丙烷脱氢技术
PDH技术简介及新型应用研究

PDH技术简介及新型应用研究丙烷脱氢技术简介及国内应用现状01、丙烷脱氢技术原理原料丙烷在专用催化剂的作用下,脱氢生成丙烯与副产品氢气。
反应式:该反应为强吸热过程,也是平衡反应,所以,提高温度和降低压力有利于脱氢反应的进行,从而获得较高的丙烷转化率。
02、国外主流丙烷脱氢技术存在问题丙烷脱氢技术主要有霍尼韦尔UOP催化脱氢连续移动床工艺和荷兰CBI循环多反应器系统工艺,2种技术都有较明显的缺点。
UOP工艺缺点:对装置原料丙烷的纯度要求高(丙烷纯度95%,且硫含量要低),单程转化率和选择性略低。
CBI工艺缺点:反应器设置较多,间歇操作,操作复杂;装置操作压力高,能耗较大;催化剂寿命短,且使用的催化剂含铬,对环境有污染。
新型丙烷脱氢技术开发现状及特点01、技术研发背景及简介目前国内已经投产的丙烷脱氢项目所用催化剂几乎全部被国外公司垄断。
国产化的新型高效丙烷脱氢制丙烯催化剂,对于打破国外技术垄断、实现国产化具有重要的意义。
中国石油大学重质油实验室李春义教授课题组开发出新型丙烷/异丁烷脱氢(ADHO)技术,并工业化试验取得成功,填补了国内空白。
该技术特点为:采用无毒、无腐蚀、非贵金属催化剂,并配套设计了高效循环流化床反应器,且成功实现生产过程连续进行。
02、ADHO技术优点(1)原料不需要预处理即可直接进装置反应,省去了脱硫、脱砷、脱铅等复杂过程;(2)既适用于丙烷、异丁烷单独脱氢,也适用于丙烷与丁烷混合脱氢;(3)反应与催化剂再生连续进行,效率高;(4)催化剂无毒,对环境无污染;(5)催化剂为难熔氧化物,无腐蚀性,有利于装置长周期安全稳定运行;(6)催化剂机械强度高,剂耗低等。
03、ADHO主要技术指标烯烃16%;反应方式为循环流该技术烷烃转换率为80%,氢气收率4%,C4化床反应,温度为600℃。
参考同类装置,该装置能耗为12600MJ/t左右。
某炼油厂应用该技术可行性分析丙烷脱氢装置原料为丙烷,产品为丙烯,副产氢气。
丙烷脱氢(PDH)介绍
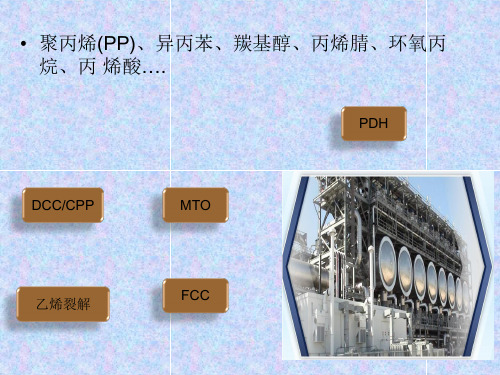
C3H6+ H2
传统的蒸汽热裂解装置(乙烯装置),C-C和C-H打断, 生产乙烯和丙烯。温度800~920℃,转化率~93%,乙烯 收率~42%,丙烯~17%。
• 催化脱氢:
所谓的“丙烷脱氢”,温度590~630 ℃ ,单程转化率 33%~44%,选择性~86%。
丙烷脱氢制丙烯反应热力学 性质
(1)吸热反应; (2)平衡常数随温度的升高而增大; (3)分子数增加的可逆反应;
• 近年来随着乙烯装置原料轻质化,丙烯相的缺口增大, 丙烷脱氢开始兴起。
• 结论:需求推动生产,丙烯属于大宗产品,需求量大尤其 下游需求大据[中国化工报]报道仅聚丙烯:预计新增产能 超过300万吨至2500万吨以上。下游需求增速约7.7%,进 口量280万吨,国内产量约2000万吨,产能利用率为80%
• 聚丙烯(PP)、异丙苯、羰基醇、丙烯腈、环氧丙 烷、丙 烯酸….
PDH
DCC/CPP
MTO
乙烯裂解
FCC
丙烷脱氢
PROPANE DEHYDROGENATION 一、丙烷脱氢反应机理 二、丙烷脱氢主要工艺技术及特点 三、工艺命脉,谁主沉浮
从丙烷脱氢到丙烯
• 反应表观方程式:
C3H8
• 热裂解脱氢:
• 设备管道材料复杂,高温钢(304H),普通碳钢 ,低温碳钢或低温合金钢(A33GR6,09MnNiDR ,3.5Ni),不锈钢。
• 反应器衬耐火材料。
• 高温管道,低温管道应力计算,反应框架的结构 设计,诸多机组采购技术服务,大型设备的专门 设计。
五、丙烷脱氢的工程特点
Catofin反应器衬里
Oleflex流程简图
反应区、
催化剂连续再生区、 产品分离区
丙烷脱氢介绍
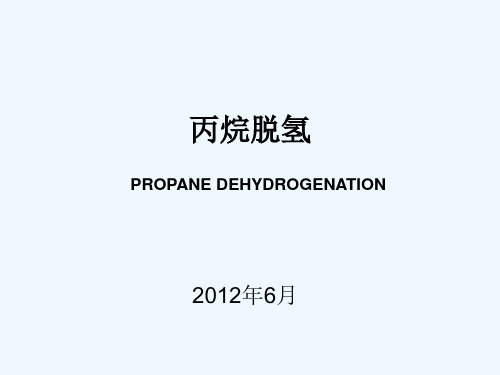
Catofin 固定床
4 连续
8 循环操作
Φ3.2m~4.2m
Φ7.9m×17.2m
639~650
590~600
0.23
-0.05
670
400(外壳)
0.65/F.V.
0.28/F.V.
304S.S
C.S&耐火材料衬里
加热炉加热反应原料
热空气加热催化剂+加热 炉适度加热反应原料
UOP提供的Pt系催化剂
南方化学公司提供的Cr 系催化剂
连续再生(CCR)
间歇切换再生
五、丙烷脱氢的工程特点
丙烷脱氢的工程特点(一)
(Catofin PDH) • 工艺参数跨度大:
温度:高温704℃;低温-104℃。
压力:负压:0.05MPa(绝);正压:2.39MPag。
五、丙烷脱氢的工程特点
丙烷脱氢的工程特点(二)
目的:通过深冷方式回收碳三,同时分离氢气、甲烷等轻 烃; 工艺介质从常温逐级冷凝冷却到-98 ℃,丙烯制冷、乙烯 制冷提供不同级别冷源: 丙烯压缩提供:13℃, -1℃ , -23℃, -35℃ 乙烯制冷提供:-63℃, -100℃
丙烷脱氢
PROPANE DEHYDROGENATION
2012年6月
提纲
一、丙烷脱氢反应机理 二、轻烃催化脱氢历史变迁 三、丙烷脱氢催化剂 四、丙烷脱氢主要工艺技术 五、丙烷脱氢的工程特点
丙烯生产技术
FCC
MTO
PDH
乙烯裂解
DCC/CPP
一、丙烷脱氢反应机理
从丙烷脱氢到丙烯
• 反应表观方程式:
C3H8
• 热裂解脱氢:
C3H6+ H2
传统的蒸汽热裂解装置(乙烯装置),C-C和C-H打断, 生产乙烯和丙烯。温度800~920℃,转化率~93%,乙烯 收率~42%,丙烯~17%。
丙烷脱氢(PDH)介绍 PPT

大家有疑问的,可以询问和交流
可以互相讨论下,但要小声点
三、丙烷脱氢催化剂
丙烷脱氢催化主要有以下几种:
铬系催化剂,如Catofin工艺采用的催化剂; 铂系催化剂,如Olefex工艺采用的催化剂; 氧化脱氢类催化剂。
(氧化脱氢是指在催化剂作用下采用适当的氧化剂与丙烷反 应生成丙烯与水,其焓变小于零,为放热反应,无需外界 加热、节省能源,与催化脱氢过程相比,可以克服热力学 平衡的限制并降低催化剂的减活作用。该催化剂离实现工 业化尚远。)
(1)吸热反应; (2)平衡常数随温度的升高而增大;适当适当的高的反 应温度 (3)分子数增加的可逆反应;反应压力越低越有利.
因此,提高反应温度和降低压力有利于反应向正方向 进行;但反应温度过高将造成非催化热裂和深度脱氢反应 加剧,导致选择性降低 。通常催化脱氢反应温度 控制在 590~630 ℃ 。
目的:通过深冷方式回收碳三,同时分离氢气、甲烷等轻 烃; 工艺介质从常温逐级冷凝冷却到-98 ℃,丙烯制冷、乙烯 制冷提供不同级别冷源: 丙烯压缩提供:13℃, -1℃ , -23℃, -35℃ 乙烯制冷提供:-63℃, -100℃
(四)产品精制:
透平的乏汽作为塔釜热源,塔釜的再沸器便是透平的表面 冷凝器。 调温水系统回收低温热能,也用于塔釜热源的一部分。
• 乙烯制冷: 多级压缩,汽-液,液体多压力下蒸发,提供不同 级别冷剂, -63℃, -100℃
• 其他配套公用工程系统(火炬,燃料气,蒸汽, 仪表空气,氮气。)
四、丙烷脱氢主要工艺技术
丙烷脱氢反应单元
四、丙烷脱氢主要工艺技术
脱乙烷塔
四、丙烷脱氢主要工艺技术
丙烷脱氢技术进展及展望

丙烷脱氢技术进展及展望引言丙烷是一种重要的烷烃化合物,在化工工业中有广泛的应用。
然而,由于丙烷分子结构中含有饱和碳氢键,丙烷的活性很低,使得其在一些重要的化学反应中反应速率较慢。
为了提高丙烷的反应活性,丙烷脱氢技术应运而生。
本文将介绍丙烷脱氢技术的进展及展望。
1. 丙烷脱氢的反应机理丙烷脱氢是指通过去除丙烷分子中的氢原子,将丙烷转化为丙烯的过程。
这一反应可以通过热解、催化剂协助和电化学等方式进行。
其中,催化剂协助的脱氢方法是目前应用最为广泛的丙烷脱氢技术。
催化剂协助的丙烷脱氢主要通过在催化剂表面上形成活性位点,吸附丙烷分子并去除其中的氢原子来实现。
常用的催化剂包括铂、钼、钴等金属催化剂,以及离子液体等非金属催化剂。
这些催化剂能够有效地提高丙烷脱氢的反应速率和选择性。
2. 近年来的研究进展近年来,在丙烷脱氢技术领域取得了一些重要的研究进展。
以下是其中的一些例子:2.1 新型催化剂的研发研究人员通过合成金属氧化物纳米颗粒、改性金属催化剂和复合催化剂等方式,开发了一系列新型催化剂用于丙烷脱氢反应。
这些新型催化剂表现出更高的反应活性和选择性,能够有效地降低丙烷脱氢反应的能耗和催化剂的用量。
2.2 反应条件的优化研究人员通过调节反应温度、压力和丙烷气体的流速等操作参数,对丙烷脱氢反应的条件进行了优化。
优化后的反应条件能够提高丙烷脱氢反应的产率和选择性,减少副反应产物的生成,并且减少催化剂的失活。
2.3 电化学脱氢技术的发展电化学脱氢技术是近年来备受关注的丙烷脱氢技术之一。
这一技术利用电解反应将丙烷转化为丙烯,具有反应条件温和、产物纯度高和催化剂可循环利用等优点。
研究人员通过改进电解池设计、优化电解液成分和选择合适的催化剂等手段,进一步提高了电化学脱氢技术的效果和经济性。
3. 展望丙烷脱氢技术在能源和化工领域具有重要的应用价值。
展望未来,我们可以预见以下方向的发展:3.1 更高效的催化剂开发通过设计合成新型催化剂,如金属氧化物纳米颗粒和金属有机骨架等,进一步提高丙烷脱氢反应的反应活性和选择性。
丙烷脱氢介绍

五、丙烷脱氢的工程特点 Catofin反应器衬里
谢谢
2020/11/26
37
技术
工艺仍在改进,殊途同归,任重道远
谢谢!
Catofin 流程简图
四、丙烷脱氢主要工艺技术 Catofin反应五步骤示意
四、丙烷脱氢主要工艺技术 Catofin反应器简图
四、丙烷脱氢主要工艺技术 Star流程简图
四、丙烷脱氢主要工艺技术 Star反应器简图
四、丙烷脱氢主要工艺技术 脱乙烷塔
湿火炬(WF) ,干火炬(DF), 冷火炬(CF),液体倒空系统(LD) 其它: 燃料气,循环水,仪表空气,工厂空气…..
丙烷脱氢的工程特点(四)
• 设备大型化,管道“设备化”。 • 设备管道材料复杂,高温钢(304H),普通碳钢,低温碳钢或低温合金钢(A33GR6,09MnNiDR
,3.5Ni),不锈钢。 • 反应器衬耐火材料。
1、反应原料加热、进出料换热、余热回收(废锅)互相交错; 2、再生空气加热、再生空气换热、余热回收(废锅)互相交错。 (二)压缩: 三段压缩,闭环的调温水系统回收低温热能,用于产品塔塔釜加热热源。
五、丙烷脱氢的工程特点
丙烷脱氢的工程特点(二) (三)产品回收(低温回收):
目的:通过深冷方式回收碳三,同时分离氢气、甲烷等轻烃; 工艺介质从常温逐级冷凝冷却到-98 ℃,丙烯制冷、乙烯制冷提供不同级别冷源:
丙烷脱氢介绍
2020/11/26
1
丙烷脱氢
PROPANE DEHYDROGENATION 一、丙烷脱氢反应机理 二、丙烷脱氢主要工艺技术及特点 三、工艺命脉,谁主沉浮
丙烷脱氢(PDH)介绍(格式整齐)

18
四、丙烷脱氢主要工艺技术
Star反应器简图
高级材料
19
高级材料
20
高级材料
21
高级材料
22
四、丙烷脱氢主要工艺技术
脱乙烷塔
高级材料
23
四、丙烷脱氢主要工艺技术
产品精制
高级材料
24
四、丙烷脱氢主要工艺技术
丙烯制冷简图
高级材料
25
高级材料
26
高级材料
27
五、丙烷脱氢的工程特点
丙烷脱氢的工程特点(一)
(二)压缩:
三段压缩,闭环的调温水系统回收低温热能,用于产品塔 塔釜加热热源。
高级材料
29
五、丙烷脱氢的工程特点
丙烷脱氢的工程特点(二)
(三)产品回收(低温回收):
目的:通过深冷方式回收碳三,同时分离氢气、甲烷等轻 烃;
工艺介质从常温逐级冷凝冷却到-98 ℃,丙烯制冷、乙烯 制冷提供不同级别冷源:
三、丙烷脱氢主要工艺技术
目前主要几种丙烷脱氢技术
高级材料
6
Ol e f le x工艺
• Ol e f le x工艺是UOP公司所拥有的一种烷 烃脱氢专利技术, 至201 4年已建成投产 1 1套生产装置,总 能力达37 40 k t / a
高级材料
7
Oleflex流程简图
反应区、
催化剂连续再生区、 产品分离区
丙烯压缩提供:13℃, -1℃ , -23℃, -35℃ 乙烯制冷提供:-63℃, -100℃
(四)产品精制:
透平的乏汽作为塔釜热源,塔釜的再沸器便是透平的表面 冷凝器。
调温水系统回收低温热能,也用于塔釜热源的一部分。
高级材料
PDH丙烷脱氢UOP工艺解答

PDH丙烷脱氢UOP工艺解答1. 工艺概述丙烷脱氢(PDH)工艺是一种重要的化学反应过程,用于生产丙烯。
UOP工艺是丙烷脱氢工艺的一种,采用UOP公司的专利技术。
本文档将详细介绍PDH丙烷脱氢UOP工艺的原理、流程、关键设备和操作要点。
2. 工艺原理丙烷脱氢反应是指在高温、高压和催化剂的作用下,丙烷与氢气发生反应,生成丙烯和氢气。
其主要反应式如下:\[ C_3H_8 + H_2 \rightarrow C_3H_6 + H_2 \]UOP工艺采用的催化剂为分子筛催化剂,具有良好的活性和选择性。
在反应过程中,丙烷和氢气在催化剂的作用下,发生脱氢反应,生成丙烯和氢气。
反应后的气体经过冷却、分离和净化,得到高纯度的丙烯。
3. 工艺流程PDH丙烷脱氢UOP工艺主要包括以下几个环节:3.1 丙烷预处理丙烷首先经过压缩,提高压力,然后进入丙烷净化装置,去除杂质和水分,确保反应的稳定进行。
3.2 氢气制备与净化氢气通过水煤气制备装置或外部供应,经过压缩和净化,去除杂质和水分,确保反应的稳定进行。
3.3 反应装置丙烷和氢气在反应装置中混合,在催化剂的作用下,发生脱氢反应,生成丙烯和氢气。
反应温度、压力和催化剂活性是影响反应的关键因素。
3.4 产物分离与净化反应后的气体经过冷却、分离和净化,得到高纯度的丙烯。
分离出的氢气可以循环使用,而其他副产物则进行进一步处理。
3.5 催化剂再生催化剂在反应过程中逐渐失去活性,需要定期进行再生。
催化剂再生过程包括活性位点的再生和结构修复,以恢复催化剂的活性。
4. 关键设备PDH丙烷脱氢UOP工艺的关键设备包括:4.1 压缩机用于提高丙烷和氢气的压力,确保反应的稳定进行。
4.2 净化装置用于去除丙烷和氢气中的杂质和水分,确保反应的稳定进行。
4.3 反应装置用于实现丙烷和氢气的脱氢反应,生成丙烯和氢气。
4.4 冷却器用于冷却反应后的气体,实现产物分离和净化。
4.5 分离器用于分离丙烯和其他组分,得到高纯度的丙烯。
- 1、下载文档前请自行甄别文档内容的完整性,平台不提供额外的编辑、内容补充、找答案等附加服务。
- 2、"仅部分预览"的文档,不可在线预览部分如存在完整性等问题,可反馈申请退款(可完整预览的文档不适用该条件!)。
- 3、如文档侵犯您的权益,请联系客服反馈,我们会尽快为您处理(人工客服工作时间:9:00-18:30)。
丙烷脱氢技术10多年来,丙烷脱氢成为工业化丙烯生产的重要工艺过程,然而,其推广应用因丙烷价值较高、工艺过程投资较大而受到某些限制。
但是,丙烯需求增长和丙烯价值提高以及过程改进,致使丙烷脱氢成为有效的增产丙烯工艺,该技术对富产丙烷和短缺丙烯的地区尤为有用。
丙烯需求的增速高于汽油和乙烯的需求增速,为此,常规丙烯供应和需求之间的差额将由丙烷脱氢来弥补。
Nexant化学系统公司指出,前20年来,丙烯需求增速高于乙烯,在美国,丙烯需求/乙烯需求之比已由1980年0.48提高到2003年0.6,其他一些地区如中东、西欧和东亚也与此相似。
在美国,丙烯短缺通过FCC装置得到,但是世界大多数其他地区受到炼油厂结构模式的限制。
另外,世界新增乙烯能力的大部分基于中东的乙烷裂解。
乙烷裂解生产丙烯仅2%,而石脑油裂解生产丙烯>33%,瓦斯油裂解为39%。
中东富产乙烷,有利于建设丙烷脱氢项目。
丙烷脱氢取决于经济地取得低费用的丙烷,丙烷本身占丙烷脱氢生产丙烯总费用的2/3,大多数丙烷脱氢新项目将建在中东和亚洲部分地区。
全世界现有8套丙烷脱氢装置,生产能力190万吨/年,见表1。
据预测,到2010年将再建10套新装置,以增产丙烯400万吨/年。
现有几套丙烷脱氢装置正在马来西亚、沙特阿拉伯、西班牙和卡塔尔建设。
卡塔尔的丙烷脱氢装置将后继25万吨/年聚丙烯装置,沙特阿拉伯的丙烷脱氢装置也将后继45万吨/年聚丙烯装置。
沙特阿拉伯已有4套丙烷脱氢装置在运转,另有4套在建设中或有投资意向。
沙特聚烯烃公司(沙特国家石化公司持股75%、巴斯夫/壳牌聚烯烃联合体巴塞尔公司持股25%的合资企业)在朱拜勒的45万吨/年丙烷脱氢装置将于2004年初投产,这套将成为世界最大的丙烷脱氢装置采用鲁姆斯Catofin技术。
沙特Al-Zamil集团也将采用Oleflex技术建设45万吨/年PP装置和丙烷脱氢装置,投资5.5亿美元的项目将于2007年完成。
沙特国家聚丙烯公司也在考虑采用Catofin工艺建设45万吨/年丙烷脱氢和45万吨/年PP装置。
鲁齐公司承接了沙特阿拉伯Alujain公司第4套丙烷脱氢项目,在沙特延布将采用UOP公司Oleflex工艺建设42万吨/年丙烷脱氢和PP装置,定于2006年三季度投产。
沙特阿美公司长期提供丙烷原料,丙烯用于生产聚丙烯。
埃及Oriental石化公司也将建设35万吨/年丙烷脱氢装置,以便为二套聚丙烯装置(已有一套为12万吨/年)提供原料,投资2.25亿美元,拟采用UOP Oleflex技术,于2004年建成。
世界最大的丙烷脱氢装置由巴斯夫公司于2003年4月在西班牙塔拉戈纳投运,该装置生产35万吨/年丙烯,由巴斯夫-Sonatrach Propanchem公司(巴斯夫与阿尔及利亚Sonatrach公司的合资企业)运作。
该装置采用UOP公司Oleflex脱氢技术,装置投资费用为2.4亿美元,是生产同能力丙烯的蒸汽裂解装置的1/3-1/4,而裂解装置还联产乙烯,当地不需要乙烯。
表1. 世界丙烷脱氢和易位转化制丙烯能力投产时间公司工艺能力,万吨/年1986/1993美国莱昂得尔易位转化271990泰国NPC脱氢11.51991韩国Hyosung脱氢16.51992比利时北海石化脱氢301993马来西亚PP脱氢81994墨西哥PEMEX脱氢351997韩国Tae Kwang脱氢252001马来西亚Petronas脱氢302003西班牙Propan化学脱氢352003美国巴斯夫-阿托菲纳易位转化312003/2004埃及Mas脱氢162004/2005沙特Alfasel脱氢352004/2005沙特NIC脱氢45丙烷脱氢法是高吸热过程,高温和低压有利于在平衡状态下有较高的烯烃浓度。
某些热裂化反应限制了最大的实用温度和压力,副反应与主反应同时发生,并生成某些轻质和重质烃类,它们会以焦炭形式沉积在催化剂上。
丙烷脱氢技术主要有UOP公司Oleflex工艺、罗姆斯公司Catofin工艺、菲利浦斯公司Star工艺、林德公司PDH工艺。
其中,Oleflex工艺和Catofin工艺业已工业化应用。
Oleflex工艺采用催化剂连续再生(CCR)技术,采用铂催化剂(DeH-12)的4台径流式反应器用于丙烷加速脱氢的吸热反应。
丙烯产率为85%,氢气产率为3.6%。
2003年初测算,对于生产35万吨/年聚合级丙烯的Oleflex装置,界区内投资为1.45亿美元,项目总投资2.1亿美元。
生产每吨丙烯的能耗为:电力200 kwh,冷却水50 m3,燃料气(输出)5024 MJ,催化剂和化学品费用14美元。
已有9套装置投运,生产丙烯和异丁烯。
其中4套生产丙烯,另有2套在建设或设计中,这些装置生产丙烯总能力超过130万吨/年。
Catofin工艺采用固定床反应器,按烃类/热空气循环方式操作。
工艺操作温度593-649℃、压力33.9-50.8kPa。
丙烷转化率大于90%。
乌德公司也开发有丙烷或丁烷脱氢工艺,采用蒸汽活化转化(STAR)技术,使用贵金属催化剂。
物耗为1.2吨丙烷或丁烷/吨丙烯或丁烯,能耗为:燃料4.9GJ/t(1.18Gcal/t),冷却水(温升10℃)200m3/t,电力170 kwh/t。
丙烯纯度大于99.7%。
已建有2套丁烷脱氢装置。
荷兰阿姆斯特丹大学开发一项新的丙烷催化氧化脱氢制丙烯工艺,该工艺采用闭合回路催化体系,以利用脱氢生成的氢气作为反应的动力。
开发的基于铈的负载型混合金属氧化物催化剂可在500~700℃反应温度下稳定运行。
工业上烷烃脱氢制烯烃过程在热力学上是不利的,需要消耗能量,而在该闭合回路体系中,能量通过燃烧氢气来提供,并可使反应平衡向生成烯烃的方向移动。
铈基催化剂的开发是关键,因为大多数负载氧化物在较高的反应温度下会熔融。
脱氢反应中纯的氧化铈选择性很低,但可以通过添加其它离子(如钨)来提高。
据称,催化剂Ce0.9W0.1O是一种性能优良的氢气氧化催化剂,结焦率几乎为零,具有良好的热稳定性,选择性大于97%。
经进一步开发之后,该催化体系有可能替代现有的丙烷脱氢技术。
丙烷脱氢装置投资费用相对较高,同时需长期经济地供应丙烷原料。
建设一套规模为30万吨/年装置的投资约需1.19亿美元。
技术改进使丙烷脱氢更为可行,第一代Oleflex装置(泰国10万吨/年装置)投资为1000美元/吨丙烯,西班牙塔拉戈纳装置(35万吨/年)的投资则降低到约650美元/吨丙烯。
脱氢催化剂也不断改进,UOP和乌德公司工艺采用铂基催化剂,鲁姆斯公司工艺采用铬基催化剂。
易位反应技术烯烃易位转化通过过渡金属化合物催化剂使乙烯和丁烯生产丙烯,反应改变碳-碳双键,在室温或接近室温下,甚至在有含水介质存在下,可从起始物料形成新的碳-碳双键。
烯烃易位转化是可逆反应,易位反应可将乙烯与丁烯-2反应生成二个分子的丙烯。
当易位反应与蒸汽裂解相结合时,可将丙烯/乙烯比由蒸汽裂解0.6提高到1.0~1.25。
鲁姆斯公司的Triolefin易位转化工艺(又称烯烃相互转化OCT工艺)在330~400℃下操作,采用钨基催化剂的固定床反应器。
催化剂促使乙烯和丁烯-2转化为丙烯,同时丁烯-1又异构化为丁烯-2。
利用正丁烯易位转化技术,即OCT的变型Automer技术,可用于产出乙烯、丙烯和共聚单体已烯-1。
在Automer技术中,丁烯可产出约10%乙烯、38%丙烯和4%己烯-1,其他为C6+。
据《烃加工》杂志2003年初报道,对于30万吨/年丙烯装置,假定进料中含86%正丁烯,以2000年中期费用为基准,投资费为2050万美元。
生产每千克产品的能耗为:燃料气790 KJ,电力79 kwh,蒸汽(0.3MPa饱和蒸汽)1636 KJ,冷却负荷2041 KJ,氮气0.13 m3。
美国莱昂得尔石化公司切内维尤石化厂已采用OCT技术和乙烯二聚技术,另有其他两套装置也采用相关技术,包括菲利浦斯66公司帕塞迪纳装置。
巴斯夫-菲纳石化合资公司在美国阿瑟港的大型烯烃装置(2001年底投运)将于2003年采用这一技术。
该乙烯装置生产95万吨/年乙烯和54万吨/年丙烯,产出的部分乙烯与丁烯进行易位反应再增产丙烯,可使丙烯产量增加58%(31万吨/年),最终可生产86万吨/年乙烯和86万吨/年丙烯。
易位反应装置可使丙烯/乙烯比提高到1.0以上。
三井化学公司也将首次选用鲁姆斯公司易位转化工艺,使乙烯和丁烯转化为丙烯。
采用这一技术后,可使三井化学公司日本大阪的烯烃装置增产丙烯14万吨/年,使丙烯能力从28万吨/年增加到42万吨/年,该技术将使该装置丙烯/乙烯生产比从0.6增大到大于1.0,以满足亚洲丙烯增长的需求,总投资为3500万美元,定于2004年完成。
上海赛科石化公司90万吨/年石脑油裂解制乙烯装置也将组合采用易位反应烯烃转化装置,将增产丙烯16万吨/年,使丙烯产量达59万吨/年,这将是这一技术在中国的首次应用。
住友化学和壳牌公司将使新加坡石化公司(PCS,裕廊岛)采用易位转化技术增产丙烯。
PCS有二套裂解装置,共生产110万吨/年乙烯和60万吨/年丙烯,采用易位转化技术后,将使丙烯增加20万~30万吨/年,乙烯产能将相应减少。
另外,Automer技术已在中国天津石化公司投入半工业化操作。
IFP-Axens公司的Meta-4易位转化工艺采用移动床反应器,催化剂连续再生。
在30~60℃低温、液相状态下发生反应,采用铼基催化剂,可减少催化剂结垢。
Axens公司通过选择性加氢和Meta-4工艺使低值热解C4馏分或富丁烯物流改质,以生产聚合级丙烯以及富异丁烯物流或MTBE。
当丁二烯市场疲软和丙烯需求强劲时尤为适用。
粗C4物流转化为丙烯和富异丁烯物流通过三个IFP步骤:(1)丁二烯和C4炔烃选择性加氢,及丁烯加氢异构化;(2)蒸馏去除异丁烯或生产MTBE;(3)易位转化(Meta-4)。
CCR Meta-4工艺采用高活性催化剂,催化剂藏量低,操作温度和压力低,液相反应。
丙烯选择性大于98%,丁烯-2总转化率达90%。
据《烃加工》杂志2003年初报道,采用Meta-4工艺生产18万吨/年丙烯,以2002年费用为基准,投资费为1900万美元。
生产每吨丙烯典型的操作费用为18美元。
已有100多套C4加氢装置采用IFP技术,CCR Meta-4技术为IFP与台湾中油公司合作开发,己在台湾省中油公司高雄炼油厂完成中试验证,同类型的移动床、催化剂连续再生技术已在Axens CCR Octanizing 和Aromizing连续重整中得以工业验证。
易位反应技术的缺点是投资费用较高(但低于丙烷脱氢),对原料杂质较为敏感。
另外还存在将高价值乙烯降级生产较低价值丙烯的经济性问题。