几种脱硫工艺选择
脱硫工艺技术对比

脱硫工艺技术对比脱硫工艺技术是指将燃煤电厂或锅炉排放的硫化物进行减排的技术方法。
目前常见的脱硫工艺技术包括湿法脱硫和干法脱硫两种。
下面将对这两种脱硫工艺技术进行对比。
湿法脱硫是一种利用化学反应将SO2转化为硫酸盐的方法。
这种技术主要包括石灰石石膏法、石灰浆喷雾吸收法和海水脱硫法等。
其中石灰石石膏法是最常用的湿法脱硫技术。
这种方法是将石灰石与SO2气体反应生成硫酸钙,然后再通过过滤的方式分离出硫酸盐。
湿法脱硫技术具有脱硫效率高、操作稳定等优点,但是其缺点是投资大、设备体积大、能耗高。
干法脱硫是一种通过化学吸附或物理吸附的方式将SO2气体去除的技术。
这种技术主要包括活性炭吸附法、电吸附法和干式法等。
其中活性炭吸附法是最常用的干法脱硫技术。
这种方法是将煤炭燃烧产生的SO2经过活性炭吸附,使其转化为硫酸盐。
干法脱硫技术具有投资小、装置简单等优点,但是其缺点是脱硫效率低、处理能力有限。
对比来看,湿法脱硫技术相较于干法脱硫技术在脱硫效率和稳定性上更有优势。
湿法脱硫技术通过化学反应将SO2转化为硫酸盐,脱硫效率可以达到90%以上,而干法脱硫技术的脱硫效率一般在70%左右。
此外,湿法脱硫技术操作相对稳定,适用范围广,可以适应不同燃煤电厂或锅炉的需求。
然而,湿法脱硫技术也存在一些问题。
首先是投资成本高,设备体积大,需要占用较多的空间。
其次是能耗高,需要大量的能源来进行操作。
另外,湿法脱硫技术还会产生大量的废水和废渣,对环境造成一定的污染。
干法脱硫技术相较于湿法脱硫技术在投资成本和能耗方面具有优势。
干法脱硫技术投资成本相对较低,适用于一些投资有限的企业。
同时,干法脱硫技术使用的能源相对较少,节省了能源成本。
然而,干法脱硫技术的脱硫效率相对较低,不能达到湿法脱硫技术的脱硫效果。
此外,干法脱硫技术对煤种的适应性较差,处理能力有限。
因此,在选择脱硫工艺技术时,需要综合考虑各种因素,选择最合适的技术方案。
综上所述,在湿法脱硫技术和干法脱硫技术之间进行对比,可以发现每种技术都有自己的优势和劣势。
脱硫塔工艺流程
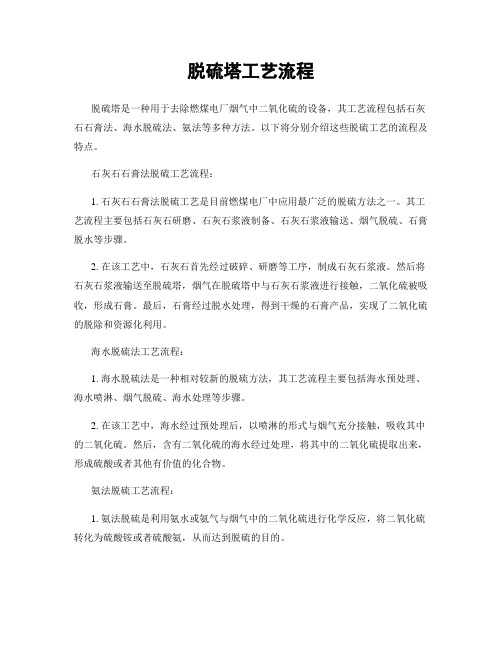
脱硫塔工艺流程脱硫塔是一种用于去除燃煤电厂烟气中二氧化硫的设备,其工艺流程包括石灰石石膏法、海水脱硫法、氨法等多种方法。
以下将分别介绍这些脱硫工艺的流程及特点。
石灰石石膏法脱硫工艺流程:1. 石灰石石膏法脱硫工艺是目前燃煤电厂中应用最广泛的脱硫方法之一。
其工艺流程主要包括石灰石研磨、石灰石浆液制备、石灰石浆液输送、烟气脱硫、石膏脱水等步骤。
2. 在该工艺中,石灰石首先经过破碎、研磨等工序,制成石灰石浆液。
然后将石灰石浆液输送至脱硫塔,烟气在脱硫塔中与石灰石浆液进行接触,二氧化硫被吸收,形成石膏。
最后,石膏经过脱水处理,得到干燥的石膏产品,实现了二氧化硫的脱除和资源化利用。
海水脱硫法工艺流程:1. 海水脱硫法是一种相对较新的脱硫方法,其工艺流程主要包括海水预处理、海水喷淋、烟气脱硫、海水处理等步骤。
2. 在该工艺中,海水经过预处理后,以喷淋的形式与烟气充分接触,吸收其中的二氧化硫。
然后,含有二氧化硫的海水经过处理,将其中的二氧化硫提取出来,形成硫酸或者其他有价值的化合物。
氨法脱硫工艺流程:1. 氨法脱硫是利用氨水或氨气与烟气中的二氧化硫进行化学反应,将二氧化硫转化为硫酸铵或者硫酸氨,从而达到脱硫的目的。
2. 其工艺流程主要包括氨水喷淋、烟气脱硫、氨水处理等步骤。
在该工艺中,氨水以喷淋的形式与烟气接触,吸收其中的二氧化硫,形成硫酸铵或硫酸氨。
然后,含有二氧化硫的氨水经过处理,将其中的硫酸铵或硫酸氨提取出来,实现了二氧化硫的脱除和资源化利用。
综上所述,脱硫塔工艺流程包括石灰石石膏法、海水脱硫法、氨法等多种方法,它们各自具有特点和适用范围。
在实际应用中,需要根据燃料特性、环保要求、成本考虑等因素选择合适的脱硫工艺,以达到高效脱硫、资源化利用的目的。
四种脱硫方法工艺简介

一、石灰石/石灰-石膏法脱硫工艺一)、工作原理石灰石/石灰-石膏法烟气脱硫采用石灰石或石灰作为脱硫吸收剂,石灰石经破碎磨细成粉状与水混合搅拌成吸收浆液,当采用石灰为吸收剂时,石灰粉经消化处理后加水制成吸收剂浆液。
在吸收塔内,吸收浆液与烟气接触混合,烟气中的二氧化硫与浆液中的碳酸钙以及鼓入的氧化空气进行化学反应从而被脱除,最终反应产物为石膏。
二)、反应过程1、吸收SO2+ H2O—>H2SO3SO3+ H2O—>H2SO42、中和CaCO3+ H2SO3—>CaSO3+CO2+ H2OCaCO3+ H2SO4—>CaSO4+CO2+ H2OCaCO3+2HCl—>CaCl2+CO2+ H2OCaCO3+2HF—>CaF2+CO2+ H2O3、氧化2CaSO3+O2—>2 CaSO44、结晶CaSO4+ 2H2O—>CaSO4·2H2O三)、系统组成脱硫系统主要由烟气系统、吸收氧化系统、石灰石/石灰浆液制备系统、副产品处理系统、废水处理系统、公用系统(工艺水、压缩空气、事故浆液罐系统等)、电气控制系统等几部分组成。
四)、工艺流程锅炉/窑炉—>除尘器—>引风机—>吸收塔—>烟囱来自于锅炉或窑炉的烟气经过除尘后在引风机作用下进入吸收塔,吸收塔为逆流喷淋空塔结构,集吸收、氧化功能于一体,上部为吸收区,下部为氧化区,经过除尘后的烟气与吸收塔内的循环浆液逆向接触。
系统一般装3-5台浆液循环泵,每台循环泵对应一层雾化喷淋层。
当只有一台机组运行时或负荷较小时,可以停运1-2层喷淋层,此时系统仍保持较高的液气比,从而可达到所需的脱硫效果。
吸收区上部装二级除雾器,除雾器出口烟气中的游离水份不超过75mg/Nm3。
吸收SO2后的浆液进入循环氧化区,在循环氧化区中,亚硫酸钙被鼓入的空气氧化成石膏晶体。
同时,由吸收剂制备系统向吸收氧化系统供给新鲜的石灰石浆液,用于补充被消耗掉的石灰石,使吸收浆液保持一定的pH值。
脱硫工艺主要有哪几种

炉内添加石灰石,炉内固硫双碱法脱硫海水脱硫等等脱硫技术分类(按相对燃烧过程的位置)燃烧前的脱硫1)煤的洗选(可脱硫30-60%)2)其他原料煤的脱硫技术(化学法,物理法,微波法,生物法。
)3)煤的转化(液化,气化,高纯水煤浆,燃气-蒸汽联合循环[wiki]IGCC[/wiki])4)燃料电池,等离子。
燃烧中脱硫1)型煤2)流化床燃烧: 鼓泡床(BFBC),循环床(CFBC),增压床合循环(PFBC-CC)3)炉内喷钙燃烧后烟气脱硫(FGD)1) 干法烟气脱硫a)炉内喷钙+尾部增湿活化(LIFAC)--下关,钱清,沾化b)旋转喷雾法(SDA)—白马,黄岛c)循环流化床烟气脱硫(CFB-FGD)恒运,漳山,榆社d)增湿灰循环法(NID)--衢州[wiki]化工[/wiki]e)荷电干粉喷射法(CDSI)--德州, 杭钢二热f)其他2)湿法烟气脱硫a) 石灰石/石灰—抛弃/石膏法—珞璜,太原。
b) 海水法—深圳西,后石c) 氨法—内江d) 镁法---e) 磷氨法—豆坝f) 其他3)其他脱硫法(同时脱硫和脱硝)a) 电子束—成都b) 脉冲电晕c)活性炭(3)烟气的预冷却大多数含硫烟气的温度为120~185℃或更高,而吸收操作则要求在较低的温度下(60℃左右)进行。
低温有利于吸收,高温有利于解吸。
因而在进行吸收之前要对烟气进行预冷却。
通常,将烟气冷却到60℃左右较为适宜。
常用冷却烟气的方法有:应用热交换器间接冷却;应用直接增湿(直接喷淋水)冷却;用预洗涤塔除尘增湿降温,这些都是较好的方法,也是目前使用较广泛的方法。
通常,国外湿法烟气脱硫的效率较高,其原因之一就是对高温烟气进行增湿降温。
我国目前已开发的湿法烟气脱硫技术,尤其是燃煤工业锅炉及窑炉烟气脱硫技术,高温烟气未经增湿降温直接进行吸收操作,较高的吸收操作温度,使SO2的吸收效率降低,这就是目前我国燃煤工业锅炉湿法烟气脱硫效率较低的主要原因之一。
(4)结垢和堵塞在湿法烟气脱硫中,设备常常发生结垢和堵塞。
目前广泛使用的5种脱硫工艺技术方案简介

目前广泛使用的5种脱硫工艺技术方案简介目录目前广泛使用的5种脱硫工艺技术方案简介 (1)1、湿法烟气脱硫工艺 (1)2、半干法烟气脱硫工艺 (3)3、烟气循环流化床脱硫工艺 (4)4、干法脱硫工艺 (5)5、NID半干法烟气脱硫 (6)目前世界上燃煤电厂烟气脱硫工艺方法很多,这些方法的应用主要取决于锅炉容量和调峰要求、燃烧设备的类型、燃料的种类和含硫量的多少、脱硫率、脱硫剂的供应条件及电厂的地理条件、副产品的利用等因素。
近年来,我国电力工业部门在烟气脱硫技术引进工作方面加大了力度,对目前世界上电厂锅炉较广泛采用的脱硫工艺都有成功运行工程,主要有湿法烟气脱硫、干法烟气脱硫和半干法烟气脱硫。
现将目前应用较为广泛的几种脱硫工艺原理、特点及其应用状况简要说明如下:1、湿法烟气脱硫工艺湿法烟气脱硫包括石灰石/石灰-石膏法烟气脱硫、海水烟气脱硫和用钠基、镁基、氨作吸收剂,一般用于小型电厂和工业锅炉。
氨洗涤法可达很高的脱硫效率,副产物硫酸铵和硝酸铵是可出售的化肥。
以海水为吸收剂的工艺具有结构简单、不用投加化学品、投资小和运行费用低等特点。
而以石灰石/石灰-石膏法湿法烟气脱硫应用最广。
《石灰石/石灰-石膏法烟气脱硫工程设计规范》中关于湿法烟气脱硫工艺的选择原则为:燃用含硫量Sar≥2%煤的机组或大容量机组(200MW及以上)的电厂锅炉建设烟气脱硫装置时,宜优先采用石灰石-石膏湿法脱硫工艺,脱硫率应保证在96%以上。
湿法烟气脱硫工艺采用碱性浆液或溶液作吸收剂,其中石灰石/石灰-石膏湿法脱硫是目前世界上技术最成熟、应用最广,运行最可靠的脱硫工艺方法,石灰石经破碎磨细成粉状与水混合搅拌制成吸收剂浆液;也可以将石灰石直接湿磨成石灰石浆液。
石灰石或石灰浆液在吸收塔内,与烟气接触混合,烟气中的SO2与浆液中的碳酸钙以及鼓入的氧化空气进行化学反应,最终反应产物为石膏,经脱水装置脱水后可抛弃,也可以石膏形式回收。
由于吸收剂浆液的循环利用,脱硫吸收剂的利用率很高。
脱硫脱硝工艺简介
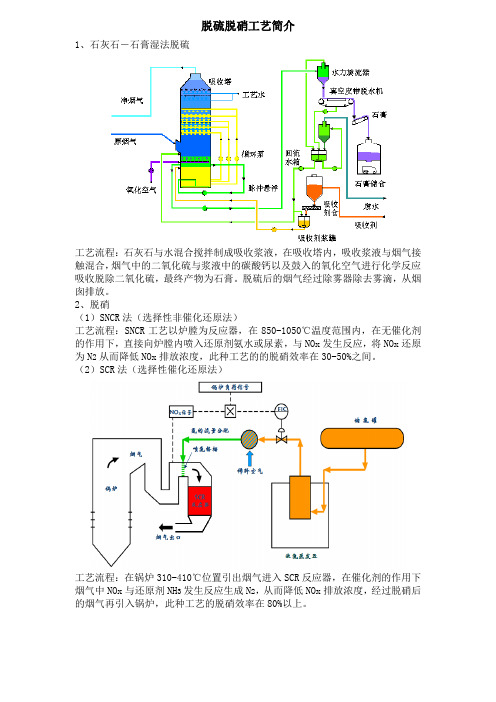
脱硫脱硝工艺简介
1、石灰石-石膏湿法脱硫
工艺流程:石灰石与水混合搅拌制成吸收浆液,在吸收塔内,吸收浆液与烟气接触混合,烟气中的二氧化硫与浆液中的碳酸钙以及鼓入的氧化空气进行化学反应吸收脱除二氧化硫,最终产物为石膏。
脱硫后的烟气经过除雾器除去雾滴,从烟囱排放。
2、脱硝
(1)SNCR法(选择性非催化还原法)
工艺流程:SNCR工艺以炉膛为反应器,在850-1050℃温度范围内,在无催化剂的作用下,直接向炉膛内喷入还原剂氨水或尿素,与NOx发生反应,将NOx还原为N2从而降低NOx排放浓度,此种工艺的的脱硝效率在30-50%之间。
(2)SCR法(选择性催化还原法)
工艺流程:在锅炉310-410℃位置引出烟气进入SCR反应器,在催化剂的作用下烟气中NOx与还原剂NH3发生反应生成N2,从而降低NOx排放浓度,经过脱硝后的烟气再引入锅炉,此种工艺的脱硝效率在80%以上。
四种脱硫方法工艺处理概述
四种脱硫方法工艺处理概述脱硫是指将煤中的硫化物转化为气体、溶液或固体形式,减少燃煤过程中产生的大气污染物。
目前,常见的脱硫方法工艺主要有湿法烟气脱硫、干法烟气脱硫、等离子体脱硫和生物脱硫四种。
湿法烟气脱硫是目前最常用的工艺,其主要原理是将炉内烟气与脱硫剂进行接触反应。
常见的湿法脱硫工艺包括喷雾吸收法、石膏法和氧化吸收法。
喷雾吸收法利用喷雾剂将脱硫剂喷入烟气中,通过物理吸收和化学反应将SO₂吸收到脱硫剂中,然后与其它气体成分一起排出。
石膏法是将石膏作为脱硫剂,将煤燃烧后生成的SO₂和石膏中的CaCO₃反应生成CaSO₄沉淀物。
氧化吸收法是将硫化物氧化为SO₂,然后利用脱硫剂将SO₂吸收并转化为不溶性的化合物。
湿法脱硫工艺具有脱硫效率高、适应能力强和废渣可利用的特点。
干法烟气脱硫是一种将烟气与固体脱硫剂进行接触反应的方法。
干法脱硫工艺通常包括活性炭吸附法、干碱法和氨喷射法。
活性炭吸附法是利用活性炭吸附烟气中的SO₂,然后再经过再生处理使其重新可用。
干碱法是将碱性物质(如氢氧化钠、氢氧化钙等)与SO₂发生反应生成不溶性的硫酸钠或硫酸钙。
氨喷射法是将氨气喷射到烟气中与SO₂反应生成硫酸铵或铵化物,然后与除尘设备中的降氮剂一起脱除。
干法脱硫工艺具有脱硫效率高、废渣排放量小和设备结构简单的优点。
等离子体脱硫是一种利用等离子体技术将烟气中的SO₂转化为不溶性的化合物。
等离子体脱硫工艺基于等离子体技术,通过电离氧化反应将SO2转化为SO3,然后与脱硫剂发生反应生成硫酸盐。
等离子体脱硫工艺具有脱硫效率高、能耗低和产物易处理等优势,但目前尚未在工业应用中广泛推广。
生物脱硫是一种利用生物菌群将煤中的硫化物转化为不溶性的化合物的方法。
生物脱硫工艺主要有细菌脱硫法和微生物脱硫法两种。
细菌脱硫法是通过培养一定的脱硫菌群,使其转化煤中的硫化物为不溶性硫化物。
微生物脱硫法是通过采集和培养天然微生物来进行脱硫,利用其代谢产物将SO₂转化为硫酸盐。
煤化工(焦化厂)焦炉煤气6大脱硫技术详解与脱硫工艺选择
煤化工(焦化厂)焦炉煤气6大脱硫技术详解与脱硫工艺选择1、焦炉煤气脱硫技术焦炉煤气常用的脱硫方法从脱硫剂的形态上来分:包括干法脱硫技术和湿法脱硫技术。
1.1焦炉煤气干法脱硫技术干法脱硫工艺是利用固体吸收剂脱除煤气中的硫化氢,同时脱除氰化物及焦油雾等杂质。
干法脱硫又分为中温脱硫、低温脱硫和高温脱硫。
常用脱硫剂有铁系和锌系,氧化铁脱硫剂是一种传统的气体净化材料,适宜于对天然气、油气伴生气、城市煤气以及废气中硫化氢含量高的气体。
常温氧化铁脱硫原理是用水合氧化铁(Fe2O3·H2O)脱除H2S,其反应包括脱硫反应与再生反应。
干法脱硫工艺多采用固定床原理,工艺简单,净化率高,操作简单可靠,脱硫精度高,但处理量小,适用于低含硫气体的处理,一般多用于二次精脱硫。
但由于气固吸附反应速度较慢,工艺运行所需设备一般比较庞大,而且脱硫剂不易再生,运行费用增高,劳动强度大,不能回收成品硫,废脱硫剂、废气、废水严重污染环境。
1.2焦炉煤气湿法脱硫技术湿法工艺是利用液体脱硫剂脱除煤气中的硫化氢和氰化氢。
常用的方法有氨水法、单乙醇胺法、砷碱法、VASC脱硫法、改良 ADA法、TH 法、苦味酸法、对苯二酚法、HPF 法以及一些新兴的工艺方法等。
1.2.1 氨水法(AS法):氨水法脱硫是利用焦炉煤气中的氨,在脱硫塔顶喷洒氨水溶液(利用洗氨溶液)吸收煤气中 H2S,富含 H2S 和 NH3的液体经脱酸蒸氨后再循环洗氨脱硫。
在脱硫塔内发生的氨水与硫化氢的反应是:H2S+2NH3·H2O →(NH4)2S+2H2O。
AS 循环脱硫工艺为粗脱硫,操作费用低,脱硫效率在 90 %以上,脱硫后煤气中的 H2S 在200~500 mg·m-3。
1.2.2 VASC法:VASC法脱硫过程是洗苯塔后的煤气进入脱硫塔,塔内填充聚丙烯填料,煤气自下而上流经各填料段与碳酸钾溶液逆流接触,再经塔顶捕雾器出塔。
煤气中的大部分 H2S 和 HCN 和部分 CO2被碱液吸收,碱液一般主要是 Na2CO3或 K2CO3溶液。
脱硫工艺的方法
脱硫工艺的方法脱硫是指将含有二氧化硫(SO2)的气体或液体中的硫化物去除的过程。
脱硫工艺的方法主要有物理方法和化学方法两大类。
下面将详细介绍几种常见的脱硫工艺方法。
一、湿法脱硫1.石灰石湿法脱硫:石灰石湿法脱硫是目前最常用的脱硫工艺方法之一。
在该方法中,二氧化硫气体与石灰石(CaCO3)中的钙氢碳酸盐反应生成硫酸钙(CaSO4)。
该方法具有脱硫效率高、可靠性好、成本较低等优点,但生成的硫酸钙需要处理和处置,产生的废水也需要处理。
2.浆液石灰石湿法脱硫:与石灰石湿法脱硫类似,浆液石灰石湿法脱硫也是利用石灰石与二氧化硫反应生成硫酸钙。
不同之处在于,石灰石不是以固体形式添加,而是以悬浮液形式添加到反应器中,使反应速率更高。
3.浆液法脱硫:浆液法脱硫是将石灰石(CaCO3)与二氧化硫气体反应生成石膏(CaSO4·2H2O)的一种方法。
该方法具有反应速度快、有效去除二氧化硫等优点,但产生的废水中含有石膏,需要处理。
二、半干法脱硫半干法脱硫是湿法脱硫与干法脱硫的组合,具有湿法脱硫的高脱硫效率和干法脱硫的低能耗特点。
该方法主要是利用气体与悬浮在气流中的碱性物质反应,生成硫酸盐或硫化盐,然后通过过滤或吸附等方法将反应产物与气体分离。
半干法脱硫可以适用于高硫煤的脱硫,是一种相对环保且经济的脱硫工艺方法。
三、干法脱硫干法脱硫是指在无水条件下进行的脱硫方法。
干法脱硫一般适用于低浓度的二氧化硫气体的处理。
干法脱硫的主要方法有:1.流化床脱硫:流化床脱硫是将石灰石或其他碱性物质和二氧化硫气体一起送入反应器,当气体通过床层时,二氧化硫与碱性物质反应生成硫酸盐或硫化物,从而达到脱硫的目的。
这种方法具有去除二氧化硫的效率高、设备结构简单等优点。
2.干燥吸附剂脱硫:干燥吸附剂脱硫是使用干燥的固体吸附剂来吸收排放气体中的二氧化硫。
常用的吸附剂有活性炭、硅胶、氧化铁等。
该方法具有脱硫效率高、处理设备简单且易于操作等优点。
四、生物脱硫生物脱硫是近年来发展起来的一种新型脱硫方法。
煤化工中各种脱硫工艺比较
一、煤化工中各种脱硫工艺比较1、AS煤气净化工艺AS流程就是以煤气中自身的NH3。
为碱源,吸收煤气中的H2S,吸收了NH3。
和H2S的富液到脱酸蒸氨工段,解析出NH3。
和H2S气体,贫液返回洗涤工段循环使用,氨气送氨分解炉生产低热值煤气后返回吸煤气管线,酸气送克劳斯焚烧炉生产硫磺。
优点:环保效果好、工艺流程短、脱硫效率高、煤气中的氨得到充分利用、加碱效果明显、热能利用高缺点:洗氨塔后煤气含氨量高、洗液温度对脱硫影响较大、富液含焦油粉尘高、硫回收系统易堵塞(克劳斯焚烧炉生产硫磺)2、低温甲醇洗(Rectisol,音译为勒克梯索尔法)低温甲醇洗与NHD法都属于物理吸收法,可以脱硫和脱碳。
低温甲醇洗所选择的洗涤剂是甲醇,在温度低于273 K下操作,因为甲醇的吸收能力在温度降低的情况下会大幅度地增加,并能保持洗涤剂损失量最少。
低温甲醇洗适合于分离和脱除酸性气体组分CO2、H2S及COS,因为这些组分在甲醇中具有不同的溶解度,而这种选择性能得到无硫的尾气。
例如有尿素合成工序的话,如果遵守环境保护规则,就可以直接排人大气或用于生产CO2。
低温甲醇洗在大型化装置中的生产业绩、工艺气的净化指标、溶剂损耗、消耗和能耗、CO2产品质量有其优势.3、NHD法脱硫NHD化学名为聚乙二醇二甲醚是一种新型高效物理吸收溶剂。
NHD法脱硫原理:NHD法脱硫过程具有典型的物理吸收特征。
H2S、CO2在NHD中溶解度较好的服从亨利定律,它们岁压力升高、温度降低而增大。
因此宜在高压、低温下进行H2S和CO2的吸收过程,当系统压力降低、温度升高时,溶液中溶解的气体释放出来,实现溶剂的再生过程。
NHD法脱硫工艺特点:能选择性吸收H2S、CO2、COS且吸收能力强;溶剂具有良好的化学稳定性和热稳定性;NHD不起泡,不需要消泡剂;溶剂腐蚀性小;溶剂的蒸汽压极低,挥发损失低;NHD工艺不需添加活化剂,因此流程短。
4、PDS法脱硫(PDS催化剂)原理:煤气依次进入2台串联的脱硫塔底部,与塔顶喷淋的脱硫液逆向接触,脱除煤气中的大部分H2S。
- 1、下载文档前请自行甄别文档内容的完整性,平台不提供额外的编辑、内容补充、找答案等附加服务。
- 2、"仅部分预览"的文档,不可在线预览部分如存在完整性等问题,可反馈申请退款(可完整预览的文档不适用该条件!)。
- 3、如文档侵犯您的权益,请联系客服反馈,我们会尽快为您处理(人工客服工作时间:9:00-18:30)。
1脱硫工艺的选择目前国外脱硫技术已有多种,而应用较为广泛的主要有:湿式石灰石/石膏法、烟气循环流化床法、新型一体化脱硫(NID)工艺、旋转喷雾半干法、炉内喷钙-尾部加湿活化法等。
国内目前通过引进技术、合资以及自行开发已基本掌握了以上几种脱硫技术,并使这几种脱硫技术在国内不同容量机组上均有应用。
1.1 湿式石灰石/石膏法湿式石灰石/石膏法其工艺特点是采用石灰石浆液作为脱硫剂,经吸收、氧化和除雾等处理过程,形成副产品石膏。
其工艺成熟、适用于不同容量的机组,应用范围最广,脱硫剂利用充分,脱硫效率可达90%以上。
并且脱硫剂来源丰富,价格较低,副产品石膏利用前景较好。
其不足之处是系统比较复杂,占地面积大,初投资及厂用电较高,一般需进行废水处理。
该法是目前世界上技术最为成熟、应用最广的脱硫工艺,特别在美国、德国和日本,应用该工艺的机组容量约占电站脱硫装机总容量的80%以上,应用的单机容量已达1000MW。
在国内已有珞璜电厂一、二期300MW机组及北京一热、重庆电厂和浙江半山电厂三个分别相当于300MW脱硫容量的机组使用。
引进技术国内脱硫工程公司总承包完成的北京石景山热电厂、太原第二热电厂五期、贵州安顺(300MW)电厂、广东台山电厂(600MW)、河北定州电厂(600MW)等也均已投入运行。
且国内有近20台600MW机组湿法脱硫正在实施中。
其基本原理与系统图如下:1.2 烟气循环流化床干法烟气循环流化床干法脱硫(CFB-FGD)技术是世界著名环保公司德国鲁奇·能捷斯·比肖夫(LLB)公司开发的世界先进水平的循环流化床干法烟气脱硫技术。
CFB-FGD是目前干法脱硫技术商业应用中单塔处理能力较大、脱硫综合效益较为优越的一种方法。
该工艺已经先后在德国、奥地利、波兰、捷克、美国、爱尔兰等国家得到广泛应用,最大已运行单机、单塔机组容量为300MW,采用该技术设计的单塔处理烟气量可达到2800000Nm3/h。
目前LLB公司的CFB-FGD技术的应用业绩达32台套,投入运行的CFB-FGD中其最高设计脱硫效率为99.7%。
该技术已由福建龙净环保科技公司引进,并实施于华能榆社电厂二期2×300MW燃煤机组上(煤种含硫量1.2%),且于2004年11月投入运行,实际脱硫效率不低于90%。
此外,山东三融环保有限责任公司、国华荏原环境工程有限责任公司也引进了该项技术。
德国的Wulff公司在该技术基础上开发了回流式循环流化床(RCFB-FGD)烟气脱硫工艺。
RCFB-FGD与CFB-FGD相比,在脱硫吸收塔上部出口区域布置了回流装置,旨在造成烟气流中固体颗粒的回流。
通过这种方式,固体颗粒在塔内的停留时间获得了延长,同时改进了气固间的混合。
此外,新开发的RCFB脱硫装置还在吸收塔底部装有紊流装置,这也强化了气固间的混合。
因此,RCFB-FGD除了具有CFB-FGD优良的传热、传质特点外,还提高了脱硫剂的利用率和脱硫效率。
由于塔内部无检修件,烟气循环流化床脱硫系统停运时,吸收塔可以直接作为旁路烟道使用。
德国WULFF公司最大单塔业绩为奥地利Theiss2000(EVN)电厂300MW机组RCFB脱硫装置,烟气量1,000,000 Nm3/h,烟气温度160~180℃,负荷变化范围45~100%。
武汉凯迪电力股份公司引进德国WULFF公司RCFB-FGD技术,应用于广州恒运210MW机组烟气脱硫工程,该项目已通过广州环保局的验收。
另外,山西漳山发电有限责任公司一期工程2×300MW燃煤空冷机组和古交发电厂2×300MW燃煤空冷机组工程的烟气脱硫均采用RCFB-FGD引进技术(其中漳山电厂已于2004年11月投入运行)。
1.3 NID干法NID(New Integrated Desulfurization)技术是ABB-ALSTOM公司在半干法DRYPAC系统上发展而成的烟气脱硫方法,它借鉴了DRYPAC技术的脱硫原理,又克服了此种技术需要制浆而产生的弊端,其原理为石灰粉经过石灰消化器(LDH)消化后进入反应器,与烟气中的SO2发生化学反应,生成CaSO3和CaSO4,烟气中的SO2被脱除,因而具有投资低,方便可行的特点,用于中小型容量机组,当煤中含硫量<2%时,脱硫效率至少可达80%。
NID技术既具有干法的廉价、简单、可靠等优点,又有湿法的高脱硫效率,且原料消耗和能耗都比喷雾干燥法有大幅度下降。
1996年在波兰安装的两台125MW样板机组运行一直很成功;在台湾Mai Liao电厂的150MW机组已调试完成,性能试验结果良好;目前正在安装和设计中的项目有美国Sward电厂2×250MW机组和美国Gibert3电厂285MW机组。
迄今NID应用在世界各国的燃油炉、煤粉炉、垃圾焚烧炉上共有近20套。
浙江菲达环保科技股份有限公司与ABB-ALSTOM公司合作,将NID干法烟气脱硫技术应用于浙江巨化热电厂80MW机组上,已投入运行。
并参与了漳山工程和榆社工程300MW机组烟气脱硫的投标。
此外,武汉凯迪兰天环保公司、辽宁科林环保工程有限责任公司也引进了该项技术。
烟气循环流化床干法与NID法原理基本类似,从下面二张图即可看出。
烟气循环流化1.4 旋转喷雾半干法旋转喷雾半干法工艺是采用生石灰粉制浆作为脱硫剂,生石灰经消化并加水制成消石灰乳,消石灰乳由泵打入位于吸收塔内的雾化装置,利用高速旋转的喷雾器喷入蒸发反应塔,在吸收塔内,被雾化成细小液滴的吸收剂与烟气混合接触,与烟气中的SO2发生化学反应,生成CaSO3和CaSO4,烟气中的SO2被脱除。
与此同时,吸收剂带入的水分迅速被蒸发而干燥,烟气温度随之降低,脱硫反应产物及未被利用的吸收剂以干燥颗粒物形式随烟气带出吸收塔,利用锅炉配置的除尘器将脱硫灰与飞灰一起捕集下来。
其特点是系统简单,投资较少,厂用电低,无废水排放,占地较少。
缺点是脱硫剂利用率低,脱硫效率一般在70%左右。
该工艺在美国及西欧一些国家应用较为广泛,国外已有300MW容量机组使用。
国内已有内江发电总厂(原白马电厂)70000Nm3/h和黄岛电厂200MW机组使用。
1.5 炉内喷钙-尾部加湿活化法炉内喷钙-尾部加湿活化法是在炉膛内喷入石灰石粉脱除部分SO2,再在锅炉尾部烟道设置的活化反应器喷入增湿水,使未利用的石灰石粉进一步得到利用以提高脱NID干法脱硫效率,利用锅炉配置的除尘器将脱硫灰与飞灰一起捕集下来。
该工艺以石灰石粉为吸收剂,石灰石粉由气力喷入炉膛850-1150℃温度区,石灰石受热分解为氧化钙和二氧化碳,氧化钙与烟气中的SO2反应,生成CaSO。
由于反应在气固两相之间进行,受到传质过程的影响,反应速3度较慢,吸收剂利用率较低。
在尾部增湿活化反应器内,增湿水以雾状喷入,与未反应的氧化钙接触,生成氢氧化钙进而与烟气中的SO2反应。
其特点是系统简单,投资较少,厂用电低,无废水排放,占地也较少。
但其脱硫剂利用率低,脱硫效率一般达75%左右,且对锅炉效率和磨损积灰有一定的影响。
该脱硫工艺在芬兰、美国、加拿大、法国等国家得到较多应用,采用这一脱硫技术的最大单机容量已达300MW。
国内目前使用的电厂有南京下关电厂和浙江钱清电厂125MW机组。
下图为南京下关电厂炉后增湿活化部分布置示意图1.6其它脱硫工艺此外还有电子束法、氨法等脱硫工艺。
其中电子束法目前尚处于试验研究阶段,在成都热电厂曾安装相当于100MW烟气脱硫试验装置。
而氨法脱硫工艺还没有在大机组上应用的业绩和经验。
而且从当地现有的条件看,电子束法、氨法脱硫所需的吸收剂液氨和氨水也难以保证供应,所以,这二种工艺均不适合本工程的情况。
在此不作详述。
1.7国内外脱硫装置的生产制造能力脱硫装置在国外是一种成熟的产品,可设计生产制造的厂家很多,主要集中在美、德、日、芬兰等国,在此不做一一介绍。
国内也已经有几十家脱硫公司引进了国外技术。
并在引进消化国外技术的基础上,已有多个公司形成了一定的生产能力。
国电龙源电力环保技术公司在北京一热、重庆电厂和浙江半山电厂采用德国STEINMILLER技术设备的基础上,引进了湿法脱硫技术。
其总承包的石景山热电厂工程已经投入运行,目前承担的北京一热、黄台300MW容量级机组、大同二电厂2X600MW机组湿法脱硫均已分别进入安装或调试阶段。
日本石川岛播磨工业株式会社通过与上海电气(集团)总公司等合资组建了上海石川岛脱硫工程有限公司,能够提供湿法脱硫的整套工程设计、设备成套供货和技术服务。
日本川崎公司提供技术与山东三融环保公司合作取得了贵州安顺电厂2×300MW、鸭溪电厂2×300MW以及山西霍州二电厂2x300MW机组的合同,现又引进了德国LLB(鲁奇-能捷斯-毕肖夫)公司湿法技术。
武汉凯迪电力股份公司利用美国B&W公司技术获得了太原二热电厂五期技改工程1×200MW、广西合山电厂2×300MW、四川广安电厂2×300MW以及常熟电厂2×600MW机组的合同。
重庆远达环保有限公司引进日本三菱重工技术,取得鸭溪电厂2×300MW合同,现又与奥地利能源(AE)公司合作,并中标河津、永济300MW机组。
上海龙净环保科技工程公司、国华荏原环境工程有限责任公司等均引进德国LLB技术并具有工程总承包能力。
其中上海龙净现已取得黄埔电厂2X300MW、镇江高姿2X600MW 机组的合同。
除此之外,浙大兰天、浙大网新、浙江天地环保、江苏苏源、国电南环所、东方锅炉厂、中国华电、北京博奇等脱硫公司均已有200-600MW机组的中标业绩。
“七五”期间,以西南电力设计院为主,在白马电厂完成了处理70000Nm3/h的旋转喷雾半干法脱硫工业试验,积累了科研、设计、设备制造、安装、调试及生产运行方面的经验。
通过对黄岛电厂200MW机组中日合作旋转喷雾半干法项目的跟踪甚至改进,西南电力设计院已具备开发大型装置的能力。
另外,广州市天赐三和环保工程有限公司也引进丹麦尼鲁公司旋转喷雾半干法技术,并也有运行业绩。
炉内喷钙-尾部加湿活化法在国外比较成熟,国内目前在南京下关电厂和浙江钱清电厂的125MW机组上使用,锅炉均为国产。
哈尔滨锅炉厂早在“七五”计划期间,就在国家环保局组织下开始进行“喷钙脱硫成套技术开发”工作,目前已经完成了大至125MW锅炉的报价设计和技术设计,并为南京下关电厂提供了锅炉,通过该工程实践积累了大量的经验和技术储备。
国内有丹麦史密斯公司在云南小龙潭电厂已经运行的125MW机组、由武汉凯迪电力技术公司引进德国WULFF公司技术在广州恒运电厂210MW燃煤机组上实施,并投入运行。
中标我省漳山工程2×300MW机组的脱硫除尘岛总承包项目,也已投入运行。