压力管道检验计案例
压力管道现场安装监督检验案例

压力管道现场安装监督检验案例本案例涉及一台新建的石油化工厂,在建设过程中需要安装一段长度为500米的石油输送管道,该管道将用于输送原油。
根据设计要求,管道材质为碳钢,额定工作压力为10MPa。
1.监督检验准备阶段:在安装之前,监督检验工作开始准备。
监督检验人员首先要熟悉设计和施工图纸,了解管道的布置和安装方法。
然后,与工程施工方组织会议,明确监督检验的相关要求和工作流程。
2.施工现场检查:监督检验人员到达施工现场后,首先对施工现场进行检查和评估。
他们要确认地基基础是否满足要求,并检查是否有足够的施工空间和设备。
同时,还需要检查压力管道的接口和组件,确保其符合规范和标准。
3.材料检验:在现场材料检验中,监督检验人员要对管道材料进行严格把关。
他们要检查管道材质是否符合设计要求,并对其进行化学成分和力学性能测试。
另外,还要查验管道配件的合格证书,以确保其质量可靠。
4.施工过程监督:在管道的安装过程中,监督检验人员要对施工现场进行实时监控和记录。
他们会检查焊接和涂层工艺,并对焊口和涂层进行质量评估。
另外,他们还会观察施工工人是否佩戴相关安全设备,确保安全规范得到遵守。
5.现场试验和功能验证:安装结束后,监督检验人员将进行现场试验和功能验证。
他们会进行水压试验,检查管道是否能承受额定工作压力。
同时,也会验证管道的功效,确保其能够稳定输送原油。
6.监督报告和验收:监督检验工作完成后,监督检验人员将撰写监督报告,并提交给工程施工方。
该报告需要详细记录检验过程、发现的问题以及建议的整改措施。
施工方根据监督报告进行相应的整改,并邀请监督检验人员进行验收。
通过上述的监督检验过程,可以及时发现和解决施工中存在的问题,确保压力管道的安装质量和安全性。
这种监督检验工作的重要性不言而喻,在各个行业都是必不可少的一环。
只有通过严格的监督检验,才能有效保障工程的质量和安全,为人们的生命财产提供有效的保护。
压力管道完整性评价原理及案例介绍
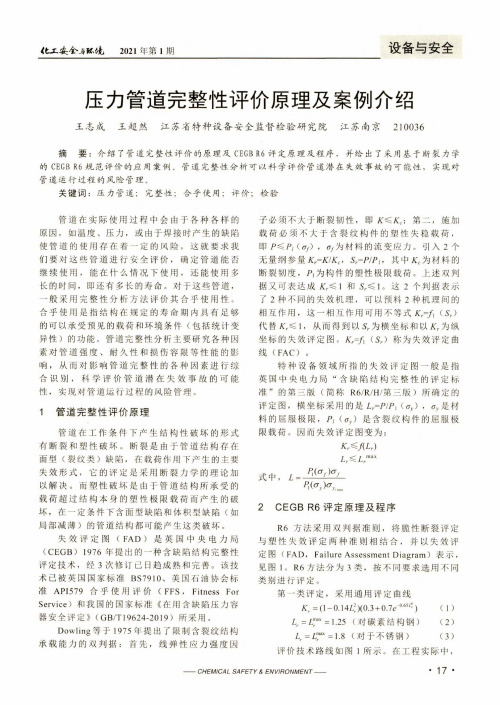
<匕1•妾舍为讯庇2021年第1期设备与安全压力管道完整性评价原理及案例介绍王志成王超然江苏省特种设备安全监督检验研究院江苏南京210036摘要:介绍了管道完整性评价的原理及CEGB R6评定原理及程序,并给出了采用基于断裂力学的CEGB R6规范评价的应用案例。
管道完整性分析可以科学评价管道潜在失效事故的可能性,实现对管道运行过程的风险管理。
关键词:压力管道;完整性;合乎使用;评价;检验管道在实际使用过程中会由于各种各样的原因,如温度、压力,或由于焊接时产生的缺陷使管道的使用存在着一定的风险,这就要求我们要对这些管道进行安全评价,确定管道能否继续使用,能在什么情况下使用,还能使用多长的时间,即还有多长的寿命。
对于这些管道,一般采用完整性分析方法评价其合乎使用性。
合乎使用是指结构在规定的寿命期内具有足够的可以承受预见的载荷和环境条件(包括统计变异性)的功能。
管道完整性分析主要研究各种因素对管道强度、耐久性和损伤容限等性能的影响,从而对影响管道完整性的各种因素进行综合识别,科学评价管道潜在失效事故的可能性,实现对管道运行过程的风险管理。
1管道完整性评价原理管道在工作条件下产生结构性破坏的形式有断裂和塑性破坏。
断裂是由于管道结构存在面型(裂纹类)缺陷,在载荷作用下产生的主要失效形式,它的评定是采用断裂力学的理论加以解决。
而塑性破坏是由于管道结构所承受的载荷超过结构本身的塑性极限载荷而产生的破坏,在一定条件下含面型缺陷和体积型缺陷(如局部减薄)的管道结构都可能产生这类破坏。
失效评定图(FAD)是英国中央电力局(CEGB)1976年提出的一种含缺陷结构完整性评定技术,经3次修订已日趋成熟和完善。
该技术己被英国国家标准BS7910.美国石油协会标准API579合乎使用评价(FFS,Fitness For Service)和我国的国家标准《在用含缺陷压力容器安全评定》(GB/T19624-2019)所采用。
一条压力管道裂纹多发的检验案例分析

一条压力管道裂纹多发的检验案例分析刘剑;李夏书;唐文强【摘要】对一个编号为AS-0841的压力管道进行定期检验,发现其泵出口处的管段存在开裂和私自补焊等现象.针对这一现象,结合该管道外部振动和内部湿硫化氢破坏等因素,分析了该管段裂纹多发的原因,并对以后的定期检验工作提出建议.【期刊名称】《化工管理》【年(卷),期】2018(000)014【总页数】2页(P121-122)【关键词】压力管道;裂纹;湿硫化氢;检验案例【作者】刘剑;李夏书;唐文强【作者单位】温州市特种设备检测研究院,浙江温州 325000;浙江省特种设备检检验研究院,浙江杭州 310000;温州市特种设备检测研究院,浙江温州 325000【正文语种】中文压力管道能够承担一定的温度与压力,从而可以作为石油化工、冶金等行业的运输流体的介质[1]。
由于压力管道需要承担易燃、易爆、毒性介质,管道输送的安全直接关系到居民的生活与正常的工业生产,因此对其安全性提出较高的要求,在管道使用过程中必须加强对于管道的检验,确保管道质量合格[2]。
本文针对一条泵出口处的管段开裂和私自补焊等现象进行了分析并提出了在今后压力管道检验方面的建议。
2014年12 月笔者对宁波某公司2390余根压力管道进行了定期检验,检验前使用单位委托中国特检院进行RBI评估。
根据RBI策略制定检验方案,并根据检验方案实施检验。
检验过程中发现其中一条管道的泵出口处的管段存在开裂和私自补焊等现象。
管道基本参数见表1,RBI策略见表2,管道单线图见图1。
表1 管道AS-0841的主要参数管道编号管道级别AS-0841 GC2投用日期管道长度2010年10月15日29.5m管道起点设计压力操作压力介质规格P0804B2 0.6MPa 0.35MPa黑水DN 100×5.0 DN 50×3.2管道止点设计温度操作温度材质上次全面检验日期AS-0828 110℃78℃20首次全面检s验表2 管道AS-0841的RBI策略管道编号潜在损失机理壁厚测定UT/RT AS-0841酸性水腐蚀+冲刷+湿硫化氢破坏+外部腐蚀几何不连续处抽查20%,不低于1处(如果有)焊口抽查10%,不低于2道口风险等级宏观检查MT/PT硬度中风险外部可见部位宏观检查焊口抽查10%,不低于2道口硬度抽查图1 管道AS-0841单线图1 缺陷情况根据制定的检验方案进行检验后,发现以下问题:经宏观检查,发现泵出口的管道有私自补焊现象,如图2所示,询问使用单位相关人员后得知,该段管道在使用过程中,多次发生贯穿性裂纹,导致泄漏,已经过更换和多次补焊。
工业管道检验案例

工业管道检验案例1. 引言1.1 管道检验检测概述失效机制影响因素外在表征如何在一定时间内有效无损地检测发现?发展规律预防措施检验人员应当根据压力管道的使用情况、失效模式制定检验方案。
改变机械地使用检验规则规定的习惯做法。
失效模式分析检测方法检测时机管道检验目的:发现并预防管道的不正常状态,避免管道失效,发生事故。
失效案例典型失效模式API 给出的腐蚀失效模式(63种)氢致损伤:氢腐蚀、氢脆(微裂纹)、堆焊层的氢致剥离 爆炸 断裂 泄漏 形过量变 表面损伤、金属损失 材料性能退化物理爆炸:物理原因(温度、内压)使应力超过强度化学爆炸:异常化学反应使压力急剧增加超过强度脆性断裂:应力腐蚀、氢致开裂、持久(蠕变)断裂、低温脆断韧性断裂疲劳断裂:应力疲劳、应变疲劳、高温疲劳、热疲劳、腐蚀疲劳、蠕变疲劳 密封泄漏:充装过量(冒顶) 腐蚀穿孔、穿透的裂纹或冶金、焊接缺陷(满足LBB 条件) 过热、过载引起的鼓胀、屈曲、伸长、凹坑(dent) 蠕变、亚稳定相的相变 电化学腐蚀:均匀腐蚀、点腐蚀、缝隙腐蚀、晶间腐蚀、沉积物下腐蚀、溶解氧腐蚀、碱腐蚀、硫化物腐蚀、氯化物腐蚀、硝酸盐腐蚀 冲蚀、气蚀 高温氧化腐蚀、金属尘化或灾难性渗碳腐蚀、环烷酸腐蚀 外来机械损伤:油气长输管线的主要失效模式之一辐照损伤脆化金相组织变化:珠光体球化、石墨化、S 相析出长大、渗碳、渗氮、脱碳、回火脆化与敏化、应变时效压力容器与管道1.2 压力管道的失效压力管道是具有潜在泄漏和爆炸危险的特种设备,对国家支柱产业有重要影响,其特点是:●量大面广:截止2009年底,我国在用固定式压力容器217.5万台,锅炉60.9万台,在用气瓶1.3亿只,压力管道68.5万公里,与承压设备相关的生产企业2万多家,年产值超过5000亿元。
●服役环境极端化:逐渐向高温、低温(液化天然气集输,-196℃)、复杂腐蚀(高硫、高酸原油炼制)、大型化等极端方向发展。
压力容器管道检验案例汇总

• 王兵
• 高级工程师 容器检验师,管道检验师 • 九三学社社员,PT-Ⅲ RT-Ⅲ AE-Ⅲ
上海派普诺管道科技发展有限公司
压力容器管道检验案例汇总
压力容器主要失效案例(杭州市特检院) 应力管道典型失效案例(浙江省特检院)
主要法规依据: TSG R7001 《压力容器定期检验规则》, TSG D7004《压力管道定期检验规则—公用管道》
压力管道检验案例 防腐层破损
案例简介:地面检测时发现防腐层破损,开挖后可见燃气管道防腐层出现不同程 度破损,破损点面积范围:1cm×1cm至25cm×49cm,管道本体发生 锈蚀,呈现均匀减薄危害管道安全运行。
原因分析:管道防腐层采用的PE胶带,防腐等级较低,且使用时间10年以上, 由于土壤复杂的环境和材料老化使防腐层破损;焊缝处未做防腐可 能施工验收不规范。
需详细的地勘报告,管道曲率应不大于1500DN。四次以上的扩孔,大厚度管材,100%无损检测, 特加强级防腐层,入土角需控制在8°-18°, 出土角4°-12°之间。拖拽力不能大于管道屈服强度。 穿越泥浆粘度控制在45—60之间。出土点误差控制。稍有疏忽、赶工期等,都会遗漏工程隐患。
压力管道检验案例 定向钻导致管道变形
原因分析:1。 管道安装过程中产生的缺陷,安装回埋时石块或是回埋机械拉断连接线; 2。 管道使用过程中,有大型动力机械经过管道,对管道周边牺牲阳极块造 成机械压力拉断牺牲阳极与管道的连接线。
处理意见:1、重新连接连接线,并在连接线与管道连接处从新做防腐,在检验无破损后 回埋。2、平时加强管道及管道周边处巡查,注意人为或施工破坏。 3、安装管道时严格规范执行管道安装。
压力管道检验案例
·
植物根系破坏
压力管道检验计算案例

压力管道检验计算案例54、某公司管道规格为Φ89×6.5mm,材料20#,最大工作压力为1.8MPa,工作温度:常温,工作介质:放空气体。
管道等级为GC2,实际使用时间为11年,本次为首次全面检验,测厚时发现管道存在局部减薄,实测最小壁厚为5.4mm,减薄区域环向长度实测最大值为50mm。
该管道本次检验时未发现其他缺陷,材料未出现性能劣化;该管道结构符合设计规范且不承受疲劳载荷。
问该管道如何定级?第四十七条管子的局部减薄,安全状况等级的确定方法如下:(一)若局部减薄在制造或验收规范所允许的范围内,则不影响定级。
(二)局部减薄超过制造或验收规范所允许的范围时,如果同时满足以下条件,则按照表3或表4定级;否则安全状况等级定为4级。
1.管道结构符合设计规范或管道的应力分析结果满足有关规范;2.在实际工况下,材料韧性良好,并且未出现材料性能劣化及劣化趋向;3.局部减薄及其附近无其它表面缺陷或埋藏缺陷;4.局部减薄处剩余壁厚大于2mm;5.管道不承受疲劳载荷。
表3 GC2或GC3管道所允许的局部减薄深度的最大值(mm)注:D为缺陷附近管道外径实测最大值,mm,以下同;t为缺陷附近壁厚的实测最小值减去至下一检验周期的腐蚀量的2倍,mm,以下同;B为缺陷环向长度实测最大值,mm;P为管道最大工作压力,MPa,以下同;P L0管道极限内压,P L0=(2/√3)σs In[(D/2)/(D/2-t)],以下同;σs为管道材料的屈服强度,MPa,以下同;C为至下一检验周期局部减薄深度扩展量的估计值,mm,以下同。
表4 GC1级管道所允许的局部减薄深度的最大值(mm)答:根据《在用工业管道定期检验规程》第四十七条,该管道存在局部减薄, 已知:P=1.8MPa ,B=50mm ,D=89mm ,MPa 245s =σ(1)18.0)8950/(3.14D)/(=⨯=πB <0.25,(B 为缺陷环向长度实测最大值,50mm ) (2).2932)2/(2/ln 32P L0 =-=t D D s σ(3)计算C 、t 值减薄量为Δ=6.5-5.4=1.1mm (原始厚度-实测最小壁厚)年腐蚀速率为:1.1mm/11年=0.1mm/年如按运行3年计算,则:C=0.1mm /年×3年=0.3mmt=5.4-2C=5.4-2*0.3=4.8mm(4)计算允许的局部减薄深度的最大值GC2管道定2级所允许的局部减薄深度的最大值为:0.33t-C=0.33*4.8-0.3=1.28mm因减薄量为Δ=1.1mm <1.28mm (小于该管道定2级运行3年所允许的局部减薄深度最大值1.28mm )。
压力管道检验案例分析

压力管道检验案例分析摘要:由于我国的经济迅速发展,很多行业都采用了不同的管材,而压力管道的应用更是越来越广,其总体的质量和安全性能直接关系到整个行业的发展,同时也关系到工人的生命安全。
为此,本文根据相关案例,对压力管道检验中出现的问题就能写分析,并提出相应的解决措施。
关键词:压力管道;检验案例;分析一、压力管道特征与意义压力管道是化工、冶金等领域中常用的一种运输介质的特种设备。
为了保证管道的运输安全和提高输送的品质,作为压力管道的检查人员应该根据管道在输送中发生的各种变化进行细致的研究,找出存在的问题,从而有针对性地采取相应的方法来进行正确的处理。
本文通过对压力管道检验案例进行分析,同时进行了相应的改进,以期为相关检验工作提供借鉴。
在实际工作中,由于压力管道(如图1)与常规管道存在着很大的差异,因此,必须保障压力管道能够经受很大的内外压,从而能够很好地适应实际工作的要求。
在管道连接时,采用大量螺栓、阀门和其他构件将各种管道进行高效的连接,以适应各种危险介质的输送要求。
原因是压力管道输送的介质大多是易燃、爆炸等危险品,因此,对压力管道质量和性能要求也很高,要确保压力管道的各个环节都是合理、安全的,从而确保了管道在各种工作条件下的工作性能和安全性。
目前,压力管道的使用范围更广,不仅在化学领域,在其他行业中均有所涉及。
但是近几年来管道材料存在不合格、安装不当、检验程序不规范等问题,使得近几年来,压力管道的质量问题越来越突出,给企业造成了巨大的经济损失,因此,加强现阶段对压力管道的检验十分重要,通过加大管理力度,促使相关的政府部门积极进行标准规范的修订和完善,保障工作人员在检验过程中严格遵循检验标准规范和制度,以便工作人员在检验过程中严格遵循检验标准规范和制度,以此来确保压力管道安全稳定运行,避免引发安全事故[1]。
图1:压力管道二、压力管道定期检验的内容与方法(一)材料质量与管道壁厚检验工作对压力管道进行检验检测过程中,对管材的检查和标识进行了细致的检查。
压力管道检验计算案例
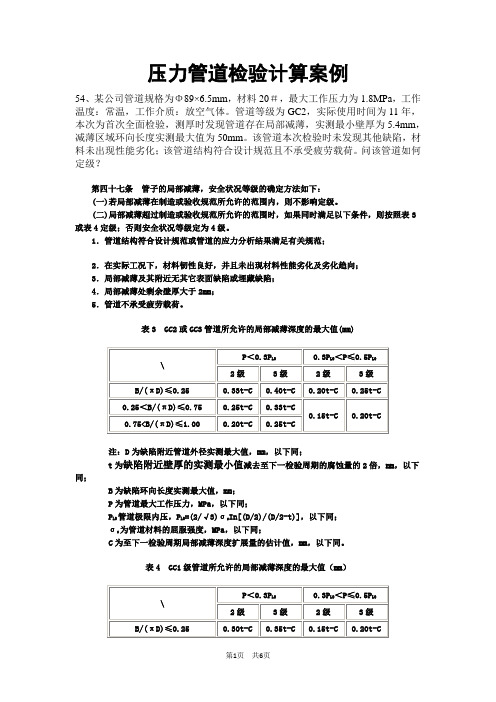
压力管道检验计算案例54、某公司管道规格为Φ89×6.5mm,材料20#,最大工作压力为1.8MPa,工作温度:常温,工作介质:放空气体。
管道等级为GC2,实际使用时间为11年,本次为首次全面检验,测厚时发现管道存在局部减薄,实测最小壁厚为5.4mm,减薄区域环向长度实测最大值为50mm。
该管道本次检验时未发现其他缺陷,材料未出现性能劣化;该管道结构符合设计规范且不承受疲劳载荷。
问该管道如何定级?第四十七条管子的局部减薄,安全状况等级的确定方法如下:(一)若局部减薄在制造或验收规范所允许的范围内,则不影响定级。
(二)局部减薄超过制造或验收规范所允许的范围时,如果同时满足以下条件,则按照表3或表4定级;否则安全状况等级定为4级。
1.管道结构符合设计规范或管道的应力分析结果满足有关规范;2.在实际工况下,材料韧性良好,并且未出现材料性能劣化及劣化趋向;3.局部减薄及其附近无其它表面缺陷或埋藏缺陷;4.局部减薄处剩余壁厚大于2mm;5.管道不承受疲劳载荷。
表3 GC2或GC3管道所允许的局部减薄深度的最大值(mm)注:D为缺陷附近管道外径实测最大值,mm,以下同;t为缺陷附近壁厚的实测最小值减去至下一检验周期的腐蚀量的2倍,mm,以下同;B为缺陷环向长度实测最大值,mm;P为管道最大工作压力,MPa,以下同;P L0管道极限内压,P L0=(2/√3)σs In[(D/2)/(D/2-t)],以下同;σs为管道材料的屈服强度,MPa,以下同;C为至下一检验周期局部减薄深度扩展量的估计值,mm,以下同。
表4 GC1级管道所允许的局部减薄深度的最大值(mm)答:根据《在用工业管道定期检验规程》第四十七条,该管道存在局部减薄, 已知:P=1.8MPa ,B=50mm ,D=89mm ,MPa 245s =σ(1)18.0)8950/(3.14D)/(=⨯=πB <0.25,(B 为缺陷环向长度实测最大值,50mm ) (2).2932)2/(2/ln 32P L0 =-=t D D s σ(3)计算C 、t 值减薄量为Δ=6.5-5.4=1.1mm (原始厚度-实测最小壁厚)年腐蚀速率为:1.1mm/11年=0.1mm/年如按运行3年计算,则:C=0.1mm /年×3年=0.3mmt=5.4-2C=5.4-2*0.3=4.8mm(4)计算允许的局部减薄深度的最大值GC2管道定2级所允许的局部减薄深度的最大值为:0.33t-C=0.33*4.8-0.3=1.28mm因减薄量为Δ=1.1mm <1.28mm (小于该管道定2级运行3年所允许的局部减薄深度最大值1.28mm )。
- 1、下载文档前请自行甄别文档内容的完整性,平台不提供额外的编辑、内容补充、找答案等附加服务。
- 2、"仅部分预览"的文档,不可在线预览部分如存在完整性等问题,可反馈申请退款(可完整预览的文档不适用该条件!)。
- 3、如文档侵犯您的权益,请联系客服反馈,我们会尽快为您处理(人工客服工作时间:9:00-18:30)。
压力管道检验计算案例54、某公司管道规格为Φ89×6.5mm,材料20#,最大工作压力为1.8MPa,工作温度:常温,工作介质:放空气体。
管道等级为GC2,实际使用时间为11年,本次为首次全面检验,测厚时发现管道存在局部减薄,实测最小壁厚为5.4mm,减薄区域环向长度实测最大值为50mm。
该管道本次检验时未发现其他缺陷,材料未出现性能劣化;该管道结构符合设计规范且不承受疲劳载荷。
问该管道如何定级?第四十七条管子的局部减薄,安全状况等级的确定方法如下:(一)若局部减薄在制造或验收规范所允许的范围内,则不影响定级。
(二)局部减薄超过制造或验收规范所允许的范围时,如果同时满足以下条件,则按照表3或表4定级;否则安全状况等级定为4级。
1.管道结构符合设计规范或管道的应力分析结果满足有关规范;2.在实际工况下,材料韧性良好,并且未出现材料性能劣化及劣化趋向;3.局部减薄及其附近无其它表面缺陷或埋藏缺陷;4.局部减薄处剩余壁厚大于2mm;5.管道不承受疲劳载荷。
表3 GC2或GC3管道所允许的局部减薄深度的最大值(mm)注:D为缺陷附近管道外径实测最大值,mm,以下同;t为缺陷附近壁厚的实测最小值减去至下一检验周期的腐蚀量的2倍,mm,以下同;B为缺陷环向长度实测最大值,mm;P为管道最大工作压力,MPa,以下同;P L0管道极限内压,P L0=(2/√3)σs In[(D/2)/(D/2-t)],以下同;σs为管道材料的屈服强度,MPa,以下同;C为至下一检验周期局部减薄深度扩展量的估计值,mm,以下同。
表4 GC1级管道所允许的局部减薄深度的最大值(mm)答:根据《在用工业管道定期检验规程》第四十七条,该管道存在局部减薄, 已知:P=1.8MPa ,B=50mm ,D=89mm ,MPa 245s =σ(1)18.0)8950/(3.14D)/(=⨯=πB <0.25,(B 为缺陷环向长度实测最大值,50mm ) (2).2932)2/(2/ln 32P L0 =-=t D D s σ(3)计算C 、t 值减薄量为Δ=6.5-5.4=1.1mm (原始厚度-实测最小壁厚)年腐蚀速率为:1.1mm/11年=0.1mm/年如按运行3年计算,则:C=0.1mm /年×3年=0.3mmt=5.4-2C=5.4-2*0.3=4.8mm(4)计算允许的局部减薄深度的最大值GC2管道定2级所允许的局部减薄深度的最大值为:0.33t-C=0.33*4.8-0.3=1.28mm因减薄量为Δ=1.1mm <1.28mm (小于该管道定2级运行3年所允许的局部减薄深度最大值1.28mm )。
因此该管道安全状况等级可定为2级,运行周期为3年。
讨论1:如按运行6年计算,则:C=0.1mm /年×6年=0.6mmt=5.4-2C=5.4-2*0.6=4.2mm0.33t-C=0.33*4.2-0.6=0.786mm<1.1mm如按运行5年计算,则:C=0.1mm /年×5年=0.5mmt=5.4-2C=5.4-2*0.5=4.4mm0.33t-C=0.33*4.4-0.5=0.952mm<1.1mm (5)如按运行4年计算,则:C=0.1mm /年×4年=0.4mmt=5.4-2C=5.4-2*0.4=4.6mm0.33t-C=0.33*4.6-0.4=1.118mm>1.1mm (4)因此该管道安全状况等级可定为2级,运行周期为4年。
根据计算,本题还可定为3级3、4、5年。
具体应根据现场实际情况定级。
关于局部减薄(凹坑)的容限说明◇原因: 腐蚀、冲蚀、机械损伤、缺陷消除打磨形成的凹坑◇国家“八五”攻关 从塑性极限载荷理论+断裂力学方法,在大量理论分析与试验研究基础上,分析了拉、压、弯曲、扭转各种载荷下的凹坑安全性,考虑适当安全系数,得到了表3(GC2、GC3),将表3的容限值除以安全系数1.1,圆整得到表4( GC1 )凹坑与局部减薄类缺陷的“死”与“活”《管检规》第46、47、48条❑ 表面缺陷打磨形成凹坑——“死”缺陷由表面缺陷打磨形成凹坑,在使用中没有介质腐蚀的话,这类凹坑或局部减薄一般不会发生变化,是“死”缺陷,而且位置固定,容易发现与监控,相对危害性较小。
❑ 腐蚀坑、冲刷磨损沟槽——“活”缺陷在使用中产生的凹坑与减薄,如腐蚀坑,冲刷磨损沟槽等等,这类缺陷是“活”缺陷,减薄尺寸会不断加大,并且可能存在于管道任何位置,难于发现,因而危害性较大,企业中的很多多爆炸事故因此而引起。
讨论2: (1)本题“实测最小壁厚为5.4mm ”,既是“缺陷附近壁厚的实测最小值”,又是“局部减薄深度的最大处厚度”。
55、某管道规格为Φ114×11mm ,材料20#钢,设计压力为8.8MPa ,设计温度40℃,管道等级为GC2,上次全面检验时发现管子存在全面减薄,实测最小壁厚为8.0mm ,安全状况等级定为3级,运行周期定为3年。
本次全面检验时,在上次最小壁厚处实测最小壁厚为7.0mm 。
该管道如何定级?(注:Y 系数取0.4,焊接接头系数Ej 取0.85,材料许用应力[]tσ取130MPa ) 第四十六条 管子或管件全面减薄时,安全状况等级的确定方法如下:(一)管子或管件的实测壁厚,扣除至下一检验周期的腐蚀量的2倍后,不小于其设计最小壁厚,则不影响定级。
(二)耐压强度校验不合格,安全状况等级为4级。
(三)如果应力分析结果符合有关标准或规范的要求,则不影响定级:否则,定为4级。
答:该管道存在全面减薄,已知P =8.8MPa ,D O =114mm ,根据GB50316-2000《工业金属管道设计规范》,可计算其设计最小壁厚:[]mm PY E PD j t5.2)(2/t 0s =+=σ 根据题目可知,年腐蚀速率为(8.0-7.0)/3=0.33mm/年如按再运行3年计算,至下一检验周期的腐蚀量的2倍2C 为:0.33mm /年×3年×2=1.98mmt=4.4mm本次全面检验实测最小壁厚为7.0mm,则7.0-2C=5.02mm>s故该管道因全面减薄,再运行3年,不影响定级,可定为3级。
焊接缺陷(不包括裂纹)的安全状况等级按第四十九条计算定级。
第四十九条焊接缺陷(不包括裂纹)的安全状况等级划分如下:(一)若焊接缺陷在制造或安装验收规范所允许的范围内,则不影响定级。
焊接缺陷超过制造或安装验收规范所允许的范围时,如果同时满足以下条件,则按本条二款有关规定定级;否则管道安全状况等级为4级。
1.管道结构符合设计规范或管道的应力分析结果满足有关规范;2.焊接缺陷附近无新生裂纹类缺陷;3.管道材料的抗拉强度小于540MPa;4.在实际工况下,材料韧性良好,并且未出现材料性能劣化及劣化趋向;5.管道最低工作温度高于-20℃,或管道最低工作温度低于-20℃但管道材料为奥氏体钢;6.管道不承受疲劳载荷。
(二)焊接缺陷的安全状况等级划分方法1.咬边GC2级或GC3级管道,咬边深度不超过0.8mm;GCl级管道咬边深度不超过0.5mm时,不影响定级。
否则应打磨消除或圆滑过渡,并按第四十七条的规定定级。
2.气孔若气孔率不大于5%,并且单个气孔的长径小于0.5t与6mm二者中的较小值,则不影响定级;否则定为4级。
注:气孔率指在射线底片有效长度范围内,气孔投影面积占焊接接头投影面积的百分比;射线底片有效长度按现行行业标准《压力容器无损检测》JB4730的规定确定;焊接接头投影面积为射线底片有效长度与焊接接头平均宽度的乘积。
3.夹渣GC2级或GC3级管道,当夹渣自身高度或宽度的最大值不大于0.35t,并且不大于6mm时,按表5定级,否则定为4级。
GC1级管道,当夹渣自身高度或宽度的最大值不大于0.3t,并且不大于5mm时,按表5定级,否则定为4级。
表5 各级管道所允许的单个焊接接头中夹渣总长度的最大值(mm)4.未焊透(1)管子的材料为20钢、16Mn或奥氏体不锈钢时,未焊透按局部减薄定级;(2)管子的材料为除20钢、16Mn或奥氏体不锈钢外的其它材料时,未焊透按未熔合定级。
5. 未熔合GC2级或GC3级管道,未熔合的长度不限,根据其自身高度按表6定级。
GC1级管道,当单个焊接接头未熔合的总长度不大于焊接接头长度的50%时,根据其自身高度按表6定级;否则定为4级。
表6 各级管道所允许的单个焊接接头中未熔合自身高度的最大值6. 错边缺陷错边缺陷,按表7定级。
当错边缺陷超过表7的范围时,若管道经过长期使用且该部位在全面检验中未发现较严重的缺陷时,安全状况等级可定为2级或3级;若伴有裂纹、未熔合、未焊透等严重缺陷时,定为4级。
表7 错边缺陷的安全状况等级评定方法56、某单位需用设计压力为3.5MPa ,设计温度为550℃的Φ159的1Cr5Mo 无缝钢管,管子壁厚附加量C 为2mm ,试按GB50136-2000《工业金属管道设计规范》计算钢管厚度。
答:根据GB50316-2000《工业金属管道设计规范》第6.2.1条,承受内压直管计算壁厚为:[])(2/t 0s PY E PD j t+=σ 式中:P =3.5MPa,,D o =159mm ,1Cr5Mo 钢管在550℃时许用应力MPa t 35][=σ,焊接接系数Ej=1.0,系数Y =0.4。
计算结果:t s =7.6mm直管设计厚度t sd =t s +C =7.6+2=9.6mm 。
故该钢管厚度可选10mm 。
57、某石化公司输送可燃流体的规格为Φ159×10、材料为1Cr5Mo 的管道系统欲进行压力试验,该系统设计压力为4.0MPa ,设计温度为575℃,钢管壁厚附加量C =1.5mm ,请按GB50235《工业金属管道施工及验收规范》和GB50316《工业金属管道设计规范》计算试验压力为多少?GB50235《工业金属管道施工及验收规范》7.5.3.7 当管道的设计温度高于试验温度时,试验压力应按下式计算: Ps =1.5P[σ]1/[σ]2 (7.5.3)式中 Ps ——试验压力(表压)(Mpa);P ——设计压力(表压)(MPa);[σ]1——试验温度下,管材的许用应力(MPa);[σ]2——设计温度下,管材的许用应力(MPa)。
当[σ]1/[σ]2大于6.5时,取6.5。
当Ps 在试验温度下,产生超过屈服强度的应力时,应将试验压力Ps 降至不超过屈服强度时的最大压力答:根据《工业金属管道施工及验收规范》的规定,管道设计温度高于试验温度时应按下式进行换算:P S =1.5P[σ]1/[σ]2查设计规范:1Cr5Mo 钢管常温下[σ]=122MPa ,570℃时[σ]=26MPa , P S =1.5×4×122/26=28.1MPa当P S 在试验温度下,产生超过屈服强度的应力时,应将试验压力P S 降至不超过屈服强度时的最大应力。