涂装车身漆膜质量检验标准
汽车涂装工艺中的漆膜质量评价指标

平整度
01
02
03
平整度
漆膜表面应光滑、连续, 无明显的凹凸、颗粒、气 泡等缺陷,以达到良好的 视觉效果。
检测方法
通过目视观察、触感检测 以及使用平整度检测仪器 进行定量测量。
影响因素
涂装过程中的施工方法、 环境温湿度、涂料粘度等 都会影响漆膜平整度。
光泽度
光泽度
漆膜表面反射光线的能力 ,体现漆膜的镜面效果。
要点二
详细描述
耐候性是指漆膜抵抗阳光、紫外线、风雨等气候因素影响 的能力。在汽车涂装工艺中,耐候性是评价漆膜质量的重 要指标之一,因为它直接影响到汽车在使用过程中的外观 保持能力。耐候性通常采用人工加速老化试验进行评估, 通过观察漆膜在模拟实际使用环境下的颜色变化、光泽丧 失、开裂等现象的发生程度来评价其耐候性能。
06
漆膜质量评价测试方法
目视评价法
总结词
通过观察漆膜表面,评估其外观、颜色 、光泽和纹理等特性。
VS
详细描述
目视评价法是最基本、最直观的漆膜质量 评价方法。评估人员通过肉眼观察漆膜表 面,检查是否存在颜色不均、气泡、裂纹 、杂质等缺陷。同时,观察漆膜的光泽和 纹理,以评估其美观度和质感。
仪器评价法
桔皮现象
桔皮现象
漆膜表面呈现类似桔皮状的纹理 ,影响外观质量。
检测方法
目视观察以及使用仪器测量桔皮的 大小和深度。
影响因素
涂料的流平性、涂装环境的温湿度 、涂装技术等都会导致桔皮现象的 产生。
Hale Waihona Puke 3漆膜物理性能评价指标硬度
总结词
硬度是衡量漆膜抵抗刮擦和划痕的能力的重要指标。
详细描述
硬度是指漆膜抵抗刮擦和划痕的能力。通常采用摆杆硬度计进行测量,摆杆硬 度计的测量原理是通过测量漆膜抵抗形变的能力来反映其硬度。硬度高的漆膜 能够更好地抵抗划痕和刮擦,保持外观的完整性。
涂装车身漆膜质量检验标准

所示红色框部分。
图1 A区域
2
以上至流水槽上边沿区域见图3所示红色框范围内。
图3 A区域
不允许有能识别的补漆痕。
不允许有砂纸纹存在,不允许有针孔、流痕存在。
不允许有露底、起泡、剥落、碰划伤、水印等缺陷。
的范围内允许有1颗直径d≤0.5mm
图5 B区域
右车门上部可视区
图6 B
图7 C区图8 C区图9 C区5.1.2后背门的内表面外露表面,见图10~所示红线区域。
图10 C区域处数C 区
图11 C区域
机舱内为C区,如图12所示红色线框内;
图12 C区域
前后保装配区域为C区,如图13~14所示红色线框内:
图13 C区域图14C区域
5.1.6 左右B柱、四轮轮罩下部打胶区域、车身内轮罩裸露区域、前舱盖内部区域、左右门下部、均为。
喷漆质量检验标准(二)2024
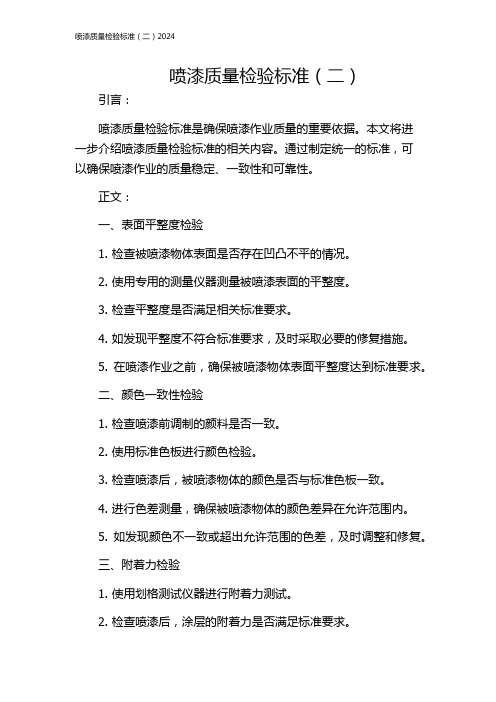
喷漆质量检验标准(二)引言:喷漆质量检验标准是确保喷漆作业质量的重要依据。
本文将进一步介绍喷漆质量检验标准的相关内容。
通过制定统一的标准,可以确保喷漆作业的质量稳定、一致性和可靠性。
正文:一、表面平整度检验1. 检查被喷漆物体表面是否存在凹凸不平的情况。
2. 使用专用的测量仪器测量被喷漆表面的平整度。
3. 检查平整度是否满足相关标准要求。
4. 如发现平整度不符合标准要求,及时采取必要的修复措施。
5. 在喷漆作业之前,确保被喷漆物体表面平整度达到标准要求。
二、颜色一致性检验1. 检查喷漆前调制的颜料是否一致。
2. 使用标准色板进行颜色检验。
3. 检查喷漆后,被喷漆物体的颜色是否与标准色板一致。
4. 进行色差测量,确保被喷漆物体的颜色差异在允许范围内。
5. 如发现颜色不一致或超出允许范围的色差,及时调整和修复。
三、附着力检验1. 使用划格测试仪器进行附着力测试。
2. 检查喷漆后,涂层的附着力是否满足标准要求。
3. 根据测试结果进行分类评定,确定涂层的附着力等级。
4. 如发现附着力不达标,进行涂层修复或重新喷漆。
5. 在喷漆过程中,确保涂层与基材之间的附着力达到标准要求。
四、漆膜厚度检验1. 使用合适的测厚仪器测量漆膜厚度。
2. 对喷漆后的涂层进行均匀性检验,确认漆膜厚度的一致性。
3. 检查漆膜厚度是否符合相关标准要求。
4. 如发现漆膜厚度不符合要求,进行涂层修复或重新喷漆。
5. 在喷漆作业中,保证漆膜厚度达到标准要求,以确保喷漆质量的稳定性和可靠性。
五、环境适应性检验1. 在不同环境条件下,对喷漆后的涂层进行测试。
2. 检查涂层在高温、低温、湿度和紫外线等条件下的表现。
3. 确保涂层能够适应各种不同的环境要求。
4. 根据测试结果进行评定,并确定涂层的环境适应性等级。
5. 如发现涂层在特定环境下性能不佳,进行相关调整和修复,以提高涂层的环境适应性。
总结:喷漆质量检验标准的建立和实施对于确保喷漆作业的质量稳定和可靠性至关重要。
车身油漆检验技术条件(3版)
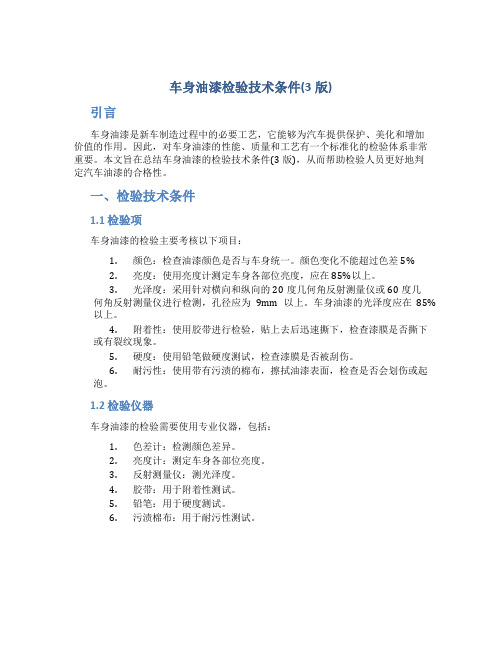
车身油漆检验技术条件(3版)引言车身油漆是新车制造过程中的必要工艺,它能够为汽车提供保护、美化和增加价值的作用。
因此,对车身油漆的性能、质量和工艺有一个标准化的检验体系非常重要。
本文旨在总结车身油漆的检验技术条件(3版),从而帮助检验人员更好地判定汽车油漆的合格性。
一、检验技术条件1.1 检验项车身油漆的检验主要考核以下项目:1.颜色:检查油漆颜色是否与车身统一。
颜色变化不能超过色差5%2.亮度:使用亮度计测定车身各部位亮度,应在85%以上。
3.光泽度:采用针对横向和纵向的20度几何角反射测量仪或60度几何角反射测量仪进行检测,孔径应为9mm以上。
车身油漆的光泽度应在85%以上。
4.附着性:使用胶带进行检验,贴上去后迅速撕下,检查漆膜是否撕下或有裂纹现象。
5.硬度:使用铅笔做硬度测试,检查漆膜是否被刮伤。
6.耐污性:使用带有污渍的棉布,擦拭油漆表面,检查是否会划伤或起泡。
1.2 检验仪器车身油漆的检验需要使用专业仪器,包括:1.色差计:检测颜色差异。
2.亮度计:测定车身各部位亮度。
3.反射测量仪:测光泽度。
4.胶带:用于附着性测试。
5.铅笔:用于硬度测试。
6.污渍棉布:用于耐污性测试。
二、检验流程2.1 样品准备取车身各部位标准色板与待检车辆做对照,在同一光线下进行检测。
2.2 检验步骤1.颜色检验:取3个样品进行检测,按顺序放在色差计上,检测色差值是否在标准范围内。
2.亮度检验:使用亮度计进行测量,注意在同一光线下检测各部位的亮度。
3.光泽度检验:使用反射测量仪进行测量,注意测量角度,避免误差。
4.附着性检验:使用胶带进行测试,贴上胶带后,迅速撕下,检查油漆漆膜是否撕下或有裂纹现象。
5.硬度检验:使用铅笔进行测试,检查油漆表面是否有刮痕。
6.耐污性检验:使用带有污渍的棉布擦拭,检查是否会产生划痕或泡沫。
2.3 结果判定根据检测结果,依据《车身油漆检验技术条件》标准确定车身油漆是否合格,记录检测因素的数据,判断是否符合标准。
油漆相关质量检验标准
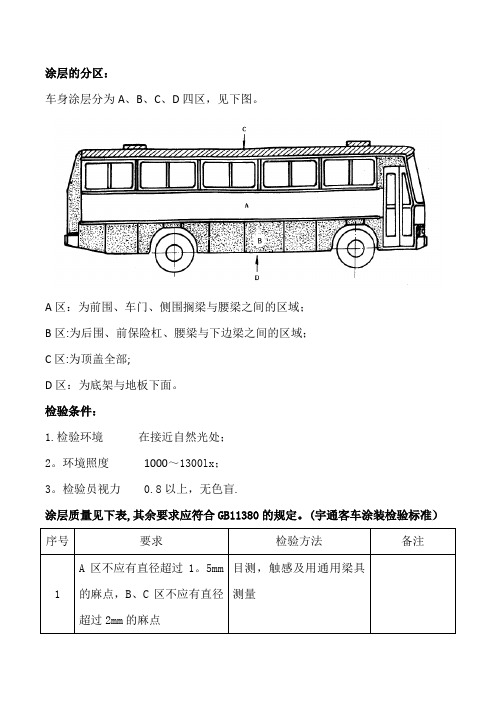
涂层的分区:车身涂层分为A、B、C、D四区,见下图。
A区:为前围、车门、侧围搁梁与腰梁之间的区域;B区:为后围、前保险杠、腰梁与下边梁之间的区域;C区:为顶盖全部;D区:为底架与地板下面。
检验条件:1.检验环境在接近自然光处;2。
环境照度1000~1300lx;3。
检验员视力 0.8以上,无色盲.涂层质量见下表,其余要求应符合GB11380的规定。
(宇通客车涂装检验标准)涂层外观缺陷分类:(引用GBT13052-91)1.麻点:涂层表面出现的凹坑现象,即由水、气泡破裂而产生的泡疤。
2.颗粒:涂层表面粘附的影响漆膜光滑度的杂质颗粒现象。
3。
针孔:涂层表面出现一些透底针状小孔的现象。
4.杂漆:涂层表面出现不相溶的多种色点(块)的现象。
5.桔皮状皱纹:涂层表面出现桔皮状纹的折皱现象.6.露白:涂层表面能见到本体材料(白—指由于底漆涂装不均匀而露本体材料本色).7.露底:涂层表面呈现前道涂层的色泽现象.8。
流痕:涂层表面出现涂料流淌痕迹的现象。
9.划伤:涂层表面出现由外力引起的不同形状的磕碰划痕的现象。
漆膜附着力测定方法(引用GB1720-1979)1.按《漆膜一般制备法》(GB1727)在马口铁板上(或按产品标准规定的底材)制备样板3块,待漆膜实干后,于恒温恒湿的条件下测定.测前先检查附着力测定仪的针头,如不锐利应予更换:提起半截螺帽(7),抽出试验台(6),即可换针。
当发现划痕与标准回转半径不符时,应调整回转半径,其方法是松开卡针盘(3)后面的螺栓、回转半径调整螺栓(4),适当移动卡针盘后,依次紧固上述螺栓,划痕与标准圆滚线图比较,如仍不符应重新调整回转半径,直至与标准回转半径5.25毫米的圆滚线相同为调整完毕。
测定时,将样板正放在试验台(6)上,拧紧固定样板调整螺栓(5)、(8)和调整螺栓(10),向后移动升降棒(2),使转针的尖端接触到漆膜,如划痕未露底板,应酌加砝码。
按顺时针方向,均匀摇动摇柄(11),转速以80~100转/分为宜,圆滚线划痕标准图长为7。
汽车喷涂产品检验标准
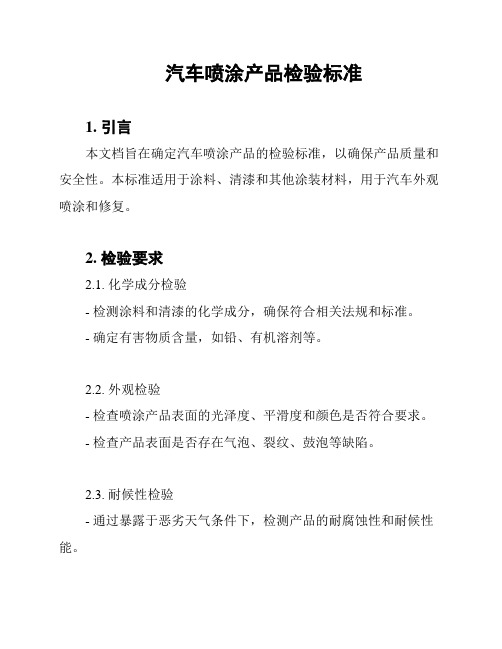
汽车喷涂产品检验标准
1. 引言
本文档旨在确定汽车喷涂产品的检验标准,以确保产品质量和安全性。
本标准适用于涂料、清漆和其他涂装材料,用于汽车外观喷涂和修复。
2. 检验要求
2.1. 化学成分检验
- 检测涂料和清漆的化学成分,确保符合相关法规和标准。
- 确定有害物质含量,如铅、有机溶剂等。
2.2. 外观检验
- 检查喷涂产品表面的光泽度、平滑度和颜色是否符合要求。
- 检查产品表面是否存在气泡、裂纹、鼓泡等缺陷。
2.3. 耐候性检验
- 通过暴露于恶劣天气条件下,检测产品的耐腐蚀性和耐候性能。
2.4. 附着力检验
- 确定涂层与底材之间的粘附力,以评估涂层的质量和稳定性。
2.5. 耐化学品检验
- 检测涂层的耐化学品性能,包括耐溶剂、酸碱、汽油等。
2.6. 薄膜厚度检验
- 测量涂层的薄膜厚度,以确保涂层均匀和符合要求。
3. 检验方法
- 使用合适的仪器和设备进行检验,包括光泽度计、显微镜、
冷热循环试验箱等。
- 根据相关标准和法规执行检验过程,并记录检测结果。
4. 结论
- 根据检验结果确定产品是否符合标准要求,以及是否能够满
足汽车喷涂的使用要求和性能。
5. 参考文献
- [相关法规和标准]
以上为汽车喷涂产品检验标准的基本内容,详细的检验流程和要求应根据具体情况和相关标准进行进一步制定。
以下内容是你可以参考的相关法规和标准:
[相关法规和标准1]
[相关法规和标准2]
[相关法规和标准3]。
车身喷漆质量标准
抛光漆
3、无杂质、针孔、砂痕、翘皮、露底、漏喷等质量缺陷。 4、边棱整洁、整齐、光滑美观、无露边、流痕、积漆等不良现象。 5、不喷漆部位保持干净。
质检签名:
年
月
日
车身喷漆质量标准 车身补漆质量标准
类别 项目 色一致,不允许有色差
量
要
求
□合格 □不合格 □合格 □不合格 □合格 □不合格 □合格 □不合格 □合格 □不合格 □合格 □不合格 □合格 □不合格 □合格 □不合格 □合格 □不合格 □合格 □不合格 □合格 □不合格 □合格 □不合格 □合格 □不合格 □合格 □不合格 □合格 □不合格 □合格 □不合格 □合格 □不合格 □合格 □不合格 □合格 □不合格 □合格 □不合格 □合格 □不合格 □合格 □不合格
1、抛光修饰后的漆蜡光泽应与大面光泽一致成略有光差,有允许有明显的磨痕
划痕与擦痕 严重划伤(包 1、补漆后后光泽和颜色与大面光泽与颜色一致或近似允许略有光差或轻微的色差 修补 括穿透面漆或 2、补漆面的平整光滑度与大面一致,不允许有颗粒杂质,精纹、砂痕、雾灯等不良现象 者穿透底漆) 3、不漆部位保持清洁,不允许有残漆雾灯不良现象 色漆 小 面 补 漆 抛光漆 金属漆 1、漆膜镜面般平滑,光泽照出人影,颜色与大面一致,不允许有杂质、桔纹及明显的色差、光差等不良现名象 2、不漆部位保持清洁,不允许有残漆雾、腻子渣、残漆迹等不良现象 1、漆膜镜面般平滑,光泽照出人影,颜色与大面一致,不允许有色差、光差、补痕等不良现象 2、玻璃、车灯、电镀件、五金件应保持清洁整齐,无残漆迹等不良现象 1、金属色浆颜色与大面一致,漆膜丰满度好,光泽高。平整光滑,无颗粒、桔纹、针孔、砂痕、灰尘及明显的补痕搭接。 2、其他漆面保持清洁,玻璃、仪表、电镀标志、车灯、车身压条等 金属色浆残迹、清漆无痕等不良现象。 1、漆膜平整光滑,鲜艳度好,光泽、颜色与整车面漆一致,不得有流泪、流挂、杂质、桔纹、针孔、气泡、麻眼等缺陷。 色漆 整 面 补 漆 金属漆 2、边棱整洁、整齐、漆膜光滑平等,不得有毛边,流痕,积漆,漏涂等缺陷。 3、不漆部位保持清洁,不允许有残漆或残胶迹(胶带粘痕等不良现象) 4、玻璃与五金件保持干净 1、金属色浆颜色与整车颜色一致 2、漆膜丰满,平滑光亮,附着力强,不得有流漆、桔纹、杂质、揭皮、气泡、针孔等缺陷 3、其他部位的漆面干净整洁、无胶迹、残漆迹、雾痕等不良现象 4、玻璃与五金件保持干净。
汽车车身油漆涂装检验标准及具体要求
********系列汽车车身涂装技术质量强制执行标准1主题内容与执行范围本标准规定了********汽车有限公司系列汽车车身油漆涂装检验的检验内容,技术要求,检验方法以及检验标准。
2引用标准下列标准所包含的条文,通过在本标准中引用而构成本标准的条文。
在标准出版时,所示版本均为有效,所有标准都会被修订,使用本标准的各方应探讨使用下列各标准最新版本的可能性。
QC/T484 汽车油漆涂层GB 1728 涂膜,腻子干燥时间测定办法GB 1764 漆膜厚度测定方法GB 1743 漆膜光泽测定办法GB 1720 漆膜附着力测定办法GB 1723 漆料粘度测定办法3用语解释3.1车身油漆涂装质量车身油漆涂装质量是指为实现装饰、防护(防锈、仿蚀)、隔音、绝热和密封抗石击等,而涂装在表面上的油漆涂层的外观质量和内在质量,以及涂装工作质量和工程质量3.2漆后车身漆后车身是指油漆涂层涂装施工完成后的车身3.3油漆涂层缺陷用语光泽:漆膜表面镜面反射的强度色差(△E):用数值表示车身颜色相对于标准颜色(以颜色标准件为基准)的差别。
桔皮:漆膜表面不光滑,有波浪纹理的外观桔子皮一样不平的表面。
油漆损伤:由于油漆表面受到摩擦或者碰撞引起的少量漆膜脱落。
发花:是指金属粉在漆膜中混乱排列流痕:喷涂在垂直面上的涂料向下流动,使漆面产生条痕的现象,轻微时叫流痕。
针孔:是指漆膜表面的像动物毛孔一样的小孔,通常在0.1mm左右。
颗粒:漆膜中间,上面或下面混入的灰粒,漆渣等凸突状异物。
絮状丝:是指奇妙上面或中间混入的长形弯形的纤维丝,绒毛等絮状的丝状异物(如絮状丝夹杂着油漆形成凸突状的漆渣,可视为漆面颗粒,按颗粒质量检验标准检验)。
砂纸纹:在面漆涂面上显示出的线条或圆圈的砂纸打磨纹。
钣金凹凸:在金属表面或底板上看得出来的局部凹凸。
缩孔:其外观像火山喷口一样的凹陷,有可能露出或不露出下面的漆层,通常直径为0.5~3mm。
划伤:漆膜完全固化后受外力等作用,产生的线状伤痕。
漆膜附着力检测标准
漆膜附着力检测标准漆膜附着力是指涂层与基材之间的结合强度,是涂料涂装质量的重要指标之一。
漆膜附着力的好坏直接影响涂层的使用寿命和性能。
因此,对漆膜附着力进行准确可靠的检测是非常重要的。
本文将介绍漆膜附着力检测的标准方法,以便为相关行业提供参考。
一、划格法。
划格法是一种常用的漆膜附着力检测方法。
其原理是利用划格刀在涂层表面划出一定间距的划痕,然后用胶带将划痕处的涂层粘起,通过观察粘起的涂层面积来评定漆膜附着力的好坏。
划格法的标准操作流程如下:1. 准备工作,将划格刀、胶带、划格板等工具准备齐全,并确保涂层表面干燥、清洁。
2. 划格操作,用划格刀在涂层表面划出一定间距的划痕,划痕的长度和深度应符合标准要求。
3. 胶带粘取,用胶带将划痕处的涂层粘起,然后迅速撕下胶带。
4. 评定结果,观察胶带上粘起的涂层面积,根据标准要求进行评定。
二、拉伸法。
拉伸法是另一种常用的漆膜附着力检测方法。
其原理是利用拉伸力将涂层从基材上拉离,通过观察涂层脱落的情况来评定漆膜附着力的好坏。
拉伸法的标准操作流程如下:1. 准备工作,将拉伸测试机、夹具、标准样品等工具准备齐全,并确保涂层表面干燥、清洁。
2. 夹具固定,将涂层样品固定在拉伸测试机的夹具上,确保夹具与涂层之间的结合牢固。
3. 施加拉伸力,启动拉伸测试机,施加逐渐增大的拉伸力,直到涂层脱落为止。
4. 评定结果,观察涂层脱落的情况,根据标准要求进行评定。
三、压接法。
压接法是一种简便易行的漆膜附着力检测方法。
其原理是利用压接机将涂层与基材之间的结合强度进行压力测试,通过观察压接后的情况来评定漆膜附着力的好坏。
压接法的标准操作流程如下:1. 准备工作,将压接机、压接头、标准样品等工具准备齐全,并确保涂层表面干燥、清洁。
2. 压接操作,将压接头置于涂层表面,启动压接机施加一定的压力,然后迅速撤除压接头。
3. 评定结果,观察压接后涂层与基材之间的情况,根据标准要求进行评定。
综上所述,漆膜附着力的检测标准方法主要包括划格法、拉伸法和压接法。
喷漆外观质量检验标准(二)(2024)
引言:喷漆外观质量检验标准是衡量喷漆产品表面质量的重要标准之一。
本文将通过引言概述、正文内容和总结等部分,系统详细阐述喷漆外观质量检验标准的相关内容。
概述:喷漆外观质量检验标准是制定和遵守的一套规定,旨在保证喷漆产品的外观质量稳定达标。
喷漆外观质量检验标准的制定包括外观缺陷分类、检验方法、测试仪器和评定标准等方面。
本文将通过正文内容,按照正条相关的检验标准,以期为喷漆外观质量检验提供详尽的指导。
正文内容:一、外观缺陷分类1.涂装表面缺陷:主要包括漆膜起皱、起泡、开裂、脱落等缺陷,要求对喷漆表面进行细致检查。
2.涂装颜色缺陷:主要包括色差、色斑、色纹等缺陷,要求使用颜色检测仪进行检验。
3.涂装光泽缺陷:主要包括发光度不均、亮度不足等缺陷,要求使用光泽度仪进行测量。
4.涂装漏喷缺陷:主要包括漆膜少喷、漆膜漏喷等缺陷,要求对喷漆的覆盖面积进行严格检查和评定。
5.涂装划伤缺陷:主要包括刀痕、刮痕等缺陷,要求对喷漆表面进行显微镜检查。
二、检验方法1.目视检查法:根据外观缺陷分类,通过肉眼观察的方法进行检验,对明显的外观缺陷进行评定。
2.仪器检测法:使用专业的检测仪器进行检验,如颜色检测仪、光泽度仪等,对颜色、光泽等外观质量进行定量检测。
三、测试仪器1.颜色检测仪:用于精确测量涂装颜色的仪器,能够判断出色差、色斑等问题。
2.光泽度仪:用于测量涂装光泽度的仪器,能够量化反射光的亮度,判断出涂装漆面是否光洁度不足。
3.显微镜:用于检查涂装划伤缺陷的仪器,能够放大细微的划痕并进行评定。
四、评定标准1.外观缺陷等级评定:根据外观缺陷的严重程度,将其分为轻微、一般、严重三个等级,并根据不同等级制定相应的处理措施。
2.涂装颜色差异评定:根据颜色差值,将涂装颜色的差异进行分级,以确定是否达到标准要求。
3.光泽度评定:通过光泽度仪测量的数值,判断涂装的光泽度是否符合标准要求。
五、小点详述1.对于涂装表面缺陷的检验,应仔细观察漆膜的起皱、起泡、开裂、脱落等情况。
- 1、下载文档前请自行甄别文档内容的完整性,平台不提供额外的编辑、内容补充、找答案等附加服务。
- 2、"仅部分预览"的文档,不可在线预览部分如存在完整性等问题,可反馈申请退款(可完整预览的文档不适用该条件!)。
- 3、如文档侵犯您的权益,请联系客服反馈,我们会尽快为您处理(人工客服工作时间:9:00-18:30)。
技术要求
试验方法
铅笔硬度
≥H
GB/T6739-1996中铅笔涂膜硬度测定法(附录A)
附着力
0~1级
GB/T9286-1998中的划格测定法(附录B)
耐冲击力
≥
GB/T1732-93 漆膜耐冲击测定法(附录C)
7 试验方法
各分区外观、色差采用目视检测。
各分区铅笔硬度检测可直接在车身漆膜表面检测。
各分区膜厚、光泽采用相应仪器在车身表面直接测量。
4 结果的表示
a)撕离胶粘带后立即在良好的照明环境中、用正常的或校正过的视力观察样 板。观察过程中,转动样板,以使试验面的观察和照明不局限在一个方向。
b)按下列标准对试验结果分级
0级:切割边缘完全平滑,无一格脱落。
1级:在切口交叉处有少许涂层脱落,但交叉切割面积受影响不能明显大于5%。
2级:在切口交叉处或沿切口边缘有涂层脱落,受影响的交叉切割面积明显大于5%,但不能明显大于15%。
标记
处数
更改依据
签字
日期
编制(日期)
审核(日期)
会签(日期)
批准(日期)
涂装检验作业指导书
涂装车身漆膜检验标准
文件编号
版本
第一版
生效日期
2012-5-23
B区漆膜综合性能见表2:
表2 漆膜综合性能
项目
技术要求
试验方法
光泽度
(60度角)≥90
光泽仪测定
硬度
≥H
GB/T6739-1996中铅笔涂膜硬度测定法(附录A)
文件编号
版本
第一版
生效日期
2012-5-23
车身前机盖及顶盖表面
车身前机盖外表面区域和前挡风玻璃上沿至顶盖区域外表面200mm区域,见图2所示红色框区域内。
图2
后盖外表面及顶盖后表面
后盖外表面(含后盖底边)以上至流水槽上边沿区域见图3所示红色框范围内。
图3 A区域
A区外观要求
不允许有能识别的补漆痕。
f)按均匀的速度拉出一段胶粘带,除去最前面的一段,然后剪下长约75mm的胶粘带。把该胶粘带的中心点放在网格上方,方向与一组切割线平行然后用手指把胶粘带在网格区上方的部位压平,胶粘带长度至少超过网格20mm。为了确保胶粘带与涂层接触良好,用手指尖用力蹭胶粘带。透过胶粘带看到的涂层颜色全面接触是有效的显示。在贴上胶粘带5min内,拿住胶粘带悬空的一端,并在尽可能接近60°的角度,在~内平稳地撕离胶粘带;
f)涂膜划破:将未满二道的铅笔硬度标号作为涂膜的铅笔硬度。
标记
处数
更改依据
签字
日期
编制(日期)
审核(日期)
会签(日期)
批准(日期)
涂装检验作业指导书
涂装车身漆膜检验标准
文件编号
版本
第一版
生效日期
2012-5-23
附录B
资料性附录
GB/T 9286-1998 漆膜附着力测定法(划格法)
1.仪器设备
切割工具:a)单刃切割刀具;
3 A区划分及要求
A区域划分
侧表面
车身左右外侧表面(含车门底边)(红色标注)以上至流水槽上边沿区和车身顶盖前挡风玻璃左右侧200mm宽的区域表面以及左右前翼子板各外表面,见图1所示红色框部分。
图1A区域
标记
处数
更改依据
签字
日期
编制(日期)
审核(日期)
会签(日期)
批准(日期)
涂装检验作业指导书
涂装车身漆膜检验标准
后背门门框为C区,如图11所示白框线内:
图11 C区域
机舱内为C区,如图12所示红色线框内;
图12 C区域
前后保装配区域为C区,如图13~14所示红色线框内:
图13 C区域 图14C区域
左右B柱 、四轮轮罩下部打胶区域、车身内轮罩裸露区域、前舱盖内部区域、左右门下部、均为C区域。
标记
处数
更改依据
签字
不允许有易识别的补漆痕存在。
车门底部(图6 B区)外观按C区要求执行,漆膜总厚度≥60um。
B区色差
漆膜颜色与标准色板一致,不应有目视的差异。
色差目视有争议时,用色差仪测定,漆膜颜色与标准色板的色差△E≦,油漆车身颜色与外饰件的色差△E≦.
B区膜厚及测定方法
B区 膜厚: 电泳底漆20±2um 金属漆总厚度≥90um 素色漆总厚度≥85um
验收区域
验收区域的照度为800~1500lx,均匀照射,采用带反射板自然纯正色日光灯照明。
验收人员
验收人员辨色力正常,视力为以上(含校正后),验收人员应具有较丰富的涂装检验知识和实践经验,了解涂装工艺规程及技术要求。
测试方法
除仪器测定外,目测点到被验收面的距离为(~)m,目测角度在被验收面的任一方向。
线孔内表面和电池箱盖内表面,见图图7-图9所示红色线框内。
图7 C区 图8 C区 图9 C区
后背门的内表面外露表面,见图10~所示红线区域。
图10 C区域
标记
处数
更改依据
签字
日期
编制(日期)
审核(日期)
会签(日期)
批准(日期)
涂装检验作业指导书
涂装车身漆膜检验标准
文件编号
版本
第一版
生效日期
2012-5-23
批准(日期)
涂装检验作业指导书
涂装车身漆膜检验标准
文件编号
版本
第一版
生效日期
2012-5-23
6 D区划分及要求
车门全部打开时,目视看不到的区域,包括车身底板、车身内顶部。
D区外观要求
要求不露金属底材,无法电泳的部位要喷补防石击涂料或中涂底漆。
D区膜厚
电泳漆≥10um
D区漆膜性能要求见表4
表4漆膜综合性能
GB/T6739-1996涂膜硬度铅笔测定法
1 工具
a)中华牌高级绘图铅笔
b).400#砂纸;
c)削笔刀。
2 材料
样板
3 测试步骤
a)选取样板一测定位置.
b) 试验用铅笔制备:用削刀笔削去木杆部分,使铅笔芯呈圆柱状,露出约3mm,然后在坚硬的平面上放置砂纸,将铅笔垂直靠在砂纸上画圆圈,慢慢地研磨直至铅笔尖端磨成平面,边缘锐利为止。
日期
编制(日期)
审核(日期)
会签(日期)
批准(日期)
涂装检验作业指导书
涂装车身漆膜检验标准
文件编号
版本
第一版
生效日期
2012-5-23
C区域外观
总体要求不露底,不流挂,不发花,色漆、清漆不漏喷,但隐蔽无法观察到的部位允许有不明显的补漆痕、流痕和清漆漏喷存在。
在100mm×100mm的范围内允许有10颗直径d≤的颗粒存在。
C区漆膜综合性能见表3
表3漆膜综合性能
项目
技术要求
试验方法
硬度
≥H
GB/T6739-1996中铅笔涂膜硬度测定法(附录A)
附着力
0~1级
GB/T9286-1998中的划格测定法(附录B)
耐冲击力
≥
GB/T1732-93 漆膜耐冲击测定法(附录C)
标记
处数
更改依据
签字
日期
编制(日期)
审核(日期)
会签(日期)
mm
图4 B区域
标记
处数
更改依据
签字
日期
编制(日期)
审核(日期)
会签(日期)
批准(日期)
涂装检验作业指导书
涂装车身漆膜检验标准
文件编号
版本
第一版
生效日期
2012-5-23
车顶盖除A区(外沿宽200mm范围为A区)以外的区域
车顶盖除A区以外的区域,见图5所示红色框线内:
图5 B区域
左右车门上部可视区域及车身门框非内饰安装部位,见图6红色框线内:
标准等国家及欧盟的环保法律法规的要求。
标记
处数
更改依据
签字
日期
编制(日期)
审核(日期)
会签(日期)
批准(日期)
涂装检验作业指导书
涂装车身漆膜检验标准
文件编号
版本
第一版
生效日期
2012-5-23
1 范围
本文件规定了涂装后车身的验收条件、漆膜涂层A、B、C、D区域划分和验收方法。
本文件适用于电动车。
2 验收条件
图6 B区域
B区外观:
不允许有露底、起泡、剥落、碰划伤、水印。
不允许有能识别的流痕存在。
在100mm×100mm的范围内允许有3颗直径d≤的颗粒存在。
在100mm×100mm的面积内允放有直径d≤的针孔存在,但数量不超过10个。
允许有不影响外观的隐约可见的、分布均匀、轻微“桔皮”存在。
允许有不影响整体外观的存在。
漆膜光泽度按《漆膜光度测量仪说明书》中规定的测定方法测定。
涂膜硬度按GB/T6739-1996中涂膜硬度铅笔测定法的规定测定,详见附录A(资料性附录)。
漆膜附着力按GB/T9286-1998中的漆膜附着力测定法(划格法)的规定测定,详见附录B(资料性附录)。
漆膜耐冲击力按GB/T1732-93漆膜耐冲击测定法的规定测定,详见附录C(资料性附录)。
涂装车身漆膜检验标准
文件编号
版本
第一版
生效日期
2012-5-23
编制说明
为了指导车身漆膜产品验收,特制定本文件。
本文件规定了电动车车身涂装检验区域A、B、C、D区域的划分与漆膜验收的技术要求。
漆膜各项性能试验,采用在工艺定型时,制备样板,进行测试。其中:
漆膜总厚度按《膜厚仪说明书》中规定的测定方法测定。
附着力
0~1级
GB/T9286-1998中的划格测定法(附录B)