各种位置的焊接方法(修)
铸铁零件的常用焊接方法
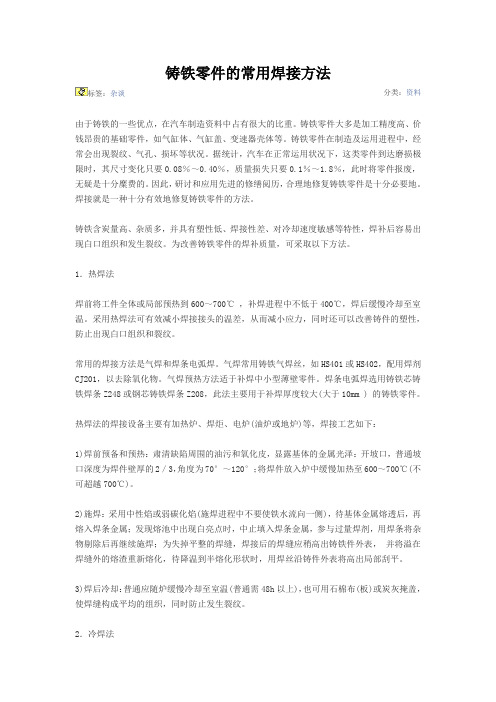
铸铁零件的常用焊接方法标签:杂谈分类:资料由于铸铁的一些优点,在汽车制造资料中占有很大的比重。
铸铁零件大多是加工精度高、价钱昂贵的基础零件,如气缸体、气缸盖、变速器壳体等。
铸铁零件在制造及运用进程中,经常会出现裂纹、气孔、损坏等状况。
据统计,汽车在正常运用状况下,这类零件到达磨损极限时,其尺寸变化只要0.08%~0.40%,质量损失只要0.1%~1.8%,此时将零件报废,无疑是十分糜费的。
因此,研讨和应用先进的修缮阅历,合理地修复铸铁零件是十分必要地。
焊接就是一种十分有效地修复铸铁零件的方法。
铸铁含炭量高、杂质多,并具有塑性低、焊接性差、对冷却速度敏感等特性,焊补后容易出现白口组织和发生裂纹。
为改善铸铁零件的焊补质量,可采取以下方法。
1.热焊法焊前将工件全体或局部预热到600~700℃,补焊进程中不低于400℃,焊后缓慢冷却至室温。
采用热焊法可有效减小焊接接头的温差,从而减小应力,同时还可以改善铸件的塑性,防止出现白口组织和裂纹。
常用的焊接方法是气焊和焊条电弧焊。
气焊常用铸铁气焊丝,如HS401或HS402,配用焊剂CJ201,以去除氧化物。
气焊预热方法适于补焊中小型薄壁零件。
焊条电弧焊选用铸铁芯铸铁焊条Z248或钢芯铸铁焊条Z208,此法主要用于补焊厚度较大(大于10mm ) 的铸铁零件。
热焊法的焊接设备主要有加热炉、焊炬、电炉(油炉或地炉)等,焊接工艺如下:1)焊前预备和预热:肃清缺陷周围的油污和氧化皮,显露基体的金属光泽:开坡口,普通坡口深度为焊件壁厚的2/3,角度为70°~120°;将焊件放入炉中缓慢加热至600~700℃(不可超越700℃)。
2)施焊:采用中性焰或弱碳化焰(施焊进程中不要使铁水流向一侧),待基体金属熔透后,再熔入焊条金属;发现熔池中出现白亮点时,中止填入焊条金属,参与过量焊剂,用焊条将杂物剔除后再继续施焊;为失掉平整的焊缝,焊接后的焊缝应稍高出铸铁件外表,并将溢在焊缝外的熔渣重新熔化,待降温到半熔化形状时,用焊丝沿铸件外表将高出局部刮平。
管道各种位置焊接操作工艺技术指南

管道各种位置焊接操作工艺技术指南(一)、水平固定管电弧焊接工艺1、管子对接焊缝只能单面焊双面成型,必须从工艺上保证根层焊缝的焊透,但又不能产生内凹和焊瘤。
2、由于焊接位置的不断变化,运条角度和焊工站立的高度必须适应变化的要求。
3、焊接热分布的规律是,上面的温度比下面高,应设置近前电阻式电流调节电器,但在焊接电流不能调正的情况下,主要靠摆动焊条来控制热量,达到均匀熔化的目的。
4、应选用有操作经验,证、质相当的焊工施焊。
5、操作技术点焊前应预先试好电流,然后检查对口是否符合要求,无误时方可点焊。
点焊使用的工艺应与正式焊接相同,一般点焊1-2点,点焊在水平或斜平焊位置上,长度为10-15mm,高度2-3mm,点焊后两端应修成缓坡形,以保持接头质量。
第一层的焊接:第一层的焊缝是决定焊接质量的关键。
采用击穿焊接法,即将钝边熔化,以保证焊缝焊透。
当对口间隙过大时,也可采用渗透法焊接,但必须焊透。
根据水平固定管的焊接特点,第一层仰焊位置采用直线运条法,平立焊位置可稍做摆动或灭弧来控制熔池温度。
每一层焊缝分两个半圆,先焊的一半称前半部,后焊的一半称后半部。
先焊一半的起头和收尾,焊到起过中心线约10-15mm,如图。
后焊的一半起头和收尾都要盖过前半的起头和收尾。
焊接从仰焊位置开始,按仰、立、平的焊接顺序进行焊接,随着焊接位置的不断变化,焊条角度也必须相应的变化,如图。
焊接时在坡口内引弧,采用酸性焊条焊接,引弧后拉长电弧预热2-3秒钟,待坡口两侧接近熔化状态,立即在低电弧开始焊接,给第一滴铁水,当铁水在坡口内形成熔池,将焊条抬起断弧,当熔池温度下降,熔池变小,再焊接形成第二个熔池,如此循环一直向前焊接。
焊接关键是要控制熔池的温度,也就是要控制电弧在熔池内停留的时间。
即要保证焊透,熔合良好,又要使铁水不往下落。
当采用碱性低氢型焊条焊接时,要直流反接,短弧操作。
引弧后就要给铁水进行焊接。
后半部焊接与前半部相同,但下接头、上收头难度较大,后半部起焊前先将接头处修成缓坡形,或用电弧接头处熔掉一部分形成缓坡状,然后再击穿焊接。
各种焊接方法的原理、特点及应用

7)中间不能停焊
电渣焊设备及电源特性
电渣焊设备主要为: 1)焊接电源 2)机头及行走机构、送丝机构、摆动机构 3)焊接过程自动调节及电控系统 4)成型块(一般纯铜制成)
电渣焊(ESW,72)
电渣焊原理
是利用电流通过液态熔渣时产生的电阻热作为 焊接热源,将工件和填充金属熔合成焊缝的垂直 位置的焊接方法。
电渣焊过程包括引弧造渣、正常焊接、引出三个 阶段。
电渣焊原理示意图
出水 进水
1工件 2金属熔池 3渣池 4导电嘴 5焊丝 6成型装置7引出板 8 金属熔滴 9 焊缝 10引弧板 11送丝轮 12焊接电源
焊带送进及校正
焊剂斗
ቤተ መጻሕፍቲ ባይዱ导电块
熔渣 焊渣(5mm)
焊道厚度(5mm)
熔敷金属
导电的液体熔渣厚度 焊剂堆高(30-40mm)
焊接方向
熔深(0.3-0.5mm)
3)电渣压力焊
铝热焊
铝热焊原理及设备
铝热焊是利用金属氧化物与铝之间的化学反应 所产生的热量,熔融金属来加热工件和填充接头 完成的一种方法。 常用的氧化剂有Fe2O3、CuO、MnO,还原剂Al。
螺柱焊应用
螺柱焊可以代替铆接或钻孔螺丝紧固等,广泛用 于汽车、造船、机车、机械、锅炉、容器、建筑、民 用等行业。
钢结构(φ22mm) 容器(φ12mm) 家用电器(φ6mm)
螺柱焊缺陷
螺柱焊质量检查
弯曲大于60° 螺柱在拉力作用下断裂 钢板上的拉断面(钢板厚度(6mm)
采用机械负荷对螺柱焊检验实例
除高频焊钢管外,还可以有其它形式的联接, 高频中间滑动接触焊如图。
电脑维修的焊接技术
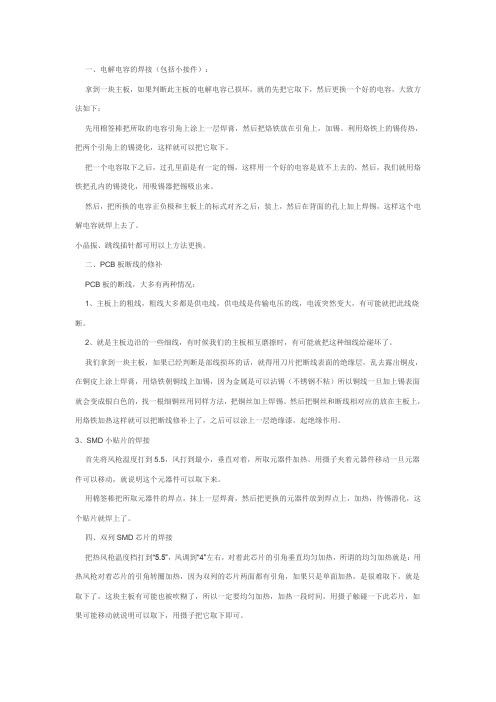
一、电解电容的焊接(包括小接件):拿到一块主板,如果判断此主板的电解电容已损坏,就的先把它取下,然后更换一个好的电容,大致方法如下:先用棉签棒把所取的电容引角上涂上一层焊膏,然后把烙铁放在引角上,加锡。
利用烙铁上的锡传热,把两个引角上的锡烫化,这样就可以把它取下。
把一个电容取下之后,过孔里面是有一定的锡,这样用一个好的电容是放不上去的,然后,我们就用烙铁把孔内的锡烫化,用吸锡器把锡吸出来。
然后,把所换的电容正负极和主板上的标式对齐之后,装上,然后在背面的孔上加上焊锡,这样这个电解电容就焊上去了。
小晶振、跳线插针都可用以上方法更换。
二、PCB板断线的修补PCB板的断线,大多有两种情况:1、主板上的粗线,粗线大多都是供电线,供电线是传输电压的线,电流突然变大,有可能就把此线烧断。
2、就是主板边沿的一些细线,有时候我们的主板相互磨擦时,有可能就把这种细线给碰坏了。
我们拿到一块主板,如果已经判断是部线损坏的话,就得用刀片把断线表面的绝缘层,乱去露出铜皮,在铜皮上涂上焊膏,用烙铁朝铜线上加锡,因为金属是可以沾锡(不锈钢不粘)所以铜线一旦加上锡表面就会变成银白色的,找一根细铜丝用同样方法,把铜丝加上焊锡。
然后把铜丝和断线相对应的放在主板上,用烙铁加热这样就可以把断线修补上了,之后可以涂上一层绝缘漆,起绝缘作用。
3、SMD小贴片的焊接首先将风枪温度打到5.5,风打到最小,垂直对着,所取元器件加热。
用摄子夹着元器件移动一旦元器件可以移动,就说明这个元器件可以取下来。
用棉签棒把所取元器件的焊点,抹上一层焊膏,然后把更换的元器件放到焊点上,加热,待锡溶化,这个贴片就焊上了。
四、双列SMD芯片的焊接把热风枪温度档打到“5.5”,风调到“4”左右,对着此芯片的引角垂直均匀加热,所谓的均匀加热就是:用热风枪对着芯片的引角转圈加热,因为双列的芯片两面都有引角,如果只是单面加热,是很难取下,就是取下了,这块主板有可能也被吹糊了,所以一定要均匀加热,加热一段时间,用摄子触碰一下此芯片,如果可能移动就说明可以取下,用摄子把它取下即可。
电子元器件维修焊接操作方法甄选范文.

电子元器件维修焊接操作方法1. 准备工具:烙铁、焊锡丝、松香/助焊剂、热风枪、镊子2. 烙铁使用方法:1) 根据各种电子元件耐温属性调节好烙铁温度;2)用烙铁对维修部位加热(预热),时间为1-2秒,目的是减少锡飞溅;3)用锡丝对修理部位进行加锡;4)锡完全溶化后将锡线移开;5)焊接完后,检查焊锡的质量,每个焊点明亮而光滑,无对周边元件造成第二次不良。
3. 热风枪使用方法:一般使用热风枪拆卸多引脚的插件、大型IC 芯片及无法用烙铁拆卸的特殊元器件等。
1) 使用热风枪取元器件时调节温度要适合; 单面板为300-330℃之间,双面板/直插元件为350-380 ℃之间;高温区360℃--390 ℃;2) 用热风枪的喷嘴对着要取下的元件来回均匀移动加热,时间控制好,单面板为3-6S ;双面板5-10S ;使锡完全溶化。
在取多PIN 脚IC 时,时间会长一些,但要仔细观察部品和铜箔变化 发现有变色和烧焦/起泡时应停止作业。
3) 用镊子将元件取出,将热风机的喷嘴移开。
4. 焊接时间与温度烙铁/热风枪 部品类别温度 单个锡 点时间SMT 工程 CHIP 元件 340±10℃2~5S SMT 工程 IC 元件 350±10℃ 2~5S烙铁与电路板成45度角 采用握笔式拿法5.IC类维修焊接方法IC类芯片多PIN脚且PIN脚间距较小,焊接时一定要格外注意。
维修步骤:●对IC-PIN脚连锡位置涂抹少许助焊剂;(图一)●清洁烙铁头:使用清洁棉擦拭烙铁头上的余锡,注意:烙铁头上不能附锡,维修时会粘附到IC-PIN上形成短路. (图二)●针对IC连锡PIN采用点焊的方式维修,烙铁头切面平压在电路板上涂助焊剂的位置,给IC PIN加热,然后平行PIN脚向外侧移动烙铁头,吸走形成短路的余锡(图三)注意:①不采用拖焊方法维修,是因为IC铜箔较长(L=2mm),装上IC后,铜箔内部还有1.0mm的空隙;在拖焊时加锡量会附着在IC内部连锡.●维修完毕,目测自检。
各种焊接方法介绍
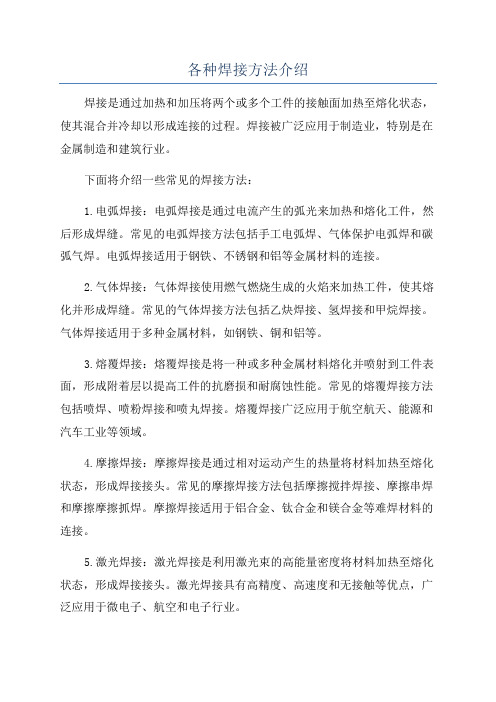
各种焊接方法介绍焊接是通过加热和加压将两个或多个工件的接触面加热至熔化状态,使其混合并冷却以形成连接的过程。
焊接被广泛应用于制造业,特别是在金属制造和建筑行业。
下面将介绍一些常见的焊接方法:1.电弧焊接:电弧焊接是通过电流产生的弧光来加热和熔化工件,然后形成焊缝。
常见的电弧焊接方法包括手工电弧焊、气体保护电弧焊和碳弧气焊。
电弧焊接适用于钢铁、不锈钢和铝等金属材料的连接。
2.气体焊接:气体焊接使用燃气燃烧生成的火焰来加热工件,使其熔化并形成焊缝。
常见的气体焊接方法包括乙炔焊接、氢焊接和甲烷焊接。
气体焊接适用于多种金属材料,如钢铁、铜和铝等。
3.熔覆焊接:熔覆焊接是将一种或多种金属材料熔化并喷射到工件表面,形成附着层以提高工件的抗磨损和耐腐蚀性能。
常见的熔覆焊接方法包括喷焊、喷粉焊接和喷丸焊接。
熔覆焊接广泛应用于航空航天、能源和汽车工业等领域。
4.摩擦焊接:摩擦焊接是通过相对运动产生的热量将材料加热至熔化状态,形成焊接接头。
常见的摩擦焊接方法包括摩擦搅拌焊接、摩擦串焊和摩擦摩擦抓焊。
摩擦焊接适用于铝合金、钛合金和镁合金等难焊材料的连接。
5.激光焊接:激光焊接是利用激光束的高能量密度将材料加热至熔化状态,形成焊接接头。
激光焊接具有高精度、高速度和无接触等优点,广泛应用于微电子、航空和电子行业。
6.点焊:点焊是通过施加电流和压力将材料加热至熔化状态,然后形成焊点连接。
点焊适用于金属薄板的连接,常见于汽车制造和电子行业。
7.水下焊接:水下焊接是在水下环境中进行的焊接,主要用于海洋工程和船舶修理等领域。
水下焊接常通过深海潜水员或水下焊接机器人进行。
总结起来,焊接是将材料通过热加工的方法连接在一起的过程。
不同的焊接方法适用于不同类型的材料和应用领域。
随着技术的不断发展,新的焊接方法也在不断涌现,为制造业和建筑行业带来了许多创新和便利。
手工焊接方法及技巧
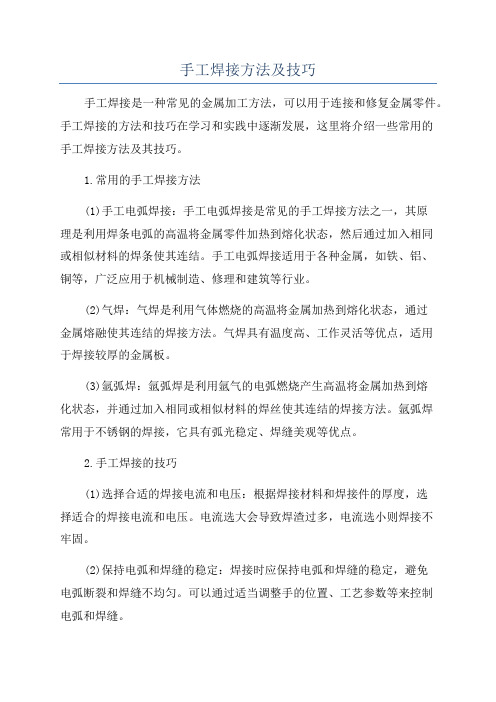
手工焊接方法及技巧手工焊接是一种常见的金属加工方法,可以用于连接和修复金属零件。
手工焊接的方法和技巧在学习和实践中逐渐发展,这里将介绍一些常用的手工焊接方法及其技巧。
1.常用的手工焊接方法(1)手工电弧焊接:手工电弧焊接是常见的手工焊接方法之一,其原理是利用焊条电弧的高温将金属零件加热到熔化状态,然后通过加入相同或相似材料的焊条使其连结。
手工电弧焊接适用于各种金属,如铁、铝、铜等,广泛应用于机械制造、修理和建筑等行业。
(2)气焊:气焊是利用气体燃烧的高温将金属加热到熔化状态,通过金属熔融使其连结的焊接方法。
气焊具有温度高、工作灵活等优点,适用于焊接较厚的金属板。
(3)氩弧焊:氩弧焊是利用氩气的电弧燃烧产生高温将金属加热到熔化状态,并通过加入相同或相似材料的焊丝使其连结的焊接方法。
氩弧焊常用于不锈钢的焊接,它具有弧光稳定、焊缝美观等优点。
2.手工焊接的技巧(1)选择合适的焊接电流和电压:根据焊接材料和焊接件的厚度,选择适合的焊接电流和电压。
电流选大会导致焊渣过多,电流选小则焊接不牢固。
(2)保持电弧和焊缝的稳定:焊接时应保持电弧和焊缝的稳定,避免电弧断裂和焊缝不均匀。
可以通过适当调整手的位置、工艺参数等来控制电弧和焊缝。
(3)控制焊条的垂直角度和推力:焊条的垂直角度和推力会影响电弧的稳定性和焊缝的质量。
垂直角度大于90度可以产生较深的焊缝,但会导致熔渣嵌入焊缝中。
推力过大会导致焊缝凹陷,推力过小会导致焊条离开焊缝。
(4)控制焊接速度:焊接速度对焊缝的质量有很大影响。
焊接速度过快会导致焊缝凹陷和质量不好,速度过慢会导致过度熔化和熔渣残留。
(5)定期修整焊条:焊条在使用过程中会产生氧化皮和熔渣,应定期使用砂轮或剪刀修整焊条,以保持焊条的良好导电性和焊接质量。
(6)做好焊后处理:焊接完成后要进行焊后处理,包括修整焊缝、清除熔渣和清洁工件等。
这样可以提高焊接质量和外观。
总之,手工焊接是一项需要技巧和经验的工艺,通过选择合适的焊接方法和掌握焊接技巧,可以实现高质量的焊接。
焊接方法介绍范文
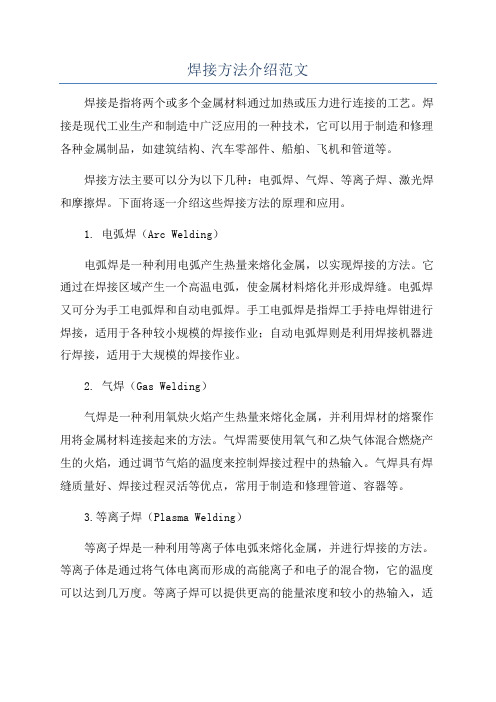
焊接方法介绍范文焊接是指将两个或多个金属材料通过加热或压力进行连接的工艺。
焊接是现代工业生产和制造中广泛应用的一种技术,它可以用于制造和修理各种金属制品,如建筑结构、汽车零部件、船舶、飞机和管道等。
焊接方法主要可以分为以下几种:电弧焊、气焊、等离子焊、激光焊和摩擦焊。
下面将逐一介绍这些焊接方法的原理和应用。
1. 电弧焊(Arc Welding)电弧焊是一种利用电弧产生热量来熔化金属,以实现焊接的方法。
它通过在焊接区域产生一个高温电弧,使金属材料熔化并形成焊缝。
电弧焊又可分为手工电弧焊和自动电弧焊。
手工电弧焊是指焊工手持电焊钳进行焊接,适用于各种较小规模的焊接作业;自动电弧焊则是利用焊接机器进行焊接,适用于大规模的焊接作业。
2. 气焊(Gas Welding)气焊是一种利用氧炔火焰产生热量来熔化金属,并利用焊材的熔聚作用将金属材料连接起来的方法。
气焊需要使用氧气和乙炔气体混合燃烧产生的火焰,通过调节气焰的温度来控制焊接过程中的热输入。
气焊具有焊缝质量好、焊接过程灵活等优点,常用于制造和修理管道、容器等。
3.等离子焊(Plasma Welding)等离子焊是一种利用等离子体电弧来熔化金属,并进行焊接的方法。
等离子体是通过将气体电离而形成的高能离子和电子的混合物,它的温度可以达到几万度。
等离子焊可以提供更高的能量浓度和较小的热输入,适用于焊接高熔点金属和薄板材料。
等离子焊常用于航空航天、电子、光学等领域。
4. 激光焊(Laser Welding)激光焊是一种利用高能激光束来熔化金属,并进行焊接的方法。
激光束具有高能量密度和高定向性的特点,可以使焊缝快速熔化并形成焊接连接。
激光焊的热影响区域小,焊接速度快,适用于精密焊接和复杂结构的焊接作业。
激光焊广泛应用于汽车工业、电子工业和医疗器械等领域。
5. 摩擦焊(Friction Welding)摩擦焊是一种将两个金属材料通过摩擦热量熔化并连接起来的方法。
摩擦焊将两个金属材料相对运动,使它们发生摩擦,摩擦产生的热量将材料加热熔化并形成焊缝,然后通过施加压力使金属材料连接起来。
- 1、下载文档前请自行甄别文档内容的完整性,平台不提供额外的编辑、内容补充、找答案等附加服务。
- 2、"仅部分预览"的文档,不可在线预览部分如存在完整性等问题,可反馈申请退款(可完整预览的文档不适用该条件!)。
- 3、如文档侵犯您的权益,请联系客服反馈,我们会尽快为您处理(人工客服工作时间:9:00-18:30)。
各种位置的焊接方法
平焊
平焊时,由于焊缝处在水平位置,熔滴主要靠自重自然过渡,所以操作比较容易,允许用较大直径的焊条和较大的电流,故生产率高。
如果参数选择及操作不当,容易在根部形成未焊透或焊瘤。
运条及焊条角度不正确时,熔渣和铁水易出现混在一起分不清的现象,或熔渣超前形成夹渣。
平焊又分为平对接焊和平角接焊。
1.平对接焊
(1)不开坡口的平对接焊
当焊件厚度小于6mm时,一般采用不开坡口对接。
焊接正面焊缝时,宜用直径为3~4mm的焊条,采用短弧焊接,并应使熔深达到板厚的2/3,焊缝宽度为5~8mm,余高应小于1.5mm,如图2-1所示。
对不重要的焊件,在焊接反面的封底焊缝前,可不必铲除焊根,但应将正面焊缝下面的熔渣彻底清除干净,然后用3mm焊条进行焊接,电流可以稍大些。
焊接时所用的运条方法均为直线形,焊条角度如图2-2所示。
在焊接正面焊缝时,运条速度应慢些,以获得较大的熔深和宽度;焊反面封底焊缝时,则运条速度要稍快些,以获得较小的焊缝宽度。
图2-2平面对接焊的焊条角度
运条时,若发现熔渣和铁水混合不清,即可把电弧稍微拉长一些,同时将焊条向前倾斜,并往熔池后面推送熔渣,随着这个动作,熔渣就被推送到熔池后面去了,如图2-3所示。
图2-3 推送熔渣的方法
3
2
1
4
图2-4 对接多层焊
(2)开坡口的平对接焊
当焊件厚度等于或大于6mm时,因为电弧的热量很难使焊缝的根部焊透,所以应开坡口。
开坡口对接接头的焊接,可采用多层焊法(图2-4)或多层多道焊法(图2-5)。
1
2
34
56
789
101112
图2-5 对接多层多道焊
多层焊时,对第一层的打底焊道应选用直径较小的焊条,运条方法应以间隙大小而定,当间隙小时可用直线形,间隙较大时则采用直线往返形,以免烧穿。
当间隙很大而无法一次焊成时,就采用三点焊法(图2-6)。
先将坡口两侧各焊上一道焊缝(图2-6中1、2),使间隙变小,然后再进行图2-6中缝3的敷焊,从而形成由焊缝1、2、3共同组成的一个整体焊缝。
但是,在一般情况下,不应采用三点焊法。
3
12
图2-6 三点焊法的施焊次序
在焊第二层时,先将第一层熔渣清除干净,随后用直径较大的焊条和较大的焊接电流进行焊接。
用直线形、幅度较小的月牙形或锯齿形运条法,并应采用短弧焊接。
以后各层焊接,均可采用月牙形或锯齿形运条法,不过其摆动幅度应随焊接层数的增加而逐渐加宽。
焊条摆动时,必须在坡口两边稍作停留,否则容易产生边缘熔合不良及夹渣等缺陷。
为了保证质量和防止变形,应使层与层之间的焊接方向相反,焊缝接头也应相互错开。
多层多道焊的焊接方法与多层焊相似,所不同的是因为一道焊缝不能达到所要求的宽度,而必须由数条窄焊道并列组成,以达到较大的焊缝宽度(图2-5)。
焊接时采用直线形运条法。
在采用低氢型焊条焊接平面对接焊缝时,除了焊条一定要按规定烘干外,焊件的焊接处必须彻底清除油污、铁锈、水分等,以免产生气孔。
在操作时,一定要采用短弧,以防止空气侵入熔池。
运条法宜采用月牙形,可使熔池冷却速度缓慢,有利于焊缝中气体的逸出,以提高焊缝质量。
2.平角接焊
平角接焊主要是指T形接头平焊和搭接接头平焊,搭接接头平焊和T形接头平焊的操作方法类似,所以这里不作单独介绍。
T形接头平焊在操作时易产生咬边、未焊透、焊脚下偏(下垂)、夹渣等缺陷,如图2-7所示。
下垂
咬边
图2-7 T形接头平焊在
操作时易产生的缺陷
为了防止上述缺陷,操作时除了正确选择焊接参数外,还必须根据两板的厚度来调节焊条的角度。
如果焊接两板厚度不同的焊缝时,
电弧就要偏向于厚板的一边,使两板的温度均匀。
常用焊条角度如图2-8所示。
图2-8 T形接头焊接时的角度
T形接头的焊接除单层焊外也可采用多层焊或多层多道焊,其焊接方法如下。
(1)单层焊焊脚尺寸小于8mm的焊缝,通常采用单层焊(一层一道焊缝)来完成,焊条直径根据钢板厚度不同在3~5mm范围内选择。
焊脚尺寸小于5mm的焊缝,可采用直线形运条法和短弧进行焊接,焊接速度要均匀,焊条角度与水平板成45°,与焊接方向成65°~80°的夹角。
焊条角度过小会造成根部熔深不足;角度过大,熔渣容易跑到前面造成夹渣。
在使用直线形运条法焊接焊脚尺寸不大的焊缝时,将焊条端头的套管边缘靠在焊缝上,并轻轻地压住它,当焊条熔化时,会逐渐沿着焊接方向移动。
这样不但便于操作,而且熔深较大,焊缝外表也美观。
焊脚尺寸在5~8mm时,可采用斜圆圈形或反锯齿形运条法进行焊接,但运条速度不同,否则容易产生咬边、夹渣、边缘熔合不良等现象。
正确的运条方法如图2-9所示,a点至b点运条速度要稍慢些,以保证熔化金属与水平板很好熔合;b点至c点的运条速度要稍快些,以防止熔化金属下淌,当从b点运条到c点时,在c点要稍作停留,以保证熔化金属与垂直板很好熔合,并且还能避免产生咬边现象,c点至b点的运条速度又要稍慢些,才能避免产生夹渣现象及保证根部焊透;b点至d点的运条速度与a点至b点一样要稍慢些;d点至e点与b点至c点相同,e点与c点相同,要稍作停留。
整个运条过程就是不断重复上述过程。
同时在整个运条过程中,都应采用短弧焊接。
这样所得的焊缝才能宽窄一致,高低平整,不产生咬边、夹渣、下垂等缺陷。
图2-9 平角焊的圆圈形运条
在T形接头平焊的焊接过程中,往往由于收尾弧坑未填满而产生裂缝。
所以在收尾时,一定要保证弧坑填满,具体措施可参阅焊缝收尾法。
(2)多层焊焊脚尺寸在8~10mm时,可采用两层两道的焊法。
焊第一层时,可采用3~4mm直径的焊条,焊接电流稍大些,以获得较大的熔深。
采用直线形运条法,在收尾时应把弧坑填满或略高些,这样在焊接第二次收尾时,不会因焊缝温度增高而产生弧坑过低的现象。
在焊第二层之前,必须将第一层的熔渣清除干净,如发现有夹渣,应用小直径焊条修补后方可焊第二层,这样才能保证层与层之间紧密的熔合。
在焊第二层时,可采用4mm 直径的焊条,焊接电流不宜过大,电流过大会产生咬边现象。
用斜圆圈形或反锯齿形运条法施焊,具体运条方法与单层焊相同。
但是第一层焊缝有咬边时,在第二次焊接时,应在咬边处适当多停留一些时间,以弥补第一层咬边的缺陷。
(3)多层多道焊当焊接焊脚尺寸大于10mm的焊缝时,如果采用多层焊,则由于焊缝表面较宽,坡度较大,熔化金属容易下垂,给操作带来一定的困难。
所以在实际生产中都采用多层多道焊。
焊脚尺寸为10~12mm时,一般用两层三道来完成。
焊第一层(第一道)时,可采用较小直径的焊条及较大焊接电流,用直线形运条法,收尾与多层焊的第一层相同。
焊完后将熔渣清除干净。
焊第二道焊缝时,应覆盖不小于第一层焊缝的2/3,焊条与水平板的角度要稍大些(图2-10中a),一般为45°~55°,以使熔化金属与水平板很好熔合。
焊条与焊接方向的夹角仍为65°~80°,用斜圆圈形或反锯齿形运条,运条速度除了在图2-9中的c点、e点上不需停留之外,其他都一样。
焊接时应注意熔化金属与水平板要很好熔合。
a
b
图2-10 多层
多道焊的焊条角度
焊接第三道焊缝时,应覆盖第二道焊缝的1/3~1/2。
焊条与水平板的角度为40°~45°(图2-10中的b),角度太大易产生焊脚下偏现象。
一般采用直线形运条法,焊接速度要均匀,不宜太慢,因为速度慢了容易产生焊瘤,
使焊缝成形不美观。
如果发现第二道焊缝覆盖第一层大于2/3时,在焊接第三道时可采用直线往复运条法,以避免第三道焊缝过高。
如果第二道覆盖第一道太少时,第三道焊接时可采用斜圆圈运条法,运条时在垂直板上要稍作停留,以防止咬边,这样就能弥补由于第二道覆盖过少而产生的焊脚下偏现象。
如果焊接焊脚尺寸大于12mm 以上的焊件时,可采用三层六道、四层十道来完成,如图2-11所示。
焊脚尺寸越大,焊接层数、道数就越多。
12
345
612
345678
9
10
图2-11多层多道焊的
焊道排列
在实际生产中,如果焊件能翻动时,应尽可能把焊件放成图2-12所示船形位置进行焊接,这种位置是最佳的焊接位置。
因为船形焊时,能避免产生咬边、下垂等缺陷,而且操作方便,易获得平整美观的焊缝,同时,有利于使用大
直径焊条和大电流,不但能获得较大的熔深,而且能一次焊成较大断面的焊缝,能大大提高生产率。
采用船形焊时,运条采用月牙形或锯齿形运条法。
焊接第一层采用小直径焊条及稍大电流,其他各层与开坡口平对接焊相似。
图12 船形焊。