混凝土泵送堵管的原因与预防措施
混凝土泵送造成堵管的原因及预防措施

混凝土泵送造成堵管的原因及预防措施一、管道连接原因导致堵管堵管原因:管道接法错误。
预防措施:(1)管道布置时应按最短距离、最少弯头和最大弯头来布管,尽量减小输送阻力,也就减少了堵管的可能性。
(2)泵出口锥管处,不许直接接弯管,至少应接入5mm 以上直管后,再接弯管。
(3)泵送中途接管时,每次只能加接一根,且应用水润滑一下管道内壁,并排尽空气,否则极易造成堵管。
二、混凝土或砂浆离析堵管原因:混凝土或砂浆遇水,造成离析。
预防措施:泵前用水湿润管道后,从管道的最低点将管道接头松开,将余水全部放掉,或者在泵水之后,泵送砂浆之前,放入一海绵球,将砂浆与水分开。
三、局部漏浆1.堵管原因:输送管道接头密封不严。
预防措施:紧固管卡或更换密封圈。
2.堵管原因:眼镜板和切割环之间间隙过大。
预防措施:调整异形螺栓来缩小眼镜板和切割环之间的间隙,若已无法调整,应立即更换磨损件(本法仅适用于“S”阀系列混凝土泵)。
3.堵管原因:混凝土活塞磨损严重。
预防措施:操作人员须经常观察水箱中的水是否浑浊、有无砂浆,一旦发现水已浑浊或水中有砂浆,表明混凝土活塞已经磨损,应及时更换。
4.堵管原因:混凝土输送缸磨损严重。
预防措施:每次更换活塞后,观察水箱中的水是否很快变浑浊,若是,而活塞是好的,则表明输送缸已磨损,此时应及时换输送缸。
5.堵管原因:眼镜板和切割环之间间隙过大。
预防措施:调整异形螺栓来缩小眼镜板和切割环之间的间隙,若已无法调整,应立即更换磨损件(本法仅适用于“S”阀系列混凝土泵)。
四、非合格泵送混凝土1.堵管原因:混凝土坍落度过大或过小。
预防措施:泵送混凝土的塌落度一般应控制在8~18cm范围内,对于长距离和大高度的泵送一般须严格控制在15cm左右。
2.堵管原因:含砂率过小、粗骨料级配不合理。
预防措施:含砂率不宜太低,应大于0%,大粒径粗骨料的含量不宜过高。
卵石的最大粒径应小于1/3口径,碎石的最大粒径应小于1/4口径,否则也易引起堵管。
泵送混凝土堵管的原因及处理方法

泵送混凝土堵管的原因及处理方法
泵送混凝土时出现堵管情况是施工中常见的问题之一,主要原因有以下几个方面:
1. 混凝土配合比不合理:混凝土配合比中水灰比过小,粉煤灰含量过高,砂粒过细等都会增加混凝土的黏性,容易堵塞管道。
2. 混凝土含水量过大:混凝土的含水量过大会导致混凝土流动性差,易产生堵塞现象。
3. 混凝土粒径不合适:过大或过小的混凝土颗粒会增加阻力,阻碍混凝土的流动,从而造成堵塞。
4. 管道磨损:长时间使用的泵送管道内壁会产生磨损,导致管道粗糙度增加,容易产生堵塞。
针对堵管问题,可采取以下处理方法:
1. 调整混凝土配合比:合理设计混凝土配合比,增加水灰比和粉煤灰含量,使用适当的砂粒粒径,提高混凝土的流动性,减少堵塞风险。
2. 控制混凝土含水量:在施工中严格控制混凝土的含水量,确保其
流动性能良好,减少堵塞的可能性。
3. 清洗管道:定期对泵送管道进行清洗,去除管道内的混凝土渣滓和堵塞物,保持管道的畅通。
4. 更换管道:如果管道磨损严重,影响混凝土的流动性,应及时更换管道,确保施工的顺利进行。
5. 控制泵送速度:适当控制泵送速度,避免过快或过慢,以减少堵塞的风险。
总之,对于泵送混凝土堵管问题,需要从混凝土配合比、含水量、管道磨损等多个方面进行综合考虑,并采取相应的处理措施,确保施工过程的顺利进行。
混凝土泵送堵管的原因分析及预防措施

混凝土泵送堵管的原因分析及预防措施一、原因分析1.混凝土过于干燥:混凝土过于干燥会造成泵送困难,增加摩擦阻力,容易导致堵塞。
2.混凝土中含有大颗粒物料:混凝土中含有大颗粒物料,会增大泵送阻力,容易引发堵管。
3.管道内积聚物:在连续施工的过程中,管道内会积聚一些混凝土渣块和杂物,堵塞管道,使得混凝土无法正常泵送。
4.泵送压力过大:泵送压力过大会导致管道内混凝土堵塞,阻力增大,影响泵送效果。
5.泵送管道弯曲过多:管道过度弯曲会增加摩擦阻力,容易造成堵管。
6.泵送速度过快:泵送速度过快会导致混凝土流动不畅,堵塞管道。
二、预防措施1.控制混凝土的配合比:合理的配合比可以有效控制混凝土的流动性,避免混凝土过于干燥,减少泵送堵塞的风险。
2.筛选合适的骨料:在施工前筛选合适的骨料,避免大颗粒物料进入混凝土中,减少堵管的可能性。
3.定期清理管道:定期清理管道内的混凝土渣块和杂物,保持管道的畅通,减少泵送堵塞的风险。
4.控制泵送压力:合理控制泵送压力,避免泵送压力过大引发管道堵塞。
5.控制管道弯曲度:合理规划管道布置,控制管道弯曲度,减少摩擦阻力,降低堵管的可能性。
6.控制泵送速度:控制泵送速度,避免速度过快造成混凝土流动不畅,堵塞管道。
7.定期检测管道:定期对泵送管道进行检测,及时发现并修复管道问题,确保泵送畅通。
8.增加润滑剂:在混凝土中加入适量的润滑剂,降低摩擦阻力,增加流动性,减少堵塞的风险。
9.配备清洗设备:为了应对堵管情况,配备相应的清管设备,及时进行清理,保证泵送的正常进行。
总之,混凝土泵送堵管问题的发生与多种因素有关,需要综合考虑。
以上提出的预防措施,旨在减少堵管的风险,提高混凝土泵送的效率与质量。
在实践中,还可以根据具体情况结合经验进行相应的调整和改进。
泵送混凝土施工通病原因分析与预防策略
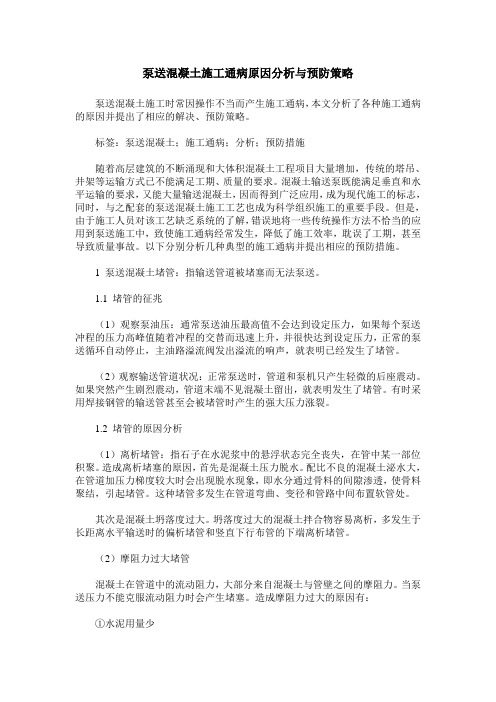
泵送混凝土施工通病原因分析与预防策略泵送混凝土施工时常因操作不当而产生施工通病,本文分析了各种施工通病的原因并提出了相应的解决、预防策略。
标签:泵送混凝土;施工通病;分析;预防措施随着高层建筑的不断涌现和大体积混凝土工程项目大量增加,传统的塔吊、井架等运输方式已不能满足工期、质量的要求。
混凝土输送泵既能满足垂直和水平运输的要求,又能大量输送混凝土,因而得到广泛应用,成为现代施工的标志,同时,与之配套的泵送混凝土施工工艺也成为科学组织施工的重要手段。
但是,由于施工人员对该工艺缺乏系统的了解,错误地将一些传统操作方法不恰当的应用到泵送施工中,致使施工通病经常发生,降低了施工效率,耽误了工期,甚至导致质量事故。
以下分别分析几种典型的施工通病并提出相应的预防措施。
1 泵送混凝土堵管:指输送管道被堵塞而无法泵送。
1.1 堵管的征兆(1)观察泵油压:通常泵送油压最高值不会达到设定压力,如果每个泵送冲程的压力高峰值随着冲程的交替而迅速上升,并很快达到设定压力,正常的泵送循环自动停止,主油路溢流阀发出溢流的响声,就表明已经发生了堵管。
(2)观察输送管道状况:正常泵送时,管道和泵机只产生轻微的后座震动。
如果突然产生剧烈震动,管道末端不见混凝土留出,就表明发生了堵管。
有时采用焊接钢管的输送管甚至会被堵管时产生的强大压力涨裂。
1.2 堵管的原因分析(1)离析堵管:指石子在水泥浆中的悬浮状态完全丧失,在管中某一部位积聚。
造成离析堵塞的原因,首先是混凝土压力脱水。
配比不良的混凝土泌水大,在管道加压力梯度较大时会出现脱水现象,即水分通过骨料的间隙渗透,使骨料聚结,引起堵管。
这种堵管多发生在管道弯曲、变径和管路中间布置软管处。
其次是混凝土坍落度过大。
坍落度过大的混凝土拌合物容易离析,多发生于长距离水平输送时的偏析堵管和竖直下行布管的下端离析堵管。
(2)摩阻力过大堵管混凝土在管道中的流动阻力,大部分来自混凝土与管壁之间的摩阻力。
混凝土泵送堵管原因及预防措施分析

混凝土泵送堵管原因及预防措施分析泵送混凝土在受场地条件限制及大型砼施工中应用广泛,但是在混凝土泵送环节容易出现堵塞问题,如果不能彻底处理,不仅影响施工进程,还会导致工程质量下降。
下面就混凝土泵送堵管原因及具体的预防措施进行分析。
一、分析混凝土泵送堵管的原因(1)工作人员操作不当进行混凝土输送中,对输送泵的操作质量要求很高,如果操作人员精力不集中,或者责任心不强,工作状态不好,就容易出现操作失误问题,进而发生混凝土堵管问题。
例如混凝土泵送时,如果粗心大意,没有观察到压力表数值发生了明显的变化,发生了堵管问题,那么造成的后果非常严重。
(2)没有科学设定泵送速度进行泵送操作中,合理选择泵送的速度至关重要,操作时不能只求速度,不顾质量。
在很多情况下发现速度越快,问题越多,欲速则不达,事与愿违。
例如操作人员进行第一次送泵时,管道内壁的阻力很大,但是操作人员不清楚,或者没有严格根据要求操作,泵的转速调整到最大,由于管道摩擦阻力大,导致整体运行的摩擦力大,管道接口容易出现脱节问题,或者泵的发动机容易出现过载问题,导致发动机出现故障。
(3)控制余量方面的问题进行混凝土送泵操作中,现场人员要随时注意料斗中的混凝土余量,剩余量不能比搅拌轴还低,但是很多操作人员都没有注意到这一点,检查时发现料斗余量比搅拌轴还低,这样就容易将空气吸入其中,导致管道的堵塞。
通过数据显示,有5%的故障和问题都是由料斗余量控制不合理导致的。
(4)管道连接方面的问题如果管道连接不合理,就容易导致管道堵塞,进行管道连接时,必须进行严格的检查,避免发生一些低级错误。
连接管道要正规,避免增加阻力。
但是现实中操作人员经常出现低级错误,管道布置不合理,距离很长,管道出现弯折,泵送中途接管时直接增加两个管等,导致运行中经常出现故障,影响工作效率。
(5)混凝土离析造成的堵管通过工作经验总结,如果砂浆、混凝土遇水,就易发生管道堵塞问题,除此之外,正在进行砂浆泵送时,容易出现管道堵塞。
混凝土泵送堵管的原因分析

混凝土泵送堵管的原因分析从管道连接、工人操作机械、局部泵管漏浆、泵机磨损、外部环境等方面分析了混凝土泵送堵管的原因,指出在实际施工中应把握要点,认真操作,才能将堵管次数尽可能降到最低。
1 管道连接不当导致堵管1) 管道连接应缩短水平距离,减少最少弯头和最大弯头来布管,混凝土阻力减小将减少堵管。
2) 垂直向下的管路,高度过高时,应安装设防离析装置,以防堵管。
3) 中途接管,每次只能加接一根,加接泵管必须湿润,否则容易堵管。
4) 高层泵送时,应在水平管与垂直管交接处安装截止阀,以防堵管。
2工人操作机械不当造成堵管1) 泵送速度过慢过快。
泵送时,选择速度过快,有时欲速则不达。
管道阻力过大,造成堵管。
刚开始泵送时,速度要慢些,一旦泵送正常时,可提高泵送速度。
2) 操作人员工作态度不认真。
操作人员应思想集中,时刻观察压力表的指针,一旦发现有异常,应立即反泵2 个~3 个行程,泵可消除。
3) 管道未清洗干净。
上次泵管道未清理干净,导致混凝土阻力过大,造成堵管。
4) 上料控制不当。
泵送时,操作人员须随时观察料斗中的混凝土,不能过多,也不能过少,太少泵机会因吸入太多空气而导致堵管。
3局部泵管漏浆造成堵管由于砂浆泄露,影响混凝土质量,坍落度减少,阻力过大,导致堵管。
操作人员连接泵管时,密封圈管卡损坏,造成漏浆。
4泵机磨损导致堵管1) 操作人员观察泵机水箱中的水是否浑浊,有无砂浆,一旦发现水已浑浊或水中有砂浆,表明活塞已经磨损,压力减少,很容易堵管。
2) 更换活塞后,水箱中的水还继续浑浊或有砂浆,则表明输送缸已磨损,须更换输送缸。
否则,也容易堵管。
5不符合要求的混凝土导致堵管用于泵送的砂必须符合配合比要求,及时调整坍落度,将不合格的混凝土泵送加剧机械磨损,容易堵管。
1) 混凝土坍落度不当。
混凝土坍落度一般在8 cm~18 cm ,坍落度过小,会增大压力,加剧机械磨损,导致堵管。
坍落度过大,混凝土易产生离析造成堵管。
泵送混凝土堵管的原因分析及预防措施

网格 间距0 m X . 喷射C 5 , . 02 2 m, 2 砼 厚度2 c 当扩挖至斜井 I 5m; = I
的设计 、 比选 , 最终确定采用爬坡 中导洞进 入正洞顶部 , 形成台
阶施工断面后 , 反向挑顶扩大形成 隧道正式施工断面的施工方
达正洞顶部 : 坡度为2 %、 O 向前施工 lm, O 创造 出施工空间后 , 再 处 ,将主洞上半断面钢架架 没在斜井 口处的门式钢横梁上 , 并 按正洞 的施工断面反向开挖 ,边挖边拆除爬坡 导坑再 临时支 焊接牢 固。正洞落底要及 时进行正洞仰拱施工, 以便初期支护
护 , 至 跨过 斜井 范 围 , 斜 井 向正 洞 的过 渡 。 直 完成
摘
要
关键 词
近年来 , 随着我国公路建设 的发 展和城市建筑 、 城市 环保 的需要 , 对混凝土产品的质量要 求越 来越 高 , 因而混凝 土采用 泵送施工 , 可以有效地保证 产品的质量。如何 防止和控制泵送 混凝土在泵送过程中发生堵管现象 , 显得十分重要。
分析 堵管 的原 因 1 . 不 当容 易造 成 堵 管 。 操作
o ●o ●o ●o ●・ ●o ●・ ● — ●o ●0 ●o ●o ●o ●o ●0 ●<> ・◇ ●0 ・0 ● 0 ●o ●0 ●0 ●0
l 余料量控制不适 当。 _ 3 泵送时 , 操作人员须随时观察料斗 中的余料 , 余料不得低于搅拌轴 。如果余 料太 少 , 极易吸人空
32 工 方 法。 .施
与仰拱尽早成环 , 确保施工安全。
4监控 量 测 .
谈混凝土泵送堵管的原因及预防措施

者通过对堵管原因的探究, 总结 出了一些操作性强 的解决混凝土泵送堵管经 好 的, 这表明输送 缸已出现磨损 , 此时需更要换输送缸来解决 问题。 验和做法 , 很值 得借鉴。 5非合格 的泵送混凝土导致的堵管 关 键 词 : 送 混凝 土 堵 管 泵 51 混 凝 土 塌 落 度过 大 或过 小 。 混 凝 土 塌 落 度 的大 小 直 接 关 系 .
ห้องสมุดไป่ตู้
减 小 。 泵 送 混 凝 土 的塌 落 度 一 般 在 8~1 c 范 围 内 , m 8 对于 长距 离 和 注意 力 时刻 观 察 泵送 压 力表 的读 数 ,一 旦发 现 压 力 表读 数突 然 增 大 , 大高 度 的泵 送 一 般 需 严 格 控 制 在 1 c 左 右 。 落度 过 小 , m 5 塌 会增 大输 说 明 出现堵 管 , 时应 立 即反 泵 2~ 这 3个 行 程 , 重 新 正 泵 , 管 即 可 送 压 力 , 再 堵 加剧 设 备磨 损 , 致堵 管 。 落 度 过 大 , 导 塌 高压 下 混凝 土 易 离 析 排除。若 已经进行了反、 正泵循环后 , 仍未排除堵管 , 应拆管清除堵垢。 而 造 成 堵 管 。 1 泵送 速度选择不 当。 - 2 泵送时速度 的选择很 关键 , 操作人 员不 52含 砂率过小、 . 粗骨料级配不合理。细 骨料按来 源可分为 : 河 能一 味地 图快 , 样 往 往 欲 速 则 不达 。 首 次 泵送 时 , 这 由于 管道 阻 力较 砂 、 工 砂 ( 机 制 砂 )海 砂 、 人 即 、 山砂 , 中河 砂 的 可 泵 性 最 好 , 制 砂 其 机 大 , 时 应 选 择 低 速 泵 送 , 送 正 常 后 , 适 当提 高速 度 。 当 出现 堵 的可 泵 性 最 差 。 细 骨 料 按 粒 径 可 分 为 : 砂 、 此 泵 可 粗 中砂 、 砂 , 中 中砂 的 细 其 管 征 兆 或某 一 车 混 凝 土 的塌 落度 较 小 时 , 也应 选 择 低速 泵送 。 可泵性最好。 粗骨料按 形状 可分为 : 卵石、 碎石。 卵石的可泵性好于碎 1 余 料 量控 制不 适 当。 送 时 , 作 人 员 须 随 时 观察 料 斗 中 的 石。 . 3 泵 操 骨料的最大粒径与输送 管道 的最小 口径也有关 系, 卵石的最 大粒 余 料 , 料 不 得 低 于 搅 拌 轴 , 果 余 料 太 少 , 易 吸 入 空 气 , 致 堵 径 应 小 于 13口径 , 石 的最 大 粒 径 应 小 于 14口径 , 则 也 易 引起 余 如 极 导 / 碎 / 否 管 。料 斗 中的 料 也 不 能堆 得 太多 , 低 于 防护 栏 , 应 以便 于 及 时清 理 粗 堵管。 由于材料 的不同 , 骨料 的含量 ( 细 即含 砂率 )粗 骨料 的级配都 、 骨 料 和超 大 骨 料 。 当某 一车 混凝 土 的塌 落 度 较 小 时 , 料 可 低 于 搅 有 一 个 最 佳 值 。 常 情 况 下 含 砂 率 不 能 过 低 , 大 于 4 % , 余 通 应 0 大粒 径 粗 拌 轴 , 制 在 “ ” 或 吸 入 口 以 上 , 减 小 搅 拌 阻 力 、 动 阻 力 和 吸 骨料 的含量不应过高。合理地选择含砂率和 确定 骨料级配对提 高混 控 S管 以 摆 入 阻力 。 本 措 施仅 适 用 于 “ ” 系列 混 凝 土 泵 。 S阀 凝 土 的 泵 送 性 能 和 预 防堵 管 至 关 重 要。 14 混凝 土 的塌 落度 过 小 时处 置 措施 不 当。当发 现有 一 斗 混凝 土 . 53 水 泥 用 量过 少 或过 多 。水 泥 在 泵 送 混 凝 土 中 起 着 胶 结 作 用 . 的塌 落 度  ̄ / 无 法 泵送 时 , EJ \ 应及 时将 混凝 土 从 料 斗 底 部 放 掉 , 不 可 和 润 滑 作 用 , 切 同时 水 泥 具 有 良好 的保 水 性 , 能使 混凝 土 在 泵 送 过 程 中 贪图省事 , 强行泵送 , 这样极易造成堵管。也切忌在料斗中加水搅拌。 不 易 泌 水 。 水 泥 的 用 量 也 有 一 个 最 佳值 , 水 泥 用 量 过 少 , 严 重 影 若 会 1 停 机时 间过 长 。停 机 期 间 , 每 隔 5 O n 具体 时 间视 当 . 5 应 ~1 mi( Ⅱ 混 凝 土 的 吸入 性 能 , 时 使 泵 送 阻 力 增 加 , 向 同 混凝 土 的 保 水 性 变差 , 日气 温 、 混凝 土塌 落度 、 混凝 土 初 凝 时 间而 定 ) 泵 一次 , 开 以防堵 管。 对 容 易 泌 水 、 析 和 发 生 堵 管 。 离 一般 情 况 下每 立 方米 混凝 土 中水 泥 的含 于 停机 时 间过 长 已出 现初 凝 现 象 的混凝 土 , 不宜 继续 进 行 泵送 作 业 。 量 应 大 于 3 0 g 但 也 不能 太大 : 2K , 用量 过 大 , 增 加 混凝 土 的粘 性 , 会 从 16管道未清洗干净。上次泵送完毕 管道 未清洗干净会造成下 而增加输送 阻力而出现堵 管。另外 ,水泥用量与骨料 的形状也有关 . 次泵送时堵 管。所 以每次泵送完毕 一定 要按 照操作规程将输送管 系 , 料 的 表 面 积 越 大 , 要 包 裹 的水 泥 浆 也 应 该 越 多 , 应 地 水 泥 骨 需 相 道 清 洗 干 净。 的 含 量 就越 大 。 因 此 , 理 地 确 定 水 泥 用 量 对 提 高 混凝 土 的可 泵 性 , 合 2 管 道 连 接原 因导 致 的 堵 管 预 防堵 管 也 很重 要 。
- 1、下载文档前请自行甄别文档内容的完整性,平台不提供额外的编辑、内容补充、找答案等附加服务。
- 2、"仅部分预览"的文档,不可在线预览部分如存在完整性等问题,可反馈申请退款(可完整预览的文档不适用该条件!)。
- 3、如文档侵犯您的权益,请联系客服反馈,我们会尽快为您处理(人工客服工作时间:9:00-18:30)。
混凝土泵送堵管的原因分析及预防措施
摘要:总结的导致堵管的几个常见原因及预防措施,在实际生产过程中,由于外界条件的变化,造成堵管的原因往往不止这些。
但只要我们严格按照操作规程操作,做到防微杜渐,不断地从每一次堵管中总结经验和教训,就一定能将堵管的可能性降到最低。
关键词:泵送混凝土堵管
1 操作不当容易造成堵管
1.1 操作人员精力不集中
输送泵操作人员在泵送施工中应精力集中,时刻注意泵送压力表的读数,一旦发现压力表读数突然增大,应立即反泵2-3个行程,再正泵,堵管即可排除。
若已经进行了反泵(正泵几个操作循环,仍未排除堵管,应及时拆管清洗,否则将使堵管更加严重。
1.2 泵送速度选择不当
泵送时,速度的选择很关键,操作人员不能一味地图快,有时欲速则不达。
首次泵送时,由于管道阻力较大,此时应低速泵送,泵送正常后,可适当提高泵送速度。
当出现堵管征兆或某一车混凝土的塌落度较小时,应低速泵送,将堵管消灭在萌芽状态。
1.3 余料量控制不适当
泵送时,操作人员须随时观察料斗中的余料,余料不得低于搅拌轴,如果余料太少,极易吸入空气,导致堵管。
料斗中的料也不能堆得太多,应低于防护栏,以便于及时清理粗骨料和超大骨料。
当某一车混凝土的塌落度较小时,余料可低于搅拌轴,控制在“S”管或吸入口以上,以减小搅拌阻力、摆动阻力和吸入阻力。
本办法仅适用于“S”阀系列混凝土泵。
1.4 混凝土的塌落度过小时采取措施不当当发现有一斗混凝土的塌落
度很小,无法泵送时,应及时将混凝土从料斗底部放掉,若贪图省事,强行泵送极易造成堵管。
切忌在料斗中加水搅拌。
1.5 停机时间过长
停机期间,应每隔5~10min(具体时间视当日气温、混凝土塌落度、混凝土初凝时间而定)开泵一次,以防堵管。
对于停机时间过长,已初凝的混凝土,不宜继续泵送。
1.6 管道未清洗干净
上次泵送完毕,管道未清洗干净,会造成下一次泵送时堵管。
所以每次泵送完毕一定要按照操作规程将输送管道清洗干净。
2 管道连接原因导致的堵管
管道接法错误很容易导致堵管。
接管时应遵循以下原则:
管道布置时应按最短距离、最少弯头和最大弯头来布管,尽量减小输送阻力,也就减少了堵管的可能性。
泵出口锥管处,不许直接接弯管,至少应接入5mm以上直管后,再接弯管。
泵送中途接管时,每次只能加接一根,且应用水润滑一下管道内壁,并排尽空气,否则极易造成堵管。
垂直向下的管路,出口处应装设防离析装置,预防堵管。
高层泵送时,水平管路的长度一般应不小于垂直管路长度的15%,且应在水平管路中接入管路截止阀。
停机时间超过5min时,应关闭截止阀,防止混凝土倒流,导致堵管。
由水平转垂直时的90度弯管,弯曲半径应大于500mm。
3 混凝土或砂浆的离析导致的堵管
混凝土或砂浆遇水时,极易造成离析。
有时在泵送砂浆时,便发生堵管现象,就是因为砂浆与管道中的水直接接触后,砂浆离析而引起的,预防办法是:泵前用水湿润管道后,从管道的最低点将管道接头松开,将余水全部放掉,或者在泵水之后,泵送砂浆之前,放入一海绵球,将砂浆与水分开。
泵送完毕清洗管道时,也要放入一海绵球,将水与混凝土分开,否则极易造成堵管。
4 局部漏浆造成的堵管
由于砂浆泄漏掉,一方面影响混凝土的质量,另一方面漏浆后,将导致混凝土的塌落度减小和泵送压力的损失,从而导致堵管。
漏浆的原因主要有以下几种:
4.1 输送管道接头密封不严
输送管道接头密封不严,管卡松动或密封圈损坏而漏浆。
此时应紧固管卡或更换密封圈。
4.2 眼镜板和切割环之间的间隙过大
眼镜板和切割环磨损严重时,二者之间的间隙变大。
当间隙大于% -- 时,须通过调整异形螺栓来缩小眼镜板和切割环之间的间隙,若已无法调整,应立即更换磨损件。
本办法仅适用于“S”阀系列混凝土泵。
4.3 混凝土活塞磨损严重
操作人员应经常观察水箱中的水是否浑浊,有无砂浆,一旦发现水已浑浊或水中有砂浆,表明混凝土活塞已经磨损,此时应及时更换活塞,否则将因漏浆和压力损失而导致堵管,同时还会加剧活塞和输送缸的磨损。
4.4 因混凝土输送缸严重磨损而引起的漏浆
若每次更换活塞后,水箱中的水很快就变浑浊,而活塞是好的,则表明输送缸已磨损,此时需更换输送缸。
5 非合格的泵送混凝土导致的堵管
用于泵送的混凝土必须符合泵送混凝土的要求,并不是所有的混凝土都可以拿来泵送,非合格的泵送混凝土将加剧泵机的磨损,并经常出现堵管、爆管等现象。
5.1 混凝土塌落度过大或过小
混凝土塌落度的大小直接反映了混凝土流动性的好坏,混凝土的输送阻力随着塌落度的增加而减小。
泵送混凝土的塌落度一般在8~18cm 范围内,对于长距离和大高度的泵送一般需严格控制在15cm左右。
塌落度过小,会增大输送压力,加剧设备磨损,并导致堵管。
塌落度过大,高压下混凝土易离析而造成堵管。
5.2 含砂率过小、粗骨料级配不合理
细骨料按来源可分为:河砂、人工砂(即机制砂)、海砂、山砂,其中河砂的可泵性最好,机制砂的可泵性最差。
细骨料按粒径可分为:粗砂、中砂、细砂,其中中砂的可泵性最好。
粗骨料按形状可分为:卵石、碎石。
卵石的可泵性好于碎石。
骨料的最大粒径与输送管道的最小口径也有关系,卵石的最大粒径应小于
1/3口径,碎石的最大粒径应小于1/4口径,否则也易引起堵管。
由于材料的不同,细骨料的含量(即含砂率)、粗骨料的级配都存在一个最佳值。
通常情况下,含砂率不宜太低,应大于40%,大粒径粗骨料的含量不宜过高。
合理地选择含砂率和确定骨料级配,对提高混凝土的泵送性能和预防堵管至关重要。
5.3 水泥用量过少或过多
水泥在泵送混凝土中,起胶结作用和润滑作用,同时水泥具有良好的保水性能,使混凝土在泵送过程中不易泌水,水泥的用量也存在一个最佳值,若水泥用量过少,将严重影响混凝土的吸入性能,同时使泵送阻力增加,混凝土的保水性变差,容易泌水、离析和发生堵管。
一般情况下每立方米混凝土中水泥的含量应大于320Kg,但也不能过大,水泥用量过大,将会增加混凝土的粘性,从而造成输送阻力的增加。
另外水泥用量与骨料的形状也有关系,骨料的表面积越大,需要包裹的水泥浆也应该越多,相应地水泥的含量就越大。
因此,合理地确定水泥的用量,对提高混凝土的可泵性,预防堵管也很重要。
5.4 外加剂的选用不合理
外加剂的种类很多,如:加气剂、减水剂、超塑化剂、缓凝剂、泵送剂等,根据混凝土的强度要求和水泥的品种,合理地选择外加剂,对提高混凝土的泵送性能起到很重要的作用。
不合理的外加剂将使混凝土的可泵性和流动性变差,从而导致堵管。
6 砂浆量太少或配合比不合格导致的堵管
6.1 砂浆用量太少
因为首次泵送时,搅拌主机、混凝土输送车搅拌罐、料斗、管道等都要吸收一部分砂浆,如果砂浆用量太少,将导致部分输送管道没有得到润滑,从而导致堵管。
正确的砂浆用量应按每200m 管道约需0.5m3
砂浆计算,搅拌主机、料斗、混凝土输送车搅拌罐等约需0.2m3左右的砂浆。
因此泵送前一定要计算好砂浆的用量。
砂浆太少易堵管,砂浆太多将影响混凝土的质量或造成不必要的浪费。
6.2 砂浆配合比不合格
砂浆的配合比也很关键。
当管道长度低于150m时,用1:2的水泥砂浆(1份水泥/2份砂浆);当管道长度大于150m时,用1:1 的水泥砂浆(1份水泥/1份砂浆),水泥用量太少也会造成堵管。
7 气温变化导致的堵管
夏季气温较高,管道在强烈阳光照射下,混凝土易脱水,从而导致堵管,因此在管道上应加盖湿草袋或其他降温用品。
冬季应采取保温措施,确保混凝土的温度。
8 结束语
以上是总结的导致堵管的几个常见原因及预防措施,在实际生产过程中,由于外界条件的变化,造成堵管的原因往往不止这些。
但只要我们严格按照操作规程操作,做到防微杜渐,不断地从每一次堵管中总结经验和教训,就一定能将堵管的可能性降到最低。