石墨电极的生产工艺流程和质量指标的及消耗原理知识讲解
石墨电极的原料及制造工艺

欢迎阅读一、石墨电极的原料1、石墨电极是采用石油焦、针状焦为骨料,煤沥青为粘结剂,经过混捏、成型、焙烧、浸渍、石墨化、机械加工等一系列工艺过程生产出来的一种耐高温石墨质导电材料。
石墨电极是电炉炼钢的重要高温导电材料,通过石墨电极向电炉输入电能,利用电极端部和炉料之间引发电弧产生的高温作为热源,使炉料熔化进行炼钢。
其他一些冶炼黄磷、工业硅、磨料等材料的矿热炉也用石墨电极作为导电材料。
利用石墨电极优良而特殊的物理化学性能,在其他工业部门也有广泛的用途。
2、石墨电极的原料(1灰分、和低硫焦((2焦块性热(3大。
粘结剂沥青一般使用软化点适中、结焦值高、β树脂高的中温或中温改质沥青,浸渍剂要使用软化点较低、 QI低、流变性能好的中温沥青。
二、石墨电极的制造工艺1、煅烧炭质原料在高温下进行热处理,排出所含的水分和挥发份,并相应提高原料理化性能的生产工序称为煅烧。
一般炭质原料采用燃气及自身挥发份作为热源进行煅烧,最高温度为1250- 1350℃。
(1)煅烧使炭质原料的组织结构和物理化学性能发生深刻变化,主要体现在提高了焦炭的密度、机械强度和导电性,提高了焦炭的化学稳定性和抗氧化性能,为后序工序奠定了基础。
(2)煅烧的设备主要有罐式煅烧炉、回转窑和电煅烧炉。
煅烧质量控制指标是石油焦真密度不小于2.07g/cm3,电阻率不大于550μΩ.m,针状焦真密度不小于2.12g/cm3,电阻率不大于500μΩ.m。
(3)原料的破碎处理和配料①在配料之前,须对大块煅后石油焦和针状焦进行中碎、磨粉、筛分处理。
中碎通常是将50mm左右的物料通过颚式破碎机、锤式破碎机、对辊破碎机等破碎设备进一步破碎到配料所需的0.5-20mm的粒度料。
②磨粉是通过悬棍式环辊磨粉机(雷蒙磨)、球磨机等设备将炭质原料磨细到0.15mm或0.075mm 粒径以下的粉末状小颗粒的过程。
③筛分是通过具有均匀开孔的一系列筛子,将破碎后尺寸范围较宽的物料分成尺寸范围较窄的几种颗粒粒级的过程,现行电极生产通常需要4-5个颗粒料粒级和1-2个粉料粒级。
石墨电极加工操作知识点总结

石墨电极加工操作知识点总结石墨电极加工操作知识点总结石墨电极是一种重要的材料,在电化学领域和工业生产中具有广泛的应用。
石墨电极加工是对石墨电极材料进行切割、磨削、加工等工序,以便制造出符合要求的石墨电极产品。
为了确保石墨电极加工的质量和效率,操作人员需要具备一定的知识和技能。
本文将从石墨电极加工的常见工艺、操作注意事项和加工机器的选择等方面进行总结。
一、石墨电极加工的常见工艺1. 切割工艺石墨电极材料通常需要根据设计要求进行切割,常见的切割方法有机械切割和电火花切割。
机械切割适用于较厚的石墨电极板材,而电火花切割则适用于较薄的石墨电极材料。
2. 磨削工艺石墨电极磨削是指对石墨电极材料进行表面磨光处理,以提高其表面质量和精度。
常见的磨削方法有手动研磨和机械磨削。
手动研磨适用于小型石墨电极或局部修复,而机械磨削适用于批量生产和大规格的石墨电极。
3. 孔加工工艺石墨电极通常需要进行孔加工,以便用于导电或液体流通。
常见的孔加工方法有钻孔、铣削孔和电火花加工孔。
钻孔适用于直径较大的孔洞,铣削孔适用于孔洞精度要求较高的情况,而电火花加工孔适用于特殊形状的孔洞。
二、石墨电极加工的操作注意事项1. 石墨电极材料的保护石墨电极材料具有一定的脆性,在加工过程中需要注意避免碰撞和摩擦,以免石墨电极表面产生裂纹或损坏。
同时,在存放和运输时要注意避免潮湿和受到化学物质的侵蚀。
2. 刀具的选择和切削参数的确定在进行切削和磨削加工时,需要根据石墨电极的材料特性和加工要求选择合适的刀具和切削参数。
刀具的选择要考虑材料的硬度和切削性能,切削参数的确定要考虑切削速度、进给速度和切削深度等因素。
3. 清洗和除尘在石墨电极加工过程中,会产生大量的切削屑和粉尘,需要及时清洗和除尘,以保持加工环境的清洁和工件的表面质量。
清洗和除尘可以使用机械设备,也可以采用手工操作。
三、石墨电极加工机器的选择1. 切割机器石墨电极切割机器主要有手动切割机、自动切割机和激光切割机等。
石墨电极生产工艺流程

石墨电极生产工艺流程石墨电极是一种用于炼钢和铝的关键材料,它具有耐高温、导电性好、化学稳定性强等优点。
以下是石墨电极生产的工艺流程。
首先,选择合适的原料。
石墨电极的主要成分是高纯度的天然石墨。
选取质量好、纯度高、粒度适中的原料,确保最终产品的质量。
接下来,对原料进行破碎和磨石处理。
通过破碎设备将原料破碎成合适的大小,并利用磨石机将原料磨成粉末状。
然后,将石墨粉与绑结剂混合。
绑结剂可以增强石墨电极的机械强度和抗氧化性能。
绑结剂的种类、添加量等要根据具体工艺要求进行调整。
混合后的石墨料放入模具中进行成型。
成型方式主要有挤压成型和压力成型两种。
挤压成型是将石墨料放入定量供料系统,通过挤出机构将料坯挤压成形。
压力成型则是将石墨料放入模具中,通过压力机具体压制成形。
成形后的石墨料需要进一步烘干。
在烘干设备中,以适当的温度和时间将水分和有机溶剂等挥发掉,使石墨料达到一定的固结度。
烘干后,石墨料进一步进行煅烧处理。
煅烧的目的是去除石墨料中的杂质,增加石墨的结晶度,并提高电导率和机械强度。
煅烧温度和时间要根据具体要求进行控制。
煅烧后,石墨电极进一步进行机械加工。
通过车床、铣床、磨床等设备对电极进行加工,使其达到规定的尺寸和形状。
最后,对石墨电极进行表面处理。
通过化学方法对电极表面进行蚀刻处理,去除表面氧化物和其他杂质,使电极表面光滑,提高使用寿命。
以上就是石墨电极生产的工艺流程。
通过合理的原料选择、破碎处理、混合绑定剂、成型、烘干、煅烧、机械加工和表面处理等步骤,最终制成具有优良性能的石墨电极,为炼钢和铝行业提供重要的工艺材料。
石墨电极生产工艺要点

石墨电极生产工艺要点石墨电极是一种用于电化学反应的重要材料,在铝电解、电石制氯碱、合成碳酸锂等工业中广泛应用。
石墨电极的生产工艺对其质量和性能具有重要影响。
下面将详细介绍石墨电极生产工艺的要点。
1.原料选择:石墨电极的主要原料是石墨粉末和绑定剂。
石墨粉末应具有良好的导电性和高温稳定性,可以选择天然石墨或人工石墨。
绑定剂可以选择环氧树脂、酚醛树脂、煤沥青等,要保证其在高温下的稳定性和粘结强度。
2.石墨粉末处理:石墨粉末需经过混合、筛分、湿混合等工艺步骤进行处理。
混合是将不同粒度和性质的石墨粉末进行均匀混合,以提高原料的均匀性。
筛分是通过筛网将粉末按粒度进行分级,以保证所得到的混合料中无大颗粒和杂质。
湿混合是将石墨粉末和绑定剂进行混合,可以提高绑定剂的粘结性能。
3.石墨浆料制备:将经过处理的石墨粉末与绑定剂按一定比例混合,并在搅拌仪器中搅拌,以制备石墨浆料。
搅拌时间和速度要控制合适,以保证石墨粉末和绑定剂充分混合,并形成均匀的浆料。
浆料的粘度、流动性和粒度分布等性能对最终成品的质量有重要影响。
4.电极模具制备:将石墨浆料注入到电极模具中,通过振动和压实工艺使其充填模具中的空隙。
模具可以采用金属模具或塑料模具,要保证模具表面光滑,以获得成型良好的电极。
5.焙烧和石墨化:将注浆完成的电极进行烘干,通常使用温度慢升、静态烘干的工艺。
烘干过程中要避免快速升温和过高温度,以避免电极产生瞬间升温造成裂纹和变形。
烘干后将电极置于高温炉中进行焙烧,以去除绑定剂和其他有机杂质,使石墨达到高纯度和高密度。
6.加工和修整:石墨电极经过焙烧后通常需要进行加工和修整,以获得符合要求的精度和表面质量。
加工包括车、铣、磨等工艺,要保证电极的形状和尺寸精度。
修整是通过表面处理、清洗和打磨等方法,去除表面的缺陷和污染物,提高电极的表面光洁度和精度。
7.石墨电极检验和包装:通过对石墨电极的外观质量、尺寸精度、导电性能等进行检验,确保产品符合要求。
石墨电极工艺流程
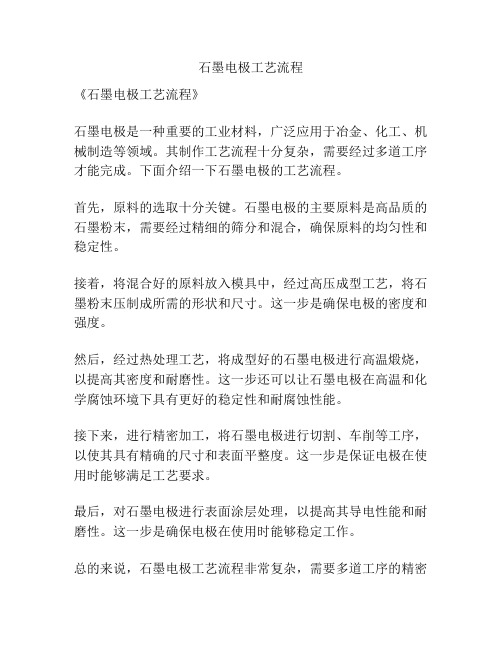
石墨电极工艺流程
《石墨电极工艺流程》
石墨电极是一种重要的工业材料,广泛应用于冶金、化工、机械制造等领域。
其制作工艺流程十分复杂,需要经过多道工序才能完成。
下面介绍一下石墨电极的工艺流程。
首先,原料的选取十分关键。
石墨电极的主要原料是高品质的石墨粉末,需要经过精细的筛分和混合,确保原料的均匀性和稳定性。
接着,将混合好的原料放入模具中,经过高压成型工艺,将石墨粉末压制成所需的形状和尺寸。
这一步是确保电极的密度和强度。
然后,经过热处理工艺,将成型好的石墨电极进行高温煅烧,以提高其密度和耐磨性。
这一步还可以让石墨电极在高温和化学腐蚀环境下具有更好的稳定性和耐腐蚀性能。
接下来,进行精密加工,将石墨电极进行切割、车削等工序,以使其具有精确的尺寸和表面平整度。
这一步是保证电极在使用时能够满足工艺要求。
最后,对石墨电极进行表面涂层处理,以提高其导电性能和耐磨性。
这一步是确保电极在使用时能够稳定工作。
总的来说,石墨电极工艺流程非常复杂,需要多道工序的精密
加工和处理才能完成。
只有严格按照工艺流程进行制作,才能保证石墨电极具有良好的性能和稳定性。
石墨电极制备

石墨电极制备石墨电极是一种重要的非金属导电材料。
它的材料性质特殊,通常用于电化学领域中,如进行电化学反应、电化学分析、电溶解或电硬化等。
同时,石墨电极在储能及新能源领域中也扮演了重要角色。
本文将深入探讨石墨电极的制备方法及其工艺流程。
石墨电极的制备方法分为物理法和化学法。
物理法主要有机械加工法和高温石墨化法,而化学法主要有喷涂石墨化法、碳化镁还原法等。
一、物理法的制备方法(一)机械加工法机械加工法是一种通过机械切削、磨削等加工方法来制得石墨电极的方法。
此方法不需要昂贵的设备,而且制备效果较好。
首先用准确的尺寸将石墨棒测量后,再用金属切削工具或磨料切削钻头进行车削或平展,直至制得所需尺寸和形状的电极。
(二)高温石墨化法高温石墨化法是一种将特制的硫酸树脂石墨球放置于加热炉中高温石墨化的方法。
制备时,将石墨球置于加热炉中,高温石墨化过程中石墨球表面出现石墨化现象,逐渐形成电极。
此方法适用于制备大体积的石墨电极,但制备过程较为耗时。
二、化学法的制备方法(一)喷涂石墨化法喷涂石墨化法是一种在基板表面涂覆石墨之后高温石墨化的方法。
首先,将石墨粉末与松香、金属铬粉混合后,喷射在金属或陶瓷基板表面,并在高温条件下石墨化成石墨层。
这种方法可制备出复杂的石墨电极形状和构成。
(二)碳化镁还原法碳化镁还原法是一种将石墨粉末和镁粉混合后,置于高温反应中还原制成石墨电极的方法。
首先将石墨粉末和镁粉混合后,置于高温炉中反应,反应时镁粉发挥还原作用,并将石墨粉末石墨化。
这种方法对石墨电极的制备质量要求较高,制备时间较长。
在制备石墨电极过程中,关键参数如温度、时间、压力等都非常重要。
常见的石墨电极制备工艺流程如下:第一步:材料准备。
根据不同的制备方法,在制备过程中所使用的原料有所差异。
第二步:进行混合。
机械加工法之类的制备方法不需要进行混合,但化学法制备方法则需要在混合上进行一些操作。
第三步:成型。
一般通过压片或者铸造等方式将待制备的电极形状做成。
石墨电极的原料及制造工艺
欢迎阅读一、石墨电极的原料1、石墨电极是采用石油焦、针状焦为骨料,煤沥青为粘结剂,经过混捏、成型、焙烧、浸渍、石墨化、机械加工等一系列工艺过程生产出来的一种耐高温石墨质导电材料。
石墨电极是电炉炼钢的重要高温导电材料,通过石墨电极向电炉输入电能,利用电极端部和炉料之间引发电弧产生的高温作为热源,使炉料熔化进行炼钢。
其他一些冶炼黄磷、工业硅、磨料等材料的矿热炉也用石墨电极作为导电材料。
利用石墨电极优良而特殊的物理化学性能,在其他工业部门也有广泛的用途。
2、石墨电极的原料(1灰分、和低硫焦((2焦块性热(3大。
粘结剂沥青一般使用软化点适中、结焦值高、β树脂高的中温或中温改质沥青,浸渍剂要使用软化点较低、 QI低、流变性能好的中温沥青。
二、石墨电极的制造工艺1、煅烧炭质原料在高温下进行热处理,排出所含的水分和挥发份,并相应提高原料理化性能的生产工序称为煅烧。
一般炭质原料采用燃气及自身挥发份作为热源进行煅烧,最高温度为1250- 1350℃。
(1)煅烧使炭质原料的组织结构和物理化学性能发生深刻变化,主要体现在提高了焦炭的密度、机械强度和导电性,提高了焦炭的化学稳定性和抗氧化性能,为后序工序奠定了基础。
(2)煅烧的设备主要有罐式煅烧炉、回转窑和电煅烧炉。
煅烧质量控制指标是石油焦真密度不小于2.07g/cm3,电阻率不大于550μΩ.m,针状焦真密度不小于2.12g/cm3,电阻率不大于500μΩ.m。
(3)原料的破碎处理和配料①在配料之前,须对大块煅后石油焦和针状焦进行中碎、磨粉、筛分处理。
中碎通常是将50mm左右的物料通过颚式破碎机、锤式破碎机、对辊破碎机等破碎设备进一步破碎到配料所需的0.5-20mm的粒度料。
②磨粉是通过悬棍式环辊磨粉机(雷蒙磨)、球磨机等设备将炭质原料磨细到0.15mm或0.075mm 粒径以下的粉末状小颗粒的过程。
③筛分是通过具有均匀开孔的一系列筛子,将破碎后尺寸范围较宽的物料分成尺寸范围较窄的几种颗粒粒级的过程,现行电极生产通常需要4-5个颗粒料粒级和1-2个粉料粒级。
石墨电极生产工艺流程
石墨电极生产工艺流程
石墨电极是一种重要的电炉材料,广泛应用于冶金、化工、电
力等行业。
其生产工艺流程包括原料选择、石墨化处理、成型、煅烧、加工和检测等环节。
下面将详细介绍石墨电极的生产工艺流程。
首先,原料选择是石墨电极生产的关键环节。
石墨电极的主要
原料是石墨粉和焦粉,其中石墨粉要求颗粒度细、结晶度高、灰分低,而焦粉要求硫、磷含量低,粒度均匀。
这些原料的选择直接影
响了石墨电极的质量和性能。
其次,经过原料的混合和石墨化处理,将原料混合后进行石墨
化处理,使其形成均匀的石墨浆料。
然后将石墨浆料进行成型,通
常采用振实成型或压模成型工艺,使其成型成型坯。
随后,成型坯经过煅烧工艺,将成型坯进行高温煅烧,使其结
晶度和密实度得到提高,从而提高石墨电极的导电性能和耐磨性能。
接下来是加工环节,经过煅烧后的石墨电极坯料需要进行加工,包括车削、铣削、线切割等工艺,最终形成符合要求的石墨电极产品。
最后是检测环节,经过加工的石墨电极产品需要进行严格的检测,包括外观检测、尺寸检测、性能检测等,确保产品符合标准要求。
总的来说,石墨电极的生产工艺流程包括原料选择、石墨化处理、成型、煅烧、加工和检测等环节,每个环节都需要严格控制,以确保最终产品的质量和性能。
希望本文对石墨电极生产工艺流程有所帮助。
石墨电极生产工艺流程
石墨电极生产工艺流程
石墨电极是用作锂离子电池、燃料电池、太阳能电池等高科技领域的重要材料之一。
下面将介绍石墨电极的生产工艺流程。
首先,石墨电极的生产原料主要是天然石墨。
天然石墨是一种矿石,需要经过矿石的采选、破碎、研磨等工艺,以得到石墨粉末。
接下来,石墨粉末需进行精细加工处理。
首先是对石墨粉末进行筛分,以去除粗糙的不合格颗粒。
然后是对石墨粉末进行混合和干燥,以保证石墨粉末的均匀性和稳定性。
然后,将石墨粉末与适量的粘合剂进行混合,形成石墨浆料。
石墨浆料需要通过搅拌和混合设备进行混合,直到形成均匀的浆料。
接下来,将石墨浆料倒入模具中,进行成型。
模具可以根据所需的电极形状而定,通常为长方形或矩形。
成型后的电极需要经过压实和挤压的工艺,以提高电极的密度和强度。
然后,成型的石墨电极需要进行烧结处理。
烧结是将电极放置在高温环境下进行加热,以去除残留的粘合剂和水分,并将石墨颗粒之间形成更紧密的结合。
烧结温度和时间需要根据不同的石墨电极要求进行调整。
最后,经过烧结处理的石墨电极需要经过一系列的加工工艺,包括机械加工、表面处理等,以获得最终的产品。
机械加工包
括磨削、切割和打磨等,以使电极表面光滑并符合要求的尺寸。
表面处理可以采用涂层技术,以提高电极的电化学性能和循环寿命。
以上就是石墨电极的生产工艺流程。
通过以上的工艺流程,可以获得高质量的石墨电极,以满足不同领域的需求。
石墨电极的生产工艺无论在原料处理、成型、烧结还是加工等方面,都需要严格控制各个环节,以保证电极的质量和性能。
石墨电极
石墨电极石墨是冶金工业中的一种重要材料,除前面所讲的用于坩埚、耐火材料等以外,还在炼钢电炉,电弧炉中作电极。
1955年开始使用人造石墨电极,近几年开始使用天然石墨电极,而且发展很快。
一、石墨电极1.石墨电极的制造工艺人造石墨电极的原料主要是石油焦和沥青焦。
它们是由石油沥青和煤沥青经焦化处理得到的,是一种低灰份、低硫份,易于石墨化的理想炭素材料。
生产人造石墨电极的工艺流程图原料经破碎加工,达到适宜的粒度后,送入1000~1300℃煅烧炉中进行热处理,以除去原料中的水份和挥发份,以提高其密度、机械强度、导热和导电性能。
石墨化工序是人造石墨电极关键的一环,它是在常压和2000℃以上的温度下,使石油焦和沥青焦的碳原子由二维空间的乱层结构,转化为三维有序排列的石墨晶粒。
石墨化的好坏对产品质量影响很大。
结晶化程度与电极的导电性能有关,石墨化工序采用大型石墨化炉进行,耗电量极高,每吨电极耗电约5000~6000kwh。
天然石墨电极生产工艺天然石墨电极的原料由高碳鳞片状石墨,中温煤沥青经破碎混合组成。
根据电极产品的规格不同,各种原料的颗粒级配有所不同。
生产时原料先进行干混。
干料混均后进行适当的加热。
再加入一定数量的沥青进行湿混,使粘结剂与原料混均,成为可塑性好的糊料。
将糊料送入电极挤压机的料缸中,经预压排除空气,再压制成型。
成型后的生坯送入焙烧炉中焙烧,使粘结剂煤沥青在一定温度下裂解,并产生聚合反应,使碳原子之间形成焦碳网络,把石墨粉紧密连接起来,形成一个具有一定机械强度和理化性能的整体。
焙烧俺一定升温曲线升至1300℃,需要时间为219~240h。
采用冶金焦和石英砂混合作填充及覆盖料。
浸渍后二次焙烧条件基本相同,时间稍短一些。
浸渍过程是将以此焙烧产品送入预热炉中,温度达260~320℃,预热3~5h后入浸渍罐。
浸渍时,液态沥青在一定的真空压力、温度条件下浸入制品的微孔中。
然后用水冷却后出罐。
一个周期要6h。
浸渍后的电极经二次焙烧后再进行加工,出厂。
- 1、下载文档前请自行甄别文档内容的完整性,平台不提供额外的编辑、内容补充、找答案等附加服务。
- 2、"仅部分预览"的文档,不可在线预览部分如存在完整性等问题,可反馈申请退款(可完整预览的文档不适用该条件!)。
- 3、如文档侵犯您的权益,请联系客服反馈,我们会尽快为您处理(人工客服工作时间:9:00-18:30)。
石墨电极的生产工艺流程和质量指标的及消耗原理目录一、石墨电极的原料及制造工艺二、石墨电极的质量指标三、电炉炼钢简介及石墨电极的消耗机理石墨电极的原料及制造工艺●石墨电极是采用石油焦、针状焦为骨料,煤沥青为粘结剂,经过混捏、成型、焙烧、浸渍、石墨化、机械加工等一系列工艺过程生产出来的一种耐高温石墨质导电材料。
石墨电极是电炉炼钢的重要高温导电材料,通过石墨电极向电炉输入电能,利用电极端部和炉料之间引发电弧产生的高温作为热源,使炉料熔化进行炼钢。
其他一些冶炼黄磷、工业硅、磨料等材料的矿热炉也用石墨电极作为导电材料。
利用石墨电极优良而特殊的物理化学性能,在其他工业部门也有广泛的用途。
生产石墨电极的原料有石油焦、针状焦和煤沥青●石油焦是石油渣油、石油沥青经焦化后得到的可燃固体产物。
色黑多孔,主要元素为碳,灰分含量很低,一般在0.5%以下。
石油焦属于易石墨化炭一类,石油焦在化工、冶金等行业中有广泛的用途,是生产人造石墨制品及电解铝用炭素制品的主要原料。
●石油焦按热处理温度区分可分为生焦和煅烧焦两种,前者由延迟焦化所得的石油焦,含有大量的挥发分,机械强度低,煅烧焦是生焦经煅烧而得。
中国多数炼油厂只生产生焦,煅烧作业多在炭素厂内进行。
●石油焦按硫分的高低区分,可分为高硫焦(含硫1.5%以上)、中硫焦(含硫0.5%-1.5%)、和低硫焦(含硫0.5%以下)三种,石墨电极及其它人造石墨制品生产一般使用低硫焦生产。
●针状焦是外观具有明显纤维状纹理、热膨胀系数特别低和很容易石墨化的一种优质焦炭,焦块破裂时能按纹理分裂成细长条状颗粒(长宽比一般在1.75以上),在偏光显微镜下可观察到各向异性的纤维状结构,因而称之为针状焦。
●针状焦物理机械性质的各向异性十分明显, 平行于颗粒长轴方向具有良好的导电导热性能,热膨胀系数较低,在挤压成型时,大部分颗粒的长轴按挤出方向排列。
因此,针状焦是制造高功率或超高功率石墨电极的关键原料,制成的石墨电极电阻率较低,热膨胀系数小,抗热震性能好。
●针状焦分为以石油渣油为原料生产的油系针状焦和以精制煤沥青原料生产的煤系针状焦。
●煤沥青是煤焦油深加工的主要产品之一。
为多种碳氢化合物的混合物,常温下为黑色高粘度半固体或固体,无固定的熔点,受热后软化,继而熔化,密度为1.25-1.35g/cm3。
按其软化点高低分为低温、中温和高温沥青三种。
中温沥青产率为煤焦油的54-56%。
煤沥青的组成极为复杂,与煤焦油的性质及杂原子的含量有关,又受炼焦工艺制度和煤焦油加工条件的影响。
表征煤沥青特性的指标很多,如沥青软化点、甲苯不溶物(TI)、喹啉不溶物(QI)、结焦值和煤沥青流变性等。
●煤沥青在炭素工业中作为粘结剂和浸渍剂使用,其性能对炭素制品生产工艺和产品质量影响极大。
粘结剂沥青一般使用软化点适中、结焦值高、β树脂高的中温或中温改质沥青,浸渍剂要使用软化点较低、QI低、流变性能好的中温沥青。
●●●下图为炭素企业石墨电极生产工艺流程图●●煅烧:炭质原料在高温下进行热处理,排出所含的水分和挥发份,并相应提高原料理化性能的生产工序称为煅烧。
一般炭质原料采用燃气及自身挥发份作为热源进行煅烧,最高温度为1250- 1350℃。
煅烧使炭质原料的组织结构和物理化学性能发生深刻变化,主要体现在提高了焦炭的密度、机械强度和导电性,提高了焦炭的化学稳定性和抗氧化性能,为后序工序奠定了基础。
煅烧的设备主要有罐式煅烧炉、回转窑和电煅烧炉。
煅烧质量控制指标是石油焦真密度不小于2.07g/cm3,电阻率不大于550μΩ.m,针状焦真密度不小于2.12g/cm3,电阻率不大于500μΩ.m。
●原料的破碎处理和配料在配料之前,须对大块煅后石油焦和针状焦进行中碎、磨粉、筛分处理。
中碎通常是将50mm左右的物料通过颚式破碎机、锤式破碎机、对辊破碎机等破碎设备进一步破碎到配料所需的0.5-20mm的粒度料。
磨粉是通过悬棍式环辊磨粉机(雷蒙磨)、球磨机等设备将炭质原料磨细到0.15mm或0.075mm粒径以下的粉末状小颗粒的过程。
筛分是通过具有均匀开孔的一系列筛子,将破碎后尺寸范围较宽的物料分成尺寸范围较窄的几种颗粒粒级的过程,现行电极生产通常需要4-5个颗粒料粒级和1-2个粉料粒级。
配料是按配方要求,对各种粒度的骨料和粉料、粘结剂分别计算、称量和聚焦的生产过程。
配方的科学性适宜性和配料操作的稳定性是影响产品质量指标和使用性能的最重要因素之一。
配方需确定5方面内容:①选择原料的种类;②确定不同种类原料的比例;③确定固体原料粒度组成;④确定粘结剂的用量;⑤确定添加剂的种类和用量。
⏹返回料的回用(生碎、石墨碎、焙烧碎)⏹配方基本原则:球体最紧密堆积原理电极配方中最大颗粒尺寸的确定大颗粒配方●混捏:在一定温度下将定量的各种粒度炭质颗粒料和粉料与定量的粘结剂搅拌混合均匀,捏合成可塑性糊料的工艺过程称为混捏。
混捏的过程:干混(20-35 min)湿混(40-55 min)混捏的作用:①干混时使各种原料混合均匀,同时使不同粒度大小的固体炭质物料均匀地混合和填充,提高混合料的密实度;②加入煤沥青后使干料和沥青混合均匀,液态沥青均匀涂布和浸润颗粒表面,形成一层沥青粘结层,把所有物料互相粘结在一起,进而形成均质的可塑性糊料,有利于成型;③部分煤沥青浸透到炭质物料内部空隙,进一步提高了糊料的密度和粘结性。
●成型:炭材料的成型是指混捏好的炭质糊料在成型设备施加的外部作用力下产生塑性变形,最终形成具有一定形状、尺寸、密度和强度的生坯(或称生制品)的工艺过程。
⏹挤压的操作①凉料:圆盘凉料、圆筒凉料、混捏式凉料等方式排出挥发份、降低至适宜温度(90-120℃)增加粘结力,使糊料块度均匀利于成型20-30 min②装料:压机升挡板----分2-3次下料----4-10MPa压实③预压:压力20-25MPa,时间3-5min,同时抽真空④挤压:压机降挡板----5-15MPa挤压----剪切----翻入冷却水槽⏹挤压的技术参数:压缩比、压机料室及嘴型温度、凉料温度、预压压力时间、挤压压力、挤压速度、冷却水温度⏹生坯的检查:体积密度、外观敲击、剖析⏹焙烧:是炭制品生坯在填充料保护下、装入专门设计的加热炉内进行高温热处理, 使生坯中的煤沥青炭化的工艺过程。
煤沥青炭化后形成的沥青焦将炭质骨料和粉料颗粒固结在一起, 焙烧后的炭制品具有较高的机械强度、较低的电阻率、较好的热稳定性和化学稳定性。
焙烧是炭素制品生产的主要工序之一, 也是石墨电极生产三大热处理过程中的重要一环, 焙烧生产周期较长(一焙22-30天,二焙依炉型5-20天), 而且能耗较高。
生坯焙烧的质量对成品质量和生产成本都有一定影响。
生坯内煤沥青在焙烧过程中焦化,排出10%左右的挥发份,同时体积产生2-3%的收缩,质量损失8-10%。
炭坯的理化性能也发生了显著变化,由于气孔率增加体积密度由1.70g/cm3降为1.60g/cm3,电阻率10000μΩ.m左右降至40-50μΩ.m,焙烧坯的机械强度也大为提高。
二次焙烧是焙烧品浸渍后进行再次焙烧,使浸入焙烧品孔隙中的沥青炭化的工艺过程。
生产体积密度要求较高的电极(除RP以外的所有品种)和接头坯料需进行二焙,接头坯料还需进行三浸四焙或二浸三焙。
⏹焙烧炉主要炉型:连续作业----环式炉(带盖、不带盖)、隧道窑间歇作业----倒焰窑、车底式焙烧炉、箱式焙烧炉⏹焙烧曲线及最高温度:一次焙烧----320、360、422、480小时,1250 ℃二次焙烧----125、240 、280 小时,700-800 ℃⏹焙烧品的检查:外观敲击、电阻率、体积密度、抗压强度、内部结构剖析⏹浸渍是将炭材料置于压力容器中,在一定的温度和压力条件下将液态浸渍剂沥青浸入渗透到制品电极孔隙中的工艺过程。
目的是降低制品气孔率,增加制品体积密度和机械强度,改善制品的导电和导热性能。
浸渍的工艺流程及相关技术参数是:焙烧坯——表面清理——预热(260-380 ℃,6-10小时)——装入浸渍罐——抽真空(8-9KPa,40-50min)——注沥青(180-200 ℃)——加压(1.2-1.5MPa,3-4小时)——返沥青——冷却(罐内或罐外)浸渍品的检查:浸渍增重率G=(W2-W1)/W1×100%一次浸渍品增重率≥14%二次浸渍品增重率≥9%三次浸渍品增重率≥5%●石墨化是指在高温电炉内保护介质中把炭制品加热到2300 ℃以上,使无定形乱层结构炭转化成三维有序石墨晶质结构的高温热处理过程。
平面六角网格层状结构石墨化的目的和作用:①提高炭材料的导电、导热性(电阻率降低4-5倍,导热性提高约10倍);②提高炭材料的抗热振性能和化学稳定性(线膨胀系数降低50-80%);③使炭材料具有润滑性和抗磨性;④排出杂质,提高炭材料的纯度(制品的灰分由0.5-0.8%降到0.3%左右)。
●石墨化过程的实现:炭材料的石墨化是在2300-3000 ℃高温下进行的,故工业上只有通过电加热方式才能实现,即电流直接通过被加热的焙烧品,这时装入炉内的焙烧品既是通过电流产生高温的导体,又是被加热到高温的对象。
目前广泛采用的炉型有艾奇逊(Acheson)石墨化炉和内热串接(LWG)炉。
前者产量大、温差大、电耗较高,后者加热时间短、电耗低、电阻率均匀但不好装接头。
石墨化工艺过程的控制是通过测温确定与升温情况相适应的电功率曲线进行控制,通电时间艾奇逊炉50-80小时,LWG炉9-15小时。
石墨化的电耗很大,一般为3200-4800KWh,工序成本约占整个生产成本的20-35%石墨化品的检查:外观敲击、电阻率测试●机械加工:炭石墨材料机械加工的目的是依靠切削加工来到达所需要的尺寸、形状、精度等,制成符合使用要求电极本体和接头。
石墨电极加工分为电极本体和接头两个独立加工过程。
本体加工包括镗孔与粗平端面、车外圆与精平端面和铣螺纹3道工序,圆锥形接头的加工可分为6道工序:切断、平端面、车锥面、铣螺纹、钻孔安栓和开槽。
电极接头连接方式:圆锥形接头连接(一吋三扣和一吋四扣)、圆柱形接头连接、凹凸连接(公母扣连接)加工精度的控制:螺纹锥度偏差、螺纹螺距、接头(孔)大径偏差、接头孔同轴度、接头孔垂直度、电极端面平整度、接头四点偏差等。
用专用环规和板规等检查。
成品电极的检查:精度、重量、长度、直径、体积密度、电阻率、预装配合精度等。
石墨电极的质量指标反映石墨电极质量和使用性能的指标主要有:体积密度d b、电阻率ρ、抗折强度σ、弹性模量E、热膨胀系数α和灰分A%。
根据这几项指标的差异以及原料和制造工艺的不同,国家标准(YB/T 4088/89/90-2000)中将石墨电极分为普通功率石墨电极(RP)、高功率石墨电极(HP)、超高功率石墨电极(UHP)三种。