石灰灯绣球的养法.doc
绣球养护方法及注意事项
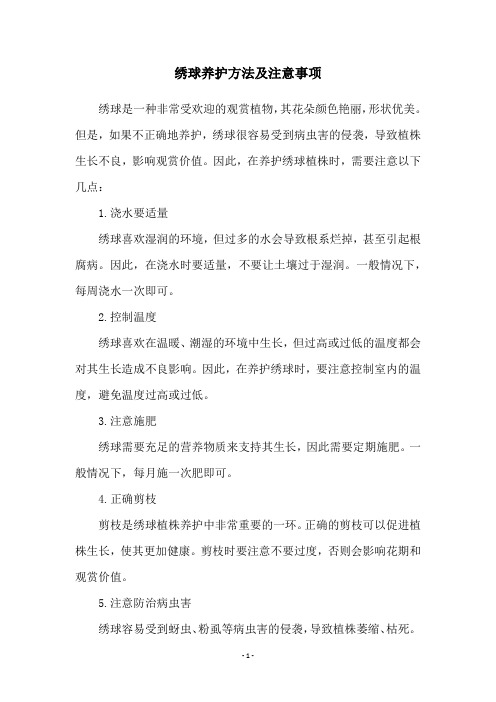
绣球养护方法及注意事项
绣球是一种非常受欢迎的观赏植物,其花朵颜色艳丽,形状优美。
但是,如果不正确地养护,绣球很容易受到病虫害的侵袭,导致植株生长不良,影响观赏价值。
因此,在养护绣球植株时,需要注意以下几点:
1.浇水要适量
绣球喜欢湿润的环境,但过多的水会导致根系烂掉,甚至引起根腐病。
因此,在浇水时要适量,不要让土壤过于湿润。
一般情况下,每周浇水一次即可。
2.控制温度
绣球喜欢在温暖、潮湿的环境中生长,但过高或过低的温度都会对其生长造成不良影响。
因此,在养护绣球时,要注意控制室内的温度,避免温度过高或过低。
3.注意施肥
绣球需要充足的营养物质来支持其生长,因此需要定期施肥。
一般情况下,每月施一次肥即可。
4.正确剪枝
剪枝是绣球植株养护中非常重要的一环。
正确的剪枝可以促进植株生长,使其更加健康。
剪枝时要注意不要过度,否则会影响花期和观赏价值。
5.注意防治病虫害
绣球容易受到蚜虫、粉虱等病虫害的侵袭,导致植株萎缩、枯死。
因此,在养护绣球时,要注意定期检查植株,发现病虫害要及时采取措施进行防治。
综上所述,养护绣球需要注意浇水、控制温度、施肥、剪枝和防治病虫害等方面。
只有正确地养护,才能使绣球生长得更加健康、美丽,成为家庭装饰的一道亮丽风景线。
绣球养殖方法和注意事项室内

绣球养殖方法和注意事项室内绣球(学名:Hydrangea spp.)是一种常见的观赏植物,广泛种植于室内花园和庭院中。
它以其美丽的花朵和多样化的颜色而受到人们喜爱。
本文将介绍绣球的养殖方法和室内注意事项,帮助读者成功培养并欣赏这种迷人的植物。
一、绣球的养殖方法1. 温度和光照:绣球适宜在室内的温暖环境下生长,理想温度为15摄氏度至25摄氏度。
避免暴露到直接阳光下,但要为其提供充足的自然光。
可将绣球放置在明亮通风的位置,如靠近窗户或者阳台。
室内温度过高或过低均会对绣球造成不良影响。
2. 水分管理:绣球对水分的需求较高。
确保土壤始终湿润,但不要积水。
浇水时可以观察土壤表层是否干燥,若是则适当浇水。
更好地给绣球提供水分的方法是将盆底放入水盆中,使其通过底部渗透浸泡到水中。
在盆底加上一层颗粒多孔材料,以保证良好的排水。
3. 土壤选择:绣球适宜生长在富含腐殖质的肥沃土壤中。
可以选择添加少量园艺炭和河沙的泥炭土或腐叶土来改善土壤质地。
同时,添加适当量的有机肥料,如腐熟堆肥或骨粉,以提供植物所需的养分。
4. 剪裁与修剪:绣球是对修剪和剪裁较为敏感的植物。
在春季开始新芽萌发前,可以通过剪短茎干和剪去衰老或虚弱的枝条来促进新梢的生长。
另外,如果希望绣球保持更紧凑、丰满的形态,应定期进行修剪,将过长或无活力的枝条剪去。
二、室内注意事项1. 监控湿度:绣球对湿度较高的环境更为适应,但要避免水汽过多引起真菌和病害的滋生。
可以在花盆周围喷水增加湿度,但要注意不要将水直接喷到花朵和叶片上,以免导致病害。
2. 种植盆与环境:选择较大的盆栽来容纳绣球的根系,以提供足够的空间生长和发展。
绣球适宜生长在通风良好、空气湿润的室内环境中,所以在安放绣球的位置上需要注意室内通风良好,远离空调出风口和暖气等直接热源。
3. 病虫防治:绣球容易受到蚜虫、白粉病和褐斑病等害虫和病菌的侵袭。
定期检查绣球的叶片和茎干,如发现害虫或病斑,应立即采取相应的防治措施。
绣球花的养殖方法和注意事项– 养殖日记
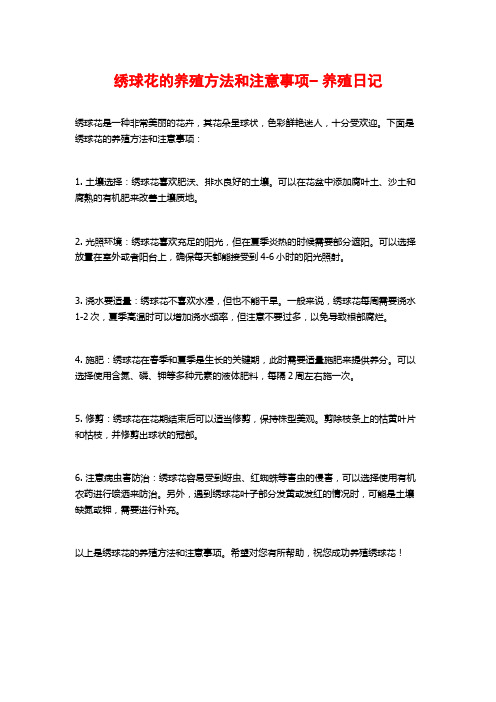
绣球花的养殖方法和注意事项–养殖日记
绣球花是一种非常美丽的花卉,其花朵呈球状,色彩鲜艳迷人,十分受欢迎。
下面是绣球花的养殖方法和注意事项:
1. 土壤选择:绣球花喜欢肥沃、排水良好的土壤。
可以在花盆中添加腐叶土、沙土和腐熟的有机肥来改善土壤质地。
2. 光照环境:绣球花喜欢充足的阳光,但在夏季炎热的时候需要部分遮阳。
可以选择放置在室外或者阳台上,确保每天都能接受到4-6小时的阳光照射。
3. 浇水要适量:绣球花不喜欢水浸,但也不能干旱。
一般来说,绣球花每周需要浇水1-2次,夏季高温时可以增加浇水频率,但注意不要过多,以免导致根部腐烂。
4. 施肥:绣球花在春季和夏季是生长的关键期,此时需要适量施肥来提供养分。
可以选择使用含氮、磷、钾等多种元素的液体肥料,每隔2周左右施一次。
5. 修剪:绣球花在花期结束后可以适当修剪,保持株型美观。
剪除枝条上的枯黄叶片和枯枝,并修剪出球状的冠部。
6. 注意病虫害防治:绣球花容易受到蚜虫、红蜘蛛等害虫的侵害,可以选择使用有机农药进行喷洒来防治。
另外,遇到绣球花叶子部分发黄或发红的情况时,可能是土壤缺氮或钾,需要进行补充。
以上是绣球花的养殖方法和注意事项。
希望对您有所帮助,祝您成功养殖绣球花!。
圆锥绣球石灰灯的养殖方法和注意事项_解释说明

圆锥绣球石灰灯的养殖方法和注意事项解释说明1. 引言1.1 概述引言部分将介绍本篇长文的主题——圆锥绣球石灰灯的养殖方法和注意事项。
圆锥绣球石灰灯是一种美丽且受欢迎的观赏植物,它具有特殊的外观特点和园艺价值。
本文将重点讨论该植物的基本介绍、养殖方法以及常见问题与解决办法。
1.2 文章结构接下来,文章将按照以下结构展开内容:简要概述引言部分,包括文章目的、大纲和章节安排。
1.3 目的本文旨在提供关于圆锥绣球石灰灯养殖方法和注意事项方面全面而实用的指导,帮助读者掌握正确养殖技巧,并解答他们可能遇到的问题。
通过详细阐述适宜环境要求、灯光和温度调控以及水肥管理等关键因素,我们希望读者能够成功地种植和护理这一优雅花卉。
以上是“1. 引言”部分内容的详细清晰描述。
2. 圆锥绣球石灰灯的基本介绍和特点2.1 石灰灯的起源和发展背景石灰灯是一种古老而神秘的园艺植物,起源于中国。
它在千年的文化沉淀中被赋予了很多象征意义,并被广泛运用于庭院景观、婚礼布置等场合。
随着时间的推移,圆锥绣球石灰灯逐渐从传统的手工制作发展到工业化生产阶段,使其养殖更加便捷和广泛。
2.2 圆锥绣球石灰灯的外观特点圆锥绣球石灰灯以其精巧而美丽的外观而受到人们喜爱。
它的整体形态呈现出圆锥形,并长有众多缀满小花朵的枝条。
这些花朵通常呈白色或粉色,配上叶片浓密且垂下,营造出一种浪漫而优雅的氛围。
圆锥绣球石灰灯可根据需要进行修剪和塑造成不同形状,如梅花、金字塔等,以满足不同的园林设计需求。
2.3 石灰灯在园艺中的应用价值圆锥绣球石灰灯作为一种观赏植物,在园艺中有着广泛的应用价值。
首先,它可以作为庭院景观的重要元素,如造景墙、花坛边缘等,增添色彩和层次感。
其次,在婚礼或其他庆典活动中,石灰灯常被用于装饰场地或制作花束、花环等。
此外,石灰灯的花朵可作为干燥花材使用,制成花茶、花香袋等,具有一定的药用和美容功效。
以上是圆锥绣球石灰灯的基本介绍和特点。
通过了解其起源背景、外观特点以及园艺应用价值,可以进一步了解并正确种植这一美丽而神秘的植物。
绣球的养殖方法和注意事项
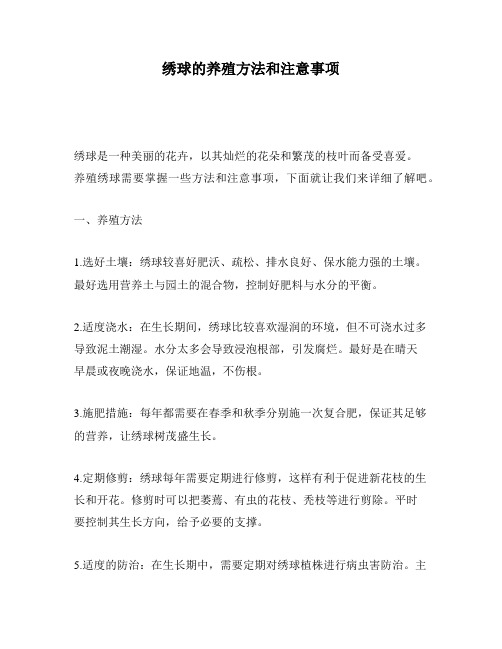
绣球的养殖方法和注意事项绣球是一种美丽的花卉,以其灿烂的花朵和繁茂的枝叶而备受喜爱。
养殖绣球需要掌握一些方法和注意事项,下面就让我们来详细了解吧。
一、养殖方法1.选好土壤:绣球较喜好肥沃、疏松、排水良好、保水能力强的土壤。
最好选用营养土与园土的混合物,控制好肥料与水分的平衡。
2.适度浇水:在生长期间,绣球比较喜欢湿润的环境,但不可浇水过多导致泥土潮湿。
水分太多会导致浸泡根部,引发腐烂。
最好是在晴天早晨或夜晚浇水,保证地温,不伤根。
3.施肥措施:每年都需要在春季和秋季分别施一次复合肥,保证其足够的营养,让绣球树茂盛生长。
4.定期修剪:绣球每年需要定期进行修剪,这样有利于促进新花枝的生长和开花。
修剪时可以把萎蔫、有虫的花枝、秃枝等进行剪除。
平时要控制其生长方向,给予必要的支撑。
5.适度的防治:在生长期中,需要定期对绣球植株进行病虫害防治。
主要步骤包括喷洒杀虫剂,饲料喷洒和清除草屑等。
二、注意事项1. 绣球花比较喜欢在日照强的环境下生长,但不能放在强阳光下直接暴晒,否则极易导致花草枯死。
2. 种植绣球时,应当根据其生长习惯选择合适的种植位置,注意避开地势较低、土壤不良的地方。
如种植在室外,可选在庭院、阳台等合适的地方。
3. 在进行肥料的选购与使用时,应当慎重选择质量优良的复合型有机肥,避免使用化学肥料。
在施肥时也应当掌握适度的施用量,过度施肥会破坏植被所在的生态环境,对它们的成长和生存具有一定的威胁。
4. 养殖绣球要定期除草,松土,保持土壤湿润。
如需要处理有害笼罩物,可将其与叶片、枝条一并剪除并放在一旁含有除草剂的筒袋中,以免影响植物的呼吸。
5. 绣球花期极短,开花时间大约为5-7天,通常需在花期结束后5个月的阶段,将花球小心挖出,经过严格分离,整理后粉质装入喷壶中存放。
在下年春天开花前喷洒在绿化植物上,能够起到一定的推进生长和开花的作用。
绣球的养殖方法和注意事项需要认真学习,掌握得越好,就能获得越好的效果和良好的繁殖,让绣球植被长势旺盛并且开花茂密,丰饶出愈加美好的景观。
石灰灯绣球的栽种方法
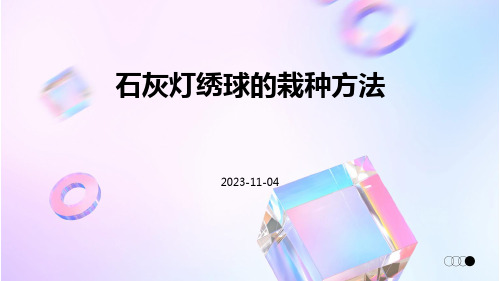
2023-11-04
目 录
• 概述 • 栽种准备 • 栽种步骤 • 养护技巧 • 收获与利用 • 常见问题与解决方案
01
概述
石灰灯绣球简介
石灰灯绣球是绣球花科绣球属的植物,也被称为 “绣球”、“粉团”、“紫阳花”。
它是一种常见的观赏植物,具有美丽的花朵和独 特的形状。
石灰灯绣球原产于中国,但现在在世界各地都有 种植,是一种受欢迎的园林植物。
3. 修剪和整理
03
定期修剪植株,保持其形态美观,同时去除枯叶和残枝,保持
植株健康。
04
养护技巧
浇水与保湿
浇水频率
根据气候和季节调整浇水的频率,保持土壤湿润。在干燥的季节 ,需要增加浇水的次数,而在多雨的季节则要减少浇水的次数。
浇水方式
采用均匀、缓慢的浇水方式,使土壤充分吸收水分。避免一次性 大量浇水,以防止土壤过度浸水。
解决方法
为了解决生长不良的问题,需要提供适宜的生长环境和营养,包括充足的阳光、 水分和肥料。同时,需要注意土壤的质量,定期进行松土和排水,保证石灰灯绣 球的健康生长。
其他常见问题的解决方法
其他问题
石灰灯绣球在生长过程中还可能会遇到其他问题,如干旱、过度浇水等。这些问题会影响石灰灯绣球的生长和 开花。
石灰灯绣球在生长过程中可能会受到病虫害的侵扰,如菌核 病、锈病等。这些病虫害会影响石灰灯绣球的正常生长和开 花。
防治方法
为了预防病虫害的发生,需要定期检查石灰灯绣球的生长情 况,及时发现并采取措施。如果发现病虫害,可以采取药物 治疗或物理治疗的方法进行防治。
生长不良问题的解决方法
生长不良问题
由于环境、气候、土壤等因素的影响,石灰灯绣球可能会出现生长不良的情况, 如植株瘦弱、叶片黄化等。
石灰灯绣球的养殖方法和注意事项
石灰灯绣球的养殖方法和注意事项石灰灯绣球是一种美丽的观赏植物,其花朵色彩丰富,花期长,非常适合在花园或阳台上种植。
然而,要想让石灰灯绣球长得健康美丽,需要掌握一些养殖方法和注意事项。
本文将介绍石灰灯绣球的养殖方法和注意事项,帮助您成功种植这种美丽的植物。
一、石灰灯绣球的养殖方法1.选择合适的土壤和容器石灰灯绣球喜欢生长在疏松、肥沃、排水良好的土壤中,最好选择腐叶土、泥炭土和沙子的混合土壤。
同时,容器也要选择透气性好的,最好在容器底部铺上一层碎石或砂石,以增加排水性。
2.适宜的温度和光照石灰灯绣球喜欢温暖、潮湿的环境,最适合生长的温度为20℃-25℃。
同时,光照也非常重要,石灰灯绣球需要充足的阳光照射,但是要避免强烈的阳光直射。
3.适量浇水和施肥石灰灯绣球需要适量的浇水和施肥,但是要注意不要过多。
一般来说,每周浇水一次即可,施肥也要适量,最好选择含有磷、钾等营养元素的肥料。
4.及时修剪和换盆石灰灯绣球的生长速度比较快,需要及时修剪,以保持良好的形态和健康的生长状态。
同时,也要注意及时换盆,以保证根系的健康和生长。
二、石灰灯绣球的注意事项1.避免过度浇水和过度施肥石灰灯绣球需要适量的浇水和施肥,但是过度浇水和过度施肥会影响其生长和健康。
因此,要注意控制浇水和施肥的量,避免过度。
2.避免强烈的阳光直射石灰灯绣球需要充足的阳光照射,但是要避免强烈的阳光直射,以免烧伤植株。
3.定期清理落叶和杂草石灰灯绣球的生长速度比较快,容易产生落叶和杂草,要定期清理,以保持环境整洁和良好的生长状态。
4.注意防虫害和病害石灰灯绣球容易受到虫害和病害的侵袭,要注意防范。
常见的虫害有蚜虫、粉虱、白蚁等,常见的病害有霉菌病、炭疽病等,要及时采取措施进行防治。
总之,石灰灯绣球是一种非常美丽的观赏植物,但是要想让它长得健康美丽,需要掌握一些养殖方法和注意事项。
希望本文能够帮助您成功种植石灰灯绣球。
石灰灯绣球的养殖方法和注意事项
石灰灯绣球的养殖方法和注意事项
1. 养殖石灰灯绣球时应保证水质清洁,并定期更换水源。
比较适合石灰灯绣球养殖的水参数范围为ph7.8-8,总碱度20-30mg/L,总氯化物4-8mg/L,比重1. 025-1. 035。
2. 养殖石灰灯绣球时应保证水温较高,水温落差应小,一般在22-28度之间,夏季应控制在30度以下,以免发生病症。
3. 食物的选择也要特别注意,建议使用鱼虫颗粒(活或冻)、鱼肝油粒、小浮游生物、液体饲料等;同时可以定期供给新鲜的蔬菜作为补充。
4. 养殖环境应根据石灰灯绣球的生长习性选择,如水草池比较适合养殖,底质要安装土质,以预防池水污染;另外,合理搭配网箱,以防止跑出来。
5. 养殖时也要注意,不要将石灰灯绣球与水质性状不同的鱼种共混养殖,石灰灯绣球与恶性鱼类共混养殖会损害到石灰灯绣球的发育。
圆锥绣球‘石灰灯’种植方法
圆锥绣球‘石灰灯’种植方法
圆锥绣球'石灰灯’种植方法:
1、换盆&土壤:生接地种植。
2、日照:需大于4个小时。
3、施肥:栽种时可混入适量的底肥,此后在4-6月里可将花多多1号和2号轮流灌根用,7月到休眠前可以一周一次花多多1号。
4、浇水:见干见湿。
5、花期:7-10月。
6、修剪:花后修剪可以剪去整体植株的三分之一高度。
7、温度:耐热,耐寒-30℃。
8、习性:多年生木本植物,冬季落叶休眠
石灰灯盆栽的养殖方法和注意事项
石灰灯盆栽的养殖方法和注意事项摘要:石灰灯盆栽是目前成为室内装饰和增添生气的常见植物之一。
它具有生长快、喜光照、易养护等特点,适合各种家居环境。
本文介绍了石灰灯盆栽的养殖方法和注意事项,帮助读者更好地了解和养护这一美丽盆栽。
正文:石灰灯盆栽是一种美丽而受欢迎的室内植物,其小巧玲珑的姿态和色彩缤纷的花朵给人带来了很多欢乐。
在养殖石灰灯盆栽时,我们需要注意以下几个方面:一、土壤与盆栽选择石灰灯盆栽对土壤要求不高,适应性很广。
但最好使用疏松通气、排水性良好的培养土,可将草木灰适量掺入其中,以增加土壤的酸碱度。
对于盆栽的选择,建议选用有透气孔的陶瓷盆或塑料盆。
陶瓷盆具有较好的透气性,能有效调节湿度,而塑料盆则便宜且轻便,适合新手养殖。
二、灯光照明石灰灯盆栽喜欢充足的光照,但并不要求直晒太阳。
因此,放置在室内靠近阳光充足的窗户旁边是个不错的选择。
如果没有足够的自然光照,可以配备适量的照明设备,熄灭时间应适当延长,以避免影响植物的休眠状态。
三、温度和湿度石灰灯盆栽适宜生长的温度范围为15℃-25℃,夏季高温天气需要注意通风降温,并防止强光照射导致水分过快蒸发。
湿度方面,可通过室内加湿器、喷雾或水盘等方式提高植物周围湿度,特别是在室内比较干燥的地方。
四、浇水和施肥石灰灯盆栽喜湿度较高的环境,但切忌盆土过于湿润,以免导致根部腐烂。
适度浇水,保持盆土表面的湿润度即可。
在生长期,每隔7-10天施一次液体肥或叶面喷雾,以保证植物养分的供给。
五、修剪和繁殖石灰灯盆栽生长迅速且具有高的生命力,所以在生长过程中需要适时修剪。
修剪时要注意保留大部分健康枝条,促进新芽的萌发和株形的美观。
此外,石灰灯盆栽还可以通过扦插和分株繁殖,选择健壮的枝条侧截植株或将根茎分成几段用河沙培植,很容易获得新苗。
六、病虫害防治石灰灯盆栽的病虫害相对较少,常见有蚧虫、蜘蛛螨等。
平时要定期检查植株,发现病虫害及时采取针对性的防治措施,如喷洒杀虫剂等。
- 1、下载文档前请自行甄别文档内容的完整性,平台不提供额外的编辑、内容补充、找答案等附加服务。
- 2、"仅部分预览"的文档,不可在线预览部分如存在完整性等问题,可反馈申请退款(可完整预览的文档不适用该条件!)。
- 3、如文档侵犯您的权益,请联系客服反馈,我们会尽快为您处理(人工客服工作时间:9:00-18:30)。
石灰灯绣球的养法
养殖石灰灯绣球时可以将园土、珍珠岩、腐叶土混合配制土壤,之后每年要让它8小时的光照,没有阳光时,可以用光照灯代替阳光照射植株。
石灰灯对肥料的要求不高,生长期每半个月要给它施一次氮肥,平时要注意预防病害。
养殖石灰灯绣球的方法1、配制土壤
石灰灯绣球属于圆锥绣球,它与绣球花最大的区别在于花形不同,它的花形大多呈伞状,而且石灰灯绣球的养法较复杂。
石灰灯绣球喜欢生长在疏松透气的土壤中,因此可以将园土、珍珠岩、腐叶土混合配制土壤。
2、光合作用
石灰灯绣球对光照的需求量较大,很耐旱,养殖时每天要让它接受8小时的光照,夏季温度高时不用给它进行遮阴处理,光照越充足石灰灯植株的长势就越好。
阴雨天没有阳光时,可以用光照灯代替阳光照射石灰灯。
3、施肥方法
养殖石灰灯绣球时要控制好施肥的量,不宜太多也不宜太少,平时不用经常施肥,生长期每半个月要给它施一次氮肥,不要给石灰灯施浓度太高的肥。
施肥前可以先水稀释肥料,这样可以从根源上解决肥害的发生。
4、预防病害
天气温度高湿度大时石灰灯很容易病害,养殖石灰灯时要注意预
防病害,它常见的病害有叶斑病和白粉病,治疗叶斑病可以往叶片上喷洒代森锌可湿性粉剂;治疗白粉病可以往叶片上喷洒粉绣宁粉剂,通常喷3~4次就能有效的缓解病情。