分布式控制系统PLC
DCS与PLC的区别

DCS与PLC的区别控制类产品名目繁多,各家叫法不一。
通常使用的控制类产品包括DCS、PLC两大类。
我们又将DCS的概念拓展到FCS。
DCS(Distributed Contorl System),集散控制系统,又称分布式控制系统。
PLC(Program Logic Control ),可编程逻辑控制器。
FCS(FieldBus Contorl Syestem),现场总线控制系统●发展到现在,DCS和PLC之间没有一个严格的界线,在大多数人看来,大的系统就是DCS,小的系统就叫PLC。
当然,这么说也不是不可以,但是还不对。
现在我们来重新建立这个观念。
●首先,DCS和PLC 之间有什么不同?1、从发展的方面来说:DCS从传统的仪表盘监控系统发展而来。
因此,DCS从先天性来说较为侧重仪表的控制,比如我们使用的YOKOGAWACS3000DCS系统甚至没有PID数量的限制(PID,比例微分积分算法,是调节阀、变频器闭环控制的标准算法,通常PID的数量决定了可以使用的调节阀数量)。
PLC从传统的继电器回路发展而来,最初的PLC甚至没有模拟量的处理能力,因此,PLC从开始就强调的是逻辑运算能力。
2、从系统的可扩展性和兼容性的方面来说:市场上控制类产品繁多,无论DCS还是PLC,均有很多厂商在生产和销售。
对于PLC系统来说,一般没有或很少有扩展的需求,因为PLC系统一般针对于设备来使用。
一般来讲,PLC也很少有兼容性的要求,比如两个或以上的系统要求资源共享,对PLC来讲也是很困难的事。
而且PLC一般都采用专用的网络结构,比如西门子的MPI总线性网络,甚至增加一台操作员站都不容易或成本很高。
DCS在发展的过程中也是各厂家自成体系,但大部分的DCS系统,比如横河YOKOGAW A、霍尼维尔、ABB等等,虽说系统内部(过程级)的通讯协议不尽相同,但操作级的网络平台不约而同的选择了以太网络,采用标准或变形的TCP/IP协议。
dcs与plc的区别

1、名称不同DCS:分散控制系统(distributedcontrol systems)。
PLC:可编程逻辑控制器(Programmable Logic Controller),只是一种控制“装置”。
2、侧重点不同DCS更侧重于过程控制领域(如化工、冶炼、制药等)主要是一些现场参数的监视和调节控制。
PLC则侧重于逻辑控制(机械加工类)。
当然现在的PLC也能很好的处理过程控制问题,但是没有DCS专业。
3、模拟量不同模拟量大于100个点以上的,一般采用DCS模拟量在100个点以内的,一般采用PLC。
4、网络形式不同DCS网络是整个系统的中枢神经,DCS系统通常采用的国际标准协议 TCP/IP。
它是安全可靠双冗余的高速通讯网络,系统的拓展性与开放性更好。
PLC因为基本上都为单个小系统工作,在与别的PLC或上位机进行通讯时,所采用的网络形式基本都是单网结构,网络协议也经常与国际标准不符。
5、出现故障不同DCS系统所有I/O模块都带有CPU,可以实现对采集及输出信号品质判断与标量变换,故障带电拔,随机更换。
而PLC模块只是简单电气转换元,没有智能芯片,故障后相应单元全部瘫痪。
扩展资料:可编程逻辑控制器是种专门为在工业环境下应用而设计的数字运算操作电子系统。
它采用一种可编程的存储器,在其内部存储执行逻辑运算、顺序控制、定时、计数和算术运算等操作的指令,通过数字式或模拟式的输入输出来控制各种类型的机械设备或生产过程。
集散控制系统是以微处理器为基础,采用控制功能分散、显示操作集中、兼顾分而自治和综合协调的设计原则的新一代仪表控制系统。
集散控制系统简称DCS,也可直译为“分散控制系统”或“分布式计算机控制系统”。
它采用控制分散、操作和管理集中的基本设计思想,采用多层分级、合作自治的结构形式。
其主要特征是它的集中管理和分散控制。
目前DCS在电力、冶金、石化等各行各业都获得了极其广泛的应用。
SCADA、DCS与PLC之间的区别
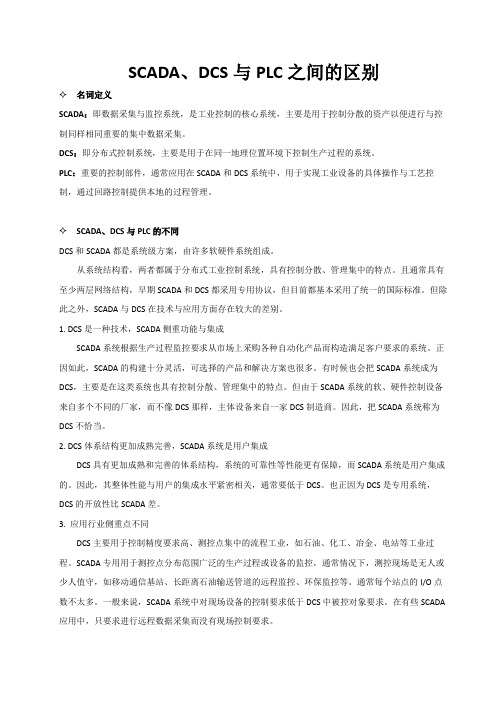
SCADA、DCS与PLC之间的区别✧名词定义SCADA:即数据采集与监控系统,是工业控制的核心系统,主要是用于控制分散的资产以便进行与控制同样相同重要的集中数据采集。
DCS:即分布式控制系统,主要是用于在同一地理位置环境下控制生产过程的系统。
PLC:重要的控制部件,通常应用在SCADA和DCS系统中,用于实现工业设备的具体操作与工艺控制,通过回路控制提供本地的过程管理。
✧SCADA、DCS与PLC的不同DCS和SCADA都是系统级方案,由许多软硬件系统组成。
从系统结构看,两者都属于分布式工业控制系统,具有控制分散、管理集中的特点。
且通常具有至少两层网络结构,早期SCADA和DCS都采用专用协议,但目前都基本采用了统一的国际标准。
但除此之外,SCADA与DCS在技术与应用方面存在较大的差别。
1. DCS是一种技术,SCADA侧重功能与集成SCADA系统根据生产过程监控要求从市场上采购各种自动化产品而构造满足客户要求的系统。
正因如此,SCADA的构建十分灵活,可选择的产品和解决方案也很多。
有时候也会把SCADA系统成为DCS,主要是在这类系统也具有控制分散、管理集中的特点。
但由于SCADA系统的软、硬件控制设备来自多个不同的厂家,而不像DCS那样,主体设备来自一家DCS制造商。
因此,把SCADA系统称为DCS不恰当。
2. DCS体系结构更加成熟完善,SCADA系统是用户集成DCS具有更加成熟和完善的体系结构,系统的可靠性等性能更有保障,而SCADA系统是用户集成的。
因此,其整体性能与用户的集成水平紧密相关,通常要低于DCS。
也正因为DCS是专用系统,DCS的开放性比SCADA差。
3. 应用行业侧重点不同DCS主要用于控制精度要求高、测控点集中的流程工业,如石油、化工、冶金、电站等工业过程。
SCADA专用用于测控点分布范围广泛的生产过程或设备的监控,通常情况下,测控现场是无人或少人值守,如移动通信基站、长距离石油输送管道的远程监控、环保监控等。
DCS和PLC区别及优缺点

plc和dcs在工业自动化控制中占有举足轻重的地位,而工业自动化控制是国家工业发展战略的核心。
PLC以及DCS在工业控制的各个环节中不断的升级、完善,已经成为现代工业生产制造中不可或缺的工具。
1、DCS和PLC的定义DCS控制系统,在国内自控行业又称之为集散控制系统。
即所谓的分布式控制系统,是相对于集中控制系统而言的一种新型计算机控制系统,它是在集中控制系统的基础上发展、演变而来的。
DCS作为一个集过程控制和过程监控为一体的计算机综合系统,在通信网络的不断带动下,DCS系统已经成为了一个综合计算机,通信、显示和控制等4C技术的完整体系。
其主要特点是分散控制、集中操作、分级管理、配置灵活以及组态方便。
现如今的DCS系统可以广泛地用于工业装置的生产控制和经营管理,在化工、电力、冶金等流程自动化领域的应用已经十分普及。
PLC,即逻辑可编程控制器,是一种数字运算操作的电子系统,专为在工业环境应用而设计的。
它采用一类可编程的存储器,用于其内部存储程序,执行逻辑运算、顺序控制、定时、计数与算术操作等面向用户的指令,并通过数字或模拟式输入/输出控制各种类型的机械或生产过程,是工业控制的核心部分。
2、DCS和PLC控制器的差别DCS和PLC控制器的主要差别是在开关量和模拟量的运算上,即使后来两者相互有些渗透,但是仍然有区别。
80年代以后,PLC除逻辑运算外,也增加了一些控制回路算法,但要完成一些复杂运算还是比较困难,PLC用梯形图编程,模拟量的运算在编程时不太直观,编程比较麻烦。
但在解算逻辑方面,表现出快速的优点。
而DCS使用功能块封装模拟运算和逻辑运算,无论是逻辑运算还是复杂模拟运算的表达形式都非常清晰,但相对PLC来说逻辑运算的表达效率较低。
3、DCS和PLC在火电厂的应用在火电厂热工自动化领域,DCS和PLC是两个完全不同而又有着千丝万缕联系的概念。
DCS和PLC都是计算机技术与工业控制技术相结合的产物,火电厂主机控制系统用的是DCS,而PLC主要应用在电厂辅助车间。
PCS FCS DCS PLC 区别
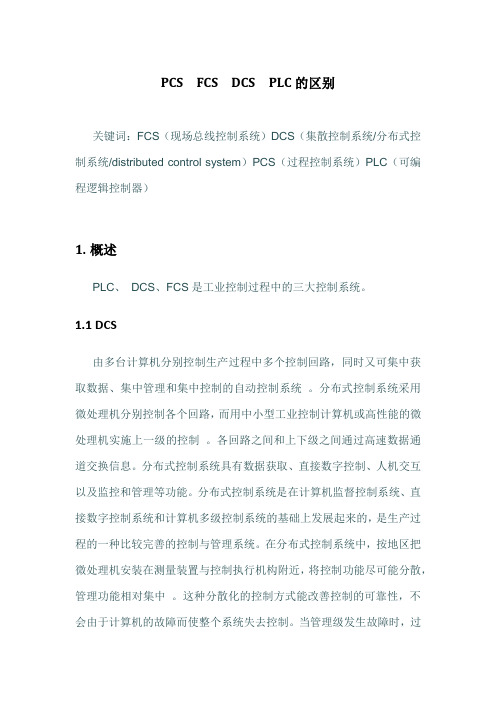
PCS FCS DCS PLC的区别关键词:FCS(现场总线控制系统)DCS(集散控制系统/分布式控制系统/distributed control system)PCS(过程控制系统)PLC(可编程逻辑控制器)1.概述PLC、DCS、FCS是工业控制过程中的三大控制系统。
1.1 DCS由多台计算机分别控制生产过程中多个控制回路,同时又可集中获取数据、集中管理和集中控制的自动控制系统。
分布式控制系统采用微处理机分别控制各个回路,而用中小型工业控制计算机或高性能的微处理机实施上一级的控制。
各回路之间和上下级之间通过高速数据通道交换信息。
分布式控制系统具有数据获取、直接数字控制、人机交互以及监控和管理等功能。
分布式控制系统是在计算机监督控制系统、直接数字控制系统和计算机多级控制系统的基础上发展起来的,是生产过程的一种比较完善的控制与管理系统。
在分布式控制系统中,按地区把微处理机安装在测量装置与控制执行机构附近,将控制功能尽可能分散,管理功能相对集中。
这种分散化的控制方式能改善控制的可靠性,不会由于计算机的故障而使整个系统失去控制。
当管理级发生故障时,过程控制级(控制回路)仍具有独立控制能力,个别控制回路发生故障时也不致影响全局。
与计算机多级控制系统相比,分布式控制系统在结构上更加灵活、布局更为合理和成本更低。
分散型控制系统(DCS)是以微处理机为基础,以危险分散控制,操作和管理集中为特性,集先进的计算机技术、通讯技术、CRT技术和控制技术即4C技术于一体的新型控制系统。
随着现代计算机和通讯网络技术的高速发展,DCS正向着多元化、网络化、开放化、集成管理方向发展,使得不同型号的DCS可以互连,进行数据交换,并可通过以太网将DCS系统和工厂管理网相连,实现实时数据上网,成为过程工业自动控制的主流。
DCS的构成方式十分灵活,可由专用的管理计算机站、操作员站、工程师站、记录站、现场控制站和数据采集站等组成,也可由通用的服务器、工业控制计算机和可编程控制器构成。
DCS、FCS、PLC的区别

DCS系统采用一个统一的开发环境,工程师站(过程管理层)用于现场控制站的组态,控制算 法的开发以及流程图画面的开发。采用一个统一数据库!而PLC用于过程控制需要不同的开发 环境,首先要对PLC(相当于DCS的现场控制站层)进行逻辑开发,建立相应的数据库,然后再通 过相应的上位机软件,例如GE FANUC 的PROFICY HMI/SCADA - IFIX 或 CIMPLICITY PLANT EDITION软件,建立与PLC相对应的数据库,然后进行流程图画面的开发。 DCS开发控制算法采用仪表技术人员熟悉的风格,仪表人员很容易将P&I图转化成DCS提 供的控制算法,而PLC采用梯形图逻辑来实现过程控制,对于仪表人员来说相对困难。尤其是 复杂回路的算法,不如DCS实现起来方便。 DCS系统通常提供完整的系统给用户,包括机柜,电源,工程师站,操作员站,用户只需 在现场简单的安装。而PLC则需要系统集成。 DCS实现顺序连锁功能相对于PLC来讲是弱势,且逻辑执行速度不如PLC, 也不如PLC编程 方便。 DCS的现场控制站层‘通常采用集中式控制,尽管支持远程分布式I/O, 但由于成本原 因, 很少采用。而PLC基于现场总线的远程分布式I/O更灵活易用,能有效的节省接线成本。 —— GE FANUC全球自动化解决方案中国区总经理贲志刚
—— 贝加莱负责APROL产品应用开发的技术经理陈志平
分析DCS与PLC的区别,最关键的是两点,一是DCS是分布式 控制,拥有全局数据库;二是PLC是顺序扫描机制,DCS是以 时间为基准的控制。我们的系统符合第一点,例如一个I/O标签 的修改,在HMI也可以同步体现。 ——罗克韦尔自动化过程市场产品经理 王广野
我们下面的比较将是针对现场级DCS与FCS的比较
现场总线控制系统
DCS与PLC的区别与联系
DCS与PLC的区别与联系DCS(分散控制系统)和PLC(可编程逻辑控制器)是在工业自动化领域中常用的控制系统。
它们在设计、功能和应用方面存在一些区别和联系。
本文将探讨DCS与PLC之间的区别与联系,旨在帮助读者更好地理解这两种控制系统。
一、DCS与PLC的定义和概述DCS是一种分层结构的控制系统,它通常由多个分布在不同位置的控制单元组成,这些控制单元可以通过网络进行通信。
每个控制单元都可以独立地执行控制任务,并与其他控制单元共享信息。
DCS广泛用于大型工业过程控制系统,例如发电厂、化工厂和石油炼厂等。
PLC是一种用于自动控制的专用计算机,它可以根据预先编写的程序来控制各种设备和过程。
PLC通常用于小型或中型控制系统,例如自动化生产线、机械设备和建筑物自动化系统等。
虽然DCS和PLC具有不同的定义和概述,但它们都能够实现工业自动化控制的目标,并在不同的应用场景中发挥重要作用。
接下来将详细讨论DCS与PLC的具体区别与联系。
二、DCS与PLC的区别1. 结构与组成DCS的结构更加复杂,由多个控制单元组成,这些单元可以相互通信和共享信息。
每个单元都具有独立的性能和功能,可以实现高度分布式和协作控制。
相比之下,PLC通常是一个单独的设备,它独立执行控制任务。
2. 网络通信DCS的控制单元通过网络进行通信,可以实现异地操作和远程监控。
这使得DCS适用于大型的、分布式的控制系统。
PLC通常通过本地连接进行通信,适用于较小规模的控制系统。
3. 灵活性和可扩展性DCS具有较高的灵活性和可扩展性,可以根据需要灵活地增加或减少控制单元,并实现系统的动态调整。
相比之下,PLC相对独立,扩展性较低。
4. 编程语言和功能DCS通常使用高级编程语言进行控制和编程,具备更为复杂的功能和逻辑。
PLC则使用简化的Ladder Diagram(梯形图)等编程语言,功能相对较简单。
这使得DCS适用于需要更复杂控制逻辑的应用,而PLC则适合于一些简单的控制任务。
ESDPLCDCS三大控制系统介绍
05
三大控制系统比较
性能比较
01
响应速度
ESD系统具有最快的响应速度,能够在毫秒级别内完成控制动作,而
PLC和DCS系统的响应速度通常在秒级别。
02
控制精度
DCS系统的控制精度最高,能够实现精确的模拟量控制,而ESD和PLC
系统的控制精度相对较低,主要用于开关量控制。
03
可靠性
PLC系统的可靠性最高,因为其结构简单,且对环境要求较低,而ESD
3
PLC系统适用于对设备自动化程度要求较高的场 合,如智能制造、交通、仓储等领域,能够实现 设备的自动化控制。
优缺点比较
ESD系统的优点是响应速度快,能够迅速切断危险源,避免事故发生;缺点是过于敏感,可能会因为 误动作而导致生产过程受到影响。
DCS系统的优点是控制精度高,能够实现整个生产流程的精确控制;缺点是结构复杂,维护成本较高。
ESD系统可以根据特定工艺和安全要求进行定制, 适应不同的控制需求。
ESD系统应用场景
01
02
03
化工行业
在化工生产过程中,ESD 系统用于监控压力、温度、 液位等关键参数,确保安 全生产的需要。
制药行业
制药生产线上的ESD系统 用于确保在异常情况下迅 速停车,避免对产品和环 境造成损害。
食品加工
02
它通常由传感器、逻辑控制器和 执行机构组成,用于监控生产过 程中的关键参数,并在异常情况 下触发紧急停车。
ESD系统特点
快速响应
ESD系统能够在几毫秒内对紧急情况作出反应, 迅速停车设备以防止事故扩大。
安全可靠
ESD系统通常采用冗余设计,确保在单个组件故 障时仍能可靠地执行紧急停车操作。
灵活性高
自动化控制英文缩写解释
自动化控制英文缩写解释自动化控制(Automation Control)是指通过计算机、电子设备和传感器等技术手段,对各种生产设备和工业过程进行监测、控制和优化的过程。
在自动化控制领域中,人们通常使用一些缩写词汇来表示特定的技术、设备或者概念。
下面是一些常见的自动化控制英文缩写及其解释:1. PLC:Programmable Logic Controller(可编程逻辑控制器)PLC是一种专门用于工业自动化控制的计算机控制系统。
它可以根据预先编写的程序,对各种设备进行逻辑控制,实现自动化生产。
2. DCS:Distributed Control System(分布式控制系统)DCS是一种将控制功能分布在多个控制器中的控制系统。
它可以实现对大型工业过程的集中监控和控制,提高生产效率和安全性。
3. SCADA:Supervisory Control and Data Acquisition(监控与数据采集)SCADA系统是一种用于监控和控制分布式设备的系统。
它可以实时采集和显示设备的运行状态,并通过远程控制实现对设备的操作。
4. HMI:Human Machine Interface(人机界面)HMI是一种用于人机交互的设备或者软件界面。
它可以通过图形化界面显示设备的状态和操作控制,使操作员更方便地进行控制和监控。
5. PID:Proportional-Integral-Derivative(比例-积分-微分)PID是一种常用的控制算法,用于调节系统的输出。
它根据系统的误差、积分和微分来计算控制量,使系统能够快速稳定地响应变化。
6. CNC:Computer Numerical Control(计算机数控)CNC是一种通过计算机控制机床运动的技术。
它可以根据预先编写的程序,实现对机床的自动加工,提高加工精度和效率。
7. MES:Manufacturing Execution System(创造执行系统)MES是一种用于管理和控制创造过程的系统。
自动化控制英文缩写解释
自动化控制英文缩写解释自动化控制是指利用计算机技术和现代控制理论,对生产过程、设备和系统进行自动化监测、调节和控制的一种技术手段。
在自动化控制领域中,有许多常见的英文缩写,下面将对其中一些常见的英文缩写进行解释。
1. PLC (Programmable Logic Controller)PLC是可编程逻辑控制器的缩写。
它是一种专门用于工业自动化控制的计算机控制系统。
PLC能够根据预先设定的程序对输入信号进行逻辑运算和控制输出信号,从而实现对生产过程的自动化控制。
2. DCS (Distributed Control System)DCS是分布式控制系统的缩写。
它是一种用于监控和控制大型工业过程的自动化系统。
DCS系统由多个分布在不同地点的控制单元组成,这些控制单元通过网络连接,实现对整个生产过程的集中控制和监测。
3. SCADA (Supervisory Control and Data Acquisition)SCADA是监控与数据采集的缩写。
它是一种用于监控、采集和控制远程设备和系统的技术。
SCADA系统通过传感器和执行器与远程设备进行通信,将实时数据传输到监控中心,操作员可以通过监控中心对远程设备进行监测和控制。
4. HMI (Human Machine Interface)HMI是人机界面的缩写。
它是一种用于人机交互的技术,通过图形化界面和操作控制设备,使操作员能够直观地监控和控制自动化系统。
HMI通常包括触摸屏、键盘、指示灯等设备,操作员可以通过这些设备与自动化系统进行交互。
5. PID (Proportional-Integral-Derivative)PID是比例-积分-微分的缩写。
它是一种常用的控制算法,用于调节和控制自动化系统的输出。
PID控制器根据当前的偏差和变化率,计算出输出信号,从而实现对系统的精确控制。
6. CNC (Computer Numerical Control)CNC是计算机数控的缩写。
- 1、下载文档前请自行甄别文档内容的完整性,平台不提供额外的编辑、内容补充、找答案等附加服务。
- 2、"仅部分预览"的文档,不可在线预览部分如存在完整性等问题,可反馈申请退款(可完整预览的文档不适用该条件!)。
- 3、如文档侵犯您的权益,请联系客服反馈,我们会尽快为您处理(人工客服工作时间:9:00-18:30)。
宋宇
第三章 DCS控制算法
工业生产中大量应用顺序控制,均已可编 程控制器PLC作为核心。
顺序控制:按照一定的逻辑关系,对各生 产阶段进行信息处理与控制。
传送带生产线控制 印刷机械
灌装及包装机械
木材加工
纺织机械
空调控制
电梯控制
第三章 DCS控制算法
3.12 PLC简介 PLC:可编程序控制器Programmable Logic
PLC的发展趋势
1)向高速度、大存储容量方向发展 (CPU处理速度nS级;内存2M字节)
2)向多品种方向发展和提高可靠性 (超大型和超小型)
3)产品更加规范化、标准化 (硬件、软件兼容的PLC)
4)分散型、智能型、与现场总线兼容的I/0 5)加强联网和通信的能力 6)控制的开放和模块化的体系结构
第三章 DCS控制算法
以上划分不包括模拟量I/0点数,且划分界限不是固定不 变的。
第三章 DCS箱体式。整体式PLC
是将电源、CPU、I/0部件都集中装在一个机箱 内。一般小型PLC采用这种结构。 模块式PLC:将PLC各部分分成若干个单独的模 块,如 CPU模块、I/0模块、电源模块和各种功 能模块。模块式PLC由框架和各种模块组成。模 块插在插座上。一般大、中型PLC采用模块式结 构,有的小型PLC也采用这种结构。 有的PLC将整体式和模块式结合起来,称为叠装 式PLC。
第三章 DCS控制算法
3.12 PLC简介 PLC的历史
✓ 1968年,美国最大的汽车制造商通用汽车公司 (GM),为了适应汽车型号不断更新的需要, 提出了十条技术指标在社会上公开招标,制造一 种新型的工业控制装置
✓ 以后,日本、德国、法国等国相继研制了各自的 PLC。
✓ 70年代中期,PLC进入了实用化阶段。
第三章 DCS控制算法
PLC的分类
(1)按 I/O点数分类 I/O点数小于 32为微型PLC; I/O点数在32~128为微小型PLC; I/O点数在128~256为小型PLC; I/O点九在256~1024为中型PLC; I/O点数大于1024为大型PLC; I/O点数在4000以上为超大型PLC。
第三章 DCS控制算法
3.12 PLC简介
✓ 辽宁无线电二厂引进德国西门子技术生产 PLC;
✓ 无锡电器和日本光洋合资生产的 PLC; ✓ 中美合资的厦门 A—B公司生产的PLC; ✓ 上海香岛机电公司引进技术生产的PLC; ✓ 上海OMRON公司; ✓ 西安Siemens公司等。
第三章 DCS控制算法
✓ 70年代末和 80年代初,PLC进入了成熟阶段。
第三章 DCS控制算法
3.12 PLC简介 美国PLC发展得最快: ✓ 1984年有48家,生产150多种PLC; ✓ 1987年有63家,生产243种PLC; ✓ 1996年有70余家,生产近300种PLC。 ✓ 著名厂家有A—B(Allen-Bradley)艾伦一布拉德利公
第三章 DCS控制算法
3.12 PLC简介
我国在 70年代末和 80年代初开始引进PLC。我国早期 独立研制PLC的单位有: ✓ 北京机械工业自动化研究所, ✓ 上海工业自动化仪表研究所, ✓ 大连组合机床研究所, ✓ 成都机床电器研究所, ✓ 中科院北京计算机所及自动化所, ✓ 长春一汽,上海起重电器厂,上海香岛机电公司, ✓ 上海自力电子设备厂 ✓ 等单位。 以上诸单位都没有形成规模化生产。
✓ 金钟默勒 AEG, ✓ 法国的施耐德 ✓ 瑞士的Selectron公司等。
第三章 DCS控制算法
3.12 PLC简介 1971年,日本从美国引进PLC技术,由日立公司研
制成功日本第一台PLC。 日本生产PLC的厂家有40余家: ✓ 三菱电机(MITSUBISHI) ✓ 欧姆龙(OMRON) ✓ 富士电机(Fuji Electric) ✓ 东芝(TOSHIBA), ✓ 光洋(KOYO),松下电工(MEW) ✓ 和泉(IDEC),夏普(SHARP) ✓ 安川等公司。
Controller 可编程序控制器的历史
60年代 继电接触控制系统 优点:简单 易懂 价格便宜
缺点:硬设备多 接线复杂 改变设计困难。
第三章 DCS控制算法
3.12 PLC简介 定义:
国际电工委员会( IEC)于 1982年11月和 1985年1月 对可编程序控制器作了如下的定义:“可编程序控制 器是一种数字运算操作的电子系统,专为在工业环境 下应用而设计。它采用可编程序的存储器,用来在其 内部存储执行逻辑运算、顺序控制、定时、计数和算 术运算等操作的命令,并通过数字式模拟式的输入和 输出,控制各种类型的机械或生产过程。可编程序控 制器及其有关设备,都应按易于与工业控制系统联成 一个整体,易于扩充功能的原则而设计”。
司,MODICON莫迪康公司,GE-FANUC公司,TI (Texas Instrument)德州仪器公司,WESTHOUSE Electric西屋电气公司, IPM(International Parallel Machines)国际并行机器公司等。
第三章 DCS控制算法
3.12 PLC简介 欧洲PLC的厂家有60余家: 西门子(Siemens)于1973年研制出第一台 PLC。
第三章 DCS控制算法
PLC著名品牌
根据美国 Automation Research Co.(ARC)的商 情调查,在1994年PLC市场上,最大的5家PLC制 造商是(80%):
✓ SIEMENS, ✓ Allen-Bradly,(Rockwell) ✓ AEG Schneider, ✓ 三菱电机, ✓ OMRON
4. PLC著名品牌 中国PLC市场排行榜上的世界十大厂家:
✓ 美国 A-B公司 (Allen-Bradley) ✓ 德国西门子公司(Siemens) ✓ 美国GE-Fanuc公司 ✓ 美国的莫迪康(Modicon)和法国的TE电器公司 ✓ 日本欧姆公司(OMRON) ✓ 日本三菱电机株式会社(MITSUBISHI) ✓ 日本富士电机株式会社(Fuji Electric) ✓ 日本东芝公司(TOSHIBA) ✓ 日本的光洋电子(KOYO) ✓ 日本松下电工株式会社(MEW)