金相检验规范
金相检验操作规程

金相检验操作规程1.试样金相试样面积小于400mm2,厚(高)度15-20mm为宜。
若试样面积过小,应经镶嵌后再进行磨制。
低倍组织酸侵试样厚度(高)度为20mm左右,酸侵低倍试样检测面应经过车加工或磨加工,表面粗糙度应不大于1.6μm。
试样检测面不得由油污及加工伤痕,必要时应预先清除。
试样的标识应清晰。
2.高倍检验操作规程2.1金相试样制备操作规程2.1.1金相试样的切取试样切取的方向、部位和数量,应根据有关技术条件的规定。
试样可用手锯、锯床或切割机等切取,必要时也可用气割法切取,但烧割边缘必须与正式试样保持相当距离,以去除热影响区。
取好的试样先在平面磨床或砂轮机上把检测面磨平,磨面上的磨痕应均匀一致。
磨样时应对试样进行冷却,以免金属组织受热发生变化。
2.1.2金相试样的磨制试样需经粗磨和细磨,粗磨用水磨砂纸,细磨用金相砂纸,应根据需要选择合适的砂纸及磨制道次。
磨样时须把前一道的磨痕磨去,方向与前一道的工序相垂直。
磨样时要防止试样磨面温度过高而使组织发生变化。
2.1.3金相试样的抛光常用的时机械抛光的方法,即把经过细磨的试样在抛光机上进行抛光。
抛光织物采取丝绒或绸布,抛光粉采用金刚砂。
抛光面光洁度要达到镜面,不允许有夹杂物拖尾、麻点、过热等现象,抛光后将试样清洗干净。
2.1.4金相试样化学侵蚀操作规程试样侵蚀前抛光面应保持干净,不得有油污或指痕,以免影响所显示组织的清晰度。
试样在盛有侵蚀剂的器皿中侵蚀,侵蚀时试样应轻微摆动,但不可擦伤抛光面。
应根据不同的需要选择侵蚀剂,并注意侵蚀适度。
侵蚀后试样应保持干燥(在酒精中浸泡、用电吹风吹干),以待观察。
配置侵蚀剂时遵照先加酒精或水、后加酸液的顺序。
侵蚀操作时要注意安全,防止酸液或酸雾对人体造成伤害。
2.2金相显微镜操作规程操作者在使用显微镜前,应仔细阅读显微镜的使用说明书,了解显微镜的功能及使用方法。
初学者操作显微镜应在专人指导下进行。
测试前应保持操作者的手及试样清洁干燥。
金相检验安全操作规程

金相检验安全操作规程金相检验是金属材料微观组织研究的重要方法之一,通过该方法可以对金属材料的晶粒大小、晶体形貌、晶界分布、相组成等进行观察和分析。
然而,由于金相检验涉及到实验操作和设备使用,所以在进行金相检验时需要遵守一定的安全操作规程,以确保实验人员的人身安全和实验结果的准确性。
下面就是金相检验的安全操作规程。
一、实验前的准备工作1.实验室应保持整洁,杂物应及时清除,柜台、工作台应整齐有序。
2.实验前应检查金相显微镜的电源、冷光源等设备是否正常,如有异常应及时维修或更换。
3.实验人员应穿戴实验服和安全帽,并佩戴防护手套和护目镜,以防止物品跌落或溅入眼睛。
二、样品的制备1.样品制备时应注意操作规范,避免产生尘埃、刺激性气体和放射性粉末,以免对人身和环境造成危害。
2.切割、打磨样品时应佩戴防护手套和护目镜,以免碎片伤人或尘埃进入眼睛。
三、试剂的使用1.实验时应使用标准的化学试剂,避免使用过期或不明确成分的试剂。
2.使用试剂时应佩戴防护手套,防止皮肤与试剂直接接触。
四、显微镜的使用1.使用显微镜时应先调整目镜和物镜,确保镜头清晰,再进行观察和拍照操作。
2.仔细调节焦距,避免眼部疲劳或眼部损伤。
五、设备的保养和维护1.实验结束后,显微镜等设备应进行清洁、维护,以保持正常的使用状态。
2.荧光涂层灯管需要定期更换,以保证金相显微镜的照明质量。
3.故障设备需及时发送到维修部门,切勿拆解和私自修理。
六、实验后的处理1.实验结束后,应及时清理实验室和工作台上的杂物和试剂,保持实验环境整洁。
2.实验结束后,及时洗手,并彻底清洗使用过的试剂瓶和实验仪器。
以上是金相检验的安全操作规程,通过严格遵守这些规程,可以保障实验人员的人身安全,并获得准确可靠的实验结果。
实验人员必须牢记实验中的安全注意事项,学会正确使用实验设备,并随时保持警觉和谨慎。
只有确保实验过程安全规范,才能更好地保障实验人员的身体健康和工作效率。
金相组织检验标准与质量判定
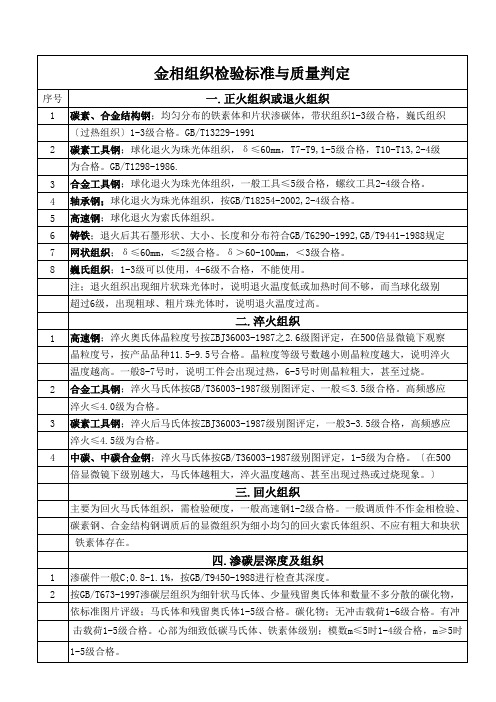
淬火≤4.5级为合格。
4 中碳、中碳合金钢;淬火马氏体按GB/T36003-1987级别图评定,1-5级为合格。〔在500 倍显微镜下级别越大,马氏体越粗大,淬火温度越高、甚至出现过热或过烧现象。〕
三.回火组织
主要为回火马氏体组织,需检验硬度,一般高速钢1-2级合格。一般调质件不作金相检验、
碳素钢、合金结构钢调质后的显微组织为细小均匀的回火索氏体组织、不应有粗大和块状
3 合金工具钢;球化退火为珠光体组织,一般工具≤5级合格,螺纹工具2-4级合格。 4 轴承钢;球化退火为珠光体组织,按GB/T18254-2002,2-4级合格。 5 高速钢;球化退火为索氏体组织。 6 铸铁;退火后其石墨形状、大小、长度和分布符合GB/T6290-1992,GB/T9441-1988规定
1-5级合格。
五.感应加热淬火淬硬层及组织
淬硬层金相组织检验在400倍显微镜小,在零件表面0.5mm处进行评定。按JB/T9204-1999 共分10级;1-2级过热〔粗、较粗马氏体〕,3-7级合格〔细、较细马氏体〕,8-10级加热 不足。〔微细马氏体+网络状极细珠光体+未溶铁素体〕均与标准图片对比评定。 注;HRC≥55时 3-7级合格,HRC<55时 3-9级合格。﹙JB/T9204-1999﹚
7 网状组织;δ≤60mm,≤2级合格。δ>60-100mm,<3级合格。
8 巍氏组织;1-3级可以使用,4-6级不合格,不能使用。 注;退火组织出现细片状珠光体时,说明退火温度低或加热时间不够,而当球化级别
超过6级,出现粗球、粗片珠光体时,说明退火温度过高。
二.淬火组织
1 高速钢;淬火奥氏体晶粒度号按ZBJ36003-1987之2.6级图评定,在500倍显微镜下观察
金相检测国标

金相检测国标
金相检测国标是指金相检测的国家标准。
金相检测是通过显微镜观察和分析金属材料的显微结构和组织来研究材料性质和结构的一种方法。
金相检测国标是制定金相检测的方法、步骤和要求的标准文件,用于指导金相检测的实施,并确保金相检测结果的准确性和可比性。
在国际上,金相检测的标准主要有ISO 4967《金属材料显微组织金相检验金属材料样品制备》、ISO 945-1《金属材料显微组织样品的制备和表面金相检验》等。
而在中国,金相检测的国标主要有GB/T 4334.1-2000《金属材料宏观金相检验方法金相组织分析方法》、GB/T 4334.3-2008《金属材料宏观金相检验方法显微硬质度测定方法》等。
这些国标具体规定了金相检测的样品制备方法、显微观察装置的要求、显微照相方法和显微结构分析方法等内容,以确保金相检测结果的可靠性和准确性。
同时,金相检测的国标还对金相检测人员的资格要求和实验室管理的要求进行了规定,以确保金相检测工作的质量和可靠性。
金相检验操作规程

金相检验操作规程1.试样金相试样面积小于400mm2,厚(高)度15-20mm为宜。
若试样面积过小,应经镶嵌后再进行磨制。
低倍组织酸侵试样厚度(高)度为20mm左右,酸侵低倍试样检测面应经过车加工或磨加工,表面粗糙度应不大于1.6μm。
试样检测面不得由油污及加工伤痕,必要时应预先清除。
试样的标识应清晰。
2.高倍检验操作规程2.1金相试样制备操作规程2.1.1金相试样的切取试样切取的方向、部位和数量,应根据有关技术条件的规定。
试样可用手锯、锯床或切割机等切取,必要时也可用气割法切取,但烧割边缘必须与正式试样保持相当距离,以去除热影响区。
取好的试样先在平面磨床或砂轮机上把检测面磨平,磨面上的磨痕应均匀一致。
磨样时应对试样进行冷却,以免金属组织受热发生变化。
2.1.2金相试样的磨制试样需经粗磨和细磨,粗磨用水磨砂纸,细磨用金相砂纸,应根据需要选择合适的砂纸及磨制道次。
磨样时须把前一道的磨痕磨去,方向与前一道的工序相垂直。
磨样时要防止试样磨面温度过高而使组织发生变化。
2.1.3金相试样的抛光常用的时机械抛光的方法,即把经过细磨的试样在抛光机上进行抛光。
抛光织物采取丝绒或绸布,抛光粉采用金刚砂。
抛光面光洁度要达到镜面,不允许有夹杂物拖尾、麻点、过热等现象,抛光后将试样清洗干净。
2.1.4金相试样化学侵蚀操作规程试样侵蚀前抛光面应保持干净,不得有油污或指痕,以免影响所显示组织的清晰度。
试样在盛有侵蚀剂的器皿中侵蚀,侵蚀时试样应轻微摆动,但不可擦伤抛光面。
应根据不同的需要选择侵蚀剂,并注意侵蚀适度。
侵蚀后试样应保持干燥(在酒精中浸泡、用电吹风吹干),以待观察。
配置侵蚀剂时遵照先加酒精或水、后加酸液的顺序。
侵蚀操作时要注意安全,防止酸液或酸雾对人体造成伤害。
2.2金相显微镜操作规程操作者在使用显微镜前,应仔细阅读显微镜的使用说明书,了解显微镜的功能及使用方法。
初学者操作显微镜应在专人指导下进行。
测试前应保持操作者的手及试样清洁干燥。
金相检测国标

金相检测国标主要参考以下几个标准:
1. GB/T 15124-2009《金属材料金相检验》:这个标准规定了金属材料金相检验的基本方法、技术要求、检验程序和报告编制等内容。
适用于钢铁、有色金属及合金等金属材料的金相检验。
2. GB/T 15125-2009《金属材料金相检验用试样和试验方法》:这个标准规定了金相检验用试样的制备方法、试验条件及检验方法等,包括了光学显微镜检验、电子显微镜检验等方法。
3. GB/T 17391-2017《金属材料钢的金相组织检验》:这个标准规定了钢的金相组织检验方法、检验程序及报告编制等,包括了晶粒度、珠光体、铁素体、渗碳体、马氏体、奥氏体等组织结构的检验。
4. GB/T 23024-2009《金属材料铝及铝合金金相检验》:这个标准规定了铝及铝合金金相检验的方法、技术要求、检验程序和报告编制等内容,适用于铝及铝合金的金相检验。
5. GB/T 30407-2013《金属材料铜及铜合金金相检验》:这个标准规定了铜及铜合金金相检验的方法、技术要求、检验程序和报告编制等内容,适用于铜及铜合金的金相检验。
金相试验操作方法和试验规程
XX机电有限公司金相试验操作方法、试验规程编号:1.试样制备:1.1 试样截取的方向,垂直于径向,长度不超过8mm.1.2试样可用手锯或切割机床等切取,不论用何种方法取样均应注意试样的温度条件,必要时用水冷却,以避免正式试样因过热而改变其组织。
2.试样的研磨2.1准备好的试样,先在粗砂轮上磨平,候磨痕均匀一致后,即移至细砂轮上续磨,磨时须用水冷却试样,使金属的组织不因受热而发生变化。
2.2经砂轮磨好、洗净、吹干后的试样,随即依次在由粗到细的各号砂纸上磨制,可采用在预磨机上进行磨制,从粗砂纸到细砂纸(W1-W6)、再换一次砂纸,试样须转90度角,与旧磨良成垂直方向。
2.3经预磨后的试样,先在抛光机上进行粗抛光(抛光织物为细绒布、抛光液为W2.5金刚石抛光膏)然后进行精抛光(抛光织物为锦丝绒,抛光液为W1.5金刚石抛光膏)抛光到试样上的磨痕完全除去而表面像镜面时为止,即粗糙度为Ra0.04以下。
3.试样的浸蚀。
3.1精抛后的试样,便可浸入盛于玻璃皿之浸蚀剂中进行浸蚀。
浸蚀时,试样可不时地轾微移动,但抛光面不得与皿底接触。
3.2浸蚀剂一般采用4-8%硝酸洒精溶液。
3.3浸蚀时间视金属的性质、检验目的及显微检验的放大倍数而定,以能在显微镜下清晰显示金属组织为宜。
试样浸蚀完毕后,须讯速用水洗净,表面两用,洒精洗净,然后用吹风机吹干。
4.金相显微镜组织检验4.1金相显微镜操作按仪器说明书规定进行。
4.2金相检验包括浸蚀前的检验和浸蚀后的检验,浸蚀前主要检验钢件的夹杂物和铸件的石墨形态、浸蚀后的检验为试样的显微组织,按有关金相标准进行检验。
5.使用金相显微镜注意事项:5.1取用镜头时,应避免手指接触透镜的表面,镜面平时应施在干燥器中妥善有效放置。
5.2物镜与试样表面接近时,调节时不要使物镜头与试样接触。
5.3显微镜不使用时需用防尘罩盖起。
质量部。
金相检验规范
1.目的通过对锻件进行金相检验,使产品质量处于受控状态,确保产品的内在质量符合国家法规、标准和客户的要求.2。
适用范围适用于本公司有金相试验要求的产品。
3.执行标准:①ASTM E381-01—2006 棒材、锻坯、大方坯和锻件的宏观侵蚀试验标准②ASTM E45—2013 测定钢材夹杂物含量的试验方法③ASTM E112-2013 测定平均晶粒度的标准试验方法4.检验人员必须经考核培训并取得相应岗位资格证书。
5.检验设备:光学显微镜、放大镜6.操作程序:6.1试样的制备a)试样截取方向、部位、数量应依据检验的目的、技术标准或双方技术合同进行;b)试样的尺寸见附图;c)试样的制备:磨平磨光(粗磨、细磨) 抛光浸蚀观察6。
2金相检验6。
2.1非金属夹杂物的检验:6.2。
1.1范围本标准规定了用标准图谱评定压缩比大于或等于3的轧制或锻制钢材中的非金属夹杂物的显微评定方法。
这种方法广泛用于对给定用途钢适应性的评估。
但是,由于受试验人员的影响,即使采用大量试样也很难再现试验结果,因此,使用本方法时应十分慎重。
6。
2.1。
2原理将所观察的视场与本标准图谱进行对比,并分别对每类夹杂物进行评级. 这些评级图片相当于100倍下纵向抛光平面上面积为0。
50mm2的正方形视场。
根据夹杂物的形态和分布,标准图谱分为A、B、C、D和DS五大类。
这五大类夹杂物代表最常观察到的夹杂物的类型和形态:——A类(硫化物类):具有高的延展性,有较宽范围形态比(长度/宽度)的单个灰色夹杂物,一般端部呈圆角;—-B类(氧化铝类):大多数没有变形,带角的,形态比小(一般〈3),黑色或带蓝色的颗粒,沿轧制方向排成一行(至少有3个颗粒);--C类(硅酸盐类):具有高的延展性,有较宽范围形态比(一般≥3)的单个呈黑色或深灰色夹杂物,一般端部呈锐角;——D类(球状氧化类):不变形,带角或圆形的,形态比小(一般<3),黑色或蓝色的,无规则分布的颗粒;-—DS类(单颗粒球状类):圆形或近似圆形的,直径≥13μm的单颗粒夹杂物。
宏观金相检测标准
宏观金相检测标准一、取样部位1. 从出厂检验合格的产品中切取至少三块代表性试样,在制样前可采用机械切割方法取下表面磨削面,并用磨光机打磨光亮。
2. 对于不能在成品上进行取样的焊缝和热影响区,则需在工厂或现场用切割、钻孔方法取得试样。
二、磨制方向1. 抛光面应向着观察面。
如果存在方向性,应将热影响区和焊缝中可能产生方向性缺陷的方向确定为观察面的相反方向。
2. 对于低合金高强度结构钢和特殊的耐磨钢,必要时抛光表面也可作为检验方向。
此时要求将金相试样打磨成轴对称试样。
三、研磨与抛光对于常规试样(抛光表面和反光表面)可采用平磨机或盘式研磨机研磨。
首先粗磨除去表面的凸凹不平,然后精磨达到镜面。
金相抛光后的抛光面应用金刚砂(氧化铝砂)轻轻研磨并抛光,然后用去离子水清洗,用滤纸吸干或吸水纸吸干试样表面,并观察表面质量。
如果发现有表面划痕、蚀斑、变色等缺陷,则不能作为合格品的判定依据。
四、观察观察的内容主要包括金属的显微组织、缺陷及其分布情况等。
对缺陷的观察应采用低倍放大镜(工作距离约30~40mm)观察,并注意缺陷的形状、大小、数量、分布情况以及与金相组织的相互关系等。
必要时可采用高倍放大镜甚至电子显微镜进行更详细的分析。
五、评级缺陷的评级应在金相显微镜下进行,评级方法应符合国家标准或行业标准的要求。
对于宏观裂纹、气孔、夹杂物等缺陷的评级,应采用目视法;对于显微疏松的评级,可采用定量法;对于晶界腐蚀的评级,可采用分级法。
评级时应注意缺陷的形状、大小、数量、分布情况以及与金相组织的相互关系等。
六、记录与分析记录的内容包括取样部位、试样的加工过程、观察到的缺陷及其分布情况等。
分析时应注意缺陷产生的原因、影响因素等,并针对具体情况提出改进措施。
七、报告报告应包括以下内容:检测项目、检测结果、分析结论等。
报告应简明扼要,数据准确可靠。
以上是宏观金相检测的基本标准,实际操作中还需要根据具体的材料、产品和使用环境等因素进行调整和优化。
金相检验标准
金相检验标准金相检验是金属材料工程中非常重要的一项检测工作,它可以帮助工程师和科研人员了解金属材料的组织结构、性能特点以及内在缺陷,从而指导材料的选用和加工工艺的优化。
金相检验标准是进行金相检验必须遵循的规范,它涵盖了金相检验的各个方面,包括样品的制备、试样的切割、研磨和腐蚀处理,金相显微镜的使用和金相组织的评定等内容。
本文将对金相检验标准进行详细介绍,以便读者更好地了解金相检验的相关知识。
首先,金相检验标准对样品的制备提出了明确的要求。
在进行金相检验之前,需要对待检材料进行切割、研磨和腐蚀处理,以便观察金相组织。
样品的制备质量直接影响着金相检验结果的准确性,因此必须严格按照标准操作,确保样品的制备达到要求。
其次,金相检验标准规定了金相显微镜的使用方法和金相组织的评定标准。
金相显微镜是进行金相检验的关键设备,它能够放大样品的微观组织结构,使人们能够清晰地观察到金属材料的晶粒、晶界、夹杂物等微观结构。
金相组织的评定标准则是根据金相显微镜下观察到的组织结构特征,对材料的组织类型、晶粒尺寸、夹杂物含量等进行评定,从而判断材料的质量和性能特点。
除了以上内容,金相检验标准还包括了金相检验的一些特殊要求,比如对特殊材料的金相检验方法、金相显微镜的技术指标要求、金相检验结果的记录和报告等。
这些内容都是金相检验过程中不可或缺的环节,对于保证金相检验结果的准确性和可靠性具有重要意义。
总的来说,金相检验标准是进行金相检验必须遵循的规范,它涵盖了金相检验的各个方面,对于确保金相检验结果的准确性和可靠性具有重要意义。
希望通过本文的介绍,读者能够更好地了解金相检验标准的相关知识,从而在实际工作中更好地进行金相检验工作,为材料的选用和加工工艺的优化提供有力的支持。
- 1、下载文档前请自行甄别文档内容的完整性,平台不提供额外的编辑、内容补充、找答案等附加服务。
- 2、"仅部分预览"的文档,不可在线预览部分如存在完整性等问题,可反馈申请退款(可完整预览的文档不适用该条件!)。
- 3、如文档侵犯您的权益,请联系客服反馈,我们会尽快为您处理(人工客服工作时间:9:00-18:30)。
1.目的通过对锻件进行金相检验,使产品质量处于受控状态,确保产品的在质量符合国家法规、标准和客户的要求。
2.适用围适用于本公司有金相试验要求的产品。
3.执行标准:①ASTM E381-01-2006 棒材、锻坯、大方坯和锻件的宏观侵蚀试验标准②ASTM E45-2013 测定钢材夹杂物含量的试验方法③ASTM E112-2013 测定平均晶粒度的标准试验方法4.检验人员必须经考核培训并取得相应岗位书。
5.检验设备:光学显微镜、放大镜6.操作程序:6.1试样的制备a)试样截取方向、部位、数量应依据检验的目的、技术标准或双方技术合同进行;b)试样的尺寸见附图;c)试样的制备:磨平磨光(粗磨、细磨)抛光浸蚀观察6.2金相检验6.2.1非金属夹杂物的检验:6.2.1.1围本标准规定了用标准图谱评定压缩比大于或等于3的轧制或锻制钢材中的非金属夹杂物的显微评定方法。
这种方法广泛用于对给定用途钢适应性的评估。
但是,由于受试验人员的影响,即使采用大量试样也很难再现试验结果,因此,使用本方法时应十分慎重。
6.2.1.2原理将所观察的视场与本标准图谱进行对比,并分别对每类夹杂物进行评级。
这些评级图片相当于100倍下纵向抛光平面上面积为0.50mm2的正方形视场。
根据夹杂物的形态和分布,标准图谱分为A、B、C、D和DS五大类。
这五大类夹杂物代表最常观察到的夹杂物的类型和形态:——A类(硫化物类):具有高的延展性,有较宽围形态比(长度/宽度)的单个灰色夹杂物,一般端部呈圆角;——B类(氧化铝类):大多数没有变形,带角的,形态比小(一般<3),黑色或带蓝色的颗粒,沿轧制方向排成一行(至少有3个颗粒);——C类(硅酸盐类):具有高的延展性,有较宽围形态比(一般≥3)的单个呈黑色或深灰色夹杂物,一般端部呈锐角;——D类(球状氧化类):不变形,带角或圆形的,形态比小(一般<3),黑色或蓝色的,无规则分布的颗粒;——DS类(单颗粒球状类):圆形或近似圆形的,直径≥13μm的单颗粒夹杂物。
非传统类型夹杂物的评定也可通过将其形状与上述五类夹杂物进行比较,并注明其化学特征。
例如:球状硫化物可作为D类夹杂物评定,但是试验报告中应加注一个下标(如:D sulf表示;D cas表示球状硫化钙;D RES表示球状稀土硫化物;D Dup表示球状复相夹杂物,如硫化钙包裹着氧化铝。
沉淀相类如棚化物、碳化物、碳氮化合物或氮化物的评定,也可以根据它们的形态与上述五类夹杂物进行比较,并按上述的方法表示它们的化学特征。
注:在进行试验之前,可采用大于100倍的放大倍率对非传统类型夹杂物进行检验,以确定其化学特征。
每类夹杂物又根据非金属夹杂物颗粒宽度的不同分成两个系列,每个系列由表示夹杂物含量递增的六级图片组成。
附录A列出了每类夹杂物的评级图谱。
评级图片级别i从0.5级到3级,这些级别随着夹杂物的长度或串(条)状夹杂物的长度(A,B,C类),或夹杂物的数量(D)类,或夹杂物的直径(DS类)的增加而递增,具体划分界限见表1。
各类夹杂物的宽度划分界限见表2。
例如:图谱A类i=2表示在显微镜下观察的夹杂物的形态属于A类,而分布和数量属于第2级图片。
表1评级界限(最小值)夹杂物的形态在很大程度上取决于钢材压缩变形程度,因此,只有在经过相似程度变形的试样坯制备的截面上才可能进行测量结果的比较。
用于测量夹杂物含量试样的抛光面面积应约为200mm2(20mm×10mm),并平行于钢材纵轴,位于钢材外表面到中心的中间位置。
取样方法应在产品标准或专门协议中规定。
对于板材,检验面应近位于其宽度的四分之一处。
如果产品标准没有规定,取样方法如下:——直径或边长大于40mm的钢棒或钢坯;检验面为钢材外表到中心的中间位置的部分径向截面;(见图1——直径或边长大于25mm、小于或等于40mm钢棒或钢坯;检验面为通过直径的截面的一半(由试样中心到边缘);(见图2)——直径或边长小于或等于25mm的钢棒:检验面为通过直径的整个截面,其长度应保证得到约200mm2的检验面积;(见图3)——厚度小于或等于25mm的钢板:检验面位于宽度1/4的全厚度截面;(见图4)——厚度大于25mm、小于或等于50mm的钢板:检验面为位于宽度的1/4和从钢板表面到中心的位置,检验面为钢板厚度的1/2截面。
(见图5)——厚度大于50mm的钢板:检验面为位于宽度的1/4和从钢板表面到中心之间的中间位置,检验面为钢板厚度的1/4截面(见图6)6.2.1.4试样制备试样应切割加工,以便获得检验面。
为了使检验面平整、避免抛光时试样边缘磨成圆角,试样可用夹具或镶嵌的方法加以固定。
试样抛光时,最重要是要避免夹杂物的剥落、变形或抛光表面被染污,以便检验面尽可能干净和夹杂物的形态不受影响。
当夹杂物细小时,上述操作要点尤其重要。
用金钢石磨料抛光是适宜的。
在某些情况下,为了使试样得到尽可能高的硬度,在抛光前试样可进行热处理。
6.2.1.5夹杂物含量的测定6.2.1.5.1观察方法在显微镜下可用下列两种方法之一检验:——投影到毛玻璃上;——用目镜直接观察。
在检验过程中应始终保持所选用的观察方法。
如果图像被投影到毛玻璃或类似装置上,必须保证放大100×±2×(在毛玻璃上)。
在毛玻璃投影屏上面或背后放一个清晰的边长为71mm的正方形(实际面积为0.50mm2)塑料轮廓线,然后用正方形的图像与标准图片(附录A)进行比较;如果用目镜检验夹杂物,则应在显微镜的适当位置上放置如图7所示试验网格,以使在图像上试验框的面积是0.50mm2。
注:在特殊情况下,可采用大于100倍的放大倍率,但对标准图谱应采用同一放大倍率,并在试验报告中注明。
6.2.1.5.2实际检验可采用下列两种方法。
6.2.1.5.2.1 A法应检验整个抛光面。
对于每一类夹杂物,按细系和粗系记下与所检验面上最恶劣视场相符合的标准图片的级别数。
6.2.1.5.2.2 B法应检验整个抛光面。
试样每一视场同标准图片相对比,每类夹杂物按细系或粗系记下与检验视场最符合的级别数(标准图片旁边所示的级别数)。
为了使检验费用降到最低,可以通过研究,减少检验视场数,并使之分布符合一定的方案,然后对试样做局部检验。
但无法是视场数,还是这些视场的分布,均应事前协议商定。
6.2.1.5.2.3 A法和B法的通则将每一个观察的视场与标准评级图谱进行对比。
如果一个视场处于两相邻标准图片之间时,应记录较低的一级。
对于个别的夹杂物和串(条)状夹杂物,如果其长度超过视场的边长(0.710mm),或宽度或直径大于粗系最大值,则应当作超尺寸(长度、宽度或直径)夹杂物进行评定,并分别记录。
但是,这些夹杂物仍应纳入该视场的评级。
为了提高实际测量(A、B、C类夹杂物的长度,DS类夹杂物的直径)的再现性,可采用图7所示的透明网格或轮廓线,并使用表1和表2规定的评级界限以及第2章有关评级图夹杂物形态的描述作为评级图片的说明。
非传统类型夹杂物按与其形态最接近的A、B、C、D、DS类夹杂物评定。
将非传统类别夹杂物的长度、数量、宽度或直径与评级图片上每类夹杂物进行对比,或测量非传统类型夹杂物的总长度、数量、宽度或直径,使用表1和表2选择与夹杂物含量相应的级别或宽度系列(细、粗或超尺寸),然后在表示该类夹杂物的符号后加注下标,以表示非传统类型夹杂物的特征,并在试验报告中注明下标的含义。
对于A、B和C类夹杂物,用L1和L2分别表示两个在或者不在一条直线上的夹杂物或串(条)状夹杂物的长度,如果两夹杂物之间的纵向距离d小于或等于40mm且沿轧制方向的横向距离s(夹杂物中心之间的距离)小于或等于10mm 时,则应视为一条夹杂物或串(条)状夹杂物。
如果一个串(条)状夹杂物夹杂物的宽度不同,则应将该夹杂物的最大宽度视频为该串(条)状夹杂物的宽度。
6.2.1.5.3结果表示6.2.1.5.3.1通则除非在产品标准中已指明,检验结果可按下述方法表示。
用每个试样的级别以及在此基础上所得的每炉钢每类和每个宽度系列夹杂物的级别算术平均值来表示结果。
这种方法与5.2.1所述的方法结合使用。
6.2.1.5.3.2 A法表示与每类夹杂物和每个宽度系列夹杂物最恶劣视场符合的级别。
在每类夹杂物代号后再加上最恶劣视场的级别,用字母e表示出现粗系的夹杂物,s表示出现超尺寸夹杂物。
例如:A2,Ble,C3,D1,B2,5s,DS0.5。
用于表示非传统类型的夹杂物下标应注明其含义。
6.2.1.5.3.3 B法表示给定观察视场数(N)中每类夹杂物及每个宽度系列夹杂物在给定级别上的视场总数。
对于所给定的各类夹杂物的级别,可用所有视场的全套数据,按专门的方法来表示其结果,如根据双方协议规定总级别(i tot)或平均级别(i moy)。
例如:A类夹杂物级别为0.5的视场数为n1;级别为1的视场数为n2;级别为1.5的视场数为n3;级别为2的视场数为n4;级别为2.5的视场数为n5;级别为3的视场数为n6;则i tot=(n1×0.5)+ (n2×1)+ (n3×1.5)+ (n4×2)+ (n5×2.5)+ (n6×3)i moy=i tot/N式中:N为所观察视场的总数。
典型夹杂物结果列于附录C。
6.2.1.5.4试验报告试验报告应包括如下各项:a)本标准号;b)钢的牌号和炉号;c)产品类型和尺寸;d)取样方法及检验面位置;e)选用的方法(观察方法、检验方法、结果表示方法);f)放大倍率(如果大于100倍时);g)观察的视场数或总检验面积;h)各项检验结果(夹杂物或串(条)状夹杂物的尺寸超过标准评级图者应予以注明);i)对非传统类型夹杂物所采用的下标的说明;j)试验报告编号和日期;k)试验员。
依据ASTM E45-2013 钢中非金属夹杂物含量的测定标准评级图显微检验法,观察整个受检面,选取有代表性的视场,按夹杂物的形态、大小、数量进行评级;评级图见标准。
6.2.2钢质模锻件金相组织检验:6.2.2.1围本标准规定了钢质模锻件的金相组织评级图(以下简称评级图)及评定方法。
本标准适用于经过调质处理、正火处理、等温正火处理、锻后控冷处理的结构钢模锻件。
本标准不适用于对锻件脱碳、过热、过烧等组织的评定。
6.2.2.2术语和定义下列术语和定义适用于本标准。
6.2.2.2.1等温正火isothermal normalization将锻件加热到高于A C3(或A C1)的某一温度,保温一段时间后,控制冷却到珠光体相变区某一温度并等温保持一段时间,使奥氏体转变为珠光体型组织,然后在空气中冷却的热处理工艺。
6.2.2.2.2锻后控冷control cooling after forging锻件在锻造成型后,利用余热通过控制锻件的冷却速度,使其得到珠光体加铁素体组织或贝氏体组织的工艺方法。