驱动桥5000字外文翻译文献
驱动桥汽车外文文献翻译、中英文翻译、外文翻译

Driving Axleautomobile driving axleThe driving axle is one of cross bars supporting a vehicle, on which the driving wheels turn .The driving axle includes a housing ,an axle drive ,a differential , tow axle shafts (half axles ),and final drives (if any ) .The axle .or main, drive is a drive-line unit that increases the torque delivered by the transmission and transmits it to the driving wheels, via the differential. In automobiles, the axle drive shaft, usually called the propeller shaft.The axle drive may be a Single or a double-stage type, the former comprising a pair of gears and the latter .tow pairs of gear. Drive pinion I may be made integral with its shaft, or it may be detachable from the shaft. Driving gears and are usually made in the form of detachable gear rings that are bolted or riveted to the differential case .Alex drive bevel pinions and gears are made with helical teeth in order to reduce noise in operation.The tow-stage axle drive consists of a pair of bevel gears and a pair of spur gears. Drive bevel pinion drives bevel gear that is fixed to the flange of the intermediate shaft made integral with 2nd–stage driving spur gear .Gears meshes with driven spur gear which is fastened to the case rotates in taper roller bearings installed in the differential carrier that makes part of the driving axle housing.The differential is a drive-line unit that divides the torque applied to it between the tow axle shafts and allows one driving wheel to turn at a different speed from the other.The differential consists of case, cross or spider pinion .and side gears, also known as axle gears .the differential pinions are freely mounted on the cylindrical arms of the spider, which is held in the differential case, and remain in constant mesh with the differential side gears.When the automobile is moving down a straight and even road, both driving wheels meet with one and the same rolling resistance. In this case, axle driven gear, or differential ring gear, causes the differential case to rotate .when the differential case rotates pinions and their spider arms move around in a circle with tow differential side gears are meshed with the pinions, the side gears must rotate, causing the axle shafts and their associated driving wheels to turn. With equal resistance applied to each wheel, the differential pinions do not rotate. They apply equal torque to the side gears and therefore both driving wheels rotate at one and the same speed is unequal ,the differential pinions rotate on their spider arms as well as drive round with the differential case .supposing that one of the axle shaft is prevented from rotating ,the differential pinions would have to walk around the stationary side gear ,causing the other side gear to rotate at twice its normal speed .You can now see how the differential can allow one driving wheel to turn faster than the other .Whenever the automobile goes around a turn ,the outer driving wheel travels a greater distance than the inner drive wheel .the inner wheel speeds up proportionately ,thanks to the differential pinions that rotate on their spider arms and ,rolling around the slower side gear send more rotary motion to the outside wheel.The differential side gears are splined on to the inner ends of the axle shafts .The other ends of the shafts are attached to the driving wheel hubs by means of flanges .Trucks use full floating axle shafts .Such axle shafts are acted upon by torque only .All the other loads acting on the driving wheels are taken by the driving axle housing, because the wheel hubs are supported by bearings mounted on the housing.Driving axle of general-purpose wheeled tractorGeneral-purpose wheeled tractors are a four-wheel drive type, they have tow driving axles-front and rear .Both axles are similar in construction, expect for the housing. Each driving axle consist if a housing, an axle drive ,a differential ,and final drives .The front and rear-axles drives are interchangeable and comprise a pair of spiral bevel gears . The axle drive pinion is made integral with a shaft that issupported by tow taper roller bearings installed in axle drive pinion carrier .The latter is accommodated in differential carrier and is fixed to it by bolts. The flange of the axle drive pinion carrier is provided with threaded holes to fit puller screws that are used to remove the axle drive pinion carrier from the differential carrier .The position of the drive pinion relative to the centerline of the axle is adjust by means of a pack of shims placed under the flange of the drive pinion carrier Shims palace under the cone of the front bearing are used to adjust the preload on the drive pinion bearings. Splined to adjust the preload on the drive pinion shaft is universal-joint flange .The axle drive gear is bolted to the differential case flange.THE DIFFERENTIAL consists of case, four pinions, and tow side gears .The differential case comprise tow halves that are bolted together and supported by taper roller bearings installed in the differential carrier .Screwed in the bearings housing from the outside are nuts used to adjust the backlash between the ring gear and drive pinion teeth and the side bearing preload.Welded to the top of the driving axle housing at both its ends are spring pads .The housing of both its ends are spring axels are provided with filler ,overflow ,and drain holes closed by plugs .Both housing also have vents ,The rotating components of the driving axles are lubricated with transmission oil .As distinct from the automobiles considered in this text, all tractors include final drives in their power trains .The final drives of general-purpose wheel tractors are referred to as wheel-hub reduction gears.While transmitting power to the driving wheels, wheel-hub reduction can increase their torque .These are planetary reduction gear sets consist of sun gear ,or wheel ,three planet ,or pinion ,gears ,planet or pinion ,carrier .stationary internal ,or ring ,gear ,and housing.The sun gear is splined to the outer end of the axle shaft is splined to the differential side gear .The cylindrical planet gears are in constant mesh with both the sun gear and the ring gear and are free to rotate on roller bearings mounted on shafts that are attached to the planet carrier .The planet carrier is fasted to the reduction gear housing by means of studs and nuts .The flange of housing ,driving wheel brake drum13,and wheel hub are clamped together by bolts .The planet carrier and reduction gear housing form the driven part of the planetary gear set and rotate with the driving wheel of the tractor .The driving gear hub is supported by taper roller bearings mounted on axle shaft housing ,or axle sleeve .The axle sleeve is connected to the stationary ring gear by means of adapter hub that has internal splines and external teeth . The splines are meshed with matching splines on the axle sleeve, and the teeth are meshed with internal teeth ring gear.Wheels and its maintainModern wheeled tractors and automobiles use pneumatic-tired disc wheels. As a result of the driving wheel tires gripping the road, the rotary motion of the wheels is transformed into the translational motion of the tractor or automobile.According to their purpose, wheels are classified as driving .driven steerable, and combination types.Trucks and general-purpose wheeled tractors have all their wheels of one and the same size .Row-crop tractors have their rear wheels larger than the front wheels .The rear wheels carry the major proportion of the load due to the weight of the tractor .The front wheels are loaded lighter and this makes them easier to turn and provide good directional steering stability, which is essential for row-crop work.A TRUCK WHEEL consists of disc and flat base rim that is made integral with it, while the other flange is formed by detachable side ring that is held to the rim by split lock ring on the rim .which doubles as a side ring and a lock ring.The wheel disc is provided with holes for mounting the wheel on the wheel mounting bolts ,or wheel studs ,on the wheel hub ,where it is fixed by nuts .Both the holes and the nuts are tapered to ensure exact location of the wheel on its hub .The rear driving axles of trucks carry tow wheels at each end .The inner wheels are held to the hubs by cap nuts that are threaded both on the inside and on the outside .and the outer wheels are mounted on the cap nuts and fixed in place by taper nuts screwed on the nuts .The wheel nuts on the right side of truck have right-hand threads, whereas the nuts on the left side of the truck are threaded left-hand .The reason is to tighten the nuts, not loosen them, and thus prevent them from working loose on acceleration andbraking.An automobile pneumatic tire consists of casing, inner tube, and flap .The tire casing comprises tread, side walls, and beads .Tires for good roads use small tread patterns, while those for bad roads or cross –country service large tread patterns.The inner tube is made in the form of a hollow elastic rubber doughnut that is inflated with air after it is installed inside the tire and the tire is put on the wheel rim .The inner tube is inflated through tire valve that consists of housing 11,valve inside ,and cap .The valve housing is made of brass in the dorm of a flanged tube that is mounted in the inner tube by means of a washer and a nut and sticks out through a hole in the wheel .Some tire valve housing are of comprise construction :the upper part is made of brass and the lower part ,of rubber that is vulcanized on to the inner tube .The valve inside is a check valve that opens to let air in the inner tube when an air closed ,spring pressure and air pressure inside the tube hold the valve .When the valve is closed ,spring pressure and air pressure inside the tube hold the valve in its seat .It includes core with a rubber ring ,a plunger pin ,and a spring .The valve inside is Screwed in the tire valve housing and is closed by the cap Screwed on the housing.To the construction of the driving and steerable wheels, each wheel comprises hub , disc with rim ,and tire with inner tube .The rim is welded to the disc and the disc is bolted to the hub .The driving wheel tires are of low-pressure type and have heavy tread bars for better traction.The driving wheel hub is keyed to axle shaft and is fixed in place by means of bolted-on insert with worm whose threads mesh with the rack teeth cut in the half axle .By turning the worm one can change the position of the wheel on the axle shaft to obtain the desired track width .Before doing this ,it is necessary to jack up the rear part of the tractor to clear the wheels of the ground and loosen the bolts that hold the inserts to the wheels hubs .Should this adjustment prove insufficient ,the track width can further be increased by placing the wheels with the concaves of their discs facing inwards.On some row-crop tractors ,the rear wheel discs are bolts to lugs welded on the wheel rims .In this case ,the crack width can be changed by bolts the discs in alternative positions to the lugs .Also the concave wheel discs may be used either with the concave facing inwards or outwards.Trouble-free operation of automobiles and wheeled tractors largely depends on the condition of the tires. Therefore, during operation, one should adhere to following rules.Prevent fuel and, or oil from getting onto the tires. Cleans the tires regularly from dirt and remove all foreign articles, such as stones, form the treads. Do not apply brakes sharply, never start away form rest with a jerk, and avoid making sharp turns, for all this causes uneven wear of the tires. Do not allow excessive slipping of the driving wheels. When preparing your tractor or automobile for a long-term storage, jack up the wheels and put trestles under the axles or frame to relieve the tires.The service life of tires is expressed in terms of their mileage. For most bias (ordinary) truck tires, the guaranteed mileage amounts to 50000 km. Observing the above rules will help prolong the useful service life of tires.驱动桥汽车的驱动桥驱动桥是一个支撑车辆的十字交叉的轴,它可以驱动车轮运动。
自动变速器与驱动桥概述 英文文献加中文翻译
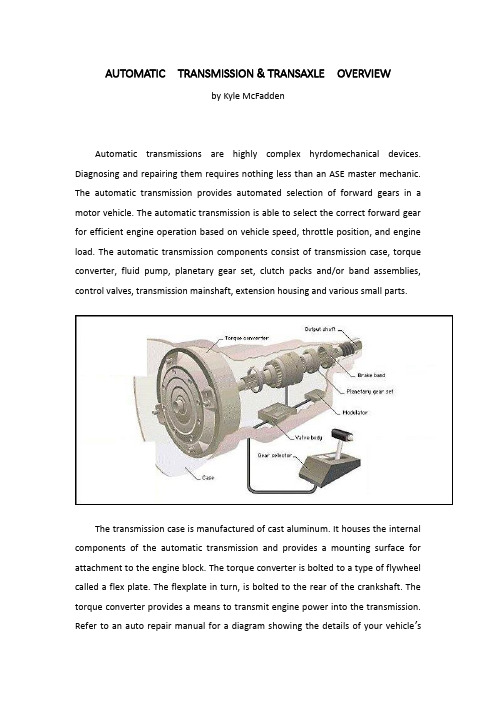
AUTOMATIC TRANSMISSION & TRANSAXLEOVERVIEWby Kyle McFaddenAutomatic transmissions are highly complex hyrdomechanical devices. Diagnosing and repairing them requires nothing less than an ASE master mechanic. The automatic transmission provides automated selection of forward gears in a motor vehicle. The automatic transmission is able to select the correct forward gear for efficient engine operation based on vehicle speed, throttle position, and engine load. The automatic transmission components consist of transmission case, torque converter, fluid pump, planetary gear set, clutch packs and/or band assemblies, control valves, transmission mainshaft, extension housing and various small parts.The transmission case is manufactured of cast aluminum. It houses the internal components of the automatic transmission and provides a mounting surface for attachment to the engine block. The torque converter is bolted to a type of flywheel called a flex plate. The flexplate in turn, is bolted to the rear of the crankshaft. The torque converter provides a means to transmit engine power into the transmission.Refer to an auto repair manual for a diagram showing the details of your vehicle’s torque converter assembly.The torque converter is a doughnut shaped device that is filled with fluid. When the engine is running, the torque converter spins, rotating and pressurizing the fluid using internally mounted blades. The spinning fluid rotates a turbine that is connected to the transmission mainshaft. A separate internal set of blades called a stator helps to direct the fluid into the turbine. The operation of the torque converter can be compared to a powered air fan spinning a non powered air fan. The powered fan will generate moving air, directed at the non powered fan blade, causing it to rotate. The powered fan becomes the driving member, while the non powered fan becomes the driven member. If the air is moving slow enough, very little torque is transmitted from the driving member to the driven member. If you wanted, you could easily stop the rotating fan blade of the non powered fan. However, if the powered fan were to operate at high speed, the non powered fan would be rotating at a much higher speed, making it more difficult to stop. This is the same principal that allows an automatic transmission equipped vehicle to idle in gearand drive down the road without using a mechanical clutch. At idle speed, fluid pressure is low, transmitting very little engine torque through the transmission. When the engine speed is raised, fluid speed and pressure increases, allowing more engine torque to be directed to the transmission. Most torque converters contain an internal locking clutch that is applied at cruise speed. This clutch, called a torque converter clutch, eliminates the slippage that occurs with a torque converter. The torque converter clutch is used as a fuel saving device, and to reduce the amount of heat generated in the transmission. When troubleshooting poor MPG issues, one culprit is a faulty torque converter, though poor MPG would also be present with shifting issues if the torque converter is the cause.Forward speeds and reverse are provided by a gear set called the planetary gears. The planetary gear set consists of a central gear, called the sun gear, placed inside a large gear called an internal gear. Rotating between the internal gear and the sun gear, are small gears, held in a carrier, known as planetary gears. Different gear ratios are made possible by holding one component of the planetary gear set and allowing the other to rotate. For example, if the sun gear were held, the internal gear would be rotated by the planetary gears revolving around the motionless sun gear. This would cause the internal gear to rotate at low speed, while the planetary gears move much faster. This would provide a low gear function for the transmission, since the slow moving internal gear would be used to transmit power to the driving wheels.An internal transmission oil pump is driven by the rotation of the torque converter. The oil pump pressurizes and circulates the transmission fluid used for the operation and lubrication of the transmission. The pressure created by the pump is often referred to as line pressure. Line pressure is utilized by the transmission to signal shift points and operate various transmission components.Bands and clutches are used to hold the components of the planetary gear set to in order to provide different forward gear ratios or reverse. They are operated by line pressure that is directed to a specific band or clutch pack by the transmission shift control valves. The shift control valves operate by responding to changes in linepressure based upon the operation of input devices that signal road speed, throttle position, and engine load. Correcting shifting issues may not involve a costly auto repair job; it may be as simply as adjusting the bands.The input devices used for transmission shift control are the governor, throttle valve, and vacuum modulator. The governor provides road speed information to the transmission to control shift points. It works by increasing line pressure as road speed increases. The throttle valve is connected by linkage to the throttle of the engine. The throttle valve modifies line pressure based on throttle position. This information is needed to vary shift points in response to driving conditions. When the throttle is moved to wide open, the throttle valve will cause send a line pressure signal to the control valves to delay shifting until higher road speed. The vacuum modulator changes shift feel in response to engine load. Since engine intake manifold vacuum changes in response to engine load, manifold vacuum is used as an input signal to the transmission. The vacuum modulator receives vacuum signal from the engine. The vacuum modulator will increase line pressure to stiffen transmission shifting based during heavy engine loads. The increased line pressure will cause clutches and bands to hold tighter and help to diminish slipping.Most vehicles today are equipped with automatic transmissions that use electronic shift controls. The operation of the electronically controlled transmission is similar in principle to the non electric transmission. However, the electronically shifted transmission uses input signals from the vehicle control module to control shift points, rather than a governor and throttle valve. The vehicle control module controls transmission shifting based on engine and transmission data sensors. The throttle position sensor is used in place of the mechanical throttle valve. The vehicle speed sensor is used to replace the governor. Engine load sensors, such as a manifold pressure sensor, are used to control shift feel. A vacuum modulator may still be used by some vehicle makes to assist in shift control. The vehicle control module will utilize this information to operate various shift control solenoids inside the transmission. These shift control solenoids in turn control line pressure to theirrespective shift control valves that in turn apply or release pressure to bands or clutches.The result of using electronic shift controls is an automatic transmission that operates more efficiently to tailor shifting to meet engine demands. Fuel economy and vehicle emission control are enhanced by more precise control of the automatic transmission. Vehicle control modules have the ability to adapt transmission shifting to meet the individual driving patterns of the vehicle. Also internal overheat protection is provided for by the control module’s ability to monitor transmission fluid temperature and change transmission shifting and operation to minimize temperature related damage. On many vehicles, the EEC (Electronic Engine Control) will “learn” a particular driver’s driving style. This information is stored in the EEC’s memory. If the battery is disconnected (during replacement, for example), the vehicle may shift erratically for a short time until the EEC re-learns the driver’s driving style and then reprograms itself. This is important to remember and a little patience can save you a trip to the auto repair shop, ie. after your battery is replaced, drive your vehicle for a day or so and see if the erratic shifting issue is resolved (most likely it will correct itself).The automatic transaxle is an automatic transmission that also contains the final drive for delivering power to the driving wheels. Operation is comparable to the operation of the conventional automatic transmission. With the exception of a differential and axle shafts located in the lower portion of the transaxle. The automatic transaxle is used almost exclusively in front wheel drive vehicles..自动变速器与驱动桥概述自动变速器是高度复杂的精密设备。
驱动桥汽车外文文献翻译、中英文翻译、外文翻译
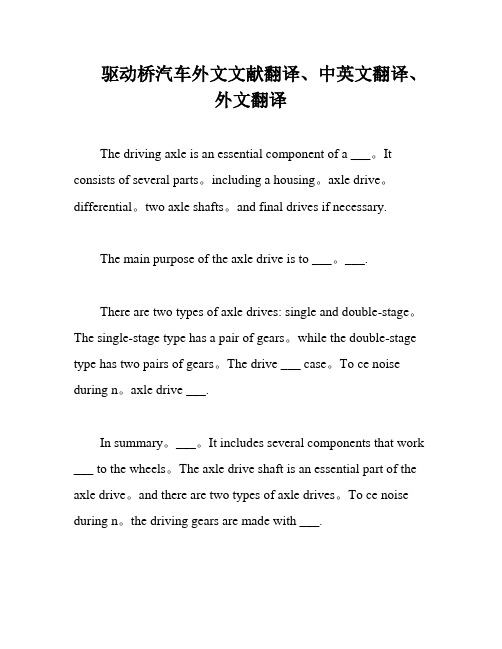
驱动桥汽车外文文献翻译、中英文翻译、外文翻译The driving axle is an essential component of a ___。
It consists of several parts。
including a housing。
axle drive。
differential。
two axle shafts。
and final drives if necessary.The main purpose of the axle drive is to ___。
___.There are two types of axle drives: single and double-stage。
The single-stage type has a pair of gears。
while the double-stage type has two pairs of gears。
The drive ___ case。
To ce noise during n。
axle drive ___.In summary。
___。
It includes several components that work ___ to the wheels。
The axle drive shaft is an essential part of the axle drive。
and there are two types of axle drives。
To ce noise during n。
the driving gears are made with ___.When a car turns。
___ a greater distance than the inner ___。
thanks to the differential ns ___ around the slower side gear。
the inner ___。
中英文文献翻译-驱动桥介绍
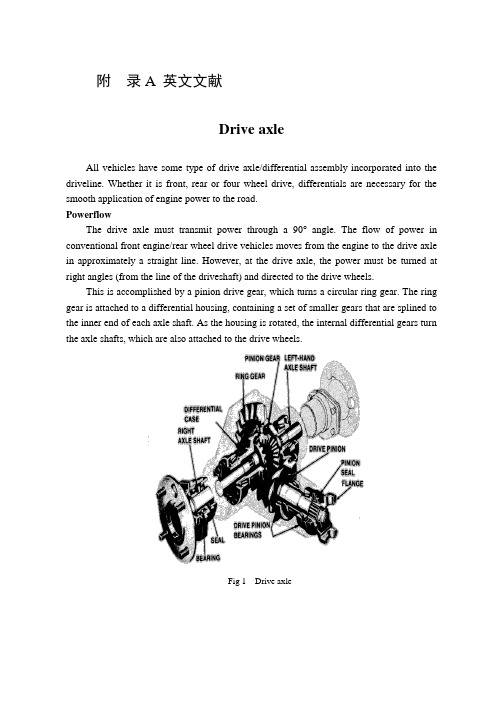
附录A 英文文献Drive axleAll vehicles have some type of drive axle/differential assembly incorporated into the driveline. Whether it is front, rear or four wheel drive, differentials are necessary for the smooth application of engine power to the road.PowerflowThe drive axle must transmit power through a 90°angle. The flow of power in conventional front engine/rear wheel drive vehicles moves from the engine to the drive axle in approximately a straight line. However, at the drive axle, the power must be turned at right angles (from the line of the driveshaft) and directed to the drive wheels.This is accomplished by a pinion drive gear,which turns a circular ring gear. The ring gear is attached to a differential housing, containing a set of smaller gears that are splined to the inner end of each axle shaft. As the housing is rotated, the internal differential gears turn the axle shafts, which are also attached to the drive wheels.Fig 1 Drive axleRear-wheel driveRear-wheel-drive vehicles are mostly trucks, very large sedans and many sports car and coupe models. The typical rear wheel drive vehicle uses a front mounted engine and transmission assemblies with a driveshaft coupling the transmission to the rear drive axle. Drive in through the layout of the bridge, the bridge drive shaft arranged vertically in the same vertical plane, and not the drive axle shaft, respectively, in their own sub-actuator with a direct connection, but the actuator is located at the front or the back of the adjacent shaft of the two bridges is arranged in series. Vehicle before and after the two ends of the driving force of the drive axle, is the sub-actuator and the transmission through the middle of the bridge. The advantage is not only a reduction of the number of drive shaft, and raise the driving axle of the common parts of each other, and to simplify the structure, reduces the volume and quality.Some vehicles do not follow this typical example. Such as the older Porsche or Volkswagen vehicles which were rear engine, rear drive. These vehicles use a rear mounted transaxle with halfshafts connected to the drive wheels. Also, some vehicles were produced with a front engine, rear transaxle setup with a driveshaft connecting the engine to the transaxle, and halfshafts linking the transaxle to the drive wheels.Differential operationIn order to remove the wheel around in the kinematics due to the lack of co-ordination about the wheel diameter arising from a different or the same rolling radius of wheel travel required, inter-wheel motor vehicles are equipped with about differential, the latter to ensure that the car driver Bridge on both sides of the wheel when in range with a trip to the characteristics of rotating at different speeds to meet the requirements of the vehicle kinematics.The accompanying illustration has been provided to help understand how this occurs.1.The drive pinion, which is turned by the driveshaft, turns the ring gear.2.The ring gear, which is attached to the differential case, turns the case.3.The pinion shaft, located in a bore in the differential case, is at right angles to the axle shafts and turns with the case.4.The differential pinion (drive) gears are mounted on the pinion shaft and rotate with the shaft .5.Differential side gears (driven gears) are meshed with the pinion gears and turn with the differential housing and ring gear as a unit.6.The side gears are splined to the inner ends of the axle shafts and rotate the shafts as the housing turns.7.When both wheels have equal traction, the pinion gears do not rotate on the pinion shaft, since the input force of the pinion gears is divided equally between the two side gears.8.When it is necessary to turn a corner, the differential gearing becomes effective and allows the axle shafts to rotate at different speeds .Open-wheel differential on each general use the same amount of torque. To determine the size of the wheel torque to bear two factors: equipment and friction. In dry conditions, when a lot of friction, the wheel bearing torque by engine size and gear restrictions are hours in the friction (such as driving on ice), is restricted to a maximum torque, so that vehicles will not spin round. So even if the car can produce more torque, but also need to have sufficient traction to transfer torque to the ground. If you increase the throttle after the wheels slip, it will only make the wheels spin faster.Limited-slip and locking differential operationFig 5 Limited-slip differentialDifferential settlement of a car in the uneven road surface and steering wheel-driven speed at about the different requirements; but is followed by the existence of differential in the side car wheel skid can not be effective when the power transmission, that is, the wheel slip can not produce the driving force, rather than spin the wheel and does not have enough torque. Good non-slip differential settlement of the car wheels skid on the side of the power transmission when the issue, that is, locking differential, so that no longer serve a useful differential right and left sides of the wheel can be the same torque.Limited-slip and locking differential operation can be divided into two major categories:(1) mandatory locking type in ordinary differential locking enforcement agencies to increase, when the side of the wheel skid occurs, the driver can be electric, pneumatic or mechanical means to manipulate the locking body meshing sets of DIP Shell will be with the axle differential lock into one, thus the temporary loss of differential role. Relatively simple structure in this way, but it must be operated by the driver, and good roads to stop locking and restore the role of differential.(2) self-locking differential installed in the oil viscosity or friction clutch coupling, when the side of the wheel skid occurs when both sides of the axle speed difference there, coupling or clutch friction resistance on the automatic, to make certain the other side of the wheel drive torque and the car continued to travel. When there is no speed difference on both sides of the wheel, the frictional resistance disappeared, the role of automatic restoration of differentials. More complicated structure in this way, but do not require drivers to operate. Has been increasingly applied in the car. About non-slip differential, not only used for the differential between the wheels, but also for all-wheel drive vehicle inter-axle differential/.Gear ratioThe drive axle of a vehicle is said to have a certain axle ratio. This number (usually a whole number and a decimal fraction) is actually a comparison of the number of gear teeth on the ring gear and the pinion gear. For example, a 4.11 rear means that theoretically, there are 4.11 teeth on the ring gear for each tooth on the pinion gear or, put another way, the driveshaft must turn 4.11 times to turn the wheels once. The role of the final drive is to reduce the speed from the drive shaft, thereby increasing the torque. Lord of the reduction ratio reducer, a driving force for car performance and fuel economy have a greater impact. In general, the more reduction ratio the greater the acceleration and climbing ability, and relatively poor fuel economy. However, if it is too large, it can not play the full power of the engine to achieve the proper speed. The main reduction ratio is more Smaller ,the speed is higher, fuel economy is better, but the acceleration and climbing ability will be poor.附录B 文献翻译驱动桥所有的汽车都装有不同类型的驱动桥和差速器来驱动汽车行驶。
汽车驱动桥设计外文文献翻译、中英文翻译、外文翻译

AppendixChina in the first half of 2008 about 93 million trucks accumulative total sales of cars, vans 61 million vehicles, year-on-year growth of 20.2%, visible light car in commercial car production has a large proportion. And driving axle is very important in the vehicle driving axle is the important car auto bearing assembly, auto frame and integral by suspension of body vertical force, to lead the longitudinal forces, transverse force and torque, and impact load; Driving axle also delivers the transmission, the maximum torque reaction is under.Automobile driving axle structure and design parameters in addition to the reliability of the automobile and durability have important influence on the outside, also for the automobile driving performance such as power, economy, smooth, through sex, mobility Automobile driving axle design involves the mechanical parts and components is widely to these varieties, spare parts, components and assemblies manufacturing also almost want to design to all modern machinery manufacturing process, design a simple structure, reliable operation and low cost, can greatly reduce the drive axle of the total cost of the vehicle production, promote economic development, and car to drive through the car studying and designing practice, can better learning and mastery of the modern car design and mechanical design of the comprehensive knowledge and skills, and the overall thinking and operation skill check, drawing, is the very important link, so ontology of a structure design of fine vans axles has certain Automobile driving axle is one of the main parts car, its basic function is to enlarge the shaft or by the torque transmission spread, then torque distribution to drive wheels, and make about driving wheel has about vehicle movement required differential function; Axles in the end of powertrain system, choose proper Lord slowdown, ensure cars than with sufficient ground clearance is achieved, gear and other transmission job need to ensure smooth are the parameters, and even bear effect on the pavement drive axle and frame or carrying body vertical force, the lead between transverse and longitudinal force and torque force. Driving axle quality, performance will have a direct impact on the vehicle's safety, economy, comfort and reliability. After the car driving axle design can make the students' comprehensive by using their This thesis research aims to overall matching car by driving axle Lord finish design of gear reducer, differential component such as type of design and calculation, and complete checking and comprehensive design single main reducer, then the batch Through the design of the vehicle driving axle should also master the understanding, including each component interaction between the body and the electricalsystem, the influence and cooperate to drive axle of the process and therefore more familiar with vehicle mastery. That in the future the production and living effectly use.附录我国2008年上半年货车累计销售约93万辆,其中轻型货车61万辆,同比增长20.2%,可见轻型汽车在商用汽车生产中占有很大的比重。
中英文文献翻译-驱动桥
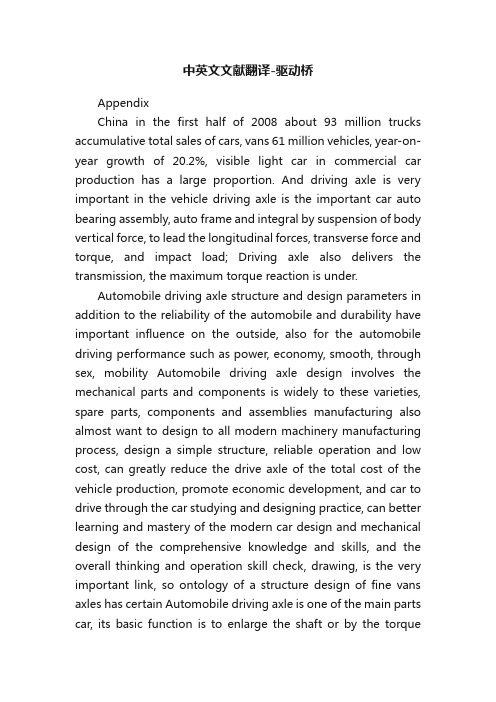
中英文文献翻译-驱动桥AppendixChina in the first half of 2008 about 93 million trucks accumulative total sales of cars, vans 61 million vehicles, year-on-year growth of 20.2%, visible light car in commercial car production has a large proportion. And driving axle is very important in the vehicle driving axle is the important car auto bearing assembly, auto frame and integral by suspension of body vertical force, to lead the longitudinal forces, transverse force and torque, and impact load; Driving axle also delivers the transmission, the maximum torque reaction is under.Automobile driving axle structure and design parameters in addition to the reliability of the automobile and durability have important influence on the outside, also for the automobile driving performance such as power, economy, smooth, through sex, mobility Automobile driving axle design involves the mechanical parts and components is widely to these varieties, spare parts, components and assemblies manufacturing also almost want to design to all modern machinery manufacturing process, design a simple structure, reliable operation and low cost, can greatly reduce the drive axle of the total cost of the vehicle production, promote economic development, and car to drive through the car studying and designing practice, can better learning and mastery of the modern car design and mechanical design of the comprehensive knowledge and skills, and the overall thinking and operation skill check, drawing, is the very important link, so ontology of a structure design of fine vans axles has certain Automobile driving axle is one of the main parts car, its basic function is to enlarge the shaft or by the torquetransmission spread, then torque distribution to drive wheels, and make about driving wheel has about vehicle movement required differential function; Axles in the end of powertrain system, choose proper Lord slowdown, ensure cars than with sufficient ground clearance is achieved, gear and other transmission job need to ensure smooth are the parameters, and even bear effect on the pavement drive axle and frame or carrying body vertical force, the lead between transverse and longitudinal force and torque force. Driving axle quality, performance will have a direct impact on the vehicle's safety, economy, comfort and reliability. After the car driving axle design can make the students' comprehensive by using their This thesis research aims to overall matching car by driving axle Lord finish design of gear reducer, differential component such as type of design and calculation, and complete checking and comprehensive design single main reducer, then the batch Through the design of the vehicle driving axle should also master the understanding, including each component interaction between the body and the electricalsystem, the influence and cooperate to drive axle of the process and therefore more familiar with vehicle mastery. That in the future the production and living effectly use.附录我国2008年上半年货车累计销售约93万辆,其中轻型货车61万辆,同比增长20.2%,可见轻型汽车在商用汽车生产中占有很大的比重。
汽车车辆专业前桥外文文献翻译中英文翻译外文翻译
外文文献(一)外文原文Front axle general is in the front of the bus, also known as steering axle or drive bridge. Automobile front axle is the last important assemblies, including the steering knuckle kingpin, steering, front beam and other components. Front axle through the suspension and frame, used to support the ground and the frame between the vertical load, but also bear the braking force and lateral force and the force of torque, and ensure that the steering rotation right movement. The axle is connected with the frame through the suspension, support most of the weight of vehicle, and wheel traction or braking force, as well as the lateral force after suspension to frame. In the car used in the steering bridge, the stress condition is more complex, so it should have enough strength. In order to ensure the wheel turns to the correct positioning of angle, make manipulation of light and reduce tire wear, steering bridge should have enough stiffness. In addition, should also try to reduce the weight of the bridge. In short, because of the automobile in the running process of the front axle, the abominable working environment, complicated working condition, the load is alternating load, thus the parts easy to fatigue cracking and even rupture phenomenon. This requires that the structural design must have enough strength, stiffness and resistance to fatigue failure of the ability.The front axle is the main load-bearing parts: the front axle, my company has a tubular and forging type two structural forms, but mainly to forging type mainly. The front ends of each with a fist shape bold part as the kingpin of the site installation. In both sides of the spring support for partial surface, used for the installation of steel plate spring and accessories. Need note here is: U type bolt passes through the front mounting holes need matter beneath the back nut in, often can appear with the front axle sleeve back band interference problem. Why can appear such problem? Design is a problem, because the front dorsal ribs affects front axle load, therefore must have a certain size requirements, and if both before and after the U bolt distance design is too small, not enough gap assembly will appear above problem. Two technical problems, technical problems in two cases. The first is the front dorsal rib symmetry is not good or mounting hole symmetrical degree andeasy to cause the problem; the second is that some host plant in order to avoid the vulnerable, without taking into account the reality of the product and blind to the sleeve outer diameter. Kingpin: is the impact of vehicle performance of main parts. Kingpin has stop groove, pin lock bolt through the stop groove masterPin fixed on the front axle kingpin bore, so that it can't move can not move axially. Knuckle pin machining accuracy is very high, my company is one of the parts of key control. Steering knuckle: steering knuckle is the main steering part of front axle. It uses the main pin and the front axle is hinged by a pair of axle bearing supporting hub combination, to achieve the function of turning. Brake assembly: is the realization of the wheel brake main component, a brake oil and gas brake two forms. Implemented in the vehicle brake command, brake friction plate through the expansion and brake drum machining surface contact friction realization of vehicle brake. Front axle brake option is very critical, if the choice is undeserved, can appear before and after the brake force is not a match, the braking force is not up to the requirements of many problems. Hub combination : by two rolling bearings mounted on the steering knuckle, drive the rotation of the wheels. At the same time with the friction plate to form a friction pair, to realize the brake wheel. Arm: straight rod arm, tie rod arm, respectively, and a straight rod assembly and the tie rod assembly. Formed a steering mechanism and a steering trapezoidal mechanism. The steering mechanism to complete the vehicle steering, steering trapezoid determines the vehicle inside and outside corner is reasonable. The tie rod assembly: is to adjust the beam before the main parts. The rod body is made of seamless steel tube manufacturing, both ends of the spherical hinge joint structure is the joint assembly, by a thread after the installation of the tie rod arm, the rod body is adjustable, so as to adjust the toe. Front axle under the front of the car weight, the car forward thrust from the frame to the wheel, and with the steering device arranged on parts make joint type connection, the implementation of the automobile steering. The front axle is the use of both ends of it through the main pin and the steering knuckle is connected to the steering knuckle, swing to realize vehicle direction.In order to make the running vehicle has good linear driving ability, front axle should meet the following requirements: in order to make the running vehicle has good linear driving ability, front axle should meet the following requirements:1sufficient strength,in order to ensure the reliable bearing wheel and frame ( or monocoque ) between the work force. 2 correct positioning of the wheels, so that the steering wheel movement stability, convenient operation and reduce tire wear. Front wheel positioning includes kingpin inclination, caster, camber and toe-in. 3sufficient rigidity, the force deformation small, ensure the main pin and a steering wheel positioned right angle remains constant. 4knuckle and master pin, steering and front axle between the friction should be as small as possible, to ensure that the steering operation for portability, and has sufficient abrasion resistance. 5 steering wheel shimmy should be as small as possible, in order to ensure the vehicle normal, stable exercise. 6 front axle quality should be as small as possible, in order to reduce unsprung mass, improve vehicle ride comfort.1mini car front axle 1mini car front mini car front suspension generally adopt the independent suspension structure. Front axle load is relatively small, the structure is simple. Mini car front axle usually disconnected movable joint structure, which is composed of a front axle body, strengthen the transverse swing arm, arm etc.. 2 car front axle2 car front axle front axle suspension with Mcpherson car. It bears the driving and steering functions, the suspension is connected with the vehicle body, and the lower end of the wheel bearing housing connected, wheel camber is through the suspension and the bearing shell of the connecting bolt to adjust, auxiliary frame through the elastic part by controlling the arm, ball hinge connected with suspension, improve the driving stability and ride comfort. 3off-road vehicle front axle3off-road vehicle front axle Off-road vehicle steering and driving front axle has two tasks, it is known as the steering driving axle. And it generally drive the movable bridge, with a main driver, differential and the axle shaft. The difference is, due to the need, half shaft is divided into two segments, and by a universal joint, while the main pin are made under paragraph two. The 4truck front axle 4truck front axle truck front axle with I-shaped cross section is mainly used to improve the front bending strength. The upper two plus wide plane, to support the steel plate spring. The front ends each having a fist shape portion, which has a through hole, as a kingpin only. Main pin and left steering knuckle hinge, with a threaded wedge pin crossed with the main pin hole of vertical through holes on the lock pin wedge surface, the main pin is fixed in the axle hole, so that it cannot rotate.In general, common material needed to define the material properties including: elastic modulus, Poisson's ratio, density, specific heat, thermal expansion coefficient. The front axle is mainly composed of two parts, material composition, i.e., front axle and steering knuckle such as zero Department of materials. The front axle is adopted as the material of45 steel, steering knuckle materials using 40Cr.Torsion bar of automobile front independent suspension is the key component, is a slender rod, the induction quenching process is the manufacturing process difficult point, this paper introduces the torsion bar quenching inductor and its process test results, determined using half ring type inductor continuous quenching technology, this method can meet the technical requirements and the quantities of torsion bar production.The forging forging molding, not only greater deformation, but also requires a certain deformation force,Therefore the selection of J53series double disc friction press comparative economics, this series press combined slipping flywheel, combined slipping flywheel can provide highly deformed large forgings with enough to form, and can provide for forgings will required deformation capacity, and not to overload, the series press equipment investment, the cost of the mold and forging cost than die forging hammer and the forging crank press cheap cheap host. At present, the domestic automobile front axle machining process are the following: (1) of two plane milling plate spring seat; the drill two spring seat plane ten holes; the rough milling of two main pin hole of upper and lower end surfaces; the fine mill main pin hole of upper and lower end surfaces; the drilling and reaming main pin hole; the broaching the main pin hole; the main pin hole on the lower end of the countersink reaming pin holes;. In this scheme, the following questionQuestions:1 adopting main pin hole positioning countersink on the lower end, and the end surface of the main pin hole verticality can not be guaranteed, the main pin hole size height can not be guaranteed to the main pin hole; the positioning of the drill pin hole, drill through the cross intersection holes, easy cutting phenomenon, students offset, causing the main pin hole and the locking pin hole center distance can not be guaranteed. (2) of two plane milling plate spring seat; the drill two spring seat plane ten holes; the drilling and reaming pin holes on the rough milling of a main pin hole on upper end; the fine mill main pin hole of upperand lower end surfaces; the drilling and reaming main pin hole. In this scheme, there are the following problems: the process is used to drill the locking pin hole after the drill main pin hole, and the pin - fL: fL size and position size is the key size, kingpin is difficult to ensure the accuracy of the first; fine mill main pin hole of the upper and lower ends after processing the main pin hole, end relative to the main pin hole verticality is difficult to guarantee. (3) of two plane milling plate spring seat; the drill two spring seat plane ten holes; the drilling and reaming pin holes; the rough milling kingpin on upper end; the drilling and reaming main pin hole; the fine mill main pin hole on the lower end surface. In this scheme, there are the following problems : the main pin hole and the pin hole cross intersecting hole size tolerance of0.1mm is not easy to maintain; to adopt the reaming main pin hole, the dimensional tolerances are not easy to be ensured; the final finish milling main pin hole on the lower end surface. The main pin hole and upper and lower end verticality is not easy to guarantee; the main pin hole size can not be guaranteed.Along with our country transportation enterprise rapid development, auto transport carrying capacity and running speed are continually increasing with. So people to the safe operation of the automobile is more and more attention, so the automobile axle design also raised taller requirement. As a result of foreign automobile development starts early, technical inputs, thus technically far ahead of China market, but also there are many insufficient places, still need to improve, technology also needs a breakthrough. Steam car industry as our focus on the development of pillar industries, its prospect is very wide. At present, auto parts production has certain potential, but most enterprises in product research, development and other aspects of the defect, especially lack of less product independent development capacity, can not adapt to the system support, delivery of modules, to participate in international division of labor. Because of this, in the future development, Chinese enterprises should actively absorb the international advanced automotive technology, and constantly improve the self body lines, such as braking systems, steering systems, expand the industry of product variety, improve the integral technology level, increase the strong technological development capability, urges the enterprise faster development, adapt to the trend of globalization of automobile industry.100 years ago, the car was just beginning, the steering is modelled on the carriageand bicycle steering mode, using a joystick or a handle to make the front wheel deflection, thus realizes the steering. Due to the manipulation of effort and unreliable, so often fatal accident. The first horseless pull four wheel vehicle comes out, have a front axle and a front wheel assembly, the assembly being mounted on the crankshaft, front axle center around a point of rotation, using a rod connecting the front axle, focus, through the floor and extends upward, the wheel is fastened on the rod end, in order to manipulate the car. This device in a vehicle speed not exceeding the speed, or very good, but when the vehicle speed is increased, the driver asks to improve steering accuracy, in order to reduce tire wear, prolong the service life of tyre. In 1817, the Germans Lincoln Spang Jay presented similar to the modern automobile, the front wheel with knuckle and beam connection, he developed a kind of automobile front wheel on the main shaft to allow independent rotary structure, which is connected with the steering wheel, steering knuckle and a rotatable pin and front axle, thereby the invention of modern steering trapezoidal mechanism.Since China's reform and opening up, execute in the country the household contract responsibility system reform, make the rural economy is all-time and active. Rural freight traffic and population flow increased dramatically, speeding up the transportation mechanization into rural classicsEconomic development urgent need, it is also the needs of the market that has Chinese distinguishing feature of transport machinery -- emerge as the times require small truck. It has solved the countryside transportation need, fill the villages, townships, towns and urban transportation network is blank, active rural economics, for the surplus rural labor force to find a way out, so that tens of thousands of farmers to be on comparatively well-off road.Small truck manufacturing process is simple, cheap, purchase a car farmers generally in a year or so we can recover the cost. In addition, the highway construction has promoted the rapid development of small truck, the98% villages are on the road, so that the small truck with play.We want to develop a small truck to optimize the design, to make new products, diversification of varieties to meet a variety of needs. In a small truck design, how the complex road conditions to ensure the smooth running of the car quickly, is a serious problem. Then there is the subject of research and design.Automobile front axle driving system important constituent, it is connected with the frame through the suspension, steering wheel mounted at both ends, used to support frame and transmission wheel and frame between a variety of force, and drives the steering knuckle swing to realize vehicle steering. Using the hinge device causes the wheel to deflect a certain angle, so as to realize the steering of a vehicle axle called steering bridge, general vehicle used for steering bridge bridge, the front for steering bridge. Steering bridge not only can make the left and right wheels arranged at the front end to deflect a certain angle to realize the steering, should also be able to bear vertical load and by the road, the brake force is exerted on the longitudinal force and lateral force and the force formed by the moment. Therefore, the steering bridge must have sufficient strength and rigidity. Wheel steering process of internal friction between the pieces should be as small as possible, and to keep the vehicle steering light and the direction stability.Steering axle is generally composed of front axle, steering knuckle, steering knuckle arm, steering knuckle pin and the hub.Front axle general is in the front of the bus, also known as steering axle or drive bridge. The suspension is connected with the frame, used to support the ground and the frame between the vertical load, but also bear the braking force and lateral force and the force moment, and ensure that the steering rotation right movement. In the car used in the steering bridge, stress is more complex, so it should have enough strength. In order to ensure the correct positioning of the steering wheel angle, make the manipulation of light and reduce tire wear, steering bridge should have enough stiffness. In addition, should also try to reduce the weight of the bridge.Front axle under the front of the car weight, the car forward thrust from the frame to the wheel, and the steering device on parts make joint type connection, the implementation of the automobile steering. The cross-country vehicle front axle but also bear and rear axle the same driving task. General cargo vehicle with front engine rear drive arrangement, the front for steering bridge.Automobile front axle design should ensure adequate design strength, to ensure reliable bear acting force between wheel and frame; ensure the adequate rigidity, so that the wheel positioning parameters constant; ensure that the steering wheel have thecorrect localization angle, so that the steering wheel movement stability, convenient operation and reduce the tire friction; steering bridge quality as small as possible, in order to reduce non spring quality, improve the ride comfort of vehicles.译文前桥一般位于汽车的前部,也称转向桥或从动桥。
汽车驱动桥壳的有限元分析和优化外文文献翻译
文献出处:Paul D. FE Analysis and Optimization of Vehicle Drive Axle Housing [J]. Journal of Engineering Computers & Applied Sciences, 2015, 12(3): 21-35.原文FE Analysis and Optimization of Vehicle Drive Axle HousingPaul DAbstractAs a main part of cars, drive axle housing supports the automobile chassis and the carriage, passes weights to the wheels. Meanwhile, the vertical force, traction, braking force acting on the drive wheels are also passed to the suspension and the frame though the axle housing; therefore, it is playing as both loading part and transmission part. Because the axle is used frequently under complex conditions, their quality and property directly affect the overall performance of the vehicle and its used life, so the drive axle housing must have characteristics of sufficient strength, stiffness and good dynamic. Currently the traditional method has been difficult to meet the requirements of drive axle housing, while because of its many advantages; the finite element method becomes an effective way to solve the problem.Keywords: Drive axle housing, Leaf spring, Collaborative Simulation1 IntroductionAs one of the main parts of truck, drive axle shell to play the role of a support vehicle load, and can transfer load to the wheels, at the same time, the driving wheel on the vertical force and tangential force, braking force and the traction), lateral force is through it passed to the frame and carriage, it play the role of a bearing load and transmit forces. In the car, drive axle shell under high load, especially when the car loaded with high speed in the uneven road surface, will produce a big road impact load of the wheels, under the action of strong impact load, the dynamic behavior of the overall car will be from the drive axle shell parts inside and outside the influence of the vibration of the incentive to produce, may even make the bridge shell produces a lot of dynamic stress, lead to crack, fracture, even seriously affect the safety of the vehicle. In automobile structure, due to the use of high frequency, drive axle shell has higher failure rate, however, the overall performance of the car and the useful life isinfluenced by its quality and performance directly, this requires that it has enough strength, stiffness, and has good dynamic characteristics, in turn, to ensure that the car's stability.2 The research statusDue to the development of computer technology, expanding the application range of the finite element method (fem), especially in the 1970 s, some famous auto companies began to apply the finite element method to the design of auto parts, raised a hot wave of finite element method (fem) in the automobile structure design, such as: ford using Nastran finite element analysis software, the finite element model with shell element definition unit, to the static analysis of car body, get the stress nephogram, high stress area is determined, and carry on the improvement of the corresponding structure. By the end of the 80 s, Japan Isuzu companies have all aspects of the finite element method is applied to every part of body design. And has a well-known Japanese company by using the finite element method is proposed for 2.5 times full of axle load of drive axle housing structure analysis standard.The famous automobile company in the conventional finite element is comparatively mature application field, its research focus has shifted to nonlinear analysis, transient response analysis, impact analysis of temperature field analysis and optimization design and analysis, etc. Due to the finite element analysis software such as ANSYS was introduced, and is widely applied in engineering practice, in recent years, many automobile company and scientific research institutions joint of drive axle shell finite element analysis.2.1 Static structure analysis"The automobile drive axle bridge shell under the condition of static finite element analysis under typical conditions was described, and the static structure analysis of drive axle shell, the analysis of drive axle shell has certain reference value for design improvement, but the literature is just to simplify the structure of drive axle housing for the static analysis, the results of the analysis has certain error." Dump truck rear axle shell finite element stress calculation" compare the original model and the reinforcement model in various typical working conditions of the static structureanalysis, fully embodies the advantage of finite element method (fem) and quick, economic and environmental protection, provides the basis for the drive axle housing structure improvement design;"ZL50 wheel loader type welding drive axle shell vibration modal analysis" in various typical working conditions are introduced, the static structural analysis of the drive axle shell, got the stress contours and strain contours, and make evaluation on its structure and performance, but the object of study is just drive axle shell, evaluation of the lack of integrity. " Automobile drive axle housing based on ANSYS finite element analysis of" stated the application of finite element method, ANSYS software of finite element analysis was carried out on the drive axle housing, and the analysis results compared with the traditional theoretical calculation results, shows many advantages of the finite element method;" automobile drive axle bridge shell finite element analysis shows that the national standards of drive axle shell, the strength, stiffness, and the different thickness of the drive axle shell finite element analysis, the results show that the thickness of several bridge shell meet the evaluation indexes.2.2 Dynamic analysis"Automobile drive axle shell finite element dynamic is analysis of ANSYS software for static structural analysis and modal analysis. Through the modal analysis, obtained the low order natural frequency and vibration mode, and the experimental results are basically the same. "Drive axle integral finite element dynamic simulation" describes the test data is only on the surface of the drive axle shell vibration, dynamic analysis method is the data on the drive axle shell unit within the node, make up the lack of experiment, and provides research foundation for vibration noise. "Mini drive axle shell structural strength and modal analysis by ANSYS modal analysis was carried out on the drive axle housing, and obtained the low-order modal frequencies and their corresponding vibration mode, analyzes the results, drive axle shell dynamic design standard.2.3 Fatigue analysisDrive axle shell in order to make use of the finite element software static structure analysis, modal analysis and the analysis of the fatigue strength, fatigue lifeof drive axle shell distribution, and the service life of the most dangerous point value;" Automobile drive axle shell under the action of random load fatigue life forecast" drive axle shell to make use of Nastran static structural analysis and fatigue analysis, the fatigue life of drive axle shell distribution, and the service life of the most dangerous point value, and compared with the bench fatigue test data, the data is consistent. Drive axle shells to make use of the finite element method of fatigue analysis, drive axle shell, the distribution of fatigue life and the life value of the most dangerous point, provided the basis for its improvement.2.4 Optimization analysisVehicle drive axle shell dynamic optimization design based on parametric drive axle housing for the reliability optimization, on the basis of this, adhere to the principle of overall lightweight, local reinforcement, continue size optimization, the results not only lightweight effect is obvious, and guarantee its mechanical performance. Drive axle bridge shell finite element analysis and structure optimization by using finite element software for structural analysis, and put forward improvement on the basis of the results of the analysis, again carries on the analysis, comprehensive evaluation of the results of the analysis, after the effectiveness of the proposed improvement measures. To sum up, in recent years, with the development of the computer, the finite element technology gradually mature, expanding its application field, application of finite element method (fem) to drive axle design, can effectively shorten the development cycle, reduce production cost, and improve competitiveness.3 Finite element modelsCreate a bridge shell entity model is a priority for the finite element analysis on it. Because its structure is complex, irregular surface is more, directly using ANSYS Workbench's own entity modeling module of drive axle shell model created there is a big difficulty, therefore, in this paper, with the aid of Solid works software strong modeling ability, create physical model of drive axle housing. When establishing finite element model, which requires it to reflect the important mechanical properties of the model itself, and USES the appropriate unit types, try to decrease the number ofunits, in order to make sure to get a precise finite element calculation results as well as shorten the calculation time, so to simplify some of the minor, the dangerous structures, while retaining the original structure of drive axle shell body, make its can still reflect the actual structure of the main characteristics and mechanical characteristics, in order to meet these requirements, set up the model, the model is correct, geometric elements, on the basis of relevant and mechanical properties of the model under the premise of do not change, its structure is necessary. For building solid model is made up of drive axle housing, leaf spring, plate spring and assembly model is composed of main reducer shell. Drive axle housing is stamping steel welded integral, including: bridge shell body and axle tube, bridge shell body made of steel plate stamping welding.4 Bridge shell finite element modelCreate a finite element model is a necessary condition for finite element analysis, it is also important link, will create the entity model of Solid works first imported to ANSYS Workbench, and then, using ANSYS Workbench material definition, contact to set, meshing, finite element model. As pretreatment module of ANSYS Workbench, the situation has a direct and significant impact on the finite element analysis. ANSYS Workbench provides powerful ability of automatic classification, through the practical intelligence can be realized by default, complex model of meshing grid can be achieved by changing parameters real-time updates. Based on ANSYS Workbench mesh with flexibility, can be achieved for different structure or targeted meshing characteristics, in order to ensure the accuracy of finite element simulation. Analysis, finite element model of nodes and the cells are involved in calculation, in the ANSYS Workbench, you can preview based on grid, to assess whether it is reasonable, and through the elaboration, has higher precision of the calculation results, however, refined grid will make analysis and calculation time, and even has higher request to the hardware, it increases the cost of computing, therefore, grid refinement to appropriate, can also through the choice of changing the type of unit to reduce the amount of calculation. The drive axle housing was established based on Solid works assembly model, based on the collaborative simulationenvironment, using ANSYS Workbench software model for material definition, meshing, loading and constraint, combined with several typical working conditions, analysis to calculate the stress and deformation of the drive axle housing, through ANSYS Workbench software on the drive axle shell body free modal analysis, calculate the each order natural frequency of the modal value and their corresponding vibration mode. To summarize evaluation calculation results, some conclusion, aiming at specific problems on the structure of the local hazardous area put forward the corresponding improvement, and the structure of the improved bridge shell model, static structure analysis and modal analysis, again will improve before and after the bridge structure, comparing the shell model of finite element analysis of the data bridge housing improvement is effective and feasible.译文汽车驱动桥壳的有限元分析和优化Paul D摘要作为载货汽车的主要部件之一,驱动桥壳支撑着汽车的车架和车厢,并将相应的载荷传递给车轮,驱动车轮承受的垂向力、制动力和牵引力、侧向力也是通过它传递给车架和车厢的,它起着承载荷重和传递作用力的作用。
汽车驱动桥常见故障分析及维修方法外文文献翻译、中英文翻译、外文翻译
汽车驱动桥常见故障分析及维修方法外文文献翻译、中英文翻译、外文翻译附录Car driver bridge just common failure analysis and repair methods Motor reducer main function is to increase the input torque, lower speed, and will accept the transfer of power to change the direction of differential. Disassembly in the maintenance process, the main reducer assembly and adjustment of the quality of the good or bad, a direct impact on the main reducer of the state of technology and the main gear reducer, vice life. Must be in accordance with technical requirements and methods to ensure that the assembly quality and accuracy of the adjustment. Reducer in the main assembly in the process of adjustment, including the main owners, driven bevel gear bearing pre-adjustments, the main, driven cone-prints and meshing gears meshing space adjustments, and so on. Reducer in the main assembly adjustment, the adjustment in order to ensure the quality of assembly, must abide by the rules as follows: First, the first adjustment of the pre-bearings, and then adjust the gear mesh, vice-prints, the final adjustment of the meshing gears, deputy space. Secondly, the main, driven gear bearing cone of pre-degree must be provided for in the original methods and numerical check and adjust the main reducer in the process of adjustment, bearing the pre-degree change may not always be in line with the original Provides value. Third, to ensure the engagement of qualified prints on the premise of the adjustment of meshing gears, deputy space. Meshing and mesh-prints of the changes in the amount of space must be in compliance with technical requirements, otherwise it is necessaryto replace the pair in pairs. Fourth, the adjustment process, such as bevel gear, bevel gear Aoli Kang and hypoid bevel gear, often moving to take the initiative to adjust the bevel gear mesh prints, driven by mobile bevel gear meshing space adjustments. The high-arc bevel gear Gleason bevel gear meshing and mesh-prints of the gap adjustment method is not special.Bearing reducer main pre-adjustments in order to remove the main, driven bevel gear shaft bearing the extra space axial and radial clearance, and reducer installed in the main, driven bevel gear shaft bearings, it should be a certain The pre-compression, and part of the balance before and after the axial load bearing. This willmake the main, driven bevel gear at work to maintain the right mesh, and can pre-and post-bearings to obtain a more uniform wear. First of all, take the initiative to adjust the bevel gear bearing the pre-, pre-adjustment of their degrees in two ways: The first method is through changes in the gasket to adjust to adjust. Adjust the location of gaskets, and some separation between the two sets of bearings, some shaft in the shoulder, some in the back of the main reducer. Adjusted increase in the pads, reducing the pre-degree; pads to reduce the adjustment, increased pre-degrees. The second method is to use an alternate set of flexibility to adjust it by the installation, according to the provisions of torque tightening nut penetration margin of the fixed disk, so that every other set of elastic deformation resulting from the initiative to ensure the bevel gear bearing the pre-degrees. Next, adjust the bevel gear follower of the pre-degree bearing. According to the driver of the bridge structure is divided into two different ways: the first is a single-stage reducer, which is driven bevel gear differential bearing bearings, drivenadjustment bevel gear bearing pre-degree differential bearing adjustment is pre - Tight, adjust the differential bearing on both sides of the nut adjustment to achieve. Adjustments on both sides of the nut tightened, pre-degree increase; on both sides of the adjustment screw pine nut, pre-degree decrease. The second is a two-stage reducer, the bevel gear driven secondary and take the initiative to slow down the cylindrical gear with a fixed axis, with both ends of the bearing shell on the main reducer. Adjust the location of gaskets in the two bearings between the shell and cover. Adjusted increase in the pads, reducing the pre-degree; pads to reduce the adjustment, increased pre-degrees. Second, the main, driven bevel gears meshing tooth prints and the adjustment of the main side of the gap, driven bevel gears meshing side of the gap-tooth-prints and adjustment: the main, be driven bevel gear teeth along the direction of the long exposure, and its location in the control gear The little-central bias, the small end-to-end from the Ministry of 2 ~ 7mm, traces of contact with the length of not less than 50% of the long teeth, tooth direction of the high-contact-prints should be not less than 50% of the high-gear, the general should be from the addendum 0 . 80 ~ 1.60mm; side of the tooth gap to 0. 15 ~ 0. 50mm, but each of the bevel gears meshingVice change in the amount of space no larger than 0.15mm. When the owners, driven bevel gears meshing side of the gap-tooth-prints and do not meet the requirements should be adjusted in accordance with the following method to simplify the formula is: "Progressive", that is, when the mating preference-prints big-time, move from gear to gear shift Near; at this time if the tooth side of the gap is too small, will take the initiative to move out of gear. "From a small", that is, when the matingpreference-prints little-time, move from gear to gear the initiative away; at this time if the tooth side of the gap is too large, the initiative will be moved closer to the gear inside. "Lord jacking", that is, when the mating preference-prints addendum, the initiative will be moved closer to the driven gear to gear; at this time if the tooth side of the gap is too small, will be driven out of gear away. "The main root out", that is, when the mating preference-prints root, it will take the initiative to gear since moving away gear; at this time if the tooth side of the gap is too large, driven gear will be moved closer to the inside.In the motor-driven mechanical automotive power train, drive power train bridge at the end of their basic function is to increase the transmission shaft or transmission came directly from the torque, torque will be allocated to the left and right wheel drive with Vehicle kinematics required by the differential function; at the same time, drivers also have to face the role of the bridge on the road or inside the frame and between the vertical, horizontal and vertical force. Therefore, vehicle drive axle should have the following functions: to ensure that the right has a reduction ratio, so that the car has the best power and fuel economy; differential with the role to ensure that the vehicle or to the uneven roads, tires do not have a Waterloo is delayed; have greater ground clearance in order to ensure the adoption of good; as much as possible to reduce weight in order to reduce vehicle weight; gear transmission and other mechanical work in a smooth, noise-free. Driver function as the bridge complex, so a higher failure rate. Its main fault: the early damage to the main reducer, made bridge-driven sound, heating and oil and so on.Bridge driver were the causes of the different and various fault is not the formation of a single isolated, but interrelated. Ifafailure occurred in a timely manner is not ruled out, it is easy to induce another failure to form a chain reaction. If the gap is too small mesh gear, it would drive axle fever, and it will lead to fat drive axle ring, but also the main cause of early damage to the reducer. Reducer is the main driver bridge in the heart of its early damage will seriously affect the life of the drive axle. Early in the form of its damage are: Vice-gear early wear, tooth fracture, early damage to the gear bearings and so on. Meshing gears are too small or too large gap caused by wear and tear in the early gears. Bearing the pre-force is too large or too small. Preload is too large, the impact on the efficiency of transmission so that the bearings overheat and shorten the life span; Preload over an hour to make the situation worse meshing of gears, contact stress increases, leading to a pair of early wear and tear. Not add gear oil requirements. Main reducer to be added as required gear oil in order to guarantee the normal lubrication of the gear, otherwise, in a very short car mileage, the tooth will be due to poor lubrication caused by pitting, and a sharp bond wear. Driven gear as a result of the adjustment locking nut loose and have a shift. Adjust the nut loose, causing a passive gear shift, the meshing gap change gear, Deputy Ambassador of early wear and tear.Common faults:1. Tooth fracture. Meshing gears too much space. When the gear mesh in time to adjust without too much space, so that the owners, driven gear engagement in the process of impact, making gear fault.2. Differential gear bearings or bearing damage. Bearing damage, roller out in the main reducer, the gear will be damaged.3. Driven gear differential with the loose bolt connections, and off, also damaged gear.4. Severely overloaded vehicle, so that the bearing load, making it lower life expectancy. Overloaded vehicle traveling through uneven pavement, gears and bearings, etc. impact on the load in a row and the role of the early damage occurred.In short, the judge ruled out and drive axle failure, it is necessary to analyze specific issues. In general, improper use, improper assembly adjustment, the quality of the parts itself is a question which drives the root causes of bridge failure. The fault has produced a number of reasons, or one; at the same time, adjustmentof the assembly, such as using incompatible with a drive axle that could cause a variety of failures.汽车驱动桥常见故障分析及维修方法汽车主减速器的功用是将输入的转矩增大,转速降低,并将接受的动力传递方向改变后传给差速器。
驱动桥的构造外文文献翻译、中英文翻译、外文翻译
附录AThe structure of driving axleThe driving axle is in the power power transmission the terminal, its basic function increases the torque which transmits by the drive shaft or the transmission gearbox, and power reasonable assignment for left and right driving gear, moreover also withstands the function vertical sets up, the longitudinal force and the transverse force between the road surface and the frame or the automobile body.The driving axle generally by the main gear box, the differential device, the wheel transmission device and the driving axle shell and so on is composed.1.Driving axle design:The driving axle design must satisfy following basic request:1). Choice main reduction gear ratios ought to be able to guarantee the automobile has the best power and the fuel economy.2). External dimensions must be small, guaranteed has the necessity ground clearance.3). Gears and other transmission piece works do steadily, the noise is small.4). Has the high transmission efficiency under each kind of rotational speed and the load.5). Under the guarantee enough intensity, the rigidity condition, should make every effort the quality to be small, under the reed the quality should be as far as possible small in particular, improves the automobile smoothness.6). Coordinated with the suspension fork guidance organization movement, regarding changes the driving axle, but also should coordinate with the rotation gear movement.7). Structures are simple, the processing technology capability is good, the manufacture is easy, disassembling, the adjustment is convenient.2.Driving axle classificationThe driving axle minute non-separation type with separates the type two big kinds.1).Non-separation type driving axleThe non-separation type driving axle also is called the integral-type driving axle, its rear axle drive pipe and main gear box shell with shaft casing rigidly connected whole Liang,thus the both sides rear axle and the driving gear swing related, passes the elastic part and the frame is connected.It by the driving axle shell 1, the main gear box, the differential device and the rear axle is composed.2). Separation type driving axleThe driving axle uses the independent suspension fork, namely the main gear box shell fixes on the frame, the both sides rear axle and the driving gear can be opposite in the rolling plane in the chassis have the relative motion to be called the separation type driving axle.In order to coordinates with the independent suspension fork, fixes the main gear box shell in the frame (or automobile body) on, the driving axle shell partition and through the hinge joint, or no longer has the driving axle shell other parts besides the main gear box shell.In order to meet the need which about the driving gear independence beats, between the differential device and between wheel rear axle each section connects with the universal joint.3.Drive axle of compositionMainly by the reducer drive, and half axle and drive axle shell, etc.1) .Main reducerThe speed reducer is usually used to change the direction of transmission, reduce speed and increase torque, guarantee cars have enough force and appropriate speed. Main reducer, have more single type, double, double speed reducer, wheel edges.a). Single main reducerBy a reduction gear reducer realization of single reducer, called. Its simple structure, light weight, dongfeng BQl090, light, medium sized truck was widely used in automobile.b). Double main reducerIn some large trucks, load demand is bigger than the slow, with single main reducer drive, driven gear diameter increases, affect to the ground clearance drive, so using twice. Usually called doublestage reducer. Two groups of double reduction gear reducer, increasing torsional twice slowdown.To improve the tapered gear pair of meshing smoothness and strength, the level of spiral bevel gears reduction gear pair is. Second gear pair is helical gears for support.Active tapered gear rotating, drive driven circular gear rotating, thus completing silver. Level Article 2 the initiative of cylindrical gears and driven tapered gear coaxial and rotate together, and bring about a follower of cylindrical gears rotate, 2. Because a follower ofcylindrical gears installed in differential shell, so, when a follower of cylindrical gears turning, through the differential and half shaft is driven wheel rotation.2).DifferentialAround half shaft are used to connect differential wheel, can make the sides with different velocity rotating torque simultaneously. Ensure the normal scroll wheel. Some more, in the car driver bridge or in the breakthrough of thansfer transmission shaft with differential between, also called the bridge between differential. Its role in the car is in turn or flat road to drive wheels, and generate differential between the role.Current domestic cars and other cars are adopted symmetric bevel gear ordinary differential. Symmetrical type gear differential planetary gear, half of planetary gear axle shaft gear, or a cross (direct axis) and differential shell, etc.Most current car using differential planetary gear, ordinary bevel gear differential by two or four conical planetary gear and planetary gear axle, two cone half shaft gear and differential shell, etc.3). Half axleHalf shaft are coming to the differential wheel, drive torque to move the car wheel rotation, the solid shaft. Due to the different structure, installation of hub axial force and the different also. Therefore, half shaft are divided into the floating, use, three/four floating three types.a). Howo fou-point suspending half axleGeneral big, medium-sized cars are adopted the floating structure. Half of the spline shaft inside with the half shaft with differential gears connected to the end of the half shaft are forging flanges, bolts and wheel connection. Hub through two far apart WenCheng tapered roller bearings in half a collar. Half a collar and driving axle shell pressure to drive, composition. Use this form, half shaft bearing no direct link with the bridge housing, half shaft driving torque and not only bear any moment under this half shaft are called "the floating" half axle. The so-called "float" means half shaft are not bending load.The float, the half axle shaft for lugs and made one. But there are some heavy trucks to lugs, and made the individual parts of the spline shaft in the half. Therefore, both ends of the spline shaft is used, can HuanTou.b). Use half axleUse of half axle within the same with the client, not withstand float bending-torsional. The client through a direct bearing on the inside of half axle shell. This means that willsupport the half axle under bending moment. Therefore, the half sleeve torque, except under bending moment, local use half shaft is called. This structure is mainly used for certain.The red flag brand limousines CA7560 type of thing. The half shaft are not bending moment, the client will inherit all external use, so called bending support.c). 3/4 floating half axleThree-quarters of floating half shaft are short of bending degree between use and the floating. This type of half axle currently used in XiaoWoChe, only on individual applications, such as M20 type car. Warsaw,4). The bridge housinga). Integral bridge housingIntegral bridge housing for the intensity and rigidity, and facilitate the good performance of the installation, adjustment and maintenance, and widely used. Integral bridge housing for manufacturing methods, which can be divided into different midway through the whole cast type, the steel casting and stamping steel welding etc.b). Drive axle shell segmentedSection type bridge housing generally fall into two, one will DuanLianCheng two by bolts. Bridge housing is segmented to casting and machining.附录B驱动桥的构造驱动桥处于动力传动系的末端,其基本功能是增大由传动轴或变速器传来的转矩,并将动力合理的分配给左、右驱动轮,另外还承受作用于路面和车架或车身之间的垂直立、纵向力和横向力。
- 1、下载文档前请自行甄别文档内容的完整性,平台不提供额外的编辑、内容补充、找答案等附加服务。
- 2、"仅部分预览"的文档,不可在线预览部分如存在完整性等问题,可反馈申请退款(可完整预览的文档不适用该条件!)。
- 3、如文档侵犯您的权益,请联系客服反馈,我们会尽快为您处理(人工客服工作时间:9:00-18:30)。
As the bearing cage rotates, read the value7. indicated on the scale.Preload normally is specified as torque re-8. quired to rotate the pinion bearing cage, so take a reading only when the cage is rotating. Starting torque will give a false reading.To calculate the preload torque, measure the 9. diameter of the bearing cage where the cord was wound. Divide this dimension in half to get the radius.10. U se the following procedure to calculate thebearing preload torque:Standard.Pull (lb) 3 radius (inches) 5 preload (lb-in.)orPreload (lb-in.) 3 0.113 (a conversion constant) 5 preload (N .m)Install the yoke, flat washer, and nut. Tighten 6. the nut snugly. Tap the end of the input shaft lightly to seat the bearings.Measure the input shaft endplay again with 7. the dial indicator. If endplay is still incorrect, repeat steps 3 through 7.With the endplay correct, seal the shim pack 8. to prevent lube leakage. Then torque the i nput shaft nut and cover capscrews to the correct value.24.5 A XLE ADJUSTMENTSAND CHECKSThis section introduces the differential carrier adjust-ments, checks, and tests that the truck technician must be capable of performing; some have beenr eferred to previously in the text. For the most part, the procedures described here are general in nature. The truck technician should refer to OEM servicel iterature for specific procedures.PINION BEARING PRELOADMost differential carriers are provided with a press-fit outer bearing on the drive pinion gear. Some older rear drive axles use an outer bearing, which slips over the drive pinion. The procedures for adjusting both types follow.Press-Fit Method AdjustmentTo adjust the pinion bearing preload using the press-fit method, use the following procedure:Assemble the pinion bearing cage, bearings, 1. spacer, and spacer washer (without drive pin-ion or oil seal). Center the bearing spacer and spacer washer between the two bearing cones (Figure 24–49).When a new gear set or pinion bearings are 2. used, select a nominal size spacer based on OEM specifications. If original parts are used, use a spacer removed during disassembly of the drive.Place the drive pinion and cage assembly in a 3. press, with the gear teeth toward the bottom.Apply and hold the press load to the pinion 4. bearing. As pressure is applied, rotate the bearing cage several times so that the bear-ings make normal contact.While pressure is held against the assembly, wind 5. a cord around the bearing cage several times.Attach a spring scale to the end of the cord 6. (Figure 24–50). Pull the cord with the scale ona horizontal line.FIGURE 24–49 Assembly of the pinion bearing cage.(Courtesy of Dana Corporation)FIGURE 24–50 Cage in press to check bearingp reload.Sleeve must applymust be against the outer bearing. If the fit between the yoke or flange splines and drive pinion splines is tight, use a press to install the yoke or flange (Figure 24–51).Temporarily install the drive pinion and cage 4. assembly in the carrier (Figure 24–52). Do not install shims under the bearing cage.Install the bearing cage to the carrier cap-5. screws. Washers are not required at this time. Hand-tighten the capscrews.Fasten a yoke or flange bar to the yoke or 6. flange (Figure 24–53). The bar will hold the drive pinion in position when the nut ist ightened.Metric.Pull (kg) 3 radius (cm) 5 preload (kg-cm) orPreload (kg-cm) 3 0.098 (a conversion constant) 5 preload (N .m)Examples. We can convert the foregoing equa-tions into examples by applying some data to them:Standard7.5 lb 3 3.31 in. 5 24.8 lb-in. (preload) or24.8 lb-in. 3 0.113 5 2.8 N .m (preload)Metric3.4 kg 3 8.4 cm 5 28.6 kg-cm (preload) or28.6 kg-cm 3 0.098 5 2.8 N .m (preload)11. I f necessary, adjust the pinion bearing preloadby changing the pinion bearing spacer. A thicker spacer will decrease preload, whereas a thinner spacer will increase the preload.12. O nce the correct bearing preload has beenestablished, note the spacer size used. Select a spacer 0.001 inch (0.025 mm) larger for use in the final pinion bearing cage assembly pro-cedures. The larger spacer compensates for slight expansion of the bearing, which occurs when pressed on the pinion shank. The trial spacer pack should result in correct pinion bearing preload in three times out of four cases.Y oke Method of AdjustmentTo adjust the pinion bearing preload using the yoke or flange method, proceed as follows:Assemble the complete pinion bearing cage 1. as recommended in the press-fit method.A forward axle pinion is equipped with a heli-2. cal gear. For easier disassembly during bear-ing adjustment procedures, use a dummy yoke (if available) in place of the helical gear.Install the input yoke or flange, nut, and 3.washer on the drive pinion. The yoke or flangeFIGURE 24–51 Using a press to install the yoke orflange to the drive pinion. (Courtesy of Arvin Meritor)FIGURE 24–52 Install the pinion and cage assembly in the carrier housing. (Courtesy of Arvin Meritor)indicated on the torque wrench (see Figure 24–55). Typical value is 50 lb-ft. (68 N .m)m aximum applied to one side gear.If the torque value exceeds the specification, 5. disassemble the differential gears from the case halves.Check the case halves, spider, gears, and 6. thrust washers for the problem that caused the torque value to exceed specifications. Re-pair or replace defective parts as required. Remove any foreign debris.Check/Adjust Pinion Cage Shim PackThis procedure is used to check and adjust the thick-ness of the shim pack used in the pinion bearing cage. Use this procedure if a new drive pinion and crownTighten the nut on the drive pinion to specifi-7. cation, typically 400 to 700 lb-ft. (542 to 950 N .m).Remove the yoke or flange bar.8. Attach a torque wrench to the drive pinion 9. nut. Rotate the drive pinion and read the value indicated on the torque wrench. Preload is correct when the torque required to rotate the pinion bearing cage is from 15 to 35 lb-in. (1.7 to 4.0 N .m).To adjust the pinion bearing preload, disas-10. semble the pinion bearing cage and change the pinion bearing spacer size. A thicker spacer will decrease preload, whereas a thin-ner spacer will increase preload.Differential Rolling ResistanceA check to measure and establish differential rolling resistance follows. To perform this check, a special tool must be made. You can easily make this tool from an old axle shaft that matches the spline size of the differential side gear. Figure 24–54 illustrates the fab-rication specifications for this special tool.To check differential resistance to rotation, use the following procedure:Install soft metal covers over the vise jaws to 1. protect the ring gear (Figure 24–55).Place the differential and crown gear assem-2. bly in the vise.Install the special tool into the differential until 3. the splines of the tool and one side gear are engaged.Attach a torque wrench to the nut of the spe-4. cial tool and rotate the differential gears. As the differential gears rotate, read the valueFIGURE 24–55 Reading the torque value to check the rolling resistance. (Courtesy of Arvin Meritor)FIGURE 24–53 Using a flange bar to hold the drivepinion in position. (Courtesy of Arvin Meritor)FIGURE 24–54 Fabrication details for a tool to checkthe rolling resistance. (Courtesy of Arvin Meritor)If the new pinion cone number is a minus (–), sub-8. tract the number from the standard shim packthickness that was calculated in step 3 or 4.The value calculated in step 7 or 8 is the 9.t hickness of the new shim pack that will bei nstalled. Figure 24–59 illustrates several e xamples of determining shim pack t hickness.Install the drive pinion, bearing cage, and new10. shim pack into the differential carrier.gear set is to be installed, or if the depth of the drive pinion has to be adjusted. You are checking the rolling resistance using a torque wrench.To check/adjust the shim pack thickness (Figure 24–56), do the following:With a micrometer, measure the thickness of 1. the old shim pack removed from under the pinion cage (Figure 24–57). Record the mea-surement for later use.Look at the pinion cone (PC) variation number 2. on the drive pinion being replaced (Figure 24–58). Record this number for later use also.If the old pinion cone number is a plus (+), 3. subtract the number from the old shim pack thickness that was recorded in step 1.If the old pinion cone number is a minus (–), 4. add the number to the old shim thickness that was measured in step 1.The value calculated in step 3 or 4 is the 5.t hickness of the standard shim pack without variation.Look at the PC variation number on the new 6. drive pinion that will be installed. Record the number for later use.If the new pinion cone number is a plus (+), 7. add the number to the standard shim packthickness that was calculated in step 3 or 4.FIGURE 24–56 Drive pinion depth controlled by shimpack thickness. (Courtesy of Arvin Meritor)FIGURE 24–57 Measuring the thickness of the old shim pack. Mike each shim individually then add tocalculate total thickness. (Courtesy of Arvin Meritor)FIGURE 24–58 Location of the pinion cone (PC)v ariation number. (Courtesy of Arvin Meritor)Adjust Differential Bearing PreloadOne of two methods can be used to check and adjust the preload of the differential bearings.Method One.Attach a dial indicator onto the mounting 1. flange of the carrier and adjust the indicator so that the plunger rides on the back surface of the crown ring gear (Figure 24–60).Loosen the bearing adjusting ring that is op-2. posite the ring gear so that a small amount of endplay is indicated on the dial indicator. To turn the adjusting rings, use a T-bar wrench that engages two or more opposite notches in the ring (Figure 24–61).Move the differential and crown gear to the 3. left and right using prybars as you read the dial indicator. Use two prybars that fit be-tween the bearing adjusting rings and the ends of the differential case (Figure 24–62). You also can use two prybars between the differential case or crown gear and the carrier at locations other than those just described. In either case, the prybars must not touch the differential bearings.EXAMPLES:Inchesmm 1.Old Shim Pack Thickness Old PC Number, PC +2Standard Shim Pack Thickness New PC Number, PC +5New Shim Pack Thickness .030.76–.002–.05.028.71+.005+.13.033.842.Old Shim Pack Thickness Old PC Number, PC –2Standard Shim Pack Thickness New PC Number, PC +5New Shim Pack Thickness .030.76+.002+.05.032.81+.005+.13.037.943.Old Shim Pack Thickness Old PC Number, PC +2Standard Shim Pack Thickness New PC Number, PC –5New Shim Pack Thickness .030.76–.002–.05.028.71–.005–.13.023.584.Old Shim Pack Thickness Old PC Number, PC –2Standard Shim Pack Thickness New PC Number, PC –5New Shim Pack Thickness.030.76+.002+.05.032.81–.005–.13.027.68FIGURE 24–59 Determining shim pack thickness.(Courtesy of ArvinMeritor Inc.)FIGURE 24–60 Dial indicator attached to carrier-mounted flange. (Courtesy of Arvin Meritor)FIGURE 24–61 Turning the adjusting ring using aT-bar wrench. (Courtesy of Arvin Meritor)FIGURE 24–62 Using pry bars to adjust play in the crown gear. (Courtesy of Arvin Meritor)Tighten the same bearing adjusting ring4.so that no endplay shows on the diali ndicator.Move the differential and crown gear to the5.left and right as needed. Repeat step 3 untilzero endplay is achieved.Tighten each bearing adjusting ring one6.notch from the zero endplay measured instep 4.Method Two.A second method of checking pre-load is to measure the expansion between the bearing caps after you tighten the adjusting rings. Use the following procedure:Turn both adjusting rings hand tight against1.the differential bearings.Measure the distance X or Y between oppo-2.site surfaces of the bearing caps (Figure24–63A) using a large micrometer of thec orrect size (Figure 24–63B). Make a note ofthe m easurement.Tighten each bearing adjusting ring one3.notch.Measure the distance X or Y again. Compare4.the dimension with the distance X or Y mea-sured in step 2. The difference between thetwo dimensions is the amount that the bear-ing caps have expanded.Example: Measurements of a carrier.Distance X or Y before tightening adjusting rings5 15.315 inches (389.00 mm)Distance X or Y after tightening adjusting rings5 15.324 inches (389.23 mm)15.324 inches minus 15.315 inches5 0.009 inch (0.23 mm) differenceIf the dimension is less than specification, repeat steps 3 and 4 as needed.Crown Gear Runout CheckTo check the runout of the crown/ring gear, do the f ollowing:Attach a dial indicator on the mounting flange1.of the differential carrier (Figure 24–64).Adjust the dial indicator so that the plunger or2.pointer is against the back surface of thecrown gear.FIGURE 24–63 (A) Location of distances measured to check expansion between bearing caps aftert ightening adjusting rings; (B) measuring this distance.(Courtesy of Arvin Meritor)FIGURE 24–64 Checking crown gear runout. (Courtesy of Arvin Meritor)Pinion and Crown Tooth ContactA djustment Correct tooth contact between the pinion and crown gear cannot be overemphasized, because improper tooth contact results in noisy operation and prema-ture failure. The tooth contact pattern consists of the lengthwise bearing (along the tooth of the ring gear) and the profile bearing (up and down the tooth). F igure 24–68 shows crown gear toothn omenclature.Adjust the dial of the indicator to zero.3. Rotate the differential and crown gear when4. reading the dial indicator. The runout of the crown gear must not exceed 0.008 inch (2 mm) (a typical value; refer to the applicable OEM service literature for the specificv alues).If runout of the crown gear exceeds the speci-5. fication, remove the differential and crown gear assembly from the carrier. Check the dif-ferential components, including the carrier, for the problem causing the runout of the gear to exceed specification. Repair or replace defec-tive components.After the components are repaired or re-6. placed, install the differential and crown gear into the carrier.Repeat the preload adjustment of the 7. differential bearings. Then repeat this runout procedure.Check/Adjust Crown Gear BacklashIf the used crown and pinion gear set is installed, ad-just the backlash to the setting that was measured before the carrier was disassembled. If a new gear set is to be installed, adjust backlash to the correct speci-fication for the new gear set.To check and adjust ring gear backlash, do thef ollowing: Attach a dial indicator onto the mounting1. flange of the carrier (see Figure 24–64).Adjust the dial indicator so that the plunger is 2. against the tooth surface at a right angle.Adjust the dial of the indicator to zero, making 3. sure that the plunger is loaded through at least one revolution.Hold the drive pinion in position.4. When reading the dial indicator, rotate the5. crown gear a small amount in both directions against the teeth of the drive pinion (Figure 24–65). If the backlash reading is not within specification (typically ranging from 0.010 to 0.020 inch or 254 to 508 mm), adjust backlash as outlined in steps 6 and 7.Loosen one bearing adjusting ring one notch 6. and then tighten the opposite ring the same amount. Backlash is increased by moving the crown gear away from the drive pinion (Figure 24–66). Backlash is decreased by moving the crown gear toward the drive pin-ion (Figure 24–67).Repeat steps 2 through 5 until the backlash is 7.within specifications.FIGURE 24–65 Check crown gear backlash. ( Courtesy of Arvin Meritor)FIGURE 24–66 Adjustments to increase backlash. (Courtesy of Arvin Meritor)the pattern in an unloaded condition (such as when you are performing this test) will be approximately one-half to two-thirds of the crown gear tooth in most models and ratios.Checking Tooth Contact Pattern on a Used Gear Set. Used gearing will not usually display the square, even contact pattern found in new gear sets. The gear will normally have a pocket at the toe-end of the gear tooth (Figure 24–71) that tails into a contact line along the root of the tooth. The more use a gear has had, the more the line becomes the dominant characteristic of the pattern.Adjusting Tooth Contact Pattern. When dis-assembling, make a drawing of the gear tooth con-tact pattern so that when reassembling it is possible to replicate approximately the same pattern. A cor-rect pattern should be clear of the toe and centers evenly along the face width between the top land and the root. Otherwise, the length and shape of the pattern can be highly variable and are usually con-sidered acceptable—providing the pattern does not run off the tooth at any time. If necessary, adjust the contact pattern by moving the crown gear and drive pinion.Checking Tooth Contact Pattern on a New Gear Set. Paint 12 crown gear teeth with a marking compound (Figure 24–69) and roll the gear to obtain a tooth contact pattern. A correct pattern should be well centered on the crown gear teeth with lengthwise contact clear of the toe (Figure 24–70). The length ofFIGURE 24–67 Adjustments to decrease backlash.(Courtesy of Arvin Meritor)FIGURE 24–68 Crown gear tooth nomenclature.(Courtesy of Dana Corporation)FIGURE 24–69 Application of a marking compoundto check tooth contact. (Courtesy of Dana Corporation)FIGURE 24–70 Correct tooth contact patternfor new gearing. (Courtesy of Dana Corporation)FIGURE 24–71 Correct tooth contact pattern for used gearing. (Courtesy of Dana Corporation)making adjustments, first adjust the pinion and then the backlash. Continue this sequence until the pattern is satisfactory.Thrust Screw AdjustmentFor those differential carriers equipped with a thrust screw, perform the following procedure. (If the carrier assembly does not have a thrust block, proceed to step 4 of this procedure.)Rotate the carrier in the repair stand until the 1. back surface of the crown gear is toward the top.Put the thrust block on the back surface of 2. the ring gear. The thrust block must be in the center between the outer diameter of the gear and the differential case.Rotate the crown gear until the thrust block 3. and hole for the thrust screw, in the carrier, are aligned.Install the jam nut on the thrust screw, one-4. half the distance between both ends (Figure 24–74).Install the thrust screw into the carrier until the 5. screw stops against the crown gear or thrust block.Loosen the thrust screw one-half turn, or 180 6. degrees.Tighten the jam nut to the correct torque value 7. against the carrier (typical values range from 150 to 295 lb-ft. or 200 to 400 N .m) (Figure 24–75).Axle TrackingAxle tracking can be measured using the older tram bar method or electronic alignment equipment. The procedures for setting axle alignment and tracking areexplained in Chapter 25.FIGURE 24–72 Two incorrect patterns when adjusting pinion position. (Courtesy of Dana Corporation)Crown gear position controls the backlash setting. This adjustment also moves the contact pattern along the face width of the gear tooth (Figure 24–72). Pinion position is determined by the size of the pinion bear-ing cage shim pack. It controls contact on the tooth depth of the gear tooth (Figure 24–73).These adjustments are interrelated. As a result, they must be considered together even though thepattern is altered by two distinct operations. WhenFIGURE 24–73 Two incorrect patterns when adjusting backlash. (Courtesy of Dana Corporation)• Most differential carriers are replaced as rebuilt/exchange units, so the role of the technician is, more often than not, to diagnose the problem and then, if necessary, to replace the defective assembly as a unit.• The technician who has disassembled and reas-sembled differential carriers should find trouble-shooting procedures easier to follow.• Follow the OEM procedure when disassem-bling differential carriers. Taking a few mo-ments to measure shim packs and gear tooth contact patterns on disassembly can save considerable time when reassembling thec arrier.• A crown and pinion gear set often can ber eused when rebuilding a differential carrier. Make sure that you inspect it properly ond isassembly.• Crown and pinion gear sets are always replaced as a matched pair during a rebuild.• When setting crown and pinion backlash, it is increased by moving the crown gear away from the drive pinion and decreased by moving the crown gear toward the drive pinion.• Adhering to OEM-recommended lubrication schedules is the key to ensuring the longest service life from both drive and dead axles.• Knowing the correct procedure to check lubricant level is essential. The level is correct when lubri-cant is exactly level with the bottom of the fill hole.• Because most OEMs approve of the use of syn-thetic lubricants in final drive carriers, lubrication drain schedules have been greatly increased in recent years. Drain schedules are determined by the actual lubricant used and the type of appli-cation to which the vehicle is subjected.• Servicing of axles on heavy-duty trucks consists of routine inspection, lubrication, cleaning, and, when required, troubleshooting and component overhaul.• Failure analysis is required to prevent recurrent failures.• Drive axle carrier components usually fail for one of the following reasons: Shock load Fatigue Spinout Lubrication problemsNormal wearFIGURE 24–74 Installing the jam nut on the thrust screw. (Courtesy of Arvin Meritor)FIGURE 24–75 Tighten the jam nut to the correct torque value. (Courtesy of Arvin Meritor)SUMMARY。