加工中心编程加工流程
数控加工中心编程

千里之行,始于足下。
数控加工中心编程数控加工中心编程是通过编写指令程序,控制数控加工中心实现自动加工的过程。
在进行数控加工中心编程时,需要考虑几个方面的因素,包括数控加工中心的坐标系、工件的具体形状和尺寸以及加工工艺等。
数控加工中心编程的基本步骤如下:1.了解数控加工中心的坐标系:数控加工中心的坐标系包括绝对坐标系和相对坐标系,需要根据实际情况选择合适的坐标系。
2.确定刀具和工件的坐标系:刀具和工件的坐标系有时候可能与数控加工中心的坐标系不同,因此需要先确定刀具和工件在数控加工中心中的坐标系。
3.绘制工件图形:根据工件的形状和尺寸,使用CAD软件或其他绘图软件绘制出工件的几何图形。
4.确定切削路径:根据工艺要求和加工的顺序,确定切削路径,包括走刀路径、刀轨和切入切出点等。
5.选择加工刀具:根据工件的材料和形状,选择合适的刀具,并确定切削参数,如切削速度、进给速度和切削深度等。
6.编写加工程序:根据确定的切削路径和刀具选择,编写数控加工中心的加工程序,包括刀具补偿、速度和进给控制等。
7.仿真和优化:在加工之前,可以使用数控软件进行仿真和优化,检查程序中的错误和潜在问题,并进行必要的修正和优化。
第1页/共3页锲而不舍,金石可镂。
8.上传程序到数控加工中心:将编写好的加工程序上传到数控加工中心,并进行机床的调试和预热工作。
9.加工:进行数控加工中心的加工操作,通过控制系统的指令,实现切削、进给和速度等操作。
10.检验和修正:在加工完成后,对加工件进行检验,检查尺寸和表面质量是否满足工艺要求,如果有问题,及时修正。
在进行数控加工中心编程时,需要注意以下几个方面的问题:1.编程语言:数控加工中心编程常用的语言有G代码和M代码,需要熟悉这两种语言的编写规范和功能。
2.刀具半径补偿:根据不同的刀具,需要进行相应的刀具半径补偿,以保证加工尺寸的准确性。
3.切削参数:不同的工件材料和形状,需要调整不同的切削参数,如切削速度、进给速度和切削深度等。
加工中心编程实例详解
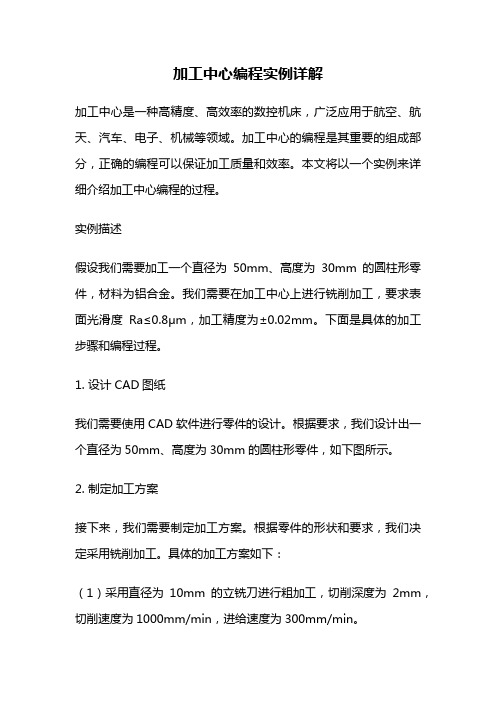
加工中心编程实例详解加工中心是一种高精度、高效率的数控机床,广泛应用于航空、航天、汽车、电子、机械等领域。
加工中心的编程是其重要的组成部分,正确的编程可以保证加工质量和效率。
本文将以一个实例来详细介绍加工中心编程的过程。
实例描述假设我们需要加工一个直径为50mm、高度为30mm的圆柱形零件,材料为铝合金。
我们需要在加工中心上进行铣削加工,要求表面光滑度Ra≤0.8μm,加工精度为±0.02mm。
下面是具体的加工步骤和编程过程。
1. 设计CAD图纸我们需要使用CAD软件进行零件的设计。
根据要求,我们设计出一个直径为50mm、高度为30mm的圆柱形零件,如下图所示。
2. 制定加工方案接下来,我们需要制定加工方案。
根据零件的形状和要求,我们决定采用铣削加工。
具体的加工方案如下:(1)采用直径为10mm的立铣刀进行粗加工,切削深度为2mm,切削速度为1000mm/min,进给速度为300mm/min。
(2)采用直径为6mm的立铣刀进行精加工,切削深度为0.5mm,切削速度为1500mm/min,进给速度为500mm/min。
(3)采用直径为3mm的球头铣刀进行光洁加工,切削深度为0.1mm,切削速度为800mm/min,进给速度为200mm/min。
3. 编写加工程序根据加工方案,我们需要编写相应的加工程序。
加工程序是一段G 代码,用于控制加工中心进行加工。
下面是具体的加工程序:(1)粗加工程序G90 G54 G17 G40 G49 G80M3 S1000G0 X0 Y0 Z30G43 H1 Z2G1 Z28 F300G1 X-25 F1000G1 Y0G1 X25G1 Y25G1 X0G1 Y-25G1 X-25G1 Y0G1 X0G1 Z30M5M30解释:G90:绝对编程模式G54:工件坐标系G17:XY平面选择G40:刀具半径补偿取消G49:刀具长度补偿取消G80:取消模态循环M3:主轴正转S1000:主轴转速1000r/minG0 X0 Y0 Z30:快速移动到起始点G43 H1 Z2:刀具长度补偿,H1表示刀具编号,Z2表示刀具长度G1 Z28 F300:Z轴移动到切削深度,F300表示进给速度G1 X-25 F1000:X轴移动到起始点,F1000表示进给速度G1 Y0:Y轴移动到起始点G1 X25:X轴移动到下一个点G1 Y25:Y轴移动到下一个点G1 X0:X轴移动到下一个点G1 Y-25:Y轴移动到下一个点G1 X-25:X轴移动到下一个点G1 Y0:Y轴移动到下一个点G1 X0:X轴移动到下一个点G1 Z30:Z轴移动到安全高度M5:主轴停止M30:程序结束(2)精加工程序G90 G54 G17 G40 G49 G80 M3 S1500G0 X0 Y0 Z30G43 H2 Z2G1 Z29.5 F500G1 X-22.5 F1500G1 Y0G1 X22.5G1 Y22.5G1 X0G1 Y-22.5G1 X-22.5G1 Y0G1 X0G1 Z30M5M30解释:G90:绝对编程模式G54:工件坐标系G17:XY平面选择G40:刀具半径补偿取消G49:刀具长度补偿取消G80:取消模态循环M3:主轴正转S1500:主轴转速1500r/minG0 X0 Y0 Z30:快速移动到起始点G43 H2 Z2:刀具长度补偿,H2表示刀具编号,Z2表示刀具长度G1 Z29.5 F500:Z轴移动到切削深度,F500表示进给速度G1 X-22.5 F1500:X轴移动到起始点,F1500表示进给速度G1 Y0:Y轴移动到起始点G1 X22.5:X轴移动到下一个点G1 Y22.5:Y轴移动到下一个点G1 X0:X轴移动到下一个点G1 Y-22.5:Y轴移动到下一个点G1 X-22.5:X轴移动到下一个点G1 Y0:Y轴移动到下一个点G1 X0:X轴移动到下一个点G1 Z30:Z轴移动到安全高度M5:主轴停止M30:程序结束(3)光洁加工程序G90 G54 G17 G40 G49 G80M3 S800G0 X0 Y0 Z30G43 H3 Z2G1 Z29.9 F200G1 X-20 F800G3 Y0 I20 J0 F200G3 X0 Y20 I0 J-20G3 Y0 X20 I-20 J0G3 X0 Y-20 I0 J20G3 Y0 X-20 I20 J0G1 X0G1 Z30M5M30解释:G90:绝对编程模式G54:工件坐标系G17:XY平面选择G40:刀具半径补偿取消G49:刀具长度补偿取消G80:取消模态循环M3:主轴正转S800:主轴转速800r/minG0 X0 Y0 Z30:快速移动到起始点G43 H3 Z2:刀具长度补偿,H3表示刀具编号,Z2表示刀具长度G1 Z29.9 F200:Z轴移动到切削深度,F200表示进给速度G1 X-20 F800:X轴移动到起始点,F800表示进给速度G3 Y0 I20 J0 F200:以Y轴为轴心,半径为20mm的圆弧插补,F200表示进给速度G3 X0 Y20 I0 J-20:以X轴为轴心,半径为20mm的圆弧插补G3 Y0 X20 I-20 J0:以Y轴为轴心,半径为20mm的圆弧插补。
加工中心宏程序编程实例

加工中心宏程序编程实例在加工中心的自动化加工过程中,宏程序编程是一项重要的技术。
通过编写宏程序,我们可以实现多道工序的连续加工,提高加工效率和精度。
下面,我将通过一个实例来介绍加工中心宏程序的编程过程。
假设我们需要在一块钢板上进行钻孔、铣削和镗孔三道工序。
首先,我们需要确定加工中心的坐标系和参考点。
假设我们以钢板的左下角为原点,并将钢板的左侧边缘和下侧边缘作为加工中心的X轴和Y轴。
第一道工序是钻孔。
我们假设钻孔的位置为(100, 50),即以加工中心坐标系为基准,钻孔位于距离X轴100mm、距离Y轴50mm的位置。
钻孔的直径为10mm,我们可以使用G81指令来编写钻孔的宏程序。
G90 G54 G00 X100 Y50 ; 将坐标系移动到钻孔位置T01 ; 选择钻头G81 X100 Y50 Z-10 R2 F500 ; 钻孔指令,X、Y为钻孔位置,Z为钻孔深度,R为回退平面,F为进给速度M30 ; 结束程序接下来是铣削工序。
假设铣削的位置为(150, 80),即以加工中心坐标系为基准,铣削位于距离X轴150mm、距离Y轴80mm的位置。
铣削的宽度为20mm,我们可以使用G01指令来编写铣削的宏程序。
G90 G54 G00 X150 Y80 ; 将坐标系移动到铣削位置T02 ; 选择铣刀G01 X170 Y80 Z-5 F1000 ; 铣削进给指令,X、Y为终点位置,Z为下刀深度,F为进给速度G01 X170 Y80 Z-10 ; 铣削下刀指令,Z为下刀深度G01 X150 Y80 Z-10 ; 铣削上刀指令,Z为上刀位置M30 ; 结束程序最后是镗孔工序。
假设镗孔的位置为(200, 100),即以加工中心坐标系为基准,镗孔位于距离X轴200mm、距离Y轴100mm的位置。
镗孔的直径为15mm,我们可以使用G85指令来编写镗孔的宏程序。
G90 G54 G00 X200 Y100 ; 将坐标系移动到镗孔位置T03 ; 选择镗刀G85 X200 Y100 Z-20 R2 F500 ; 镗孔指令,X、Y为镗孔位置,Z为镗孔深度,R为回退平面,F为进给速度M30 ; 结束程序通过以上三段宏程序的编写,我们可以实现钻孔、铣削和镗孔三个工序的连续加工。
加工中心编程操作与实例
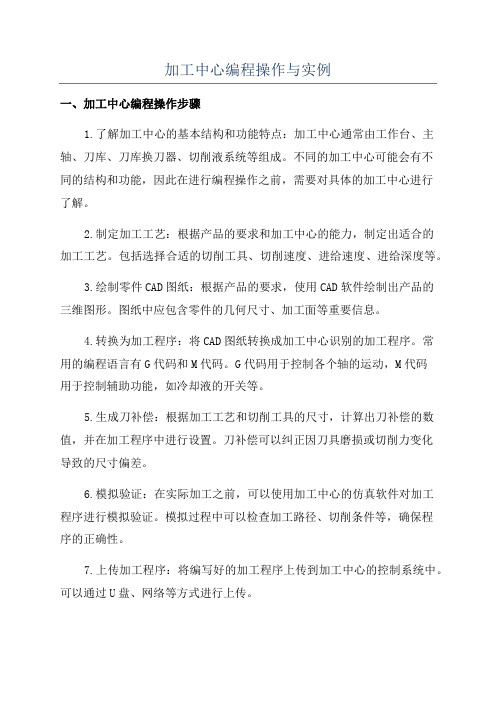
加工中心编程操作与实例一、加工中心编程操作步骤1.了解加工中心的基本结构和功能特点:加工中心通常由工作台、主轴、刀库、刀库换刀器、切削液系统等组成。
不同的加工中心可能会有不同的结构和功能,因此在进行编程操作之前,需要对具体的加工中心进行了解。
2.制定加工工艺:根据产品的要求和加工中心的能力,制定出适合的加工工艺。
包括选择合适的切削工具、切削速度、进给速度、进给深度等。
3.绘制零件CAD图纸:根据产品的要求,使用CAD软件绘制出产品的三维图形。
图纸中应包含零件的几何尺寸、加工面等重要信息。
4.转换为加工程序:将CAD图纸转换成加工中心识别的加工程序。
常用的编程语言有G代码和M代码。
G代码用于控制各个轴的运动,M代码用于控制辅助功能,如冷却液的开关等。
5.生成刀补偿:根据加工工艺和切削工具的尺寸,计算出刀补偿的数值,并在加工程序中进行设置。
刀补偿可以纠正因刀具磨损或切削力变化导致的尺寸偏差。
6.模拟验证:在实际加工之前,可以使用加工中心的仿真软件对加工程序进行模拟验证。
模拟过程中可以检查加工路径、切削条件等,确保程序的正确性。
7.上传加工程序:将编写好的加工程序上传到加工中心的控制系统中。
可以通过U盘、网络等方式进行上传。
8.运行加工程序:在加工中心上选择对应的加工程序,并进行短暂的手动操作,确认加工路径和其他参数均正确无误后,即可启动自动化加工。
二、加工中心编程操作实例1.钻孔加工:假设要对一块工件进行多个孔的钻孔加工。
首先根据孔的尺寸和位置,在CAD软件中绘制相应的图形。
然后将图形转换成加工程序,设置好刀补偿和切削参数。
最后上传程序到加工中心,进行自动化加工。
2.铣削加工:假设要对一块工件进行表面铣削加工。
首先根据工件的形状,在CAD软件中绘制出相应的曲面。
然后将曲面转换成加工程序,设置好刀补偿和切削参数。
最后上传程序到加工中心,进行自动化加工。
3.雕刻加工:假设要在一块工件上进行精细的雕刻加工。
简述加工中心的编程过程

加工中心的编程过程简述加工中心的编程过程是复杂且精细的,它涉及了从产品设计和工艺规划到实际加工操作的整个流程。
以下是这一过程的主要步骤:1. **产品设计和工艺规划**:首先,需要明确产品的设计要求和工艺规划。
这包括确定所需材料、产品尺寸、精度要求等,以及选择合适的加工方法和工具。
2. **加工工艺流程设计**:根据产品特性和要求,设计出详细的加工工艺流程。
这包括确定各道工序的具体内容、顺序、连接方式等。
3. **编程前准备**:在开始编程之前,需要准备好所有必要的工具和数据,如刀具、夹具、切削参数等。
同时,还要了解所用加工中心的控制系统的特性和操作方法。
4. **编写加工程序**:根据加工工艺流程和设备特性,使用特定的编程语言(如G代码)编写加工程序。
这一过程中,需要精确控制刀具路径、切削参数、进给速度等,以保证加工质量和效率。
5. **程序验证和调试**:完成编程后,需要在加工中心上对程序进行验证和调试。
这一步骤至关重要,它不仅可以检查程序的正确性,还可以对可能存在的工艺问题做出调整。
6. **首件加工**:进行首件加工,以进一步检查实际加工效果与预期是否一致。
如果发现问题,需对程序或工艺参数进行调整。
7. **批量加工**:在确保程序和工艺参数无误后,可以开始批量加工。
在加工过程中,需要持续监控产品质量和设备状态,以应对可能出现的问题。
8. **质量检测和后处理**:完成加工后,需对产品进行严格的质量检测,确保其满足设计要求。
如果需要进行表面处理(如抛光、去毛刺等),则还需进行相应的后处理。
9. **总结和优化**:最后,对整个编程和加工过程进行总结,分析其中的不足和问题,持续优化工艺流程和编程方法,以提高加工效率和产品质量。
通过以上步骤,我们可以完成加工中心的编程过程,实现产品的精密制造。
这一过程中,不仅需要丰富的编程和工艺知识,还需要严谨的态度和高度的责任心,以确保产品的质量和生产的顺利进行。
加工中心宏程序编程实例与技巧方法优选文档

加工中心宏程序编程实例与技巧方法优选文档一、编程实例1.实现圆形加工:在加工中心宏程序编程中,圆形加工是比较常见的加工操作。
下面是一个实现圆形加工的编程实例:(1)编程步骤:1)定义圆心坐标和半径;2)使用G90指令将切削模式设置为绝对坐标;3)使用G54指令将工件坐标系设定为程序零点;4)使用G01指令进行直线插补,将刀具移至圆弧起点;5)使用G02或G03指令进行圆弧插补,指定圆心坐标和半径;6)使用M05指令停止主轴转动。
(2)编程样例:```G90G54G01X10Y10G02X20Y10I10J0M05```2.实现孔加工:孔加工是加工中心中常见的操作之一,下面是一个实现孔加工的编程实例:(1)编程步骤:1)定义孔的位置和尺寸;2)使用G90指令将切削模式设置为绝对坐标;3)使用G54指令将工件坐标系设定为程序零点;4)使用G00指令进行快速定位,将刀具移至孔的起始位置;5)使用G01指令进行直线插补,将刀具下移到孔的底部;6)使用G00指令进行快速定位,将刀具抬起。
(2)编程样例:```G90G54G00X20Y20G01Z-10F200G00Z10```二、技巧方法1.合理选择插补指令:在加工中心宏程序编程中,合理选择插补指令可以提高加工效率。
对于直线加工,可以使用G01指令进行直线插补;对于圆弧加工,可以使用G02或G03指令进行圆弧插补。
2.使用子程序:使用子程序可以简化大段的重复代码,在加工中心宏程序编程中尤其有用。
通过使用子程序,可以将常用的加工操作封装为一个子程序,在需要使用时调用即可。
3.合理使用G代码:4.注意安全问题:在加工中心宏程序编程中,安全是最重要的。
编程时应考虑刀具与工件的安全距离,避免发生碰撞等事故。
可以通过设定安全平面、设定限制区域等方式来增加安全性。
总结:加工中心宏程序编程是数控加工的关键环节,掌握加工中心宏程序的编程实例和技巧方法对于提高加工效率和加工精度具有重要意义。
加工中心编程与操作
加工中心编程与操作
一、数控加工中心编程
1、编写程序
数控加工中心程序的编写,是将程序表示成控制程序控制加工中心的程序,以控制加工中心的工作过程。
编程主要要按照加工中心操作手册中的操作方法及要求进行编程,根据不同的加工内容,分析预先确定加工坐标系统,确定工件坐标系和工装坐标系,绘制加工的坐标系,规划加工的路径和坐标系,制定主轴和副轴的选择,选择加工工具,确定转弯,再规定加工的转速,选择通过编程机构控制其转速,完成程序的编写,根据程序的加工步骤将程序编写完成。
2、优化程序
优化加工程序是指在保证加工质量的前提下,尽可能减少加工时间和减少加工费用,以提高加工效率的过程。
常见的优化手段有:缩短加工时间,增加加工质量,减少加工物料,减少加工能耗,减少加工中出现故障的可能性,合理使用机床加工时间,增设机床,合理搭配工具,选择新型加工工艺。
二、数控加工中心操作
1、检查机床
在操作数控加工中心之前,首先要检查机床,检查机床有无损坏,有无漏油,各接口无松动现象,仪表显示正常,进给系统无阻塞等。
2、使用加工刀具
在使用加工刀具之前。
加工中心最详细讲解编程操作实例
加工中心最详细讲解编程操作实例加工中心是一种高效率、高精度的机床,广泛应用于各种金属加工领域。
它能够通过数控系统控制刀具的运动轨迹,实现复杂零件的加工。
在加工中心的编程操作中,常用的编程语言有G代码和M代码。
本文将详细讲解加工中心的编程操作,并给出一个实例。
编程前的准备工作:在编程前,我们需要了解机床的结构和加工工艺要求,还需要获取零件的图纸和加工工艺流程,以便于编写合理的程序。
编写程序的步骤:1.选择编程方式:根据实际情况选择直线插补编程方式或者圆弧插补编程方式。
2.设置坐标系:根据机床的坐标系,设置工件坐标系或者机床坐标系。
3.定义刀具:根据刀具尺寸和刀补,定义刀具的参数和类型。
4.设定工件原点:确定工件坐标系的原点位置,以便于后续运动的参考。
5.运动轨迹描述:根据加工图纸,描述刀具的运动轨迹,包括直线运动和圆弧运动等。
6.切削数据设定:根据加工要求,合理设定切削速度、进给速度和切削深度等参数。
7.编写完整程序:将以上步骤编写成完整的程序,包括G代码和M代码。
编程实例:下面以一个简单的加工任务为例,进行编程操作的详细讲解。
加工任务:在一块正方形工件上加工一个圆形凸起。
1.设置坐标系:假设工件坐标系原点为工件的左下角。
G90G54G17G49G402. 定义刀具:假设使用直径为10mm的铣刀。
T1M6S30003. 设定工件原点:假设工件原点为距离工件底边10mm的位置。
G92X10Y104.运动轨迹描述:以一定的半径和角度,描述刀具的运动轨迹。
G1Z5G3X30Y30I20J205. 切削数据设定:设定切削速度为1000mm/min,进给速度为200mm/min。
F1000F2006.编写完整程序:将以上步骤组合成完整的程序。
%O001(加工程序)G90G54G17T1M6S3000G92X10Y10G1Z5G3X30Y30I20J20G1Z5M30以上就是一个简单的加工中心编程操作的实例。
加工中心外形铣手编程序
加工中心外形铣手编程序1. 简介加工中心是一种多功能的数控机床,能够进行多种加工操作,如铣削、钻孔、镗削等。
外形铣手编程序是指在加工中心上使用铣削刀具对工件外形进行铣削加工的编程操作。
本文将详细介绍加工中心外形铣手编程序的相关知识和步骤,帮助读者了解该编程过程并能够熟练应用。
2. 编程准备在进行加工中心外形铣手编程序之前,需要做好以下准备工作:2.1 确定工件和加工要求首先需要明确待加工的工件和其加工要求,包括工件的形状、尺寸、材料等。
根据工件的要求确定铣削操作的具体参数和路径。
2.2 选择合适的铣削刀具根据工件的要求和加工过程的需要,选择适合的铣削刀具。
刀具的选择需考虑工件材料、切削力、切削速度等因素,以确保加工质量和效率。
2.3 确定坐标系和工件坐标原点在编写铣手程序之前,需要确定工件坐标系和工件坐标原点。
工件坐标系一般选择与工件形状相关的坐标系,以便于编程和加工操作。
2.4 了解加工中心的编程语言和指令不同的加工中心可能使用不同的编程语言和指令,需要事先了解所使用的加工中心的编程语言和指令集,以便正确编写程序。
3. 编程步骤下面将详细介绍加工中心外形铣手编程序的步骤:3.1 设定加工参数首先,设定加工参数,包括切削速度、进给速度、切削深度等。
这些参数需根据工件材料、刀具类型和工件要求进行设定,以确保加工质量和效率。
3.2 坐标系设定根据工件的形状和尺寸,确定工件坐标系和工件坐标原点。
在加工中心上设定好坐标系,并将工件放置在正确的位置上,以确保加工的准确性和一致性。
3.3 轨迹规划根据工件的外形和加工要求,规划铣削路径和切削轨迹。
通过加工中心的编程软件,绘制出工件的轮廓和加工路径,以便于后续的编程操作。
3.4 编写加工程序根据轨迹规划的结果,编写加工程序。
根据加工中心的编程语言和指令集,编写相应的程序代码,包括刀具半径补偿、切削速度、进给速度等参数设定。
3.5 调试程序编写完加工程序后,进行程序的调试和验证。
cnc编程加工流程 (3)
cnc编程加工流程
CNC编程加工流程如下:
1. 设计产品:根据客户需求和产品要求,设计产品的三维模型。
2. 选择加工工艺:根据产品的形状、材料和加工要求,选择合适的加工工艺,如铣削、钻孔、车削等。
3. 编写CNC程序:根据产品的三维模型和加工工艺,编写相应的CNC程序,程序中包含了加工路径、刀具参数、进给速度、切削深度等信息。
4. 导入CNC程序:将编写好的CNC程序导入到CNC控制器中,这可以通过USB或网络连接实现。
5. 选择刀具和夹具:根据加工工艺和刀具路径,选择适合
的刀具和夹具,以确保加工过程中的稳定性和精度。
6. 设置CNC机床:根据产品的尺寸和形状,在CNC机床
上安装和调整刀具、夹具,并进行必要的机床设置,如坐
标原点、工件夹紧等。
7. 开始加工:将工件放置在CNC机床上,并启动加工程序,CNC机床会根据程序中的指令自动控制刀具进行加工。
8. 监控加工过程:在加工过程中,及时监控加工情况,例
如温度、刀具磨损、加工速度等,以确保加工质量和工件
精度。
9. 检验工件:加工完成后,需要对工件进行检验和测量,
以确保加工结果符合要求。
10. 收尾工作:根据加工完工情况,进行必要的清理和保养工作,如清洁机床、更换刀具等。
以上是一般的CNC编程加工流程,具体的加工流程可能会根据不同的产品和加工要求略有差异。
- 1、下载文档前请自行甄别文档内容的完整性,平台不提供额外的编辑、内容补充、找答案等附加服务。
- 2、"仅部分预览"的文档,不可在线预览部分如存在完整性等问题,可反馈申请退款(可完整预览的文档不适用该条件!)。
- 3、如文档侵犯您的权益,请联系客服反馈,我们会尽快为您处理(人工客服工作时间:9:00-18:30)。
1、精度要求高的孔必须钻中心孔,打中心孔钻孔方式用Drll/Cbore,铝合金2.5MM钻深0.7-1MM,不锈钢0.3MM
2、第一次下刀深度:铝合金为下刀深度加1MM,不锈钢为下刀深度加0.3MM
3、通孔必须打穿,贯穿深度等于钻尖长度加0.2MM
各常用钻头钻尖长度(118度钻头)
直径MM
刻字:
进给500mm/min,转速6000转/mm,铝合金刻深0.06mm,电木和波纤板刻深0.2mm
倒角:
1、普通倒角
铝合金除特殊要求全部锐角倒角C0.2, C3以上倒角必须精铣,倒角刀刀尖超出量不得小于0.3MM
2、底座销钉倒角
C0.05,倒角刀刀尖超出量不得小于0.5MM
3、波峰焊倒角
能用15MM则用15MM倒角刀倒角,对于15MM刀倒角倒不到底的采用6.3175MM加工
加工挖槽时:
针对铝合金材料:
1、大于40*40区域采用12MM以上铣刀加工,深度分层不超过5MM每刀,不少于2MM每刀,底部精铣余量0.2MM,采用螺旋或斜线下刀方式,编程结束检查有无直接下刀的区域,避免直插撞机,走不到的地方采用小刀清角,外型或残料加工方式。
钻尖长度MM
1.9
0.6
2.5
0.75
2.9
0.9
3.3
1
3.5
1.05
3.9
1.2
4.2
1.3
4.8
1.45
5.2
1.6
光面:
当加工铝合金材料时,优先采用12MM以上加工,光面厚度不得多于0.2MM;当加工电木和波纤板材料时,采用6.35玉米棒加工,光面厚度不得多于0.5MM,光面超出量为切外型刀具直径加0.5MM
2、区域小于刀具直径1.7倍的区域,采用外型斜线渐降Ramp深度加工,底部光平,渐降高度不得大于刀具最大吃刀量,顺铣优先。
3、底座凸台精度有要求的,单边留余量0.15MM,需要2次装夹的加工余量单边留0.3MM,再用新刀加工到位,凸台不得有锥度,顺铣优先
针对电木材料:
采用6.35MM玉米棒加工,深度分层少于2.5每刀,底面精铣0.2MM,对于侧面有要求的留余量0.2,铣刀光刀位
编制:审批:生效日期:
文件确认部门
总经理
治具市场部
治具制造部
工艺工程部
品质保障部
2、外形尺寸余量每边小于6mm时,4F4MM铣刀加工,深度分层小于0.7每刀,侧面必须精铣,精铣余量不得小于0.15,必须给进退刀,以免直插过切,顺铣优先,以上两点只针对材质好,如材料较软粘刀,可视情况减小进刀量与进给量,小于2MM铝板切外型不用精铣侧面(包括2MM)
针对电木材料:
优先考虑4F6MM铣刀加工,侧面不用精铣,顺铣优先
技术指示
主题
关于加工中心编程操作规范
适用范围
刀具路径的编辑与加工操作
有效期
长期
分发部门
治具制造部、品质保障部、工艺工程部
一、目的:为规范刀路编辑的一致性,保障产品的良好品质,并减少返工率,提高工作效率。
二、操作指引:
加工外形时:
针对铝合金材料:
1、外形尺寸余量每边大于8mm时,优先采用4F6MM铣刀加工,深度分层小于2MM每刀,侧面必须精铣,精铣余量不得小于0.15,必须给进退刀,以免直插过切,顺铣优先。