塑件脱模斜度设计要点
注塑零件设计要求

注塑件设计要点1、开模方向和分型线2、脱模斜度3、零件壁厚4、加强筋5、圆角和孔6、抽芯机构及避免7、塑件的变形8、一体铰链9、嵌件10、气辅注塑11、综合考虑工艺性和零件性能注塑件设计要点1、利用注塑工艺生产产品时,由于塑料在模腔中的不均匀冷却和不均匀收缩以及产品结构设计的不合理,容易引起产品的各种缺陷:缩印、熔接痕、气孔、变形、拉毛、顶伤、飞边。
2、为得到高质量的注塑产品,我们必须在设计产品时充分考虑其结构工艺性,下面结合注塑产品的主要结构特点分析避免注塑缺陷的方法。
2.1开模方向和分型线每个注塑产品在开始设计时首先要确定其开模方向和分型线,以保证尽可能减少抽芯机构和消除分型线对外观的影响。
2.1.1开模方向确定后,产品的加强筋、卡扣、凸起等结构尽可能设计成与开模方向一致,以避免抽芯减少拼缝线,延长模具寿命。
2.1.2例如:保险杠的开模方向一般为车身坐标χ方向,如果开模方向设计成与χ轴不一致,则必须在产品图中注明其夹角。
2.1.3开模方向确定后,可选择适当的分型线,以改善外观及性能。
2.2脱模斜度2.2.1适当的脱模斜度可避免产品拉毛。
光滑表面的脱模斜度应大于0.5度,细皮纹表面大于1度,粗皮纹表面大于1.5度。
2.2.2适当的脱模斜度可避免产品顶伤。
2.2.3深腔结构产品设计时外表面斜度要求小于内表面斜度,以保证注塑时模具型芯不偏位,得到均匀的产品壁厚,并保证产品开口部位的材料密度强度。
2.3产品壁厚2.3.1各种塑料均有一定的壁厚范围,一般0.5~4mm,当壁厚超过4mm时,将引起冷却时间过长,产生缩印等问题,应考虑改变产品结构。
2.3.2壁厚不均会引起表面缩印。
2.3.3壁厚不均会引起气孔和熔接痕。
2.4加强筋2.4.1加强筋的合理应用,可增加产品刚性,减少变形。
2.4.2加强筋的厚度必须小于产品壁厚的1/3,否则引起表面缩印。
2.4.3加强筋的单面斜度应大于1.5°,以避免顶伤。
注塑件模具设计应注意的几大要点

注塑件模具设计应注意的几大要点模具工业是制造业中的一项基础产业,是技术成果转化的基础,同时本身又是高新技术产业的重要领域,在欧美等工业发达国家被称为“点铁成金”的“磁力工业”。
美国工业界认为“模具工业是美国工业的基石”;德国则认为它是所有工业中的“关键工业”;日本模具协会也认为“模具是促进社会繁荣富裕的动力”,同时也是“整个工业发展的秘密”,是“进入富裕社会的原动力”。
一、开模方向和分型线每个注塑产品在开始设计时首先要确定其开模方向和分型线,以保证尽可能减少抽芯滑块机构和消除分型线对外观的影响。
1、开模方向确定后,产品的加强筋、卡扣、凸起等结构尽可能设计成与开模方向一致,以避免抽芯减少拼缝线,延长模具寿命。
2、开模方向确定后,可选择适当的分型线,避免开模方向存在倒扣,以改善外观及性能。
二、脱模斜度1、适当的脱模斜度可避免产品拉毛(拉花)。
光滑表面的脱模斜度应≥0.5度,细皮纹(砂面)表面大于1度,粗皮纹表面大于1.5度。
2、适当的脱模斜度可避免产品顶伤,如顶白、顶变形、顶破。
3、深腔结构产品设计时外表面斜度尽量要求大于内表面斜度,以保证注塑时模具型芯不偏位,得到均匀的产品壁厚,并保证产品开口部位的材料强度。
三、产品壁厚1、各种塑料均有一定的壁厚范围,一般0.5~4mm,当壁厚超过4mm时,将引起冷却时间过长,产生缩印等问题,应考虑改变产品结构。
2、壁厚不均会引起表面缩水。
3、壁厚不均会引起气孔和熔接痕。
四、加强筋1、加强筋的合理应用,可增加产品刚性,减少变形。
2、加强筋的厚度必须≤(0.5~0.7)T产品壁厚,否则引起表面缩水。
3、加强筋的单面斜度应大于1.5°,以避免顶伤。
五、圆角1、圆角太小可能引起产品应力集中,导致产品开裂。
2、圆角太小可能引起模具型腔应力集中,导致型腔开裂。
3、设置合理的圆角,还可以改善模具的加工工艺,如型腔可直接用R刀铣加工,而避免低效率的电加工。
4、不同的圆角可能会引起分型线的移动,应结合实际情况选择不同的圆角或清角。
产品结构设计——塑胶件脱模斜度设计

4.不同材料脱模斜度设计
(4)PC 脱模斜度在部件的任何一边或凸起的地方都需要设置,包括上模和下模的地方。一般光滑 的表面1.5°至2°已很足够,然而有蚀纹的表面需要额外的脱模斜度,以每深0.25mm (0.001in)增加1°脱模角。 (5)PET 塑胶成品的筋,支柱边缘、流道壁等,脱模斜度达到0.5°就足够。 (6)PS 脱模斜度最好取1°,最小0.5°,太小会使部件难以脱模。如果部件有蚀纹,如皮革纹,每 深0.025mm就多加1°脱模角。
6.制品脱模斜度设计
(1)箱体与盖类制品
当H≤50mm时,S/H=1/30~1/50 当50<H≤100mm时,S/H=1/60
6.制品脱模斜度设计
(2)格子板形制品 当格子的间距P≤4mm时,脱模斜度α=1/10P。格子C尺寸越大,脱模斜度越大。 当格子高度H超过8mm,脱模斜度不能取太大值时,可采用图(b)的形式,使一部分进入动模一侧, 从而使脱模斜度满足要求。
4.不同材料脱模斜度设计
Байду номын сангаас
材料
PE、PP、PVC(软) ABS、PA、POM、PPO PC、PSF、PS、AS、PMMA
脱模斜度
30′~1° 40′~1°30′
50′~2°
(1)ABS 一般应用边0.5°至1°就足够。有时因为抛光纹路与出模方向相同,脱模斜度可接近至零。 有纹路的侧面需每深0.025mm(0.001in)增加1°脱模斜度。正确的脱模斜度可向蚀纹供 应商取得。
2H
型芯的脱模斜度应大于型腔。
凸台尺寸(用于3mm自攻螺纹) (mm)
6.制品脱模斜度设计
(6)最小脱模斜度 脱模斜度影响制品的脱出情况。如果脱模斜度很小,脱模阻力增大,顶出机构就会失去作用。在 一般情况下,不能小于最小脱模斜度,以防止制品留模。
注塑模具设计原则和核心是什么

注塑模具设计原则和核心是什么一、开模方向和分型线每个注塑产品在开始设计时首先要确定其开模方向和分型线,以保证尽可能减少抽芯滑块机构和消除分型线对外观的影响。
1、开模方向确定后,产品的加强筋、卡扣、凸起等结构尽可能设计成与开模方向一致,以避免抽芯减少拼缝线,延长模具寿命。
2、开模方向确定后,可选择适当的分型线,避免开模方向存在倒扣,以改善外观及性能。
二、脱模斜度1 、适当的脱模斜度可避免产品拉毛(拉花)。
光滑表面的脱模斜度应≥0.5度,细皮纹(砂面)表面大于1度,粗皮纹表面大于1.5度。
2 、适当的脱模斜度可避免产品顶伤,如顶白、顶变形、顶破。
3、深腔结构产品设计时外表面斜度尽量要求大于内表面斜度,以保证注塑时模具型芯不偏位,得到均匀的产品壁厚,并保证产品开口部位的材料强度。
三、产品壁厚1 、各种塑料均有一定的壁厚范围,一般0.5~4mm,当壁厚超过4mm 时,将引起冷却时间过长,产生缩印等问题,应考虑改变产品结构。
2 、壁厚不均会引起表面缩水。
3 、壁厚不均会引起气孔和熔接痕。
四、加强筋1、加强筋的合理应用,可增加产品刚性,减少变形。
2、加强筋的厚度必须≤ (0.5~0.7)T产品壁厚,否则引起表面缩水。
3、加强筋的单面斜度应大于1.5°,以避免顶伤。
五、圆角1、圆角太小可能引起产品应力集中,导致产品开裂。
2、圆角太小可能引起模具型腔应力集中,导致型腔开裂。
3、设置合理的圆角,还可以改善模具的加工工艺,如型腔可直接用R刀铣加工,而避免低效率的电加工。
4 、不同的圆角可能会引起分型线的移动,应结合实际情况选择不同的圆角或清角。
六、孔1 、孔的形状应尽量简单,一般取圆形。
2 、孔的轴向和开模方向一致,可以避免抽芯。
3 、当孔的长径比大于2时,应设置脱模斜度。
此时孔的直径应按小径尺寸(最大实体尺寸)计算。
4 、盲孔的长径比一般不超过4。
防孔针冲弯5 、孔与产品边缘的距离一般大于孔径尺寸。
七、注塑模的抽芯、滑块机构及避免1、当塑件按开模方向不能顺利脱模时,应设计抽芯滑块机构。
注塑结构设计注意要点

注塑设计注意要点1、利用注塑工艺生产产品时,由于塑料在模腔中的不均匀冷却和不均匀收缩以及产品结构设计的不合理,容易引起产品的各种缺陷:缩印、熔接痕、气孔、变形、拉毛、顶伤、飞边。
2、为得到高质量的注塑产品,我们必须在设计产品时充分考虑其结构工艺性,下面结合注塑产品的主要结构特点分析避免注塑缺陷的方法。
(1)开模方向和分型线每个注塑产品在开始设计时首先要确定其开模方向和分型线,以保证尽可能减少抽芯机构和消除分型线对外观的影响。
1)、开模方向确定后,产品的加强筋、卡扣、凸起等结构尽可能设计成与开模方向一致,以避免抽芯减少拼缝线,延长模具寿命。
2)、例如:保险杠的开模方向一般为车身坐标X方向,如果开模方向设计成与X轴不一致,则必须在产品图中注明其夹角。
3)、开模方向确定后,可选择适当的分型线,以改善外观及性能。
2)脱模斜度1)、适当的脱模斜度可避免产品拉毛。
光滑表面的脱模斜度应大于度,细皮纹表面大于 1 度,粗皮纹表面大于度。
2)、适当的脱模斜度可避免产品顶伤。
3)、深腔结构产品设计时外表面斜度要求小于内表面斜度,以保证注塑时模具型芯不偏位,得到均匀的产品壁厚,并保证产品开口部位的材料密度强度。
(3)产品壁厚1)、各种塑料均有一定的壁厚范围,一般〜4mm,当壁厚超过4mm时,将引起冷却时间过长,产生缩印等问题,应考虑改变产品结构。
2)、壁厚不均会引起表面缩印。
3)、壁厚不均会引起气孔和熔接痕。
(4)加强筋1 )、加强筋的合理应用,可增加产品刚性,减少变形。
2)、加强筋的厚度必须小于产品壁厚的 1 /3 ,否则引起表面缩印。
3)、加强筋的单面斜度应大于°,以避免顶伤。
(5)圆角1)、圆角太小可能引起产品应力集中,导致产品开裂。
2)、圆角太小可能引起模具型腔应力集中,导致型腔开裂。
3)、设置合理的圆角,还可以改善模具的加工工艺,如型腔可直接用R 刀铣加工,而避免低效率的电加工。
4)、不同的圆角可能会引起分型线的移动,应结合实际情况选择不同的圆角或清角。
塑料件结构设计中关于出模方向与脱模斜度的探讨

所以,塑料零件结构设计中尽量采用分模线在 零件下端的方式; 分模线在零件中间的方式设计只有在配合零件 斜度冲突不可避免且分模线在产品最终装配的非外 露表面上才可采用;
图例四通过零件出模方向的角度调整,较好的满 足了零件间隙和脱模斜度的工艺要求。虽然摆角度使 结构设计复杂化,但是如果设计阶段不考虑出摸方向 与脱模斜度等工艺因素,而在模具制造阶段增加斜度 将产生较大间隙或者干涉,问题将不可避免,无法保 证产品品质。
零件的出模方向主要由产品的造型及功能要求决定。这就是说:在产品设计 的美工造型、油泥模型、外形曲面造型、零件分件等阶段就已经要考虑了, 这里仅仅探讨在结构设计中出模方向与脱模斜度的相互关系。
首先举一例:
这是两个简单并列组装的零件,有四种设计可作对比, 简化表示如下:
对比分析:图 例一未设计脱 模斜度,NG 图例二外观间 隙较大,客户 不接受; 图例三右零件 分模线在零件 中间,? 图例四,OK
塑料件结构设计中关于出模 方向与脱模斜度的探讨
南京开维汽车设计有限公司
王秀成
塑料件与钣金件因模具工艺不同, 因而设计思想也有很大的不同,其中 之一就是塑料件的出模方向与脱模斜 度的问题。ຫໍສະໝຸດ 塑料模具可以简化表示如下:
模具母模仁 零件出模方向
零件脱模斜度
模具公模仁
在模具上,零件的主出模方向只有一个:在 模具的Z轴方向上; 在产品上,不同零件的主出模方向在3D空 间上各有不同;
分模线在零件中间与分模线在零件下端工艺对比:
塑料零件生产时,模具在数百吨的合模压力下容易产生微小的变形与 位移,特别是在模具寿命达到一定程度时; 分模线在零件中间时模具变形与位移夸张显示如下:
分模面周圈 夹线
外型面产生断差 缺陷
塑件脱模斜度
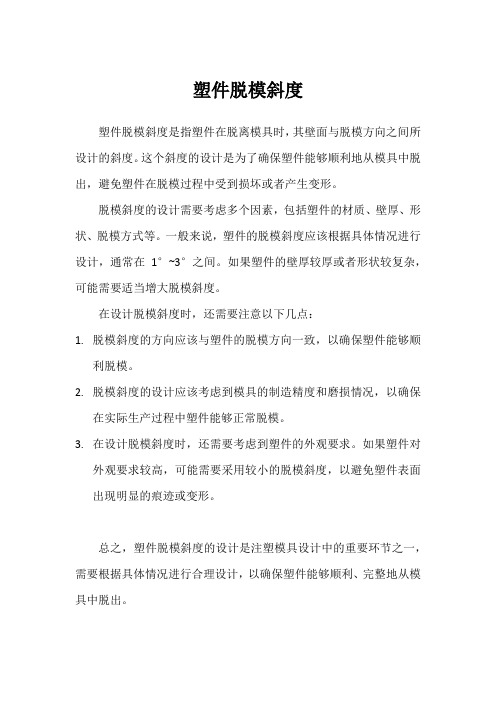
塑件脱模斜度
塑件脱模斜度是指塑件在脱离模具时,其壁面与脱模方向之间所设计的斜度。
这个斜度的设计是为了确保塑件能够顺利地从模具中脱出,避免塑件在脱模过程中受到损坏或者产生变形。
脱模斜度的设计需要考虑多个因素,包括塑件的材质、壁厚、形状、脱模方式等。
一般来说,塑件的脱模斜度应该根据具体情况进行设计,通常在1°~3°之间。
如果塑件的壁厚较厚或者形状较复杂,可能需要适当增大脱模斜度。
在设计脱模斜度时,还需要注意以下几点:
1.脱模斜度的方向应该与塑件的脱模方向一致,以确保塑件能够顺
利脱模。
2.脱模斜度的设计应该考虑到模具的制造精度和磨损情况,以确保
在实际生产过程中塑件能够正常脱模。
3.在设计脱模斜度时,还需要考虑到塑件的外观要求。
如果塑件对
外观要求较高,可能需要采用较小的脱模斜度,以避免塑件表面出现明显的痕迹或变形。
总之,塑件脱模斜度的设计是注塑模具设计中的重要环节之一,需要根据具体情况进行合理设计,以确保塑件能够顺利、完整地从模具中脱出。
塑胶产品厚度和脱模斜度设计要点

塑胶产品厚度和脱模斜度设计要点1.3、厚度设计实例塑料的成型工艺及使用要求对塑件的壁厚都有重要的限制。
塑件的壁厚过大,不仅会因用料过多而增加成本,且也给工艺带来一定的困难,如延长成型时间(硬化时间或冷却时间)。
对提高生产效率不利,容易产生汽泡,缩孔,凹陷;塑件壁厚过小,则熔融塑料在模具型腔中的流动阻力就大,尤其是形状复杂或大型塑件,成型困难,同时因为壁厚过薄,塑件强度也差。
塑件在保证壁厚的情况下,还要使壁厚均匀,否则在成型冷却过程中会造成收缩不均,不仅造成出现气泡,凹陷和翘曲现象,同时在塑件内部存在较大的内应力。
设计塑件时要求壁厚与薄壁交界处避免有锐角,过渡要缓和,厚度应沿着塑料流动的方向逐渐减小。
2 脱模斜度2.1 脱模斜度的要点脱模角的大小是没有一定的准则,多数是凭经验和依照产品的深度来决定。
此外,成型的方式,壁厚和塑料的选择也在考虑之列。
一般来讲,对模塑产品的任何一个侧壁,都需有一定量的脱模斜度,以便产品从模具中取出。
脱模斜度的大小可在0.2°至数度间变化,视周围条件而定,一般以0.5°至1°间比较理想。
具体选择脱模斜度时应注意以下几点:a. 取斜度的方向,一般内孔以小端为准,符合图样,斜度由扩大方向取得,外形以大端为准,符合图样,斜度由缩小方向取得。
如下图1-1。
图1-1b. 凡塑件精度要求高的,应选用较小的脱模斜度。
c. 凡较高、较大的尺寸,应选用较小的脱模斜度。
d. 塑件的收缩率大的,应选用较大的斜度值。
e. 塑件壁厚较厚时,会使成型收缩增大,脱模斜度应采用较大的数值。
f. 一般情况下,脱模斜度不包括在塑件公差范围内。
g. 透明件脱模斜度应加大,以免引起划伤。
一般情况下,PS料脱模斜度应大于3°,ABS及PC料脱模斜度应大于2°。
h. 带革纹、喷砂等外观处理的塑件侧壁应加3°~5°的脱模斜度,视具体的咬花深度而定,一般的晒纹版上已清楚例出可供作参考之用的要求出模角。
- 1、下载文档前请自行甄别文档内容的完整性,平台不提供额外的编辑、内容补充、找答案等附加服务。
- 2、"仅部分预览"的文档,不可在线预览部分如存在完整性等问题,可反馈申请退款(可完整预览的文档不适用该条件!)。
- 3、如文档侵犯您的权益,请联系客服反馈,我们会尽快为您处理(人工客服工作时间:9:00-18:30)。
脫模斜度的設計要點。
在塑件的內,外表面,沿脫模方向均應設計足夠的脫模斜度,否則會發生塑件脫模困難,或頂出時拉壞擦傷塑件.。
塑件常用脫模斜度為1~1.5度,也可小於0.5度.黨塑件有特殊要求時,斜度可設計外表面為5`,內表面為10`~20`.。
在不影響使用的前提下塑件脫模斜度要設計儘量大些. 圖示脫模角度
各種塑料推荐的脫模斜度
其他注意事
項。
較高,較大的尺寸,應選用較小的脫模斜度. 。
塑件形狀複雜的,不易脫模的應選用較大的脫模斜度. 。
塑料的收縮率大的,應選用較大的斜度值.。
塑件壁厚較厚時,會使成型收縮增大,脫模斜度應採用較大的數值. 。
塑件精度要求高的,應採用較小的脫模斜度. 塑件的壁厚設計。
塑件的壁厚對塑件質量影響很大.。
壁厚過小,成型時熔融塑料流動阻力大,充模困難,特別是大型且形狀複雜的塑件.。
壁厚過大,不但原料浪費,而且對熱固性塑料的成型來說增加壓塑的時間,且容易造成固化不完全.對熱
20`~1°
熱固性塑料
50`~2° 聚苯乙烯,有機玻璃 50`~2° 硬聚綠乙烯,聚碳酸酯 40`~1°30`
ABS,尼龍,聚甲醛,綠化聚醚,30`~1° 聚乙烯,聚丙烯,軟聚綠乙烯 脫模斜度 材 料
塑性塑料則增加冷卻時間,更重要的是塑件產生氣泡,縮孔,翹曲變形等缺陷.
在Notebook設計中壁厚的注意事項。
一般壁厚要大於0.8mm,如有特殊時也可達到0.6mm.。
Case_lcd_bezel壁厚一般為1.2~1.8mm.。
Case_lcd_cover壁厚一般為1.5~1.8mm.。
Case_top_case壁厚一般為1.7~1.8mm.。
Case_bottom_case壁厚一般為1.6mm.
圓角的設計。
為了避免應力集中,提高塑件的熔料流動性及便於脫模,在塑件的各面或內部連接處應採取圓弧過度.
r=(1/2~1)h
R=r+h
兩壁厚度相等
圓角半徑計算
圖示
條件
r>=(h1+h2)/2
R=r+(h1+h2)/2 兩壁厚不等
圓角半徑計算
圖示
條件。