模具厂生产进度异常原因分析
生产异常分析报告模板范文
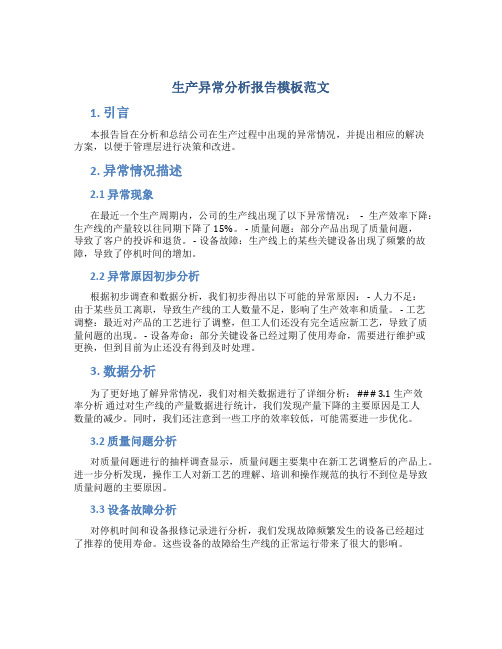
生产异常分析报告模板范文1. 引言本报告旨在分析和总结公司在生产过程中出现的异常情况,并提出相应的解决方案,以便于管理层进行决策和改进。
2. 异常情况描述2.1 异常现象在最近一个生产周期内,公司的生产线出现了以下异常情况:- 生产效率下降:生产线的产量较以往同期下降了15%。
- 质量问题:部分产品出现了质量问题,导致了客户的投诉和退货。
- 设备故障:生产线上的某些关键设备出现了频繁的故障,导致了停机时间的增加。
2.2 异常原因初步分析根据初步调查和数据分析,我们初步得出以下可能的异常原因: - 人力不足:由于某些员工离职,导致生产线的工人数量不足,影响了生产效率和质量。
- 工艺调整:最近对产品的工艺进行了调整,但工人们还没有完全适应新工艺,导致了质量问题的出现。
- 设备寿命:部分关键设备已经过期了使用寿命,需要进行维护或更换,但到目前为止还没有得到及时处理。
3. 数据分析为了更好地了解异常情况,我们对相关数据进行了详细分析: ### 3.1 生产效率分析通过对生产线的产量数据进行统计,我们发现产量下降的主要原因是工人数量的减少。
同时,我们还注意到一些工序的效率较低,可能需要进一步优化。
3.2 质量问题分析对质量问题进行的抽样调查显示,质量问题主要集中在新工艺调整后的产品上。
进一步分析发现,操作工人对新工艺的理解、培训和操作规范的执行不到位是导致质量问题的主要原因。
3.3 设备故障分析对停机时间和设备报修记录进行分析,我们发现故障频繁发生的设备已经超过了推荐的使用寿命。
这些设备的故障给生产线的正常运行带来了很大的影响。
4. 解决方案基于以上异常情况和数据分析结果,我们提出以下解决方案: ### 4.1 人力调整 - 招聘新员工:加大招聘力度,尽快补充生产线上的人力不足。
- 培训与提升:针对新工艺进行专项培训,提升工人的理解和操作能力。
4.2 工艺优化•与研发部门密切合作:与研发部门沟通,了解新工艺要求,并及时进行工艺优化。
模具检讨书范文

您好!我怀着无比懊悔的心情,向您递交这份关于模具制作过程中出现问题的检讨书。
近期,在负责模具制作的过程中,由于我的疏忽,导致模具出现了一系列问题,严重影响了生产进度和产品质量。
在此,我向您表示诚挚的歉意,并对我的失误进行深刻检讨。
以下是我对此次失误的反思和检讨:一、失误原因分析1. 对模具制作工艺掌握不足。
在模具设计阶段,我没有充分了解相关工艺要求,导致设计存在缺陷,为后续生产埋下隐患。
2. 质量意识淡薄。
在制作过程中,我没有严格按照工艺要求进行操作,对细节问题疏于关注,导致模具出现质量问题。
3. 工作责任心不强。
在模具制作过程中,我未能及时发现并解决问题,延误了生产进度,给公司造成了损失。
二、整改措施1. 加强学习,提高自身技能。
我将积极参加公司组织的模具制作培训,提高自己的专业技能,确保在今后的工作中能够熟练掌握模具制作工艺。
2. 增强质量意识。
在制作过程中,我将严格按照工艺要求进行操作,对每一个细节进行严格把关,确保模具质量。
3. 提高工作责任心。
我将认真对待每一项工作,加强责任心,确保生产进度不受影响。
4. 及时沟通,发现问题。
在模具制作过程中,我将加强与同事的沟通,及时发现问题,并采取措施予以解决。
三、道歉及承诺对于此次失误,我深感愧疚。
在此,我向您表示诚挚的歉意,并承诺在今后的工作中,一定引以为戒,严格要求自己,为公司创造更多价值。
最后,请您相信,我会以此事为鉴,努力改进,以实际行动弥补此次失误,为公司的发展贡献自己的力量。
检讨人:[姓名]日期:[年月日]。
工序质量异常报告

工序质量异常报告一、问题描述二、问题分析根据对该工序的观察和调查,分析出现质量异常的可能原因:1.设备故障:可能是设备在工作过程中出现了故障,导致该工序无法正常完成。
例如,在一些装配工序中,机器可能存在零件抓取不到位、故障导致质量问题。
2.操作不当:有可能是操作人员对该工序的操作不够熟悉或不规范,导致产品出现质量问题。
例如,在一些焊接工序中,焊接温度、时间或压力调整不当,导致焊接不牢固或焊点不均匀。
3.材料质量问题:在一些工序中,原材料的质量问题也可能导致产品质量异常。
例如,在一些喷涂工序中,喷涂粉末材料可能出现质量问题,导致涂层不均匀或颜色不符合要求。
4.工艺参数调整不当:有可能是在该工序中,工艺参数的调整不合理,导致产品质量异常。
例如,在一些注塑工序中,注塑温度、注塑时间或注塑压力调整不当,导致产品尺寸不准确或外观不符合要求。
三、解决方案针对上述问题,提出以下解决方案:1.设备维护和保养:对工作中使用的设备进行定期的维护和保养,确保设备处于良好的工作状态,减少故障发生的可能性。
2.培训操作人员:对该工序的操作人员进行培训,使其熟悉工序操作规范,掌握正确的操作技巧,提高工作效率和产品质量。
3.严格把控原材料质量:加强对原材料的质量检查,确保原材料符合要求。
并与供应商进行沟通,提高原材料质量的稳定性。
4.完善工艺参数:对该工序的工艺参数进行优化和调整,确保参数的合理性和准确性,避免因参数调整不当而导致的质量问题。
四、实施效果经过上述解决方案的实施,取得了以下效果:1.设备故障率显著下降,工序的稳定性得到了提高,减少了工作中由于设备故障导致的质量异常。
2.通过对操作人员的培训,工序的操作规范性得到了提高,操作人员能够更加熟练地完成工序,并且产品质量得到了明显的提升。
3.对原材料的质量检查得到了加强,选择了质量更稳定的原材料供应商,材料质量问题的发生几率明显降低。
4.通过对工艺参数的优化和调整,工序的稳定性得到了提高,产品质量得到了明显的改善。
影响模具质量和进度的原因分析及解决办法

影响模具质量和进度的原因分析及解决办法国际金属加工网2012年01月16日一、影响模具质量的原因分析:1、影响模具质量的外部原因有:(1)产品的设计质量产品的设计应具有良好的冲压工艺性、铸造锻造工艺性等,否则,模具难以实现产品的形状和尺寸精度要求,只能用机加的方法来实现。
如FJL205C-22001动片,产品设计成尖棱尖角,造成冲压模具凹凸模崩块或开裂,模具寿命较低。
产品尺寸精度较高时,模具无法保证产品要求。
(2)产品的工艺质量冲压工艺不合理,会造成产品的形状和尺寸精度达不到要求,如整修余量过大,会造成产品断面质量差。
毛料展开尺寸计算不准确,会造成产品弯曲或拉深后尺寸精度达不到要求。
如外贸转包产品孔的精度较高,用模具整孔时,冲头易断,改用钻孔铰孔后,可以满足生产要求。
铸造工艺不合理,!产品无法浇铸成形。
铸件、锻件、橡胶件收缩率等工艺参数给得不准确,会造成模具报废或返修。
对子返修模具,产品工艺提出的故障不全或不准确,会造成模具多次返修和试模。
(3)模具老化冲压件厂目前仍有许多六、七十年代制造的模具在使用,许多模具零件磨损,寿命已到,但是由子没有新模具的制造,为满足生产需要,死马当活马医,造成模具频繁返修,多次试模。
(4)产品材料每批次产品材料的材质如硬度、厚度的微小变化,对模具的凹、凸模间隙,产品的弯曲回弹角有较大的影响;造成使用同一套模具时,上一批产品合格,下一批产品不合格;模具随着产品材料的变化而变化。
这就增加了模具的返修次数。
(5)模具材料及热处理模具关键件均为锻件,锻件质量的好坏直接影模具的寿命;锻件组织中碳化物分布是否均匀,锻件级别是否达标,造成模具在使用中易开裂、崩刃、掉块,影响试模合格率及使用寿命。
另外热处理质量也是直接影响模具质量的一个因素,淬火硬度过高,模具易开裂、掉块;过低,影响产品尺寸及模具寿命。
(6)试模的影响试模设备的精度,试模人员的技能、经验,试模问题是否暴露全面,都对试模次数有很大影响。
模具工件异常报告
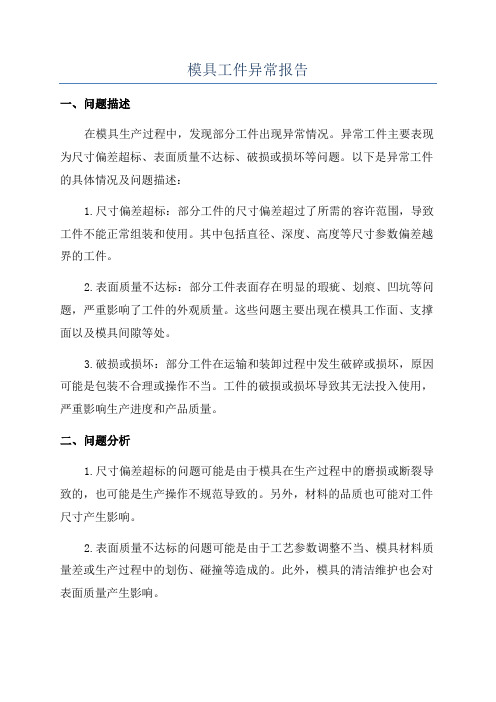
模具工件异常报告一、问题描述在模具生产过程中,发现部分工件出现异常情况。
异常工件主要表现为尺寸偏差超标、表面质量不达标、破损或损坏等问题。
以下是异常工件的具体情况及问题描述:1.尺寸偏差超标:部分工件的尺寸偏差超过了所需的容许范围,导致工件不能正常组装和使用。
其中包括直径、深度、高度等尺寸参数偏差越界的工件。
2.表面质量不达标:部分工件表面存在明显的瑕疵、划痕、凹坑等问题,严重影响了工件的外观质量。
这些问题主要出现在模具工作面、支撑面以及模具间隙等处。
3.破损或损坏:部分工件在运输和装卸过程中发生破碎或损坏,原因可能是包装不合理或操作不当。
工件的破损或损坏导致其无法投入使用,严重影响生产进度和产品质量。
二、问题分析1.尺寸偏差超标的问题可能是由于模具在生产过程中的磨损或断裂导致的,也可能是生产操作不规范导致的。
另外,材料的品质也可能对工件尺寸产生影响。
2.表面质量不达标的问题可能是由于工艺参数调整不当、模具材料质量差或生产过程中的划伤、碰撞等造成的。
此外,模具的清洁维护也会对表面质量产生影响。
3.破损或损坏的问题主要是由于在运输和装卸过程中未能采取有效的保护措施,对工件进行妥善包装和固定。
三、解决方案针对以上问题,制定以下解决方案:1.尺寸偏差超标问题:-对模具进行定期维护、保养,检查模具的磨损情况,及时更换磨损过度的模具。
-加强质量控制,并优化生产工艺参数,确保工件在规定范围内的尺寸偏差。
-对生产操作进行培训和指导,提高员工的操作规范性和技术水平。
2.表面质量不达标问题:-优化生产工艺参数,确保模具在生产过程中的温度、压力等控制合理。
-选择高质量的模具材料,确保模具的耐磨性和抗划伤性能。
-定期进行模具的清洁和维护,避免灰尘、污渍等对模具表面质量的影响。
3.破损或损坏问题:-设计合理的包装方案,确保工件在运输和装卸过程中的安全性。
-增加运输时的防震措施,保护工件免受震动和撞击的影响。
-提供专业培训,加强装卸操作人员的技能和操作规范。
鱼骨图图参考案例

原材料保障
人员保障
3、各工序长每天对每 位员工进行班产量考核
1、增加计件产品单价,提高员工福利
8、原材料质量不 良让步放行每月不 超过2批次
6、实行外部供应链管理
4、每季度末对带班 进行快速换模培训
2、每季度初对计划员进行PMC 专业技能培训
交
付
9、提高检验员巡检频次 从原来两小时一次提升
7、要求一分厂对常规、
确保工模夹具不得影 响生产进度
各工序 检验员
各工序 工序长
7月1起持续
孙美凤、 莫勇
8月15日
王再超 吴新波
操场跑步5圈 俯卧撑30个
交付及时率行动计划表
序 号
行动举措
成果要求
责任 完成时 检查 未完成赞
人
间
人
助
从原来的7人加工流
11
11.1在6月30日前完成对现有的布局进行价值 流分析 11.2优化2科检验布局 11.3最终在7月30日实现两条流水作业
入生产
片班产量1500只
2.3.在9月15日完成4台,9月30日调试完成投入 现自动排片6000
生产
只
完成时 间
检查 人
未完成赞助
8月10日 何毅 乐捐200元
9月30日 何毅 乐捐200元
塑壳项目组彻底解决全塑型产品塑壳残留问题
3.1.提交塑壳残留产品代号至项目组,6月30日完
成
3
3.2.项目组根据提交的产品代号编写项目行动计划 至二分厂,7月15日完成,所提交的行动计划最晚
付
带班技能差造成换 线、换模时间长
及
时
计划不准确
作业前准备不充分
率 低
水\电\气的异常
生产计划异常
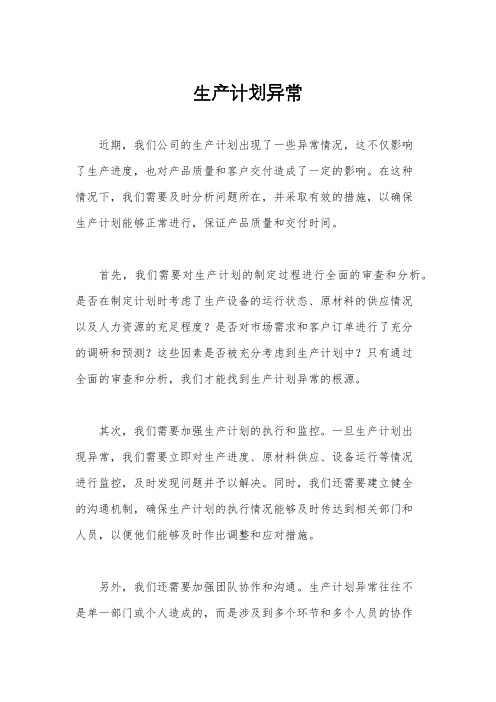
生产计划异常近期,我们公司的生产计划出现了一些异常情况,这不仅影响了生产进度,也对产品质量和客户交付造成了一定的影响。
在这种情况下,我们需要及时分析问题所在,并采取有效的措施,以确保生产计划能够正常进行,保证产品质量和交付时间。
首先,我们需要对生产计划的制定过程进行全面的审查和分析。
是否在制定计划时考虑了生产设备的运行状态、原材料的供应情况以及人力资源的充足程度?是否对市场需求和客户订单进行了充分的调研和预测?这些因素是否被充分考虑到生产计划中?只有通过全面的审查和分析,我们才能找到生产计划异常的根源。
其次,我们需要加强生产计划的执行和监控。
一旦生产计划出现异常,我们需要立即对生产进度、原材料供应、设备运行等情况进行监控,及时发现问题并予以解决。
同时,我们还需要建立健全的沟通机制,确保生产计划的执行情况能够及时传达到相关部门和人员,以便他们能够及时作出调整和应对措施。
另外,我们还需要加强团队协作和沟通。
生产计划异常往往不是单一部门或个人造成的,而是涉及到多个环节和多个人员的协作问题。
因此,我们需要加强团队之间的协作和沟通,建立起良好的工作关系和合作氛围。
只有团结一致,共同努力,才能够有效地解决生产计划异常问题。
最后,我们需要不断总结经验,改进工作方法。
在解决了当前生产计划异常问题后,我们需要对整个过程进行全面的总结和分析,找出问题所在,找出改进的方法和措施,以避免类似问题再次发生。
只有不断总结经验,不断改进工作方法,我们才能够逐步提高生产计划的执行效率和质量。
总之,生产计划异常是一个复杂的问题,需要我们全面审查和分析制定过程,加强执行和监控,加强团队协作和沟通,不断总结经验,改进工作方法。
只有这样,我们才能够有效地解决生产计划异常问题,确保生产计划的正常进行,保证产品质量和交付时间。
希望全公司上下能够共同努力,共同解决这一问题,使我们的生产计划能够更加顺利地进行。
制造业工厂生产异常处理办法

XX公司生产异常处理办法第一条目的为了规范本公司生产异常的处理,特制定本办法。
第二条范围本办法适用于一切造成生产停工或生产进度延迟的情形。
第三条异常分类1.计划异常:因生产计划或安排不当、失误等导致的异常。
2.物料异常:因物料供应不及时,物料品质问题等导致的异常。
3.设备和模具异常:因设备、模具不足或故障等原因而导致的异常。
4.制程异常:因生产过程中出现了待料、阻塞、效率低等导致的异常。
5.质量异常:生产过程中发生的各种质量问题导致的生产异常。
5.客户取消或变更订单(颜色、规格、名称、包装材料、包装规格等),公司的生产因此出现的生产异常。
6.人员不足:公司产能扩大或员工减员所致的人力不足,造成的生产异常。
7.水电异常:停电、停水导致的生产异常。
8.安全事故、工伤事故、火灾事故等导致的生产异常。
9.自然灾害:台风、洪涝、地震等自然灾害导致的生产异常。
第四条异常的常规处理程式1.标识:当生产出现异常时,应急处理得当,异常消除,不需进行标识。
但经应急处理仍无法消除异常的,应对现场物料、设备、场地等进行标识,以区别于常态,免于出现次生异常。
2.应急处理:当生产出现异常时,在场的人员都应按各自职责采取相应的应急处理措施。
以达到消除异常、恢复生产的目的。
3.上报:在完成异常的标识和处理后,异常所在部门或车间应向上级领导报告。
4.调查:根据不同异常的性质,由不同的责任部门牵头,对异常的发生原因进行调查。
5.评价:根据调查结果,应对异常情况所造成的不良影响进行评价。
6.问责:根据异常所造成的不良影响程度,对属人为责任的异常,问责相关部门和相关人员。
7.改善及预防:对发生异常的原因进行改善预防,使得今后不再重复出现相同事件。
第五条异常的应急处理一、计划异常:生产安排不当、失误、等导致的异常,应及时纠正不当的生产安排,消除异常造成的生产混乱状态,及时恢复正常的生产秩序。
二、物料异常:1.原料供应不及时,常表现为无料、有料不足等。