模具组立标准
模具作业标准

模具作业标准模具作业标准1、凸模1.1形状与尺⼨应符合图纸或提供样件的要求。
完成⼑⼝形状确认后按DR引伸件研合凸模(⽤板件合模):钳⼯仕上时应以凸模为基准,注意清⾓,避免研合时碰伤棱线,试按DR/TR之板件研配凸模。
棱线、搭接线应没有凹凸、扭曲的现象,R⾓应光滑圆顺且没有凹凸及尖⾓。
1.2凸模或凹模的研合率:管理⾯80%以上,准管理⾯70%以上。
1.3因特殊要求,铸件易磨损部位(或堆焊⼑⼝),应该⽤合⾦钢焊条(7号钢)填补,堆焊部位的深度、宽度应在10×10mm以上,或者⽤合⾦钢块镶嵌在易磨损部位。
1.4表⾯粗糙度:主要部位0.4,次要部位0.8。
1.5如凸模是分块的,则各镶块间接合⾯间隙应⼩于0.1mm。
1.6镶块与窝座(或挡块)及键的配合应⽆间隙。
1.7材料及淬⽕硬度:⼀般使⽤合⾦铸铁GM241、GM246或ICD5,⽕焰的谇⽕硬度为HRC50以上。
1.8⼑⼝应⽆裂纹、崩刃现象。
1.9⼑⼝垂直度应不⼤于0.01mm,不允许有倒锥。
1.10⼑⼝表⾯粗糙度,主要部位0.8,次要部位1.6.1.11⼑⼝镶块接合⾯缝隙,料厚⼤于0.8mm的间隙不⼤于0.15mm,料厚⼩于0.8mm的间隙应⼩于0.05mm。
1.12多孔冲及异型⾯冲载,其凸模的位置、相对⾼度应准确可靠,应保证⼑⼝的切⼊两基本⼀致,使切⼝顺利完成,若切⼝顺利完成,若⼤⾯积冲切厚板件,⼑⼝应采⽤阶梯形(有⾼低差)。
1.13凸模材料为合⾦钢,淬⽕硬度为HRC56~62.1.14销孔的表⾯粗糙度为1.6,精度为H7.2、凹模2.1形状与尺⼨应符合凸模的要求,棱线、搭接线应没有凹凸,扭曲的现象,R⾓应光滑圆顺且没有凹凸及尖⾓。
2.2⼯作部位表⾯粗糙度:主要部位低于0.8,次要部位1.6,凹模⼝圆⾓处粗糙度不低于0.4。
2.3因特殊要求,铸件易磨损部位(或堆焊⼑⼝),应该⽤合⾦钢焊条填补,堆焊部位的深度、宽度应在10×10mm以上,或者⽤合⾦钢块镶嵌在易磨损部位。
模具组立
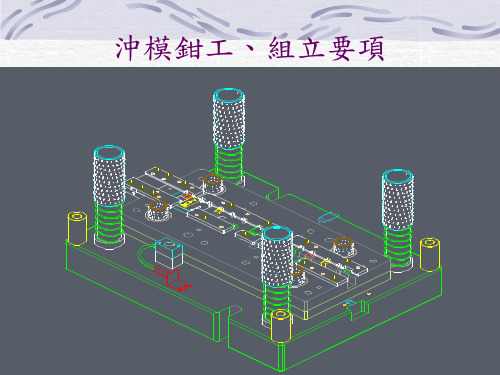
D.使用溫度(638膠在使用溫度50攝氏度以下, 其膠合強度受溫度影響不大,溫度越高,缺氧膠 強度越低.)
2在灌膠之前用酒精將主導套外表面油污清潔乾 淨
3用拋光砂輪將模座主導套內孔表面之銹蹟及氧 化層清除,並用酒敬清洗
模座鉗工、組立要項
將8~12支等高桿分別固定在上,下模座上(等高 桿的高度須確認)。
模具組立前檢查要項
檢查零件是否齊全 檢查沖子能否穿過剝板入塊 模板和契塊R角是否干涉 剝料板入塊使用ASP23 V-cut.扇形調整沖子使用V3
模座組立需準備之器具
工具:銼刀、 油石、 砂紙、 矽鋼片、 角尺 、 缺氧膠638、 酒精。
量具:槓桿量錶 ,塊規,游标卡尺.
模座鉗工、組立要項
將主導柱外表用煤油及酒精清洗乾淨后,用乾 淨布包紮好放入冷凍庫(8-12H)。
模具組立異常及分析
• 剝料板與下模板不貼合 A.模板之間有異物 B.上下模之副導套裝錯 C.剝料板鑲件與下模有幹涉 D.剝料板鑲件沒有裝平 E.倒料板與剝板有幹涉 F.倒板螺絲與剝板有幹涉 G.模板加工翹曲
模具組立異常及分析
定位銷PIN套與上模座孔配合過緊 A.主導套灌膠時,主導套與導套孔之閒細沒有調整好. B.主導套灌膠時,主導柱與膝下模座之垂直度沒有校 驗. C.合銷孔尺寸有誤 整體合模時,閉模高度過大(大於91.98MM) A.成型衝頭與下模有乾涉 B.調整桿調整過量 C.SLIDE槽讓位不夠 D.固定P02板與 P01板時,沒有用合销定位.
上模鉗工、組立要項
蓋上上模座,此時上墊板和模座應該是密合(蓋 入之前STOPPER先拆除) 用0.05㎜矽鋼片檢查ψ12合梢BUSH四周和孔璧 是否有干涉 檢查上,下模座間距離 (91.95㎜間距不得 超過91.98㎜)
模具组立手册

1.磁性產生原因﹕加工過程中﹐與磁體接觸﹐ 由于磁場的作用使模板自身帶有磁性。 2.退磁目的﹕是為了避免鐵屑或一些雜質吸附 在模板上而影響后續工作。 3.退磁方法﹕將模板放在退磁機上左右慢慢移 動模板﹐每一個來回模板都需過退磁機中線﹐ 直到磁性去除。 確認磁性去除的方法﹕用薄的錫鋼片放在模板 表面﹐拿起時感覺無磁力即可。
b 板面拋光﹕在板面上噴洒酒精﹐利用大 塊200干淨油石順著模板研磨紋路平推模 板﹐將毛刺去掉。 3.部位
前面倒角的部位。
Page 29
倒角前
Page 30
倒角后
Page 31
拋光后
Page 32
五﹑清冼
1.目的﹕保証精度 2.方法 a 氣槍吹出吸附在模板空位處的粉塵及雜質臟物。 b 用干淨抹布粘上酒精﹐清冼模板各個主要孔位 (銷釘孔﹐灌膠pin孔﹐主導柱孔﹐主導柱導套孔) 及板面。 c 再用氣槍將各個孔位及板面吹干淨。
Page 5
cad
二﹑模具零件分類
Page 6
上模 下模
導向零件
導柱 導套
Page 7
模具在固定的行程內進行往 復運動時依靠導柱與導套的 配合導向,以保証模具在高 速沖壓時的精度.
定位零件
Page 8
導位針 導料板 側刃
導 位 針
定位零件都是用來導正在送料 過程中料帶在模具中的位置精 度.
導 料 板
灌膠pin 灌膠pin頭
Page 49
限位螺絲 限位套 副導套
灌膠pin套 導柱襯套 副導柱
Page 50
二﹑模仁板標准件的裝配
將模仁板正面平放于鋪好雜布的鉗工桌上﹐將 副導套和副導套孔內涂上潤滑油﹐將副導套導引向 下垂直裝入副導套孔內﹐用力壓入﹐將鋼珠置于副 導套上﹐用銅棒將導套敲至底部﹐在敲擊過程中必 須保証副導套與板面垂直。再將模仁板翻轉180 度﹐置于三塊鋪好雜布的墊塊上﹐通過滾珠用銅棒 將導套敲至板面以下0.5mm。
五金模具组立及维修手法
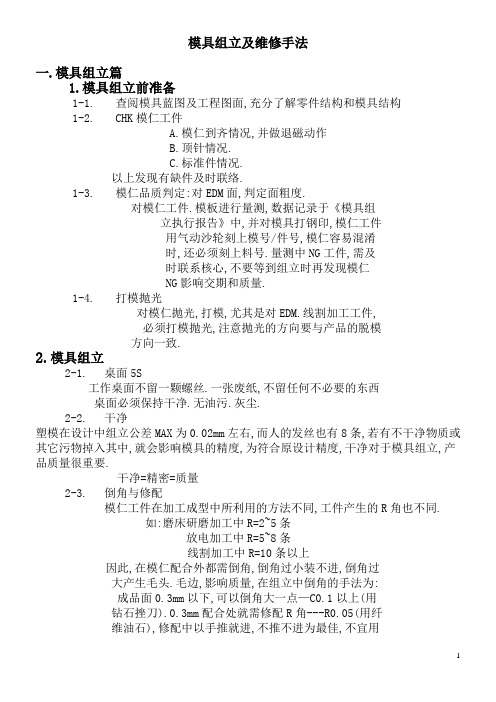
模具组立及维修手法一.模具组立篇1.模具组立前准备1-1.查阅模具蓝图及工程图面,充分了解零件结构和模具结构1-2.CHK模仁工件A.模仁到齐情况,并做退磁动作B.顶针情况.C.标准件情况.以上发现有缺件及时联络.1-3.模仁品质判定:对EDM面,判定面粗度.对模仁工件.模板进行量测,数据记录于《模具组立执行报告》中,并对模具打钢印,模仁工件用气动沙轮刻上模号/件号,模仁容易混淆时,还必须刻上料号.量测中NG工件,需及时联系核心,不要等到组立时再发现模仁NG影响交期和质量.1-4.打模抛光对模仁抛光,打模,尤其是对EDM.线割加工工件,必须打模抛光,注意抛光的方向要与产品的脱模方向一致.2.模具组立2-1.桌面5S工作桌面不留一颗螺丝.一张废纸,不留任何不必要的东西桌面必须保持干净.无油污.灰尘.2-2.干净塑模在设计中组立公差MAX为0.02mm左右,而人的发丝也有8条,若有不干净物质或其它污物掉入其中,就会影响模具的精度,为符合原设计精度,干净对于模具组立,产品质量很重要.干净=精密=质量2-3.倒角与修配模仁工件在加工成型中所利用的方法不同,工件产生的R角也不同.如:磨床研磨加工中R=2~5条放电加工中R=5~8条线割加工中R=10条以上因此,在模仁配合外都需倒角,倒角过小装不进,倒角过大产生毛头.毛边,影响质量,在组立中倒角的手法为:成品面0.3mm以下,可以倒角大一点—C0.1以上(用钻石挫刀).0.3mm配合处就需修配R角---R0.05(用纤维油石),修配中以手推就进,不推不进为最佳,不宜用铜棒敲打.在倒角中应注意:*. 模仁成型面不能倒角*. 模仁上下能翻面使用时,不能倒角*. 模仁前后左右能翻面使用时,不能倒角2-4.排气塑料填充模具时,由于注射压力.速度过大,温度过高,塑料易分解出瓦斯气体.塑料颗粒.纤维填料.结晶体等,留于模腔内,造成产品包风.烧焦.不饱模等不良的产生,并且腐蚀模仁,降低模仁的寿命.开排气的目的在于把残物和模腔内的空气排出,使烧融塑料须顺畅并全部充满模腔内.开排气中,应以最大的孔径.最短的距离.最快的速度把气体排出,排气槽的深度应根据原料的材质而定.如:h表示深度PBT: h≦0.020mm PCT: h≦0.018mmPPS: h= 0.008mm LCP: h= 0.020mm对于流速过小的产品,可利用顶出机构的间隙排出,另外在无法开排气槽的工作部位,可利用增加顶针的方法来排气,如778N3模生产的DT 001-0006-110产品,站脚因排气不良经常造成产品包风,模仁腐蚀影响质量,对此模仁站脚外增加ψ0.80的顶针改善OK.应注意事项:*最小肉厚处一定要制做排气槽*各模仁底部排气槽需与顶针相通,以利排气2-5 顶针计算切割与倒角2-5-1顶针在计算切割时要高出成品面 0.02-0.005mm2-5-2顶针视情况作倒角a.四边倒角当顶针孔为线割时,顶针因而倒角b.两边倒角当顶针孔为研磨加工时,顶针两边倒角c.三边倒角如1061N2模中1*1mm的方顶针,在装配时可倒三边,而另一边不倒,便于主体镶件向靠而成型.d.把顶针的长度.规格.数量记录于《模具组立报告》中2-6 合模2-6-1观察组立是否正确2-6-2用卡尺量测公/母模情况,防止模仁反装2-6-3用红丹靠破观察合模情况,滑块要一次组立一CAV,并确认滑动平稳,不可干涉过紧.2-6-4及时记录组立碰到的问题点,并加以改善2-6-5每互组一件模仁,需以量具检查累积厚度是否正确.3.试模3-1调整最佳成型参数并记录于《模具条件记录表》中.3-2试模OK后,量测产品尺寸,将样品及检测数据送制工评估 3-3样品课内留样3-4记录试模结果,尤其不良待改善之处.4.组模报告总结4-1对模具设计中的缺失,进行提报4-2模具需改善的地方作报告4-3成型大量生产中应注意的问题点:如1485N1模,生产中需高速.高压注射二.模具维修篇1.维修前准备1-1取得不良样品分析不良原因,确定修模内容1-2 CHK模仁备品情况,确认能否维修1-3 查阅前几次维修状况,看是否相同问题多次发生,是的改善,不是也可以给此次维修以方向.2.模具维修2-1做好修模前的5S2-2干净干净=精密为了做到干净,必须放于组模平板上维修,维修中不能戴手套.2-3拆模顺序2-3-1打开公/母模2-3-2取下滑块2-3-3拆公模底板以及模脚2-3-4拆顶出板2-3-5拆公模取Block2-3-6修公模a.拆Blockb.再NG模仁在取模仁中,不得同时把所有CAV全部拆下,应拆一个CAV修一个,并作好对比.c. 清洁模仁.模板d.开排气槽,排气槽,需导引至顶针孔e.其它维修利用磨床.研磨维修f.组立模仁每互组一件模仁需以量具检查.模仁累积厚度是否正确.2-4 维修后组立2-4-1 组立公/母模Block,并确认长.宽.高尺寸是否正确.2-4-2 组模组模后,对各模板均需擦干净,并对滑块.导柱.顶针加上黄油与顶针油.2-5 做好修模后5S3.架模试产3-1架模调机生产3-2查看产品的质量,交IPQC验测OK后填《模具维修记录》,NG 分析原因重修.4.模具维修后结案4-1填写《模具维修记录卡》4-2对领用备品登记,发现备品未达到安全库存量需提报4-3 对取下之NG模仁需交于备品管理员4-4 改模作业,需将换下的模仁.顶针.包扎标示定位放置4-5 对堵CAV或其它改善事项,填写改善报告。
模具设计规范标准规范标准

模具设计规范标准规范标准模具设计标准规范1﹑⽬的:确保模具设计规范化,统⼀化.能将设计意图正确的传达给制造部门.避免或减少失误。
2﹑范围:⼯程部设计组接收⼯程部产品组转交的图⽂件、样品等资料到图纸发⾏为⽌之阶段均属之。
3﹑权责:3.1 ⼯程部设计组:负责模具开发设计及设计变更、2D/3D产品图⾯设计、3D建模、设计模具的组⽴图、3D拆模与拆电极、绘制零件图.3.2 现场加⼯各组:加⼯各组的组长,在加⼯前需先审视加⼯图,若发现与原先检讨的不符合或有误,甚⾄不合理,需⽴即反应⼯程部检讨查核后,⽅可继续加⼯。
4. 名词释义:⽆5﹑作图环境标准:5.1⽂字标准5.1.1字体。
数字及英⽂使⽤“Arial”字体,中⽂使⽤“标楷体”。
5.1.2⽂字⼤⼩。
为了使整套图⾯⽂字视觉效果⼀致,在标准图框(即1:1图框,A4为297*210)中,设定字⾼为3.0,宽0.85。
5.2 图⾯标准5.2.1 图框:为了便于查阅,装订,保存,图框统⼀标准如下:A0图框:841*1189横印(附件⼀)A1图框:594*841横印(附件⼆)A2图框:420*594横印(附件三)A3图框:420*297横印(附件四)A4图框:297*210直印(附件五)5.2.2 图⾯要求5.2.2.1零件图⾯按照其在模具当中的位置分类摆放,以便于查找。
5.2.2.2尺⼨标注⽅式。
除了圆以外,所有模板、模仁之尺⼨均采⽤坐标标注⽅式。
5.2.2.3 视图投影关系:第三视⾓法。
5.2.3图档版本版本编号采⽤⼤写字母“A”加上⼀位数字序号,数字序号按照图⽂件完成的时间先后顺序进⾏排列。
例如A1、A2、A3等。
5.2.4 图层与线型:为了便于图形与尺⼨的识别,图层与线型统⼀标准如下:5.3编码原则5.3.1模具结构和主要零件名称如下:5.3.2零件名称与对应的编号如下:5.3.2.1模胚部分编号零件名称编号零件名称A01 上固定板A09 脱料板A02 下固定板A10 推板A03 母模板A11 上流道板A04 公模板A12 电热板A05 母模承板A13 脚垫A06 公模承板A14 浇道脚垫A07 上顶针板A08 下顶针板5.3.2.2镶件部分5.3.2.3⼀般零件部分5.3.2.3⼀般零件部分(续)5.3.2.4特殊零件部分5.3.3编码⽅式5.3.3.1模具编码⽅式。
模具组立作业指导书

模具组装作业指导书1.目的1.1便于现场修模人员维修组装作业标准化、规范化,减少失误,提高工作效率,满足生产需要2.范围本程序适用于在于本公司模具维修保养作业3.定义无4.职责4.1模具技工:熟悉模具制造技术,模具维修程序及注意事项.4.2模具师傅:负责指导、监督、检查模具维修全过程5.程序5.1依据“模具维修申请单”及“模具组立确认书”所列之异常逐一确认模具维修是否均已处理OK〈除因模具纳期关系经组内主管同意暂作保留之外〉并经模具维修负责人员逐一确认后,方可开始组立,组立前应对各部件进行保养.5.2依据记号将模仁入子逐一装入模仁(装入前应确认模仁、入子、芯子沉头处配合内角需有轻微避空倒角),并比对部品及图面有无装错.(入子装入后,沉头实装高度凹于模仁底0.01~0.02(特殊要求依实际状况确认);另模仁底面槽穴开口及顶针、作动入子孔处倒角需完善)5.3装好模仁、装上密封圈.5.3.1装上密封圈必须是OK的〈有0.7mm左右之预压量,无缺口,外径小于密封槽外径1mm左右,内径大于密封槽内径1mm左右〉,否则会造成模具漏水;装上密封圈时应在密封圈上抹上粘性黄油,以防装模时密封圈掉落.35.3.2模仁组装前小组主管需先确认各模板槽底部各孔穴处倒角是否完善,对模板有肿起先行处理(由小组主管确认).组立过程中当模仁都比较紧时,应尽量将模板平放来装模;当模板需直立装时,需注意油封掉落及入子退后的问题发生.注意: 一些较松之入子在装模时可能会退出,从而导致入子损伤甚至未被组立者发现在此时应作相应处理.5.4锁好模仁螺丝,用扳手锁紧后以1.5IB胶锤轻敲两下,不可使用加力杆,若发现有螺丝滑牙或内六角沉头损坏,应及时更换,以免造成下次拆模的麻烦.5.5装配顶针.(注意此时容易忘装回位梢弹簧.)5.5.1 装顶针前(确认回位销、弹簧孔、倒角无完善,小组主管确认),应先将顶针擦拭干凈,再喷上耐高温顶针油,以免顶针上附着的瓦斯垢堵塞了排气或造成顶针卡死,抹油时以顶针顶出行程算出顶针抹油起始位置,(如顶出行程20mm,则顶针由前端20mm处下2~5mm为抹油起始处延伸至根部)且只须喷薄薄的一层即可,以摸有油看无油为标准,以免造成部品油污.5.5.2装顶针时,先行确认顶针沉头高度配合凹入顶针板0.01~0.02mm,(新规模具顶针板沉头孔的深度以数据呈现判定)。
模具基本组立资料

分为两种,一为机台本身的空压缸,此时模具需配备2~4之顶升杆
,一为弹簧,但需用套筒螺栓将下扥料块锁紧,此时下扥料块需比
下模体高1~2mm‧
5、若为A、B、C Line的冲孔下料模时,下模体与下承板组立后需注
意,消屑孔是否正常,冲压后的铁屑是否能顺利排出,还需注意下
M8---15mm至110mm长M10---20mm至150mm长
M12---25mm至130mm长
2、套筒螺丝
套筒螺丝有2种
M8*50 mm长M10*50mm长
(2)定位销
依外径分为2种规格
1、∮8
∮8*50mm及∮8*60mm长
2、∮10
∮10*50mm及∮10*60mm长
(3)导柱
导柱分为2大类
的下脱料块须比下料下模体高约1~2mm,才能令下料后的料片不
会卡在下料下模体上,且容易将料片取出‧
3、若为500吨折角模时,首先下模需依图面全周研磨R角,下脱料
块须与工件合模至┌松紧适中┘,最后锁上下脱料块时,锁紧后的
下脱料块也需较折角下模体高2~3mm‧
4、若为A、B、C Line的吞型模时,将下模体仕上后,再组立于下承
1、若为500吨吞型模,需将下模体先仕上抛光后,方可组立在下承板
上,并注意下扥料块与下模体是否有适当的间隙(约在0.3mm以内
的间隙)‧
模具组立基本资料
NO: 3
知识类
共5页之3页
2、若模具为500吨冲孔下料模,下模体须与吞型后的工件实际合模
至松紧度适中,使工件与冲孔下料的下模体冲断、切断处能贴面
,并能在冲压后容易将工件取出,最后再组立下脱料块,组立后
钳工车间模具组立研配工艺和质量管理流程

钳工车间模具组立研配工艺和质量管理流程
一、引言
钳工车间模具组立是生产过程中关键的一环,直接影响产品质量和生产效率。
本文将详细介绍钳工车间模具组立的研配工艺和质量管理流程,旨在提高工艺水平、优化生产流程,保证产品质量。
二、模具组立工艺流程
1.材料准备:
–选择适合的材料,根据模具设计图纸准确切割材料;
–确保材料质量和尺寸符合要求。
2.零部件加工:
–按照设计要求对各零部件进行精密加工;
–采用适当的加工工艺和设备,确保零部件精度。
3.组装工艺:
–按照组立顺序进行组装,注意避免零部件损坏;
–合理利用辅助工具和夹具,保证组装精度。
4.调试验收:
–完成模具组立后进行调试验收;
–检查各部件的协调性和运行情况,调整优化。
三、模具组立质量管理流程
1.质量控制点:
–制定质量控制点,包括材料、加工、组装等环节;
–每个环节设立质量检查,确保质量过程可控。
2.检验标准:
–制定模具组立的检验标准,包括外观质量、尺寸精度等要求;
–按照标准进行抽样检验,保证产品质量。
3.记录与反馈:
–建立质量记录档案,记录每个模具的质量数据和检验结果;
–发现质量问题时及时反馈给相关部门进行改进。
四、总结
钳工车间模具组立的研配工艺和质量管理流程是保证产品质量的关键环节。
通
过严格的工艺流程和质量管理措施,可以有效提高模具组立的效率和质量,满足生
产需求,提升企业竞争力。
在实际生产中,应根据具体情况不断优化和改进流程,持续提升模具组立工艺水平和质量控制能力。
- 1、下载文档前请自行甄别文档内容的完整性,平台不提供额外的编辑、内容补充、找答案等附加服务。
- 2、"仅部分预览"的文档,不可在线预览部分如存在完整性等问题,可反馈申请退款(可完整预览的文档不适用该条件!)。
- 3、如文档侵犯您的权益,请联系客服反馈,我们会尽快为您处理(人工客服工作时间:9:00-18:30)。
模具組立標準
一﹒組立流程簡介
待組立模具圖面的清點和整理→模板确認清點→零件确認清點→
模板倒角拋光→零件倒角刻字分類→下模板組立→背板組立→
上模板組立→分站合模→上下模合模→切紙合模→裝置上下模彈簧→最后點檢二﹒組立工具
1﹒“T”型扳手一套
2﹒“L”型扳手一套附套簡
3﹐8mm,10mm扭力扳手各一把
4﹒厚薄規一把
5﹐鑽石銼刀一把
6﹒鐵工銼刀一把
7﹒气動研輪筆一支﹐附氧化鋁研輪筆頭﹐海綿砂輪筆頭各一組
8﹒大小銅棒各一支
9﹒3﹐4頂針各一支﹐窄頂杆和一支
10﹒牛油一筒
11﹒剪刀一把
12﹒小膠盤三個﹐雙面膠﹐白色膠紙﹐透明膠各一卷
13﹒奇异筆一支
14﹒5um,0.01mm,0.08mm,0.10mm矽銅片
15﹒630#潤滑油
16﹒WD-40防鏽油一瓶
17﹒面巾紙一卷
18﹒1500ML工業酒精﹐500ML煤油
19﹒電子游標卡尺一把
20﹒垂直規淮一個
21﹒45mm高度等高塊兩個
22﹒800#砂紙﹐1500#砂紙各10張
23﹒干淨碎布
24﹒2000#﹐5000#﹐8000#﹐12000#鑽石膏各少許﹐拋光液少許
25﹒竹筷﹐牙勾各一把
26﹒纖油石﹐白色油石各一塊
27﹒布輪一個﹐美工刀一把
28﹒字符一組
29﹒消磁器及附屬穩壓器一組
三﹒圖面清點
圖面清點依上﹑下模順序按模具圖面明細表進行清點﹐對此缺少的圖面可依程序向資料中心申請補充﹒圖面中的Layout Assiy Maintsnant Layout是組立時為常用的圖面﹐也是組模的依据﹒確認組模所需的下模﹐剝料板和上模的標准件的規格及數量﹒
四﹒新模板檢查
1﹒模板采用板壘板的方式依UP.UB.PH.PPS.PS.DIE.LB.LP序配對﹐檢查孔与孔﹐框口与框口的對應位置有無錯誤﹒
2﹒螺紋孔實配﹐實配時將螺釘擰到底﹐檢查螺紋孔是否完全攻絲﹒
3﹒檢查下模座﹐刀口固定板﹐背板落料孔﹐保養孔是否對正﹐有無漏加工或加工有誤﹒
4﹒檢查上模座﹐衝子固定板背板﹐衝子固定板﹐剝料背板的吊螺絲的外套與配合孔是否對正﹐有無錯位﹐套筒是否与配合孔能順利插入和拔出﹒
5﹒對上模座的衝子固定板背板衝子固定板的側沖斜梢孔﹐用斜梢試插﹐正常情況應能順利插進拔出沒有干涉﹒
6﹒將下模﹑夾板及剝料板進行實配﹐夾板与剝料板配合是否良好﹐正常情況剝料板与下模板應無干涉﹐有合理的間隙﹒
7﹒對照圖面看模板是否有漏加或錯加工﹒
8﹒模仁P﹐S﹐D類配﹐看模板框口加工是否漏加工﹐錯加工﹒
9﹒對檢查中出現的加工造成的品質异常﹐填寫品質异常聯絡單﹔退庫處理﹒
注; UP--- 上模座UB--- 上墊板PH--- 上夾板
PPS-- 脫背版PS--- 脫料版DIE-- 下模板
LB--- 下墊板LP--- 下模座
五﹒模板﹐倒角﹐拋光﹐去磁﹐清洗
1﹒對模板四周的棱角用紅色氧化鋁砂輪﹐倒角R2﹒5﹐去掉毛刺﹐防止組立時模板刮傷手﹒
2﹒模板的螺紋孔不用倒角﹐對模板的圖形定位孔﹐配合孔可用海綿砂輸倒角R0﹒5﹐但倒角時切忌划傷孔的內表面及模板工作面﹐以免損傷精度﹒
3﹒模板的模仁安裝的框口不能用砂輪筆倒角而要用鑽石銼刀倒角﹐對剝料板﹐剝料板背板﹐刀口固定板框口應清角的地方﹐可用鑽石三角挫刀輕輕將四周的90。
角清除殘留的鐵屑以利于安裝﹐防止安裝時敲崩模仁或損傷框口﹐保證組立精度﹒
4﹒將模仁倒角好以后﹐置于鉗工桌干淨碎布上﹐先用800#砂紙進行拋光﹐如果模板生鏽可用纖維油石加WD-40將跡磨掉﹐然后用1500#砂輪紙進行拋光﹐拋光時用力要均勻﹐方向要与模板平面的紋路方向一致﹒拋光至鏡面后再酒清清洗﹐然后用消磁器去磁﹒
六﹒零件的倒角﹐刻字﹐拋光
1﹒對衝子﹐成形入子﹐刀口﹐鑲件的非工作部分用氮動砂輸倒角或鑽石銼刀倒角﹒
2﹒倒角時不能傷及工作面及刀口﹒
3﹒衝子倒角及壓板的固定為槽界﹐不是衝裁刀口的部需倒角﹒
4﹒對成型入子的倒角方法是﹕成型工作面外入夾板接触面均需倒角﹒
5﹐對刀口的倒角方法是﹕根据刀口的落料斜度判定﹐刀口的上部孔徑小于底部孔徑﹐從而將孔徑大的那一面即非工作面進行倒角﹐外框可倒角﹐內孔不可倒角﹒
6﹒對鑲件的倒角方法是﹕除了對鑲件与接触的棱角倒角外﹐還應對鑲件內部要与衝子配合的接口用油石將棱角刮平滑﹐使衝子能順利插入﹒
7﹒對成型入子等成型零件要用鑽石膏進行拋光﹐以免試模壓傷成品或表面粗糙度太大﹒
8﹒對凸點下模入子要用油石將其棱角刮的圓滑一點﹐以免試模凸點易崩﹒
9﹒將倒角拋光的零件刻上料號﹐件號﹐版別﹐依各料號的p,s,d順序先用白色膠紙保護好刀口﹐再用雙面膠按序粘置于膠盤中待用﹒
七﹒組立
(一).先從模具的整体框架大的方向進行裝配
1.組立時先將与本模具相關的導套,導柱按標准件間隙裝配到下模板,脫板,夾板上.
2.按坐標基准合并夾板,脫板,下模板使其脫板,下模板重壘后能順暢在裝有導柱的夾板上滑動
(注意:不能有間隙過大導致任何一塊模板有晃動現象)
(二).把各個相關零件歸位,按圖面要求進行全方面的裝配組立.
1.將研配好的下模零件按圖面要求裝入下模板,并刻上標號以便日后型修拆裝.(注意:零件的
防呆方向)
2.脫板的裝配.(注意:導正釘及相關入塊的挂台是否与模面水平;不可高於模面.脫背板的逃孔
是否偏位或過小.)最后刻上標號,固定脫料板.
3.將裝好的下模板,脫板与只裝有導柱的夾板合并,達到順暢滑動,閉死.
插入上夾板上的沖頭,使每根沖頭都能滑動,(注意:不能有間隙過大晃動.)最后,使裝有零件的夾板,脫板,下模板都能順暢滑動.
(三)..固定應為一体的零件
1.下模板的固定:
1).用油石,淨布推平驅除表面的鐵屑髒物;
2).按基准順序先放下墊板,再放下模板,固定在下模座上.(注意:先裝螺絲不要固死,帶上即
可.再固定銷釘.銷釘固定後在鎖上螺絲)
2.上模的固定
1).先用壓板把夾板上的沖頭固定在夾板上(注意:不要固死,帶上即可.等上模板和上模座固
定好再鎖衝頭壓版)
2).把固定好的脫板与固定好的夾板合并,達到順滑.
3).用等高套將脫板与夾板對角連接,以便合模搬動時不會脫開,确保安全.
4).將上模連接好的夾板,脫料板与下模板合并達到順滑閉死狀態.
5).清洁好上墊板,上模座按基准順序固定上模(注意:螺絲要對角固定,不要一下固定死,要一
邊滑動上模与下模一邊固定,直到固死,保証上模与下模能順暢滑動.)
6).打開上模將夾板上的沖頭固死,然后用等高套連接脫板,裝入上下模的所有彈簧.
7).安裝誤送裝置開關.
八.最后點檢
總栓時﹐确認模具的限位柱﹐上下模彈簧﹐傳力梢﹐鎖模螺絲﹐全部裝好﹒刀口落料口位置是否對正﹐無誤后方可架模﹒。