变速器齿轮设计
直齿轮与齿条设计案例
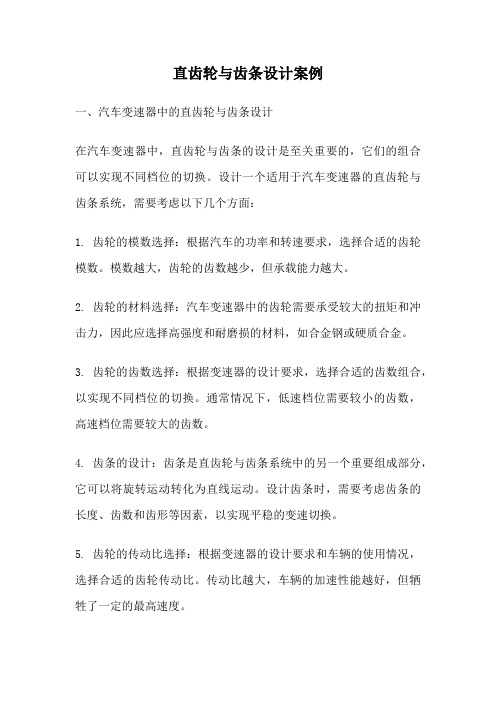
直齿轮与齿条设计案例一、汽车变速器中的直齿轮与齿条设计在汽车变速器中,直齿轮与齿条的设计是至关重要的,它们的组合可以实现不同档位的切换。
设计一个适用于汽车变速器的直齿轮与齿条系统,需要考虑以下几个方面:1. 齿轮的模数选择:根据汽车的功率和转速要求,选择合适的齿轮模数。
模数越大,齿轮的齿数越少,但承载能力越大。
2. 齿轮的材料选择:汽车变速器中的齿轮需要承受较大的扭矩和冲击力,因此应选择高强度和耐磨损的材料,如合金钢或硬质合金。
3. 齿轮的齿数选择:根据变速器的设计要求,选择合适的齿数组合,以实现不同档位的切换。
通常情况下,低速档位需要较小的齿数,高速档位需要较大的齿数。
4. 齿条的设计:齿条是直齿轮与齿条系统中的另一个重要组成部分,它可以将旋转运动转化为直线运动。
设计齿条时,需要考虑齿条的长度、齿数和齿形等因素,以实现平稳的变速切换。
5. 齿轮的传动比选择:根据变速器的设计要求和车辆的使用情况,选择合适的齿轮传动比。
传动比越大,车辆的加速性能越好,但牺牲了一定的最高速度。
6. 齿轮的装配与调试:在设计完成后,需要进行齿轮的装配与调试工作。
确保齿轮与齿条的啮合精度和传动效率达到设计要求,同时保证齿轮的运转平稳和噪音低。
二、工业机械设备中的直齿轮与齿条设计工业机械设备中常常使用直齿轮与齿条系统,实现运动传动和位置控制。
以下是一些工业机械设备中直齿轮与齿条的设计案例:1. CNC数控机床:CNC数控机床中的主轴传动系统通常采用直齿轮与齿条组合,实现工件的加工和运动控制。
通过设计合适的齿轮传动比和齿条长度,可以实现高精度的位置控制。
2. 输送机系统:在物流和生产线上,输送机系统常常使用直齿轮与齿条传动。
通过设计合适的齿轮和齿条参数,可以实现物料的平稳传送和定位。
3. 机械手臂:工业机械手臂中的关节传动通常采用直齿轮与齿条系统。
通过设计合适的齿轮模数和齿数,可以实现机械手臂的高精度运动和位置控制。
4. 提升机系统:在仓储和物流领域,提升机系统常常使用直齿轮与齿条传动。
变速器结构及主参数设计
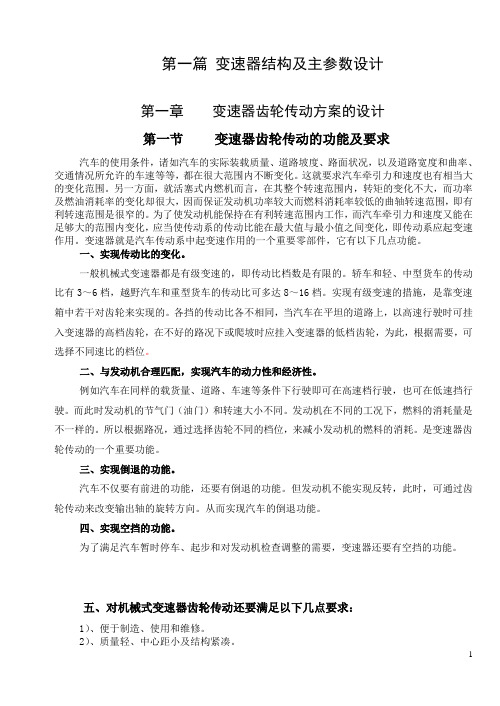
第一篇变速器结构及主参数设计第一章变速器齿轮传动方案的设计第一节变速器齿轮传动的功能及要求汽车的使用条件,诸如汽车的实际装载质量、道路坡度、路面状况,以及道路宽度和曲率、交通情况所允许的车速等等,都在很大范围内不断变化。
这就要求汽车牵引力和速度也有相当大的变化范围。
另一方面,就活塞式内燃机而言,在其整个转速范围内,转矩的变化不大,而功率及燃油消耗率的变化却很大,因而保证发动机功率较大而燃料消耗率较低的曲轴转速范围,即有利转速范围是很窄的。
为了使发动机能保持在有利转速范围内工作,而汽车牵引力和速度又能在足够大的范围内变化,应当使传动系的传动比能在最大值与最小值之间变化,即传动系应起变速作用。
变速器就是汽车传动系中起变速作用的一个重要零部件,它有以下几点功能。
一、实现传动比的变化。
一般机械式变速器都是有级变速的,即传动比档数是有限的。
轿车和轻、中型货车的传动比有3~6档,越野汽车和重型货车的传动比可多达8~16档。
实现有级变速的措施,是靠变速箱中若干对齿轮来实现的。
各挡的传动比各不相同,当汽车在平坦的道路上,以高速行驶时可挂入变速器的高档齿轮,在不好的路况下或爬坡时应挂入变速器的低档齿轮,为此,根据需要,可选择不同速比的档位。
二、与发动机合理匹配,实现汽车的动力性和经济性。
例如汽车在同样的载货量、道路、车速等条件下行驶即可在高速档行驶,也可在低速挡行驶。
而此时发动机的节气门(油门)和转速大小不同。
发动机在不同的工况下,燃料的消耗量是不一样的。
所以根据路况,通过选择齿轮不同的档位,来减小发动机的燃料的消耗。
是变速器齿轮传动的一个重要功能。
三、实现倒退的功能。
汽车不仅要有前进的功能,还要有倒退的功能。
但发动机不能实现反转,此时,可通过齿轮传动来改变输出轴的旋转方向。
从而实现汽车的倒退功能。
四、实现空挡的功能。
为了满足汽车暂时停车、起步和对发动机检查调整的需要,变速器还要有空挡的功能。
五、对机械式变速器齿轮传动还要满足以下几点要求:1)、便于制造、使用和维修。
变速器齿轮动力学性能的优化设计
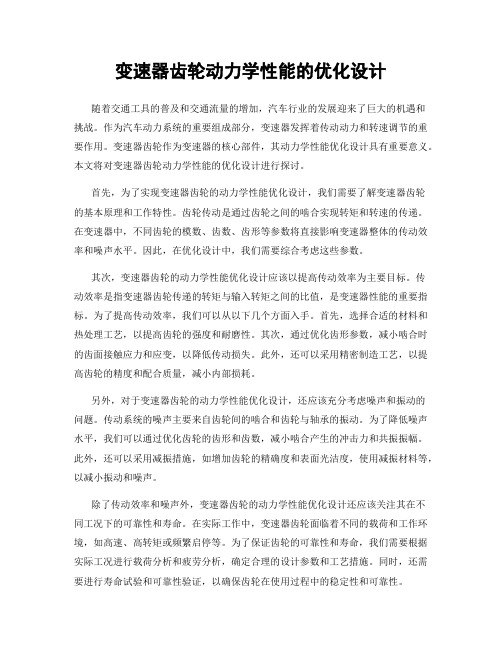
变速器齿轮动力学性能的优化设计随着交通工具的普及和交通流量的增加,汽车行业的发展迎来了巨大的机遇和挑战。
作为汽车动力系统的重要组成部分,变速器发挥着传动动力和转速调节的重要作用。
变速器齿轮作为变速器的核心部件,其动力学性能优化设计具有重要意义。
本文将对变速器齿轮动力学性能的优化设计进行探讨。
首先,为了实现变速器齿轮的动力学性能优化设计,我们需要了解变速器齿轮的基本原理和工作特性。
齿轮传动是通过齿轮之间的啮合实现转矩和转速的传递。
在变速器中,不同齿轮的模数、齿数、齿形等参数将直接影响变速器整体的传动效率和噪声水平。
因此,在优化设计中,我们需要综合考虑这些参数。
其次,变速器齿轮的动力学性能优化设计应该以提高传动效率为主要目标。
传动效率是指变速器齿轮传递的转矩与输入转矩之间的比值,是变速器性能的重要指标。
为了提高传动效率,我们可以从以下几个方面入手。
首先,选择合适的材料和热处理工艺,以提高齿轮的强度和耐磨性。
其次,通过优化齿形参数,减小啮合时的齿面接触应力和应变,以降低传动损失。
此外,还可以采用精密制造工艺,以提高齿轮的精度和配合质量,减小内部损耗。
另外,对于变速器齿轮的动力学性能优化设计,还应该充分考虑噪声和振动的问题。
传动系统的噪声主要来自齿轮间的啮合和齿轮与轴承的振动。
为了降低噪声水平,我们可以通过优化齿轮的齿形和齿数,减小啮合产生的冲击力和共振振幅。
此外,还可以采用减振措施,如增加齿轮的精确度和表面光洁度,使用减振材料等,以减小振动和噪声。
除了传动效率和噪声外,变速器齿轮的动力学性能优化设计还应该关注其在不同工况下的可靠性和寿命。
在实际工作中,变速器齿轮面临着不同的载荷和工作环境,如高速、高转矩或频繁启停等。
为了保证齿轮的可靠性和寿命,我们需要根据实际工况进行载荷分析和疲劳分析,确定合理的设计参数和工艺措施。
同时,还需要进行寿命试验和可靠性验证,以确保齿轮在使用过程中的稳定性和可靠性。
综上所述,变速器齿轮动力学性能的优化设计在汽车工程中具有重要意义。
汽车变速器齿轮设计及问题研讨

汽车变速器齿轮设计及问题研讨1. 引言1.1 研究背景汽车变速器齿轮设计是汽车传动系统中的核心部件,直接影响着汽车的性能和稳定性。
随着汽车工业的快速发展,对于汽车变速器齿轮设计的要求也越来越高。
目前市场上存在着很多变速器齿轮设计方面的问题,例如噪音过大、传动效率低、寿命短等。
这些问题不仅影响了汽车的运行效果,还可能对驾驶员的驾驶体验造成不良影响。
进一步研究汽车变速器齿轮设计原理及问题成为了当下的重要课题。
通过对现有变速器齿轮设计进行深入分析,找出问题所在,并提出优化设计方法,可以有效提高变速器齿轮的性能和可靠性。
对材料选择与加工工艺进行研究,也能够为汽车变速器齿轮的设计和制造提供更好的支持。
通过性能测试与评估,更加客观地了解汽车变速器齿轮的性能表现,为进一步的优化设计提供依据。
【这是研究背景的内容,总字数2000字。
】1.2 研究目的汽车变速器齿轮设计及问题研讨研究目的:研究目的是通过深入探讨汽车变速器齿轮设计及存在的问题,找出优化设计方法,提高变速器的效率和性能,减少故障率,增强汽车的可靠性和耐久性。
研究目的还包括对现有的材料选择和加工工艺进行分析和评估,以寻找更加适合变速器齿轮的材料和工艺,从而提高变速器的质量和寿命。
通过对变速器齿轮的性能测试和评估,进一步验证优化设计方法的可行性和效果,为汽车行驶安全和稳定提供更好的保障。
研究目的在于为汽车行业提供更加先进和可靠的变速器技术,促进汽车工程的发展和进步,为广大汽车用户提供更好的驾驶体验和安全保障。
通过本研究,希望能够为汽车变速器齿轮设计领域的研究和实践提供一定的参考和借鉴,推动汽车工业的持续发展和提升。
1.3 意义和价值汽车变速器齿轮设计及问题研讨的意义和价值在于提高汽车传动系统的效率和性能,从而提升整车的性能和驾驶体验。
通过深入研究变速器齿轮的设计原理,分析现有设计中存在的问题,探讨优化设计方法和材料选择与加工工艺,可以有效提高汽车变速器的可靠性和耐久性,减少故障率和维修成本。
纯电动汽车两挡行星齿轮自动变速器结构设计

纯电动汽车两挡行星齿轮自动变速器结构设计【摘要】本文主要探讨纯电动汽车两挡行星齿轮自动变速器的结构设计。
在我们将介绍研究背景、研究目的和研究意义。
在我们将从电动汽车变速器概述入手,深入介绍行星齿轮自动变速器原理,重点讨论纯电动汽车两挡行星齿轮自动变速器设计要点和结构设计优化,最后进行性能测试与验证。
在我们将评估设计方案的可行性,展望未来研究方向,并对整个研究进行总结。
通过本文的研究,我们旨在提高纯电动汽车的传动效率和性能,推动电动汽车技术的发展和应用。
【关键词】纯电动汽车、两挡行星齿轮自动变速器、结构设计、设计优化、性能测试、可行性、未来展望、结论总结1. 引言1.1 研究背景随着环境污染问题日益严重和对能源消耗的担忧加剧,传统内燃机汽车逐渐不再适应当今社会的需求。
新能源汽车成为了解决这些问题的重要方向之一。
在众多新能源汽车中,纯电动汽车由于其零排放、低噪音等优点逐渐受到消费者的青睐。
纯电动汽车的发展离不开先进的变速器技术。
传统汽车一般采用机械液力变速器或自动变速器,在纯电动汽车中,对变速器的性能、体积、重量等方面提出了更高的要求。
研究并开发适用于纯电动汽车的新型变速器至关重要。
本文旨在探讨纯电动汽车两挡行星齿轮自动变速器的结构设计,通过对其原理和要点进行深入研究,为纯电动汽车变速器技术的发展提供新的思路和方法。
本研究有望为纯电动汽车的性能提升和市场应用打下坚实的基础。
部分为本文研究提供了必要的背景和动机,也为后续内容的展开奠定了基础。
1.2 研究目的本文旨在通过对纯电动汽车两挡行星齿轮自动变速器结构设计的研究,探讨其在电动汽车领域中的应用以及优化方向。
具体研究目的包括以下几点:通过深入分析和研究电动汽车变速器的概念和原理,探讨行星齿轮自动变速器在纯电动汽车中的作用和意义,进一步完善电动汽车的整体性能。
通过研究设计了解纯电动汽车两挡行星齿轮自动变速器的设计要点和结构特点,分析其与传统汽车变速器的不同之处,为纯电动汽车变速器的优化提供参考。
汽车变速器齿轮设计及问题分析

汽车变速器齿轮设计及问题分析摘要:在车辆传动齿轮的设计和应用方面,越来越多地使用了两个重要的原因,即传输的强度和结构。
在这种情况下,高刚度齿轮的设计应该更深入地研究。
在传统的机械传动齿轮的设计中,模块、压力角、速度梯度和螺旋角等参数是影响机器噪声和强度的重要因素。
这些参数的计算公式是根据传输类型的选择计算的。
与此同时,齿轮的尺寸和强度可以根据相关公式精确地获得。
关键词:齿轮载荷谱;压力角;齿轮噪声指标前言:在变速箱的设计应用中,变速箱的强度和结构越来越频繁。
研究高风险变换器的设计是很有意义的,它的设计具有一定的特异性,并在这些问题的背景下进行了研究。
重要的是要确定模块的数量,压力角,齿轮齿数,螺旋桨角等,这些都是传统机械齿轮的噪声和强度的重要组成部分。
在变速箱的选择中采用了上述参数的计算公式。
与此同时,齿轮的尺寸和强度可以根据相关公式来精确计算,这是不重复的。
由于计算机的快速发展和他们的受欢迎程度,可以设计出更精确的齿轮传动齿轮传动齿轮。
但它不只是依赖于软件,它只是一个辅助计算工具,更合理的齿轮必须是由人设计的。
1齿轮载荷谱的制定在计算齿轮强度时,最重要的测量是建立齿轮载荷谱。
在齿轮上的应力是用理论的最大载荷来计算的,并与齿轮的可采性相比较。
然而,理论结果与所使用的齿轮有很大的不同。
1.1齿轮载荷的差异在齿轮的实际应用中,由于紧急停车、启动和道路状况等因素,齿轮并不总是承载额定载荷,这将导致比变速箱等传动部件的额定载荷更大的冲击载荷。
但是,当车辆处于良好状态时,负载小于额定负载。
因此,在确定试验方法时,应准确进行技术处理。
例如,峰值负载大于120%,小于50%的负载被删除,或者直接使用额定负载。
1.2齿轮工作循环次数的差别不同类别的齿轮的工作周期数必须与实际使用的周期不同。
不同的模型之间存在差异,即使它们使用相同的速度盒。
例如,起重设备和拖拉机,其使用基本上是不同的。
使用高质量的建筑设备的效率比拖拉机低,因为拖拉机通常在道路或道路上行驶。
汽车变速器齿轮设计及问题研讨

汽车变速器齿轮设计及问题研讨汽车变速器是汽车的重要部件之一,用于调整发动机输出转矩与车轮转速之间的匹配关系,以实现不同速度的行驶。
而变速器齿轮作为变速器的核心组成部分,对于变速器的性能和可靠性起着重要的影响。
本文将探讨汽车变速器齿轮的设计及可能出现的问题。
齿轮的设计需要考虑到传动比和齿轮的强度。
传动比是齿轮减速或增速的比例,决定了汽车的最高速度和加速性能。
传动比的选择需要综合考虑车辆的使用情况和发动机的特性。
齿轮的强度需要满足汽车的使用要求,避免因负载过大而导致齿轮断裂或磨损加剧。
齿轮的材料选择也是关键。
常用的齿轮材料有铸铁、钢和塑料等。
铸铁齿轮具有良好的强度和耐磨性,但重量较大;钢齿轮具有较高的强度和耐磨性,但价格较高;塑料齿轮具有较低的噪音和重量,但强度较低。
根据汽车的使用要求和经济性,需要选择适合的齿轮材料。
齿轮的几何参数也需要进行设计。
齿轮的模数、齿数和齿型都会影响其传动性能和噪音水平。
模数是齿轮齿数和齿轮直径比值的倒数,决定了齿轮的结构尺寸;齿数是指齿轮上的牙齿数目,通常选择合适的齿数可以减小齿轮噪音;齿型是指齿轮齿条的形状,常见的有直齿、斜齿、渐开线齿等。
不同的几何参数组合可以实现不同的传动特性。
汽车变速器齿轮在使用过程中可能会出现一些问题。
常见的问题包括齿轮磨损、齿轮断裂和齿轮噪音等。
齿轮磨损是由于长时间大负载工作引起的,需要定期更换齿轮。
齿轮断裂可能是由于设计上的缺陷或者负载过大引起的,需要进行结构优化或者重新选择材料。
齿轮噪音可能是由于设计不合理或制造工艺不良等原因引起的,需要加强质量控制和确定合适的齿型。
汽车变速器齿轮的设计及问题研讨是一个复杂而重要的课题。
通过合理的设计和优化,可以提高汽车变速器的可靠性和性能,进一步改善汽车的行驶体验。
机械机电毕业设计_低速载货车变速器的齿轮设计

低速载货车变速器的齿轮设计目录第一章前言第二章低速载货汽车主要参数的确定2.1质量参数的确定2.2发动机的选型2.3车速的确定第三章变速器的设计与计算3.1设计方案的确定3.1.1两轴式3.1.2三轴式3.1.3液力机械式3.1.4确定方案3.2零部件的结构分析3.3基本参数的确定3.3.1变速器的档位数和传动比3.3.2中心距3.3.3变速器的轴向尺寸3.3.4齿轮参数3.3.5各档齿轮齿数的分配3.4齿轮的设计计算3.4.1几何尺寸计算3.4.2齿轮的材料及热处理3.4.3齿轮的弯曲强度3.4.4齿轮的接触强度第一章前言低速载货汽车是一种特殊的货车,特殊在于它以前叫农用运输车,GB7258-2004[1]将“四轮农用运输车”更名为“低速货车”,明确“农用运输车”实质上是汽车的一类。
GB18320-2001[2]规定以柴油机为动力装置,中小吨位、中低速度,从事道路运输的机动车辆,包括三轮农用运输车和四轮农用运输车等,但不包括轮式拖拉机车组、手扶拖拉机车组和手扶变型运输机。
农用运输车最高设计车速不大于70km/h,最大设计总质量不大于4500kg,长小于6m、宽不大于2m和高不大于2.5m。
我国农用运输车诞生于20世纪80年代初。
我国农村运输的特点是运量小、运距短、货物分散、道路条件差。
由于同吨位的柴油车较汽油车运载能力强,燃油价格低,且柴油保管无须特殊设备,又为广大农民所熟悉,所以,农用运输车均选用柴油机为动力。
农用运输车的载质量一般不超过1.5t。
当前四轮农用运输车载质量分为4个等级,包括1.5t、1.0t、O.75t和0.5t级。
在传动系统中设置了变速器,以适应汽车在起步、加速、行驶以及克服各种道路障碍等不同行驶条件下对驱动车轮牵引力及车速的不同要求的需要。
本次设计的课题为低速载货汽车变速器的设计,该课题来源于结合生产实际。
本次课题研究的主要内容是:a.参与汽车的总体设计;b.变速器结构型式分析和主要参数的确定;c.变速器中齿轮部分的具体结构设计。
- 1、下载文档前请自行甄别文档内容的完整性,平台不提供额外的编辑、内容补充、找答案等附加服务。
- 2、"仅部分预览"的文档,不可在线预览部分如存在完整性等问题,可反馈申请退款(可完整预览的文档不适用该条件!)。
- 3、如文档侵犯您的权益,请联系客服反馈,我们会尽快为您处理(人工客服工作时间:9:00-18:30)。
凡采有常啮合齿轮传动的 挡位,其换挡方式可以用同 步器或啮合套来实现。同一 变速器中,挡位高的用同步 器换挡,挡位低的用啮合套 换挡。
图2 中间轴式五挡变速器传动方案
© GJT, 27 August 2012, Guo Zuirun; all rights reserved 5
变速器齿轮设计
图3为中间轴式六挡变速器传动方案。图3a所示方案中的一挡、倒挡和图3b 所示方案中的倒挡用直齿滑动齿轮换挡,其余各挡均匀常啮合齿轮。 常啮合齿轮传动的挡位,其换挡方式可以用同步器或啮合套来实现。同一 变速器中,一定是挡位高的用同步器换挡,挡位低的用啮合套换挡。
1、齿轮形式
齿轮形式:直齿圆柱齿轮、斜齿圆柱齿轮。 两者相比较,斜齿圆柱齿轮有使用寿命长、工作时噪声低的优点;缺点是制 造时稍复杂,工作时有轴向力。 变速器中的常啮合齿轮均采用斜齿圆柱齿轮。直齿圆柱齿轮仅用于低挡和倒。
2、档数
增加变速器的挡数能够改善汽车的动力性和经济性。挡数越多,变速器的结构 越复杂,使轮廓尺寸和质量加大,而且在使用时换挡频率也增高。 在最低挡传动比不变的条件下,增加变速器的挡数会使变速器相邻的低挡与高 挡之间的传动比比值减小,使换挡工作容易进行。 挡数选择的要求: 相邻挡位之间的传动比比值在1.8以下。 高挡区相邻挡位之间的传动比比值要比低挡区相邻挡位之间的比值小。 目前,轿车一般用4~5个挡位变速器, 货车变速器采用4~5个挡或多挡,多 挡变速器多用于重型货车和越野汽车。
图3 中间轴式六挡变速器传动方案
© GJT, 27 August 2012, Guo Zuirun; all rights reserved
6
变速器齿轮设计
图4为常见的倒挡布置方案。图4b方案的优点是倒挡利用了一挡齿轮,缩短了
中间轴的长度。但换挡时有两对齿轮同时进入啮合,使换挡困难。图4c方案能获 得较大的倒挡传动比,缺点是换挡程序不合理。图4d方案对4c的缺点做了修改。 图4e所示方案是将一、倒挡齿轮做成一体,将其齿宽加长。图4f所示方案适用于 全部齿轮副均为常啮合的齿轮,挡换更为轻便。
变速器齿轮设计
产品开发中心 2008.10.18
© GJT, 27 August 2012, Guo Zuirun; all rights reserved
变速器齿轮设计
目录 一、 二、 三、 四、 五、 六、 七、
概述 中间轴式变速器的特点 变速器主要参数的选择 直齿圆柱齿轮传动的强度计算 斜齿圆柱齿轮传动的强度计算 GJT使用的齿轮CAE分析工具 GJT齿轮开发流程
© GJT, 27 August 2012, Guo Zuirun; all rights reserved
12
变速器齿轮设计
斜齿轮传递转矩时,要产生轴向力并 作用到轴承上。设计时应力求中间轴上 同时工作的两对齿轮产生轴向力平衡。 根据图5可知,欲使中间轴上两个斜 齿轮的轴向力平衡,须满足下述条件: Fa1=Fn1tanβ1 Fa2=Fn2tanβ2 由于,为使两轴向力平衡,必须满足
图5 中间轴轴向力的平衡
© GJT, 27 August 2012, Guo Zuirun; all rights reserved
13
变速器齿轮设计
4.齿宽b
齿宽对变速器的轴向尺寸、齿轮工作平稳性、齿轮强度和齿轮工作时受力的 均匀程度等均有影响。 选用较小的齿宽可以缩短变速器的轴向尺寸和减小质量。但齿宽减少使斜 齿轮传动平稳的优点被削弱,齿轮的工作应力增加。 选用较大的齿宽,工作时会因轴的变形导致齿轮倾斜,使齿轮沿齿宽方向 受力不均匀并在齿宽方向磨损不均匀。 通常根据齿轮模数m(mn)的大小来选定齿宽b:
图1 中间轴式四挡变速器传动方案
© GJT, 27 August 2012, Guo Zuirun; all rights reserved
4
变速器齿轮设计
图2为中间轴式五挡变速器传动方案 。图2a所示方案,除一、倒挡用直 齿滑动齿轮换挡外,其余各挡为常啮合齿轮传动。图2b、c、d所示方案的各 前进挡,均用常啮合齿轮传动;图2d所示方案中的倒挡和超速挡安装在副箱 体内,可以提高轴的刚度、减少齿轮磨损和降低工作噪声。
© GJT, 27 August 2012, Guo Zuirun; all rights reserved
3
变速器齿轮设计
二、中间轴式变速器的特点
中间轴式变速器传动方案的共同特点是:(1)设有直接挡; (2)一挡有较大的 传动比; (3)挡位高的齿轮采用常啮合齿轮传动,挡位低的齿轮(一挡)可以采 用或不采用常啮合齿轮传动; (4) 除一挡以外,其他挡位采用同步器或啮合套换 挡; (5)除直接挡以外,其他挡位工作时的传动效率略低。 图1中的中间轴式四挡变速器传动方案示例的区别为图1a、b所示方案有四对 常啮合齿轮,倒挡用直齿滑动齿轮换挡,图1c所示传动方案的二、三、四挡用常 啮合齿轮传动,而一、倒挡用直齿滑动齿轮换挡。
© GJT, 27 August 2012, Guo Zuirun; all rights reserved
11
变速器齿轮设计
2.压力角α 压力角较小时,重合度较大,传动平稳,噪声较低;压力角较大时, 可提高轮齿的抗弯强度和表面接触强度。 对于轿车,为了降低噪声,应选用14.5°、15°、16°、16.5°等小 些的压力角。 对货车,为提高齿轮强度,应选用22.5°或25°等大些的压力角。 国家规定的标准压力角为20°,所以普遍采用的压力角为20°。 3.螺旋角β 齿轮的螺旋角对齿轮工作噪声、轮齿的强度和轴向力有影响。选用大 些的螺旋角时,使齿轮啮合的重合度增加,因而工作平稳、噪声降低。 试验证明:随着螺旋角的增大,齿的强度相应提高,但当螺旋角大于 30°时,其抗弯强度骤然下降,而接触强度仍继续上升。因此,从提高 低挡齿轮的抗弯强度出发,并不希望用过大的螺旋角;而从提高高挡齿 轮的接触强度着眼,应当选用较大的螺旋角。
© GJT, 27 August 2012, Guo Zuirun; all rights reserved
9
变速器齿轮设计
4之间的距离称为变速器中心距A。 变速器中心距是一个基本参数,对变速器的外形尺寸、体积和质量大小、 轮齿的接触强度有影响。 中心距越小,轮齿的接触应力越大,齿轮寿命越短。因此,最小允许 中心距应当由保证轮齿有必要的接触强度来确定。 初选中心距A时,可根据下面的经验公式计算
© GJT, 27 August 2012, Guo Zuirun; all rights reserved
2
变速器齿轮设计
一 概述
变速器用来改变发动机传到驱轮上的转矩和转速,目的是在各种行驶工况 下,使汽车获得不同的牵引力和速度,同时使发动机在最有利的工况范围内工 作。变速器由变速传动机构和操纵机构组成。 变速器的基本设计要求:
© GJT, 27 August 2012, Guo Zuirun; all rights reserved 15
变速器齿轮设计
6、各挡齿轮齿数的分配
在初选中心距、齿轮模数和螺旋角以后, 可根据变速器的挡数、传动比和传动方案来分 配各挡齿轮的齿数。下面以图6所示四挡变速器 为例,说明分配齿数的方法。 1.确定一挡齿轮的齿数 一挡传动比
直齿:b=Kcm,Kc为齿宽系数,取为4.5~8.0
斜齿:b=Kcmn,K c取为6.0~ 8.5 啮合套或同步器接合齿的工作宽度初选时可取为(2~4)m m。 第一轴常啮合齿轮副的齿宽系数Kc可取大些,使接触线长度增加、接触应 力降低,以提高传动平稳性和齿轮寿命。
© GJT, 27 August 2012, Guo Zuirun; all rights reserved
i1 z2 z7 z 1 z 8 (3-1)
轿车中间轴式变速器一挡齿 轮齿数z8可在15~17之间 选取;货车z8可在12~17 之间选取。一挡大齿轮齿数 用z7=zh-z8计算求得。
如果z7和 z8的齿数确定了,则z2与 z1的传 动比可求出。为了求z7、 z8的齿数,先求其齿 数和zh
直齿 Z h 斜齿 Z h 2A m 2 A cos mn
A K
3 A
T e max i1 g
式中,KA为中心距系数,轿车:KA=8.9~9.3,货车:KA=8.6~9.6,多挡变 速器:KA=9.5~11.0。 轿车变速器的中心距在65~80mm范围内变化,而货车的变速器中心 距在80~170mm范围内变化。
© GJT, 27 August 2012, Guo Zuirun; all rights reserved
10
变速器齿轮设计
5、齿轮参数
1.模数的选取 齿轮模数选取的一般原则: 1)为了减少噪声应合理减小模数,同时增加齿宽; 2)为使质量小些,应该增加模数,同时减少齿宽; 3)从工艺方面考虑,各挡齿轮应该选用一种模数; 4)从强度方面考虑,各挡齿轮应有不同的模数。 对于轿车,减少工作噪声较为重要,因此模数应选得小些; 对于货车,减小质量比减小噪声更重要,因此模数应选得大些。 所选模数值应符合国家标准的规定。 变速器齿轮模数范围大致如下: 微型、普通级轿车 中级轿车 中型货车 重型货车 2.25~2.75 2.75~3.00 3.5~4.5 4.5~6.0
(3-2)
1)保证汽车有必要的动力性和经济性。
2)设置空挡,用来切断发动机的动力传输。 3)设置倒挡,使汽车能倒退行驶。 4)设置动力输出装置。 5)换挡迅速、省力、方便。 6)工作可靠。变速器不得有跳挡、乱挡及换挡冲击等现象发生。 7)变速器应有高的工作效率。 8)变速器的工作噪声低。 除此之外,变速器还应当满足轮廓尺寸和质量小、制造成本低、维修方便 等要求。
为了缩短变速器轴 向长度,倒挡传动采用 图4g所示方案。缺点是 一、倒挡各用一根变速 器拨叉轴,使变速器上 盖中的操纵机构复杂一 些。 图4 倒挡布置方案