,形成部分磁通泄漏处工件表面产生了漏磁场,从而吸引磁粉形成缺陷处的磁粉堆积——磁痕,在适当的光照条件下,显现出缺陷位置和形状,对这些磁粉的堆积加以观察和解释,就实现了磁粉探伤。
无损检测技术中的焊接缺陷检测方法
无损检测技术中的焊接缺陷检测方法在工业领域中,焊接是一项常见且关键的技术。
然而,焊接过程中可能会产生各种焊接缺陷,这对产品质量和安全性造成了潜在威胁。
因此,针对焊接缺陷的快速、准确的检测方法至关重要。
无损检测技术作为一种非破坏性的检测方法,在焊接缺陷检测中起着重要的作用。
本文将介绍几种常用的无损检测技术中的焊接缺陷检测方法。
首先,常用的一种方法是超声波检测。
超声波检测通过将高频声波传播到焊接接头内部,利用声波的传播和反射特性来检测缺陷。
超声波检测可以检测出焊接中的孔洞、夹杂物、裂纹等缺陷。
它具有技术可行性高、检测效果好和操作相对简单等优点。
然而,超声波检测对设备和人员的要求较高,且对材料的传导性能有一定要求。
其次,涡流检测也是一种常用的无损检测方法。
涡流检测是通过在焊接接头上施加交变电磁场,利用焊接缺陷产生的涡流信号进行检测。
涡流检测主要用于检测表面缺陷,如焊缝错边、裂纹、包气孔等。
该方法对于高导电性材料的检测效果较好,但对于低导电性材料的检测能力较弱。
另外,磁粉检测也是焊接缺陷检测的一种常用方法。
磁粉检测通过在焊接接头上施加磁场,使得磁性颗粒集聚在缺陷处,从而通过观察颗粒呈现的形态和位置来判断缺陷的存在与否。
磁粉检测适用于铁磁材料的检测,对于裂纹和夹杂物等缺陷具有较高的敏感性。
然而,该方法在应用过程中需要密封环境,并且对于焊接接头的表面清洁度要求较高。
此外,X射线检测也是一种常用的无损检测技术。
X射线检测可以通过透射X射线或散射X射线来检测焊接接头的缺陷。
透射X射线检测可以检测较大的缺陷,如包气孔、夹杂物等,而散射X射线检测可以检测出较小的缺陷,如微裂纹。
X射线检测仪器的成本较高,且需要密封防护措施,对操作人员的辐射安全要求也较高。
最后,热红外检测是一种新兴的无损检测技术,也可用于焊接缺陷的检测。
热红外检测通过红外热像仪来检测焊接接头表面的温度分布,从而判断是否存在缺陷。
热红外检测具有操作简单、实时性好和对材料无特殊要求等优点。
- 1、下载文档前请自行甄别文档内容的完整性,平台不提供额外的编辑、内容补充、找答案等附加服务。
- 2、"仅部分预览"的文档,不可在线预览部分如存在完整性等问题,可反馈申请退款(可完整预览的文档不适用该条件!)。
- 3、如文档侵犯您的权益,请联系客服反馈,我们会尽快为您处理(人工客服工作时间:9:00-18:30)。
表面a 近表面b VT PT MT ET RT 使用产生的缺陷 点状腐蚀 ● ● ● ● 局部腐蚀 ● ● 裂纹 ◎ ● ● ◎ ◎ 焊接产生的缺陷 烧穿 ● ● 裂纹 ◎ ● ● ◎ ◎ 夹渣 ◎ ◎ ● 未熔合 ◎ ◎ ◎ ◎ 未焊透 ◎ ● ● ◎ ● 焊瘤 ● ● ● ○ ● 气孔 ● ● ○ ● 咬边 ● ● ● ○ ● 产品成型产生的缺陷 裂纹(所有产品成型) ○ ● ● ◎ ◎ 夹杂(所有产品成型) ◎ ◎ ● 夹层(板材、管材) ◎ ◎ ◎ 重皮(锻件) ○ ● ● ○ ◎ 气孔(铸件) ● ● ○ ● ●:在通常情况下,能检测。 ◎:特殊条件下,按特定技术能检测。 ○:要求专用技术和条件 a:仅能检测表面开口缺陷的无损检测方法。 b:能检测表面开口和近表面缺陷的无损检测方法。 c:可检测被检工件中任何位置缺陷的无损检测方法。 所有位置C DR UTA UTS ● ◎ ● ◎ ● ◎ ● ● ● ● ◎ ● ◎ ● ● ◎ ● ◎ ● ● ○ ◎ ◎ ◎ ◎ ◎ ● TOFD
● ● ◎ ● ● ○ ○
○