ISO9001-2015产品首件鉴定程序A0
ISO9001-2015IPQC首检巡检规范A0
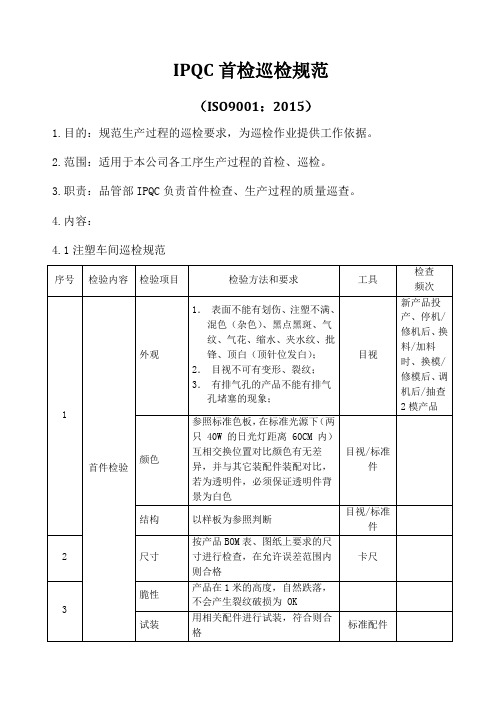
检测标准
未注明公差执行:
ISO13920-□A□B□E□F ISO2768-□f■m□H■K
□其它
检测记录
序号
检测坐标/项点
图纸要求/
技术要求
公差要求
检测方法
实测结果
判定
1
总长度
263
±0.5
卷尺
□合格□不合格
2
板厚
2
±0.08
千分尺
□合格□不合格
3
断面高度
20
0,-0.3
高度尺
□合格□不合格
标准配件
4.2
序号
工序
检验项目
检验方法和要求
工具
检查
频次
1
首件检验
外观
颜色
1.比对标准件,涂层颜色应与样板相符;
2.目视涂层表面不允许有涂层不均匀,露底色,混色,划伤,起皮,橙皮,飞油,印字/图案缺划,印字/图案歪斜;
3.喷印位置应与样板一致,不得偏斜。
目视/标准件
刚开始生产时、换料/加料时、调机/修机后/抽查10个产品
2.目视不可有变形、裂纹;
3.有排气孔的产品不能有排气孔堵塞的现象;
目视
新产品投产、停机/修机后、换料/加料时、换模/修模后、调机后/抽查2模产品
颜色
参照标准色板,在标准光源下(两只40W的日光灯距离60CM内)互相交换位置对比颜色有无差异,并与其它装配件装配对比,若为透明件,必须保证透明件背景为白色
不允许有大于厚度5%的轻微凹凸、压痕
目测、深度尺
□合格□不合格
11
主视图尺寸
75
±0.5
卷尺
□合格□不合格
IPQC
(
ISO9001-2015首件自检专检质量控制程序

首件自检专检质量控制程序(ISO9001:2015)1 范围本程序规定了产品首件自检专检的控制要求。
本程序适用于产品生产过程中首件。
2 职责2.1 生产单位负责识别需自检专检的首件,并负责首件自检。
2.2 检验部门负责首件专检。
3 工作程序3.1 对由模具保证的冲压、锻造及机械加工、焊接工序,根据产品特性及加工要求,由生产单位确定本单位需进行首件自检专检工序,并列出首件自检专检工序目录,关键件、重要件必须执行首件自检专检。
3.2 首件自检专检工序目录检验部门一份,生产单位自存一份。
3.3 首件自检专检的工序,符合以下情况之一,必须对首件实行自检、专检。
a)每个工作班开始;b)更换操作者;c)更换或调整设备、工艺装备;d)更换技术文件、工艺方法、工艺参数;e)采用新标准;f)采用新材料或材料代用;g)更换或重新化验槽液、渗透液等;h)操作者加工前应检查工序过程受控状态,确保符合下列条件;i)产品图、技术文件、工艺规程、检验规程等应是现行有效版本;j)材料符合工艺规程、技术条件的要求;k)工、夹、量、模具、测试设备和机床符合工艺规程要求。
3.4 首件产品应检验以下内容:a)首件的技术文件是否正确、完整、有效;b)首件是否符合图样和技术文件的要求;c)加工首件的工艺装备和检验用的计量器具是否符合规定要求;d)首件生产环境是否符合要求;e)生产首件的操作者是否持证上岗。
3.5 每个班次开始生产的第一个工件首先由操作者自检,合格后在首件自检专检卡片上填写检验记录,而后提请专检人员检验确认是否合格并填写检验记录。
3.6 首件自检专检是鉴定过程能力,确定是否能批量生产。
首件自检、专检合格后,方可连续生产,如首件经检验不合格,应从人、机、料、法、环、测等方面查找原因,采取纠正措施后,再生产第二件产品,继续实施首件自检、专检,直至合格,方可连续生产。
3.7 对经过检验合格的首件应标记“首件合格”,单独存放,待所在批次产品加工完毕后,方可随所在批产品放行。
ISO9001-2015首件确认程序
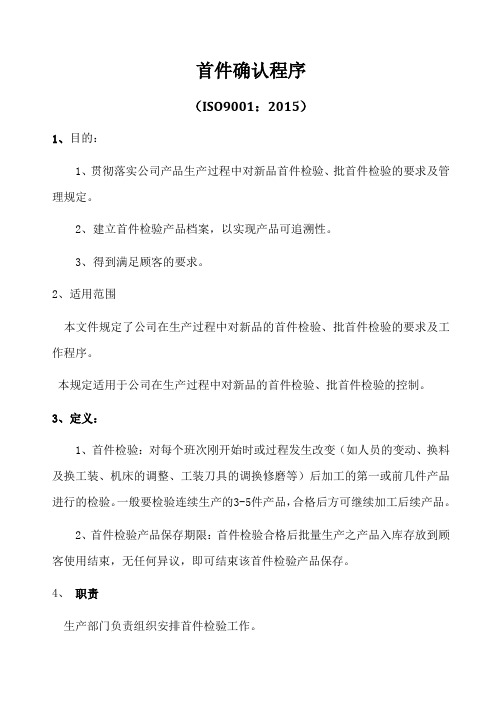
首件确认程序(ISO9001:2015)1、目的:1、贯彻落实公司产品生产过程中对新品首件检验、批首件检验的要求及管理规定。
2、建立首件检验产品档案,以实现产品可追溯性。
3、得到满足顾客的要求。
2、适用范围本文件规定了公司在生产过程中对新品的首件检验、批首件检验的要求及工作程序。
本规定适用于公司在生产过程中对新品的首件检验、批首件检验的控制。
3、定义:1、首件检验:对每个班次刚开始时或过程发生改变(如人员的变动、换料及换工装、机床的调整、工装刀具的调换修磨等)后加工的第一或前几件产品进行的检验。
一般要检验连续生产的3-5件产品,合格后方可继续加工后续产品。
2、首件检验产品保存期限:首件检验合格后批量生产之产品入库存放到顾客使用结束,无任何异议,即可结束该首件检验产品保存。
4、职责生产部门负责组织安排首件检验工作。
1、未经新品首件、批首件检验或首件检验不合格,而擅自生产产品,由此引起的质量事故,由直接责任者负责。
3、检验员、生产线负责人对首件检验的正确性负责。
4、对首件确认工作未完成,检验员开始出具质量凭证,造成的质量事故责任由检验员负责。
5、控制要求1、对生产部门首次连续性生产的第一个完工的半成品和成品,必须经过首件检验和确认。
2 、对于常规生产产品,须按批次进行首件检验。
3、由于设备、工艺等原因造成的停机,停机再开机时要进行首件检验和确认。
4、产品材料、规格变更后投入生产时要进行首件检验和确认。
5、新品首件检验时,应由生产单位负责通知检验有关人员,按现行有效的图纸、清单(或顾客提供的样件)、工艺文件进行,检验员填写检验记录,检验合格后在首件卡上签字,并将卡片挂在首件产品上做好首件标记;首件检验不合格应立即退回,重做首件,并做好记录。
未经首件检验合格的产品不得进行验收。
6、首件作为批量生产的样件,由生产部门负责保留到全批生产结束后才能最后送交。
7、首件检验中应检查产品生产过程所用的所有原辅材料必须与规定相符。
ISO9001-2015首件确认作业指导书

首件确认作业指导书(ISO9001:2015)1.目的对生产新订单的首件产品进行检验,防止批量性的问题出现,保证生产产品的质量2.适用范围适用新订单生产前的产品。
3.职责生产部:负责首样的制作、自检、签名确认及送检的工作。
品质部:负责根据工厂订单、生产通知单核对资料、检验性能。
工程部:负责核对首样是否与BOM一致。
4.作业流程生产部:1、接到新订单产品时,由拉长按工厂订单及生产通知单制作首件2、根据工厂订单及生产通知单核对资料进行自检,并在首件检验报告中填写订单号、机型、颜色、线别、首件数量、送检日期与时间且签名确认3、自检完毕后,将产品连同首样检验报告一并送至品质部交给PQA进行复检品质部:1、在接到生产部的首件样品后,按照成品检验作业指导书进行外观及性能检测2、按照包材资料核对铭牌、彩盒、外箱、说明书、保修卡的信息3、按照工厂订单及生产通知单核对包装方式及客户特要求的注意事项4、检验、核对完毕后,按照首样检验报告的项目进行签字确认,然后将产品与首样检验报告一并送至工程部交给PE进行复查工程部:1、在接到品质部的首件样品后,按照BOM表核对首件是否与BOM 表一致2、按照工厂订单及生产通知单对首件进行复查3、核对完毕后,在首样检验报告中的“PCBA板的型号”、“电源线厂家及规格”、“发热丝厂家及规格”、“各部件结构是否符合标准”的位置进行确认,并签名填写完成时间4、将产品与首样检验报告交付给生产部拉长,并放置在拉头的位置,一张订单生产完后,由拉长拿着成品入库单及首件检验报告给PQA签字5、首件确认时间:电动类30分钟(切菜机、雪糕机)、加热类1小时(干果机)5.首件确认异常处理:品质部与工程部任何一个部门在确认首样的过程中出现了异常,都必须将不良信息及时反馈给生产部,若是外观性问题,需要更换一台OK的首样产品,重新进行确认;若是包装方式或产品性能及结构异常,生产部必须及时更改,只有首样确认合格后,才可进行生产6.相关文件1、工厂订单2、生产通知单3、BOM表4、成品检验作业指导书7.记录表格首件检验报告。
ISO9001-2015自检首检巡检管理程序A0
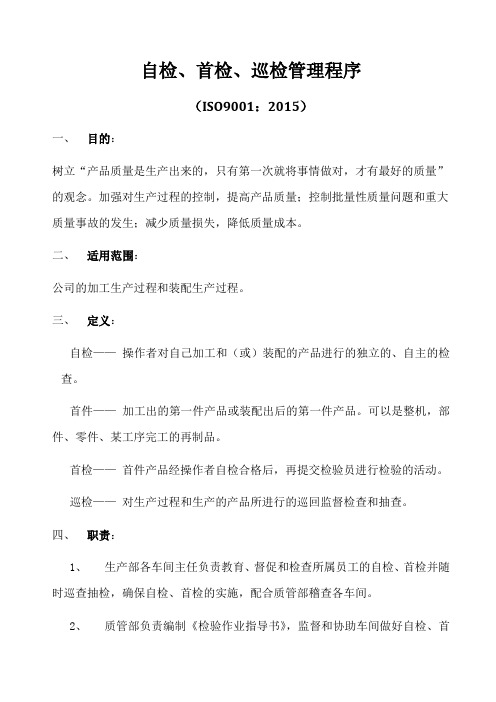
自检、首检、巡检管理程序(ISO9001:2015)一、目的:树立“产品质量是生产出来的,只有第一次就将事情做对,才有最好的质量”的观念。
加强对生产过程的控制,提高产品质量;控制批量性质量问题和重大质量事故的发生;减少质量损失,降低质量成本。
二、适用范围:公司的加工生产过程和装配生产过程。
三、定义:自检——操作者对自己加工和(或)装配的产品进行的独立的、自主的检查。
首件——加工出的第一件产品或装配出后的第一件产品。
可以是整机,部件、零件、某工序完工的再制品。
首检——首件产品经操作者自检合格后,再提交检验员进行检验的活动。
巡检——对生产过程和生产的产品所进行的巡回监督检查和抽查。
四、职责:1、生产部各车间主任负责教育、督促和检查所属员工的自检、首检并随时巡查抽检,确保自检、首检的实施,配合质管部稽查各车间。
2、质管部负责编制《检验作业指导书》,监督和协助车间做好自检、首检和巡检工作并组织生产品车间主任每周2次对车间质量稽查。
3、工艺部负责提供产品图纸、技术要求、相关技术标准、质量标准,编制相关工艺文件。
4、操作者具体实施自检、首检有关规定。
5、检验员具体负责管辖范围内的首件的专检、督促操作者自检,并进行巡检。
6、各车间班组长负责督促检查本班组员工进行自检、首检,并对本班组进行巡检。
7、稽查小组:由质管部长、质量工程师、过程检验组长、冲弯车间主任、钳焊车间主任。
五、程序:1、检验依据:产品图纸、规范和技术要求;工艺技术资料和相关标准;质量标准和相关检验资料等。
2、自检:操作者加工前应消化、理解有关图纸、工艺资料,弄清楚有疑问的地方。
核对来料、工装并按规定检查设备、工装、模具、量具、来料等均处于良好状态,方可进行生产。
操作者在加工或装配过程中应对产品在该工序的要求和产品外观不断地进行检查、核对。
发现产品有问题立即停止生产,在问题弄清楚并解决后再继续进行生产。
操作者不能弄清和解决质量问题时,必须立即向班组长、车间主任和检验员反映、汇报问题。
ISO9001-2015产品鉴别与追溯作业程序A0
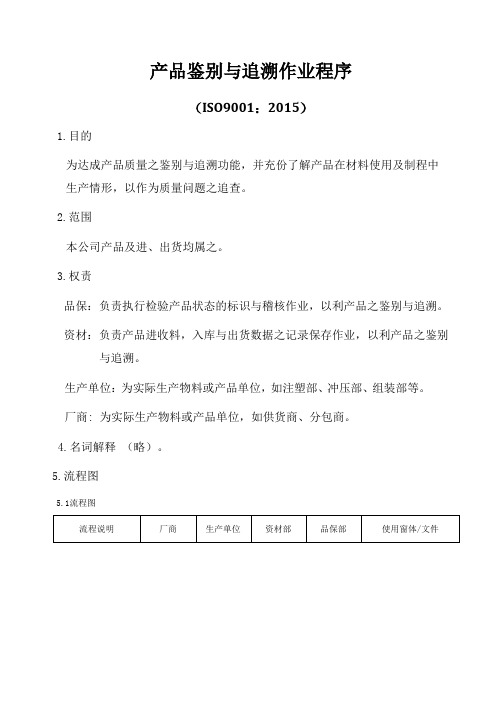
产品鉴别与追溯作业程序
(ISO9001:2015)
1.目的
为达成产品质量之鉴别与追溯功能,并充份了解产品在材料使用及制程中生产情形,以作为质量问题之追查。
2.范围
本公司产品及进、出货均属之。
3.权责
品保:负责执行检验产品状态的标识与稽核作业,以利产品之鉴别与追溯。
资材:负责产品进收料,入库与出货数据之记录保存作业,以利产品之鉴别与追溯。
生产单位:为实际生产物料或产品单位,如注塑部、冲压部、组装部等。
厂商: 为实际生产物料或产品单位,如供货商、分包商。
4.名词解释(略)。
5.流程图
5.1流程图
6.作业内容
6.1 产品之鉴别
ISO9001-2015内审员升级培训(100元) ISO9001-2015内审员培训(200元) :。
ISO9001-2015最终检验程序A0
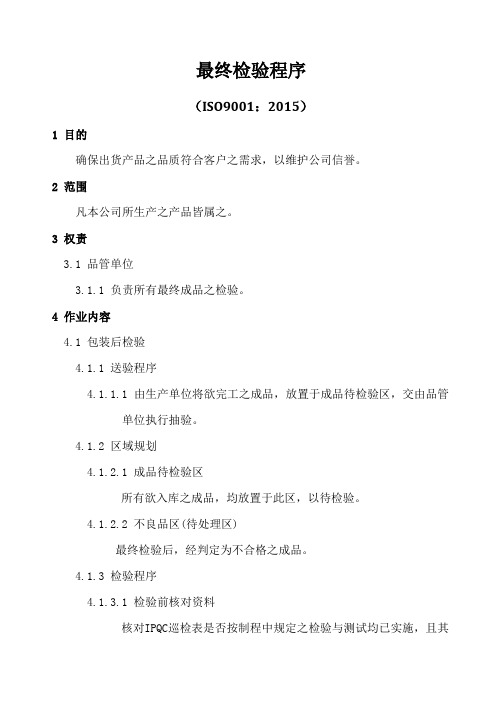
最终检验程序(ISO9001:2015)1 目的确保出货产品之品质符合客户之需求,以维护公司信誉。
2 范围凡本公司所生产之产品皆属之。
3 权责3.1 品管单位3.1.1 负责所有最终成品之检验。
4 作业内容4.1 包装后检验4.1.1 送验程序4.1.1.1 由生产单位将欲完工之成品,放置于成品待检验区,交由品管单位执行抽验。
4.1.2 区域规划4.1.2.1 成品待检验区所有欲入库之成品,均放置于此区,以待检验。
4.1.2.2 不良品区(待处理区)最终检验后,经判定为不合格之成品。
4.1.3 检验程序4.1.3.1 检验前核对资料核对IPQC巡检表是否按制程中规定之检验与测试均已实施,且其结果符合规定之要求。
4.1.3.2 检验4.1.3.2.1 外观与尺寸检验,参照各成品之检验规范实施。
4.2 入库前检验4.2.1 入库前由品管检查料号,品名,数量,功能规格,包装方式,包装标示,并核对工单编号是否制程中规定之检验及测试均已实施。
4.2.2 检查后登录于成品「FQC成品检验报告书」。
4.2.3 品管人员于检验合格后,在纸箱侧左上方贴上注有制造责任者及品检责任者之QC PASS标签.并依据「物品包装与装运管出货管制办法」办理入库。
4.3 不合格处理4.3.1 经检验不合格之成品须贴上不合格标示后置于不良品区,并通知生产单位,参照「不合格品管理程序」处置。
4.3.2 不合格成品若为客户急件时,由生管通知业务并召开物料鉴审会议讨论,参照「物料鉴审办法」办理。
4.3.3 为防止尔后生产再度发生相同之不良状况,须要求生产单位改善,参照「矫正及预防措施程序」办理。
4.4 检验设备及治工具管理4.4.1 检验设备及治工具使用前须先查看是否有合格标示及尚在有效校验期内。
4.4.2 治工具管理参照治工具管理办法。
4.4.3 检验设备管理参照仪器校验管理程序。
4.5 出货检查4.5.1 出货前由品管及业务人员依据「OQC检验报告」及「客户出货特别要求事项检核表」,检查品名,数量,合格标示及包装方式后,在销货单上盖上QC PASS章。
ISO9001-2015工序质量控制程序A0
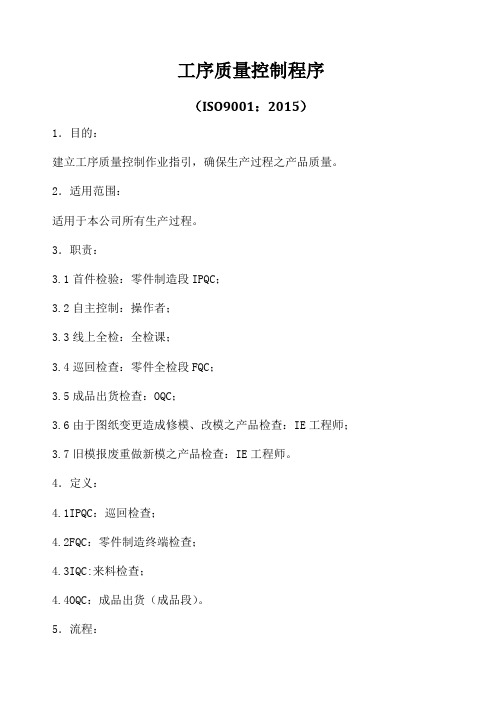
生产全检
复检工序 报废单
B 每天下班前 5.4 抽检 5.4.1 依据《控制计划》之规定和作业 指导书或产品规格书中之要求, 对相关的半成品, 成品进行检查。 检查合格,方可流入下道工序, 并做好检查不良记录。 5.4.2 巡检应将不良情况在第二天早会 不良品处 上宣导。 理单 制程检验 5.5 巡回检查 记录表 5.5.1 生产过程中的各工段,巡检根据 各段的控制计划之要求和相关作 业指导书对相关生产线做巡回检 查,按《控制计划》要求作相关 记录。 5.5.2IPQC 在巡回过程中若发现异常, 应立即知会生产单位即刻纠正。 若需其它部门配合解决时,填写 制程检验 《矫正和预防措施处理单》知会 记录表 品保部,生产部协同解决。属经 常性出现的制程异常或重大的品 质事故,应发出《矫正和预防措 施处理单》到相关责任单位,按 矫正和预 《矫正预防措施控制程序》处理 防措施处 进行。 理单 5.5.3 经协同处理的《矫正和预防措施 处理单》副本给生产部,要求生 产部严格按处理意见执行,并做
工序质量控制程序
(ISO9001:2015)
1.目的: 建立工序质量控制作业指引,确保生产过程之产品质量。 2.适用范围: 适用于本公司所有生产过程。 3.职责: 3.1 首件检验:零件制造段 IPQC; 3.2 自主控制:操作者; 3.3 线上全检:全检课; 3.4 巡回检查:零件全检段 FQC; 3.5 成品出货检查:OQC; 3.6 由于图纸变更造成修模、改模之产品检查:IE 工程师; 3.7 旧模报废重做新模之产品检查:IE 工程师。 4.定义: 4.1IPQC:巡回检查; 4.2FQC:零件制造终端检查; 4.3IQC:来料检查; 4.4OQC:成品出货(成品段) 。 5.流程:
生产者
生产过程中
- 1、下载文档前请自行甄别文档内容的完整性,平台不提供额外的编辑、内容补充、找答案等附加服务。
- 2、"仅部分预览"的文档,不可在线预览部分如存在完整性等问题,可反馈申请退款(可完整预览的文档不适用该条件!)。
- 3、如文档侵犯您的权益,请联系客服反馈,我们会尽快为您处理(人工客服工作时间:9:00-18:30)。
产品首件鉴定程序
1 目的和范围
本程序规定了产品首件鉴定的内容和要求,以确保生产工艺和生产设备满足产品要求,以验证和鉴定过程的生产能力。
本程序适用于本厂产品的首件鉴定。
2 引用标准及文件《质量管理体系要求》《质量手册》《质量记录控制程序》
3 术语和定义
无。
4 职责
a)技术处负责组织首件鉴定工作。
b)各生产单位负责编写首件生产总结
c)检验室负责编写首件检验总结
5 要求
首件鉴定是对试生产的第一件零部(组)件按设计图样和工艺规程的要求全面的过程和成品检查,以确定生产工艺和设备能否保证生产出符合设计要求的产品,以验证和鉴定过程的生产能力,并为零、部(组)件生产(工艺)定型做准备。
5.1 首件鉴定范围
a)新研制产品在工艺定型前的首件;
b)不连续的批生产,间隔一年后又恢复生产的首件;
c)设计图纸发生重大更改后生产的首件;
d)工艺规程发生重大更改后生产的首件;
e)合同要求指定的首件。
德信诚培训网
ISO9001-2015内审员升级培训(100元) ISO9001-2015内审员培训(200元) : 5.2 首件鉴定的内容
a )首件生产所依据的技术、工艺文件是否正确、完整、协调、有效;
b )产品的物理特性是否符合设计要求;
c )所用采购产品是否符合规定要求;
d )选用的所有设备能否满足生产要求,生产环境是否满足生产要求;
e )生产操作人员和检验人员是否具备资格和上岗证;
f )首件质量与其质量记录是否相符,质量问题是否按规定得到处理;
g )有顾客要求的工序是否经顾客签署认可。
5.3 首件鉴定的程序
a )技术处依据首件鉴定的范围确定产品的首件,编制首件鉴定目录,明确首件鉴定的项目、内容和要求,发送至各生产单位和检验部门;
b )生产和检验部门按规定程序,对首件做好标记,在生产过程中进行自检和专检并对实测数据进行记录,首件生产完成后,根据检查结果和记录内容,按要求编写首件生产总结和首件检验总结,提交技术处;
c )技术处组织首件鉴定会议,确定鉴定时间和鉴定组成员;
d )鉴定组长主持会议,生产单位和检验部门分别向会议报告首件生产和首件检验总结;
e )讨论并形成鉴定结论,填写首件鉴定证书;
f )首件鉴定形成结论的建议或改进措施,由技术处组织落实,质量管理处跟踪验证。
6 相关记录
a )首件鉴定目录表。