真空渗碳技术工艺控制原理
渗碳处理知识点总结
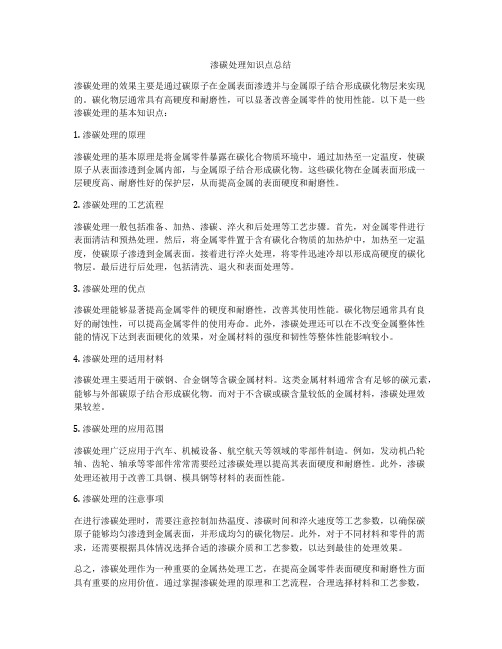
渗碳处理知识点总结渗碳处理的效果主要是通过碳原子在金属表面渗透并与金属原子结合形成碳化物层来实现的。
碳化物层通常具有高硬度和耐磨性,可以显著改善金属零件的使用性能。
以下是一些渗碳处理的基本知识点:1. 渗碳处理的原理渗碳处理的基本原理是将金属零件暴露在碳化合物质环境中,通过加热至一定温度,使碳原子从表面渗透到金属内部,与金属原子结合形成碳化物。
这些碳化物在金属表面形成一层硬度高、耐磨性好的保护层,从而提高金属的表面硬度和耐磨性。
2. 渗碳处理的工艺流程渗碳处理一般包括准备、加热、渗碳、淬火和后处理等工艺步骤。
首先,对金属零件进行表面清洁和预热处理。
然后,将金属零件置于含有碳化合物质的加热炉中,加热至一定温度,使碳原子渗透到金属表面。
接着进行淬火处理,将零件迅速冷却以形成高硬度的碳化物层。
最后进行后处理,包括清洗、退火和表面处理等。
3. 渗碳处理的优点渗碳处理能够显著提高金属零件的硬度和耐磨性,改善其使用性能。
碳化物层通常具有良好的耐蚀性,可以提高金属零件的使用寿命。
此外,渗碳处理还可以在不改变金属整体性能的情况下达到表面硬化的效果,对金属材料的强度和韧性等整体性能影响较小。
4. 渗碳处理的适用材料渗碳处理主要适用于碳钢、合金钢等含碳金属材料。
这类金属材料通常含有足够的碳元素,能够与外部碳原子结合形成碳化物。
而对于不含碳或碳含量较低的金属材料,渗碳处理效果较差。
5. 渗碳处理的应用范围渗碳处理广泛应用于汽车、机械设备、航空航天等领域的零部件制造。
例如,发动机凸轮轴、齿轮、轴承等零部件常常需要经过渗碳处理以提高其表面硬度和耐磨性。
此外,渗碳处理还被用于改善工具钢、模具钢等材料的表面性能。
6. 渗碳处理的注意事项在进行渗碳处理时,需要注意控制加热温度、渗碳时间和淬火速度等工艺参数,以确保碳原子能够均匀渗透到金属表面,并形成均匀的碳化物层。
此外,对于不同材料和零件的需求,还需要根据具体情况选择合适的渗碳介质和工艺参数,以达到最佳的处理效果。
渗碳工艺的原理过程及应用
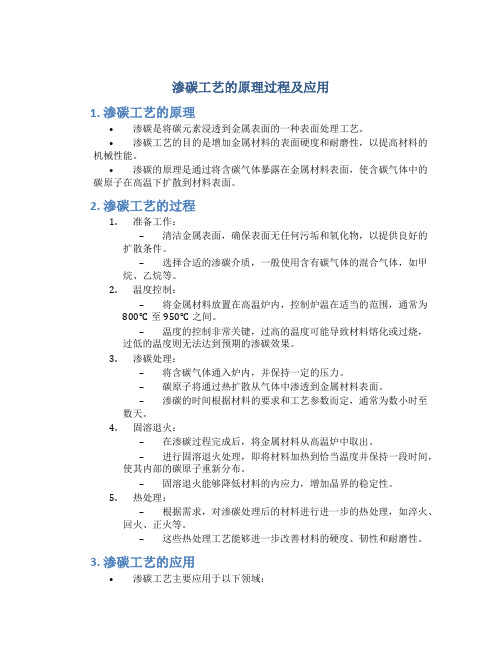
渗碳工艺的原理过程及应用1. 渗碳工艺的原理•渗碳是将碳元素浸透到金属表面的一种表面处理工艺。
•渗碳工艺的目的是增加金属材料的表面硬度和耐磨性,以提高材料的机械性能。
•渗碳的原理是通过将含碳气体暴露在金属材料表面,使含碳气体中的碳原子在高温下扩散到材料表面。
2. 渗碳工艺的过程1.准备工作:–清洁金属表面,确保表面无任何污垢和氧化物,以提供良好的扩散条件。
–选择合适的渗碳介质,一般使用含有碳气体的混合气体,如甲烷、乙烷等。
2.温度控制:–将金属材料放置在高温炉内,控制炉温在适当的范围,通常为800°C至950°C之间。
–温度的控制非常关键,过高的温度可能导致材料熔化或过烧,过低的温度则无法达到预期的渗碳效果。
3.渗碳处理:–将含碳气体通入炉内,并保持一定的压力。
–碳原子将通过热扩散从气体中渗透到金属材料表面。
–渗碳的时间根据材料的要求和工艺参数而定,通常为数小时至数天。
4.固溶退火:–在渗碳过程完成后,将金属材料从高温炉中取出。
–进行固溶退火处理,即将材料加热到恰当温度并保持一段时间,使其内部的碳原子重新分布。
–固溶退火能够降低材料的内应力,增加晶界的稳定性。
5.热处理:–根据需求,对渗碳处理后的材料进行进一步的热处理,如淬火、回火、正火等。
–这些热处理工艺能够进一步改善材料的硬度、韧性和耐磨性。
3. 渗碳工艺的应用•渗碳工艺主要应用于以下领域:1.汽车工业:–渗碳可以提高发动机零部件的硬度和耐磨性,延长零部件的使用寿命。
–例如,曲轴、凸轮轴、齿轮等关键零部件常采用渗碳工艺进行处理。
2.机械制造:–渗碳可以提高机械零部件的表面硬度,减少磨损和疲劳断裂。
–例如,齿轮、轴承、齿条等机械组件可通过渗碳工艺增加其耐磨性和使用寿命。
3.冶金行业:–渗碳可以改善冶金材料的性能,提高其硬度和耐磨性。
–例如,渗碳处理可以将普通碳钢转化为高碳钢,提高钢材的强度和硬度。
4.制造业:–渗碳工艺广泛应用于各种制造业,包括航空航天、船舶、电子、家电等行业。
真空渗碳炉工作原理

真空渗碳炉的工作原理是在真空条件下,利用渗碳气体进行渗碳处理。
具体过程如下:
1.启动设备,将工件装入真空炉中。
2.启动真空系统,对炉内进行抽真空操作,以去除炉内的空气和其他杂质。
3.在达到一定的真空度后,将碳氢化合物等渗碳剂引入炉内,进行渗碳处理。
4.在渗碳过程中,碳离子在电场的作用下轰击炉料表面,使碳元素渗透到钢件表面,从而达到所需的表面性能。
5.渗碳完成后,切断渗碳剂供应,并通过热交换器向炉内充入高纯氮气进行强制冷却。
真空渗碳炉采用高温反应和扩散力学原理,在真空条件下进行渗碳处理,具有渗碳速度快、渗层均匀、表面质量好、节能等优点,因此被广泛应用于钢铁、有色金属等材料的渗碳处理中。
真空渗碳工艺

真空渗碳工艺一、概述真空渗碳是一种高效的表面硬化处理方法,其主要作用是提高金属材料的抗磨损性能、耐腐蚀性能和疲劳寿命。
该工艺通过在真空环境中将金属样件暴露在碳源气体中,使得碳原子在样件表面形成一层均匀的硬质化合物层,从而提高材料的表面硬度和耐磨性。
二、工艺流程1. 预处理首先需要对待处理的金属样件进行清洗和除油处理,以保证样件表面干净无油污。
常用的清洗方法包括机械清洗、化学清洗和电解清洗等。
2. 装夹将经过预处理的金属样件装夹在真空渗碳设备中。
装夹时应保证样件间距适当,不得过于密集或过于疏松。
3. 真空排气启动真空泵进行排气,将渗碳设备内部压力降至目标值以下。
排气时间视设备大小和压力要求而定,通常需要数小时到数十小时不等。
4. 加热升温在排气结束后,开始进行加热升温。
加热速率应根据样件材质和要求的渗碳深度等因素进行调整,通常为10℃/min到50℃/min不等。
当样件温度达到目标温度时,保持一段时间以使其达到均匀的温度分布。
5. 渗碳在样件达到目标温度并保持一定时间后,开始注入碳源气体进行渗碳处理。
常用的碳源气体包括乙炔、甲烷、丙烷等。
渗碳时间视要求的硬化层厚度而定,通常需要数小时到数十小时不等。
6. 降温在完成渗碳处理后,开始进行降温。
降温速率应根据样件材质和硬化层深度等因素进行调整,通常为10℃/min到50℃/min不等。
当样件表面温度降至室温以下时,可以停止降温。
7. 后处理完成真空渗碳处理后,需要对金属样件进行清洗和除油处理,并对其表面进行抛光和喷涂等后处理工艺。
三、注意事项1. 清洗和除油处理应彻底,以保证样件表面干净无油污。
2. 装夹时应保证样件间距适当,不得过于密集或过于疏松。
3. 加热升温和降温速率应根据样件材质和硬化层深度等因素进行调整,过快或过慢都会影响硬化层的质量。
4. 渗碳时间应根据要求的硬化层厚度进行调整,过长或过短都会影响硬化层的质量。
5. 后处理工艺应细致,以保证金属样件表面光滑无划痕。
浅谈低压真空渗碳热处理技术

203中国设备工程 2020.07 (上)中国设备工程C h i n a P l a n t E n g i n e e r i ng为了提高航空产品渗碳类零件工艺控制水平,于2010年从法国引进了一台低压真空渗碳炉,采用低压真空脉冲渗碳。
由于低压真空渗碳与我厂以往可控气氛渗碳相异之处较大,为充分发挥其优越性,必须熟悉低压真空渗碳工作原理,编制出合理的工艺程序,才能充分展现该设备的先进性。
本文对脉冲渗碳过程进行了初步探讨,通过多次试验,编制多种不同材料、不同技术要求的渗碳工艺程序。
1 低压真空渗碳1.1 渗碳概述不管是可控气氛渗碳还是低压真空渗碳,不外乎以下三个阶段:(1)渗碳介质的分解;(2)碳原子的浅谈低压真空渗碳热处理技术吴平(长沙中传航空传动有限公司,湖南 长沙 410200)摘要:本文探讨了低压真空渗碳原理及炉气成分,以及低压真空渗碳的优势与不足,影响零件表面碳浓度的相关因素。
结合实际应用情况,确定了几种典型齿轮渗碳工艺程序,为航空产品研制生产作好了技术准备。
关键词:低压真空;脉冲渗碳;饱和含碳量;工艺程序 中图分类号:TG156.9 文献标识码:A 文章编号:1671-0711(2020)07(上)-0203-03吸收;(3)碳原子的扩散。
1.2 真空脉冲渗碳原理(1)原理及过程:低压真空渗碳热处理实际上是在低压真空状态下,通过多个强渗(通人渗碳介质)+扩散(通入保护气体)与一个集中的扩散过程,达到满足图纸要求渗层深度的工艺过程,如图1所示。
其控制方法为“饱和值调整法”,即在强渗期使奥氏体固溶碳并饱和,在扩散期使固溶了的碳向内部扩散达到目标要求值,通过调整渗碳、扩散时间比,达到控制表面碳浓度和渗层深度的目的。
T1:第一步乙炔时间(零件表面碳浓度达到1.18所需要的时间)。
T2:第一步扩散时间(零件表面碳浓度达扩散至0.95所需要的时间)。
长焰煤30%比例比长焰煤10%比例高2.7℃/1.5℃,说明长焰煤30%比例的火焰中心是相对偏上的。
渗碳的方法原理应用

渗碳的方法原理应用1. 渗碳的定义渗碳是一种金属表面处理工艺,通过在金属表面形成富碳层,提高金属材料的硬度和耐磨性。
渗碳是通过将含碳化合物加热至高温,使其在金属表面扩散,形成富碳层的过程。
2. 渗碳的原理渗碳的原理基于扩散理论,即在高温下,含碳化合物中的碳原子会从高浓度区域向低浓度区域扩散,最终在金属表面形成富碳层。
渗碳的速率取决于温度、时间和温度梯度。
3. 渗碳的方法渗碳的方法主要包括以下几种:•固体渗碳:将含碳化合物(如氰化钠、氰化钾等)与金属样品一同加入高温容器中,通过高温加热使碳原子扩散到金属表面。
•液体渗碳:通过将含有碳源的液体(如液态碳氢化合物)浸泡金属样品,使碳原子通过溶液扩散到金属表面。
•气体渗碳:通过在高温环境下,将含碳气体(如甲烷、一氧化碳等)与金属样品接触,使碳原子在金属表面扩散。
•离子渗碳:通过将含碳化合物(如氰化物)溶解在溶剂中,再通过电场作用将碳离子引入金属样品,实现渗碳。
4. 渗碳的应用渗碳广泛应用于许多领域,主要包括以下几个方面:•机械工程:在机械工程中,渗碳可以提高金属的硬度和耐磨性,用于制造轴承、齿轮等零部件,增加其使用寿命。
•汽车工业:在汽车工业中,渗碳可以用于制造曲轴、减震器等零部件,提高其耐磨性和强度。
•航空航天:在航空航天领域,渗碳可用于制造发动机零部件、航空轴承等高性能材料,提高其抗腐蚀性能和疲劳寿命。
•工具制造:在工具制造中,渗碳可以用于制造刀具、钻头等工具,提高其切削性能和寿命。
•能源领域:在能源领域,渗碳可用于制造石油钻具、钻井机零部件等设备,提高其耐磨性和使用寿命。
5. 渗碳的优点和注意事项渗碳具有以下优点:•提高材料硬度和耐磨性;•延长材料使用寿命;•显著改善材料表面性能。
渗碳需要注意以下事项:•清洁金属表面,避免表面有锈蚀、油污等影响渗碳效果;•控制渗碳工艺参数,如温度、时间,以保证渗碳层的质量;•选择合适的渗碳方法,根据不同材料和应用场景进行选择;•进行适当的后处理,如淬火、回火等,以提高渗碳层的性能。
低压真空渗碳工艺论文

低压真空渗碳工艺论文摘要:本文通过对可控气氛渗碳工艺和低压真空渗碳工艺各自特点及所采用设备的介绍,说明了低压真空渗碳工艺的优势所在,并指出其在汽车工业等领域的应用前景。
关键词:低压真空渗碳工艺、可控气氛渗碳工艺一、可控气氛渗碳工艺可控气氛渗碳工艺主要包括滴注式气体渗碳工艺、吸热式气体渗碳工艺、氮基气体渗碳工艺、直生式气体渗碳工艺。
滴注式气体渗碳工艺是在密封室内通入有机液体甲醇和丙酮(或乙酸乙酯等),以适当的数量直接滴人炉内而制得所需气氛的。
甲醇热裂分解产物的渗碳能力很低,它主要是起携带气的作用,使炉内有一定的正压;起渗碳作用的气体主要是由丙酮或乙酸乙酯热裂分解形成的。
滴注式气体渗碳工艺对设备要求较低,碳势控制精度较差,只适用于一般零件的处理。
吸热式气体渗碳工艺的渗碳气氛由吸热式气体加富化气组成,吸热式气体主要包括天然气、煤气、丙烷、丁烷等,一般采用甲烷或丙烷作富化气。
需要有吸热式气氛发生装置。
氮基气氛渗碳工艺是指以氮气作为载体添加富化气进行渗碳的工艺,富化气主要有丙烷、丙酮等,同时通入甲醇作为基础气氛。
直生式气氛渗碳工艺是将燃料与氧化剂直接通入炉内形成渗碳气氛的工艺。
采用上述各渗碳工艺时,各种有机液体热裂分解时产生的主要是CO和H。
同时还存在少量的其它产物。
在一定条件下,达到平衡时,炉气的各成分之间具有一定的比例平衡关系。
可控气氛渗碳工艺已应用多年,积累了丰富的经验,可以满足一般零件的性能要求,但也有自身的缺点,例如:无法解决表面内氧化问题,即在渗层表面出现一层很薄的非马氏体组织,影响零件的疲劳性能;无法解决高温渗碳及深层渗碳问题;生产能耗高;生产区域环境较差。
这些设备一般都布置在独立的热处理车间,或者与机加工车间组建联合厂房,但与机加工车间之间需要有隔墙,以减少对加工设备的影响,并要求加强热处理车间的排烟措施,改善生产环境。
二、低压真空渗碳工艺低压真空渗碳工艺的真空压力一般为10—100Pa。
真空渗碳炉的性能介绍

真空渗碳炉的性能介绍
真空渗碳炉具有低压渗碳、油淬和加压气冷等多种功能,该设备可以对航天航空工业及其它机械工业所使用各类零部件进行相关的热处理,诸如:18CrNi8、12Cr2Ni4A、12Cr2Ni3A等高合金渗碳钢的渗碳及渗碳后的淬火,结构渗碳钢的渗碳及渗碳后的淬火、工模具钢、精密轴承、油泵油嘴机械件、精密机器零件等各种结构钢的油淬等。
大幅提升模具的机械性能和使用寿命。
真空渗碳炉的工作原理:将工件装入真空炉中,抽真空并加热,使炉内净化,达到渗碳温度后通入碳氢化合物(如丙烷)进行渗碳,经过一定时间后切断渗碳剂,再抽真空进行扩散。
这种方法可实现高温渗碳(1040℃),缩短渗碳时间。
渗层中不出现内氧化,也不存在渗碳层表面的含碳量低于次层的问题,并可通过脉冲方式真空渗碳,使盲孔和小孔获得均匀渗碳层。
低压真空渗碳法及其优点:低压真空渗碳是在低压真空状态下,通过多次强渗+扩散过程,以达到零件渗层深度要求的工艺过程,其控制方法为“饱和值调整法”。
即在强渗期使奥氏体固溶碳饱和,在扩散期固溶的碳向内部扩散到目标的要求值,通过调整渗碳、扩散时间比,达到控制表面碳浓度和渗碳层深度的目的。
优点:1.无内氧化,能显著提高零件表面疲劳性能。
2.处理后畸变小。
3.计算机控制,渗碳精度高。
4.处理后产品表面呈光亮状,可不经清洗、喷丸工序。
真空渗碳炉的结构特点:加热元件沿加热室圆周均匀布置,温度均匀性高;加热室和冷却室分开,生产效率高、使用成本低;冷却均
匀性好,工件变形小;渗碳气体喷嘴沿加热室圆周均匀布置,渗碳层厚度均匀。
- 1、下载文档前请自行甄别文档内容的完整性,平台不提供额外的编辑、内容补充、找答案等附加服务。
- 2、"仅部分预览"的文档,不可在线预览部分如存在完整性等问题,可反馈申请退款(可完整预览的文档不适用该条件!)。
- 3、如文档侵犯您的权益,请联系客服反馈,我们会尽快为您处理(人工客服工作时间:9:00-18:30)。
真空渗碳技术工艺控制原理
与传统井式炉气体渗碳工艺不同,真空渗碳时“碳势”的概念失效,不存在气体渗碳时的气氛反应平衡,也就不能使用氧探头等设备测量真空渗碳时的“碳势”。
由于真空渗碳热处理设备的精密性、可控性好和工艺重现性好等优点,真空渗碳工艺主要采用强渗—扩散型工艺控制方法,即采用多个强渗—扩散周期,在每一个周期内通过短时间的强渗(通常强渗时间为30s ~ 180s),工件表层碳浓度达到该渗碳温度下的奥氏体饱和碳浓度,随后停止渗碳气氛供应,进入扩散阶段,当表面碳浓度达到设定的最低碳浓度时,扩散阶段结束,再次通入渗碳气氛,如此进行多个循环,直至达到工艺要求的最终表面碳浓度和渗层深度,最后执行相应的淬火工艺。
图1即为真空渗碳过程工件表面碳浓度分布图。
图1真空渗碳过程工件表面碳浓度随时间分布
真空渗碳热处理工艺过程主要分为以下几步:
(1)工件清洗、入炉,在真空条件(小于10Pa,基本达到无氧条件)下进行加热,根据工件材质可进行分段加热,可选择通入N2保持一定分压加快真空加热室内热传递速率;
(2)达到设定的奥氏体化温度并保温,关闭和抽去N2,充入C2H2,保持一定分压开始进行强渗,进入第一个渗碳周期,强渗一定时间为使工件表面碳浓度达到该温度下奥氏体饱和碳浓度;
(3)关闭和抽去C2H2,充入N2,进入扩散阶段,保持一定分压,使工件表面较高碳浓度向工件心部低碳浓度区扩散一定时间,使工件表面碳浓度下降,渗碳层厚度增加;
(4)当工件表面碳浓度下降至预先设定的碳浓度,关闭和抽去N2,再充入C2H2,保持分压,进入第二个渗碳周期,然后重复步骤(2)和(3),并在最后一个渗碳周期时给一个较长时间的扩散,以满足工件最终表面碳浓度的要求。
在这样多个渗碳周期内完成碳的扩散并调整工件表面碳浓度,达到工艺要求的渗碳层深度;
(5)真空渗碳过程结束后,工件降温至淬火温度并保温一定时间,然后将工件转移至冷室(淬火室),根据热处理工艺要求进行真空油淬。
淬火结束后对工件进行清洗,然后执行回火工艺。