轴的机械加工工艺规程设计
设计“输出轴”零件的机械加工工艺规程

设计“输出轴”零件的机械加工工艺规程1. 引言简要介绍输出轴在机械系统中的重要性,以及设计和加工输出轴零件的重要性。
2. 输出轴零件概述零件功能:描述输出轴在机械系统中的作用。
设计要求:列出输出轴的设计参数,如尺寸、材料、强度等。
3. 材料选择材料特性:介绍选择材料的理由,如硬度、耐磨性、成本等。
材料规格:提供材料的具体规格和标准。
4. 加工工艺流程工艺流程图:绘制详细的工艺流程图。
各工序描述:对每一道工序进行详细说明,包括加工方法、设备、工具、参数设置等。
4.1 毛坯准备描述如何从原材料到毛坯的过程,包括切割、锻造或铸造等。
4.2 粗加工车削:介绍粗车削的步骤和参数。
铣削:如果有铣削工序,说明其重要性和参数。
4.3 热处理目的:解释热处理对输出轴性能的影响。
工艺:详细描述热处理的类型和参数。
4.4 精加工车削:精车削的步骤和参数。
磨削:如果需要,介绍磨削工序。
4.5 钻孔和攻丝钻孔:介绍钻孔的步骤和参数。
攻丝:如果有螺纹加工,说明攻丝的步骤和参数。
4.6 表面处理目的:解释表面处理的目的,如防腐蚀、提高耐磨性等。
工艺:描述表面处理的方法,如镀层、喷涂等。
4.7 最终检验检验项目:列出需要检验的项目,如尺寸精度、表面光洁度等。
检验方法:介绍检验的方法和工具。
5. 质量控制质量标准:提供输出轴的质量标准和验收标准。
控制措施:介绍如何保证加工质量,包括过程控制和最终检验。
6. 安全与环保安全措施:介绍在加工过程中的安全措施。
环保要求:说明如何处理加工过程中产生的废弃物,符合环保标准。
7. 成本分析成本构成:分析加工输出轴的成本构成,包括材料、人工、设备折旧等。
成本控制:提出控制成本的策略和方法。
8. 工艺文件和记录工艺文件:列出需要准备的工艺文件,如工艺卡、操作指导书等。
记录和追踪:说明如何记录加工过程和追踪产品质量。
9. 结论总结整个工艺规程的关键点和优势。
10. 参考文献列出编写此工艺规程时参考的文献和资料。
轴类零件机械加工工艺规程及其设计

轴类零件机械加工工艺规程及其设计轴类零件是机械制造中广泛应用的零部件之一,其机械加工工艺规程的设计对于产品的质量和生产效率具有重要的意义。
本文将从轴类零件的加工工艺特点、机械加工工艺规程的设计方法、常见加工工艺及其应用、及加工工艺中的注意事项等方面对轴类零件机械加工工艺规程及其设计进行详细介绍。
一、轴类零件的加工工艺特点轴类零件在机械加工中属于细长杆状物的一类,其加工过程中需要考虑材料的变形、热影响、残余应力等问题,同时也需要考虑其使用过程中所承受的载荷作用,因此对于轴类零件的制造要求十分严格。
其加工工艺特点主要包括以下几点:1.加工工艺要求高精度:轴类零件的尺寸精度要求高,常见的加工公差在0.01mm以下,加工过程中需要采用高精度的机床和刀具、合理的加工参数,严格控制加工误差。
2.加工难度大:由于轴类零件的材料变形大、容易产生撞刀和毛刺,因此在加工过程中需要采用特殊的切削方法和切削工艺,如采用高速切削、切削流线型、刀具较小的切槽等。
3.轴向精度要求高:轴类零件是与轴心对称的,在加工过程中需要控制好轴向误差,以保证其在使用时能够平稳转动。
二、机械加工工艺规程的设计方法机械加工工艺规程的设计是制定出一套完整的工艺措施,通过对产品加工过程中各种工艺因素的控制,实现产品尺寸、结构、性能等方面的要求。
机械加工工艺规程的设计方法主要包括以下几点:1.确定加工工艺目标:在制定工艺规程前,需要明确产品的要求,包括加工精度、表面光洁度、机械性能等方面。
2.制定加工工艺流程:制定加工工艺流程是整个工艺规程中最为关键的一步,需要根据产品的结构和要求,确定各个加工步骤的顺序和方法。
3.确定加工参数:加工参数是指加工过程中需要调整的各种参数,包括切削速度、切削深度、切削力等,这些参数的调整需要根据实际情况进行。
4.选择合适的加工设备和刀具:不同的加工设备和刀具适用于不同的加工需求,因此在制定工艺规程时需要根据产品要求选择合适的加工设备和刀具。
轴的加工工艺规程设计
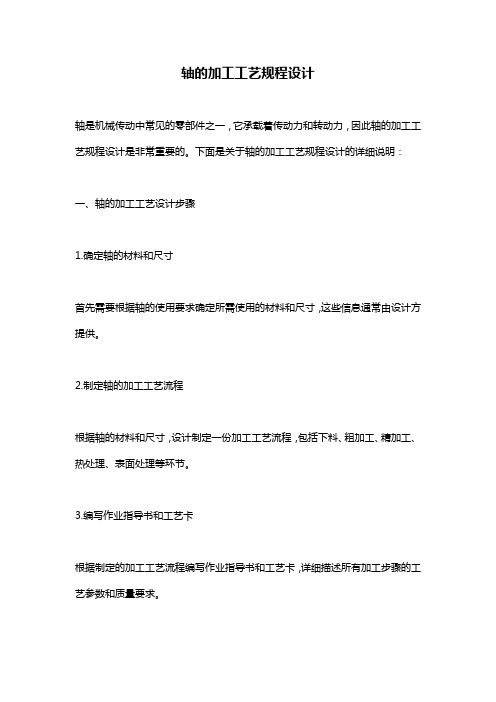
轴的加工工艺规程设计
轴是机械传动中常见的零部件之一,它承载着传动力和转动力,因此轴的加工工艺规程设计是非常重要的。
下面是关于轴的加工工艺规程设计的详细说明:
一、轴的加工工艺设计步骤
1.确定轴的材料和尺寸
首先需要根据轴的使用要求确定所需使用的材料和尺寸,这些信息通常由设计方提供。
2.制定轴的加工工艺流程
根据轴的材料和尺寸,设计制定一份加工工艺流程,包括下料、粗加工、精加工、热处理、表面处理等环节。
3.编写作业指导书和工艺卡
根据制定的加工工艺流程编写作业指导书和工艺卡,详细描述所有加工步骤的工艺参数和质量要求。
4.分配任务和安排生产进度
将加工任务分配给相应的工人和机器,根据作业指导书和工艺卡的要求安排生产进度。
5.进行加工工艺检查和质量控制
在加工过程中,需要对每一个环节进行检查并进行质量控制,确保轴的质量符合要求。
二、轴的加工工艺设计的注意事项
1. 确保轴的材料和尺寸符合设计要求。
2. 制定加工工艺流程时,要考虑到材料的物理性质和机械性能,以及加工工艺对材料的影响。
3. 作业指导书和工艺卡要详细地描述每一个加工步骤,确保工人能够正确地执行加工任务。
4. 在进行热处理和表面处理时,要严格控制温度和时间,以确保轴的性能符合要求。
5. 加工过程中需要进行质量控制,包括尺寸、表面粗糙度、硬度等方面的检查,以确保轴的质量符合要求。
以上是关于轴的加工工艺规程设计的详细说明,希望能帮助您了解轴的加工工艺规程设计的步骤和注意事项。
轴的加工工艺规程设计及夹具设计
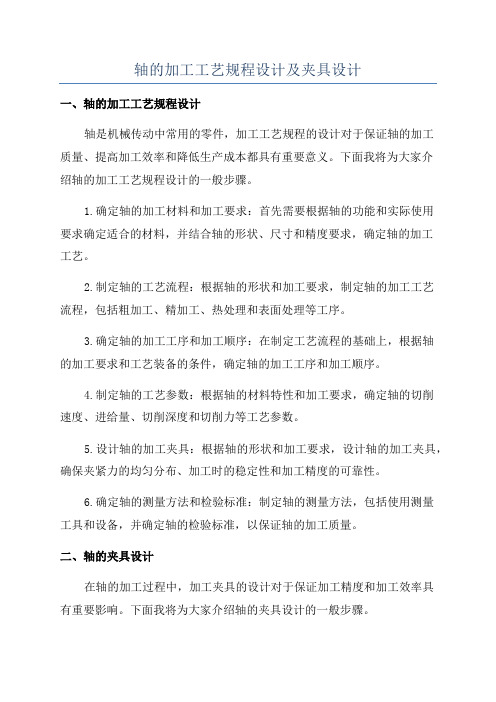
轴的加工工艺规程设计及夹具设计一、轴的加工工艺规程设计轴是机械传动中常用的零件,加工工艺规程的设计对于保证轴的加工质量、提高加工效率和降低生产成本都具有重要意义。
下面我将为大家介绍轴的加工工艺规程设计的一般步骤。
1.确定轴的加工材料和加工要求:首先需要根据轴的功能和实际使用要求确定适合的材料,并结合轴的形状、尺寸和精度要求,确定轴的加工工艺。
2.制定轴的工艺流程:根据轴的形状和加工要求,制定轴的加工工艺流程,包括粗加工、精加工、热处理和表面处理等工序。
3.确定轴的加工工序和加工顺序:在制定工艺流程的基础上,根据轴的加工要求和工艺装备的条件,确定轴的加工工序和加工顺序。
4.制定轴的工艺参数:根据轴的材料特性和加工要求,确定轴的切削速度、进给量、切削深度和切削力等工艺参数。
5.设计轴的加工夹具:根据轴的形状和加工要求,设计轴的加工夹具,确保夹紧力的均匀分布、加工时的稳定性和加工精度的可靠性。
6.确定轴的测量方法和检验标准:制定轴的测量方法,包括使用测量工具和设备,并确定轴的检验标准,以保证轴的加工质量。
二、轴的夹具设计在轴的加工过程中,加工夹具的设计对于保证加工精度和加工效率具有重要影响。
下面我将为大家介绍轴的夹具设计的一般步骤。
1.夹具加工准备:根据轴的形状和加工要求,准备夹具的加工材料和加工工艺,制定夹具的加工流程和工艺参数。
2.夹具的结构设计:根据轴的形状和加工要求,设计夹具的结构,包括夹紧方式、定位方式和支撑方式等,以确保轴在加工过程中的稳定性和精度。
3.夹具的零件设计和加工:根据夹具的结构设计,制定夹具各个零部件的形状、尺寸和精度要求,并进行相应的加工和装配。
4.夹具的调试和试验:对完成的夹具进行调试和试验,测试夹具的夹紧行为和加工精度,确保夹具的正常使用。
5.夹具的安全规程和操作说明书编制:编写夹具的安全规程和操作说明书,包括夹具的使用方法、维护保养和注意事项等,以保证夹具的安全和正常使用。
传动轴的机械加工工艺规程设计

传动轴的机械加工工艺规程设计传动轴是一种用于传递动力和转动力的重要机械零件,它通常由材料加工而成,并且需要通过一系列机械加工工艺来完成。
设计传动轴的机械加工工艺规程是为了确保传动轴的精度和质量,保证其能够正常工作。
1.材料准备:首先需要选择适合的材料,常见的传动轴材料有碳素钢和合金钢。
材料的选择应根据传动轴的使用环境和工作要求来进行,确保传动轴具有足够的强度和硬度。
2.前期准备:在机械加工之前,需要对传动轴进行前期准备工作。
首先,要进行检查和清洁,确保传动轴的表面光滑、无划痕和氧化层。
其次,要对传动轴进行标记,以便加工过程中的定位和跟踪。
3.加工工艺选择:传动轴的机械加工涉及到多个加工过程,如车削、铣削、钻孔、锯断等。
针对不同的加工工艺,需要选择合适的机床和刀具,并确定加工过程中的参数,如刀具的进给速度、切削深度和切削速度等。
4.加工顺序:传动轴的机械加工需要按照一定的顺序进行,以保证加工过程的连贯性和高效性。
通常情况下,可以按照车削、铣削、钻削的顺序进行加工,每个工序之间要进行充分的清洗和检查。
5.检验和修整:传动轴的机械加工完成后,需要进行检验和修整工作。
检验一般包括外观检查和尺寸测量,以确保传动轴的质量和精度。
如果发现问题,需要进行修整和矫正,直到达到要求的尺寸和形状。
6.表面处理:最后,需要对传动轴进行表面处理,以提高其表面硬度和耐磨性。
常用的表面处理方法有热处理、表面喷涂和镀层等,根据传动轴的使用环境和要求来选择合适的处理方法。
综上所述,设计传动轴的机械加工工艺规程是确保传动轴质量和精度的重要步骤。
通过合理的材料选择、加工工艺选择、加工顺序、检验修整和表面处理等步骤,可以确保传动轴能够满足使用要求,并且具有较高的可靠性和耐久性。
轴零件的机械加工工艺规程及夹具设计

轴零件的机械加工工艺规程及夹具设计一、轴零件的机械加工工艺规程1.材料准备:轴零件的材料通常选择优质的钢材或铸铁材料,需要根据轴零件的使用要求和工艺特点来选择合适的材料。
2.工艺路线确定:根据轴零件的形状、结构和加工要求,确定合适的工艺路线,包括车削、铣削、钻孔等加工工序的顺序和方法。
3.加工设备选择:根据轴零件的尺寸、形状和工艺要求,选择合适的加工设备,包括车床、铣床、钻床等。
4.工艺参数确定:根据轴零件的材料和加工要求,确定合适的切削速度、进给量和切削深度等工艺参数。
5.工艺操作规范:对于每个加工工序,制定相应的工艺操作规范,包括操作顺序、刀具安装、夹具装夹和加工顺序等。
6.质量检验要求:确定轴零件的质量检验要求和方法,包括尺寸偏差、表面粗糙度、硬度等指标的检验。
7.工艺文件编制:将以上所有内容整理成工艺文件,包括工艺路线图、刀具配套表、工艺操作规程和质量检验记录表等。
二、夹具设计夹具是机械加工中用来固定工件、定位和保持工件位置的装置。
在轴零件的机械加工中,夹具设计是非常重要的一环。
夹具的设计应满足以下几个要求:1.夹紧可靠:夹具的设计应保证对轴零件进行可靠的夹紧,以防止在加工过程中因工件松动而引起的加工误差。
2.定位准确:夹具的设计应能够确保轴零件在加工过程中的准确定位,以保证加工精度。
3.易于安装和调整:夹具应设计成易于安装和调整的形式,以方便操作人员进行装夹和调整。
4.加工装卸方便:夹具的设计应便于轴零件的装卸,以提高生产效率。
5.避免干涉:夹具的设计应避免与加工刀具和加工设备的干涉,以保证加工进程的顺利进行。
在夹具设计过程中,需要根据轴零件的形状、尺寸和加工要求,选择合适的夹具类型,包括平面夹具、分度夹具、对心夹具等,并进行夹具的结构设计和强度计算。
总结起来,轴零件的机械加工工艺规程及夹具设计是确保轴零件加工质量和工艺正确性的重要环节,对于提高加工效率和保证加工精度具有重要意义。
齿轮轴的机械加工工艺规程设计
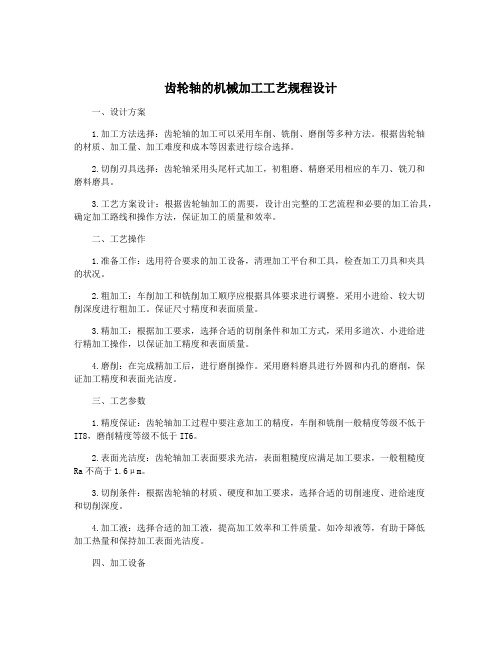
齿轮轴的机械加工工艺规程设计一、设计方案1.加工方法选择:齿轮轴的加工可以采用车削、铣削、磨削等多种方法。
根据齿轮轴的材质、加工量、加工难度和成本等因素进行综合选择。
2.切削刃具选择:齿轮轴采用头尾杆式加工,初粗磨、精磨采用相应的车刀、铣刀和磨料磨具。
3.工艺方案设计:根据齿轮轴加工的需要,设计出完整的工艺流程和必要的加工治具,确定加工路线和操作方法,保证加工的质量和效率。
二、工艺操作1.准备工作:选用符合要求的加工设备,清理加工平台和工具,检查加工刀具和夹具的状况。
2.粗加工:车削加工和铣削加工顺序应根据具体要求进行调整。
采用小进给、较大切削深度进行粗加工。
保证尺寸精度和表面质量。
3.精加工:根据加工要求,选择合适的切削条件和加工方式,采用多道次、小进给进行精加工操作,以保证加工精度和表面质量。
4.磨削:在完成精加工后,进行磨削操作。
采用磨料磨具进行外圆和内孔的磨削,保证加工精度和表面光洁度。
三、工艺参数1.精度保证:齿轮轴加工过程中要注意加工的精度,车削和铣削一般精度等级不低于IT8,磨削精度等级不低于IT6。
2.表面光洁度:齿轮轴加工表面要求光洁,表面粗糙度应满足加工要求,一般粗糙度Ra不高于1.6μm。
3.切削条件:根据齿轮轴的材质、硬度和加工要求,选择合适的切削速度、进给速度和切削深度。
4.加工液:选择合适的加工液,提高加工效率和工件质量。
如冷却液等,有助于降低加工热量和保持加工表面光洁度。
四、加工设备1.车床和铣床:齿轮轴的加工可以采用车床和铣床两种设备。
车床主要用于齿轮轴的轴身加工,铣床主要用于齿轮轴的端面加工。
2.磨床:齿轮轴磨削可以采用内圆磨床、外圆磨床和中心磨床。
内圆磨床主要用于齿轮轴的内孔磨削,外圆磨床主要用于齿轮轴的外圆磨削,中心磨床主要用于齿轮轴的中心孔磨削。
五、工装设计1.夹具设计:齿轮轴加工中,为了保证工件的安全固定,需要设计制作专门的夹具。
夹具的选择与设计应根据加工要求和工件的形状进行综合考虑。
轴的机械加工工艺规程设计
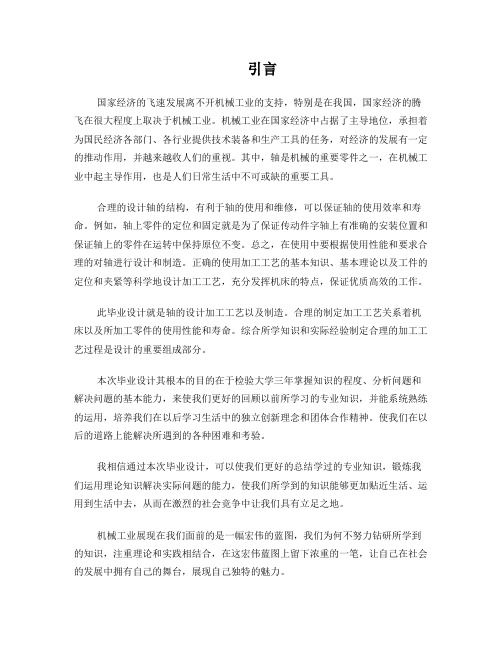
引言国家经济的飞速发展离不开机械工业的支持,特别是在我国,国家经济的腾飞在很大程度上取决于机械工业。
机械工业在国家经济中占据了主导地位,承担着为国民经济各部门、各行业提供技术装备和生产工具的任务,对经济的发展有一定的推动作用,并越来越收人们的重视。
其中,轴是机械的重要零件之一,在机械工业中起主导作用,也是人们日常生活中不可或缺的重要工具。
合理的设计轴的结构,有利于轴的使用和维修,可以保证轴的使用效率和寿命。
例如,轴上零件的定位和固定就是为了保证传动件字轴上有准确的安装位置和保证轴上的零件在运转中保持原位不变。
总之,在使用中要根据使用性能和要求合理的对轴进行设计和制造。
正确的使用加工工艺的基本知识、基本理论以及工件的定位和夹紧等科学地设计加工工艺,充分发挥机床的特点,保证优质高效的工作。
此毕业设计就是轴的设计加工工艺以及制造。
合理的制定加工工艺关系着机床以及所加工零件的使用性能和寿命。
综合所学知识和实际经验制定合理的加工工艺过程是设计的重要组成部分。
本次毕业设计其根本的目的在于检验大学三年掌握知识的程度、分析问题和解决问题的基本能力,来使我们更好的回顾以前所学习的专业知识,并能系统熟练的运用,培养我们在以后学习生活中的独立创新理念和团体合作精神。
使我们在以后的道路上能解决所遇到的各种困难和考验。
我相信通过本次毕业设计,可以使我们更好的总结学过的专业知识,锻炼我们运用理论知识解决实际问题的能力,使我们所学到的知识能够更加贴近生活、运用到生活中去,从而在激烈的社会竞争中让我们具有立足之地。
机械工业展现在我们面前的是一幅宏伟的蓝图,我们为何不努力钻研所学到的知识,注重理论和实践相结合,在这宏伟蓝图上留下浓重的一笔,让自己在社会的发展中拥有自己的舞台,展现自己独特的魅力。
正文一、轴的结构加工工艺性和技术要求轴类零件是机器中经常遇到的典型零件之一,这主要功用是支承回转零件(如:齿轮,蜗轮,带轮,链轮,联轴器等)并传递运动和动力,传递扭矩和承受载荷。
- 1、下载文档前请自行甄别文档内容的完整性,平台不提供额外的编辑、内容补充、找答案等附加服务。
- 2、"仅部分预览"的文档,不可在线预览部分如存在完整性等问题,可反馈申请退款(可完整预览的文档不适用该条件!)。
- 3、如文档侵犯您的权益,请联系客服反馈,我们会尽快为您处理(人工客服工作时间:9:00-18:30)。
课程设计说明书课程名称机械制造工艺学设计课题轴的机械加工工艺规程设计专业机械设计制造及其自动化课程设计任务书机械工程系机械设计制造及其自动化专业课程名称:机械制造工艺学设计题目:轴的机械加工工艺规程设计设计内容:1.产品零件图1张2.毛坯图1张3.机械加工工艺过程综合卡片1份4.机械加工工艺工序卡片1份5.课程设计说明书1份设计要求:大批生产设计(论文)开始日期年月日设计(论文)完成日期年月日指导老师课程设计评语机械工程系机械设计制造及其自动化专业学生姓名苏亚坤班级 B110234 学号 B11023423 课程名称:机械制造工艺学设计题目:轴的机械加工工艺规程设计课程设计篇幅:图纸共 2 张说明书共 19 页指导老师评语:年月日指导老师目录第一章序言 (1)1.1 课题 (1)1.2、设计要求 (2)第二章有关零件的分析 (3)2.1、零件工艺分析 (3)2.2、零件的结构特点 (3)2.3、确定零件毛胚 (4)第三章基准的选择 (5)3.1、有关基准的选择说明 (5)3.1.1、粗基准的选用原则 (5)3.1.2、精基准的选用原则 (5)3.2、确定零件的定位基准 (5)第四章轴类零件的材料、毛坯及热处理 (6)4.1、轴类零件的材料 (6)4.2、轴类毛坯 (6)4.3、轴类零件的热处理 (6)第五章制定加工工艺路线 (7)5.1主轴加工工艺过程分析 (7)5.2、工艺路线的拟定 (7)5.3、加工余量的确定 (8)第六章心得体会 (15)第七章参考文献 (16)第一章序言1.1 课题机械制造工艺课程设计是我们完成本专业教学计划的一个极为重要的实践性教学环节,是使我们综合运用所学过的基本课程,基本知识与基本技能去解决专业范围内的工程技术问题而进行的一次基本训练。
我们在完成课程设计的同时,也培养了我们正确使用技术资料,国家标准,有关手册,图册等工具书,进行设计计算,数据处理,编写技术文件等方面的工作能力,也为我们以后的工作打下坚实的基础,所以我们要认真对待这次综合能力运用的机会!从后面安装的手动定位销轴由于其同心精度要求很高,加工时必须注意其精度。
零件材料: 45钢技术要求:1、φ22gs6、φ25f7 、φ30gs6相互之间的跳动不大于0.08。
3、2xφ8销孔在装配时作。
生产批量:中等批量零件数据:(见零件图)图1 从后面安装的手动定位销轴1.2、设计要求要求编制一个车床主轴零件的机械加工工艺规程,按照老师的设计,并编写设计说明书。
具体内容如下:1、选择毛胚的制造方法,指定毛胚的技术要求。
2、拟定车床主轴的机械加工工艺过程。
3、合理选择各工序的定位定位基准。
4、确定各工序所用的加工设备。
5、确定刀具材料、类型和规定量具的种类。
6、确定一个加工表面的工序余量和总余量。
7、计算一个工件的单件工时。
第二章 有关零件的分析2.1、零件工艺分析图1所示轴属于纯粹的阶梯轴类零件,由圆柱面、砂轮越程槽、端面和倒角组成,该轴共有两组加工表面:1、四段外圆表面和砂轮越程槽;2、两端面和倒角。
由零件图可以看出这两组加工表面没有任何位置度的相互要求,但是表面粗糙度的要求还是比较高的,需要用磨削才能达到要求,所以考虑用粗车-半精车-粗磨-精磨这个加工路线。
其中,左端轴段的配合关系为6722js H φ,轴表面达到6级精度,显然车是不能完成的,而且,与轴套相连的轴段表面粗糙度R a 0.8,所以考虑最后加工方法为磨削。
25φ轴段与法兰的内孔配合关系为6725k H φ的过渡配合,表面粗糙度要求最高R a 0.4,这就必须得经过磨削了。
右端25φ的轴颈与左端有同样的精度要求。
中间6730js H φ的过渡配合为轴与推杆杠杆之间的配合。
最后也需要磨削加工。
两端面的粗糙度R a 3.2,车削即可达到这样的表面粗糙度的要求,而且这两个面与其他的面也没有配合关系,不需要加工的太精确。
2.2、零件的结构特点图1所示零件是从后面安装的手动定位销轴,它属于台阶型轴类零件,由圆柱面、轴肩、退刀槽和销孔等组成。
轴肩一般用来确定安装在轴上零件的轴向位置;销孔用于固定,以保证各零件相互配合。
从图1所示的从后面安装的手动定位销轴的两孔是装配基准,故对装配的两段轴颈的加工提出了很高的要求。
主轴的支撑轴颈、配合轴颈、锥孔、前端圆锥面及端面是轴的主要加工表面。
其中配合端颈本身的尺寸精度、几何形状精度、相互位置精度和表面粗糙度尤为重要。
2.3、确定零件毛胚考虑到零件的经济性和综合性能要求,零件材料为45钢。
综合考虑尺寸具体如下图图2毛坯图第三章基准的选择3.1、有关基准的选择说明3.1.1、粗基准的选用原则1、保证不加工表面与加工表面相互位置要求原则。
当有些不加工表面与加工表面之间有相互位置要求时,一般不选择加工表面作为粗基准。
2、保证各加工表面的加工余量合理分配的原则。
应选择重要加工表面为粗基准。
3.1.2、精基准的选用原则1、基准重合原则。
尽可能使设计基准和定位基准重合,以减少定位误差。
2、基准统一原则。
尽可能使用同一定位基准加工个表面,以保证各表面的位置精度。
如轴类零件常用两端顶尖孔作为统一的定位基准。
3、互为基准原则。
当两个加工表面间的位置精度要求比较高的时候,可用互为基准的原则反复加工。
4、自为基准的原则。
当要求加工余量小而均匀时,可选择加工表面作为自身的定位基准。
3.2、确定零件的定位基准主轴加工中,为了保证各主要表面的相互位置精度,选择定位基准时,应遵循基准重合、基准统一和互为基准等重要原则,并能在一次装夹中尽可能加工出较多的表面。
由于主轴外圆表面的设计基准是主轴轴心线,根据基准重合的原则考虑应选择主轴两端的顶尖孔作为精基准面。
用顶尖孔定位,还能在一次装夹中将许多外圆表面及其端面加工出来,有利于保证加工面间的位置精度。
所以主轴在粗车之前应先加工顶尖孔。
为了保证φ22gs6、φ25f7 、φ30gs6相互之间的跳动不大于0.08。
,宜按互为基准的原则选择基准面。
第四章轴类零件的材料、毛坯及热处理4.1、轴类零件的材料常用45钢,精度较高的轴可选用40Cr、轴承钢GCr15、弹簧钢65Mn,也可选用球墨铸铁;对高速、重载的轴,选用20CrMnTi、20Mn2B、20Cr等低碳合金钢或38CrMoAl氮化钢。
4.2、轴类毛坯常用圆棒料和锻件;大型轴或结构复杂的轴采用铸件。
毛坯经过加热锻造后,可使金属内部纤维组织沿表面均匀分布,获得较高的抗拉、抗弯及抗扭强度。
4.3、轴类零件的热处理锻造毛坯在加工前,均需安排正火或退火处理均,使钢材内部晶粒细化,消除锻造应力,降低材料硬度,改善切削加工性能。
调质一般安排在粗车之后、半精车之前,以获得良好的物理力学性能。
表面淬火一般安排在精加工之前,这样可以纠正因淬火引起的局部变形。
精度要求高的轴,在局部淬火或粗磨之后,还需进行低温时效处理。
第五章制定加工工艺路线5.1主轴加工工艺过程分析车φ25端面及粗车、半精车外圆、钻中心孔、倒角1×45°→车φ22端面、钻中心孔→粗车的各段外圆、倒角φ22端1×45°→半精车各段外圆、车砂轮越程槽→精车φ30端面→粗磨各段、精磨φ25f7及φ30段50mm段外圆→φ8锥孔加工(装配时加工)。
5.2、工艺路线的拟定为保证几何形状、尺寸精度、位置精度及各项技术要求,必须判定合理的工艺路线。
工艺路线5.3、加工余量的确定工艺路线拟定以后,应确定每道工序的加工余量、工序尺寸及其公差。
工序尺寸是工件加工过程中,每个工序加工应保证的尺寸,工序尺寸允许的变动范围就是工序尺寸的公差。
工序尺寸的确定与加工余量有着密切的关系。
零件图上的尺寸和公差就是最终的加工工序尺寸和公差。
将此尺寸加上加工余量就是上一工序的工序尺寸。
1、)0065.0(622±js φ外圆表面。
其尺寸精度为IT6级,表面粗糙度为8.0R a 毛坯为铸件。
工艺路线为粗车-半精车-粗磨-精磨。
由《工艺手册》查得,精磨余量0.1mm ,粗磨余量为0.3mm ,半精车余量为1.1mm ,粗车余量为3.5mm 。
由《机械制造工艺学》公式(4-1)可得加工总余量为:m mZ Z Z Z Z 135.111.13.01.043210=+++=+++=计算各加工工序基本尺寸。
精磨之后工序基本尺寸为mm 22φ;其他各工序工序基本尺寸依次为:粗磨 22mm+0.1mm=22.1mm 半精车 22.1mm+0.3mm=22.4mm 粗车 22.4mm+1.1mm=23.5mm毛坯 23.5mm+11.5mm=33mm确定各工序的加工经济度和表面粗糙度。
由《机械制造工艺学》表4-7查得:精磨后选定为IT6,m R a μ8.0;粗磨后为IT8;m R a μ25.1;半精车后选定为IT11,m R a μ5;粗车之后选定为IT13,m R a μ16。
根据上述加工经济度公差表,将查得的公差数值按“入体原则”标注在工序基本尺寸上。
查《工艺手册》可得铸造毛坯公差为2±mm 。
为清楚起见,把上述计算和查表结果汇总于表2-1中, 表2-1 工序尺寸、公差、表面粗糙度及毛坯尺寸的确定2、两625k φ)(015.0002.0++外圆表面。
其尺寸精度为IT6级,表面粗糙度为4.0R a 毛坯为铸件。
工艺路线为粗车-半精车-粗磨-精磨。
由《工艺手册》查得,精磨余量0.1mm ,粗磨余量为0.3mm ,半精车余量为1.1mm ,粗车余量为4.5mm 。
由《机械制造工艺学》公式(4-1)可得加工总余量为:m mZ Z Z Z Z 65.41.13.01.043210=+++=+++=计算各加工工序基本尺寸。
精磨之后工序基本尺寸为mm 22φ;其他各工序工序基本尺寸依次为:粗磨 25mm+0.1mm=25.1mm 半精车 25.1mm+0.3mm=25.4mm 粗车 25.4mm+1.1mm=26.5mm 毛坯 26.5mm+6.5mm=33mm确定各工序的加工经济度和表面粗糙度。
由《机械制造工艺学》表4-7查得:精磨后选定为IT6,m R a μ4.0;粗磨后为IT8;m R a μ25.1;半精车后选定为IT11,m R a μ5;粗车之后选定为IT13,m R a μ16。
根据上述加工经济度公差表,将查得的公差数值按“入体原则”标注在工序基本尺寸上。
查《工艺手册》可得铸造毛坯公差为2±mm 。
为清楚起见,把上述计算和查表结果汇总于表2-2中,表2-2 工序尺寸、公差、表面粗糙度及毛坯尺寸的确定3、()0065.0630±js φ外圆表面。
其尺寸精度为IT6级,表面粗糙度为8.0R a 毛坯为铸件。
工艺路线为粗车-半精车-粗磨-精磨。