工件材料的切削加工性
合集下载
第八章工件材料的切削加工性与切削液

第八章 工件材料的切削加工 性与切削液
8.1 工件材料的切削加工性 8.3 切削液及其合理选用
8.1 工件材料的切削加工性
8.1.1 切削加工性的相对性
工件材料的切削加工性是在一定切削条件,工件材料 切削加工的难易程度。
比如:纯铁的粗加工容易,精加工时表面粗糙度很难达 到要求;不锈钢在普通机床上加工容易,在自动化生产时因 不断屑会使生产中断等等。
8.1.2 切削加工性的衡量指标
归纳为以下几种: ➢ 1.以刀具使用寿命衡量切削加工性
在相同的切削条件下,刀具使用寿命长,工件材料的切 削加工性好。
2.以切削速度衡量切削加工性 在刀具使用寿命T相同的前提下,切削某种材料允许的 切削速度vT 高,切削加工性好;如取刀具使用寿命 T=60min,则vT可写作v60。
磨削速度高、温度高,热应力会使工件变形,甚至产生 表面裂纹,且磨削产生的碎屑会划伤已加工表面和机床滑动 表面。所以宜选用冷却和清洗性能好的水溶液或乳化液。但 磨削难加工材料时,宜选用润滑性能好的极压切削油。
(5)封闭或半封闭容屑加工。 钻削、攻丝、铰孔和拉削等需要切 削液有较好的冷却、 润滑及清洗性能,以减小刀-屑摩擦生热带走切屑,宜选用 乳化液、极压乳化液和极压切削液。
8.3.2切削液的合理选用和使用方法
➢ 1、切削液的合理选用 切削液的种类很多,性能各异,应根据工件材料、刀具
材料、加工方法和加工要求合理选用。一般选用原则如下:
(1)粗加工。 选用冷却性能为主的切削液(如质量分数为3%~5%的乳 化液),以降低切削温度。
硬质合金刀具耐热性好,一般不用切削液。 在低速切削时,刀具以硬质点磨损为主,宜选用以润滑性能 为主的切削油; 高速度下切削时,刀具主要是热磨损,要求切削液油良好的 冷却性能,宜选用水溶液和乳化液.
8.1 工件材料的切削加工性 8.3 切削液及其合理选用
8.1 工件材料的切削加工性
8.1.1 切削加工性的相对性
工件材料的切削加工性是在一定切削条件,工件材料 切削加工的难易程度。
比如:纯铁的粗加工容易,精加工时表面粗糙度很难达 到要求;不锈钢在普通机床上加工容易,在自动化生产时因 不断屑会使生产中断等等。
8.1.2 切削加工性的衡量指标
归纳为以下几种: ➢ 1.以刀具使用寿命衡量切削加工性
在相同的切削条件下,刀具使用寿命长,工件材料的切 削加工性好。
2.以切削速度衡量切削加工性 在刀具使用寿命T相同的前提下,切削某种材料允许的 切削速度vT 高,切削加工性好;如取刀具使用寿命 T=60min,则vT可写作v60。
磨削速度高、温度高,热应力会使工件变形,甚至产生 表面裂纹,且磨削产生的碎屑会划伤已加工表面和机床滑动 表面。所以宜选用冷却和清洗性能好的水溶液或乳化液。但 磨削难加工材料时,宜选用润滑性能好的极压切削油。
(5)封闭或半封闭容屑加工。 钻削、攻丝、铰孔和拉削等需要切 削液有较好的冷却、 润滑及清洗性能,以减小刀-屑摩擦生热带走切屑,宜选用 乳化液、极压乳化液和极压切削液。
8.3.2切削液的合理选用和使用方法
➢ 1、切削液的合理选用 切削液的种类很多,性能各异,应根据工件材料、刀具
材料、加工方法和加工要求合理选用。一般选用原则如下:
(1)粗加工。 选用冷却性能为主的切削液(如质量分数为3%~5%的乳 化液),以降低切削温度。
硬质合金刀具耐热性好,一般不用切削液。 在低速切削时,刀具以硬质点磨损为主,宜选用以润滑性能 为主的切削油; 高速度下切削时,刀具主要是热磨损,要求切削液油良好的 冷却性能,宜选用水溶液和乳化液.
第四章 工件材料的切削加工性

二二、、金金属属材材料料化化学学成成分分的的影影响响
铬能在铁素体中固溶,又能形成碳化物。 当含铬量小于0.5%,对切削加工性的影响 很小。含铬量进一步增加,则钢的硬度、强 度提高,切削加工性有所下降。
镍:镍能在铁素体中固溶,使钢的强度 和韧性均有所提高,导热系数降低,使切削 加工性变差。当含镍量大于8%后,形成了 奥氏体钢,加工硬化严重,切削加工性就更 差了。
3.普通铸铁:与具有相同基体组织的碳素 钢相比,切削加工性好
其金相组织是金属基体加游离态石墨。 石墨:降低了铸铁的塑性,切屑易断,有
润滑作用,使切削力小,刀具磨损小。 但石墨易脱落,使已加工表面粗糙。切削
铸铁时形成崩碎切屑,造成切屑与前刀面 的接触长度非常短,使切削力、切削热集 中在刃区,最高温度在靠近切削刃的后刀 面上。
二、金属材料化学成分的影响
氮:它在钢中会形成硬而脆的 氮化物,使切削加工性变差。
各种元素在小于2%的含量时对钢的切削加工性的影响
三、金属材料热处理状态和金相组织的影响
铁素体 : 由于铁素体含碳很少,故其性能接近
于纯铁,是一种很软而又很韧的组织。在 切削铁素 体时,虽然刀具不易被擦伤, 但与刀面冷焊现象严重,使刀具产生冷焊 磨损。又容易产生积屑瘤,使加工表面质 量恶化。故铁素体的切削加工性并不好。 通过热处理(如正火)或冷作变形,提高其 硬度,降低其韧性,可使切削加工性得到 改善。
二、金属材料化学成分的影响
钼:钼能形成碳化物,能提高钢的硬度, 降低塑性。含钼量在0.15%—0.4%范围内, 切削加工性略有改善。大于0.5%后,切削 加工性降低。
钒:钒能形成碳化物,并能使钢的 组织细密,提高硬度,降低塑性。当 含量增多后使切削加工性变差,含量 少时对切削加工性略有好处。
第七节工件材料的切削加工性

3. 粗、精加工中切削用量的选择原则
粗加工时,应以提高生产率为主,同时保证 规定的刀具寿命。
➢ 切削深度:在机床功率足够时,尽量一次完 成加工余量。
➢ 进给量:根据机床-刀具-夹具-工艺系统刚性 选择最大的进给量。
➢ 切削速度:根据已选定的切削深度和进给量、 工件材料、刀具材料,选择中等偏下的切削 速度。
最低成本刀具寿命:以每件产品(或工序)的
加工费用最低而确定的刀具寿命。
其它原则
➢ 根据刀具的复杂程度,即制造和磨刀成本选择。 ➢ 机夹可转位刀具寿命可选择的短一些。 ➢ 对装刀、换刀、调刀比较复杂的多刀机床、组
合机床、自动化加工刀具,刀具寿命要选得高 一些。 ➢ 关键工序的刀具寿命要选得低一些。 ➢ 要保证大件加工一次走刀完成加工。
第七节
工件材 料的切 削加工
性
1. 切削加工性:指工件材料被切削加工 的难易程度。
2. 衡量切削加工性的指标
以加工质量的好坏衡量切削加工性 以刀具耐用度衡量切削加工性
➢
在保证相同刀具耐用度的前提下,切削这种材料允
Hale Waihona Puke 许的最大切削速度。➢
在相同的切削条件下,切削这种材料的刀具耐用度。
➢
在相同的切削条件下,保证切削这种材料达到磨钝
2. 制定切削用量时应考虑的因素
加工质量 切削加工生产率 刀具寿命 在多刀切削和使用组合刀具切削时,应把
各刀具中允许的切削用量中最低的参数作 为调整机床的参数。在自动线加工中,还 要考虑生产节拍。
最高生产率刀具寿命:以单位时间生产最多数
量的产品或加工每个零件所消耗的生产时间最 短而确定的刀具寿命。
➢ 粗加工 根据工件材料、刀杆尺寸、 工件直径和已确定的背吃刀量选择。
第2-7节工件材料的切削加工性

参考资料1:不锈钢的切削加工性
与45钢相比,1Cr18Ni9Ti不锈钢的相对可切削性约为0.3-.05之间,是一 种难切削材料。 其难加工性主要表现在: 高温强度和高温硬度高,一般钢材切削时,随着切削温度的升高其强度 会明显降低,切屑易被切离,而1Cr18Ni9Ti在700度时仍不能降低其机 械性能,故切屑不易被切离,切削过程中切削力大,刀具易磨损。 塑性和韧性高,虽然1Cr18Ni9Ti的抗拉强度和硬度都不高,但综合性能 很好,塑性和韧性高,它的延伸率、断面收缩率和冲击值都较高, 1Cr18Ni9Ti的延伸率是40%,是40#的210-237%,是45#的250-280%, 是20Cr、40Cr钢的400-500%,所以切屑不易切离、卷曲和折断,切屑 变形所消耗的功能增多,如切除一定体积的1Cr18Ni9Ti所消耗的能量比 切除相同体积的低碳钢约高50%,并且大部分能量转化为热能,使切削 温度升高。 由 于1Cr18Ni9Ti不易加工,切屑不易切离和折断,故刀具和工件之间所 产生的摩擦热也多,而不锈钢1Cr18Ni9Ti的导热率低(约为普通钢的1/21/3),散热差,由切屑带走的热量少。大部分的热量被刀具吸收,致使 刀具的温度升高,加剧刀具磨损。
2、工件材料化学成分的影响 (1)钢材的化学成分对切削加工性的影响
碳素钢的强度与硬度随含碳量的增加而提高,而塑性与韧性 随含碳量的增加而减小。低碳钢的塑性和韧性较高,又不易断 屑,因此切削加工性较差;高碳钢的强度和硬度较高,易使刀 具磨损,因此切削加工性较差;中碳钢的切削加工性较好。 在钢中加入铬、镍、钒、钼、钨、锰、硅、铝等合金元素可 以改变钢的切削加工性。
铁的加工性比冷硬铸铁好。
(3)以切屑控制或断屑的难易为衡量指标
在自动线上或自动机床上,常以切屑控制或断屑的难易程度 作为衡量材料切削加工性的指标。
第七章 工件材料切削加工性

立方氮化硼刀具进行切削加工,或采用磨削加工方 式。该材料额韧性低,脆性大,切削时刀具破损和 磨损严重 ,刀具耐用度低。
二、复合材料的切削加工性
复合材料是指用两种或两种以上物理与化学形状 不同的物质,人工制成的多组元固体材料。复合材 料是多组元(相)体系。
复合材料的组成相: 基体相(起粘结作用)和增 强相(提高强度和刚度的作用)
第七章 工件材料切削加工性
7.1 工件材料切削加工性的概念和衡量指标
一、切削加工性的概念
切削加工性是指在一定切削条件下,对工件材料进行 切削加工的难易程度。 如难加工材料, 加工性差。
切削加工性是相对的
二、
1、以加工质量衡量切削加工性:在一定条件下, 以是否易达到所要求的表面质量的各项指标来衡量。
常以σb=0.637GPa(60 kgf/min)的45钢的
V之6相0作比为,基则准得,相写对作加工(KVv性60K()VvVj,6为600)其j 它被切材料的V60与
当Kv>1时, 表明该材料比45钢易切削; 当Kv<1时, 表明该材料比45钢难切削。 各种材料的相对加工性Kv乘以45钢的切削速度, 即可得出 切削各种材料的可用切削速度。
材料的化学成分是通过对其物理力学性能的影响而影响 切削加工性的。钢(高碳钢、中碳钢、低碳钢)
钢中加入Cr、Ni、Mn、V、Mo等可提高强度和硬度; 而加入Al、Si等易形成硬质点,加剧刀具磨损。
易切钢
铸铁(化学元素对碳的石墨化作用,促进石墨化作用 (Al、Si、Ni、Cu、Ti)时切削加工性提高,反之降低。
4.切削条件对切削加工性的影响
二、改善工件材料切削加工性的途径
1.调整化学成分,
易切钢:切削力小,容易断屑刀具耐用度高加工表面 质量好。
二、复合材料的切削加工性
复合材料是指用两种或两种以上物理与化学形状 不同的物质,人工制成的多组元固体材料。复合材 料是多组元(相)体系。
复合材料的组成相: 基体相(起粘结作用)和增 强相(提高强度和刚度的作用)
第七章 工件材料切削加工性
7.1 工件材料切削加工性的概念和衡量指标
一、切削加工性的概念
切削加工性是指在一定切削条件下,对工件材料进行 切削加工的难易程度。 如难加工材料, 加工性差。
切削加工性是相对的
二、
1、以加工质量衡量切削加工性:在一定条件下, 以是否易达到所要求的表面质量的各项指标来衡量。
常以σb=0.637GPa(60 kgf/min)的45钢的
V之6相0作比为,基则准得,相写对作加工(KVv性60K()VvVj,6为600)其j 它被切材料的V60与
当Kv>1时, 表明该材料比45钢易切削; 当Kv<1时, 表明该材料比45钢难切削。 各种材料的相对加工性Kv乘以45钢的切削速度, 即可得出 切削各种材料的可用切削速度。
材料的化学成分是通过对其物理力学性能的影响而影响 切削加工性的。钢(高碳钢、中碳钢、低碳钢)
钢中加入Cr、Ni、Mn、V、Mo等可提高强度和硬度; 而加入Al、Si等易形成硬质点,加剧刀具磨损。
易切钢
铸铁(化学元素对碳的石墨化作用,促进石墨化作用 (Al、Si、Ni、Cu、Ti)时切削加工性提高,反之降低。
4.切削条件对切削加工性的影响
二、改善工件材料切削加工性的途径
1.调整化学成分,
易切钢:切削力小,容易断屑刀具耐用度高加工表面 质量好。
工件材料的切削加工性
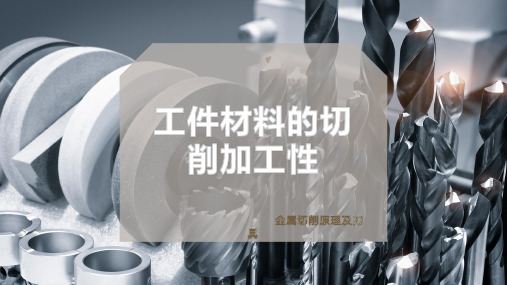
工件材料的切削加工性
以刀具耐用度衡量 以工性
1.工件材料切 削加工性的衡 量指标
以切削力和切 削温度衡量切 削加工性
以加工表面质量 衡量切削加工性
2.工件材料物理力学性能的影响
硬度
强度
塑性与韧性
导热系数
工件材料硬度 包括常温硬度、 高温硬度。
2)合金元素
为了改善钢的性能,可加入一些合金元属如铬(Cr)、镍(Ni)、 钒(V)、钼(Mo)、钨(W)、锰(Mn)、硅(Si)和铝(Al)等。
其中Cr、Ni、V、Mo、W、Mn等元素大都能提高钢的强度和硬度;Si 和Al等元素容易形成氧化铝和氧化硅等硬质点而使刀具磨损加剧。当这 些元素含量较低时(一般以0.3%为限),对钢的切削加工性能影响不 大;当这些元素含量超过0.3%时,对钢的切削加工性是不利的。
1)对钢的切削加工 性的影响
不同种类金相组织对 切削加工性有直接影 响。钢中铁素体与珠 光体的比例关系影响 钢的切削加工性。
2)对铸铁切削加 工性的影响
按金相组织的不同,铸 铁可分为白口铁、马口 铁、灰铸铁和球墨铸铁。 它们的硬度依次递减, 塑性依次增高,切削加 工性依次递增。
在钢中加入微量的硫(S)、硒(Se)、铅(Pb)、铋(Bi)、钙 (Ca)等元素会在钢中形成夹杂物,能使钢脆化,或起润滑作用,减轻 刀具磨损,改善工件材料的切削加工性。加入磷(P)虽然使钢的强度 与硬度有所提高,但可使其韧性与塑性显著下降,因此,有利于断屑。
4.工件材料金相组织的影响
工件材料金相 组织的影响
工件材料强度 包括常温强度 和高温强度。
工件材料的塑性 以延伸率表示, 工件材料的线膨 值越大,则塑性 胀系数和弹性模 越大。工件材料 的韧性以冲击韧 量也对切削加工 度表示,值越大, 性有影响。 表示工件材料在 破断时吸收的能 量越多。
以刀具耐用度衡量 以工性
1.工件材料切 削加工性的衡 量指标
以切削力和切 削温度衡量切 削加工性
以加工表面质量 衡量切削加工性
2.工件材料物理力学性能的影响
硬度
强度
塑性与韧性
导热系数
工件材料硬度 包括常温硬度、 高温硬度。
2)合金元素
为了改善钢的性能,可加入一些合金元属如铬(Cr)、镍(Ni)、 钒(V)、钼(Mo)、钨(W)、锰(Mn)、硅(Si)和铝(Al)等。
其中Cr、Ni、V、Mo、W、Mn等元素大都能提高钢的强度和硬度;Si 和Al等元素容易形成氧化铝和氧化硅等硬质点而使刀具磨损加剧。当这 些元素含量较低时(一般以0.3%为限),对钢的切削加工性能影响不 大;当这些元素含量超过0.3%时,对钢的切削加工性是不利的。
1)对钢的切削加工 性的影响
不同种类金相组织对 切削加工性有直接影 响。钢中铁素体与珠 光体的比例关系影响 钢的切削加工性。
2)对铸铁切削加 工性的影响
按金相组织的不同,铸 铁可分为白口铁、马口 铁、灰铸铁和球墨铸铁。 它们的硬度依次递减, 塑性依次增高,切削加 工性依次递增。
在钢中加入微量的硫(S)、硒(Se)、铅(Pb)、铋(Bi)、钙 (Ca)等元素会在钢中形成夹杂物,能使钢脆化,或起润滑作用,减轻 刀具磨损,改善工件材料的切削加工性。加入磷(P)虽然使钢的强度 与硬度有所提高,但可使其韧性与塑性显著下降,因此,有利于断屑。
4.工件材料金相组织的影响
工件材料金相 组织的影响
工件材料强度 包括常温强度 和高温强度。
工件材料的塑性 以延伸率表示, 工件材料的线膨 值越大,则塑性 胀系数和弹性模 越大。工件材料 的韧性以冲击韧 量也对切削加工 度表示,值越大, 性有影响。 表示工件材料在 破断时吸收的能 量越多。
金属切削与机床第4章提高金属切削效率的途径
表4-13)。
1000 c v n d w
式中: n——工件转速(r/mim); vc——切削速度(m/min); dw——工件待加工表面直径(mm)。
(4- 5)
第4章 提高金属切削效率的途径 表 4-9 切削速度公式中的系数及指数
第4章 提高金属切削效率的途径 表4-10 钢和铸铁的强度与硬度改变时切削速度的修正系数kmv
第4章 提高金属切削效率的途径 2. 进行适当的热处理 将硬度较高的高碳钢、工具钢等进行退火处理,以降低
硬度;将低碳钢通过正火处理,以降低材料的塑性,提高其
硬度;将中碳钢通过调质处理,使材料硬度均匀。这些方法 都可以改善材料的切削加工性。
3. 选择良好的材料状态
低碳钢塑性大,加工性不好,但经过冷拔之后,塑性降
v60 Kr vB60
(4-1)
第4章 提高金属切削效率的途径 式中: v60——某种材料其耐用度为60 min时的切削速度; vB60——切削45钢(σb=0.735 GPa),耐用度为60 min时 的切削速度。 当Kr >1时,表明该材料比45钢容易切削;当Kr <1时, 表明该材料比45钢难加工。
量为1.5 mm,如图4-6所示。要求加工后精度达到h11级,表 面粗糙度为Ra3.2 μ m。试选择切削用量。
第4章 提高金属切削效率的途径
图 4-6 工件加工示意图
第4章 提高金属切削效率的途径 1. 选择刀T15硬质合金焊接车刀,刀具耐用度T=60 min,刀杆尺
2) 副偏角的选择
副偏角主要按加工性质选择,一般取10°~15°,为保 证切断刀刀尖强度,可取1°~2°。
第4章 提高金属切削效率的途径 3. 刀尖形式及选择 图4-3为常见的几种刀尖形式。
第4章 影响切削加工及表面质量
4.2 刀具材料的合理选择
2. 硬质合金的分类和性能 ISO国际标准将硬质合金分为以下三大类: P类:相当于我国的 YT类,用于加工长切屑黑色金
属。 K类:相当于我国的 YG类,用于加工短切屑黑色金 属、有色金属和非金属。 M类:相当于我国的YW类,用于加工长短切屑的黑 色金属、有色金属。
常用刀具材料有碳素工具钢(T10A,T12A)、合金工 具钢(9SiCr、CrWMn)、高速钢、硬质合金、陶瓷、金刚 石、立方氮化硼等。碳素工具钢和合金工具钢因耐热性差、 允许切削速度低,所以常用碳素工具钢制造手用刀具(如锉 刀、刮刀)。用合金工具钢制造低速刀具(如丝锥,板牙 等),陶瓷、金刚石、立方氮化硼仅用于某些难加工材料和 精密、超精密切削加工。目前刀具材料中应用最多的仍是高 速钢和硬质合金。
4.2 刀具材料的合理选择
3. 硬质合金的选用 1)YG类硬质合金主要用于加工铸铁、有色金属及非金属。 加工这类材料时,切屑呈崩碎切屑,切削力、切削热集中在 刀刃附近容易崩刃, YG 类硬质合金强度高,韧性好,导热 性能好,正好满足加工要求。 YG3X、YG6X 还可用于加工 冷硬铸铁、淬火钢、高强度钢、不锈钢、高温合金、钛合金、 硬青铜、硬的和耐磨的绝缘材料。YS2(YG10H)可用于加 工高强度钢、高温合金等难加工材料。 YG6A、YG8A 可加 工铸铁和不锈钢。
4.1 工件材料的切削加工性
4.1 工件材料的切削加工性
4.1.2 影响工件材料切削加工性的因素
一、工件材料的硬度对切削加工性的影响 工件材料的硬度有常温硬度和高温硬度,它们对切削加工性的影响 是不同的。 1. 工件材料的常温硬度对切削加工性的影响 一般情况下,同类工件材料中常温硬度越高的材料其切削加工性 越低。 2. 工件材料的高温硬度对切削加工性的影响 工件材料的高温硬度越高,切削加工性越低。因为工件材料的高温 硬度越高,切削温度越高,刀具材料的硬度在高的切削温度作用下 会下降,刀具材料的硬度与工件材料的硬度比要下降,因此刀具磨 损加剧、耐用度低、切削加工性低。
工件材料的切削加工性
用切削速度来衡量 的相对切削加工性
也可用加工材料的物理、化学和力学性能的高低 来衡量切削该材料的难易程度。见表4.2
1.2 影响材料切削加工性的因素
工件材料切削加工性的好坏,主要决定于工件材料的物 理、力学性能、化学成分、热处理状态和表层质量等。
1.材料的硬度和强度
工件材料在常温和高温下的硬度和强度越高,则在加 工中的切削力越大,切削温度越高,刀具耐用度越低,故 切削加工性就越差。有些材料在常温下其硬度和强度并不 高,但随着切削温度的升高,其硬度和强度也提高,切削 加工性变差。例如不锈钢。
●适当选择热处理方法——例如对于低碳钢进行正火处 理,可适当提高硬度、降低塑性和韧性,使切削加工性得到 改善。对高碳钢或工具钢进行球化退火处理,使金相组织中 的片状和网状渗碳体转变为球状渗碳体,从而降低其硬度, 改善了切削加工性。对于高强度合金钢,通过退火、回火或 正火处理可改善切削加工性。
●采用新的切削加工技术——例如加热切削、低温切削、 振动切削、真空中切削和绝缘切削等,可有效的解决难加工 材料的切削难题。当然,新的切削方法需要专门的设备,增 加了加工成本。
● 此外,还可通过选择加工性能较好的材料状态,以及 选择合理的刀具几何参数,制定合理的切削用量,选用合适 的切削液等措施来改善难加工材料的切削加工性。
金属切削加工
金属切削加工
工件材料的切削加工性
工件材料的切削加工性——是指工件材料可被切削的难 易程度。
1.1 切削加工性的评定指标
●考虑生产率和刀具耐用度的标志方法 生产率一定时,刀具耐用度越高,切削加工性越好。 刀具耐用度一定时,所允许的切削速度越高,切削加工性 越好。切削速度一定时,以达到刀具磨钝标准时所切除的 金属材料体积越大,则材料的切削加工性就越好。
工件材料切削加工性
3.5 工件材料的切削加工性
工件材料切削加工性 指材料被加工成合格零件的难易程度 是一个相对的概念
3.5.1 衡量材料切削加工性的指标 1.以刀具使用寿命T 或切削速度vT来衡量
相同切削条件比T ;T 一定,比速度vT或切除材料体积
2.以切削力或切削温度来衡量 粗加工、机床刚性或功率不足用力或功率;导热差用温度
3.5.3 改善材料切削加工性的途径
1. 调整材料的化学成分
钢中加硫、铅等元素;铸铁中增加石墨成分
2. 进行适当的热处理
低、中碳钢宜选正火处理,均匀组织,调整硬度塑性; 高碳钢宜用球化退火,降低硬度,均匀组织,改善加工性; 中碳以上的合金钢硬度较高,需退火以降低硬度; 不锈钢常要进行调质处理,降低塑性,以便加工; 铸铁需进行退火处理,降低表皮硬度,消除内应力
切削有硬皮的铸、锻件或不锈钢等加工硬化严重的材料时, 应尽量使ap超过硬皮或冷硬层厚度,以避免刀尖过早磨损。
(2)进给量f 的选择 粗加工时,f 的大小主要受机床进给机构强度、刀具的强度 与刚性、工件的装夹刚度等因素的限制。 精加工时,f 的大小主要受加工精度和表面粗糙度的限制。
生产实际中常根据经验或查表法确定f 。 粗加工时根据工件材料、车刀刀杆尺寸、工件直径及以确定 的背吃刀量按表3-6来选择f 。 在半精加工和精加工时,则按加工表面粗糙度要求,根据工 件材料、刀尖圆弧半径、切削速度按表3-7来选择f 。
vc 对T 影响最大,进给量f 次之,背吃刀量ap影响最小。
粗加工中选择切削用量时,应首先选择尽可能大的背吃刀 量ap,其次在工艺条件允许下选择较大的进给量f ,最后 根据合理的刀具使用寿命,用计算法或查表法确定切削速
度vc。这样使vc、f 、ap 的乘积最大,以获得最大生产率
工件材料切削加工性 指材料被加工成合格零件的难易程度 是一个相对的概念
3.5.1 衡量材料切削加工性的指标 1.以刀具使用寿命T 或切削速度vT来衡量
相同切削条件比T ;T 一定,比速度vT或切除材料体积
2.以切削力或切削温度来衡量 粗加工、机床刚性或功率不足用力或功率;导热差用温度
3.5.3 改善材料切削加工性的途径
1. 调整材料的化学成分
钢中加硫、铅等元素;铸铁中增加石墨成分
2. 进行适当的热处理
低、中碳钢宜选正火处理,均匀组织,调整硬度塑性; 高碳钢宜用球化退火,降低硬度,均匀组织,改善加工性; 中碳以上的合金钢硬度较高,需退火以降低硬度; 不锈钢常要进行调质处理,降低塑性,以便加工; 铸铁需进行退火处理,降低表皮硬度,消除内应力
切削有硬皮的铸、锻件或不锈钢等加工硬化严重的材料时, 应尽量使ap超过硬皮或冷硬层厚度,以避免刀尖过早磨损。
(2)进给量f 的选择 粗加工时,f 的大小主要受机床进给机构强度、刀具的强度 与刚性、工件的装夹刚度等因素的限制。 精加工时,f 的大小主要受加工精度和表面粗糙度的限制。
生产实际中常根据经验或查表法确定f 。 粗加工时根据工件材料、车刀刀杆尺寸、工件直径及以确定 的背吃刀量按表3-6来选择f 。 在半精加工和精加工时,则按加工表面粗糙度要求,根据工 件材料、刀尖圆弧半径、切削速度按表3-7来选择f 。
vc 对T 影响最大,进给量f 次之,背吃刀量ap影响最小。
粗加工中选择切削用量时,应首先选择尽可能大的背吃刀 量ap,其次在工艺条件允许下选择较大的进给量f ,最后 根据合理的刀具使用寿命,用计算法或查表法确定切削速
度vc。这样使vc、f 、ap 的乘积最大,以获得最大生产率
- 1、下载文档前请自行甄别文档内容的完整性,平台不提供额外的编辑、内容补充、找答案等附加服务。
- 2、"仅部分预览"的文档,不可在线预览部分如存在完整性等问题,可反馈申请退款(可完整预览的文档不适用该条件!)。
- 3、如文档侵犯您的权益,请联系客服反馈,我们会尽快为您处理(人工客服工作时间:9:00-18:30)。
P E =7.5KW,取机床传动效率 η m =0.8,则
Pm 2.64
m
=
0.8
KW=3.3KW<P =7.5KW E
校核结果表明,机床功率是足够的。
13
3.6.2 切削用量三要素的选用
(5)校核机床进给机构强度 由上可知,主切削力 Fz =1800N, 再 由 同 样 办 法 , 分 别 计 算 出 本 例 的 背 向 力 Fy =392N , 进 给 力 Fx =894N。考虑到机床导轨和溜板之间由 Fz 和 Fy 所产生的摩擦力, 设摩擦系数 μ s =0.1,则机床进给机构承受的力为
2.切削用量的选用原则
◆粗加工阶段切削用量的选用原则
粗加工阶段切削用量应根据切削用量对刀具耐用度的影响大小,首先 选取尽可能大的背吃刀量ap,其次选取尽可能大的进给量f,最后按照刀 具耐用度的限制确定合理的切削速度vc。
◆精加工阶段切削用量的选用原则
精加工阶段切削用量应选用较高的切削速度vc、尽可能大的背吃刀量ap 和较小的进给量f。
3.5.1 衡量材料切削加工性的指标
➢刀具耐用度T或一定耐用度下允许的切削速度vT指标 在切削普通金属材料时,常用刀具耐用度达到60min 时所允许的切削速度的高低来评定材料加工性的好坏 ,记作v60。 ➢切削力、切削温度或切削功率指标
在粗加工或机床刚性、动力不足时,可用切削力作 为工件材料切削加工性指标。在相同加工条件下,凡 切削力大、切削温度高、消耗功率多的材料较难加工 ,切削加工性差;反之,则切削加工性好。
9
3.6.2 切削用量三要素的选用
10
3.6.2 切削用量三要素的选用
解 为达到规定的加工要求,此工序应安排粗车和半精车两
次走刀,粗车时将 50mm 外圆车至 45mm;半精车时将 45mm
外圆车至
44
0 0.062
mm。
1.确定粗车切削用量
(1)背吃刀量 a P a P =(50-45)/2mm=2.5mm。 (2)进给量 f 根据已知条件,从表 3-7 中查得 f=0.4~
2
3.5.2 改善材料切削加工性的途径
➢采用热处理改善材料切削加工性
同样成分的材料,当金相组织不同时,它们的物理机械 性能就不一样,因而可切削加工性就有差别。此时可通过
适当的热处理来改善材料的切削加工性。 ➢调整材料的化学成分
材料的化学成份直接影响其力学性能,如碳素钢的强度 、硬度随其含碳量的增加而提高,而塑性韧性则降低。因 此,高碳钢和低碳钢的切削加工性都不如综合机械性能居 于其中的中碳钢的切削加工性。
6
3.6.2 切削用量三要素的选用
1. 确定切削深度 ap 粗加工时:尽可能一次切除全部余量,余量过大时可分 2 次走刀,第一次走刀的切削深度取单边余量的 2/3~3/4 , 第二次走刀取加工余量的 1/4~1/3。 半精加工时:通常取ap =0.5~2mm 精加工时:通常取ap =0.1~0.4mm
知:
毛坯:直径为 d= 50mm,材料为 45 钢,σ b =0.637GPa;
加工要求:车外圆至
44 0 0.062
,表面粗糙度为
R
a
3.2μm;
刀具:焊接式硬质合金外圆车刀,刀片材料为 YT15,刀杆截
面尺寸为 16mm 25mm;
车刀切削部分几何参数:
=15
,
=8
,
r
=75
,
' r
=10
,
s =0 ,r =1mm。试求该车削工序的切削用量。
1
3.5.1 衡量材料切削加工性的指标
➢加工表面质量指标 对于精加工而言,希望最终获得比较高的精度和表
面质量,因此常以易获得好的加工表面质量作为衡量材 料切削加工性的指标。加工中凡容易获得好的加工表 面质量的材料,其切削加工性较好,反之较差。 ➢切屑控制或断屑的难易指标
切削时,凡切屑易于控制或断屑性能良好的材料, 其切削加工性好,反之则较差。
0.5mm/r , 按 CA6140 车 床 说 明 书 中 实 有 的 进 给 量 , 确 定
f=0.48mm/r。
11
3.6.2 切削用量三要素的选用
(3)切削速度 vc :切削速度可由式(3-30)计算,也可查表确
定,本例采用查表法确定。
查表 3-9 可取 vc =100m/min,由此可推算出机床主轴转速为
F j = Fx + s ( Fz + Fy )=[894+0.1 (1800+392)]N=1113.2N
(4)校核机床功率 由有关手册查出相关系数和计算公式,
先计算出主切削力 Fz (F c ),再将主切削力 Fz 代入公式计算出切
削功率 Pm 。通过计算,本例的主切削力 Fz =1800N,切削功率
Pm =2.64KW 。 查 阅 机 床 说 明 书 知 , CA6140 车 床 主 电 机 功 率
3
3.5.2 改善材料切削加工性的途径
➢随堂作业
1.衡量材料切削加工性的指标有哪些? 2.如何改善材料切削加工性?
4
机械制造技术基础
第3章 金属切削过程及控制
3.6 切削用量的合理选择
5
3.6.1 切削用量的选用原则
1.制定切削用量时考虑的因素 两个因素:生产率和刀具耐用度
制定切削用量时不能仅仅单一地考虑生产效率,还要兼顾到刀具 耐用度
2. 确定进给量 f ◆ 粗切时根据工艺系统强度和刚度条件确定(计算或查表3-7) ◆ 精切时根据加工表面粗糙度要求确定(计算或查表3-7)
7
3.6.2 切削用量三要素的选用
3. 确定切削速度 vc 粗加工时,切削速度 受刀具耐用度和机床功率的限制; 精加工时,机床功率足够,切削速度 主要受刀具耐用度 的限制。(可通过计算或查表获得)
1000vc 1000 90 n= d = 3.14 50 r/min=573r/min 按 CA6140 车床说明书选取实有的机床主轴转速为 560r/min, 故实际的切削速度为
nd 3.14 560 50
vc = 1000 = 1000 m/min=87.9m/min
12
3.6.2 切削用量三要素的选用
4. 校验机床功率(仅对粗加工)
由:Fzvc≤PEη×1000
,可导出:vc≤PEη×1000/Fz
式中 PE —— 机床电机功率(KW); ηm—— 机床传动效率; Fz —— 主切削力(N)。
8
ቤተ መጻሕፍቲ ባይዱ
3.6.2 切削用量三要素的选用
例 3-1 工件在 CA6140 型车床上车外圆,如图 3-31 所示。已