混凝土泵送造成堵管的原因及预防措施
泵送混凝土堵管的防治措施
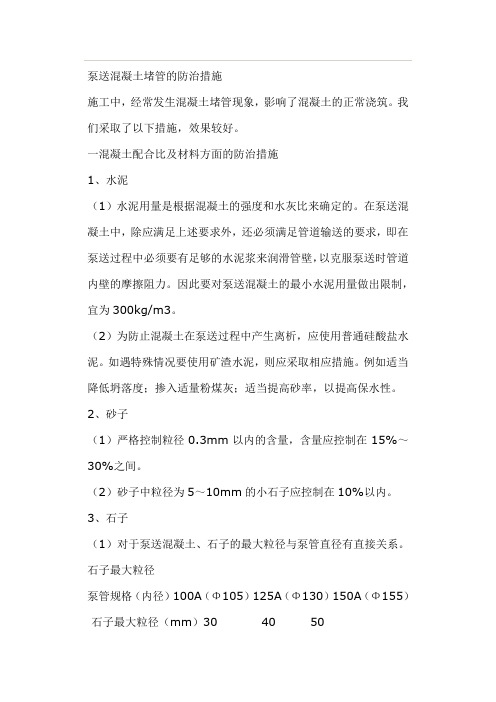
泵送混凝土堵管的防治措施施工中,经常发生混凝土堵管现象,影响了混凝土的正常浇筑。
我们采取了以下措施,效果较好。
一混凝土配合比及材料方面的防治措施1、水泥(1)水泥用量是根据混凝土的强度和水灰比来确定的。
在泵送混凝土中,除应满足上述要求外,还必须满足管道输送的要求,即在泵送过程中必须要有足够的水泥浆来润滑管壁,以克服泵送时管道内壁的摩擦阻力。
因此要对泵送混凝土的最小水泥用量做出限制,宜为300kg/m3。
(2)为防止混凝土在泵送过程中产生离析,应使用普通硅酸盐水泥。
如遇特殊情况要使用矿渣水泥,则应采取相应措施。
例如适当降低坍落度;掺入适量粉煤灰;适当提高砂率,以提高保水性。
2、砂子(1)严格控制粒径0.3mm以内的含量,含量应控制在15%~30%之间。
(2)砂子中粒径为5~10mm的小石子应控制在10%以内。
3、石子(1)对于泵送混凝土、石子的最大粒径与泵管直径有直接关系。
石子最大粒径泵管规格(内径)100A(Φ105)125A(Φ130)150A(Φ155)石子最大粒径(mm)30 40 50(2)石子采用连续级配,保证石子之间的空隙率和砂浆用量;针片状颗粒含量不宜大于10%。
4、砂率砂率为混凝土中粗细骨料之间的关系,砂率变化会使混凝土和和易性产生变化,影响混凝土泵送性。
砂率可按下式计算。
砂率=细骨料/(粗骨料+细骨料)×100%。
泵送混凝土的砂率宜为38%~45%。
5、水灰比水灰比即为混凝土中水与水泥用量的比值,设计配合比时应保证设计强度和泵送混凝土所需的坍落度,且不发生离析。
泵送混凝土的水灰比宜为0.4~0.6。
6、泵送剂泵送剂应根据每盘的用量,提前装袋,保证泵送剂用量的准确。
二、台设备影响泵送效果的防治措施1、砂子、石子由料斗投入配料斗的顺序改为先投石子、再投砂子。
这样可以避免砂子过湿时沾在料斗上,从而保证砂子用量。
2、输送泵地坑不宜过深,输送泵混凝土出口应与地面水平布管高度项适宜,以避免混凝土因出口过低而影响混凝土的初速度。
泵送混凝土在施工中易出现的问题及防治

泵送混凝土在施工中易出现的问题及防治泵送混凝土是现代建筑施工中的一项重要工艺,它可以降低施工成本,提高施工效率,但同时也存在一些问题,如果不及时防治,就会对施工质量和安全产生影响。
下面就是泵送混凝土在施工中易出现的问题及防治方法。
一、混凝土泵堵塞混凝土泵堵塞一般都是由于混凝土中的固体颗粒过大或沉积在泵管弯头处引起的。
堵塞现象非常严重,如果处理不当,就会使混凝土泵发生管道炸裂、沉积等情况,严重危及施工安全。
因此,防治混凝土泵堵塞是十分重要的。
防治方法:1、设计合理的配合比和粘度,避免混凝土密实和易结块,以减少管道的摩擦力。
2、使用高质量的混凝土,避免使用过期或劣质的混凝土。
3、在泵送混凝土前,要检查泵道内是否有杂物,如有杂物必须清除干净,以避免引起管道堵塞。
二、泵送混凝土的坍落度过低坍落度过低是指混凝土在泵送过程中坍落度下降,造成泵送阻力加大,从而导致泵发送生卡顿、停顿等不良反应。
通常情况下,泵送混凝土时的坍落度应当控制在8-15cm,否则将会影响施工效率。
防治方法:1、严格按照混凝土的设计配合比进行施工,在施工过程中控制水灰比,避免混凝土坍落度过低。
2、混凝土在泵送前需要经过充分的搅拌,以克服混凝土颗粒之间的内部摩擦力。
3、在泵送混凝土时可以添加流动性剂、减水剂等辅助剂来提高混凝土的坍落度,降低其粘度,从而达到更好的泵送效果。
三、管道磨损泵送混凝土时,管道内的混凝土将高速流动,如果管道质量不好或运输时管道与拖车摩擦,就会引起管道的磨损和变形,从而影响施工效果。
防治方法:1、采用耐磨性好的材料进行管道制造,如铸铁、钢等材料,尽量减少使用塑料、橡胶等易损耗材料。
2、管道的支架及接头必须牢固、可靠,防止管道发生位移、震动等情况。
3、运输过程中要对管道进行严格的包装和保护,避免管道与运输工具摩擦,产生磨损和变形。
四、安全隐患泵送混凝土有很多危险因素,例如:管道炸裂、人员伤亡、电击等。
这些危险因素可能会对施工人员和现场环境产生严重影响。
泵送混凝土堵管的原因及处理方法

泵送混凝土堵管的原因及处理方法
泵送混凝土时出现堵管情况是施工中常见的问题之一,主要原因有以下几个方面:
1. 混凝土配合比不合理:混凝土配合比中水灰比过小,粉煤灰含量过高,砂粒过细等都会增加混凝土的黏性,容易堵塞管道。
2. 混凝土含水量过大:混凝土的含水量过大会导致混凝土流动性差,易产生堵塞现象。
3. 混凝土粒径不合适:过大或过小的混凝土颗粒会增加阻力,阻碍混凝土的流动,从而造成堵塞。
4. 管道磨损:长时间使用的泵送管道内壁会产生磨损,导致管道粗糙度增加,容易产生堵塞。
针对堵管问题,可采取以下处理方法:
1. 调整混凝土配合比:合理设计混凝土配合比,增加水灰比和粉煤灰含量,使用适当的砂粒粒径,提高混凝土的流动性,减少堵塞风险。
2. 控制混凝土含水量:在施工中严格控制混凝土的含水量,确保其
流动性能良好,减少堵塞的可能性。
3. 清洗管道:定期对泵送管道进行清洗,去除管道内的混凝土渣滓和堵塞物,保持管道的畅通。
4. 更换管道:如果管道磨损严重,影响混凝土的流动性,应及时更换管道,确保施工的顺利进行。
5. 控制泵送速度:适当控制泵送速度,避免过快或过慢,以减少堵塞的风险。
总之,对于泵送混凝土堵管问题,需要从混凝土配合比、含水量、管道磨损等多个方面进行综合考虑,并采取相应的处理措施,确保施工过程的顺利进行。
混凝土泵送堵管的原因分析及预防措施

混凝土泵送堵管的原因分析及预防措施一、原因分析1.混凝土过于干燥:混凝土过于干燥会造成泵送困难,增加摩擦阻力,容易导致堵塞。
2.混凝土中含有大颗粒物料:混凝土中含有大颗粒物料,会增大泵送阻力,容易引发堵管。
3.管道内积聚物:在连续施工的过程中,管道内会积聚一些混凝土渣块和杂物,堵塞管道,使得混凝土无法正常泵送。
4.泵送压力过大:泵送压力过大会导致管道内混凝土堵塞,阻力增大,影响泵送效果。
5.泵送管道弯曲过多:管道过度弯曲会增加摩擦阻力,容易造成堵管。
6.泵送速度过快:泵送速度过快会导致混凝土流动不畅,堵塞管道。
二、预防措施1.控制混凝土的配合比:合理的配合比可以有效控制混凝土的流动性,避免混凝土过于干燥,减少泵送堵塞的风险。
2.筛选合适的骨料:在施工前筛选合适的骨料,避免大颗粒物料进入混凝土中,减少堵管的可能性。
3.定期清理管道:定期清理管道内的混凝土渣块和杂物,保持管道的畅通,减少泵送堵塞的风险。
4.控制泵送压力:合理控制泵送压力,避免泵送压力过大引发管道堵塞。
5.控制管道弯曲度:合理规划管道布置,控制管道弯曲度,减少摩擦阻力,降低堵管的可能性。
6.控制泵送速度:控制泵送速度,避免速度过快造成混凝土流动不畅,堵塞管道。
7.定期检测管道:定期对泵送管道进行检测,及时发现并修复管道问题,确保泵送畅通。
8.增加润滑剂:在混凝土中加入适量的润滑剂,降低摩擦阻力,增加流动性,减少堵塞的风险。
9.配备清洗设备:为了应对堵管情况,配备相应的清管设备,及时进行清理,保证泵送的正常进行。
总之,混凝土泵送堵管问题的发生与多种因素有关,需要综合考虑。
以上提出的预防措施,旨在减少堵管的风险,提高混凝土泵送的效率与质量。
在实践中,还可以根据具体情况结合经验进行相应的调整和改进。
混凝土泵送堵泵原因分析及解决方法

混凝土泵送堵泵原因分析及解决方法导言使用过混凝土输送泵的人都知道,在使用过程中都不可避免的会出现堵管现象。
那么到底是什么原因造成了堵管问题呢?我们应如何合理解决呢?堵管原因1.操作不当操作人员精力不集中;泵送速度选择不当;余料量控制不适当;混凝土的坍落度过小时采取措施不当;停机时间过长。
2.管道未清洗干净3.管道连接不当4.混凝土或砂浆的离析5.局部漏浆造成的堵管输送管道接头密封不严;眼镜板和切割环之间的间隙过大;混凝土活塞磨损严重;因混凝土输送缸严重磨损而引起的漏浆。
6.非合格的泵送混凝土导致的堵管混凝土坍落度过大或过小;含砂率过小、粗骨料级配不合理;水泥用量过少或过多;外加剂的选用不合理。
解决措施1.合理布管和操作(1)根据工程需要,领用足够的管道、管箍、橡胶密封圈等用品。
(2)服从前场工长指挥,按泵机安全操作规程操作,根据现场实际情况合理布管。
(3)泵机连接直管不得小于10m,尽量减少弯头,软管后不得连接6m以上的直管。
(4)严禁软管做弯管使用,生产中软管不得小于90°使用。
(5)操作过程必须配戴好安全帽,穿好工作服。
2.防止混凝土泵送过程中管路跳动(1)泵送连接平管,每10m应浇筑600mm×400mm×400mm混凝土稳定墩,固定混凝土泵管至立管位置。
(2)立管必须用钢管架牢固,并每班检查,合格后使用。
(3)在泵送过程中,应沿管路检查管道有无磨损、管卡有无松动、橡胶密封圈有无破损和漏浆、漏气现象。
3.防止堵管的措施(1)生产结束后,清理所有管道,拆除立管以下所有管道,清除管内沉积的残留物。
(2)卡箍、密封胶圈按规范装置,不得漏浆、漏气。
(3)向下布管时不得按90°垂直敷设管道,应按30°~45°倾斜布管。
(4)当敷设较长的管路时,应尽可能减少弯管、软管的数量和弯管的度数,当不得不采用90°弯管时,应尽可能使用半径为1m的90°弯管。
混凝土泵送堵管原因及预防措施分析

混凝土泵送堵管原因及预防措施分析泵送混凝土在受场地条件限制及大型砼施工中应用广泛,但是在混凝土泵送环节容易出现堵塞问题,如果不能彻底处理,不仅影响施工进程,还会导致工程质量下降。
下面就混凝土泵送堵管原因及具体的预防措施进行分析。
一、分析混凝土泵送堵管的原因(1)工作人员操作不当进行混凝土输送中,对输送泵的操作质量要求很高,如果操作人员精力不集中,或者责任心不强,工作状态不好,就容易出现操作失误问题,进而发生混凝土堵管问题。
例如混凝土泵送时,如果粗心大意,没有观察到压力表数值发生了明显的变化,发生了堵管问题,那么造成的后果非常严重。
(2)没有科学设定泵送速度进行泵送操作中,合理选择泵送的速度至关重要,操作时不能只求速度,不顾质量。
在很多情况下发现速度越快,问题越多,欲速则不达,事与愿违。
例如操作人员进行第一次送泵时,管道内壁的阻力很大,但是操作人员不清楚,或者没有严格根据要求操作,泵的转速调整到最大,由于管道摩擦阻力大,导致整体运行的摩擦力大,管道接口容易出现脱节问题,或者泵的发动机容易出现过载问题,导致发动机出现故障。
(3)控制余量方面的问题进行混凝土送泵操作中,现场人员要随时注意料斗中的混凝土余量,剩余量不能比搅拌轴还低,但是很多操作人员都没有注意到这一点,检查时发现料斗余量比搅拌轴还低,这样就容易将空气吸入其中,导致管道的堵塞。
通过数据显示,有5%的故障和问题都是由料斗余量控制不合理导致的。
(4)管道连接方面的问题如果管道连接不合理,就容易导致管道堵塞,进行管道连接时,必须进行严格的检查,避免发生一些低级错误。
连接管道要正规,避免增加阻力。
但是现实中操作人员经常出现低级错误,管道布置不合理,距离很长,管道出现弯折,泵送中途接管时直接增加两个管等,导致运行中经常出现故障,影响工作效率。
(5)混凝土离析造成的堵管通过工作经验总结,如果砂浆、混凝土遇水,就易发生管道堵塞问题,除此之外,正在进行砂浆泵送时,容易出现管道堵塞。
泵送混凝土堵管的原因分析及预防措施
网格 间距0 m X . 喷射C 5 , . 02 2 m, 2 砼 厚度2 c 当扩挖至斜井 I 5m; = I
的设计 、 比选 , 最终确定采用爬坡 中导洞进 入正洞顶部 , 形成台
阶施工断面后 , 反向挑顶扩大形成 隧道正式施工断面的施工方
达正洞顶部 : 坡度为2 %、 O 向前施工 lm, O 创造 出施工空间后 , 再 处 ,将主洞上半断面钢架架 没在斜井 口处的门式钢横梁上 , 并 按正洞 的施工断面反向开挖 ,边挖边拆除爬坡 导坑再 临时支 焊接牢 固。正洞落底要及 时进行正洞仰拱施工, 以便初期支护
护 , 至 跨过 斜井 范 围 , 斜 井 向正 洞 的过 渡 。 直 完成
摘
要
关键 词
近年来 , 随着我国公路建设 的发 展和城市建筑 、 城市 环保 的需要 , 对混凝土产品的质量要 求越 来越 高 , 因而混凝 土采用 泵送施工 , 可以有效地保证 产品的质量。如何 防止和控制泵送 混凝土在泵送过程中发生堵管现象 , 显得十分重要。
分析 堵管 的原 因 1 . 不 当容 易造 成 堵 管 。 操作
o ●o ●o ●o ●・ ●o ●・ ● — ●o ●0 ●o ●o ●o ●o ●0 ●<> ・◇ ●0 ・0 ● 0 ●o ●0 ●0 ●0
l 余料量控制不适 当。 _ 3 泵送时 , 操作人员须随时观察料斗 中的余料 , 余料不得低于搅拌轴 。如果余 料太 少 , 极易吸人空
32 工 方 法。 .施
与仰拱尽早成环 , 确保施工安全。
4监控 量 测 .
混凝土泵堵管原因分析及控制措施
混凝土泵堵管原因分析及控制措施混凝土泵是一种将混凝土从搅拌站输送到施工现场的设备。
然而,由于各种原因,混凝土泵在工作过程中可能会出现管道堵塞的情况。
本文将就混凝土泵堵管的原因进行分析,并介绍相应的控制措施。
一、堵管原因分析1.混凝土质量问题:如果混凝土的配合比例不合理,或者掺有过多的泥浆和杂质,就容易造成堵管。
此外,混凝土中的颗粒过大,也容易导致泵管堵塞。
2.施工操作不当:在施工过程中,如果操作不当,例如混凝土泵的进料速度过大、管道弯曲角度过小、管道内的气压不稳定等,都会导致混凝土泵堵塞。
3.泵送距离过远:混凝土泵的管道长度限制了泵送距离。
如果超过了泵送距离的限制,就容易造成堵管现象。
二、控制措施1.选用合适的混凝土:在施工前应根据实际情况选择合适的混凝土配合比例,并确保混凝土的质量符合要求。
此外,混凝土中的颗粒大小应适中,以免造成管道堵塞。
2.加强施工管理:在施工过程中,应加强对混凝土泵的操作指导,确保操作人员按照正确的方式进行操作。
例如,控制混凝土泵的进料速度和管道的弯曲角度,保持管道内的气压稳定等。
3.控制泵送距离:在施工前应对泵送距离进行合理规划,确保不超过混凝土泵的管道限制。
如果需要泵送距离较远,可以适当增加泵送设备或采用其他辅助措施,如分段泵送、增加管道直径等。
除了以上的控制措施之外,还可以采用以下几种方法来解决混凝土泵堵管问题:1.冲击管道:如遇到轻微的堵塞情况,可以通过向堵塞部位喷水或用气压冲击的方式进行疏通。
2.更换泵送管道:如堵塞较严重,无法通过冲击疏通,则需要更换泵送管道。
3.清洗管道:定期对混凝土泵的管道进行清洗,以去除管道内的混凝土残留物,并保持管道畅通。
总之,要想有效控制混凝土泵堵管问题,首先需要保证混凝土的质量和施工操作的正确性。
此外,合理规划泵送距离、定期清洗管道等措施也是必不可少的。
只有通过科学有效的控制措施,才能降低混凝土泵堵管的发生率,提高施工效率。
混凝土堵管原因分析及改进措施
混凝土堵管原因分析及改进措施一、造成堵管原因:a、现场准备不充分,泵管接头布置不合理,换管慢;b、现场施工人员技术不熟练,换管慢、堵管后处理慢,泵车司机不是专业司机;c、泵管气密性可能有问题,接头处有漏水现象;d、气温高,混凝土塌落度损失不易控制,可泵性降低,混凝土初凝时间缩短也更加容易产生施工缝。
二、下一步改进措施1、调整浇注时间,尽量选择晚饭后开盘,避开白天高温时段浇注二衬,争取第二天天亮前完成浇筑。
2、加强施工现场与拌合站的信息沟通,要求根据现场情况确定第三车混凝土的开始拌合时间。
由现场值班经理或技术员与拌合站调度电话联系。
一般在当车混凝土泵送顺利的情况下开始第三车拌合。
3、提前做好施工现场的准备:a、人员配备:泵车司机1人、振捣工2人、模板观察及加固2人、混凝土卸料1人、换管3人(其中一个熟练)、现场指挥调度1人,共10人。
b、设备方面:维修保养地泵主机;将泵管清理干净,检查泵管气密性,更换老化的橡胶垫圈;检查软管内管壁,是否光滑,否则要更换,软管长度在满足现场需要的前提下应尽量短;合理布置泵管,尽量减少弯头。
通过以上准备工作,确保泵送系统可靠。
同时准备振捣棒3台(用于边墙振捣),附着式振捣器4台(拱顶交错布置)。
台车:提前布置好拱顶泵管接头;丝杆在振捣完成后由模板观察员紧固,下侧模板铰接处和底部加撑方木;推出台车,重新打磨模板,刷油,保证刷油后3天内浇注混凝土,建议在脱模所用的新机油内掺加少量柴油。
模板铰接处有错台,要求用砂轮机打磨一下。
测量人员应对模板尺寸、弧度进行检查,检测第一板混凝土浇筑后台车模板是否有变形。
现场准备:所有施工缝,混凝土接触面须提前凿毛;两板接触位置,台车模板面与既有二衬表面之间应贴密封条。
4、做好施工过程控制试验方面:泵送混凝土的塌落度一般控制在14-18cm,要求混凝土到场塌落度按18cm控制。
试验人员根据塌落度损失情况,确定混凝土的出站塌落度。
若现场塌落度过小,依照施工技术指南可在技术员指导下添加减水剂,以改善混凝土塌落度,使其满足泵送要求。
混凝土输送泵的堵泵原因及预防措施解决办法
避免使用不合格的骨 料和外加剂,以免影 响混凝土的稳定性。
管道预防措施
使用合格的管道,并确保其符 合相关标准和规范。
在安装管道时,要确保管道连 接牢固、密封良好,避免出现 松动或漏气现象。
定期检查管道的磨损和老化情 况,及时更换损坏的管道。
泵车预防措施
泵车操作人员需经过专业培训, 熟练掌握操作技能和维护方法。
防止混凝土离析
离析是指混凝土中的粗骨料和细骨 料分离,导致泵送困难。应采取措 施防止离析,如适当加入外加剂或 调整配合比。
管道解决方案
管道清洗
每次泵送完成后,应立即清洗管道,防止残留物堵塞管道。
管道安装
管道安装不当容易造成堵泵,应按照规范安装管道,避免出现弯 折、扭曲等现象。
管道维护
定期对管道进行检查和维护,及时更换损坏的管道部件。
在操作过程中,要密切关注泵车 的运行状态和压力变化,发现异
常及时停机检查。
定期对泵车进行维护和保养,确 保其机械部件正常运转。
03
CATALOGUE
解决方案
混凝土解决方案
保证混凝土质量
使用质量稳定、级配良好的混 凝土,避免使用不合格的混凝
土。
控制混凝土坍落度
坍落度是混凝土的重要参数,坍落 度过小容易导致堵泵,应适当调整 坍落度。
混凝土输送泵的 堵泵原因及预防 措施解决办法
汇报人: 日期:
目录
• 堵泵原因分析 • 预防措施 • 解决方案 • 案例分析
01
CATALOGUE
堵泵原因分析
混凝土因素
01 02
粗骨料最大粒径过大
粗骨料的最大粒径过大是造成混凝土输送泵堵泵的主要原因之一。粗骨 料的最大粒径过大,会增大输送管道的阻力,导致混凝土难以通过管道 ,从而引起堵泵。
- 1、下载文档前请自行甄别文档内容的完整性,平台不提供额外的编辑、内容补充、找答案等附加服务。
- 2、"仅部分预览"的文档,不可在线预览部分如存在完整性等问题,可反馈申请退款(可完整预览的文档不适用该条件!)。
- 3、如文档侵犯您的权益,请联系客服反馈,我们会尽快为您处理(人工客服工作时间:9:00-18:30)。
混凝土泵送造成堵管的原因及预防措施
一、管道连接原因导致堵管
堵管原因:管道接法错误。
预防措施:(1)管道布置时应按最短距离、最少弯头和最大弯头来布管,尽量减小输送阻力,也就减少了堵管的可能性。
(2)泵出口锥管处,不许直接接弯管,至少应接入5mm 以上直管后,再接弯管。
(3)泵送中途接管时,每次只能加接一根,且应用水润滑一下管道内壁,并排尽空气,否则极易造成堵管。
二、混凝土或砂浆离析
堵管原因:混凝土或砂浆遇水,造成离析。
预防措施:泵前用水湿润管道后,从管道的最低点将管道接头松开,将余水全部放掉,或者在泵水之后,泵送砂浆之前,放入一海绵球,将砂浆与水分开。
三、局部漏浆
1.堵管原因:输送管道接头密封不严。
预防措施:紧固管卡或更换密封圈。
2.堵管原因:眼镜板和切割环之间间隙过大。
预防措施:调整异形螺栓来缩小眼镜板和切割环之间的间隙,若已无法调整,应立即更换磨损件(本法仅适用于“S”阀系列混凝土泵)。
3.堵管原因:混凝土活塞磨损严重。
预防措施:操作人员须经常观察水箱中的水是否浑浊、有无砂浆,一旦发现水已浑浊或水中有砂浆,表明混凝土活塞已经磨损,应及时更换。
4.堵管原因:混凝土输送缸磨损严重。
预防措施:每次更换活塞后,观察水箱中的水是否很快变浑浊,若是,而活塞是好的,则表明输送缸已磨损,此时应及时换输送缸。
5.堵管原因:眼镜板和切割环之间间隙过大。
预防措施:调整异形螺栓来缩小眼镜板和切割环之间的间隙,若已无法调整,应立即更换磨损件(本法仅适用于“S”阀系列混凝土泵)。
四、非合格泵送混凝土
1.堵管原因:混凝土坍落度过大或过小。
预防措施:泵送混凝土的塌落度一般应控制在8~18cm范围内,对于长距离和大高度的泵送一般须严格控制在15cm左右。
2.堵管原因:含砂率过小、粗骨料级配不合理。
预防措施:含砂率不宜太低,应大于0%,大粒径粗骨料的含量不宜过高。
卵石的最大粒径应小于1/3口径,碎石的最大粒径应小于1/4口径,否则也易引起堵管。
3.堵管原因:水泥用量不当。
预防措施:将每m³混凝土中水泥的含量控制在大于320kg,但也不能过大。
水泥用量过大,将会增加混凝土的粘性,从而造成输送阻力的增加。
五、砂浆量太少或配比不合
1.堵管原因:砂浆用量太少。
预防措施:泵送前一定要计算好砂浆的用量。
砂浆太少易堵管,砂浆太多将影响混凝土的质量或造成不必要的浪费。
2.堵管原因:砂浆配合比不合格。
预防措施:当管道长度低于150m时,用1:2的水泥砂浆(1份水泥/2份砂浆);当管道长度大于150m时,用1:1 的水泥砂浆(1份水泥/1份砂浆),水泥用量太少也会造成堵管。
六、气温变化
堵管原因:气温变化快且缺少预防。
预防措施:夏季在管道上应加盖湿草袋或其他降温用品。
冬季应采取保温措施,确保混凝土的温度。