【机械制造业】插床机械传动系统设计
机械课程设计插床

机械课程设计插床一、教学目标本节课的教学目标是让学生了解和掌握插床的基本原理、结构和工作过程,培养学生对机械制造工艺的认识和实际操作能力。
具体来说,知识目标包括:掌握插床的定义、分类和基本结构;理解插床的工作原理和操作方法。
技能目标包括:能够正确操作插床,进行简单的零件加工;能够分析插床加工过程中可能出现的问题,并采取相应的解决措施。
情感态度价值观目标包括:培养学生对机械制造行业的兴趣和热情,提高学生对机械加工工艺的重视程度,培养学生的创新意识和团队合作精神。
二、教学内容本节课的教学内容主要包括插床的定义、分类和基本结构,插床的工作原理和操作方法,以及插床加工过程中的注意事项。
具体来说,教学大纲如下:1.插床的定义、分类和基本结构1.1 插床的定义和作用1.2 插床的分类及特点1.3 插床的基本结构组成及功能2.插床的工作原理和操作方法2.1 插床的工作原理2.2 插床的操作方法及步骤2.3 插床加工过程中的注意事项3.插床加工过程中的注意事项3.1 刀具的选择和使用3.2 工件的装夹和调整3.3 切削参数的设置和调整3.4 加工过程中的安全防护三、教学方法为了提高教学效果,本节课将采用多种教学方法相结合的方式进行。
包括:1.讲授法:教师通过讲解插床的基本原理、结构和工作过程,引导学生掌握相关知识。
2.讨论法:教师学生进行小组讨论,分享对插床操作方法和注意事项的理解,促进学生之间的交流与合作。
3.案例分析法:教师提供一些实际的插床加工案例,让学生分析案例中存在的问题,并提出解决措施,提高学生的分析和解决问题的能力。
4.实验法:教师安排学生在实验室进行插床的操作实践,让学生亲身体验插床加工过程,增强学生的实际操作能力。
四、教学资源为了支持本节课的教学内容和教学方法的实施,我们将准备以下教学资源:1.教材:选用符合教学大纲要求的机械制造工艺教材,为学生提供系统的理论知识。
2.参考书:提供一些与插床相关的参考书籍,丰富学生的知识储备。
机械设计课程设计插床

机械设计课程设计插床一、教学目标本课程旨在通过机械设计课程设计插床的学习,让学生掌握插床的基本结构、工作原理和设计方法,培养学生具备一定的机械设计能力和创新意识。
具体目标如下:1.知识目标:(1)了解插床的分类、结构及工作原理;(2)掌握插床的设计方法,包括刀具、夹具和床身的设计;(3)熟悉插床的加工工艺,并能应用于实际生产。
2.技能目标:(1)能够独立完成插床的基本设计;(2)具备分析并解决插床加工过程中问题的能力;(3)学会使用相关设计软件进行插床设计。
3.情感态度价值观目标:(1)培养学生对机械设计的兴趣,提高专业素养;(2)培养学生团队合作精神,提高沟通与协作能力;(3)培养学生创新意识,提高解决实际问题的能力。
二、教学内容本课程的教学内容主要包括插床的基本结构、工作原理、设计方法和加工工艺。
具体安排如下:1.插床的基本结构和工作原理:介绍插床的分类、主要部件及其功能,分析插床的工作原理。
2.插床的设计方法:讲解刀具、夹具和床身的设计方法,并结合实例进行分析。
3.插床的加工工艺:介绍插床的加工工艺,包括加工顺序、切削参数等,并结合实际生产案例进行分析。
4.设计软件应用:教授如何使用相关设计软件进行插床设计,提高设计效率。
三、教学方法为了提高学生的学习兴趣和主动性,本课程将采用多种教学方法,如讲授法、讨论法、案例分析法和实验法等。
具体应用如下:1.讲授法:用于讲解插床的基本概念、原理和设计方法。
2.讨论法:学生针对插床设计中的问题进行讨论,培养团队合作精神。
3.案例分析法:通过分析实际生产中的插床加工案例,使学生更好地理解插床的应用。
4.实验法:安排学生进行插床实验,提高学生的动手能力和解决实际问题的能力。
四、教学资源为了支持本课程的教学内容和教学方法的实施,丰富学生的学习体验,我们将准备以下教学资源:1.教材:选用权威、实用的插床设计教材,为学生提供系统性的知识学习。
2.参考书:提供相关领域的参考书籍,拓展学生的知识视野。
机械原理课程设计插床机械设计

机械原理课程设计设计计算说明书设计题目插床机械设计设计任务书1.1 设计题目插床1.2 插床简介插床是用于加工中小尺寸垂直方向的平面或直槽的金属切削机床,多用于单件或小批量生产。
为了适用不同材料和不同尺寸工件的粗、精加工,要求主执行构件—插刀能以数种不同速度、不同行程和不同起始位置作垂直方向的往复直线移动,且切削时插刀的移动速度低于空行程速度,即插刀具有急回现象;安装工件的工作台应具有不同进给量的横向进给,以完成平面的加工,工作台还应具有升降功能,以适应不同高度的工件加工。
1.3 设计要求及设计参数设计要求:要求主执行机构工作行程切削平稳、压力角较小。
进给机构压力角不超过许用值。
设计参数如下所示:插床机构设计3号题目参数题号 3主执行机构曲柄转速n2/(r/min)50 曲柄l O2A/mm75插刀行程H/mm120行程速比系数K 1.8 连杆与导杆之比l BC0.55 力臂d(mm) 108 工作阻力F max(N) 10800导杆质量m4(kg) 22 导杆转动惯量J S4(kgm2) 1.2 滑块质量m6(kg) 60进给机构从动件最大摆角max20凸轮从动件杆长(mm) 130 推程许用压力角[]推程42回程许用压力角[]回程50滚子半径r r(mm) 15刀具半径r c(mm) 0.08一:主执行机构设计与分析1:插床机械设计参数以及相关参数计算曲柄转速n 2/(r/min ) 曲柄长度l O2A =75mm插刀行程H=120mm行程速度比系数K=1.8连杆与导杆之比l BC =0.55力臂d=108mm 工作阻力F=10800N导杆4的质量m 4=22kg 导杆4的转动惯量Js4=1.1滑块6的质量m 6=60 一、插床导杆机构的综合1、计算极位夹角 、曲柄角速度1ω、曲柄角加速度1εn 2=50l O2A =75m mH=120m mK=1.8l BC =0.55d=108mmF=10800Nm 4=22kgJs4=1.1m 6=6046.667θ=1 4.922/rad sω=2、求导杆长度CD L 、连杆长度DE L 、中心距AC L 根据插床机构结构示意图,由几何条件可得138.286CD L mm =因为/0.55DE CD L L =,76.06DE L mm =152.114AC L mm =3、求弓形高b 、导路距离e L13.695CD L mm =283.553e L mm =二:主执行机构运动分析已知:曲柄的转速n=45 rad/min ,滑块质量为50kg ,导杆的质量为28kg ,其质心转动惯量为1.2 kg ·2m ,力臂d=110mm ,工作阻力F=9000N 。
机械原理课程设计实例插床
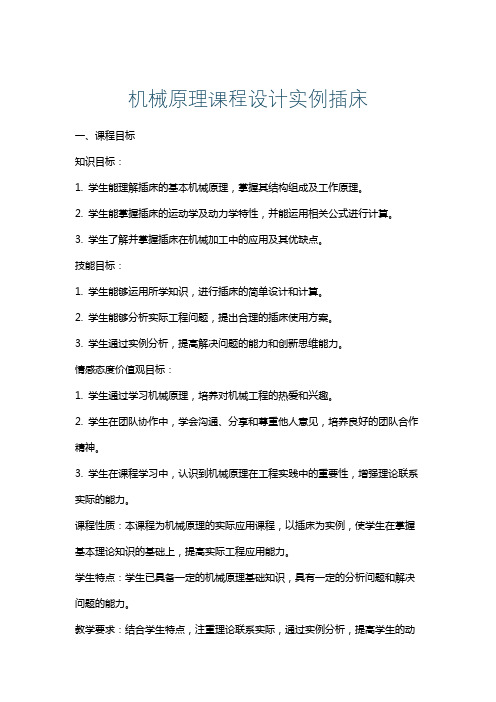
机械原理课程设计实例插床一、课程目标知识目标:1. 学生能理解插床的基本机械原理,掌握其结构组成及工作原理。
2. 学生能掌握插床的运动学及动力学特性,并能运用相关公式进行计算。
3. 学生了解并掌握插床在机械加工中的应用及其优缺点。
技能目标:1. 学生能够运用所学知识,进行插床的简单设计和计算。
2. 学生能够分析实际工程问题,提出合理的插床使用方案。
3. 学生通过实例分析,提高解决问题的能力和创新思维能力。
情感态度价值观目标:1. 学生通过学习机械原理,培养对机械工程的热爱和兴趣。
2. 学生在团队协作中,学会沟通、分享和尊重他人意见,培养良好的团队合作精神。
3. 学生在课程学习中,认识到机械原理在工程实践中的重要性,增强理论联系实际的能力。
课程性质:本课程为机械原理的实际应用课程,以插床为实例,使学生在掌握基本理论知识的基础上,提高实际工程应用能力。
学生特点:学生已具备一定的机械原理基础知识,具有一定的分析问题和解决问题的能力。
教学要求:结合学生特点,注重理论联系实际,通过实例分析,提高学生的动手能力和创新能力。
在教学过程中,注重培养学生的团队合作精神和实际操作技能。
将课程目标分解为具体的学习成果,以便于后续的教学设计和评估。
二、教学内容1. 插床概述:介绍插床的定义、分类及其在机械加工中的应用。
- 教材章节:第一章第二节- 内容列举:插床的结构组成、工作原理、主要类型。
2. 插床的运动学分析:讲解插床的运动规律、速度和加速度的计算。
- 教材章节:第二章第一节- 内容列举:直线运动、旋转运动、复合运动的速度和加速度计算。
3. 插床的动力学分析:探讨插床在加工过程中的力学特性,强度、刚度分析。
- 教材章节:第二章第二节- 内容列举:受力分析、强度计算、刚度计算。
4. 插床的设计与计算:结合实例,讲解插床的设计方法和计算步骤。
- 教材章节:第三章- 内容列举:设计原则、计算公式、参数选择、优化设计。
5. 插床的应用与优缺点分析:分析插床在实际工程中的应用场景、优缺点及改进措施。
机械原理课程设计插床

机械原理课程设计插床一、引言。
插床作为一种常见的机械加工设备,在工业生产中起着重要的作用。
本文旨在对插床的结构、工作原理以及设计要点进行介绍,以便于机械原理课程设计的学习和实践。
二、插床的结构。
插床通常由床身、工作台、主轴、进给装置、传动装置、刀架等部分组成。
床身是插床的基础部分,承受整个机床的重量和切削力,具有高强度和刚性。
工作台用于夹紧工件,是加工的基准面。
主轴是插床的主要运动部件,通过主轴传动装置实现不同速度和进给速度的调节。
进给装置用于控制工件的进给运动,传动装置则用于驱动主轴和进给装置的运动。
刀架是刀具的安装和刀具进给的部分,通过刀架的运动实现工件的切削加工。
三、插床的工作原理。
插床的工作原理是利用主轴带动刀具进行切削加工,工件在工作台上进行相对运动,实现对工件的加工。
在加工过程中,刀具通过刀架的进给运动,沿工件的轴向或径向进行切削,完成对工件的加工。
同时,进给装置控制工件的进给速度,使得切削过程得以顺利进行。
四、插床的设计要点。
1. 结构设计,插床的结构设计应注重床身的刚性和稳定性,确保机床在加工过程中不产生振动和变形,影响加工精度。
同时,主轴和进给装置的设计要满足不同加工要求,具有良好的可调性和稳定性。
2. 刀具选择,在插床的设计中,应根据加工工件的材料和形状选择合适的刀具,确保切削效果和加工质量。
同时,刀具的安装和调整要方便快捷,提高生产效率。
3. 进给系统设计,进给系统的设计要满足不同工件的加工要求,具有可调性和稳定性。
同时,进给系统的传动装置要可靠耐用,确保加工过程的安全和稳定。
4. 控制系统设计,插床的控制系统应具有良好的响应速度和精度,能够实现对加工过程的精确控制。
同时,控制系统的操作界面要简单直观,方便操作和维护。
五、结论。
插床作为一种常见的机械加工设备,在工业生产中具有重要的作用。
通过对插床的结构、工作原理以及设计要点的介绍,可以更好地理解和掌握插床的工作原理和设计方法,为机械原理课程设计提供参考和指导。
插床的机械原理课程设计

插床的机械原理课程设计一、课程目标知识目标:1. 学生能理解插床的基本结构组成及其工作原理;2. 学生能掌握插床的主要机械部件名称及其功能;3. 学生能了解插床在制造业中的应用和重要性。
技能目标:1. 学生能够运用所学知识,分析并解释插床机械运动的过程;2. 学生能够通过实际操作,掌握插床的安全操作规程和简单维护方法;3. 学生能够通过小组合作,设计并制作简单的插床模型,培养动手能力和团队协作能力。
情感态度价值观目标:1. 学生能够培养对机械原理学习的兴趣,增强探索精神和创新意识;2. 学生能够树立安全意识,养成严谨的科学态度和良好的操作习惯;3. 学生能够认识到插床在国民经济中的地位,培养爱国主义情怀和民族自豪感。
课程性质分析:本课程为机械原理实践课,注重理论联系实际,通过讲授、演示、实践等教学手段,使学生掌握插床的基本原理和操作技能。
学生特点分析:学生为初中年级,具备一定的物理知识和动手能力,对新鲜事物充满好奇,但注意力集中时间有限,需要通过趣味性和实践性强的教学活动激发学习兴趣。
教学要求:结合学生特点,注重启发式教学,引导学生主动参与,提高课堂互动性。
强调实践操作,培养学生动手能力,同时关注安全意识和团队协作能力的培养。
通过教学评估,确保课程目标的实现。
二、教学内容1. 插床概述- 插床的定义、分类及用途;- 插床在机械加工中的地位与作用。
2. 插床的结构与工作原理- 插床的主要部件及其功能;- 插床的工作原理及运动分析。
3. 插床的操作与维护- 插床的操作规程及注意事项;- 插床的日常维护与保养。
4. 插床的应用案例- 插床在实际加工中的应用实例;- 插床加工零件的工艺流程。
5. 插床模型设计与制作- 小组合作设计插床模型;- 动手制作插床模型,并进行调试。
教学大纲安排:第一课时:插床概述及用途;第二课时:插床结构与工作原理;第三课时:插床操作与维护;第四课时:插床应用案例分析与讨论;第五课时:插床模型设计与制作。
插床机械传动系统设计说明
机械设计课程设计说明书题目插床机械传动系统设计指导教师院系物理与机电工程学院班级 10机械(2)学号姓名完成时间 2012.12.6目录一.设计任务书 (3)二、传动方案拟定 (6)三、电动机的选择 (6)四、计算总传动比及分配各级的传动比 (7)五、运动参数及动力参数计算 (7)六、传动零件的设计计算 (9)七、轴的设计计算 (25)八、滚动轴承的选择及校核计算 (38)九、联轴器的选择 (42)十、润滑剂、密封装置的设计 (42)十一、箱体的设计 (43)十二、总结 (44)计算与说明主要结果机械设计课程设计任务书一、课程设计题目:插床机械系统方案设计二、工作原理插床机械系统的执行机构主要是由导杆机构和凸轮机构组成。
附图1为其参考示意图,电动机经过减速传动装置(皮带和齿轮传动)带动曲柄2转动,再通过导杆机构使装有刀具的滑块6沿导路y—y作往复运动,以实现刀具的切削运动。
刀具向下运动时切削,在切削行程H中,前后各有一段0.05H的空刀距离,工作阻力F为常数;刀具向上运动时为空回行程,无阻力。
为了缩短回程时间,提高生产率,要求刀具具有急回运动。
刀具与工作台之间的进给运动,是由固结于轴O2上的凸轮驱动摆动从动件l O8D和其它有关机构(图中未画出)来完成的。
三、设计要求电动机轴与曲柄轴2平行,使用寿命10年,每日一班制工作,载荷有轻微冲击。
允许曲柄2转速偏差为±5%。
要求导杆机构的最小传动角不得小于60o;凸轮机构的最大压力角应在许用值[α]之内,摆动从动件8的升、回程运动规律均为等加速等减速运动,其它参数见设计数据。
执行机构的传动效率按0.95计算。
按小批量生产规模设计。
四、设计数据(见附表1)五、设计内容1、设计题目(包括设计条件和要求);2、根据电机转速和曲柄轴转速的比值,选择传动机构并定性比较,确定传动系统方案;3、电动机类型和功率的选择;4、确定总传动比、分配各级传动比;5、计算传动装置的运动和动力参数;6、传动零件(带传动及齿轮传动(或蜗杆传动))设计计算;7、传动轴的结构设计及校核;8、滚动轴承的选择和寿命计算;9、键连接的选择和校核计算;10、联轴器的选择计算;11、润滑剂及润滑方式、密封装置的选择;12、减速器箱体的结构和主要尺寸设计;13、执行机构方案及尺寸设计(在机械原理设计中完成,本次不做);14、执行机构构件及零件的结构尺寸设计(由设计者自定是否涉及);15、运用计算机软件(Solidworks、Pro/E、AutoCAD等)设计及绘图;16、列出主要参考资料并编号;17、设计的心得体会和收获;六、设计工作量1、减速器装配图1张,要求计算机采用A0图纸出图,图纸格式为留装订边,标题栏、明细栏参考机械设计手册国标规定;2、传动轴零件图1张;传动零件1张,均要求计算机采用A3图纸出图,图纸格式为及箱体设计(2)减速器箱体设计;6、计算机绘图设计(1)减速器三维零件图及装配图(可不做);(2)绘制减速器装配图;(3)绘制轴及传动零件的零件图;11(或13)周星期六至12(或14)周星期三7、编写设计计算说明书(1)编写设计计算说明书,内容包括所有的计算,并附有必要的简图;(2)说明书中最后应写出设计总结。
1、插床传动系统机构设计
M
0
er
d 可求得 M ed 的值, 进而可得出最大盈亏功Δ Wmax ,
900ΔWmax
(π 2 n 2 δ
即可计算出飞轮转动惯量,然后按照飞轮尺寸的确定原则
进行飞轮结构设计。 (6)运动循环图
6
机械原理课程设计
①
首先确定执行机构的运动循环时间 T 因选取曲柄导杆机构作为插床的执行机构, 确定组成运动循环的各个区段插床的运动循环由两段组成, 即插刀进给的工作形成 确定执行机构各个区段的运行时间及相应的分配轴转角插床的运动循环时间 T=1s,
图 6.8 滑块位移、速度、加速度曲线
(5)飞轮设计 机构简化模型如图 6.9:
由动能定理: W dE 参照运动简图展开得:
图 6.9 机构模型简化
( M d 1 - Qvs 5 G3 vs 3 cos 3 G5 vs 5 cos 5 )dt [ M d 1 - Qvs 5 - G3 vs 3 cos 3 - G5 vs 5 cos 5 ]dt
l AO1 lO1O 2 sin O1O2 A
②
按刀具行程要求确定 BO2 和 BC 长度
作图(如图 6.3)分析:
按 lBC=lBO2 即几何关系,算出:
l AO1 LBO 2 H
③ 析:
按传力性能要求(压力角尽量小)确定导轨 y-y 到 O2 的距离 作图(如图 6.4)分
导轨 y-y 落在图中两点划线之间时,压力角相对较小。由几何关系即可得 y-y 轴到 O2 点的距离约为 93. 3mm。 ④ 6.5: 选取适当长度比例尺,作主传动机构运动简图 包括滑块的两个极限位置,如图
5
d[ 1 J 112 1 m3 vs23 1 J s 332 1 m5 vs25 ] 2 2 2 2
插床机械设计课程设计
插床机械设计课程设计一、课程目标知识目标:1. 让学生理解插床机械的基本原理和设计流程;2. 掌握插床机械的主要结构、部件及其功能;3. 了解插床机械在设计过程中需考虑的技术参数和性能指标。
技能目标:1. 培养学生运用CAD软件进行插床机械零部件的设计和绘制能力;2. 提高学生运用工程制图知识,准确表达插床机械设计方案的能力;3. 培养学生运用理论知识分析、解决插床机械设计过程中遇到的问题。
情感态度价值观目标:1. 培养学生对机械设计学科的兴趣,激发其创新意识;2. 培养学生具备团队协作精神,能够在团队中发挥积极作用;3. 增强学生的工程意识,使其认识到机械设计在国民经济和制造业中的重要性。
分析课程性质、学生特点和教学要求,本课程将目标分解为以下具体学习成果:1. 学生能够独立完成插床机械设计方案,并运用CAD软件进行绘制;2. 学生能够针对插床机械设计过程中遇到的问题,提出合理的解决方案;3. 学生能够以团队形式开展项目,充分发挥团队协作能力,共同完成设计任务;4. 学生能够通过本课程的学习,增强对机械设计学科的兴趣和热情,为后续专业课程学习打下坚实基础。
二、教学内容根据课程目标,教学内容主要包括以下几部分:1. 插床机械原理及设计流程:讲解插床机械的基本原理、设计流程及主要技术参数,对应教材第一章内容。
2. 插床机械结构及功能:详细介绍插床机械的主要结构、部件及其功能,分析各部件在插床机械运行中的作用,对应教材第二章内容。
3. CAD软件在插床机械设计中的应用:教授CAD软件的基本操作,以实际案例演示插床机械零部件的设计和绘制方法,对应教材第三章内容。
4. 工程制图与表达:结合插床机械设计,讲解工程制图的基本知识,培养学生准确表达设计方案的能力,对应教材第四章内容。
5. 插床机械设计实践:指导学生进行插床机械设计方案制定,运用CAD软件进行绘制,针对实际问题提出解决方案,对应教材第五章内容。
插床机构课程设计
插床机构课程设计一、课程目标知识目标:1. 学生能够理解插床机构的基本概念,掌握其分类和结构特点。
2. 学生能够掌握插床机构的工作原理,了解其运动规律。
3. 学生能够了解插床机构在机械加工中的应用,掌握相关工艺参数。
技能目标:1. 学生能够运用所学知识,分析并解决插床机构在实际应用中遇到的问题。
2. 学生能够通过实际操作,掌握插床机构的调试和维护方法。
3. 学生能够运用绘图软件,绘制插床机构的示意图,提高空间想象能力。
情感态度价值观目标:1. 学生通过学习插床机构,培养对机械制造的兴趣,提高学习积极性。
2. 学生能够认识到插床机构在制造业中的重要性,增强对制造业的认同感。
3. 学生在学习过程中,培养团队合作意识,提高沟通与协作能力。
课程性质:本课程为机械制造专业课程,以理论教学与实践操作相结合的方式进行。
学生特点:学生已具备一定的机械基础知识和动手能力,对新鲜事物充满好奇。
教学要求:教师应注重理论与实践相结合,激发学生兴趣,提高学生的动手操作能力和解决问题的能力。
通过课程学习,使学生能够将所学知识应用于实际工作中,为我国制造业培养高素质的技术人才。
二、教学内容1. 插床机构概述- 插床机构的概念、分类及结构特点- 插床机构在机械加工中的应用2. 插床机构工作原理- 运动规律及其分析- 传动系统及其工作原理3. 插床机构的设计与计算- 基本设计原则- 相关工艺参数的选择与计算4. 插床机构的调试与维护- 调试方法及注意事项- 常见故障分析与排除- 维护保养方法5. 插床机构应用案例- 案例分析- 实际操作演示6. 插床机构绘图与识图- 绘图软件的使用- 插床机构示意图的绘制教学内容安排与进度:第一周:插床机构概述第二周:插床机构工作原理第三周:插床机构的设计与计算第四周:插床机构的调试与维护第五周:插床机构应用案例及实际操作演示第六周:插床机构绘图与识图教材章节及内容:第一章:机械加工基本概念第二章:插床机构概述第三章:插床机构工作原理第四章:插床机构设计与计算第五章:插床机构的调试与维护第六章:插床机构应用案例及绘图识图技巧教学内容根据课程目标和教学要求进行科学性和系统性组织,注重理论与实践相结合,提高学生的综合应用能力。
- 1、下载文档前请自行甄别文档内容的完整性,平台不提供额外的编辑、内容补充、找答案等附加服务。
- 2、"仅部分预览"的文档,不可在线预览部分如存在完整性等问题,可反馈申请退款(可完整预览的文档不适用该条件!)。
- 3、如文档侵犯您的权益,请联系客服反馈,我们会尽快为您处理(人工客服工作时间:9:00-18:30)。
(机械制造行业)插床机械传动系统设计机械设计课程设计说明书题目插床机械传动系统设计指导教师院系物理与机电工程学院班级10机械(2)学号姓名完成时间2012.12.6目录一.设计任务书 (3)二、传动方案拟定 (6)三、电动机的选择 (6)四、计算总传动比及分配各级的传动比 (7)五、运动参数及动力参数计算 (7)六、传动零件的设计计算 (9)七、轴的设计计算 (25)八、滚动轴承的选择及校核计算 (38)九、联轴器的选择 (42)十、润滑剂、密封装置的设计 (42)十一、箱体的设计 (43)十二、总结 (44)机械设计课程设计任务书一、课程设计题目:插床机械系统方案设计二、工作原理插床机械系统的执行机构主要是由导杆机构和凸轮机构组成。
附图1为其参考示意图,电动机经过减速传动装置(皮带和齿轮传动)带动曲柄2转动,再通过导杆机构使装有刀具的滑块6沿导路y—y作往复运动,以实现刀具的切削运动。
刀具向下运动时切削,在切削行程H中,前后各有一段0.05H的空刀距离,工作阻力F为常数;刀具向上运动时为空回行程,无阻力。
为了缩短回程时间,提高生产率,要求刀具具有急回运动。
刀具与工作台之间的进给运动,是由固结于轴O2上的凸轮驱动摆动从动件l O8D和其它有关机构(图中未画出)来完成的。
三、设计要求电动机轴与曲柄轴2平行,使用寿命10年,每日一班制工作,载荷有轻微冲击。
允许曲柄2转速偏差为±5%。
要求导杆机构的最小传动角不得小于60o;凸轮机构的最大压力角应在许用值[α]之内,摆动从动件8的升、回程运动规律均为等加速等减速运动,其它参数见设计数据。
执行机构的传动效率按0.95计算。
按小批量生产规模设计。
四、设计数据(见附表1)五、设计内容1、设计题目(包括设计条件和要求);2、根据电机转速和曲柄轴转速的比值,选择传动机构并定性比较,确定传动系统方案;3、电动机类型和功率的选择;4、确定总传动比、分配各级传动比;电动机型号Y904S-4额定功率1.1kw满载转速1400r/min i=2.5i=2.772=1.1KWV带:Z型a=359mm =163Z=4=384.53N 斜齿圆柱齿轮8级精度V=0.93m/s =97a=95mm =45mm5、计算传动装置的运动和动力参数;6、传动零件(带传动及齿轮传动(或蜗杆传动))设计计算;7、传动轴的结构设计及校核;8、滚动轴承的选择和寿命计算;9、键连接的选择和校核计算;10、联轴器的选择计算;11、润滑剂及润滑方式、密封装置的选择;12、减速器箱体的结构和主要尺寸设计;13、执行机构方案及尺寸设计(在机械原理设计中完成,本次不做);14、执行机构构件及零件的结构尺寸设计(由设计者自定是否涉及);15、运用计算机软件(Solidworks、Pro/E、AutoCAD等)设计及绘图;16、列出主要参考资料并编号;17、设计的心得体会和收获;六、设计工作量1、减速器装配图1张,要求计算机采用A0图纸出图,图纸格式为留装订边,标题栏、明细栏参考机械设计手册国标规定;2、传动轴零件图1张;传动零件1张,均要求计算机采用A3图纸出图,图纸格式为留装订边,标题栏、明细栏参考机械设计手册国标规定;3、设计说明书一份(应包含设计主要内容,在说明书中列出必要的计算公式、设计计算的全部过程。
),可打印,封面格式见《机械设计课程设计指导书》;4、以组为单位进行答辩,答辩要求制作PPT。
七、设计时间:14、15周=40mm斜齿圆柱齿轮8级精度V=0.37m/sa=110mm电动机键C856GB/T1096 轴I键C645GB/T1096-2 003轴II键一8 56GB/T1096-2 003键二8 32GB/T1096-2 003轴III键1250GB/T1096-26.1、带传动的失效形式和设计准则(1)主要失效形式A、打滑当传递的圆周力F超过了带与带轮之间摩擦力的总和的极限时,发生过载打滑,使传动失效。
弹性滑动和打滑的区别:a)从现象上看:弹性滑动是局部带在带轮的局部接触弧面上发生的微量相对滑动;打滑则是整个带在带轮的全部接触弧面上发生的显著相对滑动;b)从本质上看:弹性滑动是由带本身的弹性和带传动两边的拉力差(未超过极限值)引起的,带传动只要传递动力,两边就必然出现拉力差,所以弹性滑动是不可避免的。
而打滑则是带传动载荷过大使两边拉力差超过极限摩擦力而引起的,因此打滑是可以避免的。
B、疲劳破坏带在变应力的长期作用下,因疲劳而发生裂纹、脱层、松散,直至断裂。
(2)设计准则带传动的主要失效形式是打滑和疲劳破坏,因此,带传动的设计准则是:在保证带在工作时不打滑的条件下,带传动具有足够的疲劳强度和寿命。
6.2、普通V带传动的设计步骤和方法(1)V带设计参数1、确定计算功率:,查表8-7得工作情况系数(空、轻载启动,载荷有轻微冲击),故2、选择V带的带型:根据,查表8-1选用Z型()。
3、确定带轮的基准直径并验算带速v:(1)初选小带轮的基准直径:查表8-6、表8-8取小带轮的基准。
(2)验算带速v:因为5m/s<v<30m/s,故带速合适。
(3)计算大齿轮的基准直径:,由表圆整为180mm。
4、确定V带的中心距a和基准长度:(1)根据公式,初定中心距。
(2)通过计算得到该组带轮所需的基准长度:查表8-2得:。
(3)计算实际中心距:。
根据得:中心距a的变化范围为。
5、验算小带轮上的包角:>90°6、计算带的根数z:(1)计算带根V带的额定功率:由和,查表8-4a知根据,和Z型带查表8-4b得:,查表8-5得,查表8-2得,于是(2)计算V带的根数z:,取4根。
7、计算单根V带的初拉力的最小值:查表8-3得Z型带的单位长度质量,应使带的实际初拉力8、计算应轴力:压轴力的最小值为:9、带轮结构设计:查机械设计课程设计指导书得:Y90S-4电动机轴伸直径D=24mm,轴伸长度E=60mm。
根据小带轮基准直径做成实心式结构参照机械设计书图8-14(a)和表8-10,可求其结构尺寸和轮缘横截面尺寸。
大带轮基准直径做成腹板式结构参照机械设计书图8-14(b)和表8-10,可求出其结构尺寸和轮缘横截面尺寸。
小带轮参数:小带轮=71mm,孔径d=24mm,带轮宽B=50mm,查相关机械手册知小带轮采用实心式;大带轮参数:大带轮=180mm,查相关机械手册知大带轮采用四孔板式,则孔径d=28mm,带轮宽B=50mm,轮毂直径和宽度皆为。
6.3、solidworks带轮3D制图(1)小带轮绘制:(2)大带轮绘制:6.4、参考资料[1]宋宝玉:《机械设计课程设计指导书》,高等教育出版社2006年版[2]濮良贵、纪名刚:《机械设计》,高等教育出版社2006年版[3]邢邦圣:《机械制图与计算机制图》,化学工业出版社2008年版[4]江洪、陈燎:《solidworks2008完全自学手册》,机械工业出版社2008年版[5]谢昱北:《solidworks2007典型范例》,电子工业出版社207年版7、齿轮传动设计7.1、齿轮传动的失效形式和设计准则一般情况下齿轮传动的失效主要发生在轮齿,轮毂、轮辐很少失效,因此轮毂、轮辐部分的尺寸按经验设计。
齿轮的失效可分为轮齿整体失效和齿面失效两大类。
(1)失效形式A、轮齿折断直齿轮轮齿的折断一般是全齿折断;斜齿轮和人字齿齿轮,由于接触线倾斜,一般是局部齿折断。
齿轮在工作时,轮齿像悬臂梁一样承受弯矩,在其齿根部分的弯曲应力最大,而且在齿根的过渡圆角处有应力集中,当交变的齿根弯曲应力超过材料的弯曲疲劳极限应力时,由于材料疲劳对拉伸应力比较敏感,在齿根处受拉一侧首先就会产生疲劳裂纹,随着裂纹的逐渐扩展,致使轮齿发生疲劳折断。
而用脆性材料(如铸铁、整体淬火钢等)制成的齿轮,当受到严重短期过载或很大冲击时,轮齿容易发生突然过载折断。
提高轮齿抗折断能力的措施有:减小齿根应力集中,对齿根表层进行强化处理,采用正变位齿轮传动,增大轴及其支承刚度,采用合适的热处理方式增强轮齿齿芯的韧性。
全齿折断局部齿折断B、齿面点蚀齿面点蚀是一种齿面接触疲劳破坏,经常发生在润滑良好的闭式齿轮传动中。
在变化的接触应力、齿面摩擦力和润滑剂反复作用下,轮齿表层下一定深度产生裂纹,裂纹逐渐发展导致轮齿表面出现疲劳裂纹,疲劳裂纹扩展的结果是使齿面金属脱落而形成麻点状凹坑,这种现象就称为齿面疲劳点蚀。
发生点蚀后,齿廓形状遭破坏,齿轮在啮合过程中会产生剧裂的振动,噪音增大,以至于齿轮不能正常工作而使传动失效。
实践表明,疲劳点蚀首先出现在齿面节线附近的齿根部分。
提高齿轮的接触疲劳强度的措施:提高齿面硬度、降低齿面粗糙度、合理选用润滑油粘度,采用正变位齿轮传动等。
设计时为避免齿面点蚀失效,应进行齿面接触疲劳强度计算。
疲劳点蚀C、齿面磨粒磨损在齿轮传动中,随着工作环境的不同,齿面间存在多种形式的磨损情况。
当齿面间落入砂粒、铁屑、非金属物等磨粒性物质时,会发生磨粒磨损。
齿面磨损后,齿廓失去正确形状,引起冲击、振动和噪声,磨损严重时,由于齿厚减薄而可能发生轮齿折断。
磨粒磨损是开式齿轮传动的主要失效形式。
提高抗磨料磨损能力的措施:改善密封和润滑条件、在润滑油中加入减摩添加剂、保持润滑油的清洁、提高齿面硬度等。
齿面磨损D、齿面胶合互相啮合的轮齿齿面,在一定的温度或压力作用下,发生粘着,随着齿面的相对运动,粘焊金属被撕脱后,齿面上沿滑动方向形成沟痕,这种现象称为胶合。
胶合发生在:高速重载齿轮传动中(如航空齿轮传动),使啮合点处瞬时温度过高,润滑失效,致使相啮合两齿面金属尖峰直接接触并相互粘连在一起,造成胶合;重载低速齿轮传动中,不易形成油膜,或由于局部偏载使油膜破坏,也会造成胶合。
胶合发生在齿面相对滑动速度大的齿顶或齿根部位。
齿面一旦出现胶合,不但齿面温度升高,而且齿轮的振动和噪声也增大,导致失效。
减缓或防止齿面胶合的方法有:减小模数,降低齿高,降低滑动系数;提高齿面硬度和降低齿面粗糙度;采用齿廓修形,提高传动平稳性;采用抗胶合能力强的齿轮材料和加入极压添加剂的润滑油等。
齿面胶合E、塑性变形塑性变形属于轮齿永久变形,是由于在过大的应力作用下,轮齿材料处于屈服状态而产生的齿面或齿体塑性流动所形成的。
齿面塑性变形常发生的齿面材料较软、低速重载的传动中。
当轮齿材料较软,载荷很大时,轮齿在啮合过程中,齿面油膜破坏,摩擦力剧增,而塑性流动方向和齿面所受摩擦力的方向一致,齿面表层的材料就会沿着摩擦力的方向产生塑性变形。
提高抗塑性变形能力的措施:适当提高齿面硬度,采用粘度高的润滑油,可防止或减轻齿面产生塑性变形。
塑性变形(2)设计准则齿轮失效形式的分析,为齿轮的设计和制造、使用与维护提供了科学的依据。