工艺方案的选择与论证
污水处理工艺论证
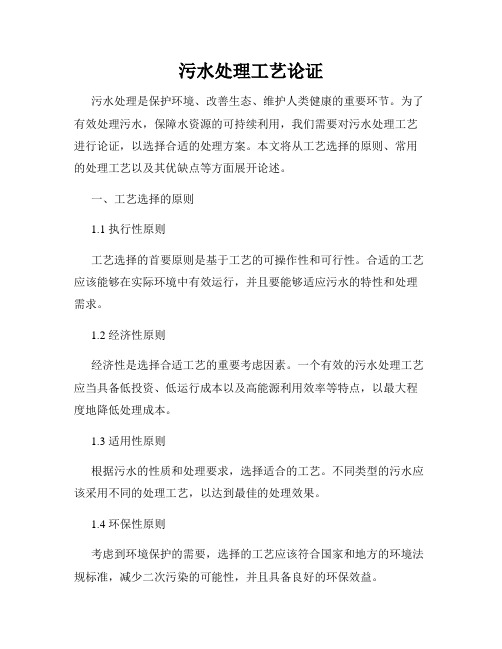
污水处理工艺论证污水处理是保护环境、改善生态、维护人类健康的重要环节。
为了有效处理污水,保障水资源的可持续利用,我们需要对污水处理工艺进行论证,以选择合适的处理方案。
本文将从工艺选择的原则、常用的处理工艺以及其优缺点等方面展开论述。
一、工艺选择的原则1.1 执行性原则工艺选择的首要原则是基于工艺的可操作性和可行性。
合适的工艺应该能够在实际环境中有效运行,并且要能够适应污水的特性和处理需求。
1.2 经济性原则经济性是选择合适工艺的重要考虑因素。
一个有效的污水处理工艺应当具备低投资、低运行成本以及高能源利用效率等特点,以最大程度地降低处理成本。
1.3 适用性原则根据污水的性质和处理要求,选择适合的工艺。
不同类型的污水应该采用不同的处理工艺,以达到最佳的处理效果。
1.4 环保性原则考虑到环境保护的需要,选择的工艺应该符合国家和地方的环境法规标准,减少二次污染的可能性,并且具备良好的环保效益。
二、常用的污水处理工艺2.1 传统的物理化学处理工艺传统的物理化学处理工艺包括沉淀、过滤、吸附等方法。
这些方法通过去除悬浮物、溶解物和微生物等污染物,达到净化水体的目的。
然而,这些方法存在处理效率低、对混合污水处理能力差、处理成本高等问题。
2.2 生物处理工艺生物处理工艺是目前最常用的污水处理方法之一。
生物处理通过利用微生物来分解、氧化和吸附污染物,将污水中的有机物转化为无害物质。
生物处理工艺包括活性污泥法、固定化床法、厌氧消化等。
生物处理工艺具有处理效果好、运行成本低的优点,但也存在对温度、COD/COD比例等条件较为敏感的问题。
2.3 膜分离技术膜分离技术是近年来发展较快的一种污水处理技术。
它通过膜的筛选作用,将水中的悬浮物、溶解物、微生物等分离出来,实现有效的污水净化。
膜分离技术具有处理效率高、占地面积小、适用于中小型处理装置等优点,但也存在较高的能耗和运维成本。
三、污水处理工艺的优缺点3.1 物理化学处理工艺的优缺点物理化学处理工艺的优点是处理效率高,较适用于处理工业污水或特殊的废水。
工艺方案论证

工艺方案论证一、引言在制造业领域,工艺方案的选取和论证是非常关键的环节。
一个合理有效的工艺方案不仅可以提高产品的质量和生产效率,还可以降低成本并增强企业的竞争力。
本文将围绕工艺方案的论证展开讨论,重点介绍论证的重要性、论证的基本原则以及一些常用的论证方法。
二、论证的重要性1. 提高产品质量通过对工艺方案的论证,可以充分考虑产品的特性和要求,找出最合适的生产工艺,从而有效提高产品的质量。
论证工艺方案可以避免一些生产中的问题,如缺陷、不合格品等。
2. 提高生产效率一个合理的工艺方案可以提高生产效率,使生产过程更加顺利和高效。
论证工艺方案可以帮助企业合理规划生产流程,优化生产设备配置,减少生产环节,从而提高生产效率。
3. 降低成本通过对工艺方案的论证,可以选择更加经济和高效的生产工艺,从而降低成本。
论证工艺方案可以帮助企业找到成本最低的生产方案,减少资源浪费,提高经济效益。
4. 增强竞争力一个合理有效的工艺方案可以提高产品质量、生产效率和降低成本,从而增强企业的竞争力。
通过论证工艺方案,企业可以不断优化生产工艺,提高产品的市场竞争力,更好地满足消费者的需求。
三、论证的基本原则1. 客观性原则论证工艺方案要客观公正,避免主观臆断和个人偏见的影响。
应该充分考虑各种因素的影响,如技术要求、硬件设备、人员素质等,以客观的态度进行论证。
2. 综合性原则论证工艺方案要综合考虑各方面的因素,不能片面地追求某一方面的利益。
要综合考虑质量、效率、成本等多个方面的因素,找到最优解决方案。
3. 可行性原则论证工艺方案要具有可行性,不能只是理论上可行,而是在实际操作中能够实施的方案。
要考虑实际生产条件、现有资源和技术水平等因素,确保方案的可实施性。
4. 成本效益原则论证工艺方案要追求最佳的成本效益。
要综合考虑成本和效益的关系,确保在成本可控的情况下实现最大程度的效益。
四、常用的论证方法1. 数据分析法通过对相关数据进行分析,了解产品的特性、工艺要求、生产设备的性能等,基于数据进行论证,找出最合适的工艺方案。
生产硫酸工艺方案模板及论证

生产硫酸工艺方案模板及论证
生产硫酸的工艺可以分为烟气法和液相法两种,常用的是烟气法,方案如下:
1. 原料采购:选择纯度高的硫矿或黄铁矿作为原料。
2. 矿石选矿:经过磨矿、选矿等工艺处理,将原料中的杂质去除,达到要求的纯度。
3. 烧结:烧结炉内矿石在高温下发生氧化反应,产生SO2气体,同时生成硫酸铁和硫酸铜等。
4. 净化:将SO2气体经过吸收装置,净化处理,以去除SO2中的尾气。
5. 催化氧化:经过浓硫酸的催化作用,将净化处理后的SO2氧化成SO3。
6. 吸收成硫酸:将SO3与浓硫酸反应,生成硫酸。
7. 精制:硫酸精制后,达到标准纯度要求,即可包装出售。
论证:
1. 选矿工艺流程的选择,应根据原料的品质进行选择,确保原料达到要求的纯度。
2. 烧结技术的选择,应确保SO2的产生量达到设计要求,同时减少废气排放的量。
3. 净化技术的选择,应确保废气中的二氧化硫得到有效地去除,排放达标。
4. 催化氧化技术的选择,应确保SO2的氧化率达到要求,同时减少催化剂消耗量。
5. 吸收成硫酸技术的选择,应确保硫酸转化率达到要求,同时减少反应时间和反应温度。
6. 精制工艺的选择,应确保最终产品的质量达到标准,同时减少废料产生的量。
工程方案论证包括哪些内容

工程方案论证包括哪些内容一、项目概述本项目是一家新建的化工生产厂家,主要生产石油化工产品。
项目位于国家级经济技术开发区内,总投资为5000万元,占地面积20000平方米。
该项目拟引进先进技术和设备,采用现代化生产工艺,力争成为国内领先的化工产品生产企业。
二、技术方案1.生产工艺本项目主要生产石油化工产品,采用先进生产工艺,包括原料处理、生产反应、产品分离、精制、成品储存等过程。
为提高产品质量和节约能源,项目拟引进节能环保的生产设备和技术,建设现代化化工生产线。
2.生产设备项目拟购置先进的化工生产设备,包括反应釜、分离设备、精馏塔、压缩机、泵等设备。
引进高效环保的设备将有助于提高生产效率和降低能耗,满足市场需求。
三、经济效益1.投资回收期根据市场调研及资金筹措方案,预计本项目投资回收期为5年。
2.盈利分析项目建成后,预计年销售收入为8000万元,年净利润为2000万元,达产后将能够形成较为稳定的盈利。
3.就业效益该项目投产后,预计可提供就业岗位100个以上,为地方经济发展和劳动力就业提供了有力支持。
四、风险分析1.市场风险化工行业较为成熟,市场竞争激烈。
可能存在原料价格波动、产品销售不畅等因素,增加了市场竞争风险。
2.生产风险化工生产存在一定的安全风险,可能导致生产事故,给企业造成财产损失及不良影响。
3.政策风险化工行业受到国家政策、环保法规的影响较大,政策调整可能对企业经营造成一定影响,需要加大政策研判力度。
五、环境影响评价1.资源利用本项目主要借用当地的电力、水资源等,对当地资源利用具有良好的兼容性。
2.环境保护项目采用现代化的生产工艺和环保设备,能够有效减少污染排放和资源浪费,具有较好的环保性。
3.环境风险项目建设过程中,需加强环境保护工作,减少噪音、粉尘和废水排放,以减少对周边环境的不良影响。
以上是对工程方案论证所涉及的基本内容进行了详细阐述,希望对您有所帮助。
施工方案论证(3篇)
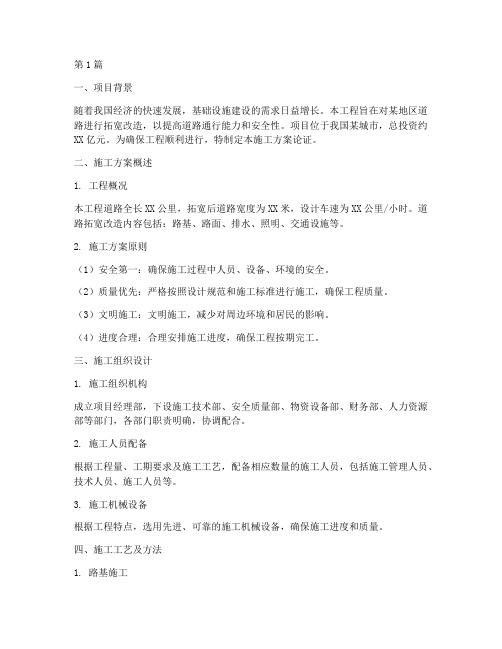
第1篇一、项目背景随着我国经济的快速发展,基础设施建设的需求日益增长。
本工程旨在对某地区道路进行拓宽改造,以提高道路通行能力和安全性。
项目位于我国某城市,总投资约XX亿元。
为确保工程顺利进行,特制定本施工方案论证。
二、施工方案概述1. 工程概况本工程道路全长XX公里,拓宽后道路宽度为XX米,设计车速为XX公里/小时。
道路拓宽改造内容包括:路基、路面、排水、照明、交通设施等。
2. 施工方案原则(1)安全第一:确保施工过程中人员、设备、环境的安全。
(2)质量优先:严格按照设计规范和施工标准进行施工,确保工程质量。
(3)文明施工:文明施工,减少对周边环境和居民的影响。
(4)进度合理:合理安排施工进度,确保工程按期完工。
三、施工组织设计1. 施工组织机构成立项目经理部,下设施工技术部、安全质量部、物资设备部、财务部、人力资源部等部门,各部门职责明确,协调配合。
2. 施工人员配备根据工程量、工期要求及施工工艺,配备相应数量的施工人员,包括施工管理人员、技术人员、施工人员等。
3. 施工机械设备根据工程特点,选用先进、可靠的施工机械设备,确保施工进度和质量。
四、施工工艺及方法1. 路基施工(1)清除地表植被、杂物,进行路基平整。
(2)分层填筑,每层厚度控制在XX厘米,确保压实度达到设计要求。
(3)进行路基边坡防护,采用植草、喷播等技术。
2. 路面施工(1)铺设基层,采用水泥稳定碎石、沥青稳定碎石等材料。
(2)铺设沥青面层,采用沥青混凝土、改性沥青混凝土等材料。
(3)进行路面标线、路面排水设施施工。
3. 排水施工(1)设置排水沟、雨水井、检查井等排水设施。
(2)采用混凝土、预制构件等材料进行施工。
4. 照明施工(1)设置路灯、道路照明电缆等。
(2)采用LED路灯,节能环保。
5. 交通设施施工(1)设置交通标志、标线、隔离栏等。
(2)采用高质量、耐候性强的材料。
五、施工进度计划1. 施工准备阶段:XX个月。
2. 路基施工阶段:XX个月。
工艺流程的选择

工艺流程的选择
《工艺流程的选择》
在工业生产中,工艺流程的选择对产品的质量和生产效率至关重要。
不同的工艺流程可能会导致产品的性能和外观出现巨大的差异,因此企业需要慎重选择适合自己生产需求的工艺流程。
首先,企业需要考虑产品的特性和需求。
比如,如果产品需要精密加工,那么工艺流程必须要具备高精度的加工能力;如果产品需要大批量生产,那么工艺流程必须要具备高效的生产能力。
对于不同的产品特性和需求,企业需要选择不同的工艺流程来满足生产要求。
其次,企业还需要考虑生产成本和资源消耗。
一些工艺流程可能需要大量的能源和原材料,导致生产成本较高;而另一些工艺流程可能具有较低的资源消耗和生产成本。
因此,企业需要综合考虑成本和资源消耗,选择最经济和环保的工艺流程。
最后,企业还需要考虑技术水平和人力资源。
有些工艺流程需要高水平的技术和人力资源来进行操作和控制,而另一些工艺流程则相对简单,能够更容易地进行操作和控制。
因此,企业需要评估自身的技术水平和人力资源情况,选择适合自己的工艺流程。
综合以上因素,企业需要进行全面的分析和评估,选择适合自己需求的工艺流程。
只有选择合适的工艺流程,才能保证产品
的质量和生产效率。
因此,工艺流程的选择是企业生产中的重要环节,需要引起足够的重视和注意。
工艺方案论证
工艺方案论证近年来,随着科技的飞速发展,在各个行业中,工艺方案论证变得越来越重要。
工艺方案论证是指对所采用的工艺方案进行认真研究和论证,以确保其能够实现预期的技术目标和经济效益。
本文将从不同角度探讨工艺方案论证的重要性、内容和方法。
一、重要性工艺方案论证对于项目的成功实施至关重要。
首先,它能够帮助确定最优的工艺方案。
通过综合考量技术、经济和环境等因素,选择最适合的工艺方案将能够最大程度地提高生产效率和降低成本。
其次,工艺方案论证能够提前发现潜在问题和风险,在项目实施前进行充分评估和规避,避免后期出现巨大的损失。
最后,它还能够提升项目的可持续性,减少资源浪费和环境污染,符合可持续发展的要求。
二、内容1. 技术可行性论证技术可行性论证是工艺方案论证的核心内容,主要涉及工艺流程、设备选型和技术指标等方面。
通过对各种技术方案的比较和分析,确定最适宜的技术路线和工艺流程,以确保项目的技术可行性和稳定性。
其中,设备选型是工艺方案论证中的一个关键环节,需要充分考虑设备的技术性能、成本和维护保养等因素。
2. 经济效益论证经济效益论证主要涉及项目的投资、成本和收益等方面。
通过对不同工艺方案的经济效益进行比较和评估,确定最优的经济方案。
在进行经济效益论证时,需要综合考虑项目的投资回收期、成本核算和收益预测等因素,确保项目的经济可行性和盈利能力。
3. 环境影响论证环境影响论证是对工艺方案的环境影响进行评估和规划。
通过综合考虑项目的废物排放、能源消耗和环境保护等因素,制定出最佳的环境保护策略和措施,以减少对环境的负面影响,促进资源的可持续利用。
三、方法1. 实地考察在工艺方案论证的过程中,实地考察是必不可少的环节。
通过实地考察,能够了解现场的具体情况,获取准确的数据和信息,为后续的论证和评估提供有力的依据。
实地考察还可以与项目相关方进行深入交流,探讨技术问题和风险,提前预防和解决潜在的困难和挑战。
2. 数据分析数据分析是工艺方案论证的重要手段。
工艺方案的选择及论证
工艺方案的选择及论证3.1对二甲苯生产工艺选择及比较3.1.1对二甲苯的生产工艺1、由石油制取原油根据馏程不同被切割成不同组分,其中可用于制取甲苯和对二甲苯的馏分被称为“直馏轻质石脑油”,包括从戊烷到终沸点在105℃~170℃之间的所有馏分,这些馏分就是传统工艺中用于生产石油轻芳烃的原料。
用轻质石脑油生产对二甲苯的一般流程是:首先生产石油芳烃BTX(苯、甲苯、二甲苯)馏分,然后经过芳烃转化将苯、甲苯等其它芳烃转换为二甲苯,然后再从混合二甲苯中分离出对二甲苯。
(1)BTX的制取以石脑油为原料制取粗BTX的方法主要有两种:催化裂化和催化重整。
得到的粗BTX是芳烃非芳烃的混合物,再通过萃取精馏、共沸精馏、选择性变压吸附、结品分离和络合物分离等方法便可以得到纯芳烃。
催化裂化是最重要的重质油轻质化过程之一,其主要原料是重质馏分油,主要是直馏减压馏分油(VGO),也包括焦化重馏分油(CGO,通常需加氢精制),经过反再系统、分馏系统、吸收稳定系统得到干气、汽油、柴油、重质油及焦炭,副产物为芳烃。
通常情况下,每生产1t乙烯可产出约1t裂解汽油,其中苯质量分数约为29.1%,BTX总质量分数可高达58.8%。
在催化裂化工艺中,芳香烃的苯核在工艺条件下十分稳定,但是连接在苯核上的烷基侧链则很容易断裂生成小分子烯烃,而且断裂的主要位置就是侧链和苯核连接的键上。
可见,催化裂化副产的C8、C9芳烃主要来自多侧链和长侧链烷基苯的脱烷基反应.同时环烷烃的脱氢反应和烯烃的芳构化反应也会贡献出一些BTX。
催化重整是一个以汽油(主要是直馏汽油)为原料生产高辛烷值汽油及轻芳烃(苯、甲苯、二甲苯)的重要炼油过工程,同时也产生相当数量的副产氢气。
美国UOP公司于1949年开发了活性高稳定性好的铂催化剂,提高了烷烃转化率同时加长了开车周期,从而使催化重整工艺有了极大的发展。
到上世纪80年代初期,该法提供的BTX占世界芳烃总量的65%。
(2)芳烃转化上文中已经提到过,BTX中甲苯及C9芳烃在工业中的需求量与苯和二甲苯相比很少,附加值较低,如将其转换为高附加值的二甲苯,则可实现极大的经济效益。
工艺技术方案论证报告
[工艺名称]技术方案论证报告撰写人(签名):完成日期:文档验交(签名):验交日期:评审负责人(签名):评审日期:目录1.引言 (1)1.1编写目的 (1)1.2背景 (1)1.3定义 (1)1.4参考资料 (1)2.技术方案的前提 (1)2.1要求 (1)2.2目标 (1)2.3假定和限制 (2)2.4进行工艺技术方案论证的方法 (2)2.5评价准则 (2)3.工艺技术方案论证准备 (2)3.1产品工艺结构分析与尺寸解算 (2)3.1.1产品工艺结构分析 (2)3.1.2产品工艺结构尺寸解算 (2)3.2生产线经济技术指标分析解算 (2)3.3产品加工工艺逻辑分析与流程图设计 (2)3.4产品工艺控制参数解算 (2)3.5产品质量参数映射分析 (2)4.建议的工艺技术方案 (2)4.1建议的工艺技术方案概述 (2)4.2工艺技术方案说明 (3)4.2.1工艺装备结构工作原理分析说明 (3)4.2.2工艺装备动力源及传动分析说明 (3)4.2.3工艺装备控制方案分析说明 (3)4.3目标满足度 (3)4.4影响 (3)4.5局限性 (3)4.6工艺技术方案的可行性分析 (3)4.6.1工艺技术方案总体分析 (3)4.6.2工艺技术方案中采用的成熟技术 (3)4.6.3工艺技术方案中采用的新技术 (3)4.6.4工艺技术方案中需要进行预研的子项 (3)5.可选择的其它工艺技术方案 (3)5.1可选择的工艺技术方案1 (3)5.2可选择的工艺技术方案2 (4)6.工艺技术方案评价 (4)7.已选工艺技术方案的技术风险分析 (4)7.1技术风险识别 (4)7.2技术风险估计 (4)7.3技术风险评价 (4)7.4技术风险管理与监控 (4)7.5预研子项的研究结果分析 (4)8.结论 (4)1.引言1.1编写目的在对PEC卷产品制造需求研究的基础上,对其加工技术关键及难点进行预研,提出产品工艺技术方案。
针对所选定的工艺技术方案和预研结果,分别对PEC卷生产线的总体、所采用的关键技术与预研结果进行分析,以论证所选工艺技术方案的可行性和正确性。
金隆公司20万吨电解工艺方案论证与选择
电 流密度 高 , 其槽 电压 一般高 于常 规 电解 法 , 有效 电
流效 率也 低 于 常规 电解 法 。 因此 , R P C技术 的 电能
铜 电解 精 炼 的方 法 主要 包 括 传 统法 电解 、 永久 不锈 钢 阴极 法 和周期 反 向电流 电解 。传 统法 电解 又
电解在 保加 利亚 铜精 炼厂 首次应 用 于工业 规模 的生
产 。从那 以后 , 用这 一技术 的工 厂不 断增 加 , 应 达到
1 大极 板 常规 电解 与 永 久 不锈 钢 阴极
电解 综 合 比 较
1 1 铜 电 解 方 法 及 其 发 展 前 景 .
Байду номын сангаас
了所 有 电解 厂数 的 1 %。 由于 P C技术 所 采 用 的 6 R
De o s r t nd S l c o 0 / p e e t o y i o e s o m n t a e a e e tf r 2 0 kt a Co p r El c r l ss Pr c s f
Jn o g C p e i ln o p r
行 技 术 、 济 、 绩 等 综 合 比较 , 终 选 择 了 KI D 电解 工 艺 。 经 业 最 D
关 键 词 : 电 解 ; 久 不 锈 钢 阴极 电解 ;S 铜 永 I A电 解 ; D 电解 KI D 中 图分 类 号 - F 1 T 81 文 献 标 识码 : A 文 章 编 号 :0 7 5 52 0 } 1 0 2 4 1 0 —7 4 { 0 7 0 —0 0 —0
- 1、下载文档前请自行甄别文档内容的完整性,平台不提供额外的编辑、内容补充、找答案等附加服务。
- 2、"仅部分预览"的文档,不可在线预览部分如存在完整性等问题,可反馈申请退款(可完整预览的文档不适用该条件!)。
- 3、如文档侵犯您的权益,请联系客服反馈,我们会尽快为您处理(人工客服工作时间:9:00-18:30)。
工艺方案的选择及论证3.1对二甲苯生产工艺选择及比较3.1.1对二甲苯的生产工艺1、由石油制取原油根据馏程不同被切割成不同组分,其中可用于制取甲苯和对二甲苯的馏分被称为“直馏轻质石脑油”,包括从戊烷到终沸点在 105℃~170℃之间的所有馏分,这些馏分就是传统工艺中用于生产石油轻芳烃的原料。
用轻质石脑油生产对二甲苯的一般流程是:首先生产石油芳烃 BTX(苯、甲苯、二甲苯)馏分,然后经过芳烃转化将苯、甲苯等其它芳烃转换为二甲苯,然后再从混合二甲苯中分离出对二甲苯。
(1)BTX 的制取以石脑油为原料制取粗 BTX 的方法主要有两种:催化裂化和催化重整。
得到的粗 BTX 是芳烃非芳烃的混合物,再通过萃取精馏、共沸精馏、选择性变压吸附、结品分离和络合物分离等方法便可以得到纯芳烃。
催化裂化是最重要的重质油轻质化过程之一,其主要原料是重质馏分油,主要是直馏减压馏分油(VGO),也包括焦化重馏分油(CGO,通常需加氢精制),经过反再系统、分馏系统、吸收稳定系统得到干气、汽油、柴油、重质油及焦炭,副产物为芳烃。
通常情况下,每生产 1t 乙烯可产出约 1t 裂解汽油,其中苯质量分数约为29.1%,BTX 总质量分数可高达 58.8%。
在催化裂化工艺中,芳香烃的苯核在工艺条件下十分稳定,但是连接在苯核上的烷基侧链则很容易断裂生成小分子烯烃,而且断裂的主要位置就是侧链和苯核连接的键上。
可见,催化裂化副产的 C8、C9 芳烃主要来自多侧链和长侧链烷基苯的脱烷基反应.同时环烷烃的脱氢反应和烯烃的芳构化反应也会贡献出一些 BTX。
催化重整是一个以汽油(主要是直馏汽油)为原料生产高辛烷值汽油及轻芳烃(苯、甲苯、二甲苯)的重要炼油过工程,同时也产生相当数量的副产氢气。
美国 UOP 公司于 1949 年开发了活性高稳定性好的铂催化剂,提高了烷烃转化率同时加长了开车周期,从而使催化重整工艺有了极大的发展。
到上世纪 80 年代初期,该法提供的 BTX 占世界芳烃总量的 65%。
(2)芳烃转化上文中已经提到过,BTX 中甲苯及 C9 芳烃在工业中的需求量与苯和二甲苯相比很少,附加值较低,如将其转换为高附加值的二甲苯,则可实现极大的经济效益。
相关工艺一般有甲苯歧化和烷基转移、二甲苯异构化以及甲苯.甲醇烷基化等。
2、苯歧化与烷基转移甲苯歧化与烷基转移工艺是一种促使芳烃之间相互转变的技术,通过该技术可以将产量相对过剩而附加值又相对降低的甲苯和 C9 芳烃转化为具有高附加值的苯和甲苯。
其中甲苯歧化反应指的是两分子甲苯在催化剂上发生反应生成一分子苯和一分子二甲苯,烷基转移反应指的是甲苯与多烷基芳烃在催化剂上发生反应,使多烷基芳烃上的烷基转移到甲苯上来,得到二甲苯,如一分子甲苯与三甲苯反应生成两分子的二甲苯。
甲苯歧化及烷基转移工艺理论上并不消耗氢,设备和公用 T 程消耗也比较低,因此一直是生产对二甲苯的主要方法。
目前常用的甲苯歧化及烷基转移方法的典型工艺有:美国环球油品(UOP)和日本东丽公司联合开发的“Tatoray”工艺、ExxonMobil 公司开发的“MTDP.3”T 艺、Arco 公司开发的“Xylene—Plus”工艺、UOP 公司开发的“Px—Plus”工艺、Mobile Oil 公司开发的 MTDP 工艺和 Mobile 公司开发MSTDP 工艺等。
其中,“Xylene.Plus”工艺采用 Y.型分子筛 D.8 硅铝小球作为催化剂,使用移动床反应器,其他均采用氢型丝光沸石或者 ZSM-5 沸石催化剂和固定床反应器。
②二甲苯异构化由于受到平衡热力学限制,通过甲苯歧化等工艺得到的 C8 芳烃中,对二甲苯含量仅占芳烃混合物总量的 23%左右,其余大部分芳烃为与二甲苯沸程相近的乙苯。
为最大限度增产对二甲苯,需要使 C8 混合物在催化剂上发生异构化反应,使乙苯转化成二甲苯甚至对二甲苯。
具体反应如下:CH3 常用的异构化工艺有:UOP 公司的 Isomer 工艺、东丽公司的 lsolene 工艺、Engelhard 公司的 Octafining 工艺等。
国内各炼油石化企业、科研院校也陆续开发出了自己的异构化催化剂,比如中石化股份公司天津分公司采用 SKI.400 沸石铂金属催化剂得到了很好的生产效益,并在国内得到广泛使用;梁战桥等调整 ZSM-5 催化剂与丝光沸石催化剂的配比后开发出了乙苯转化型二甲苯异构化催化剂,其性能可与 IFP 公司的 EU—I 媲美;桂鹏[也在着手开发高空速乙苯转化型催化剂。
这些催化剂的共同点都是,在尽可能减小对二甲苯损失的同时,通过使乙苯发生异构化甚至脱烷基化和歧化反应,提高乙苯转化率,降低乙苯含量,提升二甲苯收率。
3、煤化工制取煤焦化反应可得到副产物——粗芳烃,同样可作为生产甲苯和二甲苯的工艺原料,上世纪 40 年代之前,煤化工一直是芳烃的唯一来源。
但是这种方法有着明显的局限性,即低收率,每吨煤只能得到 0.26 吨芳烃。
随着近些年煤化工业的发展,煤液化成为了制取芳烃尤其是甲苯、二甲苯的新方法。
煤和石油都具有芳香性,不同之处在于,煤中含有多个不同苯环数的缩合芳烃,这些芳烃通过不同的桥键连接,最终形成了煤。
加氢液化工艺可以将这些桥键打开,使煤解离为多个芳烃结构,从而得到芳烃混合物,再通过上述的工艺转化便可得到对二甲苯。
(1)甲苯甲醇烷基化如上所述,目前工业上生产对二甲苯的工艺主要是甲苯歧化与烷基转移方法,近年来,随着相关催化剂的深入研究,甲苯择型歧化工艺也越来越受到重视。
但是这些工艺的副产物较多,需要多个分离设备进行分离来得到对二甲苯产品,造成高设备费用和能量浪费;同时,歧化反应在一分子甲苯生成对二甲苯的同时会有一分子甲苯转化为附加值较低的苯,导致甲苯的浪费。
于是近年来,研究人员开发出了一种新的对二甲苯制备工艺——甲苯甲醇烷基化技术,该技术是在高温低压条件下,使一分子甲苯和一分子甲醇发生反应,择型生成二甲苯和水,大大提高了甲苯利用率,而另一个反应物甲醇是煤化工的中间产物,受国内快速增长的产能和廉价进口甲醇的竞争影响,很长一段时间内甲醇将处于低价位,从而降低甲苯甲醇烷基化工艺的原料成本,同时甲醇作为典型的 C1 化合物,其利用空间有限,甲苯甲醇烷基化工艺填补了 C1 化合物利用领域的又一空白。
由上述反应机理可知,在烷基化过程中会生成不同的二甲苯产品,而为了达到增产目标、实现经济效益,就需要在反应过程中尽可能多的得到对二甲苯产品,促进临、间二甲苯转化成对二甲苯或者组织甲苯甲醇反应生成临、问二甲苯的反应。
为了达到这一目的,研究者们进行了长期不懈的努力,并且取得了丰硕的成果。
上世纪 70 年代,Yashima 等人首先注意到在 Y 沸石催化剂上发生甲苯与甲醇的烷基化反应,可得到 45%~50%含量的对位异构体,打破了热力学平衡值,呈现出一定对位选择性。
美国 Mobil 公司最早发明了MFI 结构的 ZSM-5 分子筛催化剂,从而较早地开展了以之为催化剂材料的甲苯甲醇烷基化反应研究,从那之后 ZSM-5 分子筛催化剂一直是甲苯甲醇烷基化反应的研究中的热点。
GTC 技术公司,以高硅分子筛为催化剂,开发了GT.TolAlk 工艺。
反应在固定床反应器中进行反应,反应温度为 400~450℃,反应压力为 O.1~0.5MPa 对二甲苯选择性大于 85%。
综上所述,原料甲醇的低廉价位和反应中甲苯的高利用率都使甲苯甲醇烷基化反应具有极好的经济性,同时对甲醇的利用还可以缓解国内甲醇的产能过剩,促进煤化二产业的发展。
鉴于其客观的经济和社会效益,甲苯甲醇烷基化工艺作为新兴的芳烃转化技术必将受到广泛的关注。
3.1.2生产工艺的比较与选择经过我们小组讨论,结合本次设计所用的原料,本项目采用大连理工大学工业催化剂研究所研制成功选择合成对二甲苯催化剂即采用纳米 ZSM-5 分子筛为基质,通过组合改性调节催化剂的孔结构和酸性能,研制成功高选择性、高活性、高稳定性合成对二甲苯新技术。
反应原料甲苯与甲醇,在临氢临水、常压条件下,于 400~500℃反应,选择合成对二甲苯(选择性大于 98%),催化剂连续运转 1000 小时活性不下降。
上述催化剂使用工业品纳米 ZSM-5 分子筛为母体,用工业生产技术制备,具备大生产条件。
甲苯用甲醇烷基化生产二甲苯,一直是许多公司投入大量精力研究的课题,这些公司包括阿莫科(现为 BP)、杜邦、联碳(现为陶氏)、埃克森美孚、联合油和 UOP。
近来 GTC 技术公司开始出售由印度石化公司(1PCL)开发的甲苯甲基化工艺(GT-TolAkl)。
GTC 称,用专有高硅分子筛催化剂,对二甲苯选择性可达 85%以上。
反应是在氢和水存在的条件下,在固定床反应器中进行的。
对二甲苯的回收一般在结晶系统中进行。
GT-TolAkl 系统的操作条件如下:温度400-450℃,压力 100-500kPa,重时空速 1-2 时-1,对二甲苯选择性 80%-90%(质量)。
与 STDP 装置比较,甲苯甲基化路线的优点是:①每吨对二甲苯所需的甲苯数量可由约 2.8 吨降到 1.0 吨;②甲醇容易得到,比较便宜(如 2001 年l 季度为 79 美分/加仑,是 5 年中的最高价);③苯的产生可以忽略(每磅对二甲苯产生 0.006 加仑苯)。
根据甲苯甲基化工艺的概念设计,补充的甲苯和甲醇被蒸发,并与循环甲苯、氢结合,用反应器流出物预热,用加热炉进一步加热到 400~C。
将这种进料送入甲基化反应器,生成二甲苯和各种副产物(如苯、乙苯、一氧化碳、二氧化碳和氢)。
由于放热,反应温度升至 450℃。
反应器流出物通过与反应器进料的换热冷却,然后再通过一台部分冷凝器,在这里一些有机产品,如苯、乙苯、甲苯和二甲苯被冷凝。
剩余的气相产物(一氧化碳、二氧化碳和氢)在一台分离罐中与有机液体分离,部分气体循环,提供反应所需要的氢,其余的气体被排放,用作副产物燃料。
液体产物被送到苯塔,苯在塔顶作为副产物回收。
苯塔塔底产品再送至甲苯回收塔。
由于反应器中甲苯单程转化率低,反应器流出物的液体中含有较多甲苯,因而较大的甲苯回收塔和较多的蒸汽消耗是必要的。
两段甲苯蒸馏模式中,其中第一段的操作压力高于第二段,与一段操作模式相比,两段模式蒸汽耗量可明显减少。
通过定制蒸馏的段数有可能进一步减少蒸汽消耗。
高压甲苯蒸馏塔塔顶产品可用作低压塔再沸器的能源。
通过在低压塔再沸器的冷凝,甲苯与低压塔塔顶产品结合,循环回甲基化反应器。
低压塔塔底产品含有混合二甲苯和乙苯,被送到结晶装置。
含混合二甲苯的物流中,80%-90%是对二甲苯,此外包含小量的乙苯。
在结晶工艺中,混合二甲苯被冷却,然后进入第一段结晶,包括一段或两段串联的结晶器,主要取决于进料组成。
一段结晶的浆液流入连续离心部分,80%-90%的对二甲苯结晶与滤液分开。